TM自升式塔式起重机液压系统设计.docx
《TM自升式塔式起重机液压系统设计.docx》由会员分享,可在线阅读,更多相关《TM自升式塔式起重机液压系统设计.docx(42页珍藏版)》请在冰豆网上搜索。
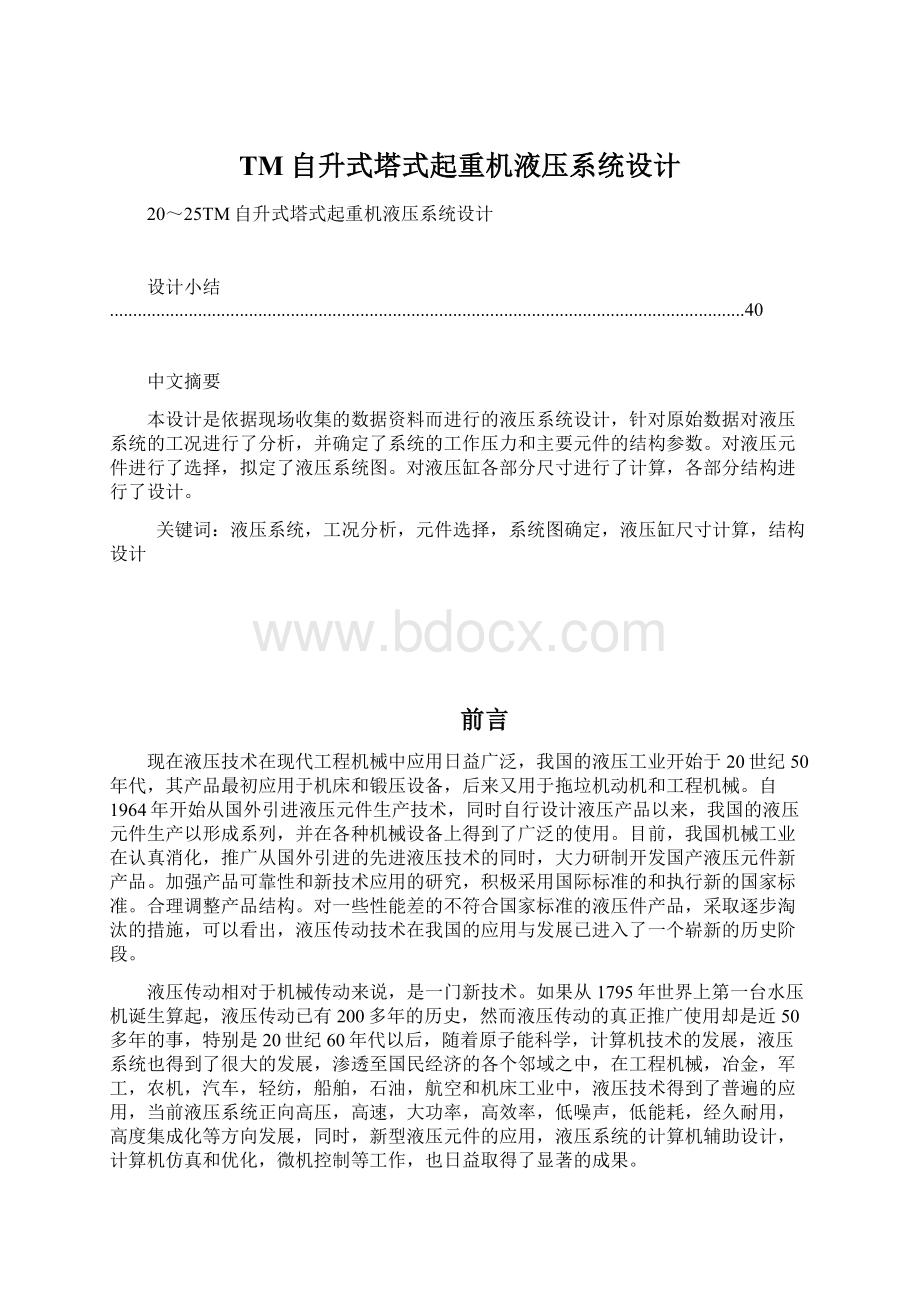
TM自升式塔式起重机液压系统设计
20~25TM自升式塔式起重机液压系统设计
设计小结.........................................................................................................................................40
中文摘要
本设计是依据现场收集的数据资料而进行的液压系统设计,针对原始数据对液压系统的工况进行了分析,并确定了系统的工作压力和主要元件的结构参数。
对液压元件进行了选择,拟定了液压系统图。
对液压缸各部分尺寸进行了计算,各部分结构进行了设计。
关键词:
液压系统,工况分析,元件选择,系统图确定,液压缸尺寸计算,结构设计
前言
现在液压技术在现代工程机械中应用日益广泛,我国的液压工业开始于20世纪50年代,其产品最初应用于机床和锻压设备,后来又用于拖垃机动机和工程机械。
自1964年开始从国外引进液压元件生产技术,同时自行设计液压产品以来,我国的液压元件生产以形成系列,并在各种机械设备上得到了广泛的使用。
目前,我国机械工业在认真消化,推广从国外引进的先进液压技术的同时,大力研制开发国产液压元件新产品。
加强产品可靠性和新技术应用的研究,积极采用国际标准的和执行新的国家标准。
合理调整产品结构。
对一些性能差的不符合国家标准的液压件产品,采取逐步淘汰的措施,可以看出,液压传动技术在我国的应用与发展已进入了一个崭新的历史阶段。
液压传动相对于机械传动来说,是一门新技术。
如果从1795年世界上第一台水压机诞生算起,液压传动已有200多年的历史,然而液压传动的真正推广使用却是近50多年的事,特别是20世纪60年代以后,随着原子能科学,计算机技术的发展,液压系统也得到了很大的发展,渗透至国民经济的各个邻域之中,在工程机械,冶金,军工,农机,汽车,轻纺,船舶,石油,航空和机床工业中,液压技术得到了普遍的应用,当前液压系统正向高压,高速,大功率,高效率,低噪声,低能耗,经久耐用,高度集成化等方向发展,同时,新型液压元件的应用,液压系统的计算机辅助设计,计算机仿真和优化,微机控制等工作,也日益取得了显著的成果。
通过对液压系统的设计,使我们对液压缸的结构,液压元件的选择,液压回路有了更深刻的理解,同时也使我们对液压系统甚至一般机械系统的设计有了初步的了解。
由于设计水平有限,在设计过程中错误在所难免,望老师指正。
第一章设计任务书
1.设计题目
20~25TM自升式塔式起重机液压系统设计
1、工作原理
在建筑施工中塔式起重机用于提升和下放重物,随着建筑物的升高,起重机的塔身逐步升高,起重机的塔身是由一节一节的塔身标准节通过螺栓连接起来的,在塔身升高接入标准节时,需要将标准节接入即起重机上部顶升起来,标准节接入并连接好后,再将顶升起来的起重机上部落下,该任务是由液压系统来完成的。
2、主要参数
顶升力:
150KN——190KN
工作行程:
1600mm
——/min
2.设计任务
1、进行设计计算,确定设计方案,内容包括:
1)确定执行元件(液压缸)的主要结构尺寸
2)绘制液压系统图
3)选择各类元件及辅助元件的型号和规格
4)确定系统的主要参数
5)设计整机布局
2、绘制设计图纸(6)张
液压系统图一张(1号图纸)
液压缸装配图一张(1号图纸)
液压站总装图一张(1号图图纸)
零件图:
液压缸缸体图(2号图纸)
液压缸活塞杆图(2号图纸)
液压缸活塞图(2号图纸)
3.设计文件
说明书:
一本(不少于1.5万字)
设计图纸6张
第二章液压缸各部分尽寸计算和结构设计
第一节:
计算液压缸的主要结构尺寸
液压缸主要设计参数如图(2—1)图a为液压缸活塞杆工作在受压状态,图b为活塞杆工作在受拉状态。
A2V1
dFW
P1P2
图(a)
V1
A1A2
d
P2P1
图(b)
图2—1液压缸主要设计参数
活塞杆受压时F=
=P1A1-P2A2
活塞杆受拉时F=
=P1A2-P2A1
式中A1=
—无杆腔活塞有效作用面积(m2)
A2=
—有杆腔活塞有效作用面积(m2)
P1—液压缸工作腔压力(Pa)
P2—液压缸回油腔压力(Pa)即背压力,其值根据
回路具体情况而定初算时可参考表2—1取值,
差动连接时另行考虑。
D—活塞直径(m)
d—活塞杆直径(m)
表2—1执行元件背压力
系统类型
背压力/MPa
简单系统或轻载节流调速系统
回油路带调速阀的系统
回油路设置有背压阀的系统
用补油泵的闭式回路
回油路较复杂的工程机械
1.2~3
回油路较短,且直接回油箱
不忽略不计
本设计方案取背压力为0.5MPa。
一般液压缸在受压状态下工作,其活塞面积为
A1=
试用上式须事先确定A1和A2的关系或是活塞杆径d与活塞直径D的关系,令杆径比φ=d/D可按表2—2、2—3选取
表2—2按工作压力选取d/D
工作压力/MPa
≤
≥
d/D
表2—3按速比要求确定d/D
V1/V2
2
d/D
本设计方案取φ
D=
=
=
=
液压缸直径D和活塞直径d的计算要按国标规定的有关标准时行圆整,如与标准液压缸参数相近,最好选用国产相当规模准液压缸,免于自行加工,常用液压缸内径及活塞杆直径见表2—4、表2—5
表2—4常用液压缸内径D(mm)
40
50
63
80
90
100
110
125
140
160
180
200
220
250
表2—5活塞杆直径d(mm)
速比
缸径
40
50
63
80
90
100
110
2
22
28
35
45
45
50
50
60
55
70
63
83
速比
缸径
125
140
160
180
200
220
250
2
70
90
8
0
100
90
110
100
125
110
140
125
140
故按表进行圆整本设计取D=160mm
d=110mm
当工作速度很低时,还必须按最低速度要求验算液压缸尺寸
A≥
式中A—液压缸有效工作面积(m2)
qmin—系统最小稳定流量(m2/S)在节流调速中取决于回路中所设调速阀的最小稳定流量,容积调速中决定于变量泵的最小稳定流量
Vmin—运动机构要求的最小工作速度(m/s)
从液压元件手册中查qmin=/min
Vmin为0.3m/min
A=
=16.7cm2
而有杆腔有效作用面积为2
无杆腔有效作用面积为2
故A<A2 <A2
满足稳定性要求
a)压杆稳定性校核
对行程与活塞杆直径比L/d>10的确受压柱塞或活塞杆,需要做压杆稳定性验算
本设计方案中L=1600mm
d=110mm
=
=14.6>10
故需做压杆稳定性校核
稳定性验算如下
λ1=
式中E为活塞杆材料的弹性模量一般取σp为材料的许用应力,查材料手册σp取280MPa
故λ1=
=86
活塞杆可简化成两端铰支杆μ =1
(一端自由,一端刚性固定μ=2、两端铰接μ=1)
截面为圆形i=
=
λ=
=
=
i为惯性半径μ是安装导向系数
由于λ<λ1
所以不能用欧拉公式计算临界压力,若用直线公式由表2—6查得优质钢的a和b分别是
a
表2—6直线公式的系数a和b
材料(δb δs的单位为MPa)
a(MPa)
B(MPa)
A3钢
δb≥372
δs=235
304
优质碳钢
δb≥ 471
δs=306
461
硅钢
δb≥510
δs=353
587
铬钼钢
9807
铸铁
强铝
373
松木
δs为材料屈服强度查材料手册δs取350MPa
λ2=
=
由上述计算可见活塞杆的柔度λ介于λ1和λ2之间(λ2≤λ≤λ1)是中性柔度压杆,由直线公式求出临界应力为
σcr=a-bλ×
临界压力是Pcr=σcrA=
(110×10-3)2××106
活塞杆的工作这安全系数为
n=
=
=
nst—安全系数一般nst—5
本设计取nst=5
n≥nst
因此活塞杆满足稳定性要求
第二节:
缸筒壁厚计算
δ=
Pmax为试验压力x,当P>16MPa时
×20=25MPa
σ是材料许用应力
[σ]=
σb为材料抗拉强度,查机械设计手册45号钢
σb=600
—5一般取5
故σ=
=120
δ==
参考表2—7
额定压力(MPa)
缸筒内径/mm
材料
40
50
63
80
100
125
140
160
180
200
缸筒外径/mm
55
65
80
97
124
铸铁
60
70
86
100
124
16
50
60
76
95
121
146
168
194
219
245
20钢
20
50
60
76
95
121
146
168
194
219
245
40钢
25
50
60
83
102
121
152
168
194
219
245
32
54
83
102
127
152
168
194
219
245
固此径圆整后取缸外径为194mm
δ=17mm
1、缸底厚度计算t(m)
一般情况下液压缸多为平底缸盖,其有效厚度t按强度要求可用下式进行近拟计算
无孔时t≥2
有孔时t≥
本设计为无孔
D2为缸底内孔孔径(m)
式中P为试验压力
图2-2
t≥×110
≥
故t取22mm
2、最小导向长度的确定
当活塞全部外伸时,从活塞支撑面中点到缸盖,滑动支承面中点的距离H称为最小导向长度,如果最小导向长度过小时将便液压缸的初始挠度(间隙引起的挠度)增大,影响液压缸的稳定性,因此设计时必须保证有一定的最小导向长度,对于一般液压缸最小导向长度H应满足以下要求
H≥
+
式中L为液压缸最大行程
D为液压缸的内径
H≥
+
=160mm
3、缸盖滑动支撑面长度确定
一般当缸筒内径D≤80mm—)D
当缸筒内径D>80mm—1.0)d其中d为活塞杆直径
×110=66mm
4、活塞密度确定
—1.0倍,但也要根据密封材料,导向环的安装沟槽尺寸来决定对长行程的液压缸为了避免负载引起的侧向力,要考虑加长活塞宽度
X160=112mm
图2-3
为保证最小导向长度H,若过他增大b和B,都是不合适的,必要时可在缸盖与活塞之间增加一隔套来增加H的值,隔套宽度由最小导向长度决定,隔套不仅能保证最小导向长主,还可以提高导向套和活塞的通用性
C=H-
(b+B)
=160-
(66+112)
=71mm
5.缸体内部长度的确定
液压缸缸体内部长度应等于活塞行程和活塞宽度,以及导向套长度之和,缸体外形长度还要考虑两端盖的厚度,一般液压缸缸体长度不应大于内径的20—30倍
即缸体内部长度为L内=1600+112+160+71
=1943mm
第三节:
液压缸结构设计
1.缸体缸的连接形式
由于要求设计的结构较为简单故采用对焊方式,如图2-4
图2-4
焊接处的拉应力为
σ=
×10-6(MPa)
式中F液压缸输出的最大推力N
F=
ΦAL2P
φAL—液压缸直径m
P—系统最大工作压力Pa
D1—液压缸外径
D2—焊缝底径m
η—
式中F即F=PA
=20MP×2
=402KN
σ=
×10-6
σ≤
查σb取600MPan取安全系数5
=
故该方案可行
活塞杆与活塞的连接有几种常见的连接方式,分整体式结构和组合式结构,组合式结构又分为螺纹连接,半环连接和锥销连接。
本设计方案采用螺纹式连接:
该连接方式加工容易应用较多,如组合机床与工程机械上的液压缸如图2—5
图2-5
活塞杆处密封圆形有O型、Y型、V型和YX型密封圆等。
为了清除活塞杆处外露部分沾附的飞尘,保证油液清洁及减少磨损,在端盖外侧增加防尘圈,常用的有无骨架防尘圈和j型橡胶防尘圈,也可用毛毡圈防尘,活塞及活塞杆处的密封圈选用、应根据密封部位使用压力,温度,运动速度的范围不同而选择不同类型的密封圈。
如图2-6,2-7
图2-6
图2-7
液压缸带动工作部件运动时,固运动的质量较大,速度高,则在到在行程终点时会产生液压冲击,甚至使活塞与缸筒端盖之间产生机械碰撞,为防止此现象发生,在行程末端,设置缓冲装置。
由于本设计方案的液压回路中使用回油调速,故在时油时,回油路上有背压,所以不会产生冲动现象,进油稳定,既在设计液压缸是缓冲装置可以省略。
5.液压缸的排气装置
对于运动速度稳定性要求较高的机床液压缸和大型液压缸,则需要设置排气装置,如排气阀等。
排气阀一般安装在液压缸两端的最高处,双作用液压缸需设两个排气阀,当液压缸需要排气时,打开相应的排气阀,空气连同油液过锥部缝隙和小孔排出缸外,直至连续排油时(不易气)就将排气阀关闭。
如图2-8
图2-8
第三章液压系统主要参数分析计算
第一节:
工况分析
通过工况分析,可以看出液压执行元件在工作过程中速度和载荷变化情况,为确定系统各执行的参数提供依据。
液压系统的主要参数是压力和流量,它们是设计液压系统,选择液压元件的主要依据。
压力决定于外载荷。
流量取决于液压执行元件的运动速度和结构尺寸。
1、液压缸载荷的组成与计算
液压缸的载荷包括三种类型
(1)工作载荷Fg
常见的工作载荷有作用于活塞杆轴线上的重力、切削力、挤压力等,这些作用力的方向与活塞运动方向相同学负,相反为正。
本设计中Fg为150~190KN本方案选fg=180KN
(2)导轨摩擦载荷Ff
由于本设计中塔式起重机的液压系统中无需导轨,故在此不做考虑,但对于机床而言
平导轨道Ff=µ〔G+Fn〕
对于V型导轨Ff=µ
式中G—运动部件所承受重力
FN—外载荷作用于导轨上的正压力
µ—摩擦系数
α—V型导轨的夹角,一般为900。
(3)惯性载荷Fa
Fa=ma=
式中g—重力加速度g=m/s2
△V—速度变化量(m/s)
△t—起动或制动时间(s)一般机械
△—s,对载低速运动部件取小值,对重载高速部件取大值,行走机械一般取△V/△—/s2
以上三种载荷之和称为液压缸的外载荷Fw
起动加速时Fw=Fg+Ff+Fa
稳态运行时Fw=Fg+Ff
减速制动时Fw=Fg+Ff-Fa
工作载荷Fa并非每阶段都存在,如该阶段没有工作,则Fg=0
除外载荷外,作用于活塞上的载荷F还包括液压缸密封处的摩擦阻力Fm。
由于各种缸口密封材质和密封形成不同,密封阻力难以精确计算,一般估算为:
Fm=(1-ηm)F
式中?
m——
F=
由于塔式起重机本身质量就很大,而液压缸所占部分质量对整体的影响不大,故在本设计中惯性载荷部分可以忽略不计。
由于无加、减速运行,本设计中
Fw=Fg取180KN
故F=
=
因为塔式起重机是液压缸的密封性能要求较高,相对而言密封阻力应取大值
本设计取η
所以F=
=
=189.5KN
第二节:
初选系统工作压力
压力的选择要根据载荷的大小和设备的类型而定,还要考虑到执行元件的装配空间,经济条件及元件供应情况的限制,在载荷一定的情况下,工作压力低,要加大执行元件的结构尺寸,对某些设备来说,尺寸要受到限制,从材料消耗角度看也不经济,反之,压力选得太高,对泵缸,阀等元件的材质,密封制造精度也要求很高,必然要提高设备成本,一般来说对于固定的尺寸不太受限制的设备,压力可以选低一些,行走机械重载设备要选得高一些,具体可以参考表3—1和3—2
表3—1按载荷选择工作压力
载荷/KN
<5
5~10
10~20
20~30
30~50
>50
工作压力
<~1
~2
~3
3~4
4~5
≥5
表3—2各种机械常用的系统工作压力
机械类型
机床
农业机械
小型机械
建筑机械
液压机
液压机
大中型挖掘机
重型机械
起重运输机械
磨床
组合机床
龙门刨床
拉床
工作压力/MPa
~2
3~5
2~8
8~10
10~18
20~30
本设计是起重机械,根据经验数据,本设计方案取工作压力为:
Pa=20MPa
第四章液压元件的选择
第一节:
液压泵工作压力的泵定
PP≥P1+∑p
式中P1—液压缸或液压马达的最大工作压力
∑△P—从液泵出口到液压马达入口之间总的管路损失,∑△P的准确计算要待执行元件选定并给出管路图时才能进行,初算时可按经验数据选取。
简单管路,流速不大的取∑△—0.5)MPa
复杂管路,进口有调速阀的取∑△—1.5)MPa
本设计方案取∑△
PP≥
1.确定液压泵的流量qp
多液压缸或液压马达同时工作时,液压泵的输出流量应为
qp≥K∑qmax
式中K——
∑qmax—×10-4m3/s
第二节:
计算液压缸或液压马达所需流量
1、液压缸工作时所需流量
q=AV
式中A—液压缸有效作用面积(m2)
V—活塞与缸体相对速度(m/s)
(1)、计算无杆腔排量
A=π/4D2=π)2=2
以V=/min即(m/s)时
q=AV
×/s
=3/s
=10L/min
以V=/min即(/s)时
q=AV
×
=3/s
=/min
(2)、计算有杆腔排量
A=
(D2-d2)
=
2-2)
=2
当V=/min即(/s)时
q=VA
×
=3/s
=/min
当V=/min即(/s)时
q=VA
×
=3/s
=3L/min
故qmax=10L/min
qp≥K(∑qmax)计算
qP≥1.2(10+0.05)
≥L/min
2、选择液压泵规格
根据上述计算得PP=20.5MPaqp=/min按系统中拟定的液压泵形式,从产品样本中选择相应的液压泵,为使液压泵有一定的压力储备,所选泵的额定压力一般要比最大工作大25%—60%
查机械设计手册稳定MCY14—1B型斜盘式轴向柱塞泵
排量为15L/min
额定压力32MPa
额定转速1500r/min
驱动功率10Kw
容积效率>92%
最高压力40MPa
3、电动机的选择
P=
式中PP—液压泵最大工作压力Pa
qp—液压泵流量m3/s
ηP—液压泵总效率见表5—1
表4—1液压泵总效率
液压泵类型
齿轮泵
螺杆泵
叶片泵
柱塞泵
总效率
—
—
—0.75
—0.85
本设计方案采用的是柱塞泵故ηP—
本方案采用ηP
P=
×
查机械设计手册选择电机YR200L1—4型
封闭绕组型三相异步电动机
转速1465r/min
效率89%
功率因数COSφ
该型电动机由于结构型式为封闭式,因此在尘土飞扬,水土飞溅的建筑工地中使用很合适
4、液压阀的选择
阀的规格根据系统的工作压力和实际通过该阀的最大流量选择有定型产品的阀件,溢流阀按液压泵最大流量选取,选择节流阀和调速阀时要考虑最小稳定流量应满足执行机构最低速度要求
控制阀的流量一般要选的比实际通过的流量大一些,必要时,也允许有20%以内的短时间过流量。
选择阀的型号见表4—2
表4—2液压阀型号规格
元件名称
型号
工作压力(MPa)
通过流量(L/min)
数量
液控单向阀
2AY—F10D—AB
40
I
三位四通阀
34SM—L10H—T
21
20
I
单向节流阀
LA—F10D—AB
40
I
溢流阀
Y2—Ha10
32
40
I
滤油器
3XU—B48×100
48
I
压力计开关
KF—L8/E
I
压力计
Y—100T
I
5、确定油管尺寸
管道内径计算
d=2
式中q通过管道的流量(m3/s)
V—管道内允许的流速(m/s)见表4—3
表4—3
管道
液压泵吸油管道
液压系统压油管道
液压系统回油管道
推荐流速
—
3—6压力高管道短,粘度大取小值
—2.6
在本设计方案中取油泵吸油管道流速为1m/s,压油管道流速为/s回油管道流速为2m/s
则进油管道直径
d=2
=2
=
查液压传动设计手册取d=20mm无缝钢管,钢管外径为28mm
油泵回油管径
d=2
=2
=
查液压传动设计手册d=15mm无缝钢管外径为22mm
油泵压油管径
d=2
=2
查液压传动设计手册取d=12无缝钢管,外径为18mm。
6、确定油箱容积
初始计算设计,先按下式确定油箱容量,待系统确定后,再按散垫要求进行校核,油箱容积的经验公式为
V=aqv
式中qv为液压泵每分钟排出动压力油的容积为m3
a经验系数
系统类型
行走机械
低压系统
中压系统
锻压机械
冶金机械
a
1—2
2—4
5—7
6—12
10
本设计方案a取12
V=aqv
=12×15×10-3m3
=180L
在确定油箱尺寸时,一方面满足系统供油需求,还要保证执行元件全部排油时,油箱不可能溢出,以及系统中最大可能充满油时,油箱的油位不能低于最低限度。
第五章拟定液压系统回路
第一节:
调速方案拟定
液压执行元件确定之后,其运动方向和运动速度的控制是拟定液压回路的核心问题,速度控制是指通过改变液压执行元件输入或输出的流量或者利用密封空间的容积变化来实现的控制方法,相应的调速方式有节流调速,容积调速以及二者结合——容积节流调速
节流调速是指靠改变定量泵供油,用流量控制阀改变输入或输出液压执行元件的流量来调节速度,此种调速方式结构简单。
而容积调速是靠改变液压泵或液压马达的排量来达到调速的目的,其优点是没有溢流损失和节流损失,效率高,但为了散热和补充泄露,需要有辅助泵,此种调速方案适用于功率大运动速度高的液压系统。
本设计本着满足控制要求,经济,结构简单可行的原则,综合考点