煤化工钢结构安装施工方案.docx
《煤化工钢结构安装施工方案.docx》由会员分享,可在线阅读,更多相关《煤化工钢结构安装施工方案.docx(34页珍藏版)》请在冰豆网上搜索。
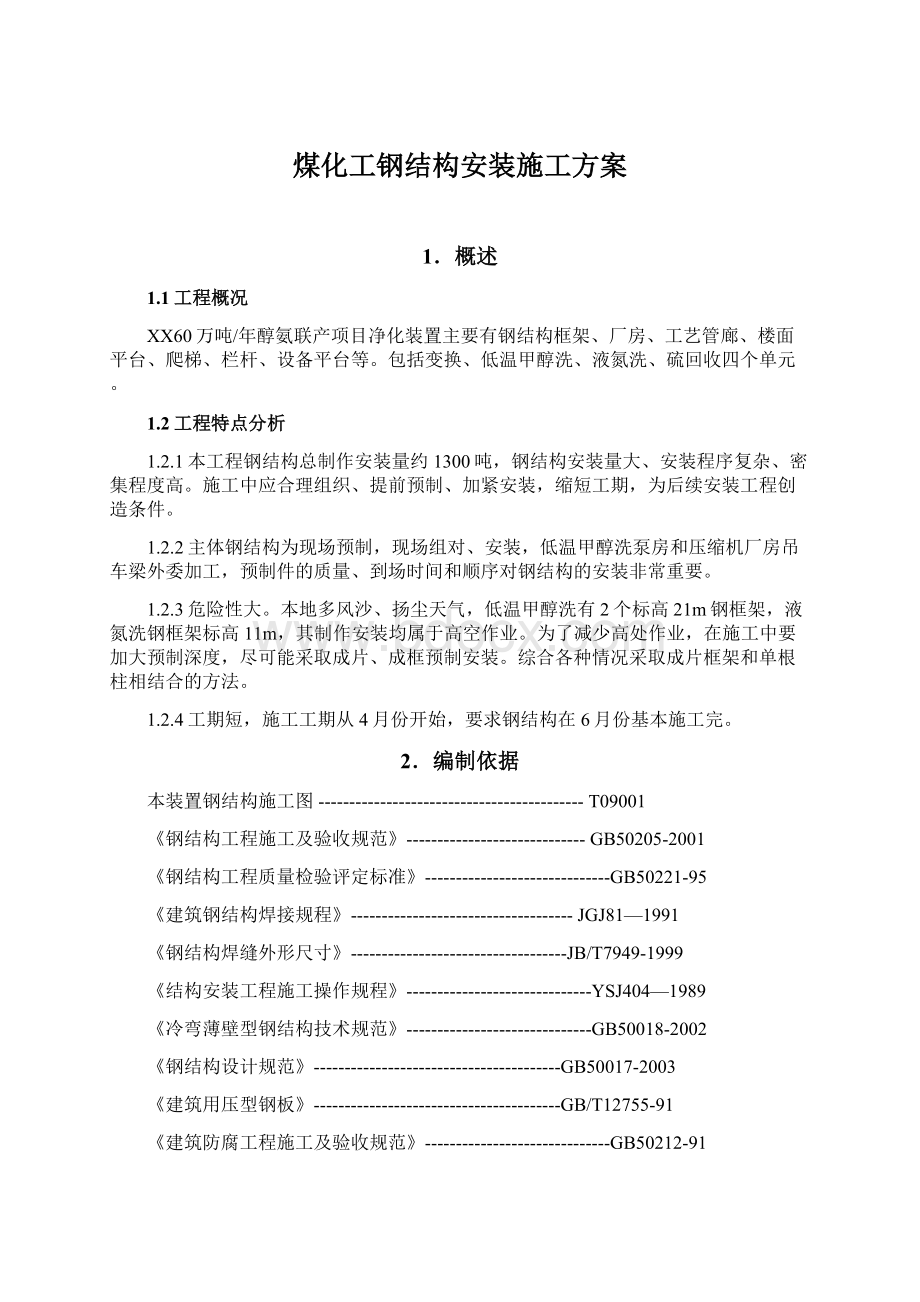
煤化工钢结构安装施工方案
1.概述
1.1工程概况
XX60万吨/年醇氨联产项目净化装置主要有钢结构框架、厂房、工艺管廊、楼面平台、爬梯、栏杆、设备平台等。
包括变换、低温甲醇洗、液氮洗、硫回收四个单元。
1.2工程特点分析
1.2.1本工程钢结构总制作安装量约1300吨,钢结构安装量大、安装程序复杂、密集程度高。
施工中应合理组织、提前预制、加紧安装,缩短工期,为后续安装工程创造条件。
1.2.2主体钢结构为现场预制,现场组对、安装,低温甲醇洗泵房和压缩机厂房吊车梁外委加工,预制件的质量、到场时间和顺序对钢结构的安装非常重要。
1.2.3危险性大。
本地多风沙、扬尘天气,低温甲醇洗有2个标高21m钢框架,液氮洗钢框架标高11m,其制作安装均属于高空作业。
为了减少高处作业,在施工中要加大预制深度,尽可能采取成片、成框预制安装。
综合各种情况采取成片框架和单根柱相结合的方法。
1.2.4工期短,施工工期从4月份开始,要求钢结构在6月份基本施工完。
2.编制依据
本装置钢结构施工图-------------------------------------------T09001
《钢结构工程施工及验收规范》-----------------------------GB50205-2001
《钢结构工程质量检验评定标准》------------------------------GB50221-95
《建筑钢结构焊接规程》------------------------------------JGJ81—1991
《钢结构焊缝外形尺寸》-----------------------------------JB/T7949-1999
《结构安装工程施工操作规程》------------------------------YSJ404—1989
《冷弯薄壁型钢结构技术规范》------------------------------GB50018-2002
《钢结构设计规范》----------------------------------------GB50017-2003
《建筑用压型钢板》----------------------------------------GB/T12755-91
《建筑防腐工程施工及验收规范》------------------------------GB50212-91
3.钢结构施工工艺
3.1钢结构施工工序流程图
3.2施工准备
3.2.1技术准备
a)施工图纸已经会审;
b)施工方案已经编制;
c)对班组进行技术交底。
3.2.2现场准备
a)现场道路已经畅通;
b)现场预制场地已经准备就绪,包括钢平台搭设、机具布置、堆放场地等;
c)施工用的工器具已备齐。
3.3材料的检验
材料进货、检验程序要按公司的质量保证体系文件运行。
对于钢结构框架中所使用的材料应满足如下要求:
3.3.1所有钢材应具有质量证明书,并应符合设计的要求。
当对钢材的质量有疑义时,应按国家现行有关标准的规定进行抽样检验。
3.3.2钢材表面质量除应符合国家现行有关标准的规定外,尚应符合如下规定:
a)当钢材表面有锈蚀、麻点或划痕等缺陷时,其深度不得大于该钢材厚度负偏差的1/2;
b)钢材表面锈蚀等级应符合现行国家标准《涂装前钢材表面锈蚀等级和除锈等级》规定的A、B、C级。
如锈蚀达到D级,不得用作结构材料。
3.3.3钢结构所采用的连接和涂装材料,应具有出厂质量证明书,并应符合设计要求。
3.3.4对于不合格的材料应坚持退货处理,不能投入使用。
3.3.5合理堆放:
钢结构材料用量大,规格多,应分类堆放整齐,并作明显标记。
3.3.6材料发放:
坚持领料的有关制度,班组不能随便取拿,以防用错。
3.3.7材料如有代用,材料部门应提出书面要求,报业主材料主管部门、设计单位和监理单位审核同意后方可执行。
4钢结构的制作
4.1放样、号料
4.1.1放样和号料应根据工艺要求预留制作和安装时的焊接收缩余量及切割加工余量。
4.1.2放样和样板(样杆)的允许偏差应符下表的规定。
放样和样板(样杆)的允许偏差
项目
允许偏差(mm)
平行线距离和分段尺寸
±0.5mm
对角线差
1.0mm
宽度、长度
±0.5mm
孔距
±0.5mm
加工样板的角度
±20mm
4.1.3号料的允许偏差应符合下表规定。
号料的允许偏差
项目
允许偏差
零件外形尺寸
±1.0mm
孔距
±0.5mm
4.2下料方法
4.2.1切割前应将钢材切割区域表面的铁锈、污物等清除干净,切割后应清除熔渣、毛刺和飞溅物。
切割的允许偏差应符合下表的规定。
切割的允许偏差(mm)
项目
允许偏差
零件宽度、长度
±2.0mm
局部缺口深度
1.0
4.2.2被切割的钢材应校平垫稳,割缝下面应留有足够的空隙。
当采用自动或半自动切割时,其轨道应经机械加工,采用手工切割时应使用滑轮和靠尺。
(附气体切割预留割口宽度2mm)
气体切割预留割口宽度(mm)
板厚
6-9
10-20
22-30
32-40
42-60
预留宽度
2
3
4
5
6
4.2.3当切割长度大于1500mm宽度小于400mm时,宜采用跳割法,跳割段与段间的间距和两端宜留出200mm,待退热后再将所留部分割断,也可采用循环切割法。
4.2.4切割各种型钢时,不得在切口处和肋部造成破损和缺口。
钢材切割后,切割线和号料线之间的允许偏差应符合下列规定:
手工切割:
±2.0mm
自动、半自动切割:
±1.5mm
4.2.5沿钢板厚度走向(包括角钢的两肢、工字钢和槽钢的翼缘板和腹板的厚度方向),其垂直度偏差不得超过钢材厚度的10%,且不得不大于2.0mm。
4.2.6对于小型的板件可采用剪板机下料,在剪切前,应对剪板机进行下列检查:
a)刀刃的角度是否正确,有无崩牙、卷刃和其它损伤。
b)上下刀刃的缝隙是否符合下表既定。
c)档板螺栓是否拧紧(在操作过程中还要经常检查、调整)。
d)压料装置和各压脚与平台间的间隙是否一致。
剪板机上下刀刃缝隙表(mm)
钢板厚度
4
5
6
7
8
9
10
11
12
间隙
0.05
0.20
0.25
0.20
0.35
0.40
0.45
0.50
0.55
4.2.7板材下料防变形措施和变形处理
4.2.8板材下料采用自动或半自动切割机进行,将画好套裁图的板材用桥式吊车吊到下料架上,然后按下料几何尺寸进行切割,如果此板件需切坡口,需预留坡口加工时的铣边余量。
4.2.9板材在切割过程中,可能发生或大或小的变形,一般地,板材弯曲有起拱和侧弯两种,前一种发生的机率较小。
此两种变形矫正可采取火焰热矫法进行,对低合金结构钢而言,加热温度不得超900℃,且应缓慢冷却。
其矫正方法参见“焊接变形矫正”。
钢材矫正后的允许偏差(mm),见下表:
项目
允许偏差
钢板的局部不平度
t≤14
1.5
t>14
1.0
型钢弯曲矢高
L/1000
5.0
角钢肢的垂直度
b/100
双肢栓接角钢的角度不得大于90℃
槽钢翼缘对腹板的垂直度
b/80
工字钢、H型钢翼缘对腹板的垂直度
B/100
2.0
4.2.10型钢及杆件下料时,要预先计算统计,将长件和短件相结合排料,使整根料得到充分的利用,杆件下料尺寸应考虑焊接间隙及焊接收缩量,以免产生累计误差。
4.3制孔
4.3.1制孔采用摇臂钻制孔,制孔前应仔细核对孔的位置,孔径及孔的中心距。
零部件上有不同直径的孔眼时,应将同一直径的孔眼制完后,再制另一种直径的孔眼。
4.3.2用钻床在零部件钻孔时,应将零件放平、夹紧,并宜采用成迭钻孔(配钻),采用成迭钻孔时,应使零部件的两个边缘(基准面)对齐,并保证最低层的钻孔质量。
4.3.4开钻时应将钻头对准孔眼轻轻压下,以检查钻头外径是否对准了孔的检查圈,当孔眼接近钻透时,应减轻压力,所有部件均宜在工作台上进行,如不在工作台上钻孔,应将零件垫高地面150mm左右,放平、垫稳,不应因受钻头压力而倾斜,部件应与钻头垂直。
4.3.5孔眼的边缘不应有裂纹,飞刺和大于1.0mm的缺棱。
4.3.6C级螺栓孔孔壁表面粗糙度Ra不应大于25μm,允许偏差符合下表规定。
C级螺栓孔的允许偏差(mm)
项目
允许偏差
直径
+1.0
圆度
2.0
垂直度
0.03且不大于2.0
4.3.7螺栓孔距的允许偏差应符合下表规定:
螺栓孔孔距的允许偏差(mm)
项目
允许偏差
≤±500
501---1200
1200---3000
>3000
同一组内任意两孔间距离
±1.0
±1.5
______
_____
相邻两组的端孔间距离
±1.5
±2.0
±2.5
±3.0
4.3.8为保证工程质量,构件体开孔宜采用成品开孔,如采用单体部件开孔后拼装时,应有防焊接变形措施,保证各开孔位置符合孔距允许偏差要求。
4.4平台、栏杆、梯子的制作
4.4.1梯子、栏杆制作前,应按照设计图纸所要求的形式、尺寸进行放样下料。
4.4.2梯子的横梁上开孔时,应采用钻孔的方法,并且准确的定位,保证孔的位置准.确,并及时进行焊接。
4.4.3钢斜梯的踏步采用压型法或拼接法进行制作。
4.4.4栏杆制作时,应注意保护管材不受挤压,以免发生局部变形。
4.4.5所有构件表面应光滑、无毛刺,制作完后的钢斜梯不应有歪斜、扭曲、变形及其它缺陷。
4.4.6制作完后梯子、栏杆必须涂防锈漆,安装后再涂表面漆。
4.4.7平台的内外环行圈梁应采用煨制,煨制完到现场用样板进行检查,曲率不合适的,进行现场校圆。
4.4.8所有悬臂梁、三角架、直梯、斜梯、平台支撑等均应在平台上集中预制;焊接完毕用磨光机打磨光滑,进行标识,分类摆放。
4.4.9圆形平台根据吊装及安装的要求,进行分块预制,卧式设备的小型方平台,可制作成整体,大型方平台可分块预制。
平台梯子预制的允许偏差见下表和示意图
序号
项目
允许偏差
1
平台长度A
2/1000且全长不大于10mm
2
平台宽度B
±3mm
3
对角线长度差
≤6mm
4
平台各侧面挠曲矢高(平台长≤6m)
≤6mm
5
平台各侧面挠曲矢高(平台长>6m)
≤10mm
6
梯子长度L
±5mm
7
梯子宽度H
±3mm
8
梯子纵向挠曲矢高
≤L/1000
9
斜梯踏步与边梁夹角a
±1°
10
梯子踏步间距t
±2mm
梯子示意图
4.5钢结构拼装
对钢结构拼装的要求
拼装过程中应保证制成构件的实际尺寸,允差不得超过下列要求:
项目
允许偏差
平台标高
±10.0
平台长度和宽度
±5.0
平台两对角线差
6.0
平台表面平面度(1m范围内)
6.0
平台梁水平度
l/1000
20.0
平台支柱垂直度
H/1000
15.0
承重平台梁侧向弯曲
l/1000
10.0
承重平台梁垂直度
h/250
15.0
4.6钢结构的焊接和焊接检验
4.6.1焊接
4.6.1.1参加本工程施工的焊工,应持有焊工操作证,施焊项目满足需要并在有效期内。
4.6.1.2焊条必须有质量保证书;并在施焊前按技术说明书规定的烘焙温度和时间进行烘焙;经烘焙后应放入保温筒随用随取。
4.6.1.3焊工焊接时必须严