铝型材挤压工艺规程.docx
《铝型材挤压工艺规程.docx》由会员分享,可在线阅读,更多相关《铝型材挤压工艺规程.docx(8页珍藏版)》请在冰豆网上搜索。
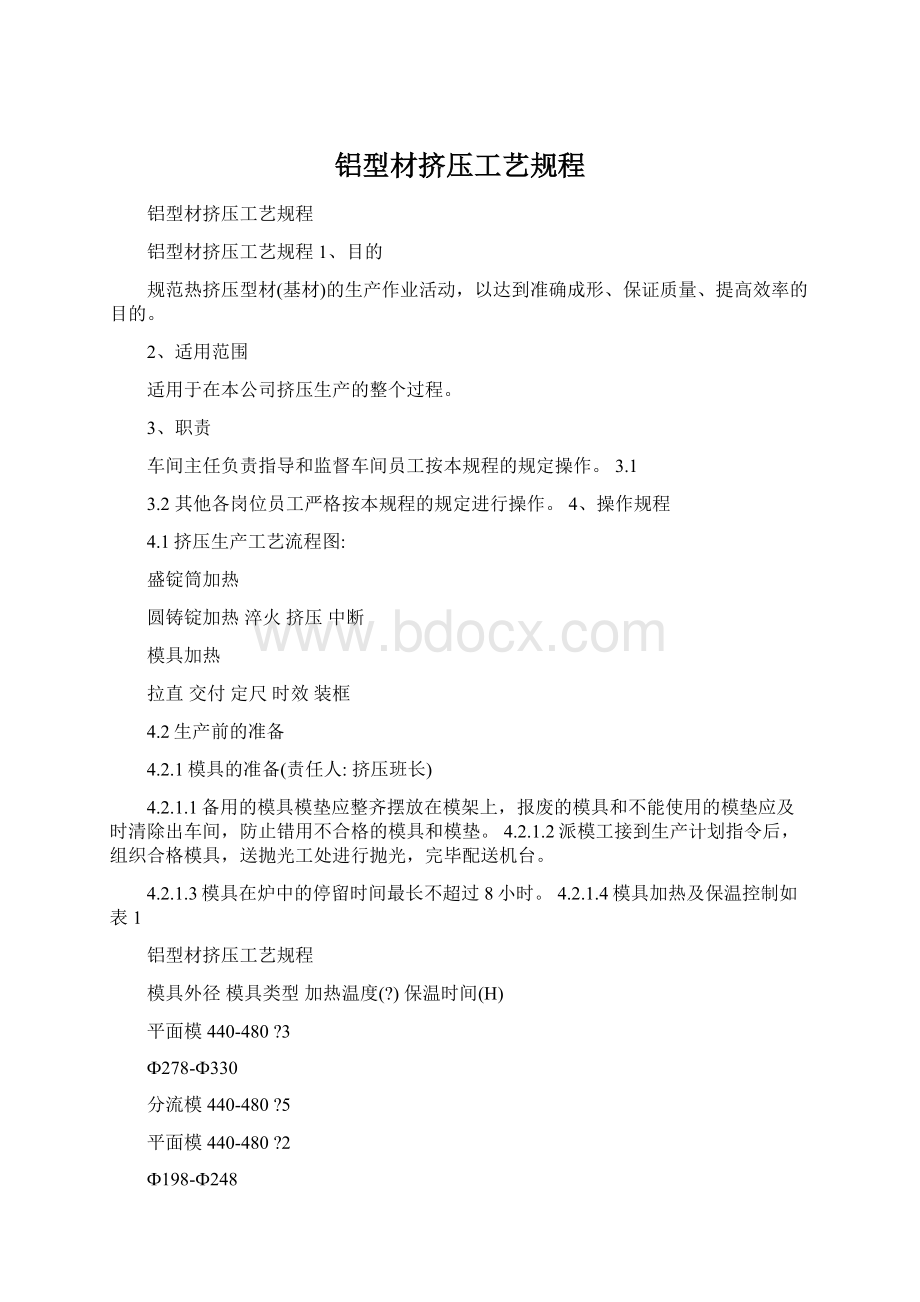
铝型材挤压工艺规程
铝型材挤压工艺规程
铝型材挤压工艺规程1、目的
规范热挤压型材(基材)的生产作业活动,以达到准确成形、保证质量、提高效率的目的。
2、适用范围
适用于在本公司挤压生产的整个过程。
3、职责
车间主任负责指导和监督车间员工按本规程的规定操作。
3.1
3.2其他各岗位员工严格按本规程的规定进行操作。
4、操作规程
4.1挤压生产工艺流程图:
盛锭筒加热
圆铸锭加热淬火挤压中断
模具加热
拉直交付定尺时效装框
4.2生产前的准备
4.2.1模具的准备(责任人:
挤压班长)
4.2.1.1备用的模具模垫应整齐摆放在模架上,报废的模具和不能使用的模垫应及时清除出车间,防止错用不合格的模具和模垫。
4.2.1.2派模工接到生产计划指令后,组织合格模具,送抛光工处进行抛光,完毕配送机台。
4.2.1.3模具在炉中的停留时间最长不超过8小时。
4.2.1.4模具加热及保温控制如表1
铝型材挤压工艺规程
模具外径模具类型加热温度(?
)保温时间(H)
平面模440-480?
3
Ф278-Ф330
分流模440-480?
5
平面模440-480?
2
Ф198-Ф248
分流模440-480?
2
平面模440-480?
1
Ф138-Ф148
分流模440-468?
2
平面模440-480?
1
Ф138
分流模440-480?
1.54.2.2盛锭筒的准备(责任人:
挤压班长)
4.2.2.1盛锭筒必须保持干净,无严重磨损或大肚,否则,挤压产品将会出现夹渣或气泡。
4.2.2.2盛锭筒与模具配合的端面应平整无损伤和粘铝,否则挤压时会跑料。
4.2.2.3盛锭筒的加热元件必须完好并有足够的加热能力。
否则,盛锭筒将无法达到工艺要求的温度。
4.2.2.4盛锭筒温度控制在380?
-430?
之间,严禁超出范围。
4.2.2.5每班上班前,应对盛锭筒进行一次清缸。
在正常挤压时,每隔20-50支锭应进行一次清缸,以确保盛锭筒内清洁干净。
4.2.2.6盛锭筒应避免急冷急热,在正常情况下,盛锭筒应在工艺要求的温度范围内长期保温,交班时不要断电。
4.2.3铝合金圆铸锭的准备(责任人:
主机手)
4.2.3.1根据排产单的要求选用相应牌号的合金,其数量由生产任务
的多少决定。
4.2.3.2各机台所使用的铝合金圆铸锭必须是有炉次编号的圆铸锭。
4.2.3.3圆铸锭在入炉加热之前,应作表面质量自检,自检由主机手
铝型材挤压工艺规程
负责,凡是有明显夹渣、冷隔、中心裂纹和弯曲的圆铸锭,
都不应入炉加热,应将其挑选出来退回熔铸车间。
4.2.3.4不允许圆铸锭在地面上滚动,凡是表面有泥沙、灰尘时,均
应清理干净后再入炉加热。
4.2.3.5出口端的燃烧器主要用作控制铸锭温度,但要靠热工仪表的
准确定温来控制燃烧器自动着火和熄火,以确保铸锭温度符
合工艺要求。
4.2.3.6加热炉的温度设定加热阶段设定300?
-450?
,铝棒上机时温
度控制,根据壁厚应符合T?
1.4mm以温度控制在440?
-540?
,T,1.4mm温度控制在400?
-540?
,具体情况根据
品种、模具结构、合金种类而定。
4.2.4其他准备:
挤压之前应将清锯口的小刀、铁钳、铁钊、卡尺、
图纸、取样用的冷却水、排产单及其他生产工具准备好。
4.3挤压(责任人:
主机手)
4.3.1在生产前应试空车,让挤压机和棚架都空载运行一次。
检查机
械电器运转是否正常,确认无任何问题后,才可正式投料挤压。
4.3.2在开机前先检查盛锭筒温度是否达到工艺要求,确认盛锭筒温
度符合工艺要求以后,再测量模具温度和铝合金铸锭温度,当
三者温度都达到工艺要求时,才好装模上机挤压。
4.3.3模具上机时,应用手提测温仪测量温度并记录在《挤压车间生产
工艺原始记录》中。
装模过程应迅速快捷,而且要防止模具冷却。
4.3.4圆铸锭上机挤压前应先测量温度,不符合温度要求的铸锭不准
上机挤压,上机的第1个铸锭最好取规定的高限温度,以防塞
模。
4.3.5铸锭加热温度的监控:
挤压过程中,挤压班长要每隔10-20个
铸锭用手提测温仪测量一次温度,并如实作好记录,以便随时
掌握铸锭温度变化情况,保持正常挤压温度。
24.3.6挤压时,要注意压力的变化。
起压时不超过210kg/cm。
正常挤
铝型材挤压工艺规程
压时,压力会随过程下降,若在起压后超过1分钟压力不下降,
则应停止挤压,以防损坏设备和模具。
4.3.7排气:
每压一个铸锭,在起压初期的墩粗阶段,当压力达到
2-160kg/cm时,应卸压放气,然后再重新起压进行正常挤压。
110
4.3.8控制好挤压速度:
要保持型材光滑平直,应使挤压过程前、中、
后挤速恒定。
各机台的挤压速度根据型材表面质量而定,在保
证表面质量符合相关的表面处理要求的前提下尽可能快。
4.3.8.1应根据不同合金的不同特性控制挤压速度,低杂质合金挤压
速度可高些,高杂质合金挤压速度会慢些。
4.3.8.2若铝棒温度偏高,应减低挤压速度,若想加大挤压速度,应
将铝棒温度控制低些。
4.3.8.3为了控制好力学性能出料口的温度最低必须?
500?
。
4.3.9首件检查:
上模挤压出来的第1支型材应将其料头切下500mm
长留给修模作依据,第1支与第2支棒切下500mm长交巡检员
作外观尺寸和形位公差检查,以确认是否符合图纸尺寸及装
配关系要求,从而判定该模具可否继续生产。
4.3.10若决定卸模后,巡检员应在料头及样板上用油性笔标明模具型
号、序号,并在样板及检验记录上注明缺陷位置。
4.3.11为了防止模具端面、盛锭筒端面和挤压垫片端面粘铝,允许
在模具端面和垫片端面上涂少量脱模油脂,但要尽量少涂或
不涂,而且不允许涂及模具型腔和盛锭筒内壁,以免油脂污
染型材。
4.3.12要正确使用挤压垫片,保护挤压垫片不被碰伤。
当挤压垫片
磨损太大,变成圆角,清缸不干净时,应及时更换新垫片。
4.3.13每次挤压时,都要特别注意垫片是否已放好,防止因挤压垫
片没放好造成设备事故。
4.3.14挤压过程中应注意液压油温度的变化:
当油温升高到约
45-50?
时,挤压力会大大下降,挤压机会变得无力,此时应
铝型材挤压工艺规程
停机并设法将油温降下来,然后才能再开机挤压。
4.3.15一套模具一次在挤够表3所列的铸锭数后,应主动卸模换上
第二套模具进行挤压。
(表4)
挤压机吨位(吨)60010001650
每套模具一次挤压铸锭数
100-15060-8040-80
(个)
4.3.16为了防止挤压死区的气体及脏物流入铝型材和为了保护挤压杆不
致破坏,限定压余长度不许过厚,也不允许过簿,压余控制
15-30mm厚度。
4.4淬火(责任人:
主机手)
4.4.16063挤压型材T6淬火采用强制风冷,T5自然冷却,型材流出
后不可小于80?
/分的速度冷却至170?
以下。
4.4.26061挤压型材淬火采用强风、水雾或直接水冷方式,并要在
2-3分钟将温度降至200?
以下。
4.4.3其他合金根据其力学性能不同而定。
4.5中断(责任人:
中断工)
4.5.1型材在正常挤压时,要做好牵引和中断工作。
中断时,应使前
段型材(驳口之前的一段型材)的长度为6米的倍数加拉直余
量。
4.5.2两次挤压间型材的驳口,不允许留在成品型材中,所以应当在
驳口处切断型材。
4.6拉直(责任人:
拉直锯切工)
4.6.1型材在冷床上要冷却到50?
以下才能进行拉直。
4.6.2等待拉直的型材,用步进方式或用输送带输送方式送到拉直机
前。
4.6.3型材拉直时,其拉直量应控制在1-2%左右,超厚型材的拉直变
铝型材挤压工艺规程
形量允许稍大一些,但不许超过3%。
4.6.4拉直前后必须查看开口尺寸,对有装配关系的型材必须做装配
试验,以便调整拉伸量。
4.6.5对形状复杂的型材,应找出与它相配的垫块协助夹料。
4.6.6对长度较长的型材,当看不清楚是否扭拧或型材易磨擦时,中
间需有人协助拉直和测量,检查拉直后型材形位尺寸是否符合
要求,以便随时调整拉直量。
4.6.7拉直时,要注意保护装饰面不被擦伤,尽可能做到以非装饰面
接触棚架输送带。
4.6.8经过拉直的型材应该无波浪、弯曲、扭拧存在,同时又要避免
由拉直所引起的收口、张口、桔皮、形位尺寸超差和不平度出
现。
4.7定尺(责任人:
拉直锯切工)
4.7.1型材的切断长度应严格按照排产单的要求执行。
4.7.2型材在定尺之前,应清楚其长度公差要求。
若客户有特殊要求
时,应按客户要求执行;若无特殊要求,长度公差一律按+15mm
控制,以倍尺交货时,总偏差为+20mm。
4.7.3校好定尺位后,切出第1支型材时验长度是否符合要求,必须
是正偏差,不许负偏差,确认无错后,开始成批定尺锯切。
4.7.4定尺时,应注意将拉直夹头部分引起型材变形的区段切除掉,然后
定尺。
4.7.5定尺之前先逐支检查型材表面质量,将有起皮、气泡、波浪、
弯曲、扭拧、划伤、碰伤、压凹等不合格部分切除掉,再定尺
成品。
4.7.6为防止型材擦伤,不要将型材叠起来锯切,型材前进时,应先
将锯台上的铝屑吹扫干净。
4.7.7锯切时,应在锯片涂油润滑,但要防止润滑油粘到铝材表面上。
4.7.8锯切后型材的锯口应垂直于轴线,锯口应无毛刺、飞边和扭歪
铝型材挤压工艺规程
变形。
为了有漂亮的锯口,应经常保持锯片的锋利,应注意清
除锯片上的积铝,当锯片不够锋利时,应及时换下来打磨锯齿
或换用新锯片。
4.7.9定尺后的型材应用压缩空气吹干净铝屑,然后装框。
4.7.10定尺后的检验(责任人:
巡检员)
4.7.10.1型材定尺后,大料逐支检查,中小料按10%的比例抽查,并
如实填写《挤压车间检验原始记录表》。
4.7.10.2检查的内容是平面度、弯曲度、扭拧度、张口、收口、表面
质量。
4.7.10.3检查合格的产品才能装框,不合格的产品可以整形合格的坯
料,用专用框装好整形,不能整形的当即报废处理。
4.7.11整形(责任人:
整形工)
4.7.11.1了解整形型材的型号、为什么要整形、是什么缺陷,并测量
确认缺陷的严重程度。
4.7.11.2了解基材的内控标准和产品图纸的要求,确认应纠正到何种
程度才能保证产品质量符合规定要求。
4.7.11.3准备好测量整形前后量值数据的量具。
4.7.11.4决定整形方法,安装能实现整形的相应滚轮和辅助器具。
4.7.11.5先试整形一支,加压应从小到大,并反复整形2-3次,确认
应使用何种滚轮和应加载多大压力才能保证型材合格。
4.7.11.6确认整形方法后,可大批进行整形。
4.8装框(责任人:
拉直锯切工)
4.8.1型材定尺并检查合格后,要两人轻轻地抬着放于料框中,小心
摆放整齐,不要互相碰撞和磨擦。
装框时应戴干净的纱手套,
手套绝对不能有油、水和其他脏物。
4.8.2装框时,长料、重料在框下层,短料、轻料在框上层。
4.8.3放完一层后,根据型材长度及其承受自重的程度,适当放4-8
支横隔条,再放第二层型材,不允许型材垂弯及叠起堆放。
铝型材挤压工艺规程
4.8.4凡是细料、纵向不能通风的实心型材,应使用带通风孔的小方
管横隔条分层隔开,以便于时效通风传热。
4.8.5最上一层型材的平面要低于料框的平面,以防叠框时压坏型材。
4.8.6装在框上的型材都应是经过自检或巡检确认是合格的产品。