木塑挤出机机头设计大学论文.docx
《木塑挤出机机头设计大学论文.docx》由会员分享,可在线阅读,更多相关《木塑挤出机机头设计大学论文.docx(29页珍藏版)》请在冰豆网上搜索。
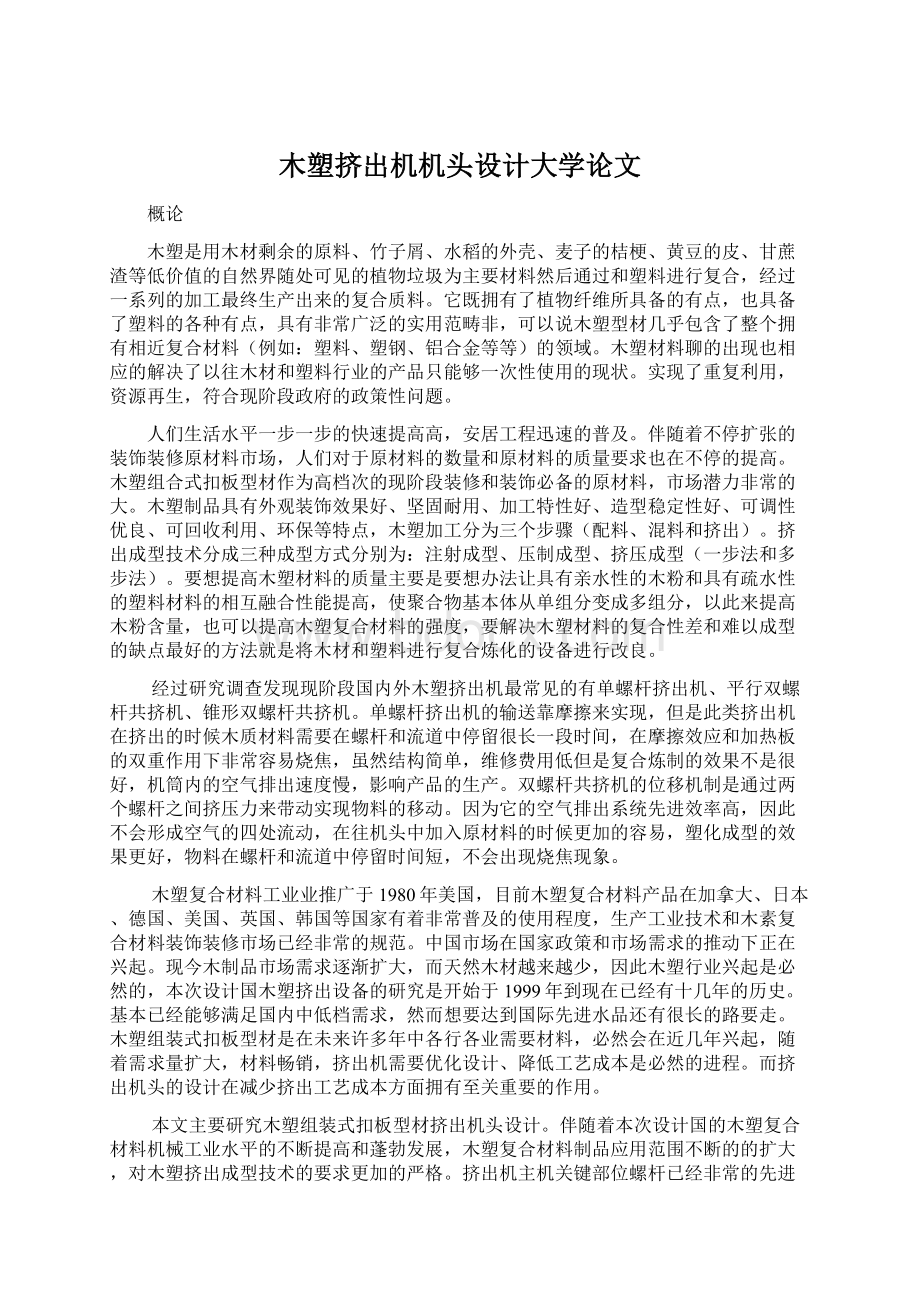
木塑挤出机机头设计大学论文
概论
木塑是用木材剩余的原料、竹子屑、水稻的外壳、麦子的桔梗、黄豆的皮、甘蔗渣等低价值的自然界随处可见的植物垃圾为主要材料然后通过和塑料进行复合,经过一系列的加工最终生产出来的复合质料。
它既拥有了植物纤维所具备的有点,也具备了塑料的各种有点,具有非常广泛的实用范畴非,可以说木塑型材几乎包含了整个拥有相近复合材料(例如:
塑料、塑钢、铝合金等等)的领域。
木塑材料聊的出现也相应的解决了以往木材和塑料行业的产品只能够一次性使用的现状。
实现了重复利用,资源再生,符合现阶段政府的政策性问题。
人们生活水平一步一步的快速提高高,安居工程迅速的普及。
伴随着不停扩张的装饰装修原材料市场,人们对于原材料的数量和原材料的质量要求也在不停的提高。
木塑组合式扣板型材作为高档次的现阶段装修和装饰必备的原材料,市场潜力非常的大。
木塑制品具有外观装饰效果好、坚固耐用、加工特性好、造型稳定性好、可调性优良、可回收利用、环保等特点,木塑加工分为三个步骤(配料、混料和挤出)。
挤出成型技术分成三种成型方式分别为:
注射成型、压制成型、挤压成型(一步法和多步法)。
要想提高木塑材料的质量主要是要想办法让具有亲水性的木粉和具有疏水性的塑料材料的相互融合性能提高,使聚合物基本体从单组分变成多组分,以此来提高木粉含量,也可以提高木塑复合材料的强度,要解决木塑材料的复合性差和难以成型的缺点最好的方法就是将木材和塑料进行复合炼化的设备进行改良。
经过研究调查发现现阶段国内外木塑挤出机最常见的有单螺杆挤出机、平行双螺杆共挤机、锥形双螺杆共挤机。
单螺杆挤出机的输送靠摩擦来实现,但是此类挤出机在挤出的时候木质材料需要在螺杆和流道中停留很长一段时间,在摩擦效应和加热板的双重作用下非常容易烧焦,虽然结构简单,维修费用低但是复合炼制的效果不是很好,机筒内的空气排出速度慢,影响产品的生产。
双螺杆共挤机的位移机制是通过两个螺杆之间挤压力来带动实现物料的移动。
因为它的空气排出系统先进效率高,因此不会形成空气的四处流动,在往机头中加入原材料的时候更加的容易,塑化成型的效果更好,物料在螺杆和流道中停留时间短,不会出现烧焦现象。
木塑复合材料工业业推广于1980年美国,目前木塑复合材料产品在加拿大、日本、德国、美国、英国、韩国等国家有着非常普及的使用程度,生产工业技术和木素复合材料装饰装修市场已经非常的规范。
中国市场在国家政策和市场需求的推动下正在兴起。
现今木制品市场需求逐渐扩大,而天然木材越来越少,因此木塑行业兴起是必然的,本次设计国木塑挤出设备的研究是开始于1999年到现在已经有十几年的历史。
基本已经能够满足国内中低档需求,然而想要达到国际先进水品还有很长的路要走。
木塑组装式扣板型材是在未来许多年中各行各业需要材料,必然会在近几年兴起,随着需求量扩大,材料畅销,挤出机需要优化设计、降低工艺成本是必然的进程。
而挤出机头的设计在减少挤出工艺成本方面拥有至关重要的作用。
本文主要研究木塑组装式扣板型材挤出机头设计。
伴随着本次设计国的木塑复合材料机械工业水平的不断提高和蓬勃发展,木塑复合材料制品应用范围不断的的扩大,对木塑挤出成型技术的要求更加的严格。
挤出机主机关键部位螺杆已经非常的先进,温度调节控制系统也已经基本完善。
但是挤出模的结构仍然没有得到快速发展,结构设计仍需优化。
本文的主要设计任务是对挤出机机头的各个部分零件的工作面的尺寸、外型的尺寸和整体的构造进行优化。
1木塑复合材料的国内外发展概况
1.1木塑复合材料
木塑复合材料的生产起源于1900年的欧洲,在传入北美洲之后渐渐的发展起来。
1916年罗斯公司将木塑复合材料应用于变速器的控制手柄从而开拓了市场,从那以后的几十年各种大小型工厂总是使用热固性塑料黏结植物材料并以此来生产制造木塑复合材料。
1960年以后一般使用乙烯基单体或含有碳碳双键的预聚物来浸泡和注射实体的木材以此来达到木材的预处理,在此之后用具有很高能量的各种射线或自由基激发剂来激发聚合物,用来制造高机能的木塑复合材料。
1980年以后日本、印度、美国等国家致力于研究塑料填充改性技术,但是收效不大。
到1990年以后采用热塑性材料为木塑复合材料的原材料,用来制造托盘和包装盒等产品。
日本EIN株式会社在2001年研究出了更加优良性能的木塑板才用于制造墙板和门窗等家具产品。
欧洲各国则研发了用挤出、注射和压延等方法来制造各种各样的木塑复合材料。
国内对木塑复合材料的研发和制造起始于20世纪90年代,经过不懈的努力终于大功告成研发出包装盒、木塑复合材料宽幅版材和多种多样的镂空型材产品。
从21世纪初到现在本次设计国和木塑复合材料研发方面有关的各种期刊、书籍和文献资料公开发表的大约有200篇左右,专利80多项,发展非常迅速,但是大部分研究成果还没有在实际生产中应用。
现今木塑复合材料产品销量位居世界第二,是仅次于北美地区的第二木塑复合材料生产基地,发展态势良好,发展前景广阔。
据估计中国木塑材料的市场状况每年的增长情况都会超过去年的30%。
在本次设计国各个科研机构和各大木塑企业的努力下,新产品开发迅速木塑复合材料的微发泡成型技术就是现阶段研究的热点。
经过微孔发泡的原料,发出的泡孔的尺寸和密度比起以前经过发泡的发泡材料是远远小于的。
小气泡能更好的防止原料在发泡过程中产生的裂缝的扩张,通过使裂缝的比较尖锐的一端变钝从而让材料的韧性、冲击的强度等各方面的机能提高,泡孔的存在可以使材料的密度减小,利于搬运,提高产品的使用性能。
在各大企业中生产制造木塑复合材料板材主要使用挤出成型、热压成型和注射成型这3种方法。
其中挤出成型又分为一步法和两步法。
目前国内的大部分公司都使用两步法进行木塑复合材料的生产。
从21世纪初到现在隶属于北京化工大学的特种挤出技术研究中心一直致力于新型一步法木塑复合材料挤出成形技术的研发,而且已经完成,具备了一整套的生产工艺规程。
热压成型技术适合用于具有高含量木材纤维(大约70%左右)的木塑复合材料制造。
热压成型工艺是将木制的纤维原料在20摄氏度左右的温度下进行充分的搅拌复合之后,再对其进行加热加压形成木塑复合材料的生产过程。
和其它成型技术相比较,热压成型技术的优点是能够使用不同形态下的木质纤维原料和塑料复合在一起加工生产出完整的型材。
但是很少有企业用热压成型技术来生产木塑复合型材,因此和挤出成型技术相比较热压成型技术的研究要少很多。
目前本次设计国的木塑产业正在向模块化、大型化、高效化、精密化、专业化、电子化、网络化、多功能化方向发展。
木塑复合材料有以下特点
1.抗弯曲性能强:
国标要求地板载荷≥2500N,而现阶段大部分木塑复合材料的载荷介于3500~6800N,是国标要求的3倍多。
因为在木塑复合材料当中加入了塑料,从而木塑复合材料具有良好的弹性模量,由于其中木质纤维和塑料完全复合在一起从而具备良好的抗压、抗弯曲的能力。
比普通木质材料更加耐用以及拥有更高的强度。
2.具有良好的加工性能:
木塑复合材料是由木质纤维和塑料复合制造而成,与木料的加工特性相似易于加工并且机械性能比木质原料更加优良。
3.具有优良的可调整性能:
在添加的助剂的作用下原料中的塑料产生了发泡、聚合、改性、固化等等的一系列的变化,并且以此来达成了对木塑复合材料的强度和硬度的改变。
还具备了防静电、抗老化、阻止燃烧等其它优良的性能。
4.具有耐水、耐腐性能:
木塑材料因为加入了塑料因而与木质材料相比耐水耐腐蚀性能有了显著提高,并且虫子不喜欢减少了虫蛀的烦恼,没有细菌的繁殖。
所以使用寿命更长了。
5.具备光稳定性,在染色的时候能够很好的着色,染上的颜色不易脱落。
6.变废为宝材料来源广泛:
其最大优点便是使用的原材料比较廉价,来源广泛,而且可以实现100%回收再使用。
它最重要的原材料是聚乙烯或者聚丙烯和木头粉末、玉米秸秆、水稻的外壳或木纤维等常见材料以及少许添加剂。
可以自己分解,不会在环境污染越来越严重的今天进一步加重对于环境的破坏,给能够减轻政府处理垃圾的负担,是真正的绿色环保产品。
7.形状尺寸随心所欲:
能够随自己的心意来设计制造共挤机头中的型芯和口模,加工自己需要的形状尺寸。
使适用范围更加广阔。
木塑型材的主要用途是在资源越来越短缺的今天尽量减少资源的浪费减少环境破坏及污染,用合成的“木”来代替天然形成的木。
木塑复合材料因为这些作用又被称为“生态木”和“环保木”。
现今全球的木材资源短缺,让木塑复合材料有了巨大的市场。
目前使用频率比较高的木塑复合材料产品大概有以下几种:
装饰类、包装类、结构类和特型类等。
从原材料的特性方面看,木塑复合材料的适用范围似乎可以完全覆盖了像塑料、原木、铝合金、塑钢这种类型的复合材料现在的所能够使用范畴,可以对它们进行替代。
而且已经在向其它行业进军,抢占市场,发展势头凶猛,不可遏制。
同时因为木塑材料具有环保等特性符合可持续发展的方针政策,因此会得到政府的大力支持和推广。
1.2挤出机
挤出机分为很多种,比如:
单螺杆共挤机,双螺杆共挤机、联合共挤机、多螺杆共挤机。
图1-1单螺杆共挤机
Figure1-1Singlescrewco-extruder
最早的单螺杆共挤机是三段式的螺杆,根据添加塑料的类型(结晶型与非结晶型)分为渐变型与突变型螺杆。
单螺杆挤出机的物料运送靠的是摩擦力和剪切力来完成的,但因为摩擦和粘度的影响木材的粉末在螺杆及流道停留时间过长容易烧焦。
虽然混炼效果不好排气效果差,但是它更换螺杆简单,制造安装容易,造价比较低,维修费用低。
随着科学的发展和复合材料的不断更新,螺杆也在不断的推陈出新现在已经拥有200多种新型螺杆具有代表性的有:
分流型螺杆、沟槽型螺杆、分离型螺杆、变流道螺杆、屏障型螺杆剪切锥螺杆、排气型螺杆、分段螺杆和空心螺杆等。
伴随着这些螺杆的现世,单螺杆挤出机的生产率大幅度提高,向着高效率、专业化方向不断的发展。
图1-2双螺杆共挤机
Figure1-2Twin-screwextruder
因为单螺杆挤出机的种种不便以及添加剂、填充剂的增多双螺杆共挤机也在迅速的发展。
因为单螺杆生产一定数量的产品所产生的消耗比双螺杆生产相同数量的产品所产生的消耗要高很多,这也促使人们加大了对双螺杆共挤机的研发力度。
单螺杆的消耗比双螺杆的大是因为单螺杆将计量段的啰槽做的比较浅,以此来防止因为挤出机机头的压力形成的物料反向流动。
这个反向流动的压力和啰槽的深度的立方成正相关。
就是因为啰槽设计的浅了,才会在挤出的时候将更多的机械能转变成热能输送进熔融状物料中去。
所以单螺杆挤出机同产量的消耗比双螺杆的高。
也就是说,单螺杆挤出机的效率比双螺杆共挤机的低。
双螺杆还有一个比单螺杆优秀的地方是他能够“自己清洁”,因为双螺杆的两根螺杆是相互咬合在一起的,他们的这种咬合可以有效的防止机筒内无物料区域的物料的滞留。
这样就能够很好的阻止了物料在机筒内停留过长时间防止烧焦和氧化。
由于双螺杆共挤机中原料的接触面积大,所以能够有效的将从外部吸收的热量进行会转化,而且不会产生过热现象将物料烧焦。
现阶段国内外各大企业使用的的双螺杆共挤机大概分为以下几种:
按照旋转方向分为异向旋转和同向旋转;按照啮合程度可以分为啮合型和非啮合型;按照轴线方向可以分为平等的和锥形的;按照转速可以分为高速的和低速的;按照结构可以分为整体式的和组合式的[1]。
双螺杆共挤机是靠螺杆之间的咬合来运送原材料所以没有物料会因为挤出机的压力而回流往机筒中加入材料的时候更加方便,机筒中空气排出效果好,塑化效果强,材料停留时间短不会出现烧焦的现象。
虽然双螺杆共挤机具有很多的优点,但是仍然有着很多难以攻克的难题,比如所在对复合原材料进行切割让其形成粒状材料的时候,异型材的口模就会因为强大的反向压力而让物料承受的剪应力增加。
这种情况会造成机器过热,为了避免这种个情况只能降低机器工作时候的转速。
但是这样效率会很低,影响生产。
联合型挤出机中的双节挤出机很好的解决了这个问题,它分为混炼和挤出两个部分第一部分只用于对原材料的复合炼制,在复合炼制之后