第二章发动机连杆胀断工艺内容教材.docx
《第二章发动机连杆胀断工艺内容教材.docx》由会员分享,可在线阅读,更多相关《第二章发动机连杆胀断工艺内容教材.docx(15页珍藏版)》请在冰豆网上搜索。
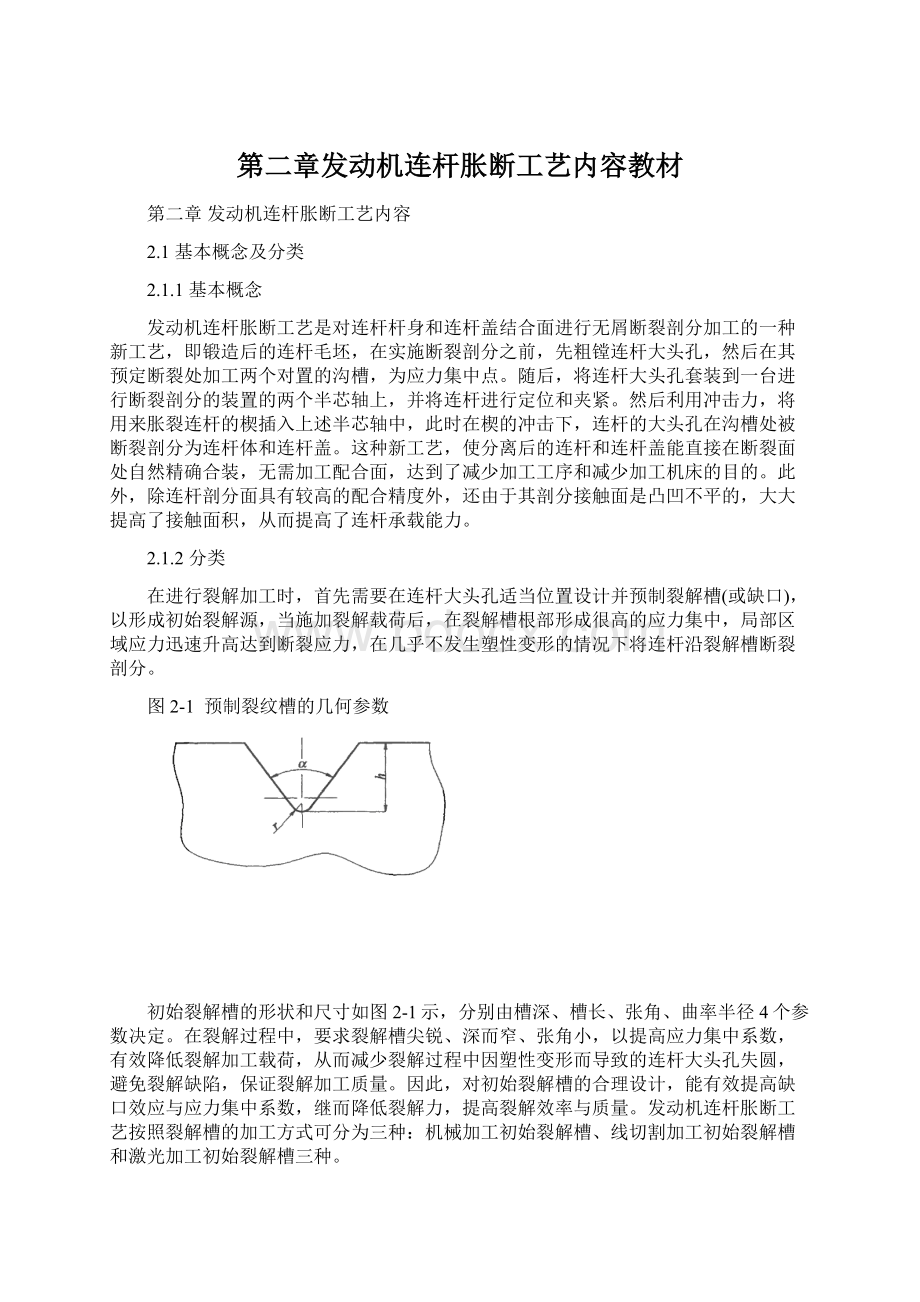
第二章发动机连杆胀断工艺内容教材
第二章发动机连杆胀断工艺内容
2.1基本概念及分类
2.1.1基本概念
发动机连杆胀断工艺是对连杆杆身和连杆盖结合面进行无屑断裂剖分加工的一种新工艺,即锻造后的连杆毛坯,在实施断裂剖分之前,先粗镗连杆大头孔,然后在其预定断裂处加工两个对置的沟槽,为应力集中点。
随后,将连杆大头孔套装到一台进行断裂剖分的装置的两个半芯轴上,并将连杆进行定位和夹紧。
然后利用冲击力,将用来胀裂连杆的楔插入上述半芯轴中,此时在楔的冲击下,连杆的大头孔在沟槽处被断裂剖分为连杆体和连杆盖。
这种新工艺,使分离后的连杆和连杆盖能直接在断裂面处自然精确合装,无需加工配合面,达到了减少加工工序和减少加工机床的目的。
此外,除连杆剖分面具有较高的配合精度外,还由于其剖分接触面是凸凹不平的,大大提高了接触面积,从而提高了连杆承载能力。
2.1.2分类
在进行裂解加工时,首先需要在连杆大头孔适当位置设计并预制裂解槽(或缺口),以形成初始裂解源,当施加裂解载荷后,在裂解槽根部形成很高的应力集中,局部区域应力迅速升高达到断裂应力,在几乎不发生塑性变形的情况下将连杆沿裂解槽断裂剖分。
图2-1预制裂纹槽的几何参数
初始裂解槽的形状和尺寸如图2-1示,分别由槽深、槽长、张角、曲率半径4个参数决定。
在裂解过程中,要求裂解槽尖锐、深而窄、张角小,以提高应力集中系数,有效降低裂解加工载荷,从而减少裂解过程中因塑性变形而导致的连杆大头孔失圆,避免裂解缺陷,保证裂解加工质量。
因此,对初始裂解槽的合理设计,能有效提高缺口效应与应力集中系数,继而降低裂解力,提高裂解效率与质量。
发动机连杆胀断工艺按照裂解槽的加工方式可分为三种:
机械加工初始裂解槽、线切割加工初始裂解槽和激光加工初始裂解槽三种。
2.1.2.1机械加工初始裂解槽
机械加工裂解槽是以推/拉削加工为主,如图2-2所示。
在切削过程中,通过刀柄上安装的刀具对裂解槽进行分层切削,从拉刀端头开始刀柄上每层刀具依次递增量为0.1mm,刀片数量根据裂解槽的深度来决定,并且裂解槽的张角、曲率半径均由推/拉刀具刃口来决定。
图2-2裂解槽机械加工示意图
2.1.2.2线切割加工初始裂解槽
线切割放电加工裂解槽是利用线切割机床在连杆大头孔剖分面切割出裂解应力槽(见图2-3)。
裂解槽的张角和曲率半径等参数均由钼丝直径来决定,通过在线切割设备上安装相应的夹具便能够完成初始裂解槽的加工。
图2-3线切割裂解槽示意图
2.1.2.3激光加工初始裂解槽
激光加工连杆裂解槽的原理是利用激光束与金属材料相互作用的特性进行精密切割。
激光切割裂解槽可根据光束传输通道的不同分为光纤导光激光切割和常规光束激光切割。
2.2EA888发动机连杆胀断工艺内容
2.2.1EA888连杆毛坯加工工艺及关键控制点
2.2.1.1原材料的选择
连杆材料对连杆裂解起决定性作用,它不仅影响连杆的产品性能和切削性,而且,还决定连杆的可裂开性及断面质量。
为满足裂解加工的质量要求,连杆材料要在保证强韧综合指标的前提下,限制连杆的韧性指标,使断口呈现脆性断裂特征。
EA888连杆对材料的要求比较高。
目前,白城中一精锻公司采用的是德国进口的材料36MnVS4,该连杆材料是最早在室温条件下采用裂解加工的锻钢连杆,也是目前应用最为广泛的裂解连杆材料。
其成分特点是低硅、低锰、添加微量合金元素钒及易切削元素硫,合金元素的范围要求窄、材料纯净度要求高。
材料牌号为36MnVS4,主要成分如下表2-1示:
(以重量百分含量计):
表2-1:
元素
C
Si
Mn
P
S
成份范围
0.38
0.65
0.97
0.015
0.069
元素
Al
Cr
Mo
Ni
V
成份范围
0.01
0.20
0.36
0.12
0.3
此材料采用电炉冶炼,炉外精炼,真空除气,热轧制成φ40圆棒料。
热轧材料的金相组织为珠光体+少量铁素体。
它利用锻后控制冷却速度的方法代替锻后重新调质处理,其金相组织为珠光体加断续的铁素体。
2.2.1.2EA888连杆毛坯加工工艺
精密剪切下料→中频感应加热→多工步辊锻制坯→程控液压模锻锤精密模锻→压力机切边、校正→空冷处理→抛丸处理→硬度检验→荧光探伤→螺旋压力机精压→自动称重仪称重→终检→防腐包装
2.2.2连杆毛坯锻造工艺关键控制点
2.2.2.1锻造加热温度和冷却速度的确定
连杆毛坯锻造工艺的关键在于锻造加热温度和冷却速度的确定。
36MnVS4裂解连杆毛坯要求:
金相组织为珠光体+铁素体,铁素体含量不超过35%。
力学性能指标如表2-2示:
表2-2:
抗拉强度
屈服强度
延伸率
断面收缩率
900~1050MPa
≥520MPa
≥10%
20~40%
为了达到上述要求,关键是确定合理的锻造温度和锻后的冷却速度。
为此,笔者在白城中一精锻公司做了大量实验,将棒料分别加热至1150℃、1200℃、1250℃、1300℃锻造,分别用强风冷、弱风冷、空冷3种不同的冷却方式对锻件进行冷却,检验其硬度和锻件的整体拉伸强度(曲线图2-5示)。
图2-5加热温度、冷却速度对硬度的影响
硬度(压痕直径)
拉断力(kN)
图2-6加热温度对连杆整体抗拉强度的影响
从图2-5结果可以看出,在同一锻造加热温度下,冷却速度越快,连杆的硬度越高;冷却速度相同,在一定温度范围内,随锻造加热温度的增高,硬度降低,但锻造的加热温度达到1300℃时,其硬度、略有增高。
从图2-6可知,随加热温度的升高,拉断力有所下降,但一定温度范围内变化较小。
生产中降低锻造的加热温度,可以提高强度指标,但由于胀断式连杆在胀断时有胀断力的要求,不是强度指标越高越好。
所以根据技术标准要求和试验结果,生产中将锻造加热温度控制在1230℃~1260℃左右(终锻温度为960℃~1010℃),锻造后经过弱风冷却,锻件的硬度及强度均能达到较好状态。
2.2.2.2毛坯残余内应力的控制
毛坯内应力直接影响裂解部位质量,如果毛坯存在内应力,胀断后内应力释放出来,导致裂解部位变形,断裂面不能完全啮合,即裂解错位,裂解错位是裂解连杆加工过程中的典型缺陷之一,按照大众公司要求裂解连杆裂解部位上下错位量≤0.02mm,错位量大于0.02mm的连杆就要报废。
白城中一精锻公司最初生产裂解连杆锻坯时,裂解错位就是最为突出的问题。
白城中一精锻公司原有的工艺流程是:
精密剪切下料→中频感应加热→多工步辊锻制坯→程控液压模锻锤精密模锻→压力机切边、校正→空冷处理→抛丸处理→硬度检验→荧光探伤→螺旋压力机精压→自动称重仪称重→终检→防腐包装
从这个工艺流程可以看出,毛坯在冷态下需要用螺旋压力机精压表面,这个压下量一般在0.6mm左右,常温下金属在瞬间要发生这么大的变形,势必需要很大冲击力作用,变形部位因此会存在很大的内应力。
为了验证冷精压产生的内应力对连杆裂解错位的影响,我们做了如下试验:
在同一工艺状态下共生产了26件奇瑞1.9L连杆毛坯,其中13件进行冷精压处理,而另外13件未进行冷精压(热压)处理。
然后依据Mauser-WerkeOberndorfMaschinenbauGmbh公司提供的关于毛坯内应力的检验方法,对其进行检测。
具体检测方法如下:
1)如上图3所示,分别测量DL、DQ1、DQ2尺寸,并记录下来。
2)将连杆夹紧在夹钳中,使其保持水平位置.
3)用铣刀沿大头孔中心慢慢垂直切开,切口宽度2-2.5mm,切割过程中使用足够的散冷剂,以防止连杆升温。
4)重复测量上述三个尺寸,将前后两次测量结果进行比较。
5)理想值:
0-20μm;可用值:
20-30μm;尚可接受值:
30-40μm;不可接受值:
>40μm。
经过冷精压处理的13件连杆毛坯,检测结果如下表2-3示:
奇瑞1.9L连杆内应力检测报告单(冷精压)
工件编号
部位编号
加工前尺寸(mm)
部位编号
加工后尺寸(mm)
差值
(mm)
1
DQ1
49.9645
ADQ1
49.9935
ADQ1-DQ1:
0.0290
DQ2
49.9635
ADQ2
49.9900
ADQ2-DQ2:
0.0265
DL
49.9675
ADL
49.9905
ADL-DL:
0.0230
2
DQ1
49.9695
ADQ1
49.9925
ADQ1-DQ1:
0.0210
DQ2
49.9675
ADQ2
49.9914
ADQ2-DQ2:
0.0239
DL
49.9685
ADL
49.9901
ADL-DL:
0.0216
3
DQ1
49.9685
ADQ1
49.9915
ADQ1-DQ1:
0.0230
DQ2
49.9665
ADQ2
49.9895
ADQ2-DQ2:
0.0230
DL
49.9665
ADL
49.9894
ADL-DL:
0.0229
4
DQ1
49.9685
ADQ1
49.9917
ADQ1-DQ1:
0.0232
DQ2
49.9675
ADQ2
49.9893
ADQ2-DQ2:
0.0218
DL
49.9625
ADL
49.9890
ADL-DL:
0.0265
5
DQ1
49.9665
ADQ1
49.9890
ADQ1-DQ1:
0.0225
DQ2
49.9655
ADQ2
49.9905
ADQ2-DQ2:
0.0250
DL
49.9635
ADL
49.9895
ADL-DL:
0.0260
6
DQ1
49.9975
ADQ1
49.9985
ADQ1-DQ1:
0.010
DQ2
49.9945
ADQ2
49.9960
ADQ2-DQ2:
0.0015
DL
49.9955
ADL
49.9961
ADL-DL:
0.0006
7
DQ1
49.9595
ADQ1
49.9985
ADQ1-DQ1:
0.0390
DQ2
49.9545
ADQ2
49.9901
ADQ2-DQ2:
0.0365
DL
49.9465
ADL
49.9800
ADL-DL:
0.0435
8
DQ1
49.9665
ADQ1
49.9926
ADQ1-DQ1:
0.0261
DQ2
49.9525
ADQ2
49.9896
ADQ2-DQ2:
0.0371
DL
49.9475
ADL
49.9875
ADL-DL:
0.0400
9
DQ1
49.9655
ADQ1
49.9924
ADQ1-DQ1:
0.0319
DQ2
49.9515
ADQ2
49.9907
ADQ2-DQ2:
0.0392
DL
49.9535
ADL
49.9900
ADL-DL:
0.0365
10
DQ1
49.9595
ADQ1
49.9920
ADQ1-DQ1:
0.0325
DQ2
49.9475
ADQ2
49.9903
ADQ2-DQ2:
0.0428
DL
49.9455
ADL
49.9893
ADL-DL:
0.0438
11
DQ1
49.9585
ADQ1
49.9926
ADQ1-DQ1:
0.0341
DQ2
49.9475
ADQ2
49.9900
ADQ2-DQ2:
0.0425
DL
49.9455
ADL
49.9909
ADL-DL:
0.0454
12
DQ1
49.9625
ADQ1
49.9920
ADQ1-DQ1:
0.0295
DQ2
49.9555
ADQ2
49.9903
ADQ2-DQ2:
0.0388
DL
49.9495
ADL
49.9908
ADL-DL:
0.0413
13
DQ1
49.9585
ADQ1
49.9924
ADQ1-DQ1:
0.0339
DQ2
49.9555
ADQ2
49.9906
ADQ2-DQ2:
0.0391
DL
49.9475
ADL
49.9902
ADL-DL:
0.0427
从检测结果看,合格状态的连杆毛坯共8支,其中,错位量在0~20μm的仅1支(6#);错位量在20~30μm,共5支(1#,2#,3#,4#,5#);错位量在30~40μm,共2支(8#,9#);不合格状态,错位量超过40μm,共5支(7#,10#,11#,12#,13#),合格率仅为61.5%。
未经过冷精压处理的13件连杆毛坯,具体检测结果如下表2-4示:
奇瑞1.9L连杆内应力检测报告单(未精压)
工件编号
部位编号
加工前尺寸(mm)
部位编号
加工后尺寸(mm)
差值(mm)
1
DQ1
49.9775
ADQ1
49.9903
ADQ1-DQ1:
0.0128
DQ2
49.9765
ADQ2
49.9910
ADQ2-DQ2:
0.0145
DL
49.9735
ADL
49.9867
ADL-DL:
0.0132
2
DQ1
49.9685
ADQ1
49.9705
ADQ1-DQ1:
0.0020
DQ2
49.9695
ADQ2
49.9711
ADQ2-DQ2:
0.0016
DL
49.9675
ADL
49.9684
ADL-DL:
0.0009
3
DQ1
49.9625
ADQ1
49.9725
ADQ1-DQ1:
0.010
DQ2
49.9635
ADQ2
49.9650
ADQ2-DQ2:
0.0015
DL
49.9655
ADL
49.9663
ADL-DL:
0.0008
4
DQ1
49.9665
ADQ1
49.9900
ADQ1-DQ1:
0.0235
DQ2
49.9655
ADQ2
49.9852
ADQ2-DQ2:
0.0197
DL
49.9625
ADL
49.9845
ADL-DL:
0.0220
5
DQ1
49.9735
ADQ1
49.9906
ADQ1-DQ1:
0.0171
DQ2
49.9765
ADQ2
49.9884
ADQ2-DQ2:
0.0119
DL
49.9745
ADL
49.9893
ADL-DL:
0.0148
6
DQ1
49.9885
ADQ1
49.9905
ADQ1-DQ1:
0.0020
DQ2
49.9865
ADQ2
49.9881
ADQ2-DQ2:
0.0016
DL
49.9875
ADL
49.9892
ADL-DL:
0.0017
7
DQ1
49.9665
ADQ1
49.9855
ADQ1-DQ1:
0.0190
DQ2
49.9685
ADQ2
49.9873
ADQ2-DQ2:
0.0188
DL
49.9655
ADL
49.9809
ADL-DL:
0.0154
8
DQ1
49.9595
ADQ1
49.9602
ADQ1-DQ1:
0.0007
DQ2
49.9575
ADQ2
49.9588
ADQ2-DQ2:
0.0013
DL
49.9545
ADL
49.9549
ADL-DL:
0.0004
9
DQ1
49.9725
ADQ1
49.9844
ADQ1-DQ1:
0.0119
DQ2
49.9715
ADQ2
49.9807
ADQ2-DQ2:
0.0092
DL
49.9745
ADL
49.9866
ADL-DL:
0.0121
10
DQ1
49.9685
ADQ1
49.9830
ADQ1-DQ1:
0.0145
DQ2
49.9655
ADQ2
49.9793
ADQ2-DQ2:
0.0138
DL
49.9675
ADL
49.9816
ADL-DL:
0.0141
11
DQ1
49.9905
ADQ1
49.9907
ADQ1-DQ1:
0.0002
DQ2
49.9885
ADQ2
49.9888
ADQ2-DQ2:
0.0003
DL
49.9875
ADL
49.9881
ADL-DL:
0.0006
12
DQ1
49.9625
ADQ1
49.9729
ADQ1-DQ1:
0.0104
DQ2
49.9585
ADQ2
49.9701
ADQ2-DQ2:
0.0116
DL
49.9595
ADL
49.9717
ADL-DL:
0.0122
13
DQ1
49.9595
ADQ1
49.9820
ADQ1-DQ1:
0.0225
DQ2
49.9545
ADQ2
49.9786
ADQ2-DQ2:
0.0241
DL
49.9575
ADL
49.9812
ADL-DL:
0.0237
从检测结果看,所有的连杆毛坯均是合格的。
错位量在0~20μm,11支(1#,2#,3#,5#,6#,7#,8#,9#,10#,11#,12#);错位量在20~30μm,共2支(4#,13#);合格率为100%。
2.2.3EA888发动机连杆加工工艺
EA888连杆采用激光加工初始裂解槽,其工艺流程具体如下:
粗磨连杆两侧面→粗镗大小头孔、半精镗大小头孔→钻、攻螺纹孔→钻油道孔→清洗→激光切割裂解槽、裂解、装配、压衬套、精整衬套、倒角→精磨两侧面→半精镗、精镗大小头孔→铰珩连杆大小头孔→清洗→称重分组→终检
2.2.3.1激光切割裂解槽质量控制
如图2-8所示,连杆裂解前要先在连杆大头孔的两侧面拉削出两条对称裂解槽,使连杆裂解时产生应力集中,以实现定位断裂。
由于连杆初始裂解槽属于窄缝盲槽,其加工精度和槽面质量要求很高,一般的二氧化碳激光器无法满足裂解槽的加工精度和槽面的质量要求。
由于Nd:
YAG固体激光器的输出波长短、与金属的耦合效率高、加工性能良好、可与光导纤维耦合,且结构紧凑、质量轻,并能借助时间分割和功率分割成多路系统,便于柔性和远程激光加工,因此成为加工连杆裂解槽的首选光源。
利用Nd:
YAG固体激光器进行裂解槽的加工时,首先将从Nd:
YAG激光发生器发射出的激光束通过导光系统聚焦成具有高功率密度的激光束,并照射于连杆内壁欲切割处,激光能量迅速被连杆吸收,使欲切割处局部温度急剧上升,到达沸点后材料开始汽化并形成孔洞。
随着光束与连杆相对位置的移动,最终在连杆大头孔的切割部位形成切缝。
同时,切缝处汽化的金属被具有一定压力的辅助气体吹除,通过除尘系统将残渣吸收到残渣收集器,避免了环境污染。
激光加工裂解槽通常有单激光切割头和双激光切割头两种形式。
在使用1个切割头进行加工时。
利用激光分时输出到两个交叉成90°布置的聚光器上,对2条裂解槽进行顺次切割,即在1次运动中只切割1条裂解槽。
而采用双激光切割头加工裂解槽时,利用了功率分割的方法,将光束同时分配到2个呈90°布置的聚光器上,通过1次向下运动可以同时完成2条裂解槽的切割。
裂解槽加工质量对连杆裂解加工有着决定性的影响,目的是制造缺口效应,提高应力集中系数,满足张开型断裂条件,保证断裂发生在预定位置,并有效降低裂解加工载荷,保证裂解加工质量。
目前,裂解槽多采用激光加工的方式替代原有的拉削加工,激光加工裂纹槽生产效率高,裂解加工后大头孔的圆度误差及裂纹线与断裂面的水平误差最小,而拉削加工的裂纹槽上述两项误差值最大,线切割加工方式居中。
裂解槽的形状与深度,直接影响连杆裂解的裂解压力,从而影响变形,如图2-9所示。
由此可见,裂解槽深时裂解压力小,相应变形小,但槽深过大,将使裂解后大头孔精镗余量加大,在精加工后仍存留裂纹槽痕迹,甚至会造成废品。
反之,裂解槽浅时,将使裂解加工过程中的裂解力增大,同时会导致裂解后连杆大头孔圆度变化增加,而且较大的裂解力必然带来较大的残余应力,使连杆装机后残余应力的释放影响发动机的工作性能。
经试验证明,裂解槽深限定在0.4~0.57mm比较适宜。
图2-9裂解槽深与裂解压力关系示意图
此外,还要保证大头孔中心两侧的裂解槽位置对称、槽深一致,减少槽深偏差,以保证最终获得两个高质量的断裂剖分面。
若两侧槽深不一致,则会产生一边开裂一边未开裂的“单边断裂”现象。
2.2.3.2裂解工位质量控制
在裂解工位上,为保证裂解时压力均匀,必须使工件精确定位,由电控比例阀油缸带动楔铁涨套移动,到达匀速运动后,涨套对连杆内径产生压力,使其首先在裂解槽尖角部开裂,到螺栓孔后向两侧延展,直到连杆完全涨开,如图2-10所示。
图2-10裂解工位示意图
裂解夹具是影响裂解质量的因素之一,连杆裂解后拧紧螺栓前,结合面的啮合十分重要,所以要求裂解工位夹紧稳定,往复运动精度高,夹具使分离面完全啮合。
另外,涨套与楔铁的尺寸直接影响裂解压力与工作行程。
当机床调整、涨套与楔铁尺寸都很好时,裂解缺陷很少,此时裂解压力9~10MPa、工作节拍13s,但由于长时间工作必然造成磨损和塑性变形,当单边塑性变形量达到0.25mm后涨套就无法使用了。
2.2.3.3裂解的辅助工艺
在裂解前,楔铁从0加速到一定速度是空行程,裂解过程是一个匀速过程。
涨开后,压缩空气工位清理涨断口;楔铁再次工进,以确认连杆是否完全裂开。
2.2.3.4裂解连杆断裂截面设计
裂解连杆断裂截面的形状直接影响裂解的结果。
裂纹首先在连杆大头孔内表面开始起裂,然后向两侧的螺栓孔及外侧表面扩展,当裂纹扩展至螺栓孔处时由一条裂纹分成上下两条裂纹,越过螺栓孔后上下两条裂纹重新汇合。
接近于圆形的截面有利于上下两条裂纹在同一点汇合,从而提高裂解质量。
相反,断裂截面越接近矩形,上下两条裂纹不在同一点汇合的风险就越大,结果会产生暴口缺陷。
所以裂解连杆的断裂截面越接近圆形就越好。
2.3与其他发动机连杆胀断工艺的区别
EA888连杆与其它发动机连杆胀断工艺的区别,在于采用激光切割的方法加工初始裂解槽。
激光加工与其它加工方法的区别:
由于在连杆初始裂解槽的预制过程中经激光加工的裂解槽在其根部附近有淬火效应,使裂解更容易进行,并且试验数据显示激光加工裂解槽比机械拉槽的裂解力降低1/3左右,裂解后连杆大头孔圆度仅是机械拉削的l/4~1/6,裂解变形明显减小,断裂线偏离理论位置的情况也得到改善,因此激光加工在裂解槽的加工质量、生产效率、后续裂解质量及连杆产品质量等方面具有如下优势。
a加工过程中无刀具磨损和钼丝的损耗,生产工艺重复性和稳定性高,灵活通用;并且切缝窄,槽深及槽宽均匀,尺寸及位置精度高,可保障后续加工质量。
b加工后的裂解槽易裂解,可显著减少裂解力及大头孔裂解变形,使得后续精加工大、小头孔精度明显提高,从而避免掉渣、错位、夹屑等质量缺陷的出现。
c激光加工的光束能量密度高、移动速度快,对非激光照射部位没有影响或影响极小,使工件的热变形很小,后续加工量减小。
d激光加工技术采用干式加工代替湿式加工,省去了线切割过程中乳化液的冷却,减少了环境污染。