高速钢的淬火.docx
《高速钢的淬火.docx》由会员分享,可在线阅读,更多相关《高速钢的淬火.docx(13页珍藏版)》请在冰豆网上搜索。
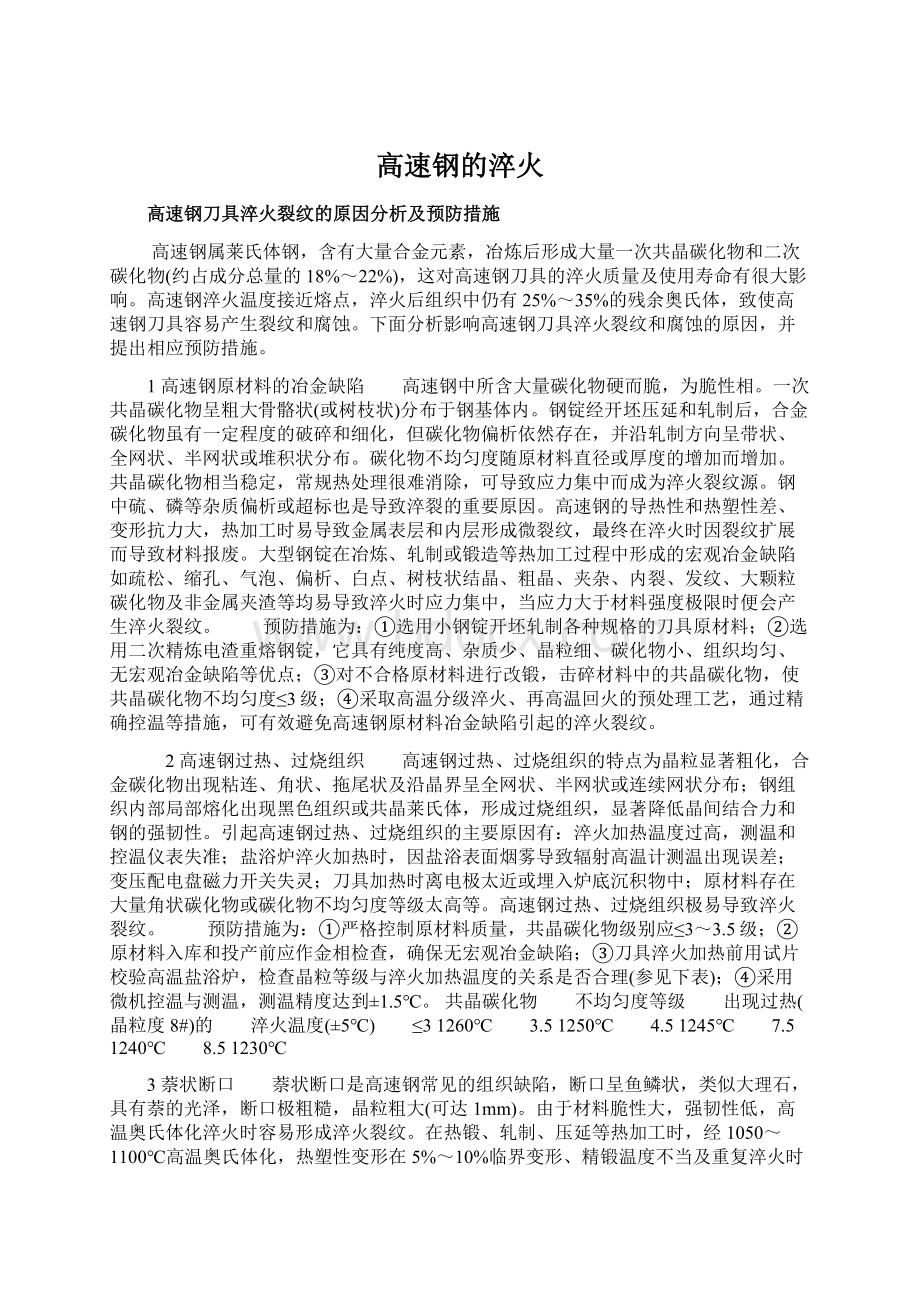
高速钢的淬火
高速钢刀具淬火裂纹的原因分析及预防措施
高速钢属莱氏体钢,含有大量合金元素,冶炼后形成大量一次共晶碳化物和二次碳化物(约占成分总量的18%~22%),这对高速钢刀具的淬火质量及使用寿命有很大影响。
高速钢淬火温度接近熔点,淬火后组织中仍有25%~35%的残余奥氏体,致使高速钢刀具容易产生裂纹和腐蚀。
下面分析影响高速钢刀具淬火裂纹和腐蚀的原因,并提出相应预防措施。
1高速钢原材料的冶金缺陷 高速钢中所含大量碳化物硬而脆,为脆性相。
一次共晶碳化物呈粗大骨骼状(或树枝状)分布于钢基体内。
钢锭经开坯压延和轧制后,合金碳化物虽有一定程度的破碎和细化,但碳化物偏析依然存在,并沿轧制方向呈带状、全网状、半网状或堆积状分布。
碳化物不均匀度随原材料直径或厚度的增加而增加。
共晶碳化物相当稳定,常规热处理很难消除,可导致应力集中而成为淬火裂纹源。
钢中硫、磷等杂质偏析或超标也是导致淬裂的重要原因。
高速钢的导热性和热塑性差、变形抗力大,热加工时易导致金属表层和内层形成微裂纹,最终在淬火时因裂纹扩展而导致材料报废。
大型钢锭在冶炼、轧制或锻造等热加工过程中形成的宏观冶金缺陷如疏松、缩孔、气泡、偏析、白点、树枝状结晶、粗晶、夹杂、内裂、发纹、大颗粒碳化物及非金属夹渣等均易导致淬火时应力集中,当应力大于材料强度极限时便会产生淬火裂纹。
预防措施为:
①选用小钢锭开坯轧制各种规格的刀具原材料;②选用二次精炼电渣重熔钢锭,它具有纯度高、杂质少、晶粒细、碳化物小、组织均匀、无宏观冶金缺陷等优点;③对不合格原材料进行改锻,击碎材料中的共晶碳化物,使共晶碳化物不均匀度≤3级;④采取高温分级淬火、再高温回火的预处理工艺,通过精确控温等措施,可有效避免高速钢原材料冶金缺陷引起的淬火裂纹。
2高速钢过热、过烧组织 高速钢过热、过烧组织的特点为晶粒显著粗化,合金碳化物出现粘连、角状、拖尾状及沿晶界呈全网状、半网状或连续网状分布;钢组织内部局部熔化出现黑色组织或共晶莱氏体,形成过烧组织,显著降低晶间结合力和钢的强韧性。
引起高速钢过热、过烧组织的主要原因有:
淬火加热温度过高,测温和控温仪表失准;盐浴炉淬火加热时,因盐浴表面烟雾导致辐射高温计测温出现误差;变压配电盘磁力开关失灵;刀具加热时离电极太近或埋入炉底沉积物中;原材料存在大量角状碳化物或碳化物不均匀度等级太高等。
高速钢过热、过烧组织极易导致淬火裂纹。
预防措施为:
①严格控制原材料质量,共晶碳化物级别应≤3~3.5级;②原材料入库和投产前应作金相检查,确保无宏观冶金缺陷;③刀具淬火加热前用试片校验高温盐浴炉,检查晶粒等级与淬火加热温度的关系是否合理(参见下表);④采用微机控温与测温,测温精度达到±1.5℃。
共晶碳化物 不均匀度等级 出现过热(晶粒度8#)的 淬火温度(±5℃) ≤31260℃ 3.51250℃ 4.51245℃ 7.51240℃ 8.51230℃
3萘状断口 萘状断口是高速钢常见的组织缺陷,断口呈鱼鳞状,类似大理石,具有萘的光泽,断口极粗糙,晶粒粗大(可达1mm)。
由于材料脆性大,强韧性低,高温奥氏体化淬火时容易形成淬火裂纹。
在热锻、轧制、压延等热加工时,经1050~1100℃高温奥氏体化,热塑性变形在5%~10%临界变形、精锻温度不当及重复淬火时未经中间退火(或退火不充分)等因素均易形成萘状断口,导致淬火裂纹。
预防措施为:
①合理选择精锻温度,严格控制终锻温度(≤1000℃),锻后缓冷;②锻坯淬火前应充分退火;③避免在5%~10%临界变形;④进行超晶粒细化处理等。
采取以上措施可有效抑制高速钢萘状断口的形成,避免产生淬火裂纹。
4机械设计与冷加工不当引起应力集中 刀具厚薄不均、因棱角、锐边、尖角、沟槽、孔、凸台等形状突变而产生缺口效应以及冷加工表面粗糙、刀纹较深、存在碰伤及打标记等均可导致高速钢刀具淬火时应力集中,从而诱发淬火裂纹。
如刀具淬火前存在较大冷加工内应力(尤其是磨削内应力)未予消除,在淬火加热和冷却时将形成多种应力叠加,当叠加应力超过材料强度极限时,将产生淬火裂纹和畸变。
预防措施为:
①改进刀具设计,使刀具形状合理、厚薄均匀。
厚处可开工艺孔,薄处可增加肋条,变形悬殊处可制成斜坡;②将刀具的棱角、直角、尖角倒圆,孔口处倒角;③冷加工表面光洁度应达到设计要求,防止产生粗大刀纹,用万能笔书写标记;④淬火前通过退火消除冷加工内应力;⑤采用热浴分级淬火、等温淬火等工艺减少组织应力和热应力,避免应力集中。
5淬火内应力与淬火冷却介质 高速钢的组织应力、热应力和附加应力均为淬火内应力。
对高速钢进行高温奥氏体化淬火时,过冷奥氏体转变为淬火马氏体,由于前者比容小,后者比容大,钢从收缩状态逆转为膨胀状态,金属内外层相变引起的比容变化不同时性产生的内应力为组织应力。
大型刀具的表面和中心以及厚薄不同处因加热和冷却速度不一致形成温度差,导致体积膨胀与收缩不同而产生的内应力为热应力。
刀具表面和内部组织结构不均匀以及工具内部弹性变形不一致形成的内应力为附加应力。
当以上三种应力之和大于材料的破断抗力时,则形成淬火裂纹。
当淬火冷却介质冷速过大,超过该钢种的临界淬火冷速时,则易形成较大的淬火内应力,导致刀具淬裂。
当淬火冷却介质冷速过小,小于该钢种临界淬火冷速时,则得不到所需组织性能。
获得淬火马氏体转变的最小冷却速度为临界淬火冷却速度。
高速钢淬透性极佳,中小型刀具空冷即可淬硬。
但用硝盐进行等温淬火时,如硝盐含水过量,可能造成淬火冷却速度过大,或当刀具淬火未冷至室温即转入水中清洗,可使大量过冷残余奥氏体在水中高冷速下转变为淬火马氏体,从而产生大的淬火内应力,导致刀具淬裂。
预防措施为:
①选用在钢的C曲线拐点处(鼻部)快冷、在鼻部Ms点以下缓冷的淬火介质(如氯化钙饱和水溶液、C?
-1有机淬火剂、聚乙烯醇水溶液、高锰酸钾淬火液等)作为理想淬火冷却介质;②采用热浴(硝盐浴、碱浴等)分级淬火、等温淬火以及淬火前预处理等措施,细化组织,消除冷、热加工应力,可有效预防和避免淬裂和刀具淬火畸变。
6氢脆 高速钢刀具酸洗、电镀时侵入钢中的初生态氢(H)原子转变为氢分子(H2)时将发生膨胀,产生巨大压力,导致在钢的晶界上发生龟裂,称为氢脆。
酸洗是金属氧化物与酸的化学反应,它使金属氧化物变为可溶性盐而脱离金属表层。
淬火高速钢有强烈的酸洗氢脆龟裂倾向。
通常用硫酸或盐酸酸洗刀具时,其化学反应方程式为 FeO+H2SO4<====>FeSO4+H2O FeO+HCl<====>FeCl+H2O Fe+H2SO4—→FeSO4+H2↑ Fe+HCl—→FeCl+H2↑ 预防措施为:
①酸洗时,如产生过量初生态氢原子(H),则需严格控制酸液浓度、温度和酸洗时间;②刀具酸洗和电镀后及时用净水冲洗和中和残酸,并在4小时内进行190~200℃×2~4h的低温时效,使氢气释放,可有效消除氢脆龟裂。
7冷处理裂纹 高速钢刀具经高温奥氏体化,保温后在大于或等于该钢种的临界冷却速度下淬火得到淬火马氏体组织,但尚有部分过冷奥氏体未转变,成为残余奥氏体(AR)(约占25%~35%)。
若再进行-60℃~-160℃的液氮冷处理,则可使残余奥氏体转变为马氏体(M)。
由于残余奥氏体比容小,马氏体比容大,钢件发生膨胀,将产生较大的二次淬火相变组织应力,并与一次淬火应力叠加,当叠加应力大于该钢种的破断抗力,则会产生冷处理二次淬裂。
预防措施为:
①冷处理前将淬火刀具用100℃沸水煮30~40分钟,或低温回火1小时。
试验表明,此方法可消除20%~30%的淬火内应力。
由于残余奥氏体稍趋稳定,经冷处理后仍可保留2%~5%。
残余奥氏体既脆又韧,可吸收马氏体的急剧膨胀能量,松驰及缓和相变应力;②冷处理后将刀具放入室温水(或热水)中升温,可消除50%~60%的冷处理二次淬火应力;③采用多次高温回火等措施,促使残余奥氏体转变为马氏体,可有效预防冷处理裂纹。
8磨削裂纹 高速钢磨削裂纹常发生在磨削加工过程中,裂纹细而浅(深度不到1mm),呈辐射网状分布于表面,大多与磨削方向垂直,类似淬火网状裂纹,但形成原因不同。
当磨削速度较高、进给量较大、冷却不良时,可使钢件表层金属温度急剧升高至淬火加热温度,随后冷却即形成金属表层二次淬火,产生二次淬火应力;当材料存在严重的碳化物偏析未予消除,或淬火刀具中存在较多残余奥氏体未被转变,在磨削加工时则易发生应力诱发相变,促使残余奥氏体转变为马氏体,使组织应力增大,并与磨削加工二次淬火应力相叠加,形成二次淬火表层磨削裂纹。
预防措施为:
①降低磨削速度和进给量,选用缓和磨削冷却液;②严格原材料入库和投产前检查,控制材料共晶碳化物级别(≤3级),超过3级者应进行改锻;③避免过高奥氏体化淬火加热温度,采用计算机控温,采用热浴分级淬火、等温淬火、多次高温回火等措施降低组织应力、热应力和残余奥氏体数量等,可有效避免磨削裂纹。
9电火花线切割加工显微裂纹 火花放电加工时,被熔化的金属有一部分残留在放电点的电蚀坑周围。
由于电火花加工在油或水中进行,因此脉冲放电结束后熔化金属迅速冷却凝固,因收缩而产生较大拉应力,使原应力场重新分布,形成厚度0.02~0.10mm的熔化变质层。
该变质层为树枝状结晶铸态组织,冷却后形成二次高温淬火硬化层,生成大量极稳定的残余奥氏体。
变质层收缩产生的拉应力与变质层二次高温淬火应力相叠加,在变质层上形成显微裂纹,且随着电火花加工电气参数的加大而加深扩大。
预防措施为:
①在电火花线切割加工前应充分消除刀具内应力;②严格控制线切割电气参数;③留足磨削及抛光的加工余量,通过后续加工去除变质层;④通过150~200℃×2~4h油浴消除应力回火,防止电火花加工时产生显微裂纹。
10回火不当引起二次淬火裂纹 高速钢刀具具有高温回火二次硬化特性。
第一次马氏体淬火后保留了较多残余奥氏体,高温回火时,在回火冷却过程中残余奥氏体相变为马氏体,若在水中或油中快速冷却,形成二次淬火马氏体时将产生较大淬火内应力;如回火时采用火焰或高频快速加热,表层金属将发生收缩,而内部依然为马氏体组织,因比容大而处于膨胀状态,从而使表层产生较大拉应力,与一次、二次淬火应力叠加,导致因回火不当引起二次硬化淬火裂纹。
刀具表面脱碳会加速裂纹的形成。
预防措施为:
①在保护气氛炉、真空电炉和经充分脱氧的盐浴炉中加热刀具,可防止氧化脱碳;②淬火刀具冷却至该钢种Ms点附近时取出转入缓和冷却介质中,宜在硝盐热浴、碱热浴中分级淬火、等温淬火和在理想冷却介质中淬火;③低温(≤100℃)入炉回火,缓慢升温至≥300℃后可随炉升温至所需回火温度,高温回火保温后出炉空冷至室温,在回火缓冷过程中实现残余奥氏体(AR)→马氏体(M)相变,避免水冷、油冷,防止产生较大二次淬火应力。
总之,淬火后及时回火,防止淬火应力萌生与扩大;充分回火,获得稳定组织;多次高温回火,促使残余奥氏体(AR)→马氏体(M)充分转变,并消除二次淬火应力;较长时间和合回火,提高抗断裂韧性和综合力学性能等措施均能有效防止回火不当引起的二次淬火裂纹。
11刀具腐蚀 目前,我国高速钢刀具热处理工艺的淬火加热一般在盐浴炉中进行,回火加热一般在硝盐浴炉中进行。
此外必须进行酸洗。
刀具淬火局部加热时,靠近盐浴面以上部位与高温盐浴挥发氯气等有害气体接触,不仅易发生氧化脱碳,而且还会导致液面与空气交界处形成一定宽度的带状麻点腐蚀。
预防措施为:
采用高温加热包盐法,即刀具整体入盐后,再将局部不淬火加热部位露出液面,使之包上一层粘附盐壳,与空气中的有害气体隔绝,避免腐蚀。
大型整体刀片在高温盐浴炉中淬火加热时,因温度高、保温时间长,易与盐浴中氧化铁(FeO)等有害物质起化学反应而发生腐蚀。
预防措施为:
严格执行盐浴加热介质热处理技术条件:
纯度≥98%,硫酸盐(BaSO4、Na2SO4、K2SO4)等杂质含量≤0.3%,碳酸盐(BaCO3、Na2CO3、K2CO3)等杂质含量≤0.1%,水不溶解物≤0.1%;每一工作班必须对盐浴进行脱氧捞渣,每周掏炉一次,彻底清除炉膛内炉渣杂质。
刀具酸洗时,因酸洗过度或未冲净残酸,使硝酸与硝盐发生化学反应,将引起电化学腐蚀。
预防措施为:
刀具酸洗后,两次用流动净水冲洗,再彻底中和,并及时喷砂强化,在空气中停放不超过8小时,并采取油封方式,可有效防止酸洗腐蚀。
对于高速钢而言,退火的目的是消除锻造后的应力,降低淬火的预热,这是考虑到高速钢的导热性差,塑性低,而淬火温度高,直接放入高温炉内势必会出现大的内应力,容易引起刀具的变形和开裂。
另外也会间接的延长了在高温下的停留时间·增加了氧化和脱碳的倾向。
一般而言预热有一次预热和二次预热两种,形状简单、截面较小的刀具则在800~850℃进行一次预热,保温时间按20~30s/mm计算;反之需作二次预热即在500~550℃和800~850℃分别预热·在盐浴炉中的保温时间为40s/mm、20~30s/mm。
②淬火加热淬火加热温度应根据钢的化学成分、刀具的工作条件、形状、尺寸等具体而定,其基本原则为使足够多的碳和合金元素溶于奥氏体中,晶粒度控制在要求的范围内,防止出现过热和过烧,经加热后的高速钢淬火和回火后则可获得高硬度和热硬性等。
.淬火温度的高低同时依据刀具的具体用途确定,对要求高硬度和高热硬性的车刀则采用较高的加热温度;而对于有较高韧性的中心钻和滚丝轮则使用较低的温度,如要求硬度和韧性同时兼顾,则采用中限温度加热。
③淬火加热时间它的作用是既能使合金碳化物充分溶解,又不使晶粒显著长大,根据经验盐浴炉中的J』IJ热按(6-15s/mm计算,当然根据刀具的类型、装炉量和所用的r装火县等,在加热时间上也应灵活掌握,文献[27.31。
37_=J介绍:
考虑到碳化物的溶解需要一段时间,则最少的加热时间不少于90S。
④淬火冷却尽管高速钢可以进行空冷,但为了防止碳化物的析出而影响热硬性和防止空冷时刀具表面的氧化等,生产中一般不进行空冷,而是采用图3—21中的淬火冷却方法。
油冷是指刀具在油中冷却到300~400℃出油空冷,适用于形状简单的刀具;考虑到350~625℃范围内出现过冷奥氏体极稳定的区域,根据刀具变形开裂的倾向大小,刀具可选择一次或二次分级淬火.一次分级是在580~620℃进行,保温后空冷,二次分级是在580~620~C和260~280℃冷却后空冷;等温淬火是适用于截面很大、形状复杂的细长刀具,是在分级冷却后投入240~280℃的硝盐中等温2~4h。
⑤高速钢的回火根据高速钢具有“二次硬化”的特点.因此淬火后要进行550~570~C三次高温回火,每次保温在1~1.5h,回火后的硬度在62~66(HRC)。
回火是在i00%的硝酸钾中进行,应当注意不要使加热温度高于600~C,否则其热分解后产生氧气造成盐浴的爆炸。
为便于系统学习和掌握高速钢的热处理工艺.
钢的淬火是将钢加热到临界温度Ac3(亚共析钢)或Ac1(过共析钢)以上某一温度,保温一段时间,使之全部或部分奥氏体[1]化,然后以大于临界冷却速度的冷速快冷到Ms以下(或Ms附近等温)进行马氏体(或贝氏体)转变的热处理工艺。
通常也将铝合金、铜合金、钛合金、钢化玻璃等材料的固溶处理或带有快速冷却过程的热处理工艺称为淬火。
淬火的目的是使过冷奥氏体进行马氏体或贝氏体转变,得到马氏体或贝氏体组织,然后配合以不同温度的回火,以大幅提高钢的强度、硬度、耐磨性、疲劳强度以及韧性等,从而满足各种机械零件和工具的不同使用要求。
也可以通过淬火满足某些特种钢材的的铁磁性、耐蚀性等特殊的物理、化学性能。
淬火能使钢强化的根本原因是相变,即奥氏体组织通过相变而成为马氏体组织(或贝氏体组织)。
淬火
将金属工件加热到某一适当温度并保持一段时间,随即浸入淬冷介质中快速冷却的金属热处理工艺。
常用的淬冷介质有盐水、水、矿物油、空气等。
淬火可以提高金属工件的硬度及耐磨性,因而广泛用于各种工、模、量具及要求表面耐磨的零件(如齿轮、轧辊、渗碳零件等)。
通过淬火与不同温度的回火配合,可以大幅度提高金属的强度、韧性及疲劳强度,并可获得这些性能之间的配合(综合机械性能)以满足不同的使用要求。
另外淬火还可使一些特殊性能的钢获得一定的物理化学性能,如淬火使永磁钢增强其铁磁性、不锈钢提高其耐蚀性等。
淬火工艺主要用于钢件。
常用的钢在加热到临界温度以上时,原有在室温下的组织将全部或大部转变为奥氏体。
随后将钢浸入水或油中快速冷却,奥氏体即转变为马氏体。
与钢中其他组织相比,马氏体硬度最高。
钢淬火的目的就是为了使它的组织全部或大部转变为马氏体,获得高硬度,然后在适当温度下回火,使工件具有预期的性能。
淬火时的快速冷却会使工件内部产生内应力,当其大到一定程度时工件便会发生扭曲变形甚至开裂。
为此必须选择合适的冷却方法。
根据冷却方法,淬火工艺分为单液淬火、双介质淬火、马氏体分级淬火和贝氏体等温淬火4类。
淬火效果的重要因素,淬火工件硬度要求和检测方法:
淬火工件的硬度影响了淬火的效果。
淬火工件一般采用洛氏硬度计,测试HRC硬度。
淬火的薄硬钢板和表面淬火工件可测试HRA的硬度。
厚度小于0.8mm的淬火钢板、浅层表面淬火工件和直径小于5mm的淬火钢棒,可改用表面洛氏硬度计,测试HRN硬度。
在焊接中碳钢和某些合金钢时,热影响区中可能发生淬火现象而变硬,易形成冷裂纹,这是在焊接过程中要设法防止的。
由于淬火后金属硬而脆,产生的表面残余应力会造成冷裂纹,回火可作为在不影响硬度的基础上,消除冷裂纹的手段之一。
淬火对厚度、直径较小的零件使用比较合适,对于过大的零件,淬火深度不够,渗碳也存在同样问题,此时应考虑在钢材中加入铬等合金来增加强度。
淬火是钢铁材料强化的基本手段之一。
钢中马氏体是铁基固溶体组织中最硬的相(表1),故钢件淬火可以获得高硬度、高强度。
但是,马氏体的脆性很大,加之淬火后钢件内部有较大的淬火内应力,因而不宜直接应用,必须进行回火。
表1钢中铁基固溶体的显微硬度值
淬火工艺在现代机械制造工业得到广泛的应用。
机械中重要零件,尤其在汽车、飞机、火箭中应用的钢件几乎都经过淬火处理。
为满足各种零件干差万别的技术要求,发展了各种淬火工艺。
如,按接受处理的部位,有整体、局部淬火和表面淬火;按加热时相变是否完全,有完全淬火和不完全淬火(对于亚共析钢,该法又称亚临界淬火);按冷却时相变的内容,有分级淬火,等温淬火和欠速淬火等。
工艺过程包括加热、保温、冷却3个阶段。
下面以钢的淬火为例,介绍上述三个阶段工艺参数选择的原则。
加热温度以钢的相变临界点为依据,加热时要形成细小、均匀奥氏体晶粒,淬火后获得细小马氏体组织。
碳素钢的淬火加热温度范围如图1所示。
由本图示出的淬火温度选择原则也适用于大多数合金钢,尤其低合金钢。
亚共析钢加热温度为Ac3温度以上30~50℃。
从图上看,高温下钢的状态处在单相奥氏体(A)区内,故称为完全淬火。
如亚共析钢加热温度高于Ac1、低于Ac3温度,则高温下部分先共析铁素体未完全转变成奥氏体,即为不完全(或亚临界)淬火。
过共析钢淬火温度为Ac1温度以上30~50℃,这温度范围处于奥氏体与渗碳体(A+C)双相区。
因而过共析钢的正常的淬火仍属不完全淬火,淬火后得到马氏体基体上分布渗碳体的组织。
这-组织状态具有高硬度和高耐磨性。
对于过共析钢,若加热温度过高,先共析渗碳体溶解过多,甚至完全溶解,则奥氏体晶粒将发生长大,奥氏体碳含量也增加。
淬火后,粗大马氏体组织使钢件淬火态微区内应力增加,微裂纹增多,零件的变形和开裂倾向增加;由于奥氏体碳浓度高,马氏体点下降,残留奥氏体量增加,使工件的硬度和耐磨性降低。
常用钢种淬火的温度参见表2。
表2常用钢种淬火的加热温度
实际生产中,加热温度的选择要根据具体情况加以调整。
如亚共析钢中碳含量为下限,当装炉量较多,欲增加零件淬硬层深度等时可选用温度上限;若工件形状复杂,变形要求严格等要采用温度下限。
保温时间由设备加热方式、零件尺寸、钢的成分、装炉量和设备功率等多种因素确定。
对整体淬火而言,保温的目的是使工件内部温度均匀趋于一致。
对各类淬火,其保温时间最终取决于在要求淬火的区域获得良好的淬火加热组织。
加热与保温是影响淬火质量的重要环节,奥氏体化获得的组织状态直接影响淬火后的性能。
-般钢件奥氏体晶粒控制在5~8级。
冷却方法要使钢中高温相——奥氏体在冷却过程中转变成低温亚稳相——马氏体,冷却速度必须大于钢的临界冷却速度。
工件在冷却过程中,
表面与心部的冷却速度有-定差异,如果这种差异足够大,则可能造成大于临界冷却速度部分转变成马氏体,而小于临界冷却速度的心部不能转变成马氏体的情况。
为保证整个截面上都转变为马氏体需要选用冷却能力足够强的淬火介质,以保证工件心部有足够高的冷却速度。
但是冷却速度大,工件内部由于热胀冷缩不均匀造成内应力,可能使工件变形或开裂。
因而要考虑上述两种矛盾因素,合理选择淬火介质和冷却方式。
冷却阶段不仅零件获得合理的组织,达到所需要的性能,而且要保持零件的尺寸和形状精度,是淬火工艺过程的关键环节。
分类可按冷却方式分为单液淬火、双液淬火、分级淬火和等温淬火等。
冷却方式的选择要根据钢种、零件形状和技术要求诸因素。
单液淬火将工件加热后使用单一介质冷却,最常使用的有水和油两种,其变、温曲线如图2中的曲线1。
为防止工件过大的变形和开裂,工件不宜在介质中冷至室温,可在200~300℃出水或油,在空气中冷却。
单液淬火操作简单易行,广泛用于形状简单的工件。
有时将工件加热后,先在空气中停留-段时间,再淬入淬火介质中,以减少淬冷过程中工件内部的温差,降低工件变形与开裂的倾向,称为预冷淬火。
图2各种淬火冷却的变温曲线示意图曲线1-单液淬火;曲线2-双液淬火;曲线3-分级淬火;曲线4-等温淬火
双液淬火工件加热后,先淬入水或其他冷却能力强的介质中冷却至400℃左右,迅速转入油或其他冷却能力较弱的介质中冷却。
变温曲线如图2中曲线2。
所谓“水淬油冷”法使用得相当普遍。
先淬入冷却能力强的介质,工件快速冷却可避免钢中奥氏体分解。
低温段转入冷却能力较弱的介质可有效减少工件的内应力,降低工件变形和开裂倾向。
本工艺的关键是如何控制在水中停留的时间。
根据经验,按工件厚度计算在水中停留的时间,系数为O.2~O.3s/mm,碳素钢取上限,合金钢取下限。
这种工艺适用于碳素钢制造的中型零件(直径10~40mm)和低合金钢制造的较大型零件。
分级淬火工件加热后,淬入温度处于马氏体点(ms)附近的介质(可用熔融硝盐、碱或热油)中,停留一段时间,然后取出空冷。
变温曲线如图2中曲线3。
分级温度应选择在该钢种过冷奥氏体的稳定区域,以保证分级停留过程中不发生相变。
对于具有中间稳定区(“两个鼻子”)型TTT曲线的某些高合金钢,分级温度也可选在中温(400~600℃)区。
分级的目的是使工件内部温度趋于一致,减少在后续冷却过程中的内应力及变形和开裂倾向。
此工艺适用于形状复杂,变形要求严格的合金钢件。
高速钢制造的工具淬火多用此工艺。
等温淬火工件加热后,淬入温度处于该钢种下贝氏体(B下)转变范围的介质中,保温使之完成下贝氏体转变,然后取出空冷,变温曲线如图2中的曲线4。
等温温度对下贝氏体性能影响较大,温度控制要求严格。
常用钢种的等温温度和时间列于表3。
等温淬火工艺特别适用于要求变形小、形状复杂,尤其同时还要求较高强韧性的零件。
回火是工件淬硬后加热到AC1以下的某一温度,保温一定时间,然后冷却到室温的热处理工艺。
回火一般紧接着淬火进行,其目的是:
(a)消除工件淬火时产生的残留应力,防止变形和开裂;
(b)调整工件的硬度、强度、塑性和韧性,达到使用性能要求;
(c)稳定组织与尺寸,保证精度;
(d)改善和提高加工性能。
因此,回火