C1004方案 分片.docx
《C1004方案 分片.docx》由会员分享,可在线阅读,更多相关《C1004方案 分片.docx(30页珍藏版)》请在冰豆网上搜索。
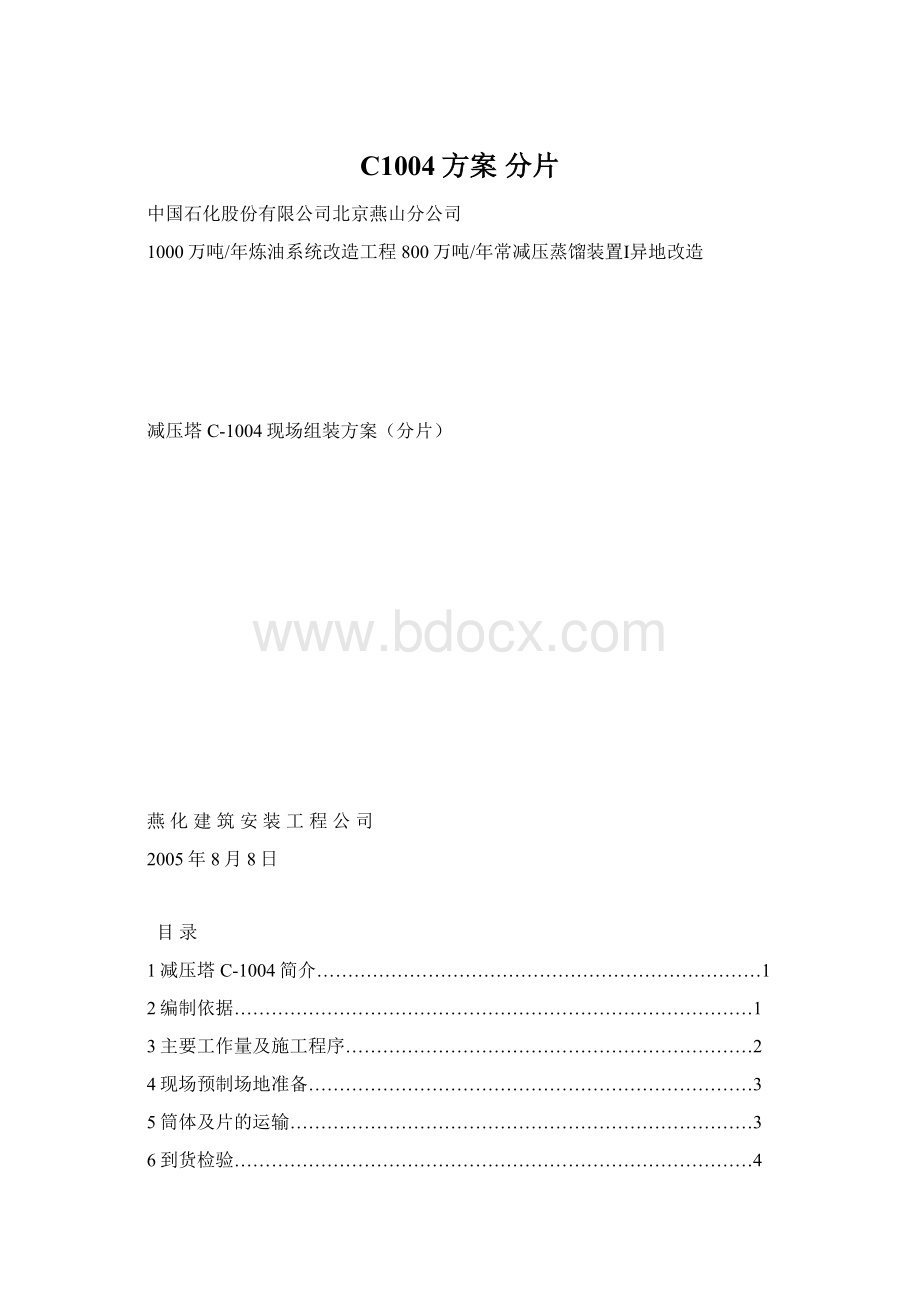
C1004方案分片
中国石化股份有限公司北京燕山分公司
1000万吨/年炼油系统改造工程800万吨/年常减压蒸馏装置Ⅰ异地改造
减压塔C-1004现场组装方案(分片)
燕化建筑安装工程公司
2005年8月8日
目录
1减压塔C-1004简介………………………………………………………………1
2编制依据…………………………………………………………………………1
3主要工作量及施工程序…………………………………………………………2
4现场预制场地准备………………………………………………………………3
5筒体及片的运输…………………………………………………………………3
6到货检验…………………………………………………………………………4
6.1分段筒体的检验……………………………………………………………4
6.2椭圆形封头的检验…………………………………………………………4
6.3复合板分片到货检验………………………………………………………5
6.4球形过渡段瓣片的检验……………………………………………………6
7基础验收…………………………………………………………………………7
8安装前的预制工作………………………………………………………………8
8.1基地进行的预制工作………………………………………………………9
8.2现场预制工作………………………………………………………………9
9现场塔体组装方法……………………………………………………………10
10塔体开孔及塔内固定件的组焊………………………………………………13
11复层酸洗钝化…………………………………………………………………15
12安装上部球形过渡段及Φ6.4m部分筒节……………………………………15
13组装后检查……………………………………………………………………16
14不锈钢复层的保护……………………………………………………………16
15塔平台安装……………………………………………………………………17
16.水压试验及沉降观测试验…………………………………………………18
17焊缝抽检………………………………………………………………………19
18质量管理措施…………………………………………………………………19
19交工技术文件…………………………………………………………………20
20.现场安全措施…………………………………………………………………21
1减压塔C-1004简介
减压塔C-1004金属质量为313吨,壳体材质采用16MnR+0Cr13复合板,材质特殊、结构复杂,设计、制造要求很高。
我公司采用复合钢板制造这种大型设备还是第一次,无类似经验,因此施工中难点很多。
因为塔直径较大,本方案采用在现场分片组装的方式进行,即把Φ9.8m部分筒体分片运输到现场,在设备基础上现场组装,其余部分在基地预制成段。
设备主要参数见下表:
试验压力(立式)
0.125MPa
主体材质
16MnR+0Cr13
壳体重量
313t
介质
油、油气和水蒸汽
设备容积
2786M3
设备充水质量
3099吨
设计压力(顶)
0.1MPa
设计温度
410℃
设备规格
Ф6400×12400×23/Ф9800×20800×29/Ф5400×3200×21/Ф3800×2000×21(总51618)
2编制依据
2.1工程图纸(中国石化工程建设公司设计)
2.2《压力容器安全技术监察规程》1999
2.3《钢制压力容器》GB150-1998
2.4《塔器设计技术规定》HG20652
2.5《钢制塔式容器》JB4710-92
2.6《复合板塔体制造技术要求》
2.7《化工塔类设备施工及验收规范》HGJ211-85
2.8《钢制压力容器用封头》JB/T4746-2002
2.9《石油化工立式圆筒形钢制储罐施工工艺标准》SH3530-1993
2.10《石油化工钢制塔、容器现场组焊施工工艺标准》SH3524-1999
2.11《复合板塔体制造技术要求》及附件
3主要工作量及施工程序
减压塔现场分片组装主要工作量为:
筒节组对,分片安装,无损检测,接管、平台安装,塔内支撑件焊接,内件安装,酸洗钝化,水压试验及沉降试验。
现场施工流程如下图:
施工准备
筒体,瓣片,塔壁板,接管,内件支撑件的检验
放置临时钢支架
安装裙座
吊装φ5.4m部分放在钢支架上,并加固
吊装球形过渡段并与裙座焊接
预制球形过渡段
提升φ5.4m部分与球封焊接
逐圈安装第4到15圈壁板
填料开箱检查
安装接管人孔,焊接固定件
内壁酸洗钝化,安装填料
吊装φ6.4m部分
安装接管人孔,焊接固定件
填料开箱检查
内壁酸洗钝化,安装填料,塔盘
吊装封头
人孔封闭,水压试验及沉降观测
筒体外部焊缝磁粉检测
4现场预制场地准备
球形过渡段需要在现场预制,要铺设预制平台。
根据其直径,并考虑吊车站位、塔壁板预制件的摆放位置等,在减压塔安装位置附近铺设预制平台。
见下图,平台大小为11×28m,用料为δ=20mm的钢板,支撑用I20,I10。
5筒体及片的运输
5.1分段筒体用拖车立置运输,每段高度限制在4.6m以下。
5.2塔壁板和球形过渡段瓣片用卡车运输,制作专用弧形胎具,每车运输8块,在塔壁板内表面铺上胶皮,防止磕碰及污染,每两块板之间用木条垫实。
搬运时用四个卡兰进行吊装,四个吊点应受力均匀,以免造成扭曲。
到现场后将板片立置放在钢平台上。
胎具的制作如下图。
6到货检验
6.1分段筒体的检验
6.1.1筒体上的材料代号,排板编号,焊工代号均应有醒目标记,且与排板图一致。
在四个方位上应标有中心线。
6.1.2分段到货的筒体同一断面处的不圆度应小于25mm(取内直径最大值和最小值之差)。
6.1.3两相邻筒体分段处外圆周长之差允差为6mm(用钢盘尺测量外圆周长偏差)。
分段筒体纵焊缝的错边量为1mm(用焊接检验尺测量),焊缝棱角小于4.9mm(用弦长为D/6的内样板和外样板检查)。
6.1.4筒体分段处端面不平度偏差不大于2mm(用连通管及水平仪测量水平度)。
6.1.5坡口形式及尺寸应按照《复合板制造技术要求》中4.3.3的要求进行检验。
坡口表面应平滑,熔渣、氧化皮应清除干净。
表面不得有裂纹,分层,夹渣等缺陷。
6.1.6筒体上的接管,塔盘支撑圈,填料支撑件均应焊接完毕,按照图纸要求进行检查。
其中塔盘支持圈的上表面在300mm弦长内的不平度不得超过1mm,整个支持圈上表面的水平度应不大于10mm,相邻两层支持圈的间距偏差不得超过3mm。
6.2椭圆形封头的检验
塔顶φ6.4m×23的封头应对其按照JB/T4746-2002进行形状公差检验。
6.2.1检查封头内表面的形状公差,样板与封头内表面间的间隙:
外凸不得大于1.25%D即80mm,内凹不得大于0.625%D即40mm。
(如下图,样板弦长4.8m,检查时应使样板垂直于待测表面,可以避开焊缝进行测量)。
6.2.2封头直边处应进行切边,封头直边部分不得存在纵向皱折,直边高度按图纸为40mm,允许偏差为-2~4mm。
6.2.3直边部分的内径值公差为-4~6mm(在直边部分测量等距离分布的四个内径值,取其平均值)。
直边部分的不圆度应小于25mm。
6.2.4封头总深度公差为-12.8~38.4mm(在封头端面任意两直径位置上拉上钢丝,在钢丝交叉处垂直测量)。
6.2.5封头实测厚度应不小于图纸规定的23mm(沿封头端面圆周0°,90°,180°,270°四个方位,在厚度必测部位检测其厚度,如下图)。
6.3复合板分片到货检验
用弦长为2.5m的样板检查板片的弧度,样板与板片的间隙不得大于3mm。
复合板宽度允许偏差±1mm,两对角线弦长之差不得大于3mm。
坡口的检查按本方案6.1进行。
6.4球形过渡段瓣片的检验
6.4.1球形过渡段应在基地进行预组装,并将组装卡具及胎具一同带至现场。
坡口的检查按本方案6.1进行。
6.4.2用样板检查球形过渡段瓣片的曲率(如下图),其允许间隙如下表所示:
(a)(b)
球封瓣片曲率检查示意图
球封瓣片曲率允许偏差
瓣片弦长L(m)
样板弦长(m)
允许间隙e′(mm)
L≥2
≥2
≤3mm
2>L≥1.5
≥1.5
L<1.5
1
6.4.3球形过渡段瓣片的几何尺寸偏差应符合下图要求:
7基础验收
7.1安装施工前,塔基础经正式交接验收,基础施工单位应提交质量合格证书、测量记录及其他施工技术资料,基础上应明显地画出标高基准线、纵横中心线和沉降观测水准点。
7.2基础外观不得有裂纹、蜂窝、空洞及露筋等缺陷,混凝土强度应达到设计要求,周围土方应回填实、整平。
7.3基础各部尺寸及位置的偏差应符合下表要求:
设备基础的允许偏差
项目
偏差名称
允许偏差值(mm)
1
基础坐标位置(纵、横轴线)
±20
2
基础不同平面的标高
-20~0
3
基础平面外形尺寸
±20
4
基础平面的水平度:
每米/全长
5/10
5
竖向偏差:
每米/全高
5/20
6
预埋地脚螺栓:
标高(顶端)
中心距(在根部和顶部两处测量)
0~20
±2
7
预留地脚螺栓孔:
中心位置
深度
孔壁铅锤度
±10
0~20
10
8
预埋活动地脚螺栓锚板:
标高
中心位置
水平度(带槽的锚板)
水平度(带螺纹孔的锚板)
0~20
±5
5
2
7.4基础表面在塔安装前应进行修整。
需灌浆抹面处要铲好麻面;基础表面不得有油垢或疏松层;放置垫铁处应铲平;预留地脚螺栓孔内杂物应清除干净。
7.5地脚螺栓不得弯曲,螺纹部分无损坏及锈蚀,应涂上润滑油加以保护。
8安装前的预制工作
Φ9.8m的筒体(包括球形过渡段,裙座)在基地预制成片,在现场分片安装,其它部分在基地预制,到现场后直接组装。
在壳体组对过程中进行填料的安装。
8.1基地进行的预制工作
8.1.1Φ3.8m的部分,筒节
和封头在基地预制成整体;
8.1.2Φ5.4m的部分,筒节
和下方球形过渡段在基地预制成整体,筒节
单独预制。
8.1.3Φ6.4m的部分,筒节
,
组成一部分,筒节
,
组成一部分,筒节
,
组成一部分,封头和筒节
各为一部分。
8.1.4Φ9.8m的筒体塔壁板(包括部球形过渡段和裙座),在基地压制成片。
8.2现场预制工作
8.2.1制作用于支撑Φ5.4m部分筒体的临时钢支架,钢支架另绘图制作。
8.2.2球形封头的现场预制
8.2.2.1在钢平台上划出组装基准圆(按筒节的基准圆),将基准圆按照封头的分瓣数等分,至少在距等分线两侧约100mm处各设置一块定位板;
8.2.2.2在组装基准圆内或外,设置封头组装胎具,以定位板和组装胎具为基准,用工卡具使瓣片紧靠定位板和胎具,并调整对口间隙和错边量;
8.2.2.3瓣片在钢平台上组对成封头后,应对每道焊口进行检查,检测结果应符合下列要求:
a)对口间隙应符合焊接施工方案要求;
b)焊接接头对口错边量小于等于1mm;
c)棱角小于2.3mm;
d)不圆度不大于25mm。
上封头组装好后,与筒节
组成一段。
下封头组装好后,与筒节
组成