通用桥式起重机制造过程检验记录.docx
《通用桥式起重机制造过程检验记录.docx》由会员分享,可在线阅读,更多相关《通用桥式起重机制造过程检验记录.docx(17页珍藏版)》请在冰豆网上搜索。
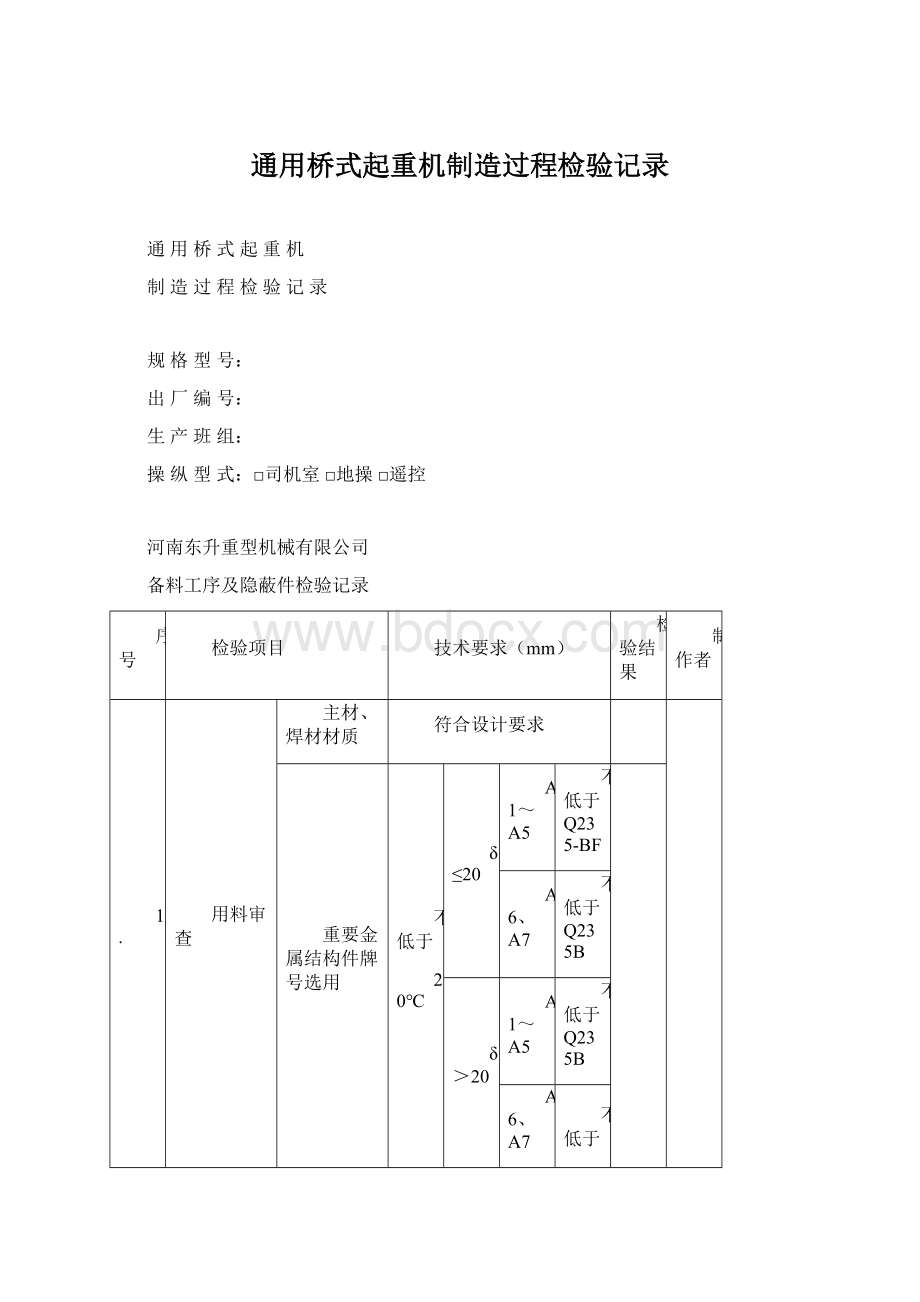
通用桥式起重机制造过程检验记录
通用桥式起重机
制造过程检验记录
规格型号:
出厂编号:
生产班组:
操纵型式:
□司机室□地操□遥控
河南东升重型机械有限公司
备料工序及隐蔽件检验记录
序号
检验项目
技术要求(mm)
检验结果
制作者
1.
用料审查
主材、焊材材质
符合设计要求
重要金属结构件牌号选用
不低于
20℃
δ≤20
A1~A5
不低于Q235-BF
A6、A7
不低于Q235B
δ>20
A1~A5
不低于Q235B
A6、A7
不低于Q235C
低于-20~25℃
δ≤20
不低于Q235D
δ>20
不低于16Mn
8.
材料标记移植
主要受力结构件材料标记移植应准确无误,并且与实际用材相符
9.
材料代用
如存在材料代用,应按规定办理代用手续
1.
焊接质量
外观质量
外观检测,焊缝不得有可见裂纹、孔穴、固体夹杂、未熔合和未焊透、形状缺陷以及上述以外的其他缺陷
2.
无损检测
1、主梁受拉区的对接焊缝应当进行100%射线或者超声检测;
2、按GB/T3323-2005,合格级别为Ⅱ级,或JB/T10559-2006按照1级焊缝合格要求进行评定。
3.
对接焊缝错位
>200,且避开跨中
4.
药皮、飞溅物
清除干净
5.
咬边、漏焊
不得漏焊,局部咬边深度≤0.3
6.
焊疤
清除干净
7.
锤击伤
≤0.5
8.
割伤
补焊磨平
9.
杂物
清除干净
10.
预处理
打磨干净去除底漆70%
11.
涂装防锈底漆
不得有漆流挂等缺陷
检验结论:
经检验合格同意转到下道工序
检验员:
年月日
主梁结构件制造工序检验记录
序号
检验项目
技术要求(mm)
检验结果
制作者
1
下盖板与腹板角焊缝
外观检测,焊缝不得有可见裂纹、孔穴、固体夹杂、未熔合和未焊透、形状缺陷以及上述以外的其他缺陷
2
上拱度F
F=(0.9/1000~1.4/1000)S
(在跨中S/10范围内)
3
主梁旁弯度f
f≤S1/2000(S1:
两端始于第一块大筋板的实测长度)
4
主梁腹板的
局部平面度
主梁腹板不应有严重不平,其局部平面度,在离受压翼缘板H/3以内不大于0.7δ,其余区域不大于1.2δ
5
上翼缘板水平偏斜
c≤B/200
6
上翼缘板平面度
δ≤10≤3
δ>10≤4
7
腹板垂直偏斜
h≤H/200
端梁结构件制造工序检验记录
1
端梁成型尺寸
B×H×W
2
水平弯曲
f=W/2000(只能向内弯)
3
腹板垂直偏斜
≤H/250
4
盖板水平倾斜
≤B/250
5
弯板到上盖板相对差
≤2
6
弯板垂直偏差
≤1.5
7
端梁扭曲
≤3(以弯板水平为准)
8
一组弯板平行差
≤2
9
一组弯板孔距差
±3(相对差3)
10
一组弯板中心线与端梁纵向中心线偏差
≤2
11
基距相对偏差
≤5
检验结论:
经检验合格同意转到下道工序
检验员:
年月日
桥架装配工序检验记录
序号
检验项目
技术要求(mm)
测量结果(mm)
1.
起重机跨度S(m)
S≤10m
±2
主动侧:
被动侧:
S>10m
±[2+0.1×(S-10)]
2.
起重机跨度的相对差|S1-S2|
5
3.
主梁上拱度F
(0.9~1.4)S/1000,且最大上拱度应控制在跨中的S/10内
主动侧:
被动侧:
4.
桥架对角线的相对差
|L1-L2|
5
5.
主梁旁弯度f
f≤S1/2000(S1:
两端始于第一块大筋板的实测长度)
主动侧:
被动侧:
6.
主梁腹板的
局部平面度
主梁腹板不应有严重不平,其局部平面度,在离受压翼缘板H/3以内不大于0.7δ,其余区域不大于1.2δ。
主动侧:
被动侧:
7.
上翼缘板水平偏斜
c≤B/200
主动侧:
被动侧:
8.
腹板垂直偏斜
h≤H/200
主动侧:
被动侧:
9.
小车轨道
小车轨道宜用接头焊为一体的整轨,否则必须满足以下五项
10.
接头高低差
≤1
11.
接头侧向错位
≤1
12.
接头间隙
≤2
13.
正轨、半偏轨箱形梁
轨道接缝应放在筋板上,允差≤15
14.
两端最短一段轨道长度
≥1.5m,并在端部加挡铁
15.
偏轨梁小车轨道中心线对承轨梁腹板中心线的位置偏移
δ≥12,g≤δ/2,
δ<12,g≤6
序号
检验项目
技术要求(mm)
测量结果(mm)
16.
小车轨距
K
极限偏差
正轨半偏轨箱形梁
跨端
±2
跨中
S≤
19.5m
+1~+5
S>
19.5m
+1~+7
其他梁
±3
20.
同一截面上
小车轨道高低差c
K≤2.0m
3
2.0m0.0015K
K>6.6m
10
21.·
小车轨道侧向直线度
每2m
≤1
S≤10m
≤6
S>10m
≤6+0.2(S-10),且最大为10
24.
车轮垂直偏斜tgα
镗孔直接装车轮时,-0.0005≤tgα≤0.0025
主左
主右
被左
被右
用角型轴承箱时,车轮端面外偏,且α≤l/400
主左
主右
被左
被右
32.
车轮水平偏斜
tgφ
镗孔装车轮
机
构
工
作
级
别
M1
≤0.0010
主左
主右
被左
被右
M2~M4
≤0.0008
M5~M7
≤0.0006
33.
用角型轴承箱
M1
L/800
主左
主右
被左
被右
M2~M5
L/1000
M6~M7
L/1200
36.
同一端梁下的
车轮同位差
两轮
≤2
三轮或
以上
≤3,
同一平衡梁上≤1
序号
检验项目
技术要求(mm)
测量结果(mm)
38.
车轮端面圆跳动
车轮直径
≤250
0.1
主左
>250~500
0.12
主右
>500~800
0.15
被左
>800~900
0.2
被右
42.
制动轮径向圆跳动
制动轮直径
≤250
0.1
>250~500
0.12
>500~800
0.15
45.
空运转试验
启动电机,做正、反运转各5min以上运转无异常
制作者:
检验结论:
经检验合格,具备出厂条件
检验员:
日期:
年月日
小车架制造工序检验记录
(图号)
序号
检验项目
技术要求(mm)
检验结果
制作者
1.
小车架梁角焊缝
外观检测,焊缝不得有可见裂纹、孔穴、固体夹杂、未熔合和未焊透、形状缺陷以及上述以外的其他缺陷
2.
小车架弯板处角焊缝
3.
各梁之间的连接焊缝
4.
固定滑轮座焊缝
5.
小车架跨度偏差
≤±2
6.
主动侧与被动侧跨度差
≤4
7.
各梁腹板的垂直偏差
H/200H-腹板高度
8.
梁的扭曲
≤2
9.
上平面的平面度
≤3/m
10.
弯板同位差
≤2
11.
弯板90°偏差
对角尺的间隙≤1.5
12.
对角线差
≤3
检验结论:
经检验合格同意转到下道工序
检验员:
日期:
年月日
小车架装配工序检验记录
(图号)
序号
检验项目
技术要求(mm)
测量结果(mm)
1.
车轮垂直偏斜tgα
镗孔直接装车轮时,-0.0005≤tgα≤0.0025
主左
主右
被左
被右
用角型轴承箱时,车轮端面外偏,且α≤l/400
主左
主右
被左
被右
9.
车轮水平偏斜
tgφ
镗孔装车轮
机构工作级
别
M1
≤0.010
主左
主右
被左
被右
M2~M4
≤0.0008
M5~M7
≤0.0006
12.
用角型轴承箱
M1
l/800
主左
主右
被左
被右
M2~M5
l/1000
M6~M6
l/1200
15.
车轮端面圆跳动
车轮直径
≤250
0.1
主左
>250~500
0.12
主右
>500~800
0.15
被左
>800~900
0.2
被右
19.
制动轮径向圆跳动
制动轮直径
≤250
0.1
>250~500
0.12
>500~800
0.15
22.
空运转试验
开动各机构做正、反运转各5min以上运转无异常
检验结论:
经检验合格,具备出厂条件
检验员:
日期:
年月日
制作者:
油漆检验记录
序号
检测项目
技术要求
检验结果
制作者
1
油漆漆膜厚度
每层漆膜厚度25~35;
漆膜总厚度75~105(GB/T14406―93.4.10.2)
2
漆膜附着力
应符合GB9286―中I级质量要求
3
涂装前钢材表面除锈等级
不低于JB/ZQ4000.10中C级,手工除锈达到
级
4
涂一次性防锈漆
符合工艺要求
5
外露的加工件表面涂青漆
6
第一次面漆
符合工艺要求
7
最后一道面漆
8
油漆外观质量
油漆干燥时间必须符合工艺要求;面漆均匀、光亮、完整和色泽一致,不得有粗糙不平、漏漆、错漆、皱纹、针孔及严重流挂等缺陷。
检验结论:
经检验合格,同意出厂
检验员:
日期:
年月日
起重机电器(气)设备配置检验记录
(图号)
序号
检验项目
技术要求
检验结果
制作者
1.
电线、电缆
符合图纸要求
2.
室内接线
符合图纸,接头牢固,导线两端与其相接的端子上有永久性线号或端子号并且正确,连接端必须用冷压铜端头连接导线。
3.
电缆敷设的弯曲半径
>5dd-电缆直径
4.
护线管及布线
护线管应牢固地固定在桥架上,管口应装有护线嘴,护线管内敷设的导线不得有接头,弯曲半径5-6D,不圆度≤0.1D
5.
电气设备前的通道
一般应大于500mm
6.
操纵件
规格、型号符合图纸,应操作灵活,档位准确,零位手感明显。
7.
起升高度限位器
按GB6067和TSGQ0002-2008的要求设置
8.
超载限制器
9.
超速保护装置
10.
应急断电开关
11.
电气设备选用
所有的电气元件、控制柜应不低于合格品,并满足起重机要求
12.
短路、失压、过压、断错相保护
起重机必须有短路、失压、过压、断错相保护。
13.
门联锁装置
按GB6067的要求设置
14.
大、小车限位器、缓冲器、止挡装置
15.
电控设备中各电路的对地绝缘电阻
一般环境≥0.8MΩ
潮湿环境≥0.4MΩ
16.
照明电源
不超过220V,用隔离变压器从主断路器前获取
检验结论:
经检验合格,同意出厂
检验员:
日期:
年月日
起重机整机检验结论:
经检验合格,同意出厂
检验员:
质检部门(章):
日期:
年月日日期:
年月日