MRP制造资源计划的原理与实施.docx
《MRP制造资源计划的原理与实施.docx》由会员分享,可在线阅读,更多相关《MRP制造资源计划的原理与实施.docx(26页珍藏版)》请在冰豆网上搜索。
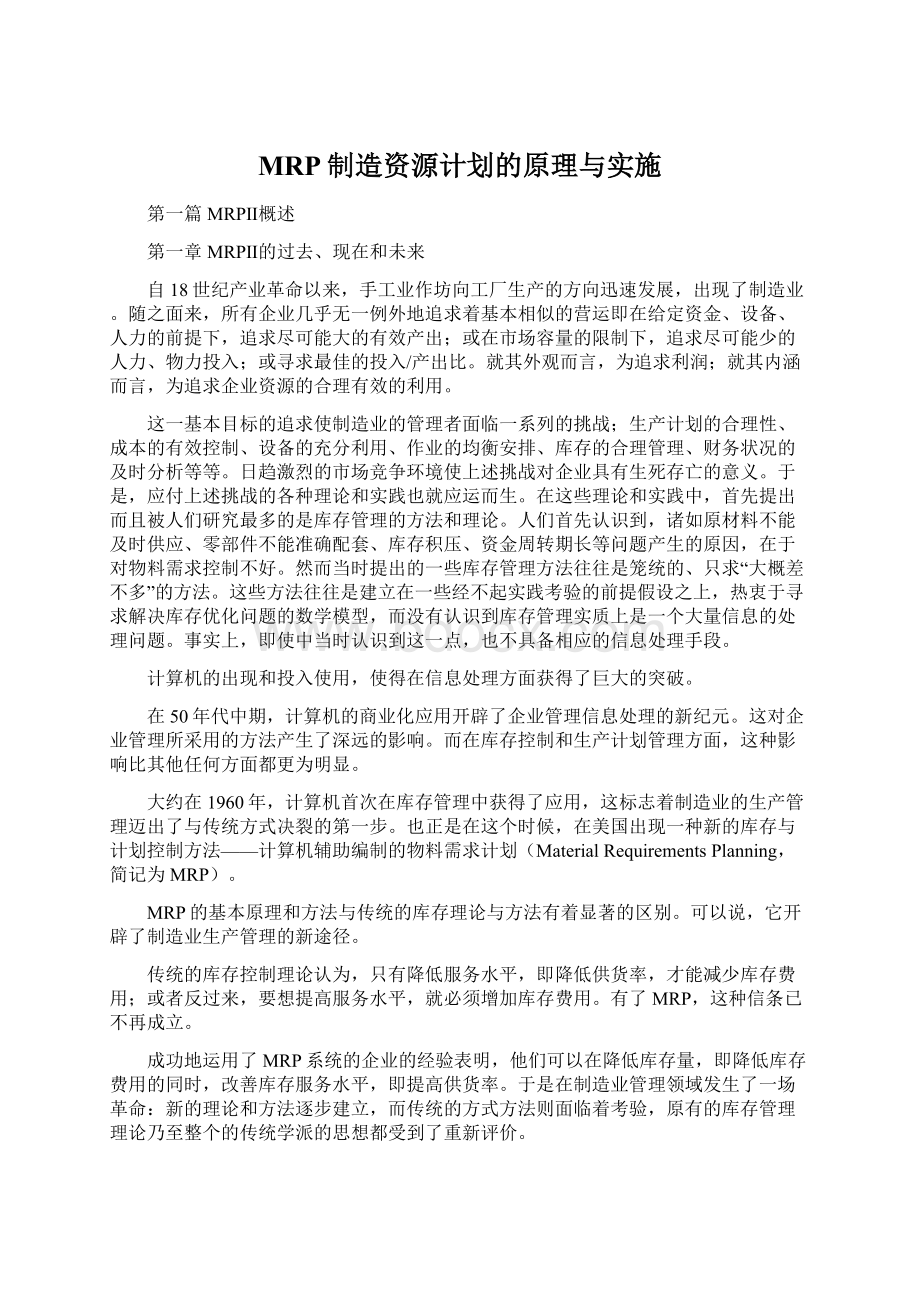
MRP制造资源计划的原理与实施
第一篇MRPⅡ概述
第一章MRPⅡ的过去、现在和未来
自18世纪产业革命以来,手工业作坊向工厂生产的方向迅速发展,出现了制造业。
随之面来,所有企业几乎无一例外地追求着基本相似的营运即在给定资金、设备、人力的前提下,追求尽可能大的有效产出;或在市场容量的限制下,追求尽可能少的人力、物力投入;或寻求最佳的投入/产出比。
就其外观而言,为追求利润;就其内涵而言,为追求企业资源的合理有效的利用。
这一基本目标的追求使制造业的管理者面临一系列的挑战;生产计划的合理性、成本的有效控制、设备的充分利用、作业的均衡安排、库存的合理管理、财务状况的及时分析等等。
日趋激烈的市场竞争环境使上述挑战对企业具有生死存亡的意义。
于是,应付上述挑战的各种理论和实践也就应运而生。
在这些理论和实践中,首先提出而且被人们研究最多的是库存管理的方法和理论。
人们首先认识到,诸如原材料不能及时供应、零部件不能准确配套、库存积压、资金周转期长等问题产生的原因,在于对物料需求控制不好。
然而当时提出的一些库存管理方法往往是笼统的、只求“大概差不多”的方法。
这些方法往往是建立在一些经不起实践考验的前提假设之上,热衷于寻求解决库存优化问题的数学模型,而没有认识到库存管理实质上是一个大量信息的处理问题。
事实上,即使中当时认识到这一点,也不具备相应的信息处理手段。
计算机的出现和投入使用,使得在信息处理方面获得了巨大的突破。
在50年代中期,计算机的商业化应用开辟了企业管理信息处理的新纪元。
这对企业管理所采用的方法产生了深远的影响。
而在库存控制和生产计划管理方面,这种影响比其他任何方面都更为明显。
大约在1960年,计算机首次在库存管理中获得了应用,这标志着制造业的生产管理迈出了与传统方式决裂的第一步。
也正是在这个时候,在美国出现一种新的库存与计划控制方法——计算机辅助编制的物料需求计划(MaterialRequirementsPlanning,简记为MRP)。
MRP的基本原理和方法与传统的库存理论与方法有着显著的区别。
可以说,它开辟了制造业生产管理的新途径。
传统的库存控制理论认为,只有降低服务水平,即降低供货率,才能减少库存费用;或者反过来,要想提高服务水平,就必须增加库存费用。
有了MRP,这种信条已不再成立。
成功地运用了MRP系统的企业的经验表明,他们可以在降低库存量,即降低库存费用的同时,改善库存服务水平,即提高供货率。
于是在制造业管理领域发生了一场革命:
新的理论和方法逐步建立,而传统的方式方法则面临着考验,原有的库存管理理论乃至整个的传统学派的思想都受到了重新评价。
初期的MRP,即物料需求计划,是以库存控制为核心的计算机辅助管理工具。
而当今的MRPⅡ,已延伸为制造资源计划(ManufacturingResourcePlanning)。
它进一步从市场预测、生产计划、物料需求、库存控制、车间控制延伸到产品销售的整个生产经营过程以及与之有关的所有财务活动中。
从而为制造业提供了科学的管理思想和处理逻辑以及有效的信息处理手段。
MRPⅡ的发展经历了四个阶段:
140年代的库存控制订货点法(OrderPoint);
260年代的时段式MRP(TimePhasedMaterialRequirementsPlanning);
370年代的闭环MRP(ClosedloopMRP);
480年代发展起来的MRPⅡ。
下面分别介绍这四个发展阶段的主要特点,然后介绍MRPⅡ的趋势。
1.1订货点法
在计算机出现之前,发出订单和进行催货是一个库存管理系统在当时所能做的一切。
库存管理系统发出生产订单和采购订单,但是确定对物料的真实需求却是靠缺料表,这种表上所列的是马上要用,但却发现没有库存的物料。
然后,派人根据缺料表进行催货。
订货点法是在当时的条件下,为改变这种被动的状况而提出的一种按过去的经验预测未来的物料需求的方法。
这种方法有各种不同的形式,但其实质都是着眼于“库存补充”的原则。
“补充”的意思是把仓库填满到某个原来的状态。
库存补充的原则是保证在任何时候仓库里都有一定数量的存货,以便需要时随时取用。
当时人们希望用这种做法来弥补由于不能确定近期内准确的必要库存储备数量和需求时间所造成的缺陷。
订货点法依靠对库存补充周期内的需求量预测,并要求保留一定的安全库存储备,以便应付需求的波动。
一旦库存储备低于预先规定的数量,即订货点,则立即进行订货来补充库存。
订货点的基本公式是:
订货点=单位时区的需求量*订货提前期+安全库存量。
如果某项物料的需求量为每周100件,提前期为6周,并保持两周的安全库存量,那么,该项物料的订货点可如下计算:
100*6+200=800
当某项物料的现有库存和已发出的订货之和低于订货点时,则必须进行新的订货,以保持足够的库存来支持新的需求。
订货点法曾引起人们广泛的关注,对它进行讨论的文献也非常多,按这种方法建立的库存模型被称为“科学的库存模型”。
然而,在实际应用中却是面目全非。
其原因在于,订货点是在某些假设之下,追求数学模型的完美。
下面,我们逐一对这些假设进行讨论。
1.对各种物料的需求是相互独立的
订货点法不考虑物料项目之间的关系,每项物料的订货点分别独立地加以确定。
因此,订货点法是面向零件的,而不是面向产品的。
但是,在制造业中有一个很重要的要求,那就是各项物料的数量必需配套,以便能装配成产品。
由于对各项物料分别独立地进行预测和订货,就会在装配时发生各项物料数量不匹配的情况。
这样,虽然单项物料的供货率提高了,但总的供货率却降低了。
因为不可能每项物料的预测都很准确,所以积累起来的误差反映在总供货率上将是相当可观的。
例如,用10个零件装配成一件产品,每个零件的供货率都是90%,而联合供货率却降到34.8%。
一件产品由20至30个零件组成的情况是常有的。
如果这些零件的库存量是根据订货点法分别确定的,那么,要想在总装配时不发生零件短缺,则只能是碰巧的事了。
应当注意,上述这种零件短缺并非由于预测精度不高而引起,而是由于这种库存管理模型本身的缺陷造成的。
2.物料需求是连续发生的
按照这种假定,必须认为需求相对均匀,库存消耗率稳定,每次发货的数量都远远小于订货总数。
而在制造业中,对产品零部件的需求恰恰是不均匀、不稳定的。
库存消耗是间断的。
这往往是由于下道工序的批量要求引起的。
我们假定最终产品是活动扳手。
零件是扳手柄。
原材料是扳手毛坯。
活动扳手不是单件生产的,当工厂接到一批订货就在仓库中取出一批相应数量的扳手柄投入批量生产。
这样一来,扳手柄的库存量就要突然减少。
有时会降到订货点以下。
这时就要立即下达扳手柄的生产指令,于是又会引起扳手毛坯的库存大幅度下降。
如果因此引起原材料库存也低于订货点,则对扳手毛坯也要进行采购订货。
由此可见,即使对最终产品的需求是连续的,由于生产过程中的批量需求,引起对零部件和原材料的需求也是不连续的。
需求不连续的现象提出了一个如何确定需求时间的问题。
订货点法是根据以往的平均消耗来间接地指出需要时间。
但是对于不连续的非独立需求来说,这种平均消耗率的概念是毫无意义的。
事实上,采用订货点法的系统下达订货的时间常常偏早,在实际需求发生之前就有大批存货放在库里造成积压。
而另一方面,却又会由于需求不均衡和库存管理模型本身的缺陷造成库存短缺。
3.提前期是已知的和固定的
这是订货点法所作的最重要的假设。
但在现实世界中,情况并非如此。
对一项指定了六周提前期的物料,其实际的提前期可以在48小时至三个月的范围内变化。
把如此大的时间范围浓缩成一个数字,用来作为提前期已知和不变的表示,显然是不合理的。
4.库存消耗之后,应被重新填满
按着这种假定,当物料库存量低于订货点时,则必须发出订货,以重新填满库存。
但如果需求是间断的,那么这样做非但没有必要,而且也不合理。
因为很可能因此而造成库存积压。
例如,某种产品一个年中可以得到客户的两次订货,那么制造此种产品所需的钢材则不必因库存量低于订货点而立即重新填满。
5.“何时订货”是一个大问题
“何时订货”被认为是库存管理的一个大问题。
这并不奇怪,因为库存管理正是订货并催货这一过程的自然产物。
然而真正重要的问题却是“何时需要物料?
”当这个问题解决以后,“何时订货”的问题也就迎刃而解了。
订货点法通过触发订货点来确定订货时间,再通过提前期来确定需求日期,其实是本末倒置的。
从以上讨论可以看出,订货点库存模型是围绕一些不成立的假设建立起来的。
今天看来,订货点法作为一个库存模型是那个时代的理论错误。
因此不再有实用价值。
但它提出了许多在新的条件下应当解决的问题,从而引发了MRP的出现。
1.2时段式MRP
时段式MRP是在解决订货点法的缺陷的基础上发展起来的,亦称为基本MRP,或简称MRP。
1.2.1MRP与订货点法的主要区别
MRP与订货点法的主要区别有两点。
一是将物料需求区分为独立需求和非独立需求并分别加以处理,二是对库存状态数据引入了时间分段的概念。
如前所述,传统的库存管理方法是彼此孤立地推测每项物料的需求量,而不考虑它们之间的关系。
而MRP则把所有物料分为独立需求项和非独立需求项,并分别加以处理。
如果某项物料的需求量不依赖于企业内其它物料的需求量而独立存在,则称为独立需求项,如果某项物料的需求量可由企业内其它物料的需求量来确定,则称为非独立需求项或相关需求项。
如原材料、零件、组件等都是非独立需求项,而最终产品则是独立需求项。
独立需求项的需求是在主生产计划(MasterProductionSchedule,简记为MPS)中考虑的(主生产计划是MRP的第一个前提条件),其需求量和需求时间通常由预测和客户订单、厂际订单等外在因素来决定。
而构成最终产品的所有下属项(即非独立需求项)的需求数量和时间则由MRP系统来决定。
所谓时间分段,就是给库存状态数据加上时间坐标,亦即按具体的日期或计划时区记录和存储库存状态数据。
在传统的库存管理中,库存状态的记录是没有时间坐标的。
记录的内容通常只包含库存量和已订货量。
当这两个量之和由于库存消耗而小于最低库存点的数值时,便是重新组织进货的时间。
因此,在这种记录中,时间的概念是以间接的方式表达的。
直到1950年前后,这种落后的方法才有了一些改进,在库存状态记录中增加了两个数据项:
需求量和可供货量。
其中,需求量是指当前已知的需求量,而可供货量是指供未来的需求量。
这样库存状态记录由四个数据组成,它们之间的关系可用下式表达:
库存量+已订货量—需求量=可供货量。
例如:
某项物料的状态数据如下:
库存量:
30;已订货量:
25;需求量:
65;可供货量:
一10。
其中,需求量可能是直接由客户订单决定的,也可能是来自市场预测,还可能是作为非独立需求推算出来的。
当可供货量是负数时,就意味着库存储备不足,需要再组织订货。
这样一个经过改进的库存系统可以更好地回答订什么货和订多少货的问题,但却不能回答何时订货的问题。
表面上看,当可供货量是负值时即是订货时间,似乎已经回答了这个问题。
其实不然。
已发出的订货何时到货?
是一次到达?
还是分批到达?
什么时候才是对这批订货的需求实际发生的时间?
该需求是应一次满足还是分期满足?
什么时候库存会用完?
什么时候应完成库存补充订货?
什么时候应该发出订货?
对于这一系列的问题,50年代的库存管理系统是回答不出来的。
当时,库存计划员只能凭经验来作出决定。
时间分段法使所有的库存状态数据以周为单位给出时间坐标,则可能是下面的样子:
库存量:
30301010-2500000已订货量:
00002500000
需求量:
0200350000010可供货量:
301010-250000010
现在,我们便可以回答前面所提出的各个与时间有关的问题了。
从记录中看到,这里有一批已发出的订货,总计25件,将在第五周到货;在第二周、第四