锻造加工技术.docx
《锻造加工技术.docx》由会员分享,可在线阅读,更多相关《锻造加工技术.docx(39页珍藏版)》请在冰豆网上搜索。
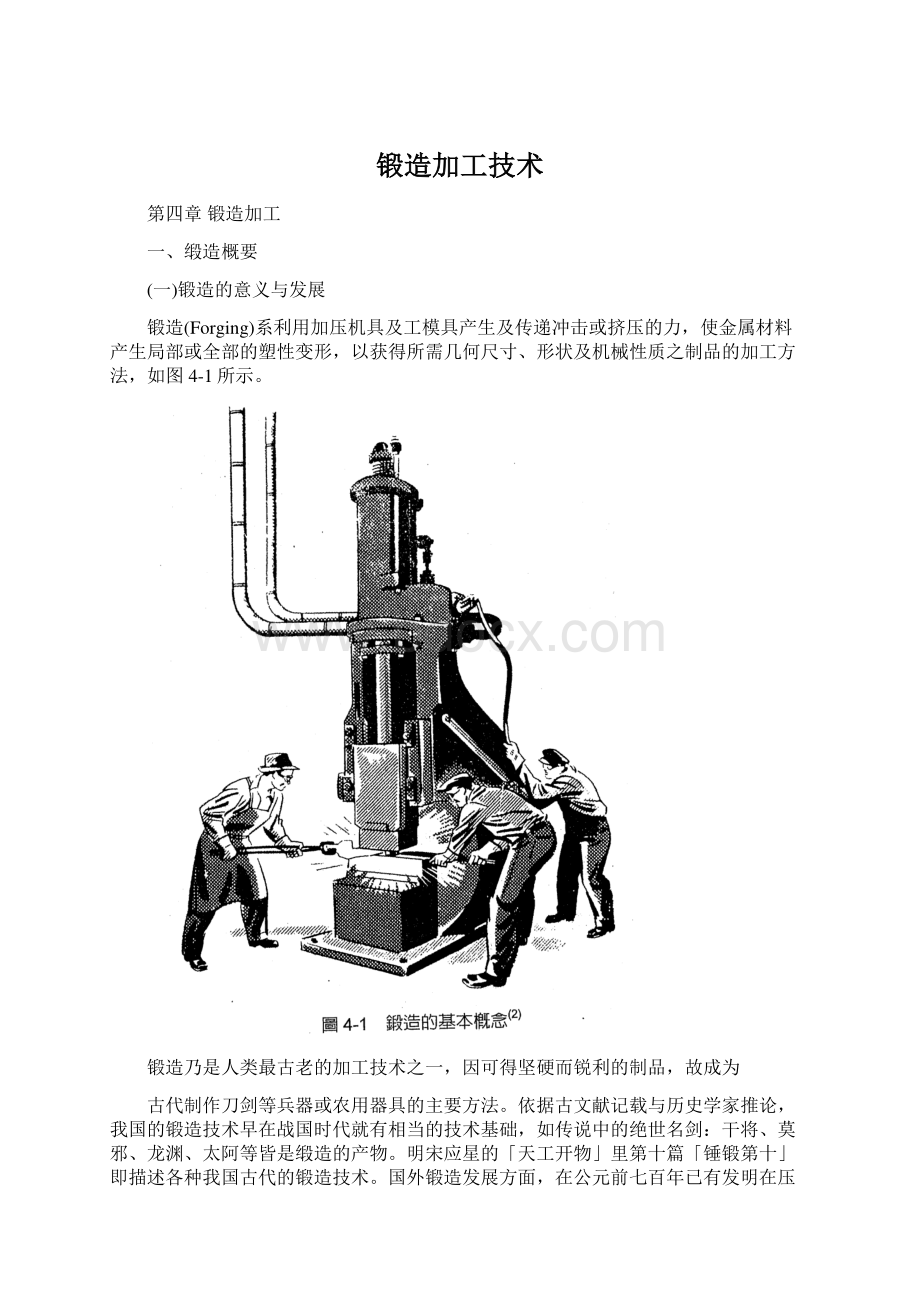
锻造加工技术锻造加工技术第四章锻造加工一、缎造概要
(一)锻造的意义与发展锻造(Forging)系利用加压机具及工模具产生及传递冲击或挤压的力,使金属材料产生局部或全部的塑性变形,以获得所需几何尺寸、形状及机械性质之制品的加工方法,如图4-1所示。
锻造乃是人类最古老的加工技术之一,因可得坚硬而锐利的制品,故成为古代制作刀剑等兵器或农用器具的主要方法。
依据古文献记载与历史学家推论,我国的锻造技术早在战国时代就有相当的技术基础,如传说中的绝世名剑:
干将、莫邪、龙渊、太阿等皆是缎造的产物。
明宋应星的天工开物里第十篇锤锻第十即描述各种我国古代的锻造技术。
国外锻造发展方面,在公元前七百年已有发明在压砧的上模锻货币的记载,另外亦有记录利用水车及一些曲柄连杆机构做为锻造工具,但一直到十五世纪才有利用冲压机具来制造货币的记录,而有关使用落锤锻造机的记载则于十七世纪方有记述。
(参阅图4-2及图4-3)经由锻造加工而得之锻件,由于在锻压过程中强迫材料塑性变形,因而可改善晶粒组织,使材质细密化、均质化,并获得优良的抗疲劳性、韧性及耐冲击性等机械性质,故极适合制造各种高强度之金属制品或零组件。
因此锻造已是现今产业发展相当重要的加工技术,尤其若需求物理性能高、韧性好、强度高的零件就非锻制品不可。
其与汽车工业、重工业、手工具业有密切的关系,从一般典型的民间用品,如船舶用柴油引擎之曲轴、汽车曲柄、轮圈、齿轮、活塞头、连结器、螺栓、手工具,至技术层次较高的产品,如轧钢机转轴、铁道车辆组件、涡轮机圆盘、飞机引擎、电动机转轴、战机及飞弹构件等,皆是锻造加工的产物。
因此锻造加工的应用范围乃涉及机械工业、化学工业、汽车工业、矿业、土木工业等,如表4-1所示。
(二)锻造的特点与目的锻造在古代即扮演重要加工角色,至今亦能成为现代产业发展相当重要的加工技术,主要是具有下列特点1.对于相同零件而言,施以锻造则较其它机械加工法,可获得细密的晶粒组织,并且可减少零件内部气孔、罅裂等缺陷。
2.可获致连续的晶粒流动而形成机械性的纤维化状态,材料因而能得到最大方向性的强度、耐冲击及抗疲劳等优良机械性质。
3.对于形状复杂的零件而言,锻造加工较机械加工更具经济性,且适合大量生产,可降低生产成本。
4.借着金属流动的方式,锻造加工比其它切削加工可节省较多材料,减少材,料损耗,降低生产成本。
但下列各点亦是相关研究人员不断试图改善与解决的方向1.在热间锻造时,胚料表面容易氧化而迅速产生一层锈皮,当锻打时,锈皮会不断脱落,也因而影响锻件的精度。
2.锻造模具造价较高,换模作业也耗时,故不适于进行少量生产。
3.锻造制程变量很多,技术经验需长期累积,因此掌握不易,也因而影响制程及结果的控制与成效。
具体言之,锻造有二种目的1.锻炼:
破坏粗大铸造组织,使之细粒化,并使胚料内的空隙压着,并随着流动变形而形成机械性纤维化的组织团锻流线(Forgingflowline)(如4-4),以提高韧性、强度等机械性质。
2.成形:
将胚料锻成具有连绩锻流线的各种制品形状,如图4-5所示。
(三)锻造的分类锻造的分类如图4-6所示,兹简述如后:
1.依工作温度之不同而分(参阅表4-2)
(1)热间锻造(Hotforging):
将金属材料加热至再结晶温度而锻造者,简称热锻。
热间锻造因在高温作业,金属流动性良好,可塑性佳,变形所需的压力、能量较小,且复杂形状与大型锻件易于成形。
但是锻件易生氧化皮,表面欠光平,尺寸难达精确,加热费用高,且因锻模表面温度上升,硬度降低使锻模寿命灭短,同时作业环境差,管理不易。
(2)冷间锻造(Coldforging):
若材料不加热而在室温进行者谓之冷间锻造,简称冷锻。
冷锻因系在常温下进行塑性变形,故引起加工硬化,且相同制品所须锻造能量较热锻为大,同时为避免锻模变形保持其刚性,故要使用高价值的模具材料,一般仅适合小型工件的生产。
但冷锻亦有其优点,如经锻造的表面平滑无氧化皮,尺寸精度高,由于加工硬化可以提高锻件的机械性质,并利用其特性,使用低廉材料锻造后可以直接使用,锻造后不须再切削加工或仅小量切削加工,能节约材料及后续加工之浪费。
(3)温间锻造(Warmforging):
加热温度在再结晶温度以下室温以上而锻造者谓之,简称温锻。
此法系取冷、热锻的中间温度进行锻造作业,所以材料仍在加热状态,变形所需负荷不高,尺寸亦可控制较热锻准确,且表面情况亦较佳,可说是得冷、热锻两者之利而去其弊的锻造法,发展潜力相当高。
2.依受力形态之不同而分
(1)冲击锻造(Impactforging):
简称冲锻,其锻造的负荷是成瞬间冲击的形态施给,材料塑性变形亦是在极短时间内完成。
由于材料在模穴内受力进行的流动时间较短,因此较适合锻件体积小且形状较不复杂的加工。
(2)压挤锻造(Pressforging):
简称压锻,此法之锻造压力是以渐进的方式增加,以促使金属材料产生降伏而变形,因此其施力运作时间也较长。
因为材料在模穴内受力流动时间较长,胚料有较充裕的时间进行流动充模,因此可用于体积较大或形状较复杂锻件的加工。
3.依模具型式之不同而分(参阅图4-7)
(1)开模锻造(Open-dieforging):
又称自由锻造(Freeforging),乃是将金属胚料放置在平面或简易形状面的上下锻模之间,施行加压锻打的加工。
此种锻造法可利用普通的工具,对金属材料施予局部压力逐渐变彤,复制性差,在金属流动及尺寸等方面之控制较难,完全依操作人员之技术,但它具有低廉的模具和安装费用,适合于少量生产及闭模锻造用之预锻成形。
(2)闭模锻造(Closed-dieforging):
乃是将金属胚料放置在具有三度空间模穴内,使上下模密合而成形的锻造法。
因闭模锻造之胚料被限制在模穴中流动,故能有精确的尺寸控制,亦可以顾虑晶粒流动,而获最大强度方向,且具有高度的复制牲。
但设备较昂贵,模具成本高,非大量生产无法达到其经济牲。
4-94.依施力来源之不同而分
(1)手工锻造(Handforging):
此法系直接用人的双手握持各种锻打工具对胚料进行加压锻打。
在古代大都用此法制造各种器具,但现今之锻件几乎全部用机器锻造,手锻仅限于修理工作及小量零件使用。
(2)机器锻造(Machineforging):
此法系利用各种不同型式的锻造机器产生强大的外力,对金属胚料进行锻炼或成形的加工。
由于压力强大,速度快,适合大量生产及大型胚料的锻制,是现今锻造方法的主流。
(四)锻造的流程锻造制程依锻件性质需求不同及生产条件的差异,过程简繁各异,通常一个锻件从锻胚的准备到成形、检验,约需经过八个步骤,即备料、加热、预锻、模锻、整形、修整、热处理、检验。
1.备料系包括胚料之检视、截锯成适当大小及长度、修整清洁表面等。
2.加热则是利用瓦斯、燃油、电阻热与感应式之加热炉,将胚料加热至所需的锻造温度。
3.预锻系针对较复杂之锻件无法一次锻打完成者,先利用锻粗、延伸等体积分配、弯曲及粗锻等方式预先锻成过渡形状,以减低锻造压力、材料流动阻力及溢料损失等。
4.模锻系利用所需各模穴进行最后的锻打成形。
5.整形则是以剪边机、整形机或相关锻造机来进行模锻后的整形校直,通常大锻件或薄截面且复杂锻件才需要,如以近净形锻造之锻件,则无需再进行剪边处理。
6.修整系利用钳工工具、手提研磨机或喷砂、酸洗等方式来清除锻件表面的毛头、缺陷或氧化麟皮等。
7.热处理则是依据不同材质做适当之加热与冷却处理,以达所要求之机械性质。
8.检验系包括各项尺寸外观之检测、机械性质试验及检视锻件缺陷之各种非破坏检验。
图4-8为典型锻造工厂的作业流程。
因此,整个锻造工程可概括为六大领域:
锻品设计、锻模设计与制作、胚料准备、前处理及磨润,锻造成形、锻件后处理及检验,如图4-9所示。
二、锻造基础
(一)锻造负荷锻造在进行前为便于进行锻造机的选择及锻模受力状况的估计,须先估算锻造所需负荷及能量,较正确的方法可采用各种锻造力学解析法来推导,但有时为方便起见,常依经验来做概略的估算。
一般而言,锻件愈复杂,投影面积愈大,腹板及肋愈薄或愈高,则所需之负荷愈高。
如图4-10所示为典型的模锻负荷与冲程图,负荷随着胚料之充模而逐渐增加,当废边形成时,负荷急速增高,至闭模时负荷达于顶点。
负荷-冲程曲线下所包含的面积即为锻造所需的能量。
依据一般学理的经验公式,锻造负荷F=kA,其中k是压力乘积因子(锻件属形状简单而无废边时为35,形状简单而有废边时为58,形状复杂而有废边时为812),为材料的塑流应力,A为包含废边之锻件投影面积。
(二)可锻性可锻性(Forgeability)乃是锻造时材料能产生塑性变形且不破裂损毁的承受能力。
影响可锻性的因素除了温度之外有二类:
冶金因素与机械因素。
1.冶金因素
(1)结晶构造:
FCC大于BCC,BCC大于HCP。
(2)成份:
纯金属较合金佳。
(3)纯度:
金属中含有不溶解化合物时可锻性大为增进。
(4)相位数:
双相合金较单相合金低。
(5)晶粒大小:
晶粒越小可锻性越佳。
2.机械因素
(1)应变率:
通常金属在冷锻温度显示低延性者在应变率增大时,可锻性降低,如为高延牲者,则在应变率增大时,其可锻性不致受影响至可察觉的程度。
(2)应力分布:
应力分布较均匀,能得到较均匀的金属流动,可锻性较佳。
图4-11为各种材料之可锻性比较。
(三)锻造温度锻造温度为锻造制程的重要变量,如果加热温度太低将减少可能锻打时间,反复重新加热亦降低锻造效率,材料加热耗损大,而且温度过低,只形成锻件表面的锻击,致使材料表面产生过大的应力,生成外观不易察觉的裂痕,又如果温度太高,不但有过度的氧化,使材料表面产生所谓之焚烧现象,同时过高的加热温度会使结晶粗大,如此材料加热至此温度已不值得做为锻造材料,尚且易使加热炉损伤。
表4-3为各种材料的锻造温度,碳钢为锻造最常用的材料,其锻造温度范围依其含碳量之多寡而异,因其固相线温度随含碳量的增加而降低,所以锻造温度范围之上限,亦随含碳量之增加而降低,但其温度下限则保持不变,皆在再结晶温度之上。
至于温度上限,一般约在固相线以下500600F之间,如图4-12所示。
(四)锻造润滑锻造使材料塑性变形,将导致胚料表面积与微视结构的变化、新生面的露出,因此润滑处理有其重要性。
锻造润滑主要的目的有:
降低摩擦以减小锻模之磨损与过热,避免锻模与材料间的黏着使锻件易于脱模,控制及增进金属流动的均匀性及充模能力,减低锻造所需的负荷,避免锻件激泠缺陷的产生。
选用锻造润滑剂需考虑润滑剂的特性:
绝缘性、低阻性、冷却性、绝热性、润湿性、稳定性、分离性、安定性、纯净性、安全性、经济性等。
表4-4为锻造润滑剂示例。
通常热间锻造是将石墨等润滑剂喷涂在锻模模穴上,而冷间锻造则可对锻胚施以皮膜化成处理(Conversioncoating)。
三、锻造机具设备
(一)概说锻造在生产过程中所需的机器设备,大致有锻打设备(包含手工锻造工具、锻造机)、材料切断设备、加热设备、表面清洁设备、模具制作设备、试验检查设备、搬运设备及其它辅助设备等。
常见的手工锻造工具如图4-13所示,铁砧是于工锻造时工件放置其上来进行锻击的工具,火钳系用来夹持工件以便进行加热及锻打,铁锤用于直接或间接锻打经加热的工件,凿子则用于刻痕或切断工件,冲头做为工件冲孔之用,型砧及型锤用来锻制各形凹凸件,花砧系用以配合锻制特定形状。
锻造机依力、能特点之不同可区分为:
限能量(Energyrestricted)、限行程(Strokerestricted)及限负荷(Loadrestricted)三大类。
限能量锻造机之变形能乃由一个或多个运动体之动能(Kineticenergy)转换而来,锻打时,工件变形到该运动体可用能量用完为止,主件欲继续变形则需再次打击,因此设备之规格常以每次打击之最大有效动能来表示,各种落锤锻造机、螺旋压床均是。
限行程锻造机之力与能的传递,主要靠旋转的曲柄或偏心轴,通过连杆或楔形块,将回转运动变成滑块之直线运动,同时将电动机之能量藉由装设于锻锤(滑块)上之模具传递到锻件上,达到成形之目的。
这种设备被设计制造完成后,其运行都有一定行程,故称之限行程设备,锻件之变形只能在一次行程中完成,而其规格即以行程中最大可能出力之大小而订定。
典型之设备有由柄压床(Crankpress)、肘节压床(Knucklepress)等。
限负荷锻造机在工作时,可能施加于胚料或锻件上使其变形之最大压力,于行程中之任何位置上都是一定的,典型设备有油压压床(Hydraulicpress)、轨迹锻造机(Orbitalpress)等。
普通锻造机基本上可大致分为二类:
1.落钮锻造机(Drophammerforgingmachine)简称落锤(Hammer)。
2.压力锻造机(Pressforging)简称锻造压床(Press)。
如图4-14所示。
(二)落锺锻造机落锺锻造机(Drophammerforgingmachine)系利用锻锤(Ram)及上模自某一高度落下产生冲击力作用于胚料,使材料产生塑性变形以成形的机器。
落锤锻造机约有三种,即重力落锤锻造机、动力落锤锻造机及相击落锤锻造机。
重力落锤锻造机(Gravity-drophammerforgingmachine)又称自由落下落锤锻造机,其锻击力完全藉锻锤及上模之重量,自某一高度落下产生之重力加速度,冲击至下方的下模所产生之力量,并没有施加额外的外力。
此种锻造机依其提升机构之不同而有皮带式、链条式、板式及活塞式四种,如图4-15所示,图4-16系板式重力落锤锻造机。
动力落锤锻(Power-drophammerforgingmachine)其锻击能量之产生除由锻锤及上模之重量外,同时也利用其它动力使锻锤向下施加更大的力量。
此种机器之锻击力较重力落锤锻造机大,同时其锻击力可由操作者自由控制,对于预锻之体积分配相当有益。
图4-17系空气式动力落锤锻造机的构造。
相击落锤锻造机(Counterblowhammerforgingmachine)系动力落锤锻造机的改良,其锻锤的打击是来自两个锻锤的运动,此两锻锤是同时由反方向迫近,而在中间点相遇以产生强大的锻击力。
与单动锻造机相较,此机冲击震动少,能量损失少,锻锤运动部摩擦少,运转寿命增加o此种机器其动力有些是气压式或液压式,亦有些是机械液压合并式或机械气压合并式。
如图4-18为直立式相击落锤锻造机的构造。
除此之外,开模锻造用之动力落锤锻造机虽然与闭模锻造用之动力落锤锻机类似,但基本上有二个不同点:
1.闭模锻造之动力落锤锻造机其落锤系采用脚踏来操作控制,但开模者其操作控制则采用两个板杆,并连接到一群组件以手操纵,因此操纵较灵活。
2.开模锻造机之锻锤之砧与机是分开,但冲击锤与上模则包括在机架上,由于百砧与机架分开,所以砧所承受的冲击力不会传到机架,一般是使用橡树枕木来吸收部份锤击力,如图4-19所示。
(三)压力锻造机压力锻造机(Pressforgingmachine)系以缓慢的压力,使胚料在锻模模穴内成形的机器。
应用此种机器来锻造,因胚料受力时间较长,锻击能量不仅施于胚料表面,且亦达到心部,所以表里受力一致,锻件质量较佳。
压力锻造机依其动力来源之不同,而有液压式及机械式,液压式动作较慢,但能量较大,而机械式则动作较快,但能量较小,表4-5为其性能比较。
液压式压力锻造机(Hydraulicpressforgingmachine)系利用高压液体递压力,驱动锻锤之活塞以低速运动,来进行挤压作用的锻造机器,如图4-20为液压式压力锻造机的外观。
机械式压力锻造机(Mechanicalpressforgingmachine)则是利用曲轴等机械构件来传动,将电动机的回转运动经由飞轮、|曲轴或偏心轴等转换成直线运动,带动滑块锻模以进行锻打成形的机器。
如图4-21为机械压力锻造机的外观。
机械式压力锻造机依其驱动滑块机构之不同,可分为曲轴式(Crank)、偏心式(Eccentric)、肘节式(Knuckle)、凸轮式(Cam)、连杆式、小齿轮式(Pinion)等。
兹将较常见的简述如后:
l.曲轴式压力锻造机:
如图4-22所示,系以马达带动飞轮,经由小齿轮轴、小齿轮、主齿轮,将飞轮肘存之能量传到IB轴,再经由连杆使滑块作上下运动以达到锻打的目的。
2.肘节式压力锻造机:
如图4-23所示,乃是将曲轮运动再经由肘节机构(Togglejoint)传递于锻锤上。
3.楔形压力锻造机(Wedge-typepressforgingmachine):
此种锻造机的原理与曲轴式压力锻造机的原理相仿,系由飞轮贮存之能量经由曲轴传送,而使楔子作水平方向往复运动,以带动滑块作上下运动,如图4-24所示。
4.苏格兰轴压力锻造机:
如图4-25所示,此系偏心式压力锻造机之一,在滑块中有苏格兰轭(Scotchyoke)构件,当曲轴开始回转时,苏格兰轭前进运动使滑块开始下|降,随着曲轴连续回转,使苏格兰轭作前后方向往复运动,滑块因而作上下运动。
5.摩擦式压力锻造机:
又称螺旋压力锻造机(Screwpressforgingmachine),此机器系利用旋转摩擦轮驱动飞轮,而飞轮之运动则被主轴上的多线螺杆及螺帽转换成直线运动,如图4-26所示为其外观构造。
(四)特种锻造机为配合特殊工作需要,因而特种型式的锻造机的种类也就各式各样,兹将较常见的几种简述如下。
1.高能率锻造机高能率锻造机(High-energy-rateforgingmachine)系一种高能量、高速度的锻造机,且整体重量很小,它是采用相击原理,而且是用高压惰性气体来驱动锻锤以获得高能量之打击能力。
此种锻造机通常是用来锻造对称形或同心的锻件,譬如齿轮、轮圈等,对于非对称形锻件,因锻打时有偏心荷重,故较不适用。
如图4-27为锻锤内机架式高能率锻造机。
2.锻粗锻造机锻粗锻造机(Upsettingforgingmachine)系用来使棒料端部扩大的机器,其运动机构与机械式压力锻造机类似,亦是用飞轮及曲轴来驱动滑块锻粗冲头,使胚料沿轴向运动而压缩,外径因而粗大成形,如图4-28为水平式锻粗锻造机的外观及构造。
3.滚锻机滚锻机(Rollforgingmachine)乃是利用一组反向回转辊轮将材料之横断面变小且延伸的机器,其主要作用一可以做为闭模锻造之预锻成形的体积分配,另一可就做为主成形的锻造作业。
滚锻机有直形滚锻机及环形滚锻机两类,如图4-29所示。
4.型锻机型锻机(Swagingmachine)系利用一动力驱动之环,以高速旋转,使滚子推动凸轮表面以迫压各分段之锻模,使圆杆或管件胚料端部施以高频率之击压而成形,如图4-30所示,此机依其模具运作之不同可分为旋转模型锻机(Rotarydieswagingmachine)及固定模型锻机(Stationarydieswagingmachine)二类,前者系锻模旋转撞击工作,使之迅速成形,后者系中心之锻模块固定,由四周滚轮转动撞击工件成形。
5.回转锻造机回转锻造机(Rotaryforgingmachine)又称轨迹锻造机(Orbitalforgingmachine),系使用一对模具在连续加工中使胚料逐渐变形而成形的一种渐进锻造设备。
此机器因在同一时间内只有胚料之小部分产生变形,故锻造所需力量的为传统锻造的10%因此机器和模具之变形及摩擦力减小,适合生产高精密度锻件,亦适用于多类少量之锻件,且其震动噪音也很小,如图4-31为其构造。
(五)锻造机的选用选用锻造机之前应先对锻造机的种类、特性及能力等有相当的认识与了解。
并依订单的特性斟酌厂内现有设备加以运用,使锻造工作得以顺利进行。
如图4-32为其运用程序,另图4-33为锻造机的特性要素。
兹将数种主要锻造机的选用归纳如后:
1.落锤锻造机:
用于中、小量之生产,因不易使其自动化,不适宜大量生产,主要用在开模锻造,一般依经验通常多选用工件重量为落锤型砧的15%之机器。
2.相击落锤锻造机:
因两型砧对打,锻击能量没有损失,直立式相击落锤锻造机因下型砧亦在运动,被加工件不易被夹住,故较少用于小型工件之锻造,而适合于大型工件锻造。
小型工件通常以水平式相击落锤锻造机来生产。
3.曲轴式压力锻造机:
机构上挠性较大,压力能量不高,但有下死点,故加工尺寸精度颇高,大多用于小型工件之挤压、模锻、废边整缘及固定型多模穴组合型锻。
4.肘节式压力锻造机:
行程较短,但在下死点时之压力极大,可用于需要大压力之整形及冷锻之用,适合于大量生产。
5.液压式压力锻造机:
行程甚长、速度慢,适合大型压制工件之矫正、废边剪除及铸绽锻炼,但不适合多道次之锻造工作。
6.摩擦式压力锻造机:
性能介于落锤锻造机及压力锻造机之间,适用于小型锻粗之工件,圆形小型工件之锻造及需分割模之锻造,如螺栓、管弯头等。
7.锻粗锻造机:
适于轴状零件、中空零件、较长工作件之体分配,圆长形工件需多道次加工之锻造。
8.滚锻锻造机:
铸锭之锻炼、型料、棒料、管料、板料之加工制造,以及简单形状之成形。
9.型锻锻造机:
适用于小件之杆料、管材之缩小成形,可自动化用于大量生产。
四、锻件与锻模设计
(一)锻件设计由零件图绘制成冷锻件图,其主要的设计要项有锻件形状、分模线、拔模斜度、内外图角、肋及腹板、余块、锻件公差及加工裕留量等。
简述如下:
1.锻件形状设计锻件基本上可分为两类,一为开模锻件(自由锻件),二为闭模锻件,两者之差别在于是否以三维(Threedimension)之模闭穴形状来限制锻造时金属之流动成形。
闭模锻件一般又可分为粗锻件(Blocker-typeforging)、普通锻(Conventionalforging)及精密锻件(Precisionforging)三类,如图4-34所示。
锻件形状种类繁多,因此锻件设计时其形状并没有特定之依据可遵循,但设计时应尽量使锻件能有最少之完工加工面,且使其有简单及对称的形状,避免有陡急的断面变化、过度的材料堆积、强烈的方向的转变及棱锐之边缘,在连接部分也应有充份的圆弧角,避兔有过分凹入或凸起的角、线或窄肋,尺寸精度高的部分尽量集中在上模或下模上,此外也应尽可能使锻件废边的切除容易。
2.分模线设计分模线(Partingline)或称分离线、分割线,它是上下锻模的分开线。
通常设计锻件的第一步骤就是决定分模线的位置与形状。
分模线可为直线,亦可为不规则曲线,通常视最后锻品的几何形状而定。
分模线位置和形状选择的正确与否,会影响到模锻锻造制程、锻件质量、锻模与切边模制程的复杂程度等。
而选择分模线时之最基本要求是必须确保锻件能很容易的从成形模穴中取出,此外,还须能尽量满足金属容易充满模穴、简化模具制造、容易检查错模、能平衡模锻错模力、毛边能切除干净等要求、如表4-6所示。
有些锻件在选择分模面时无法同时满足上述要求,则需依据具体情况进行分析,以满足其主要要求为前提。
最常见之情况为只满足锻造流线的要求,如图4-358所示。
3.拔模斜度锻件分模线决定之后,还应考虑锻件是否易于从锻模模穴中取出,影响锻件脱模容易与否,可以脱模力之大小来解释之,脱模力大小概括受两因素影响:
模壁因回弹作用而来紧锻件,锻件因冷收缩而造成锻件外壁与内孔之夹紧力。
由于这两个因素所致夹紧力的存在与变化,更兼其所导致摩擦力之存在,故须额外施以脱模力才有可能使锻件脱模。
脱模力之施加可用两种基本方式:
(1)拔模角设计:
拔模角(Draftangle)(如图4-36)系于锻件周围锻造方向倾斜的高度。
拔模角之存在会使脱模力降低甚多,最后仅须依靠锻件自身重量或夹钳的些微施力即可脱模。
(2)顶出装置之作用:
通常而言,有顶出装置之成形设备其拔模角可较小甚至取零,但此时其所须之脱模力则变大。
拔模斜度角大小的设定并无一定的规则可遵循,通常为按锻造材料、锻件形状、锻造备及方法等等之不同而异。
最普通的拔模斜度角是7,而外拔模斜度角可较内拔模斜度角小。
如表4-7所示。
4.内外圆角之设计由