由天然气合成甲醇装置实习指导.docx
《由天然气合成甲醇装置实习指导.docx》由会员分享,可在线阅读,更多相关《由天然气合成甲醇装置实习指导.docx(13页珍藏版)》请在冰豆网上搜索。
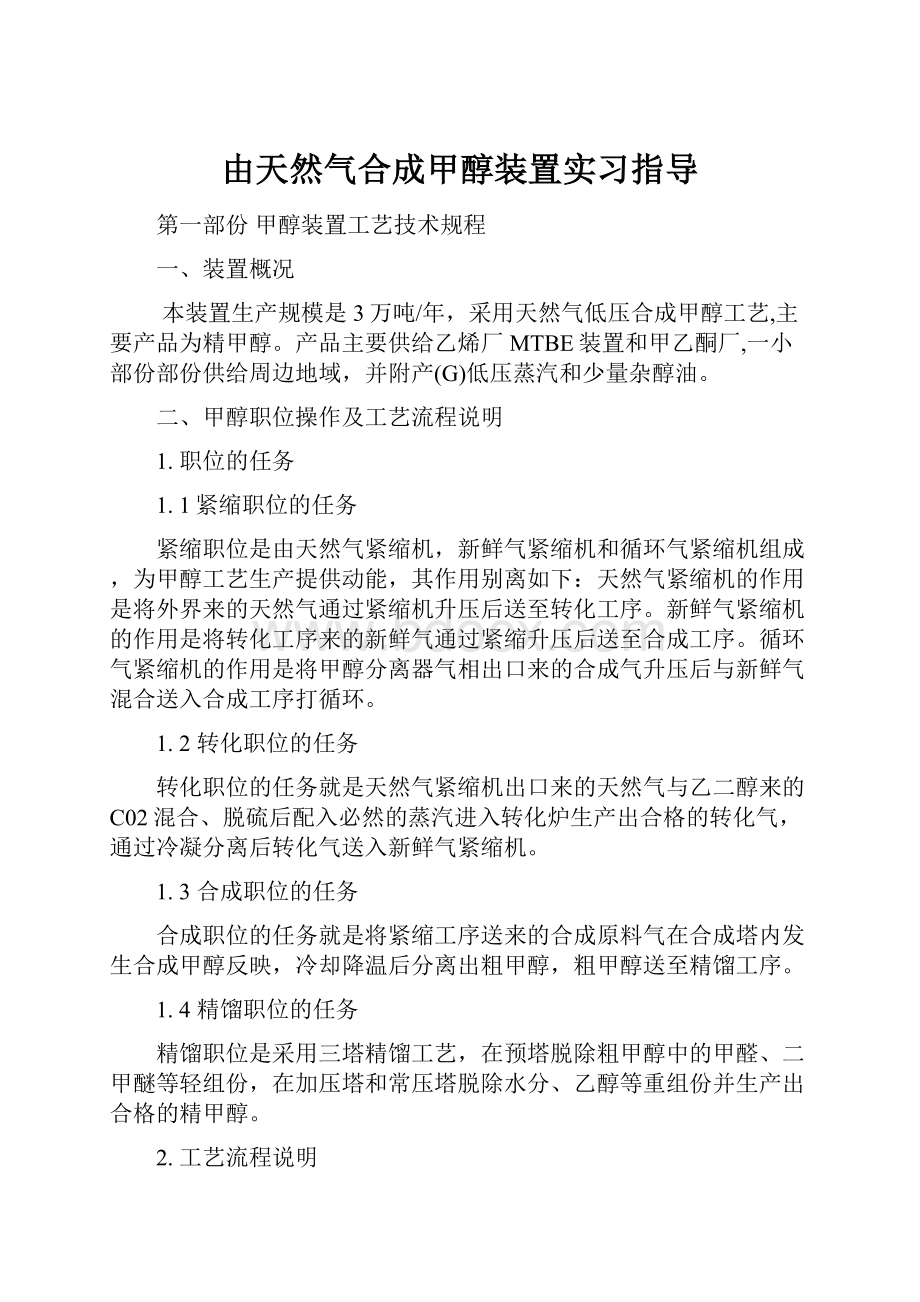
由天然气合成甲醇装置实习指导
第一部份甲醇装置工艺技术规程
一、装置概况
本装置生产规模是3万吨/年,采用天然气低压合成甲醇工艺,主要产品为精甲醇。
产品主要供给乙烯厂MTBE装置和甲乙酮厂,一小部份部份供给周边地域,并附产(G)低压蒸汽和少量杂醇油。
二、甲醇职位操作及工艺流程说明
1.职位的任务
1.1紧缩职位的任务
紧缩职位是由天然气紧缩机,新鲜气紧缩机和循环气紧缩机组成,为甲醇工艺生产提供动能,其作用别离如下:
天然气紧缩机的作用是将外界来的天然气通过紧缩机升压后送至转化工序。
新鲜气紧缩机的作用是将转化工序来的新鲜气通过紧缩升压后送至合成工序。
循环气紧缩机的作用是将甲醇分离器气相出口来的合成气升压后与新鲜气混合送入合成工序打循环。
1.2转化职位的任务
转化职位的任务就是天然气紧缩机出口来的天然气与乙二醇来的C02混合、脱硫后配入必然的蒸汽进入转化炉生产出合格的转化气,通过冷凝分离后转化气送入新鲜气紧缩机。
1.3合成职位的任务
合成职位的任务就是将紧缩工序送来的合成原料气在合成塔内发生合成甲醇反映,冷却降温后分离出粗甲醇,粗甲醇送至精馏工序。
1.4精馏职位的任务
精馏职位是采用三塔精馏工艺,在预塔脱除粗甲醇中的甲醛、二甲醚等轻组份,在加压塔和常压塔脱除水分、乙醇等重组份并生产出合格的精甲醇。
2.工艺流程说明
2.1流程叙述
2.1.1工艺流程叙述
由外界来的(G)天然气首先进入天然气紧缩机入口缓冲罐V101,分离掉其中的游离水和机械杂质,进入天然气紧缩机,经天然气紧缩机加压至(G),然后经天然气出口缓冲罐V102送到转化工序,出口温度约87℃,再经流量调节器FIC201控制流量后,与乙二醇装置来的通过FRC213调节流量后的二氧化碳气体混合,经天然气(CH4+C02)预热器加热至约380℃左右依次进入脱硫槽R201A/B和R202,使原料气净化并达到硫含量小于×10-6,净化后的原料气与蒸汽过热器来的过热中压蒸汽(G)、370℃)混合(按水碳比H2O/C≥),原料气混合气进入混合气预热器,加热到530℃左右,经上集气总管及上猪尾管,均匀地进入48根Φ124×12的转化管中,转化管内装有CN-16YQ催化剂,气体从上到下经催化剂床层进行转化反映,反映后的气体经转化管的下猪尾管进人下集气管出蒸汽转化炉。
转化气出转化炉的温度约830℃,压力约为(G),其中残余甲烷含量约为%(干基),转化气进入转化气1#废锅和转化气2#废锅的管程,壳程别离产生(G)和(G)的饱和蒸汽,出废热锅炉的转化气温度降至270℃,再依次进人中压锅炉给水预热器,低压锅炉给水预热器,脱盐水预热器,转化气温度降至130℃回收余热;再经转化气水冷器E20六、E207转化气温度降至低于40℃,进入分离器V210,分离出其余的工艺冷凝液,各换热器和分离器分离出的凝液通过液位调节阀控制进入凝液总管,经冷凝液水冷器冷却后排地沟。
分离器顶部出来的转化气压力约为(G),进入紧缩工序新鲜气入口缓冲罐V103,经新鲜气紧缩机C102A/B紧缩至(G),紧缩后的新鲜气温度约为109℃,进入合成气混合罐V105,与循环机出口来的循环气充分混合后送入合成工序。
混合后的合成气(入塔气)先在入塔气预热器E301壳程中预热升温至200℃后进入甲醇合成塔R301管程进行反映,反映后气体(出塔气)温度约为230~260℃,然后进入入塔气预热器E301管程与入塔气进行换热,温度降至90℃左右,再经甲醇水冷器E302进一步冷却,温度降至40℃以下,反映生成的甲醇等产物在此温度下几乎全数冷凝下来,气液混合物送入甲醇分离器V301进行分离,气体从分离器上部排出,按照系统压力情况和惰性气体含量情况一小部份气体由PRCA302调节后去转化工序作燃料,一部份去转化工序作返氢原料,另一大部份气体作为循环气送到循环机入口缓冲罐V104,经循环气紧缩机C103A/B紧缩升压后进入合成气混合罐V105,与新鲜气混合后送往合成塔打循环。
甲醇分离器中分离下来的粗甲醇,经液位调节阀LICA301控制减压后进入闪蒸槽V302,粗甲醇在闪蒸槽中压力降至(G),闪蒸出大部份溶解气体,闪蒸槽中的粗甲醇经液位调节阀LICA302控制去精馏工序粗甲醇贮槽V401,由闪蒸槽压力调节阀PICA303控制闪蒸槽压力,闪蒸气去燃料气管网。
由合成工序闪蒸槽来的粗甲醇,先进入粗甲醇槽V401,再经粗甲醇泵P401送出,经FIC-402调节流量后进入粗甲醇预热器E401,粗甲醇在预热器中与预精馏塔T401及精甲醇加压塔T402的再沸器E404及E405所排放的蒸汽冷凝液换热,预热至65℃左右,进入预精馏塔T401的上半部,此塔为浮阀塔,内设48块浮阀塔板,在第30、34、38块板上设有三根进料管线,正常生产时,粗甲醇由第34块板入塔,但最适宜的进料板位置,必需按照生产实践来肯定,其总的要求是:
在进料板上轻馏分的浓度与进料粗甲醇中轻馏分的浓度大体相等。
在预精馏塔第14块塔板上,设有Na0H溶液的进料管线,用碱液泵P409a/b,持续向塔内注入少量的NaOH的稀溶液,中和粗甲醇中的少量有机酸如甲酸,乙酸等,以避免粗甲醇中的有机酸被浓缩后对本系统的碳钢设备和管道产生侵蚀,尤其是避免对常常处于高温操作条件下的精甲醇加压塔T402、精甲醇常压塔T403底部及其再沸器列管的侵蚀。
加碱量的多少,取决于粗甲醇中酸性杂质的含量,本装置预期加碱量为浓度%的NaOH溶液50l/h左右,使预后甲醇溶液中的PH值在7~8之间。
预精馏塔塔顶气相的温度约为74℃,其相应的塔顶压力约为(G),塔顶气相的冷凝系统是由预塔冷凝器E402和膨胀气冷却器E403组成。
在预塔冷凝器中,只冷凝塔顶蒸汽的大部份,最好不过冷或极少过冷蒸汽冷凝液,在膨胀气冷却器中,则冷凝其余的塔顶蒸汽,使冷凝液降至30~40℃,这样既可以减少甲醇的损失,又可使粗甲醇中轻馏分的脱除接近最佳值。
剩下的不凝气体和大部份二甲醚等低沸点杂质和少量的甲醇蒸汽,从膨胀气冷却器排出,经调节阀PIC401控制压力后排至高点放空。
由预塔冷凝器和膨胀气冷却器排出的冷凝液进入预塔回流槽V402,经液位调节阀LICA407控制液位后再经预塔回流泵P402a/b升压,送回预精馏塔顶部作为回流。
若是预塔冷凝器冷凝太多,即冷凝液过冷较多,则须减少冷却水量,若是回流液中的轻馏分浓度较高,则通过TIC40l减少入膨胀气冷却器的冷却水量,增加不凝气的排出量。
预精馏塔所需的热量,由(G)低压蒸汽在立式热虹吸再沸器E404壳程中冷凝而提供,加热蒸汽的量由流量调节阀FIC-401控制再沸器排出的冷凝液量而控制。
预精馏塔底部的甲醇水溶液,叫预后甲醇,其温度约为85℃,经液位控制阀LICA401控制液位后,再经加压塔进料泵P403升压,进入精甲醇加压塔T402,由第6块塔板入塔,精甲醇加压塔为一浮阀塔,内有85块浮阀塔板。
从精甲醇加压塔塔顶排出的甲醇蒸汽温度约120℃入冷凝器/再沸器E406向精甲醇常压塔T403提供热量,加压塔顶的压力由压力调节阀PIC402控制,塔顶甲醇蒸汽冷凝后进入加压塔回流槽V403,由回流槽抽出部份甲醇经回流液冷却器E414,冷至约117℃经加压塔回流泵P404a/b升压,再经流量调节阀FRC403调节流量后入加压塔进行回流,其余的精甲醇经液位调节阀LICA403,调节液位后入加压塔精甲醇冷却器E407,冷却到40℃,产品经FR410送至精甲醇计量槽V406a/b。
精甲醇加压塔所需的热量,由(G)低压蒸汽在立式热虹吸再沸器E405壳程中冷凝来提供,加热蒸汽的量由流量调节阀FIC405控制再沸器排出的冷凝液量来控制。
由精甲醇加压塔底出来的甲醇溶液,经液位调节阀LICA402调节液位后送至精甲醇常压塔T403的下半部,此塔为一浮阀塔,内有85块浮阀塔扳,在第16、18、20块板上有三根进料管线,正常生产时,甲醇溶液由第18块板入塔。
其要求是:
在进料板上物料的组分与进料的组分大体上差不多。
精甲醇常压塔顶蒸汽的温度约为65℃,其相应的塔顶压力约0.0063MPa(G),塔顶蒸汽的冷凝系统是由常压塔冷凝器E408和常压塔精甲醇冷却器E409组成。
塔顶蒸汽经冷凝器冷却降至40℃进入常压塔回流槽V404,经液位控制阀LICA406控制液位后,再常常压塔回流泵P405a/b升压,部份甲醇经流量调节阀FIC406调节流量后入常压塔进行回流,其余部份作为产品经FR-411和加压塔精甲醇E407冷却器出来的精甲醇一路送至精甲醇计量槽V406a/b,再经精甲醇外送泵P408a/b升压,FRQ412计量(计量数据不做为最终产量数据,只起参考作用,准确数据要读罐液位来计算)后去销售车间。
以乙醇为主的重馏分,在精甲醇常压塔底部积聚,其富集区大约在6~10块塔板之间,故在第6、8、10块塔板上各设有一条侧线抽出管线,正常生产时,侧线抽出管线设在第8块塔板,抽出的液体叫侧线抽出物,用遥控阀HIC402控制入杂醇油冷却器E413冷却到40℃,进入杂醇油贮槽V407,再经杂醇油泵P410升压,送出本工序。
精甲醇常压塔塔底水中含甲醇约%(wt),温度约111℃,经液位控制阀LICA405控制液位后,经废水泵P406a/b升压,送至废水汽提塔T404处置。
废水汽提塔为填料塔,内有三段环矩鞍填料,进料有两股物料,即精甲醇常压塔塔底水,精甲醇常压塔侧线抽出物(一般去杂醇油贮槽)。
这两股物料进入废水汽提塔的第一、二段填料之间。
由转化工序来的压力为(G)的饱和蒸汽经压力调节阀PIC404将压力调节至(G),再经FIC404调节流量后直接从塔底进入。
塔顶排出的蒸汽主要为甲醇,其温度约为73℃,压力约为(G),塔顶蒸汽进人塔顶冷凝器E410中,其中大部份蒸汽被冷凝。
冷凝液借助位差流至塔顶作回流液,剩下未冷凝的蒸汽经遥控阀HIC401控制压力后排放,排至高点放空。
塔底水温度约为110℃,压力约为(G),含有少量的甲醇和微量的乙醇,经液位控制阀LICA404控制液位后,排至废水冷却器E411,冷却至40℃,经废水泵P407a/b升压后去工业水处置装置。
2.1.2燃料气流程叙述
来自装置天然气总管的燃料气(天然气)经压力调节阀PIC206调节压力后(压力控制在)进入燃料气混合罐V201,与合成工序来的弛放气充分混合后进入燃料气预热器F201-1进行预热,出口温度约为100℃,预热后的燃料气经燃料气压力调节阀PRC208调节,均匀进入36个转化炉炉顶烧嘴,由PRC-208按照炉子温度需要调节燃料气加入量,由HIC20一、HIC20二、HIC203控制各排烧嘴背压一致。
2.1.3炉水和蒸汽系统流程叙述
(1)脱盐水、锅炉给水流程
来自界外的脱盐水进入装置后一部份进入第一给水预热器F201-7中预热,出口温度约100℃,另一部份进入脱盐水预热器E205换热,出口温度约100℃,两部份脱盐水混合后通过脱氧槽液位调节阀LICA204由脱氧槽顶部进入脱氧槽V207,由LICA204控制上水量。
脱盐水进入脱氧槽后被由下向上的蒸汽充分加热,解析出水中的大部份物理氧,在脱氧槽下部与加入的联胺N2H4反映,将氧含量降至控制指标,给各汽包供水。
化学除氧方程:
N2H4+O2====2H2O+N2
由脱氧槽底部来的炉水(除氧后的脱盐水)加入氨水溶液后别离进入中压汽包给水泵P202A/B、低压汽包给水泵P203A/B和合成汽包给水泵P206A/B。
中压汽包给水泵P202A/B出口炉水通过PV217调整压力后,经FI209流量计首先进入中压给水预热器E203,与管程中的高温转化气进行换热,出口温度约170℃,换热后的炉水进入锅炉给水第二预热器F201-2进行换热,出口温度约220℃,出口炉水一部份进入1#中压汽包V203,一部份进入2#中压汽包V205,供汽包上水,由各汽包的液位控制阀控制上水量。
低压汽包给水泵P203A/B出口炉水通过FI210流量计进入低压锅炉给水预热器E204,与管程中的转化气进行换热,出口炉水温度150℃,换热后的炉水经调节阀LICA203控制进入低压汽包V206,由LICA203控制上水量。
合成汽包给水泵P206A/B出口炉水通过LICA303进入合成汽包V303,由LICA303控制合成汽包上水量。
(2)蒸汽系统流程叙述
炉水进入1#中压汽包V203后,沿下降管进入烟气废锅F201-3与管外的对流段高温烟气充分换热,在管内产生饱和蒸汽,沿上升管返回汽包,汽液两相在汽包中充分分离,蒸汽由汽包顶部经压力调节阀PRC-209调压后进入中压蒸汽管网。
炉水进入2#中压汽包后,沿下降管进入转化气1#废锅E201壳程,与管程中的高温转化气充分换热,在壳程产生饱和蒸汽,沿上升管返回汽包,汽液两相在汽包中充分分离,蒸汽由汽包顶部经压力调节阀PRC212调压后进入(G)中压蒸汽管网。
炉水进入合成汽包V303后,沿下降管进入合成塔R301壳程,与管程中的合成反映气充分换热,在壳程内产生饱和蒸汽,沿上升管返回汽包,汽液两相在汽包中充分分离,蒸汽由汽包顶部压力调节阀PRCA301调压后并入(G)中压蒸汽管网。
(G)中压蒸汽一部份进入汽水分离器V202分离掉蒸汽中所带的水,蒸汽从V202顶部出来经FRC202调节流量后进入蒸汽过热器F201-4,被管外对流段的高温烟气加热,出口蒸汽温度约370℃,出口过热蒸汽与工艺原料气(天然气和二氧化碳的混合气)混合,作为原料气进转化管参加转化反映。
另一部份经压力调节阀PRC210调节压力后并入(G)低压蒸汽管网。
炉水进入低压汽包V206后,沿下降管进入转化气2#废锅E202壳程与管程中的转化气充分换热,在壳程内产生饱和蒸汽,沿上升管返回汽包,汽液两相在汽包中充分分离,蒸汽由汽包顶部经压力调节阀PRC213调压后进入(G)低压蒸汽管网。
(G)的低压蒸汽大部份减压后去精馏工序,作为预塔和加压塔再沸器蒸汽,一部份直接作为精馏汽提塔蒸汽;一部份经压力调节阀PIC215调节后进入脱氧槽,为脱氧槽提供蒸汽;还有一部份作为联胺槽、氨水槽和磷酸盐槽的搅拌蒸汽利用(中断利用);剩下的多余蒸汽经压力调节阀PIC214A调压后送入外界低压蒸汽管网。
在各汽包(除V206)中,别离加入了磷酸盐溶液,目的是为了避免炉水结垢,在各汽包中部位置设置有持续排污点,在各汽包底部、各废锅和合成塔壳程底部都设有中断排污点,要按时按要求进行排污操作,确保炉水质量。
2.2工艺原理及工艺参数
2.2.1紧缩工艺原理
本工序共有三组紧缩机,均为一开一备,共六台。
为使天然气达到转化压力,天然气紧缩机未来自界外的天然气从(G)加压到(G),送到200#转化工序。
新鲜气紧缩机未来自转化工序的新鲜气从(G)加压至(G)送到合成气混合罐V105。
循环气紧缩机未来自300#合成工序的循环气从(G)加压至(G),送到合成气混合罐V105,与加压后的新鲜气混合后送到300#合成工序。
2.2.3转化工艺原理
本工序是将天然气、二氧化碳组成的混合气和蒸汽发生蒸汽转化反映,从而制得含CO、CO2和H2的新鲜气。
(1)因少量硫会使转化催化剂中毒并失去活性,为了知足蒸汽转化时转化催化剂的要求,制气前需将硫化物脱除净,另外,甲醇合成铜基催化剂对硫的作用也十分敏感,催化剂对硫化物、氮化物、重金属等的中毒,都会影响其活性和利用寿命,因此,制气前须除去原料气中的硫化物。
我工序脱硫由MF-2脱硫和氧化锌脱硫两部份组成,其脱硫原理别离如下:
a.MF-2脱硫:
MF-2型脱硫剂中的氧化锰、氧化铁等可热解或氢解有机硫,同时将硫化氢吸收掉,反映如下:
热解:
2CH3SH====2H2S+C2H4
CH3SCH3====H2S+C2H4
氢解:
COS+H2====H2S+CO
CS2+4H2====2H2S+CH4
CH3SH+H2====H2S+CH4
CH3SCH3+H2====H2S+C2H6
吸收硫化氢:
H2S+MnO====MnS+H2O
H2S+ZnO====ZnS+H2O
3H2S+Fe3O4+H2====3FeS+4H2O
b.氧化锌脱硫剂:
不仅能脱除硫化氢之类的无机硫,而且可以脱除硫醇、硫氧化碳等有机硫,脱硫的主要化学反映有:
脱除H2S:
ZnO+H2S====ZnS+H2
(1)
脱除RSH:
ZnO+C2H5SH====ZnS+C2H50H
(2)
ZnO+C2H5SH====ZnS+C2H4+H2(3)
当气体中有氢存在时,硫氧化碳、二硫化碳转化成硫化氢,然后被氧化锌吸收。
COS+H2====H2S+C0(4)
CS2+4H2====2H2S+CH4(5)
本装置中,氧化锌脱硫是按反映
(1)来完成,这是一个放热反映,平衡常数随温度升高而减小。
氧化锌脱硫剂的活性温度范围为270~400℃,随着温度的升高,反映速度显著增大。
MF-2脱硫剂还原见后附资料。
MF-2脱硫剂还原利用说明:
MF-2脱硫剂中的MnO2和Fe2O3等利用前需用H2或CO还原,还原反映如下:
MnO2+H2====MnO+H2O
MnO2+CO====MnO+CO2
3Fe2O3+H2====2Fe3O4+H2O
3Fe2O3+CO====2Fe3O4+CO2
由于还原反映放出大量热,若是控制不妥,则可能发生脱硫剂床层温度“飞升”现象,损坏脱硫剂和设备,所以脱硫剂的升温还原应严格按规定程序进行。
①升温还原介质最好用氮气或净化后的原料气(在升温进程中可加入1~5%氢),也可直接利用原料气;
升温还原压力控制在~(G),空速维持在300时-1以上(气体流速应大于米/秒);
进入脱硫槽的温度尽快将床层温度升至150℃,恒温2~4小时后,再将床层温度升至180℃(还原从低于180℃开始),再恒温1~2小时,观察脱硫剂上层温度有无“飞升”现象;
床层温度在180℃恒温期间如按
、
条件进行操作,在整个升温还原进程中一般不会发生超温现象。
果真如此,可按30~50℃/小时的升温速度将床层升温至250℃,恒温2~4小时后,再继续将床层升温至400℃,再恒温14~16小时,升温还原结束;
如床层出现温度“飞升”现象(30秒内床层温度飞涨50℃左右),应采取停止预热,加大气量(即增大空速)带走床层反映热以迅速控制床层温度不超过500℃。
迫不得已,也可采用切断升温还原气,加入蒸汽带走反映热。
整个床层的温度“飞升”消除后,方可逐渐将脱硫剂床层的温度升至400℃,再恒温14~16小时,升温还原结束。
升温还原结束进程中出口气CO2、O2和硫含量合格后,即可将原料气通入下一工序。
(2)天然气的蒸汽转化
天然气蒸汽转化,是以水蒸汽为氧化剂,在Ni催化剂的作用下,将天然气中的烃类物质转化,取得合成甲醇的原料气,这一进程为强吸热进程。
生产是在天然气(本装置中尚配入适量的CO2气)中配入水蒸汽,使H2O/C>(vol),由转化炉辐射段燃烧燃料气提供反映所得的热量,在Ni催化剂层发生如下反映:
CH4+H2O(g)====C0+3H2kJ/mol
CnH2n+2+nH2O(g)====nCO+(2n+1)H2-Q
C0+H2O(g)====C02+H2+kJ/mol
CH4+2H2O====CO2+4H2/mol
C2H6+2H2O====C0+5H2-Q
副反映主要有:
2CO====C+C02+kJ/mol
CO+H2====C+H2O–kJ/mol
CH4====C+2H2–kJ/mol
由于烃类蒸汽转化反映是一个吸热、体积增大的可逆进程,故提高转化温度对反映有利,从热力学观点看,提高压力对反映进行不利,但适当合理的提高转化压力,可加速反映速度,减少催化剂用量和设备投资,综合经济指标较好;另外,在必然的温度和压力下,增大水碳比,不仅可以提高烃类的转化率,还可避免催化剂析碳;空速对转化反映也有影响,增大空速虽然可以提高设备的生产能力,但如果超过允许范围就会使系统阻力增大,转化率降低,残余甲烷含量将上升。
后三个反映是造成转化炉结碳的原因,应该尽力避免。
2.2.5合成工艺原理
以CO、CO2和H2为原料,在铜基甲醇催化剂的作用下反映生成甲醇,大体反映式:
C0+2H2====CH30H+kJ/mol
C02+3H2====CH30H+H2O+kJ/mol
实际上,这二种反映组份之间和其与生成物之间,还会发生许多其它反映,例如:
C02+H2====C0+H2O
CO+H2====HCH0(甲醛)
2CO+4H2====(CH3)2O+H2O(二甲醚)
2CO+4H2====C2H50H+H2O(乙醇)
4CO+8H2====C4H90H+3H2O(丁醇)
另外,尚有甲酸甲酯、乙酸甲酯及其它高级醇、高级烷烃类生成。
选用适当的催化剂和操作条件,使反映大体上只向生成产品甲醇的方向进行,而使杂质的生成量减至最小,以铜为主体的铜基催化剂对于甲醇合成具有极高的选择性,而且在不太高的压力及温度下就具有很高的活性,但这种催化剂对硫、氯这样的毒物超级敏感,要求合成气的净化极完全,不然其活性将很快丧失,再就是它的耐热性较差,要求维持催化剂在最佳的温度下操作。
铜催化剂一般可以在270~290℃下操作,视催化剂的型号及反映器型式不同,其最佳操作温度范围也略有不同,管壳式反映器的最佳操作温度在230~260℃。
在铜催化剂上合成甲醇,适合的压力是~MPa(G),对于合成气中C02含量较高的情况,压力的提高对提高反映速度有比较明显的效果,由于本装置规模较小,选择合成压力为~(G),若进一步提高操作压力效果不显著,反而多耗能量。
合成气的成份对甲醇合成反映的影响较大,由前述反映式可见要降低能耗,应采用较高的C02浓度的合成气是适合的,若合成气中C02含量太高,会加重精馏工序的负担,并增加了能耗。
适合的新鲜气成份是:
(H2-CO2)/(CO+CO2)≈
适合的合成气成份是:
(H2-CO2)/(CO+CO2)≈
甲醇合成是强烈的放热反映,必需在反映进程中不断的将热量移走,反映才能正常进行,管壳式反映器利用管子与壳体间副产中压蒸汽来移走热量,合成反映温度的控制是依托控制蒸汽压力来实现的,必然的蒸汽压力对应着必然的饱和蒸汽温度。
三.装置生产原理
1.气体紧缩的原理
由于气体分子之间间距较大,分子间作使劲较弱,所以通过紧缩机等设备对气体做功,使分子间距变小,分子间作使劲变大,其宏观表现为气体体积缩小,压力升高。
2.天然气蒸汽转化原理
在反映器中必然温度和压力下,通过Ni催化剂的催化作用,使天然气和蒸汽反映生成CO、CO2和H2。
3.合成原理
在反映器中必然温度和压力下,通过甲醇合成铜催化剂的催化作用,使合成气中的CO、CO2和H2反映生产甲