熔体成型速率对微晶玻璃显微结构的影响 1.docx
《熔体成型速率对微晶玻璃显微结构的影响 1.docx》由会员分享,可在线阅读,更多相关《熔体成型速率对微晶玻璃显微结构的影响 1.docx(13页珍藏版)》请在冰豆网上搜索。
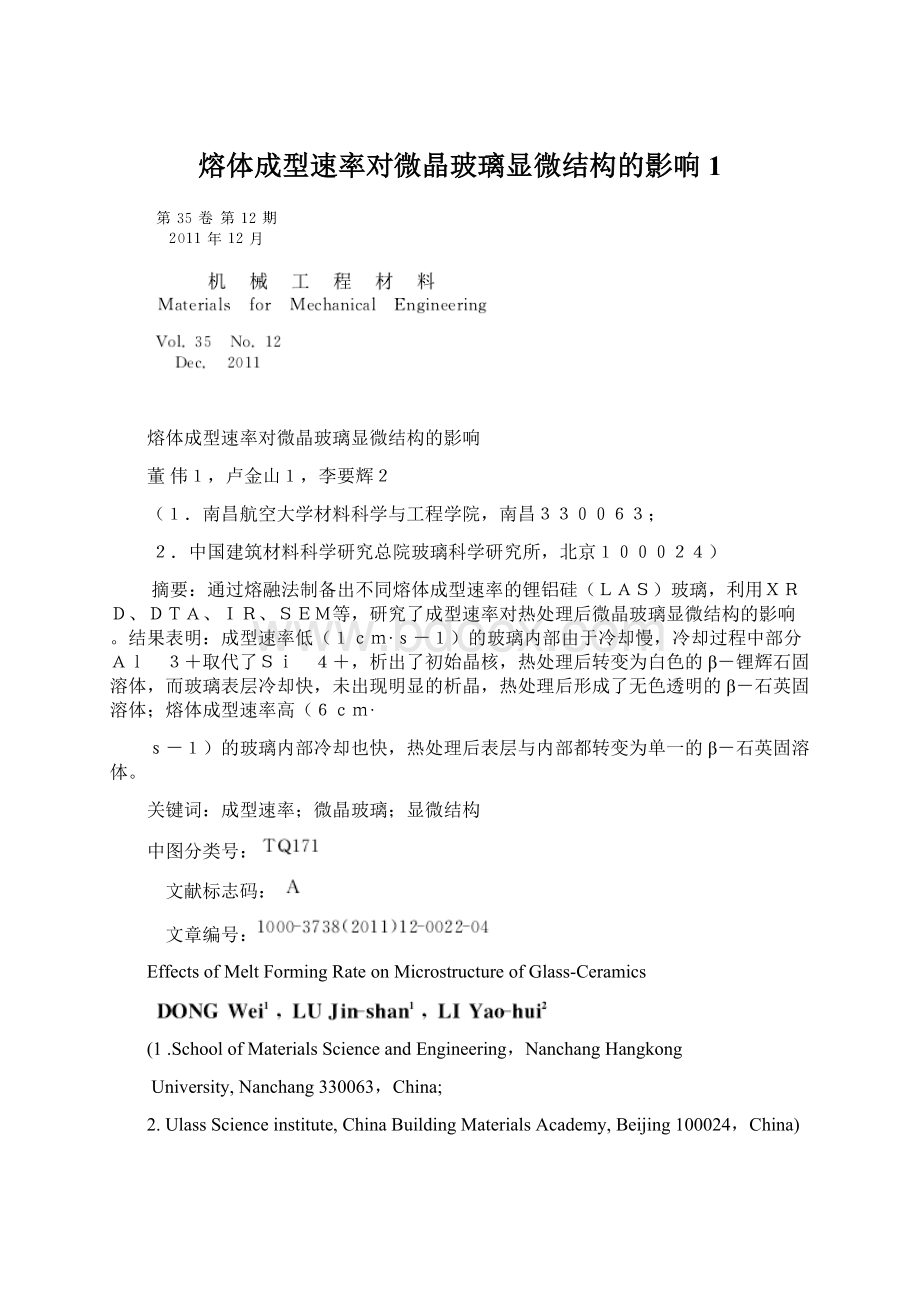
熔体成型速率对微晶玻璃显微结构的影响1
熔体成型速率对微晶玻璃显微结构的影响
董伟1,卢金山1,李要辉2
(1.南昌航空大学材料科学与工程学院,南昌330063;
2.中国建筑材料科学研究总院玻璃科学研究所,北京100024)
摘要:
通过熔融法制备出不同熔体成型速率的锂铝硅(LAS)玻璃,利用XRD、DTA、IR、SEM等,研究了成型速率对热处理后微晶玻璃显微结构的影响。
结果表明:
成型速率低(1cm·s-1)的玻璃内部由于冷却慢,冷却过程中部分Al 3+取代了Si 4+,析出了初始晶核,热处理后转变为白色的β-锂辉石固溶体,而玻璃表层冷却快,未出现明显的析晶,热处理后形成了无色透明的β-石英固溶体;熔体成型速率高(6cm·
s-1)的玻璃内部冷却也快,热处理后表层与内部都转变为单一的β-石英固溶体。
关键词:
成型速率;微晶玻璃;显微结构
中图分类号:
文献标志码:
文章编号:
EffectsofMeltFormingRateonMicrostructureofGlass-Ceramics
(1.SchoolofMaterialsScienceandEngineering,NanchangHangkong
University,Nanchang330063,China;
2.UlassScienceinstitute,ChinaBuildingMaterialsAcademy,Beijing100024,China)
Abstract:
Lithiumaluminosilicateglasswithdifferentmeltformingrateswerepreparedbythemeltingmethod.heeffectofformingrateonthemicrostructureofheattreatedglass-ceramicswasanalyzedusingXRD,DA,lRandSEMtechniques.heresultsshowthatthereplacementofsomeAl''+forSi'+occurredintheinteriorofglasswithlowformingrateintheprocessofslowcooling(1cm·s),whichledtotheprimarynucleiprecipitated.Theglassinteriorconvertedintoawhitespodumenestructureafterheattreatment.Meanwhile,becauseofrapidcoolingoftheglasssurface,thenucleationdidnotoccurobviously.Atransparentandcolorlessquartzsolidsolutionwasformedafterheattreatment.Highmeltformingrate(6cm·s)ledtorapidcoolingintheinteriorofglass,too.Asinglequartzsolidsolutionwasformedonsurfaceandininteriorafterheattrcament.
0 引言
锂铝硅系(LAS)微晶玻璃具有高透明度和低热膨胀系数两大特点,广泛应用于高温观察窗、光学器件、激光陀螺等方面[1]。
熔融法制备LAS微晶玻璃需要进行玻璃料熔制、玻璃熔体成型以及玻璃晶化热处理等工艺步骤,玻璃成型过程中如果停留在有利于晶体形成和生长的温度区间,内部便会出现析晶,形成“析晶结石”缺陷[2-3]。
由于LAS玻璃熔制温度高(1 600℃
以上)、玻璃熔体黏度大,成型过程中玻璃表层冷却快,但内部散热慢,仍处于高温状态,容易形成高温析晶,从而破坏玻璃表层和内部组织结构的均匀性,导致热处理后的微晶玻璃内部可能出现乳浊,影响其光学性能。
为了防止玻璃熔体
凝固成型时的高温析晶,需要提高熔体成型速率,以使玻璃内部温度尽快降至析晶温度以下。
目前有关玻璃熔体成型速率对相应微晶玻璃结构影响的研究工作未见公开报道,作者以LAS玻璃成型为例,确定玻璃熔体成型速率为熔体浇注速率,即单位时间内熔体在不锈钢板表面的浇注长度,研究了不同成型速率对微晶玻璃显微结构的影响及其机理,并提出了改善微晶玻璃结构均匀性的有效途径。
1 试样制备与试验方法
1.1 试样制备
玻璃原料主要成分为
(质量分数/%,下同),同时引入4.5%的TiO2和ZrO2作为晶核剂,加入8.5%的Na2O、CaO、BaO、MgO和Sb2O3等作为助熔剂和澄清剂,以改善玻璃的熔制性能,所有原料均为分析纯。
使用陶瓷研钵研磨混合粉料0.5h,装入高纯氧化铝坩埚,在1 650℃的高温熔化炉内恒温熔制4h。
熔制好的玻璃熔体分别以1,6cm·s-1的速率浇注于事先预热到550℃的不锈钢板上,并手动压成厚度为2mm的玻璃片,然后迅速置于550℃退火炉中退火2h,随炉冷却至室温,得到无色透明LAS玻璃,成型速率为1,6cm·s-1的玻璃试样编号分别为A、B。
玻璃试样在830℃热处理1,
10h,得到相应的LAS微晶玻璃。
1.2 试验方法
采用DZ-3331型热分析仪(DTA)测定玻璃的晶化温度,升温速率为10℃·min-1;采用D8Ad-vance型X射线衍射仪(XRD)分析玻璃的晶体结构,工作电压和电流分别为40kV和40mA,扫描速率为5(°)/min;采用FTIR Nicolet 5700型傅里叶变换红光谱仪(IR)分析玻璃的结构,试样为粒径低于43μm的玻璃粉,测试波数范围为3502 500cm-1;微晶玻璃试样经过磨抛,在体积分数为5%的氢氟酸水溶液中浸泡30s,然后用蒸馏水冲洗后吹干,采用JSM-5600F型扫描电镜(SEM)观察表面形貌;采用IE 300X型能量色散光谱仪(EDS)分析不同区域的元素组成。
2 试验结果与讨论
2.1 玻璃和微晶玻璃的相组成
由图1可以看出,成型速率低的玻璃试样A的晶化峰温度(833℃)略高于成型速率高的试样B的(830℃),但晶化峰强度明显低于试样B的。
Gup-ta[4]研究认为,玻璃DTA曲线中晶化峰强度和晶化温度与试样中的晶核数目有关,它是判断玻璃形核和晶化的有力判据。
成型过程中如果玻璃熔体内部冷却慢,容易出现析晶现象[3],即成型后玻璃内部已有晶核生成。
热处理时已析晶的玻璃内部晶粒长大所释放的能量低于未析晶玻璃的,后者热处理过程中析晶和晶粒长大同时进行,故晶化放热峰强度更高
为了进一步确定玻璃内部结构的变化,对试样A、B进行红外光谱分析,如图2所示。
在1 381cm-1和1 620cm-1处的红外吸收峰均为玻璃表面吸附的羟基振动吸收引起的;2 360cm-1处的吸收峰为表面吸附的CO2引起的;1 200~1 000cm-1范围的红外吸收带是Si-O-Si键的反对称伸缩振动、O-Si-O键的伸缩振动引起的;在800~600cm-1范围的是Si-O-Al的振动吸收峰,460~420cm-1范围的为[AlO4]5-的振动吸收峰,试样A的这两个吸收峰波
数明显增大,这是由于Al 3+取代Si 4+导致O-Al振动所引起的[5]。
与此相反,试样A在波数为1 200~1 000cm-1处的红外吸收带明显移向低波数,并且吸收带更宽,这是由于玻璃中的Al 3+取代Si 4+,使得Si-O键振动频率降低,吸收谱带向低波数方向移动,并导致吸收带宽化。
由于玻璃转变成微晶玻璃时,一部分Al 3+和Li+会取代[SiO4]4-中的Si 4+[6],从红外光谱可知成型速率低的试样A中部分Al 3+取代了Si 4+,Al-Si-O组分的初始晶核已经形成,进一步证实了图1中两种试样放热峰的差异是由试样A内部析晶引起的。
根据试样DTA曲线的晶化峰温度,将玻璃试样A和B在830℃处理1h[7]。
从热处理后两种试样的外观来看,试样A内部为白色,表层为无色透明,两者界面上出现大量裂纹;而试样B整体为无色透明。
对热处理前后的玻璃表面进行XRD分析,如图3所示。
不同成型速率玻璃试样的XRD谱均为典型的非晶态漫散射谱,热处理后微晶玻璃表面的透明区都为LixAlxSi1-2xO2(PDF:
40-0073)结构的β-石英固溶体,但试样A内部的白色区为Li-AlSi2O6(PDF:
71-2058)结构的β-锂辉石固溶体。
由此可以初步判定,试样A的微晶玻璃分层现象是由于玻璃内部已出现析晶,在该试样的热处理后表层和内部形成了不同晶相,两种晶相之间热膨胀系数失配,从而导致热处理过程中界面上产生大量裂纹。
Fig.3XRDpatternsofsampleswithdifferentformingratesandstates;(a)beforethermaltreatment;(b)thetransparentpartafterthermaltreatmentand(c)thewhitepartinsidethesampleAafterthermaltreatment
2.2 微晶玻璃的显微结构
由图4可见,成型速率低的试样A内部白色区比较致密,而透明区明显存在一些长裂纹;表层透明区有棒状颗粒,长度约为300nm,宽度为50~
100nm,颗粒表面分布着球状小晶粒;颗粒间存在大量玻璃相(氢氟酸腐蚀后留下的孔隙);白色区微观形貌比较单一,如图4(c)所示,由50nm左右的球状颗粒相互连接成珊瑚状,颗粒间隙很小(玻璃相少),比透明区致密,并出现颗粒粘连现象,阻挡了可见光的通过,而β-锂辉石固溶体不具有透光性,所以试样A的微晶玻璃内部呈现白色。
成型速率高的试样B热处理后晶粒均匀细小,晶粒尺寸为100nm左右。
Fig.4SEMmorphologyofLASglass-ceramics;(a)interfacebetweentransparentand
(b)transparentpartofsampleA;(c)whitepartofsampleAand(d)whitepartsinsampleA;
sampleB
为了进一步确定成型速率低的微晶玻璃表层和内部结构的差别,对试样A的透明区和白色区分别进行EDS能谱分析,如图5所示,可知透明区的铝含量明显高于白色区的。
LAS
微晶玻璃的化学结构通式为Li2O·Al2O3·nSiO2,当n值在4~10之间时为β-锂辉石固溶体[8-9]。
EDS分析结果表明,透明区的n值为1.2,而白色区的n值为5.5,由此可见,晶化后试样A的白色区具有β-锂辉石固溶体结构,这与图3
中热处理后的微晶玻璃内部XRD谱相吻合。
由于β-石英固溶体是β-锂辉石固溶体的亚稳相[10-11],从透明区SEM形貌可以看出,棒状颗粒表面有很多球状小晶粒,这表明亚稳态的棒状β-石英固溶体开始向球状β-锂辉石固溶体转变。
将试样A的晶化时间延长至10h,发现微晶玻璃内部白色区明显扩大,表层透明区缩小,甚至完全消失。
由图6可见,晶化时间为10h的微晶玻璃中物相都转变为β-锂辉石结构,说明延长晶化时间后,棒状亚稳结构的β-石英固溶体转变为球状不透β-锂辉石固溶体,这种相变过程通常伴随着球状小晶粒的长大。
从上述成分和结构分析结果可以推测,玻璃熔体成型速率低时,玻璃内部在成型阶段冷却慢,长时间处于高温状态,析出Al-Si-O成分的初始晶核,热处理阶段初始晶核促进了
β-石英固溶体晶粒的生长,并随热处理时间的延长β-石英固溶体转变成β-锂辉石固溶体;而玻璃表层由于冷却快,初始晶核的密度显著低于玻璃内部的,热处理阶段主要通过晶核剂(TiO2/ZrO2)形核,形成β-石英固溶体,即成型速率低时玻璃表层和内部由于冷却速率相差很大,初始晶核密度存在显著差别,导致两个区的形核机制不同,前者主要依靠玻璃组分中的晶核剂在热处理阶段形核,后者主要是靠玻璃成型阶段形成的初始晶核,并在热处理开始之后直接促进β-石英固溶体晶粒的生长。
微晶玻璃表层中棒状颗粒表面存在的球状小晶粒也与这两种形核机制有关。
在这种情况下,LAS微晶玻璃的表层和内部晶相不同,两种晶相的光学透明度和热膨胀系数差别大,导致玻璃出现分层以及界面裂纹。
当玻璃熔体成型速率大时,玻璃表面和内部都没有出现析晶,只在热处理阶段通过晶核剂形核,所以整体结构均匀。
由此可见,在试验和生产过程中熔体的成型速率应当尽可能高,或者在熔融温度下成型,以确保热处理后微晶玻璃结构的均匀性。
3 结论
(1)玻璃熔体成型速率低(1cm·s-1)时玻璃结构不均匀,部分Al 3+
取代了Si 4+,析出初始晶核,热处理后晶核长大形成β-锂辉石固溶体,引起表层
与内部分层;成型速率高(6cm·s-1)时,内部冷却快,没有出现析晶,热处理后得到单一均匀的β-石英固溶体。
(2)为了制备结构均匀的微晶玻璃,应尽可采用较高的玻璃熔体成型速率,使成型后玻璃能够快速冷却,内部温度尽快降至析晶温度以下,以避免玻璃内部出现析晶现象。
时,即XDRX=1,稳态应力对应的应变范围(如表2所示)。
将这些条件代入式(10)中,求得m的平均值为2.473 61。
至此将m,εc,ε*,Z代入式(10)可
得到7075铝合金动态再结晶的动力学模型。
3 结论
(1)通过确定7075铝合金真应力-真应变曲线及硬化率曲线中动态再结晶的初始临界应变εc、峰值应力对应的应变εp、最大软化速率对应的应变ε*三大特点,及动态再结晶激活能,最后引入修正的Avrami方程,以无量纲的中间变数Z/A为纽带将动态再结晶体积分数、应力、应变量、应变速率、温度等参数建立起动态耦合关系模型。
(2)随应变量增加,动态再结晶逐渐完成,增大应变速率或降低变形温度均会抑制动态再结晶的发生。