储物箱的注射模具设计.docx
《储物箱的注射模具设计.docx》由会员分享,可在线阅读,更多相关《储物箱的注射模具设计.docx(36页珍藏版)》请在冰豆网上搜索。
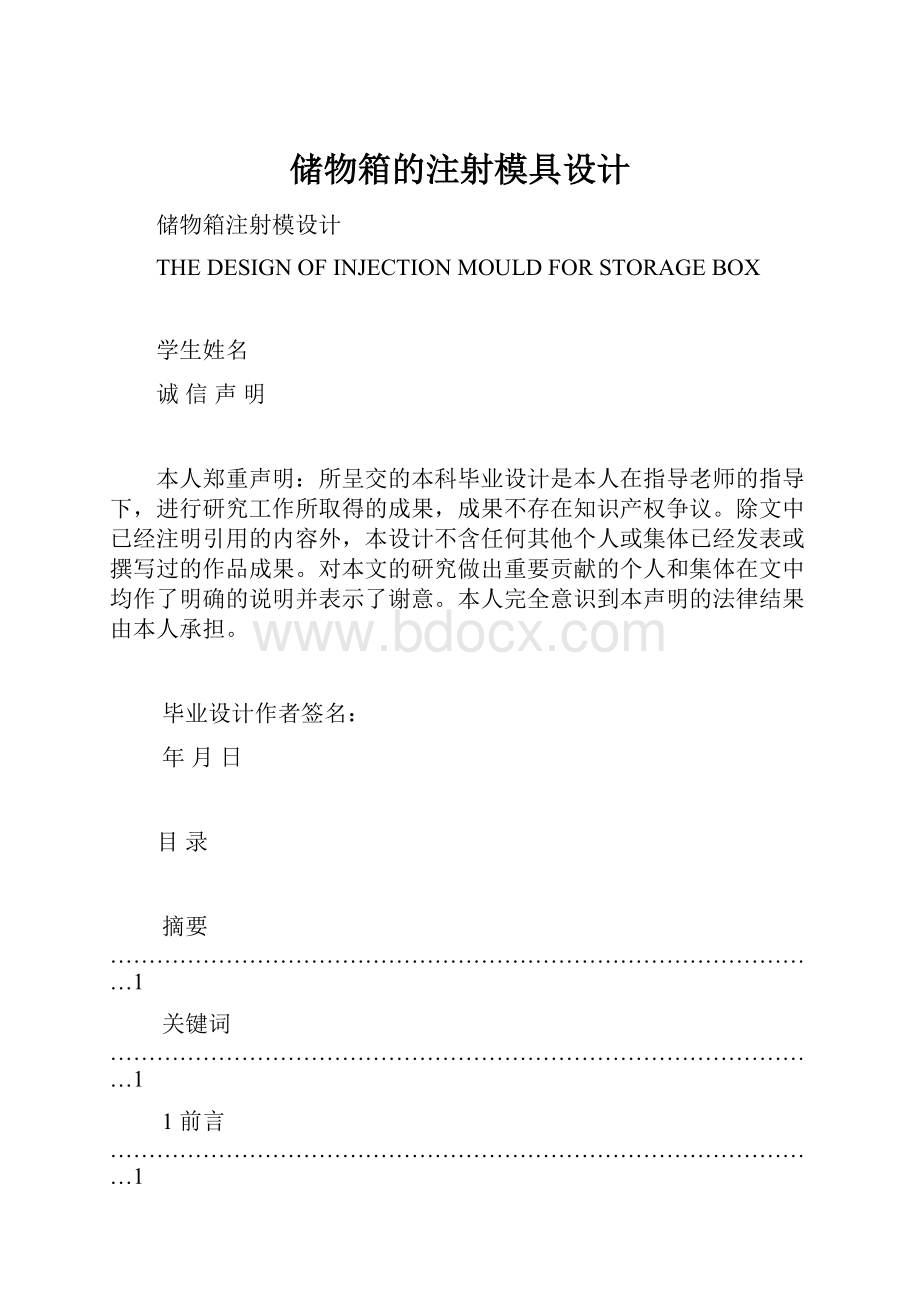
储物箱的注射模具设计
储物箱注射模设计
THEDESIGNOFINJECTIONMOULDFORSTORAGEBOX
学生姓名
诚信声明
本人郑重声明:
所呈交的本科毕业设计是本人在指导老师的指导下,进行研究工作所取得的成果,成果不存在知识产权争议。
除文中已经注明引用的内容外,本设计不含任何其他个人或集体已经发表或撰写过的作品成果。
对本文的研究做出重要贡献的个人和集体在文中均作了明确的说明并表示了谢意。
本人完全意识到本声明的法律结果由本人承担。
毕业设计作者签名:
年月日
目录
摘要…………………………………………………………………………………1
关键词…………………………………………………………………………………1
1前言…………………………………………………………………………………1
1.1塑料模具研究的意义……………………………………………………………2
1.2国内外研究及其发展趋势………………………………………………………2
2塑件成型工艺性分析………………………………………………………………3
2.1塑件分析…………………………………………………………………………3
2.2塑件的结构及成型工艺分析……………………………………………………3
2.2.1结构分析…………………………………………………………………4
2.2.2成型工艺分析……………………………………………………………4
2.3热塑性塑料的注射过程及工艺参数……………………………………………4
2.3.1注射成型过程……………………………………………………………4
2.3.2注射过程…………………………………………………………………4
2.3.4塑件的后处理……………………………………………………………5
2.3.5聚丙烯的注射工艺参数…………………………………………………5
3模具结构形式的确定………………………………………………………………6
3.1分型面位置的确定………………………………………………………………6
3.2型腔数量的确定…………………………………………………………………6
3.3浇注系统形式的确定……………………………………………………………6
3.3.1浇口形式的确定………………………………………………………6
3.3.2浇口数量的确定…………………………………………………………6
3.4推出机构的确定…………………………………………………………………7
3.5抽芯机构的确定…………………………………………………………………7
3.6选择模架………………………………………………………………………7
4模具设计及其理论计算……………………………………………………………8
4.1热流道系统的计算和结构尺寸的确定…………………………………………8
4.1.1流道系统尺寸的确定……………………………………………………8
4.1.2热流道板结构设计………………………………………………………9
4.2注射机型号的确定……………………………………………………………12
4.3温度调节系统的设计…………………………………………………………14
4.3.1冷却系统………………………………………………………………14
4.3.2冷却系统的计算………………………………………………………14
4.3.3凸凹模加热计算………………………………………………………16
4.4排气系统设计…………………………………………………………………16
4.5脱模推出机构的设计…………………………………………………………17
4.5.1压缩空气顶出的基本要求……………………………………………18
4.5.2顶出方式………………………………………………………………18
4.5.3脱模力的计算…………………………………………………………18
4.5.4定模脱模力……………………………………………………………20
4.6成型零件设计…………………………………………………………………20
4.7安装尺寸的校核………………………………………………………………21
4.8典型零件的制造工艺…………………………………………………………21
4.8.1型腔的加工工艺………………………………………………………21
4.8.2凸模的加工工艺………………………………………………………22
4.9模具工作过程…………………………………………………………………22
5结论………………………………………………………………………………23
参考文献……………………………………………………………………………23
致谢…………………………………………………………………………………24
储物箱注射模设计
学生:
李尹
指导老师:
董亮
(湖南农业大学工学院,长沙410128)
摘要:
本文主要内容是通过分析储物箱的工艺特点,详细介绍了储物箱的结构设计和模具设计的过程以及要点,设计包括了储物箱的塑件结构的设计方法,分型面外置的选择,模具型腔数目的确定和模架的选择,以及模具分型面和推出结构等设计过程。
整个设计过程表明该模具能够达到此塑件所要求的成型工艺和质量。
关键词:
储物箱;塑料模具;注射模;分型面
TheDesignofInjectionMouldforStorageBox
Student:
LiYin
Tutor:
DongLiang
(CollegeofEngineeringHunanAgriculturalUniversity,Changsha410128)
Abstract:
Thispaperismainlyintroducedtheprogressandthemainpointsofthelockerstructuredesignandthediedesignthroughtheanalysisofthetechnologyofthestoragebox.Itincludesthedesignmethodoftheplasticstructurepartsofthelocker,theselectionoftheexternalpartingsurface,confirmingthenumberofmoldcavityandchoosingformwork,andthedesignprocessofmoldpartingsurfaceandpushmechanism.Thewholedesignprocessillustratesthatthemoldcanfulfilltherequirementsofmoldingprocessandqualityoftheplasticparts.
Keywords:
storage;mouldofplastics;injectionmould;partingline
1前言
1.1塑料模具研究的意义
塑料工业是当今世界上增长最快的工业门类之一,而注射模具是其中发展最快的的种类。
因此,研究注射模具对了解塑料产品的生产过程和提高产品质量有很大的意义。
模具行业是制造业的重要组成部分,也是国民经济的基础工业。
受到政府和企业的高度重视,具有广阔的前景。
通过本次设计可以使我掌握注射模的模具结构机构的设计,对CAD,PRO/E等一系列软件的应用熟练,让我们能更快适应生产工作。
培养自己综合运用所学基础和专业基本理论、基本方法分析和解决测量与控制及其它相关工程实际问题的能力,在独立思考、独立工作能力方面获得培养和提高。
随着塑料制品在机械、电子、交通、国防、建筑、农业、等各个行业广泛应用,对塑料模具的需求日益增加,塑料模在国民经济中的重要性也日益突出。
模具作为一种高附加值和技术密集型产品,其技术水平的高低已经一个国家制造业水平的重要标志之一。
1.2国内外研究现状及发展趋势
我国在注塑模CAD技术开发研究与应用方面起步较晚。
从20世纪80年代中期开始,国内部分大中型企业先后引进了一些国外知名度较高的注塑模CAD系统。
同时,某些高等学校和科研院所也开始了注塑模CAD系统的研制与开发工作,我国注塑模CAD/CAE/CAM研究始于07年代末,发展较为迅速多年来,我国对注塑模设计制造技术及其CAD的开发应用十分重视,在“八五”期间,由北京航空航天大学、华中理工大学、四川联合大学等单位联合进行了国家重点科技攻关课题“注塑模CAD/CAE/CAM集成系统”,并于1996年通过鉴定,部分成果己投入实际应用,使我国的注塑模CAD/CAE/CAM研究和应用水平有了较大提高.目前拥有自主版权的软件有,华中理工大学开发的塑料注塑模CAD/CAE/CAM系统HscZ0,郑州工业大学研制的2一MOLD分析软件等.这些软件正在一些模具企业中推广和使用,有待在试用中逐步完善。
这些项目的成果对促进我国注塑模CAD技术的迅速发展起了重要作用,使我国注塑模CAD技术及应用水平很快提高。
目前,我国经济仍处于高速发展阶段。
一方面,国内模具市场将继续高速发展,另一方面,模具制造也逐渐向我国转移以及跨国集团到我国进行模具采购趋向也十分明显。
因此,放眼未来,模具技术的发展趋势主要是模具产品向着更大型、更精密、更复杂及更经济的方向发展,模具产品的技术含量不断提高,模具制造周期不断缩短,模具生产朝着信息化、无图化、精细化、自动化的方向发展,模具企业向着技术集成化、设备精良化、产批品牌化、管理信息化、经营国际化的方向发展。
近二十多年间,国外注塑模CAD/CAE技术发展相当迅速。
70年代许多研究者对一维流动进行了大量研究,由最初的CAD技术和CAM技术以图纸为媒介传递信息向CAD/CAM一体化方向发展。
80年代初开展三维流动与冷却分析并把研究扩展到保压分子取向以及翘曲预测等领域。
80年代中期注塑模CAD/CAE进入实用阶段,出现了许多商品化注塑模CAD/CAE软件,比较著名的有:
1.澳大利亚MOLDFLOW公司的MOLDFLOW系统;2.美国PTC公司的Pro/Engineer软件;3.美国UG公司的UGllUNIGRAPHICSl系统等等.这些先进软件的熟练掌握极大地促进了国外模具行业的发展。
因此,未来的一段时间内,他们将朝着大型、精密、复杂与长寿命模具的方向发展[1]。
2塑件成型工艺分析
2.1塑件分析
塑件模型如图1下所示。
塑件名称:
聚丙烯PP.色调:
半透明、白色生产纲领:
大批量
图1储物箱
Fig1Stroragebox
2.2塑件的结构及成型工艺分析
2.2.1结构分析:
该塑件为储物箱,结构应近可能的简单,且强度和刚度应满足需要,在底部设有较多的加强肋板,在上边缘设有一圈弧形加强肋以增加储物箱的刚度和强度。
该塑件长端有两处安装提手的孔,当储物箱上盖盖上以后,安装到孔中的提手又起着卡扣作用,该部位为受力较集中的部分,故此处的壁厚应该适当的加厚,已满足其力学的性能的要求。
当箱子中装有东西多而重量较大搬运困难时,特意在箱子底部设计了有安装滚轮轴的卡槽,滚轮在轴上转动,而滚轮轴安装在卡槽中,以便于箱子在室内移动[2]。
2.2.2成型工艺分析
注射模精度等级:
采用一般精度4级。
脱模斜度:
该塑件壁厚约为3mm,其脱模斜度查表得到聚丙烯PP其型腔脱模斜度为:
25°~45°,其型芯脱模斜度为:
20°~45°。
由于该塑件没有狭小部分,且塑件整体造型已具备了一定的斜度,所以只有塑件底部肋板处放脱模斜度取1°。
2.3热塑性塑料的注射成型过程及其工艺参数
2.3.1注射成型过程
注射成型工艺过程包括:
成型前的准备,注射成型过程以及塑件的后处理三个阶段[3]。
2.3.2成型前准备
分析检验成型物料质量:
根据塑料工艺性能要求,检验其各种性能指标,如含水量等。
对于该塑件材料PP参考文献知道聚丙烯PP吸水率‹0.03%,允许水含量0.05%~0.20%。
由于该塑料不易吸水,故可以不进行干燥处理。
2.3.3注射过程
注射过程是塑料转变成塑件的主要阶段。
它包括加料、塑化、注射、保压、冷却定型和脱模等步骤。
1)加料:
由注射机的料斗落入一定量的塑料,以保证操作稳定、塑料塑化均匀、最终获得良好的塑件。
通常其加料量由注射机计量装置来控制。
2)塑化:
塑化是指塑料在料筒内经加热达到熔融流动状态,并且有良好的可塑性全过程。
3)注射:
注射机用柱塞或螺杆推动具有流动性和温度均匀的塑料熔体,从料筒中经过喷嘴、浇注系统,直接压入模腔。
4)保压:
保压时自注射结束到柱塞或螺杆开始后移的这段过程,即压实工序。
5)冷却定型:
当浇注系统的塑料已经冷却凝固。
继续保压不在需要,此时可退回柱塞或螺杆,由于冷却水、空气等冷却介质,对模具进一步冷却,这一阶段称冷却定型、实际上冷却定型过程从塑料注入型腔就开始,它包括从注射完成、保压到脱模前这段时间[4]。
6)脱模:
塑件冷却到一定温度即可开模,在推出机构的作用下将塑件推出模外。
2.3.4塑件的后处理
塑件进行注射成型后,除去浇口凝料。
修饰浇口处余料及飞边毛刺外,常需要进行适当的后处理,借以改善和提高塑件性能,塑件的后处理主要是退火和调湿处理。
通过查找文献知道该塑料不需要任何后处理。
2.3.5聚丙烯PP的注射工艺参数
1﹚料筒温度:
30℃~220℃
2﹚熔料温度:
220℃~250℃
3﹚料筒恒温:
220℃
4﹚模具温度:
80℃~90℃
5﹚注射压力:
PP具有很好的流动性,避免采用过高的折射压力,一般在80MPa~140MPa之间,一些薄壁包装容器可达180MPa.
6﹚保压压力:
避免制品产生壁缩,需要较长时间对制品进行保压:
约为
注射压力的30%~60%。
7﹚背压:
2MPa~5MPa
8﹚注射速度:
对薄壁包装容器需要高的注射速度;中等注射速度往往比较适合于其他类的塑料制品。
9﹚螺杆转速:
高速螺杆转速﹙线速度约为1.3m/s﹚是允许的,只需要满足冷却时间结束前完成塑化过程就可以。
10﹚计量行程:
0.5D~4D;4D的计量行程为熔料提供足够长的驻留时间是很重要的。
11﹚残料量:
2mm~8mm,取决于计量行程和螺杆转速。
12﹚预烘干:
不需要;如果储藏不好,在80℃的温度下烘干1h就可以。
13﹚回收率:
可达100%回收。
14﹚收缩率:
1.2%~2.5%;收缩程度高;24h后不会收缩。
15﹚浇口系统:
点式浇口或多点浇口;加热式热流道,保温式热流道;浇口位置在制品最厚点,否则易发生大的收缩。
3模具结构形式的确定
3.1分型面位置的确定
在塑件设计阶段,就应该考虑成型时分型面得形状和位置,否则无法完成模具成型。
在模具设计阶段,应首先确定分型面和浇口的位置,然后选择模具的结构。
该塑件在进行结构设计时已经充分考虑到了模具的分型面,同时从所提供的塑件图样可以看出该塑件为典型的箱体。
将分型面设计在塑件上边缘外援处,在提手处,将分型面沿提手最大外援处设置分型面,以方便出模。
3.2型腔数量的确定
当塑件分型面位置确定之后,就需要考虑是采用单型腔模还是多型腔模。
一般来说,大型塑件和精度要求高的小型塑件优先采用一模一腔的结构,此塑件属于大型塑件,故采用一模一腔结构形式[5]。
3.3浇注系统形式的确定
3.3.1浇口形式和位置的确定
该塑件属于大型腔盒形件,分型面只能采用一个,根据塑件结构不能采用侧浇口、潜伏式浇口或护耳式浇口,因为浇口完全偏置一边不利进料。
只能采用直接浇口或点浇口,浇口位置在塑件底部。
3.3.1浇口数量的确定
在确定塑件的浇口时,还应考虑塑料熔体所允许的最大流动距离比,当采用直接浇口时,如图1可估算出流动比K=L/t=230,这在PP塑料的流动比范围之内,基本符合要求。
但采用直接浇口塑件上印痕较大,不利于塑件的美观和浇口处的力学性能,流程比也接近于上限值,不利于塑料熔体对型腔的填充。
若采用普通流通道点浇口两点进料的话,在定模部分必须要有一个分型面一边取出浇注系统的凝料,这样模具结构相当的复杂而又浪费材料,显然也不是可取的。
如果采用热流道点浇口,上述问题不复存在,是一个较好的解决方案。
在该模具中使用主流道杯,热流道板,浇口喷嘴都采用加热式的结构,热流道如图2下所示。
1—浇口;2—喷嘴分流道;3—热流道分流板4—主流道
图2热流道布置示意图
Fig2Hartingdecoratesschemes
3.4推出机构的确定
该塑件属于大型腔薄壁型半透明塑件,对表面质量要求很高,在塑件表面不允许有推杆痕迹,同时塑件的推模力也比较大,因此经过反复的考虑,决定采用气动推出,所以标准架设在动模的推出机构就可以省略。
这样降低了模具的高度,也节约了成本。
3.5抽芯机构的确定
提手处的两个小孔应用侧抽芯来成型,但塑件全部位于定模型腔内,若采用机动抽芯,在动模部分还要设置一个分型面,对于大型模具来说,尽量不要设置多个分型面,因为移动的零件多了,对模具的强度、刚度和精度都不利,因此提手小孔可采用液压或气动来完成抽芯。
对于成型滚轮轴卡扣槽部分,在定模采用四个镶件滑块来成型,为了使该模具能够长寿命工作,若采用强制脱模以避免侧向抽芯,模具的可靠性不高,同样采用液压或气动抽芯,模具结构不太负责,而可靠性提高了[6]。
3.6选择模架
为了将该设计和工厂模具设计相结合,在此使用Pro/E软件对该塑件进行分型面设计。
大体步骤如下,先在Pro/E里对塑件进行建模,然后进入Pro/E的模具设计模块,将塑件模型调入,然后使用公式1=Scp,Scp值为0.02设置该塑件的收缩率,然后增加体积块,体积块的尺寸按照模架的动模板和定模板尺寸来定义,再设计分型面,并通过分型面将模具动模和定模板分开。
以达到分模的目的。
由于该塑件外形较大,故不再在定模中设置模仁,模架中的A板直接加工出型腔来,而动模的主型芯应单独加工出来,然后镶入动模固定板中,这样能够节省材料和加工工时。
参考国家标准初步选用直接浇口型模架,型号A80100-420×160GB/T12555-2006。
因为该模具采用气体推出,所以动模部分的推出机构及其零件都不需要,所以在原来模架的基础上省去了部分零件,但又采用热流道,又必须加一块安放热流道板的型腔垫板,所以形成了定模三板块(定模座板,型腔垫板和凹模型腔板),动模二块板(动模座板和凸模固定板)组成,简化的模架[7]。
4模具设计及其理论计算
在对模具的分型面、型腔数量、浇注系统的形式和模具结构初步确定以后,就应对模具的各个系统进行详细的分析和计算。
并最终确定各个工作零件的尺寸。
4.1热流道系统的计算和结构尺寸的确定
在本设计的热流道系统中,流道比较简单,如图2所示,且为平衡式布置,所以不需要进行复杂的流变学计算。
而热流道喷嘴是标准件,所以先按塑料熔体通过浇口允许的剪切速率来初步确定浇口直径,然后在计算相应的其他流道尺寸。
最后根据热流道尺寸确定其他结构尺寸。
4.1.1流道系统尺寸的确定
1﹚所需注射量的计算。
对于该设计,提供了塑料图样,据此在Pro/E中建立模型并对此分析,可知塑件体积为V1≈2.7×10³㎝3
2﹚喷嘴浇口尺寸的确定。
注射时间根据类似产品取10s,
则主流道体积流率Qs=V/t=2.7×1000÷10=270cm³/s
(1)
分流道的体积流率Qr=Qs/2=270/2=135cm³/s
(2)
根据表查数据,PP最大允许的剪切速率γ=105s-1,而喷嘴浇口是最小的部位,用此剪切速率求出浇口直径。
Dg=
=0.24㎝(3)
而热流道喷嘴浇口直径2.7mm、3.9mm、4.5mm等标准尺寸,而本设计浇口采用开放式直接浇口带有一段凝料,有利于布置水道对浇口进行冷却,储物箱底部的肋板高为20mm,凝料长定位30mm比较合适。
由于凝料有一个脱模斜度,通过计算,浇口直径取4.5mm,脱模斜度取3°,流道最小直径为
Dg=4.5-2×30tan1.5°=2.93mm(4)
再校核最小截面处的剪切速率
γG=32Qg/πDg³=54695/s<105s-1(5)
剪切速率符合要求。
3﹚喷嘴流道直径的确定。
对低粘度PP,流道剪切速率取γ=1000s-1进行初步估算,因此喷嘴流道直径为:
Dr=
=1.112㎝(6)
取标准直径Dr=1cm,则分流道剪切速率为
γR=32Qr/πDr3=1375.8s-1(7)
在5×100~5×1000s-1,比初取值大37..58%,如果分流道直径取12mm,剪切速率就显得有些小,所以分流道剪切速率合理。
考虑到喷嘴安装方面等因素,参考文献中图,可以采用标准喷嘴BP25型.
4﹚流道板分流道直径的确定。
根据热流道喷嘴与流道板的安装结构、热流道板分流道直径比喷嘴道直径大0.5mm~1mm,取分流道直径为11mm。
与上面计算值11.12mm相差不大,剪切速率在预定的范围内,可行。
5﹚主流道直径尺寸的确定。
本设计的分流道仅有两条,且分流道的剪切速率不太大,所以主流道直径也取11mm,与分流道直径一样大,主流道剪切速率为
γs=32Qs/πDs3=2067.3s-1(8)
在5×100~5×1000S,主流道剪切速率合理[8]。
4.1.2热流道板结构设计
热流道板应该具有良好的加热和绝热设施,保证加热器安装方便和温度控制有效。
热流道板根据浇口数量和位置的不同,可分别采用Ⅰ字、H字等各种外形。
该塑件结构比较简单确定采用两点进料,故采用Ⅰ字型热流道板。
分流道通常用圆形截面直径一般在1mm~5mm.流道转折处应圆滑过渡,防止塑料熔体滞留。
分流道端孔用细牙螺栓堵头封住并用铜质或聚四氟乙烯封垫圈防漏。
热流道板应该选用比热容小和热传导率高的材料,通常采用中碳钢和高强度的铜合金制造,本设计热流道板采用H13中碳钢。
1﹚热流道板几何尺寸的确定。
根据上述的计算,主流道、分流道直径取11mm,两浇口之间的距离取260mm,流道采用外加热的方式,在流道板铣削嵌入电加热器的槽,考虑到流道板的固定和其他零件的连接等因素。
2﹚流道板加热功率的计算。
流道板加热功率,是在一定时间内流道板从室温加热升温到塑料熔体注射温度所需要的功率。
当流道板达到给定的温度时,由温度调节器自动控制,补偿热损失功率,维持热流道温度恒定。
流道板升温加热功率,在热流道系统初步设计完成,获知了流道板的体积后,按质量m的经验公式计算。
以每1kg钢升温需100W电热功率计算。
小模具可增大些比值,升温时间可少于20min,而大型模具要减小比值。
片面追求快速升温,不利于电热加热和温度调节系统的设计。
加热流道板所需要的功率有三部分组成。
其一是达到设置注射温度所需电功率;其二是补充流道板的传导、对流和辐射热损耗功率;其三是考虑电网电压波动影响和加热器的热效率。
工程设计时,计算流道板的加热器功率公式如下:
P=mc/60tη0(9)
式中P——流道板加热器的电功率(kw)
m——流道板的质量(kg)
流道板质量,通过在Pro/E建模后,进行质量分析,密度为7.85kg/dm³,其质量为m=9.27kg。
C——流道板材料的比热容[kJ/(kg•℃)],对于钢材,C=0.48kJ/(kg•℃);
T——流道板的加热