第二部份回流焊接技术的种类和原理.docx
《第二部份回流焊接技术的种类和原理.docx》由会员分享,可在线阅读,更多相关《第二部份回流焊接技术的种类和原理.docx(11页珍藏版)》请在冰豆网上搜索。
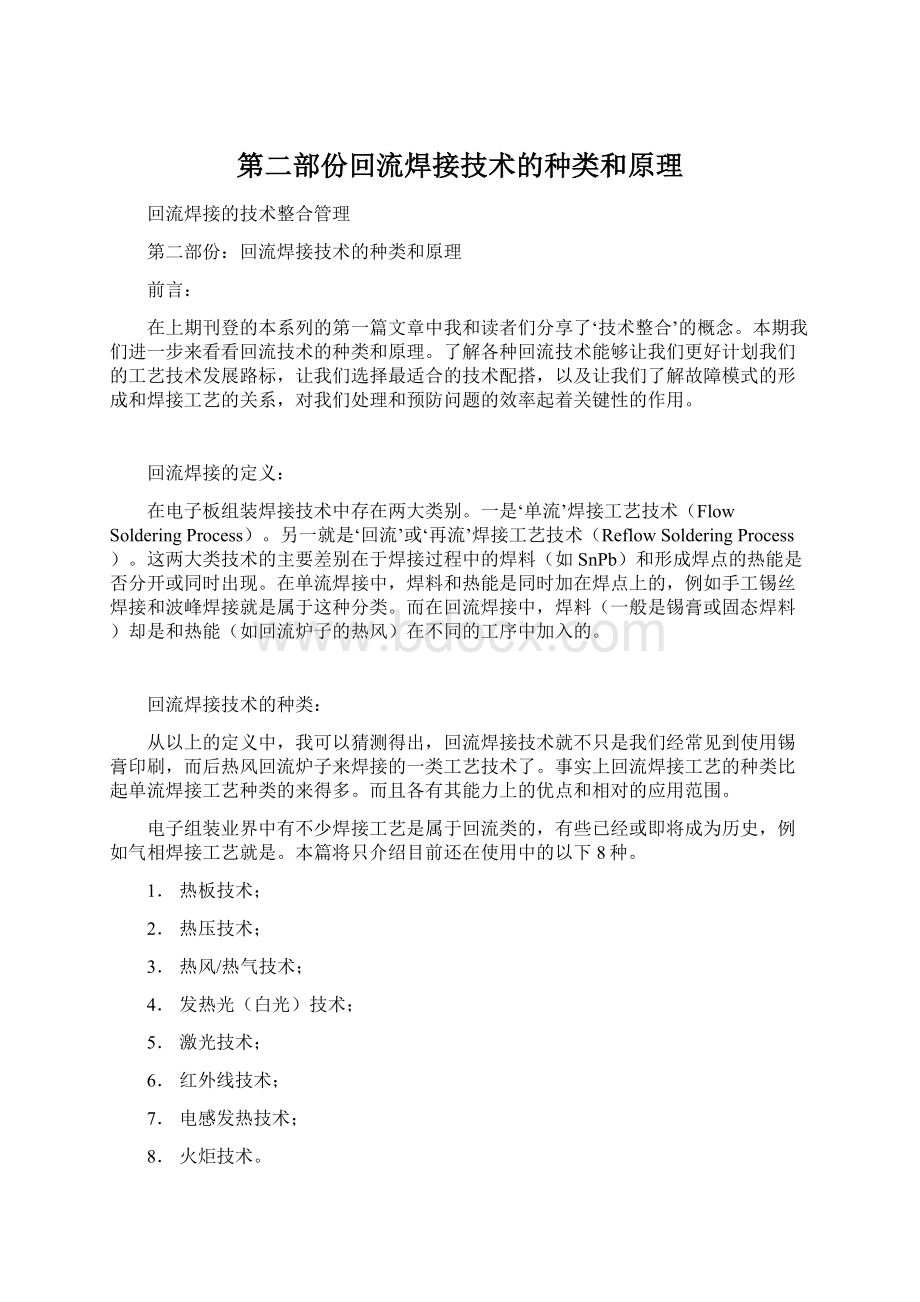
第二部份回流焊接技术的种类和原理
回流焊接的技术整合管理
第二部份:
回流焊接技术的种类和原理
前言:
在上期刊登的本系列的第一篇文章中我和读者们分享了‘技术整合’的概念。
本期我们进一步来看看回流技术的种类和原理。
了解各种回流技术能够让我们更好计划我们的工艺技术发展路标,让我们选择最适合的技术配搭,以及让我们了解故障模式的形成和焊接工艺的关系,对我们处理和预防问题的效率起着关键性的作用。
回流焊接的定义:
在电子板组装焊接技术中存在两大类别。
一是‘单流’焊接工艺技术(FlowSolderingProcess)。
另一就是‘回流’或‘再流’焊接工艺技术(ReflowSolderingProcess)。
这两大类技术的主要差别在于焊接过程中的焊料(如SnPb)和形成焊点的热能是否分开或同时出现。
在单流焊接中,焊料和热能是同时加在焊点上的,例如手工锡丝焊接和波峰焊接就是属于这种分类。
而在回流焊接中,焊料(一般是锡膏或固态焊料)却是和热能(如回流炉子的热风)在不同的工序中加入的。
回流焊接技术的种类:
从以上的定义中,我可以猜测得出,回流焊接技术就不只是我们经常见到使用锡膏印刷,而后热风回流炉子来焊接的一类工艺技术了。
事实上回流焊接工艺的种类比起单流焊接工艺种类的来得多。
而且各有其能力上的优点和相对的应用范围。
电子组装业界中有不少焊接工艺是属于回流类的,有些已经或即将成为历史,例如气相焊接工艺就是。
本篇将只介绍目前还在使用中的以下8种。
1.热板技术;
2.热压技术;
3.热风/热气技术;
4.发热光(白光)技术;
5.激光技术;
6.红外线技术;
7.电感发热技术;
8.火炬技术。
工业界对焊接技术也有另外一种分类的做法,就是按照热的传递方式来分类。
也就是按‘传导’、‘辐射’和‘对流’传热模式来分类。
例如以上1和2类的热板和热压工艺都属于‘传导’加热工艺;第3类的热风属于‘对流’加热工艺;而第4到第6项则属于‘辐射’加热工艺。
至于那些不采用以上任何方法的,业界将其列为‘特别焊接技术’。
而在应用上,这些‘特别焊接技术’也是用在较特别的焊点特性上的。
例如热容量超大的焊点等。
上述7和8都属于这类焊接技术。
一般而言,前三种技术(传导、辐射和对流)都是用在通用的焊点和PCBA上的。
不过他们之间存在一定的特性差异。
首先是‘传导’加热技术。
这门技术一般的特性是成本低,工艺能力和质量水平也较低。
同时由于属于接触式的焊接,也就存在热和机械力同时存在的风险问题,一般多被采用在低成本、低质量和寿命要求的场合中。
‘辐射’加热技术的优势,是其稳定性在三者中属最好的。
一旦工艺参数设置正确,产品的Cp可以是三种技术中最高的。
其技术成本也属于中等。
介于‘传导’和‘对流’技术之间。
不过这门适合高效率生产的技术,会出现材料吸热程度不均的不良现象。
所以‘辐射’加热技术在大批量生产技术上基本上被‘对流’加热技术所取代。
而只在局部或选择性焊接中保有优势。
另外,焊接时会出现过热的风险也是这门技术的一个弱点。
‘对流’技术在大批量生产中是目前的回流焊接技术主流。
随着气相技术的被淘汰,现有的技术是处于以强制热空气为主和热气体(无氧环境)为辅的状况。
对流技术的最强点,是其能够使焊接对象(PCBA)上各点的温差保持在最小的程度。
不过对流技术的难以掌握和控制,以及设备的成本却是这门技术的缺点。
‘辐射’和‘对流’技术都是属于‘非接触式’的焊接技术。
使他们在质量风险的考虑上强于‘传导’技术。
下面我们来看看八种回流焊接技术的特性和优缺点。
热板焊接技术:
这是一种有长久历史的SMT焊接工艺。
其工艺原理是将贴片好的PCBA放置在加热板上(见图一),加热板通过PCBA基板传热到上面的各个焊点进行焊接。
在焊接完成后将PCBA移开完成整个工艺。
为了能处理较大热容量的PCBA,热板本身必须具备足够巨大的热容量。
而这就影响了温度的反应速度。
所以这类焊接技术的设备以采用多段式加热板的设计为佳。
热板技术的优点是简单和低成本。
缺点是使用范围较小以及工艺能力较差。
由于它必须通过基板传热,基板的材料必须具备良好的导热以及耐高温性能。
而且基板必须和热板保持很好的接触。
也就是在整个焊接过程中必须平整,不允许产生曲翘,更不能有通孔插件。
电子业中常用的FR系列基材是难以满足这些条件的。
也因此这门技术甚少用于FR系列的基板上。
倒是陶瓷基材能很好的满足这些条件。
加上陶瓷基板上焊点所面对的焊点疲劳和蠕变问题程度较低,这类热板焊接技术能够满足其要求而同时可以降低加工成本。
热压焊接技术:
这是另外一种常见的接触式热传导焊接技术。
通过外形尺寸配合焊端的发热焊接头,接触事先已经上好的固态焊料进行焊接(见图二)。
为了确保传热效率,焊接头必须和焊点有良好的接触。
这有赖于足够的接触面积以及适当的压力。
这工艺需求以及需要很大个性化的焊接头设计成为了这门技术的缺点。
所以这技术并不能使用在所有的焊点设计上。
而常做为局部(或称选择性)焊接技术。
由于局部焊接技术对器件本体的热危害很小,这类技术也常用来进行对热敏感器件的焊接。
热压的另外一个强处,使通过准确的设备定位,可以进行微间距焊接。
这些应用的典型的例子就是柔性板和刚性板之间的焊接(图三)和TAB焊接上(图四)。
白热光焊接技术:
这类技术通过光学镜片将高热能的白热光聚焦到焊点上进行焊接(见图五)。
做为局部或选择性焊接技术,这是种加热快速、焊接质量控制力强的技术。
但由于其焊接方法还是以逐个焊点来进行的方式,对焊点数量多的整个PCBA来说,其焊接速度还是不如红外线或热风回流炉等的表现。
所以目前从事大批量生产的用户不多,多用在非PCBA或有热敏感器件的焊接应用上。
由于光学的聚焦能力强,所以这技术的局部性只次于激光技术,能够焊接十分细小的焊点。
光学的非接触性焊接也是本技术优点之一。
不过相对高的焊接成本,白热光的刺眼,以及辐射加热的可能超温特性却限制了本技术的推广。
激光焊接技术:
激光焊接类似白热光焊接技术,也是属于辐射局部焊接技术。
不过在能力上较强于白热光技术。
激光技术的局部性可以达到只有25um的细小程度,对于处理微间距技术有很好的能力。
加上激光的能量控制可以很精确,重复性很高,加热速度快(较白热光快,可达每点少于0.1秒的速度)等等,使这门技术从工艺角度来说,成为最好的焊接工艺。
我在1994年曾在欧洲考察这门焊接技术。
它是我评估过最能够精确控制焊点结构,以及可以避免焊点气孔的焊接技术。
激光技术可以和贴片工艺整合在一起,在同一台设备中进行贴片和焊接。
这概念对与处理位数很少的特别器件(如高精度、热敏感、寿命要求高的器件)十分有用。
图六显示了这种整合的概念图。
在精度上,由于贴片头起着定位和控制压力的作用,这类技术可以处理非常高的组装精度,我曾见过间距小到0.15mm的(和TAB技术相当)。
我也见过前同事的一份研究报告,对于0.3mmQFP的组装成功率高达17dpmo!
(注一)
激光技术当然也有弱点。
我认为最不理想的是其工艺设置十分麻烦。
因为用户必须设置激光的能量。
而不同热特性的焊点需要不同的能量。
在工艺上我们一直都习惯用温度时间来量化,‘能量’和温度/时间的概念是较模糊的。
对于每一种封装焊点,激光技术都必须首先制定其工艺参数标准。
这就增加了前期的工作量,影响导入的速度。
而这正是牵涉到人性的弱点上,对于那些注重方便多于实际效果的用户是不会被接受的。
不过我认为,这方面的问题如果结合红外线技术,是可以给予议定程度的改善,有利于推广的。
此外,激光技术的成本十分高,研究开发的供应商少,单点焊接虽然快但整板速度仍然较慢等等。
这些也是阻碍其发展的原因。
从对激光技术的了解中,我认为这门技术应该在高质量(寿命)要求的业界中被重视和推广。
红外线焊接技术:
红外线焊接技术曾有段时间是大批量生产中回流焊接的主流技术。
原理是通过选择适当波长的红外线对焊点进行辐射加热来完成焊接工作(见图七)。
红外线之所以曾经成为技术主流,是因为它具备好些优点。
例如成本不高、有很高的稳定性、热容量和加热效率高等。
这些在回流工艺中都是重要的。
不过由于红外线属于辐射技术,它自然免不了附带辐射技术中的弱点,就是有超温的风险以及无法处理热特性差异造成的焊点间温差的问题。
这技术,如果设备(炉子)在加热效率设计上不良时,甚至会拉大焊点间的温差。
这是个很不受欢迎的弱点。
加上不同器件和材料对辐射波存在不同的吸收能力,以及高密度布局或器件本身结构可能造成的‘阴影效应’等问题,造成这技术逐渐被越来越成熟的热风技术所取代。
笔者认为,这技术事实上还可以被有效的利用在热风回流炉中。
用以取代设计困难和能力不足的前温区(一般前2到3个温区)。
但目前业界似乎还没有出现这种设计。
热风/热气焊接技术:
在大批量加工生产中,热风焊接技术是目前焊接技术的主流。
这技术是通过使用空气或惰性气体做为传热媒介来对焊点进行加热焊接(见图八)。
目前绝大部分的回流炉子都采用这门技术。
而其中最主要的原因,就是热风技术能够最好的处理焊点间温差的问题,以及它在照顾到工艺质量的同时,能提供高效率的生产而使焊接成本较低。
所以它是在质量和成本平衡上做得较好的一种技术。
不过热风温度控制和对流的设计是门复杂的技术,导致许多设备的表现事实上还不够理想。
这问题却由于业界很缺乏在设备上和焊点寿命上的测量认证做法,而没有被明显化。
我在将来有关设备的一文中会和读者分享更多这方面的经验信息。
除了以上所说的适合大批量生产的强制热风焊接技术外,热风/热气焊接技术也有在局部焊接方面的应用。
这种技术最为人熟悉的是使用在返修工作上。
其原理和热风回流炉子类似。
只是热空气或惰性气体是通过单一喷嘴来输送的(图九)。
由于只有一个喷嘴,温度/时间曲线的变化只能靠热空气温度的控制来获得。
这就要求在热空气的加热/冷却反应上必须灵敏。
设备的设计难度具有相当的挑战性。
不过热空气通道的热损失却带来了自然存在的热冲击限制或保护。
这类技术的应用,不论是手工或是半自动操作,在对流控制设计上都不太理想。
所以使用在多焊点的器件时(例如BGA)其温差控制能力较不理想。
另一方面,由于空气的流动较难控制,这类技术的局部性不如辐射技术。
在焊料方面,局部热风焊接技术可以使用锡膏或固态锡(Preform)。
电感涡流焊接技术:
这是一种通过电感效应在焊点内部产生大量涡流发热的焊接方法(见图十)。
热容量很大且加热迅速是这门技术的能力优势。
很适合于高热容量的焊点焊接。
加上其发热是源自焊点内部而非由外传入,对于一些外材料沉热很快的结构,例如焊接柔性板在金属块上,是种很好的应用。
虽然在特别情况下的应用效果很好,但电感焊接技术存在相当大的弱点,使其无法成为通用技术。
其中最严重的问题有:
1.电感头的设计很高难度;
2.位置敏感,工艺参数设置困难;
3.有较高的超热风险;
4.高频电感对一些器件可能造成破坏。
电感技术现在几乎都用在高产量高热容量的三级组装应用上。
如果有好的供应商的支持配合,也不失为一种良好的技术。
火炬焊接技术:
火炬焊接技术的应用范围很接近电感焊接技术,也是对热容量特高的焊点有效的技术。
由设备的喷嘴喷出可燃气体形成火炬,直接对焊点加热(见图十一)。
一般使用氢氧混合气体做为燃料。
这门技术的工艺质量水平和电感焊接相当,不过限制使用的条件较少也因此可应用的场合较多。
基本上只需要在设计上照顾到设备(火炬)所需要的空间就足够了。
火炬焊接也可以被使用在单流焊接上(和锡丝自动焊接类似,如图十一中所示)。
火炬技术的弱点是在设置上较慢,整体焊接速度较慢,以及易燃和需要有防火工作。
目前还只是被采用在少数特别焊接需求的场合上。
回流焊接技术的选择:
以上为读者们要点介绍了业界中使用的回流焊接技术。
其中没有单一的技术是全能的。
所以用户必须针对本身的应用需求和条件进行适当的选择。
一般来说都必须配合两种以上的技术才完整和有效益的处理问题。
这包括了配合不在本文范围内的单流焊接。
例如较常见的是配合热风回流(大批量技术和局部焊接技术)和波峰焊接回流。
在选择适当的焊接技术时,我建议考虑以下几方面的因素。
1.产品(PCBA)的基材(例如FR4,陶瓷板,柔性板等等)和特性;
2.插件和表面贴装器件的比例;
3.主要器件的封装种类和数量比例;
4.组装密度(器件间距以及布局密度);
5.单面或双面组装;
6.单一或混装(THT和SMT);
7.关键器件的焊接特性以及热敏感器件的使用情况;
8.产量/批量特性;
9.返修的量和技术要求;
10.制造成本压力。
用户必须对各种技术有一定的了解后才能做出比较准确的配搭选择。
我们该了解到的,是选择出‘能够使用的技术’,并不等于选择出‘优化的技术配搭’。
而这选择工作的质量,就有赖于选择、决策者本身心态和对相关知识的掌握了。
事实上,本区域没有多少人有对焊接技术的选择进行科学性的分析。
这是因为我们在制造技术的应用管理上还缺乏认识。
有机会的读者可以自己制定一个表格,从以上建议的十项因素对各种焊接技术进行比较分析。
而后您就可以一目了然的作出有意义的判断和选择了。
回流焊接的技术要求:
在上期的文章中我们谈了‘技术整合’的概念和重要性。
在回流焊接技术里,有关‘技术整合’的概念还是不变的。
所以回流焊接技术的要求也是来自设计(DFM)、工艺、设备和材料方面。
而他们的配搭情况就决定了最终的焊点质量水平(包括了直通率和寿命)。
我在将来对技术整合中的各课题如DFM、设备和材料等都有专题文章。
这里暂时就不细说了。
要用好回流焊接技术,原则上的要求是:
1.选择采购有足够能力的回流炉子;
2.详细和准确的制定您的工艺规范。
包括温度/时间曲线的标准和可用材料特性等等;
3.确保您或您的客户的工艺设计符合您的工艺能力;
4.按第2项的规范,找出最适合加工该产品(包括基板、器件、板上所有材料)和锡膏特性的温度和时间关系(即回流曲线),并确保PCBA上的各个焊点都满足这温度曲线;
5.设置并控制好已定的工艺参数,使正确的工艺不断的在所有PCBA上重复。
以上1和5项照顾到技术整合中的设备因素部份,2、4和5项照顾到工艺因素部份,第3项照顾到DFM因素部份,2、3和4则照顾到材料因素部份。
而在第5项中,还有需要用上质量监控的知识和手段。
所以这5个要求,事实上就是一套技术整合的概念应用。
强制热风焊接技术:
本系列文章中我将把焦点放在目前绝大部分用户使用的‘强制热风焊接技术’上。
对于这门技术在工艺原理上的较详细描述,我曾在2004年5月份也为KIC公司撰写了一篇专题文章。
这里由于篇幅问题我就不再重提。
读者可以参考该标题为“回流焊接技术的工艺要点和技术整合考虑”的文章。
后语:
在今天的SMT界中,人类经过许多年的相竞开发,已经产生出许许多多有用的技术知识。
这些技术都有它们个别的优缺点。
如何选择和应用将是个竞争成败的要素。
可惜的是,忙碌的企业技术管理人员并非都有机会去了解这些技术的特质和价值。
甚至连接触的机会都没有。
在‘技术整合管理’的理念中,一个重要的概念就是对技术进行最优的配搭。
了解越多的技术就更能发挥各种技术间互补的能力。
本文因此对各种焊接技术做了一个简介,希望能促使用户们去更好的学习、了解这些焊接技术,并较竞争对手更好的使用它们来为本身企业效劳。
SMT技术兼管理顾问
薛竞成
2006年8月
------------------------------------------------------------------------------------------------------------
注一:
这是在欧洲的一个工艺能力认证工作。
成功的因素不只在于激光焊接,而是同时舍弃了锡膏印刷工艺,改用预先电镀焊料的器件工艺。
笔者的实际经验中,如果采用传统的锡膏+热风回流技术,0.3mmQFP的工艺质量水平约在20~40万dpmo左右。
17dpmo的激光技术显然是个很大的改进。