璃钢制品表面涂装的常用材料和基本工艺方法.docx
《璃钢制品表面涂装的常用材料和基本工艺方法.docx》由会员分享,可在线阅读,更多相关《璃钢制品表面涂装的常用材料和基本工艺方法.docx(15页珍藏版)》请在冰豆网上搜索。
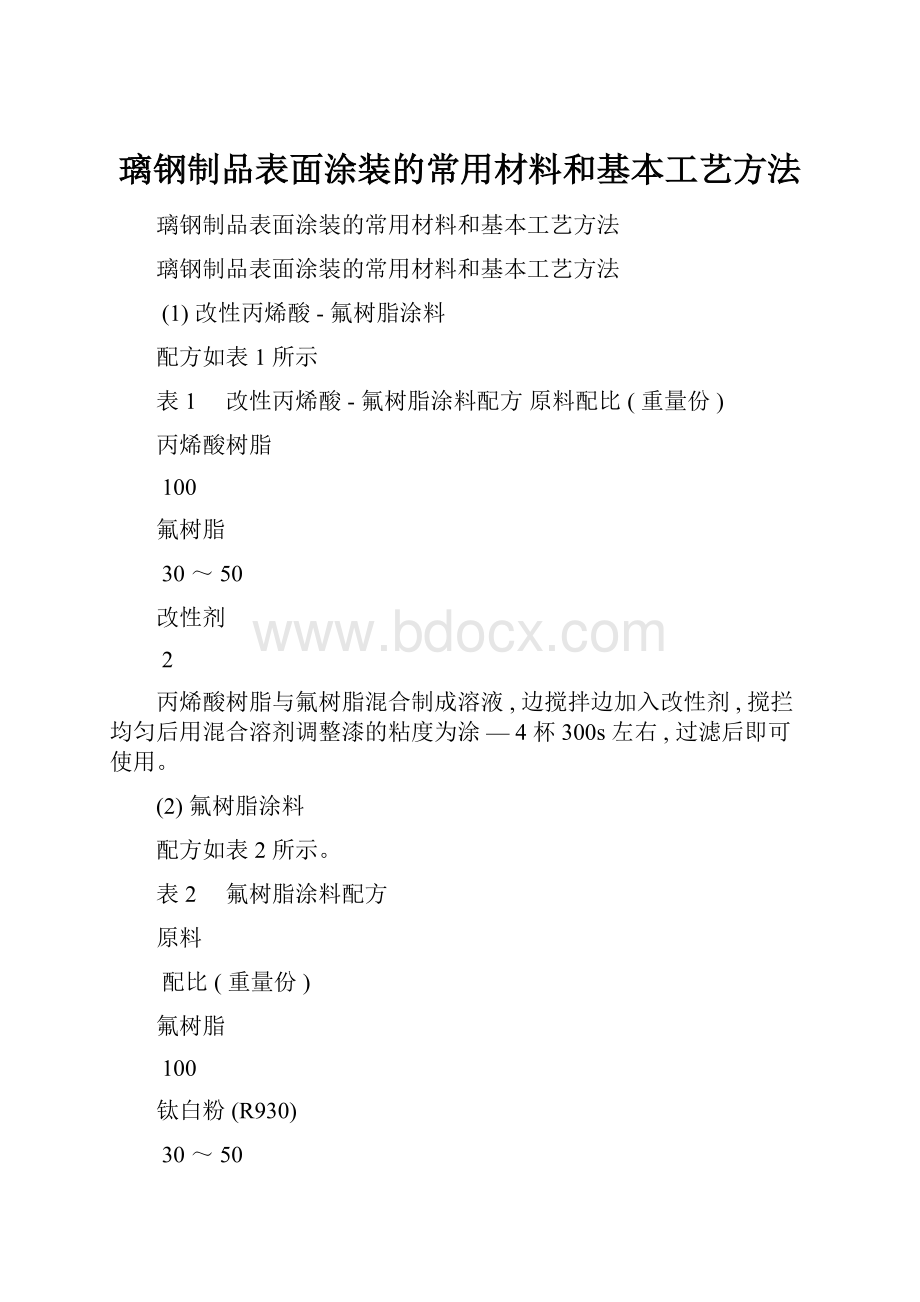
璃钢制品表面涂装的常用材料和基本工艺方法
璃钢制品表面涂装的常用材料和基本工艺方法
璃钢制品表面涂装的常用材料和基本工艺方法
(1) 改性丙烯酸 - 氟树脂涂料
配方如表 1 所示
表 1 改性丙烯酸 - 氟树脂涂料配方 原料配比 ( 重量份 )
丙烯酸树脂
100
氟树脂
30 ~ 50
改性剂
2
丙烯酸树脂与氟树脂混合制成溶液 , 边搅拌边加入改性剂 , 搅拦均匀后用混合溶剂调整漆的粘度为涂 — 4 杯 300s 左右 , 过滤后即可使用。
(2) 氟树脂涂料
配方如表 2 所示。
表 2 氟树脂涂料配方
原料
配比 ( 重量份 )
氟树脂
100
钛白粉 (R930)
30 ~ 50
分散剂 (B YK — P104S)
5
消泡剂 (B YK — 141)
3
催化剂
3
甲苯
5
缩二脲 (N75 , 固化剂 )
8
在氟树脂中加入分散剂、消泡剂和催化剂 , 低速搅拌均匀 ; 加入钛白粉 , 高速分散 ( > 1000rpm) , 检查细度到 30 μ m 以下 ; 加入碳酸钙 , 高速分散 , 检查细度到 45 μ m 以下 ; 密封保存。
(3) 无机水性涂料
无机水性涂料是所有涂料中价格较高的 , 一次性投资较大。
该产品对玻璃钢制品表面的保护作用和美化装饰效果很好 , 适用于各种工艺成型的玻璃钢制品表面。
最大优点是由无机材料组成 , 涂装后的挥发物为水 , 没有环境污染 , 涂层可自洁。
2 . 2 喷塑工艺
(1) 静电喷塑工艺
静电喷塑工艺运用高压电场感应效应 , 使粉末涂料和被涂覆物件分别带上彼此相反的电荷 , 粉末在电场力的作用下飞向并吸附在制品表面 , 然后加热使粉末涂料熔融成膜。
静电喷塑具有效率高、涂层均匀、污染少等特点 , 适应于规模化自动涂料生产线。
随着各种高性能、中低温固化的粉末涂料的开发 , 该工艺在玻璃钢方面的应用前景良好 , 是当前工艺研究的重点之一。
此工艺最关键的问题是玻璃钢的导静电问题。
由于玻璃钢表面导电率低 , 不能良好地静电吸附涂料粉末。
通过技术攻关 , 本文已成功地解决了涂层与玻璃钢的界面问题 , 实现了高性
能粉末涂料的涂装。
(2) 热熔喷塑工艺
综合塑料粉末涂装工艺的优缺点以及对玻璃钢制品的性能分析和要求 , 新开发了热熔喷塑工艺。
它类似于静电喷塑工艺 , 但此工艺省略了静电喷塑中对玻璃钢制品的导静电要求 , 粉末塑化温度较低 , 适用于基材厚度较大的玻璃钢制品。
选择合适分子量阶段的聚合物 , 熔融后在制品的表面形成一层塑料薄膜 , 以吸收紫外线、避免机械伤害和利用涂层优良的耐老化、耐腐蚀等性能保护制品。
该工艺通过加热玻璃钢制品 , 粉末在热空气压力下飞向制品并热熔 , 附着在制品表面后塑化 , 形成保护涂层。
涂层厚度由制品的温度控制 , 涂层与玻璃钢的界面良好 , 质量控制参数容易掌握 , 可实现工业化生产。
技术关键是玻璃钢表面的前处理工艺和基体温度的确定。
(3) 粉末浸塑工艺
粉末涂料在压缩空气的作用下悬浮 , 将预热到高于粉料熔点温度的玻璃钢制品浸入容器中 ; 粉料均匀地粘附于制品表面 , 到预定时间取出制品机械振动 , 除掉多余的粉末 ; 最后将制品送入塑化炉流平、塑化 , 冷却 , 得到均匀的涂层。
玻璃钢制品的粉末浸塑工艺和普通的钢铁制品的浸塑不同之处在于玻璃钢制品不能象钢铁制品一样加高温后在流化床中涂粉再高温塑化。
因此 , 此工艺主要应用于耐高温的厚壁玻璃钢制品 , 如 SMC 、缠绕等玻璃钢制品的表面防护。
由于目前性能较好的粉末涂料的溶点一般较高 , 它主要应用于有特殊功能要求的制品表面涂覆 , 以增加制品的功能。
2 . 3 模内涂层技术
模内涂层技术是当前国际上水平较高的表面涂装技术 , 主要用于 SMC 模压制品。
它省略了二次底涂工序及所需设备 , 避免了挥发性溶剂的污染 , 解决了常规成型制品和二次涂装制品易出现的针孔、鼓泡等缺陷 , 可实现 A 级表面。
基本操作步骤是① 将片材加入模具中 , 闭合压机 , 使制品成型 , 直至获得最低的初始强度 ; ② 开启模具约 0. 5mm , 将涂料注入制件表面 ; ③ 闭合压机 , 其压力较成型压力低 , 使涂料固化 ; ④ 开启压机 , 取出制件。
IMC 需要计算机控制。
在批量大、制件质量要求高的情况下 , IMC 的优越性将显示出来。
在 IMC 的基础上国外已开发出多种表面涂装技术 , 如高压模内涂层技术 (HPIMC) 、 RIM 模内着 色技术和粒化注射喷涂技术 (GIPT) 等。
3 涂装技术的应用前景
玻璃钢应用的发展给表面处理技术提供了广阔的应用前景。
从 80 年代初开始 , 我国的民用玻璃钢制品的研究开始为人们所重视 , 并且迅速发展。
预计到 2010 年我国的玻璃钢产量将达到 90 万 t , 并居世界第二位。
从经济角度分析 , 玻璃钢表面涂装技术具有以下优势 :
① 目前由于技术、工艺等原因 , 玻璃钢制品的表面不尽如人意。
大批成品仅由于表面的缺陷而成为不合格品 , 造成不必要的成本增加。
运用玻璃钢表面涂装技术 , 可以提高制品的表观质量 , 从而降低制品的废品率。
② 在某些条件下可用相对价低的中碱纤维、通用树脂来代替无碱纤维、耐腐蚀树脂 , 在不影响制品的使用性能的前提下 , 降低原材料的成本。
以 SMC 片材为例 , 用中碱纤维代替无碱纤维可节约成本 7 % 。
③ 玻璃钢表面涂装技术还可以提高助剂的利用率 , 如紫外线吸收剂、抗氧化剂等。
因为这些助剂只需在表面层使用。
④ 试验研究表明 , 玻璃钢的老化一般都是从表面开始的 , 并且主要在 0. 7mm 范围内。
主要表现在表面起花、纤维外露。
表面涂装技术可以增加玻璃钢制品的使用寿命 , 节约维护成本。
玻璃钢表面涂装技术是玻璃钢行业的一项新兴的技术 , 工艺简单、成本较低、性能可靠。
它有很好的发展前景。
减少涂装公害、降低涂装成本、提高涂装质量一直是涂装技术发展的主题。
本文分别从涂装材料、涂装工艺、涂装设备、涂装管理四大方面简要介绍了国内外汽车涂装技术的发展动态。
涂装材料、涂装工艺、涂装设备、涂装管理是汽车涂装的四大要素,相互之间相辅相成,促进了涂装工艺和技术的进步与发展。
21世纪被称为面向环境的新世纪,环境保护倍受全球关注,并已成为人类最迫切研究的课题。
汽车及其零部件的涂装是汽车制造过程中能耗最高且产生三废最多的环节之一。
因此,减少涂装公害、降低涂装成本、提高涂装质量一直是涂装技术发展的主题。
新涂装材料的应用
新涂装材料的应用是涂装技术进步的先导,在不断满足涂层性能要求的前提下,始终以应用可减少公害、降低涂装成本的材料为主要发展目标。
由生物可降解性活性剂配制的脱脂剂、无镍磷化液、无亚硝酸盐磷化液、无铬钝化剂、低温脱脂剂(处理温度43℃)、性能与常规相同的低温(35℃)少渣(比常规低10%~30%)磷化液、无铅无锡阴极电泳涂料及低温固化(160℃ 10min)、低加热减量(4%以下)、低VOC挥发量(0.4%~0.8%)型阴极电泳涂料在欧美及日本已经推广应用多年。
在北美和欧洲,可替代传统中涂的二次电泳涂料已经开始应用。
在欧洲,有些汽车公司已经在近几年新建涂装线上全部采用水性涂料,VOC排放量已低于法规要求的35g/m2(德国TA-Luft,1995年)。
从20世纪90年代开始,所有新建涂装线底漆全部采用了电泳底漆或粉末涂料,中涂采用水性涂料或高固体分材料,面漆采用水性底色加高固体分清漆。
目前,粉末清漆已经开始应用于轿车的车身涂装。
继粉末罩光漆工业化应用后,粉末金属底色也已经商业化。
在北美,粉末中涂已经工业化应用多年,同时水性面漆底色近几年普及得非常快,高固体分中涂和面漆应用也相当普遍。
欧美的紫外光(UV)固化涂料在汽车涂装中的应用技术已经接近成熟。
日本也在积极开发和推广水性涂料、高固体分及超高固体分罩光漆。
随着全球环境的不断恶化,我们必须大幅度提高汽车涂层的耐酸雨性能和抗擦伤性能。
近几年来,减小车身内外表面电泳底漆膜厚差的高泳透力、低颜料分的电泳涂料、耐酸雨和抗擦伤面漆、多色中涂和采用粘度控制技术涂料等得到普遍应用。
我国几大汽车公司在漆前处理材料和电泳漆的应用方面与国际水平相差不大,但由于应用水性中涂和水性面漆必须使用专用设备,因此提高了涂装成本。
尽管国外独资及合资企业具备在国内生产水性中涂和水性面漆的能力,但汽车涂装中涂和面漆仍采用传统的中低固体分溶剂型涂料,涂装VOC排放远落后于欧洲。
涂装工艺及设备
近十多年来,涂装工艺及设备的进步主要体现在环保型涂装材料的应用,减少废水、废渣的排放,降低成本,优化汽车生产过程等几个方面。
由于涂装材料的进步,车身涂层体系的设计也有了革命性的进展,几种典型的新涂装体系及新技术已经或即将用于工业生产。
我国目前的涂装工艺及设备总体相当于欧美10年前的水平,有些企业在新涂装线上采用了一些当今国际先进水平的新设备。
1.节水及废料回收技术
前处理和电泳是汽车涂装耗水量和废水排放量最大的环节。
随着膜技术的不断成熟,采用膜分离技术(UF和RO)回收脱脂液,再生清洗水和前处理废水,使得实现真正意义的电泳闭路清洗成为可能。
目前,膜分离技术已经开始应用。
近几年来,随着发达国家环保涂料的工业化应用,一些涂料的循环利用技术(如粉末浆再循环利用技术,粉末底色及清漆回收技术,废漆絮凝干燥器技术,超滤法、冷却法和静电吸附法回收水性漆技术,过喷漆雾的水性漆回收技术等)也得以应用,从而使涂装线的涂料利用率进一步提高,最大限度地减少废漆渣的排放。
目前,我国在涂装节水及三废综合利用方面重视程度不够,在新技术应用方面相对落后。
2.几种新的车身涂装工艺
逆过程工艺:
在车身外表面先喷涂粉末涂料,待热熔融后再进行电泳涂装,随后粉末/电泳涂膜一起烘干。
使用这种工艺约可减少60%的电泳涂料用量,用厚度为70μm的粉末涂层替代车身外表面的电泳底漆和中涂层,取消中涂及烘干工序,从而节省材料和能源费用,降低VOC排放量。
二次电泳工艺:
采用两涂层电泳材料,用第二层电泳(35~40μm)替代中涂。
电泳工艺自动化施工稳定可靠性高,一次合格率高,材料利用率高,设备投资少(不需空调系统),因此可节省费用的48%,减少了维修频次及传统中涂的漆渣和VOC排放。
一体化涂装工艺(三涂层概念):
采用与面漆同色的功能层(15μm)替代中涂,功能层与面漆底色间不需烘干,取消中涂线,在提高生产效率的同时,大幅降低了VOC排放量。
3.敷膜技术替代塑料覆盖件涂装
敷膜技术是预制一种适应于热成形的面漆涂膜,其经热成形后的产品的面漆性能和外观与传统的烘烤喷涂涂膜非常相近。
该技术主要应用于塑料件生产,采用“夹物模压”或“内模”工艺将预制好的复合涂膜在塑料件浇注成形的同时完成成形并与塑料件熔为一体,得到无缺陷的涂装覆盖件。
车身骨架采用传统冲压焊装工艺制造,涂装车间只对车身骨架进行涂装,面漆采用粉末喷涂技术。
由于车身骨架外露面积较小,所以面漆颜色不必与覆盖件相同,深浅各1种即可。
大面积的覆盖件都是采用敷膜技术制造的塑料件,颜色有上千种。
这样大大简化了车身涂装工艺,在降低涂装成本的同时,使涂装的VOC排放达到7g/m2左右,远低于欧洲排放法规的要求。
4.车身涂装P2 ZERO概念
所谓P2 Zero概念就是零排放油漆车间。
在满足苛刻的环保要求和用户质量要求的前提下,减少三废处理的成本,减少油漆车间操作成本和简化油漆工艺。
车身钢板的防腐底漆在制成零件前进行涂覆,进入油漆车间的车身不需再涂底漆,只喷涂一道粉末底色和一道粉末罩光,因此,可最大限度地减少工艺等待时间、取消传统的调漆间、工艺调整更加灵活、从钢板到涂漆前车身的生产过程取消防锈工艺、彻底消除传统涂装焊缝及空腔结构防腐差的问题、节省涂装车间面积、降低三废处理费用、无需漆渣系统及废漆处理系统、无喷漆室排气、空气污染和固体废料趋于零、无液体排放、涂料制造及使用效率大于95%、无气味无危险。
5.底盘类零件的涂装
在发达国家,底盘类零件涂装普遍采用磷化、阴极电泳或粉末喷涂工艺,大总成一般是零件先进行电泳或粉末喷涂,然后装配,根据需要再对总成喷涂低温或室温固化面漆。
由于阴极电泳和粉末涂层具有良好的机械性能,有些零件的机械加工可以在涂装后进行,这样可以避免零件在涂装前因加工时间长而锈蚀。
车架、底盘类零件毛胚多是热轧板和铸件,成形前或涂装前多采用喷丸或喷砂处理,酸洗处理已经逐渐被淘汰。
目前,我国的零部件涂装生产规模普遍较小,总体上相对落后。
轿车及其他小型乘用车相对较好,载货车、客车、农用运输车的涂装工艺和使用的涂料水平都不高。
6.新型涂装运输机
国内目前车身涂装线前处理和电泳采用的典型运输机有推杆悬链、摆杆链和程控葫芦。
它们各有优缺点,共同的缺点是都不能解决车身内部诸多空腔结构体内的有效排气问题,尤其是车顶盖内的气袋问题。
这些部位不能得到磷化和电泳处理。
新型的多功能穿梭机(Vario-Shuttle)和滚浸运输机(RoDip)诞生后,不仅解决了这些问题,而且继承了前述的运输机的所有优点。
多功能穿梭机还具备在一条生产线上实现多品种不同工艺的功能,完全符合自动化柔性涂装生产的要求。
这两种运输机在国内新建车身涂装线上已经开始应用。
7.其他涂装设备结构和功能的改进
在欧洲,涂装设备的结构材料以不锈钢为主,设备的电气线路均设计在设备结构中,取消了电气管路,设备的模块化设计和车间的立体分区布置,最大限度地保证涂装的高清洁度要求和安全防火要求。
无外部风管及内部辐射强化对流的新一代烘干室,大幅度提高了热效率和烘干温度的均匀性。
随着机器人技术的进步,车身自动涂装机逐渐被多自由度的喷涂机器人取代,喷涂和密封大量采用机器人自动操作,比涂装机更适应柔性化生产。
机械化传动链条普遍采用非金属材料,大幅度降低传动噪音。
涂装管理
涂装管理包括涂装材料的订货、材料质量控制和施工过程的控制等方面。
由于汽车涂装使用的材料品种繁多、在储运过程中易变质、工艺流程长、需要控制的参数多等原因,在汽车生产管理中其复杂程度最高。
在汽车工业发达国家,汽车涂装材料的发展促进了汽车涂装技术的进步,为了降低涂装成本,供货方式也从单一的材料供货过渡为系统供货。
系统供货方式始于20世纪90年代初,目前在欧美已经基本普及。
世界各大汽车制造企业历来对涂装管理极为重视,由涂料厂商直接负责涂装生产的技术管理,使汽车生产厂的涂装管理大大简化,涂装一次合格率提高,生产成本降低。
目前,这种管理方式在国内各汽车公司仍处于尝试阶段。
近几年,部分有实力的涂装材料公司和涂装设备公司又推出了BOT服务模式,即汽车公司的涂装车间由涂装材料公司或涂装设备公司投资建设,并负责生产管理,根据汽车公司的整车生产计划进行涂装生产,供给汽车公司的是合格的涂膜。
汽车公司只需制定技术标准的和验收监督涂装产品质量。
这将成为涂装管理的一大发展趋势。
结束语
我国汽车涂装技术与国际水平的差距在不断缩小,但发展仍不均衡,就涂装质量的保证而言,几大轿车生产企业已经达到国际水平,但综合比较仍有10年左右的差距,主要体现在清洁生产技术方面;就汽车涂装生产关键装备技术而言,我国可能在今后相当长的时间内主要依赖进口。
预计我国在未来10~15年内,汽车涂装水平将全面与国际接轨,加快节省资源和环保技术的应用。
11楼ABB涂装线技术资料
一.工艺流程:
上挂 静电除尘 底漆涂装I 流平室I 底漆涂装II 流平室II 面漆涂装 流平室III 烤炉
二.涂装治具:
在现有环境条件一定的情况下,涂装治具设计和使用的合理性会直接影响涂装品质.
1.A治具与B治具之间应留有稍许间隙.
目的:
a.防止溢漆.
b.避免治具换用频率过高,造成浪费.
2.B治具应尽量设计简易,可采用直条扁平钢板来代替现有B治具.
目的:
a.利於清洗和重复使用.
b.可节省治具费用和模具费用.
3.c治具底座裸露在外面,喷涂时及易积漆形成漆渣,宜在喷房内输送链两边装软塑胶布.
目的:
1.可覆盖治具底座,易清洗和更换.
2.可减少杂质的产生.
4.所有治具应放置於无室内,上线前应确认A治具使用次数和治具清洁程度.必要时治具应进行清洁除尘.
5.各种颜色涂装用A,B治具不能混用,以免造成异色.
三.静电除尘:
静电除尘是保持喷房环境、保证涂装品质的重要因素.现有之静电除尘设备除尘效果不佳,宜采用有自动识别功能的全自动静电除尘消除仪.除去静电的同时要除去灰尘等异物.
注意事项:
静电除尘室必须通风畅通,以保证除尘效果.
四.涂装:
油漆粘度、雾化压力和喷幅是决定涂装品质的三大决定因素.常见的主要涂装不良原因和对策如下:
1.流挂.
垂直表面上进行涂装时,漆膜在成膜过程中由於重力的作用向下流动.这种状态保持到成膜之后.
因素:
a.溶剂挥发性.溶剂挥发快有利於防止流挂,但不易流平.
b.油漆粘度.粘度低易流挂.
c.涂料固化速度慢易流挂.
d.膜厚.膜厚厚易流挂.
对策:
a.正确选择溶剂和稀释剂.
b.控制粘度.
C膜厚管理.参数控制:
涂料量空气压力行枪速度角度方向距离
D涂装环境:
温度湿度.
2.白化.
涂料在干燥过程中或成膜后产生云雾状白色漆膜.
原因:
涂装过程中漆膜中混入水份.
A.溶剂快速蒸发引起涂膜表层温度急剧降低至露点以下.
B.压缩空气中水分未分离而混入涂料.
对策:
a.选择恰当溶剂和稀释剂,控制其挥发速度.
b.控制湿度<70%,如果湿度>70%可加入防潮剂.
c.压缩空气过滤.
3.渗色:
底漆或底材中的颜料渗入面漆中导致面漆颜色改变或发花.
原因:
底涂层中的著色颜料被面漆的溶剂溶解并迁移至面漆中.
对策:
a.底漆完全固化后再涂面漆.
b.面漆溶剂选择溶解力较差的溶剂.
4.裂纹:
漆膜表面产生微细裂纹.
原因:
制品内应力和外部应力.
对策:
a.降低溶剂蒸发速度.
b.选择适当的干燥方法和升温程序,减少应力产生.
5.桔皮:
原因:
漆膜不能很好的流平.
a.涂料的粘度上升至一定程度后停止流动.
b.涂料的浓度上升至屈伏值以上停止流动.
对策:
a.加入流平剂.
b.控制空气压力,保证涂料充分雾化.
c.控制漆膜厚度,保证足够的晾乾时间和流平.
d.控制喷房温度在20度左右.
e.调整正确的喷枪距离和角度.
6.气孔和针孔:
涂料成膜后可观察到漆膜表层以下存在氯泡或者是在漆膜表面上生成凹穴.氯孔处於涂层内,针孔在表面有开口.
原因:
a.润湿不良和消泡不佳.
b.涂料的粘度、表面张力、溶剂的挥发速度、涂装环境、清洁程度等.
对策:
a.根据不同的涂料体系选用消泡剂.
b.保证足够长的晾置时间,严格控制升温速度.
c.干燥和清洁底材表面,保持涂装环境清洁.
d.加入适当高沸点的溶剂改进溶剂挥发性和流动性.
7.缩孔和露底:
在平滑涂层表面出现随机分布、大小不一的凹穴,其中露出底材的称露底.
原因:
a.低表面能的油脂、过量的硅油、压缩空气带来的矿物油等.
b.与涂料体系不相溶的溶剂.
c.氯泡 .
d.固体粉尘.
对策:
a.加入适量有机硅助剂.
b.保持涂装环境清洁.
c.充分除去压缩空气中的水分和油分.
8.表面裂纹:
PC.ABS或PMMA等热塑性塑料涂装后,漆膜表面产生的微细裂纹.
原因:
a.聚合物与溶剂接触后其表面能降低.
b.溶剂分子渗入聚合物内部.
c.溶剂挥发后表层体积收缩,产生应力.
d.溶剂使聚合物表层发生溶胀.
对策:
a.涂料溶剂和稀释剂的适当选择,即溶剂的溶解力和挥发度的搭配.
b.选择适当的涂料干燥方法和升温程序,减少干燥过程中产生应力.
c.涂装前对塑料制品进行退火处理,消除塑料加工的残余内应力.
9.杂质:
在涂装过程中细小的灰尘漆渣等杂物镶嵌的油漆之中,其表面有凸起.
原因:
a.A、B治具不净,附有灰尘.
b.素材除尘效果不佳.
c.A、B、C治具上积聚的油漆渣.
d.通风系统带进杂质.
e.喷房和烤炉没有维持正压,外界不洁空气进入系统.
f.人为因素,如:
不穿防尘衣进出喷房.
对策:
a.保持治具清洁,极时更换治具.
b.改善静电除尘装置,提高除尘效果.
c.极时更换过滤网,保持通风系统的干净.
d.维持喷房和烤炉正压.
e.进入喷房和无尘室必须穿防尘衣.
10.漆点:
大量油漆聚集在漆膜一小面积处,其表面与其它涂面有色差.
原因:
a.涂装不均匀.
b.油漆没有充分搅拌.
c.喷枪长时间使用没有清洗.
d.喷枪氯压太小,油漆没有完全雾化.
e.油漆粘度太高,油漆不能雾化.
11.油污:
素材表面附著油渍,涂装后漆膜有色差,颜色偏暗.
对策:
用异丙醇或酒精擦拭.
12.刮伤:
漆膜甚至素材被破坏,有明显的凹痕和划迹.
原因:
a.上下挂造成刮伤.
b.治具峦形偏向一边,致使产品与隔风板之间有磨擦.
对策:
a.加强对员工的教育训练.
b.校正治具.
临时对策:
有刮伤之治具不上素材.
13.附著力不够:
附著力用来检测漆膜与素材之间的附著程度.
通常用百格试验验证.
影响附著力的因素:
a.表面处理.
b.油漆性能.
c.涂装工艺.
由於目前烤漆厂素材只有经过静电处理,没有经过溶剂清洗和表面研磨处理,但第一道底漆涂装使用的是低固体分及具有一定反应活性的底漆,其对素材有一定的表面处理功能.烤漆厂现用面漆是双组份油漆,如果底漆喷涂正常,在喷面漆时如果只喷清漆而没有喷固化剂,清漆便不能固化.若再喷一次面漆,则会造成附著力不够.
五.流平室:
温度:
55℃ 线速:
1.35m/min
作用:
1.在一定温度和时间的控制下,利用油漆的流动性,增加涂装表面的光滑度和流平性.
2.使溶剂等挥发物缓慢挥发,防止垂流、针孔、氯孔、桔皮等不良的发生.
六.烘烤:
温度:
80度 线速:
1.35m/min 时间:
40min
注意事项:
1.保持烤炉正压,以免不洁空氯污染烤炉甚至流平室和喷房.
2.保持烤炉正常通风和清洁.
七.通风系统:
维系正压,各间区隔,带走杂物,更换空气
注意事项:
1.过滤网要极时更换.
2.保持各室通风处於正常状况