模具制造工艺复习题张荣清.docx
《模具制造工艺复习题张荣清.docx》由会员分享,可在线阅读,更多相关《模具制造工艺复习题张荣清.docx(21页珍藏版)》请在冰豆网上搜索。
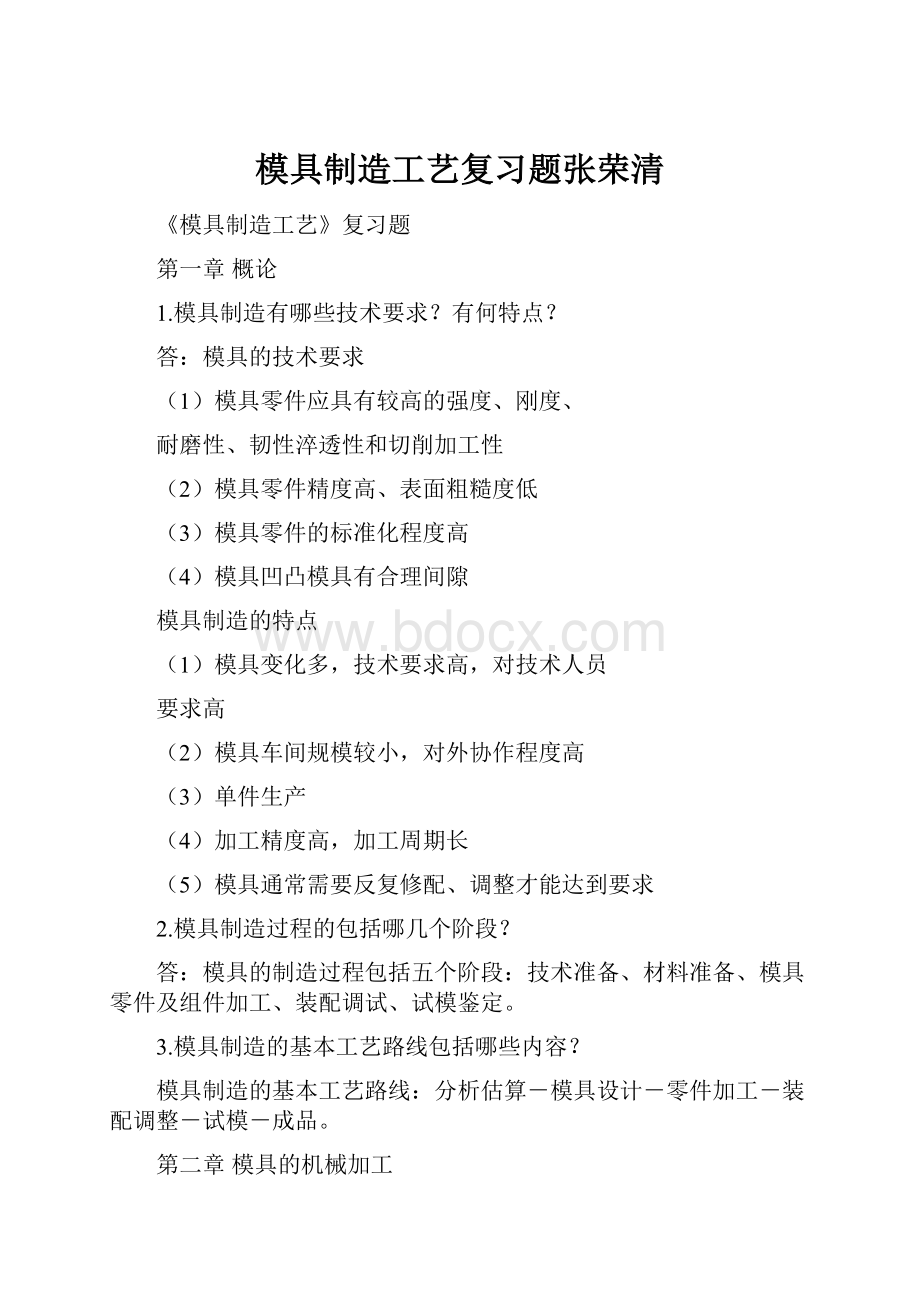
模具制造工艺复习题张荣清
《模具制造工艺》复习题
第一章概论
1.模具制造有哪些技术要求?
有何特点?
答:
模具的技术要求
(1)模具零件应具有较高的强度、刚度、
耐磨性、韧性淬透性和切削加工性
(2)模具零件精度高、表面粗糙度低
(3)模具零件的标准化程度高
(4)模具凹凸模具有合理间隙
模具制造的特点
(1)模具变化多,技术要求高,对技术人员
要求高
(2)模具车间规模较小,对外协作程度高
(3)单件生产
(4)加工精度高,加工周期长
(5)模具通常需要反复修配、调整才能达到要求
2.模具制造过程的包括哪几个阶段?
答:
模具的制造过程包括五个阶段:
技术准备、材料准备、模具零件及组件加工、装配调试、试模鉴定。
3.模具制造的基本工艺路线包括哪些内容?
模具制造的基本工艺路线:
分析估算-模具设计-零件加工-装配调整-试模-成品。
第二章模具的机械加工
1.解释名词:
夹具磨削法,计算机辅助设计CAD,计算机辅助制造CAM。
夹具磨削法:
指将工件至于成形夹具上,利用夹具调整工件的位置,使工件在磨削过程中作定量移动或转动,由此获得所需形状的加工方法。
计算机辅助设计CAD:
利用计算机及其图形设备帮助设计人员进行设计工作。
计算机辅助制造CAM:
在机械制造业中,利用电子数字计算机通过各种数值控制机床和设备,自动完成离散产品的加工、装配、检测和包装等制造过程。
2.模具机械加工的主要方法有那几种?
答:
车削加工、铣削加工、磨削加工、镗削加工、钻削加工、刨削和插削加工等
3.了解车削加工、铣削加工、刨削和插削加工、磨削加工用于模具加工的主要加工对象以及正常条件所能达到的技术要求?
车削加工:
对象:
圆盘类、轴类零件的加工。
如导柱、导套、顶杆、模柄等,技术要求:
加工精度达IT6-IT8,粗糙度Ra=。
铣削加工:
对象:
利用不同类型的铣刀和附件(分度头、回转台)以及工装夹具可加工各种平面、斜面、沟槽、台肩、型腔和孔。
加工精度可达IT10-IT8,Ra=刨削加工:
主要加工对象为模具零件的外形。
加工精度:
IT10,μm
插削加工:
主要加工对象为模具零件的成形内孔。
加工精度:
IT10,μm
磨削加工:
加工对象为模具尺寸精度和表面粗糙度要求较高的型腔、型面,导柱的外圆,导套的内外圆表面及模具零件接触面。
加工精度:
磨削平面可达IT5~IT6,~μm,内圆可达IT6~IT7,~μm(高精度磨削可达更高精度和更低的表面粗糙度~μm),外圆可达IT5~IT6,~μm。
4.常用的仿形加工方法有哪些?
答:
仿形车削、仿形铣削加工、仿形磨削
5.仿形铣削要做哪些工艺准备?
答:
制作靠模、选择适当的仿形触头,将毛坯粗车成形、并留有较少的加工余量
6.了解常用的模具精密加工方法以及所能达到的技术要求?
(个人意见)
答:
电火花加工、高速切削加工、磨削加工、超声波加工、激光加工等
7.成形磨削方法有哪两种?
说明其工作过程,在何种机床上进行?
用于成形磨削的夹具有哪些?
答:
成形磨削方法:
1)成形砂轮磨削法利用工具将砂轮修整成与工件型面完全吻合的相反型面,再以此砂轮加工工件
2)夹具磨削法将工件置于成形夹具上,利用夹具调整工件位置,使工件在磨削过程中作定量移动或转动来获得所需形状工件。
磨床:
两种方法都在成形磨床上进行。
夹具:
正弦精密平口钳、正弦磁力台、正弦分中夹具、万能夹具等。
8.万能夹具上工件的装夹方法通常有哪几种?
各有什么特点?
答:
(1)螺钉装夹法利用工件上原有的螺孔或预制的工艺孔,用螺钉和垫柱使工件固定在转盘上。
(2)精密平口钳装夹法精密平口钳紧固在转盘上,然后将工件安装在精密平口钳上,工件一次装夹只能磨出部分形面。
(3)电磁吸盘装夹法电磁吸盘紧固在转盘上,然后将工件安装在电磁吸盘上,工件一次装夹只能磨出部分形面
(4)用磨回转体的夹具装夹
9.在数控成形磨床上进行成形磨削有哪几种主要方法?
各适应与哪些工件的加工?
答:
(1)以成形砂轮磨削适用于加工面窄且批量大的工件
(2)仿形磨削适用于加工宽面工件
(3)复合磨削用于磨削具有多个相同型面的工件(如齿条形和梳形等)
第三章模具的特种加工
1.解释名词:
特种加工,电火花线切割加工,电规准,电化学抛光,电解磨削,超声波抛光。
特种加工:
是指区别于传统切削加工方法,利用化学、物理(电、声、光、热、磁)或电化学方法对工件材料进行加工的一系列加工方法的总称
电规准:
在电火花加工过程中使用的一组电脉冲参数,如电流、电压、脉冲宽度、脉宽间隙等
电火花线切割加工:
用线状电极(钼丝或铜丝)靠火花放电对工件进行切割的一种工艺形式。
电化学抛光:
也称电解抛光,利用阳极溶解法对工件表面进行腐蚀抛光的(被抛工件为阳极,不溶性金属为阴极)
电解磨削:
电解作用与机械磨削相结合的一种磨削工艺(工件作为阳极与直流电源的正极相连;导电磨轮作为阴极)
超声波抛光:
利用超声波传递能量,使抛光工具按一定频率振动、冲击和抛磨工件被加工表面,达到降低加工表面粗糙度值的目的的加工方法。
2.掌握电火花加工的基本原理及特点。
答:
电火花加工的原理是利用工件与电极之间脉冲放电时的电腐蚀现象,并有控制的除去工件材料,以达到一定的形状、尺寸及表面粗糙度要求。
电火花加工的特点
(1)可以加工硬、脆、韧及高熔点的导电材料;
(2)工具电极与工件不接触;
(3)工件表面热影响区很小;
(4)可在同一机床上作粗、精加工;
(5)易实现自动化。
3.评价电火花加工工艺效果的指标有哪些?
各个指标的影响因素有哪些?
如何影响?
工艺指标:
加工速度,加工精度,加工表面质量,工具电极相对损耗
影响加工速度的主要因素:
①电参数②极性效应③工件材料的热学常数④工作液⑤排屑条件
影响加工精度的主要因素:
①尺寸精度②形状精度
影响加工表面质量的主要因素:
①表面粗糙度②加工表面层的组织变化③表面微观裂纹
降低工具电极相对损耗:
①正确选择加工极性②选择合适的电极材③建立碳黑保护层
④利用电喷镀现象⑤利用电化学作用
4.掌握电火花线切割加工原理及特点。
原理同电火花加工,不同的是工具电极为移动金属丝
电火花线切割加工的特点:
①不需要制造专用的电极,电极丝可反复使用,生产成本低,缩短了生产周期;
②电极丝常用钼丝、铜丝、钨丝制成,直径在~之间;
③加工精度高,尺寸精度mm,表面粗糙度~μm;
④生产效率高,易于实现自动化;
⑤一般不需要电规准的转化;
⑥不能加工盲孔及阶梯类成形表面;
⑦可以一模两用。
5.掌握典型零件电火花线切割加工程序的编制方法。
(p69)(课件第三章62-69)
6.电火花加工的电规准包含哪些参数?
电规准转换是什么意思?
答:
参数包括电流、电压、脉冲宽度、脉宽间隙;
从一个电规准调整到另一个电规准的过程,称为电规准的转换
7.掌握影响电火花线切割工艺效果的因素。
答:
切割速度、加工精度、加工表面粗糙度
8.掌握线切割电极丝的选择原则。
答:
丝电极应具有良好的导电性和抗电蚀性,抗拉强度高,材质均匀,常用丝电极有钼丝、钨丝、黄铜丝(慢速走丝一般选黄铜丝,快速一般选钼丝)<电极丝直径的选择应根据切缝宽窄、工件厚度和拐角尺寸大小来选择>
9.电化学加工有哪几种类型?
各有何应用?
答:
A类(阳极溶解法)
(1)电解加工:
用于形状尺寸加工
(2)电解冶炼:
用于形状尺寸加工
(3)电化学抛光:
用于表面加工
B类(阴极沉积)
(1)电铸:
用于形状尺寸加工
(2)电镀:
用于表面加工
C类(复合加工法)
(1)电解放电加工(阳极溶解、电火花蚀除)用于形状尺寸加工
(2)电解磨削(阳极溶解、机械磨削):
用于形状尺寸加工
10.激光加工有何特点及应用?
答:
激光加工的特点
①无需借助工具或电极,不存在工具损耗问题,易于实现自动化加工;
②功率密度高,几乎能加工所有的材料;
④效率高,速度快,热影响区较小;
⑤能加工深而小的微孔和窄缝;
⑥能够透过透明材料对工件进行各种加工
激光加工的应用:
激光打孔、激光切割加工、激光焊接加工、激光表面处理、制作模具
第四章现代模具制造技术
1.什么是数控加工?
数控加工有什么特点?
答:
数控加工:
是用数字化信号对机床的运动及其加工过程进行控制的一种方法;
特点:
加工精度和加工质量高、生产效率高、自动化程度高
2.数控机床与普通机床相比有何优点?
答:
与普通机床相比,数控机床的主要优点有:
①自动化程度高,生产率高。
②加工精度高,产品质量稳定。
③适应性强。
3.数控机床如何分类?
掌握数控机床的基本工作原理。
答:
按加工方式分类:
(1)金属切削类:
数控车床、数控铣床、数控镗床、数控磨床、数控钻床、加工中心等;
(2)金属成形类:
数控折弯机、数控冲床等;
(3)特种加工类:
数控电火花成形加工机床、数控电火花线切割加工机床、数控激光切割加工机床;
(4)其他类。
基本工作原理:
数控装置内的计算机对以数字和字符编码方式所记录的信息进行一系列处理后,向机床进给等执行机构发出命令,执行机构则按其命令对加工所需各种动作,如刀具相对于工件的运动轨迹、位移量和速度等实现自动控制,从而完成工件的加工。
4.说明数控加工编程的一般步骤与方法。
答:
步骤:
(1)确定工艺路线
(2)计算刀具轨迹坐标值(3)编写加工程序(4)程序输入数控系统(5)程序检验
方法:
有手工编程与自动编程两种方法。
5.什么是快速原型制造技术?
常用的快速成型工艺方法有哪些?
答:
快速原型制造技术又称快速自动成型技术,是近年来发展起来的直接根据CAD模型快速生产样件或零件的成组技术总称,它集成了CAD技术、数控技术。
快速成型工艺方法:
光固化立体造型SLA、分层物件制造LOM、选择性激光烧结SLS、熔融沉积造型FDM、三维印刷系统法-TDP、喷墨印刷法-IJP
6.什么是逆向工程技术?
怎样利用该技术制造模具?
答:
逆向工程技术是指用一定的测量手段对实物或模型进行测量,根据测量数据通过三维几何建模方法重构实物的CAD模型的过程。
应用:
①复制样本模具;②以实物零件为对象设计制造模具并复制零件
7.高速切削有什么特点?
与传统加工方法相比,模具加工采用高速铣削有哪些优点?
特点:
加工效率高;
切削力低,刀具寿命长;
热变形小;
加工精度高;
综合经济效益好。
采用高速铣削的优点:
主轴转速(切削速度)高10000~30000r/min;
进给速度快5~60m/min;
切削深度小~;
切削行距小以下。
第五章模具典型零件加工
1.掌握冷冲模模架典型结构类型及其主要组成零件。
典型结构
形式
简图
特点和作用
滑
动
导
向
模
架
对
角
导
柱
模
架
凹模面积的对角中心线上有一前导柱和一后导柱受力平衡,上模座在导柱上滑动乎稳,无偏斜现象有利于延长模具寿命,使用条料时因受导柱间距离的限制,不可太大
后
侧
导
柱
模
架
两导柱,导套分别装在模架后侧,可以使用宽度较大的条料冲制,且可用边角料,送料和操作方便,但因导柱在一侧,上模座在导柱上滑动不够乎稳,影响模具寿命,只适用于中等复杂和一般精度要求的模具
中
间
导
柱
模
架
在模架左右中心线上装有两尺寸不同的导柱,导向精度高,上模座在导柱上滑动平稳.但只适用于横向送料,常用于弯曲摸和复合模
四
导
柱
模
架
四个导柱分布在模座四角,模架受力平衡,导向精度高;适用于大型制件或精度要求特别高的冲压模具,以及大量生产和自动化冲模上
主要组成零件
序号
零件名称
作用
1
模柄
连接压力机滑块与上模的零件
2
上模板
支撑、安装凸模固定板及凸模零件
3
导柱
导向零件。
保证上、下模上下对中及模具精度的零件
4
导套
导向零件。
与导柱配合能保证上、下模上下对中及模具精度的零件
5
下模板
固定和安装凹模、凹模固定板的零件,并用螺栓通过下模板将模具固定在压力机工作台上
2.导柱、导套采用何种配合形式?
其技术要求如何?
答:
间隙配合
导柱技术要求:
1导柱的工作部分圆柱度公差应满足以下几点:
导柱直径d<30mm时,公差为0.003~0.004ram;
d>30—45mm时,公差为0.004—0.005mm;
d>,45mm时,公差为0.005~0.006ram。
②导柱与固定模座配合部位直径的同轴度公差,不应超过工作部分直径公差的1/2。
③导柱加工后,必须符合零件图样中所要求的各部分尺寸精度、表面质量以及热处理要求。
④导柱加工后,应该进行渗碳处理,而且工作表面的渗碳层要均匀,深度一般为0.8~1.2mm。
⑤导柱工作表面应具有耐磨性。
导套的技术要求①导套与导柱配合面的表面
粗糙度R。
应小于0.41.1,m。
2导套加工后其工作部分圆柱度公差应满足以下要求:
导套内孔直径d<30mm时,公差为0.004—0.005mm;
d>30~45mm时,公差为0.005—0.007mm:
d>45mm时,公差为0.007—0.008mm。
3导套加工后,应进行渗碳处理,工作表面的
渗碳层要均匀,渗碳后淬火硬度为58—62HRC。
④导套与固定模座装合部位直径的同轴度公差,应不超过工作部分直径公差的1/2。
⑤导套加工后,必须符合零件图样中所要求的形状以及尺寸精度。
3.磨削导套时常出现“喇叭口”这样的缺陷,试述其产生的原因,怎样防止?
答:
原因:
是研磨时工件的往复运动使磨料在孔口处堆积,在孔口处切削作用增强所致。
防止:
在研磨过程中应及时清除堆积在孔口处的研磨剂,防止和减轻这种缺陷的产生。
4.冷冲模凸模表面、凹模型孔的加工方法有哪些?
掌握其适应条件。
答:
冷冲模凸模表面加工方法圆形凸模的制造比较简单,先在车床上加工成毛坯,经热处理后,用外圆磨床精磨,最后将工件抛光即可。
·非圆形凸模的加工比较费时,可根据具体情况采用以下几种方法:
1)用凹模压印再锉修成形压印法是模具钳工常用的一种方法。
2)·用仿形刨床加工仿形刨床用于精加工凸模及其它形状复杂的表面3)成型磨削。
4)电火花切割。
凹模型孔常用的加工方法主要有:
钻、铰、镗、铣和坐标磨削,另外还常使用电火花成形加工、数控线切割和数控铣加工,使用研磨和抛光作为光整加工。
5.塑料模制造应达到哪些技术要求?
要求:
(1)构成塑料模具所有零件的材料、加工精度和热处理质量等均应符合图样的要求。
(2)构成模架的零件应达到规定的制造要求(3)模具应具备的功能要求:
①侧向抽芯和顶出装置动作正常;②温度调节部分能正常工作。
(4)试模和调整直至成型合格的塑件。
6.掌握塑料模型腔加工工艺路线。
型腔加工通常有哪几种加工方法?
其适应条件如何?
1.车削加工:
主要用于加工回转曲面的型腔或型腔的回转曲面部分
2.铣削加工
(1)普通铣床加工型腔立铣和万能工具铣床:
适合于加工平面结构的型腔。
μm
(2)仿形铣床加工型腔特别适合于加工具有曲面结构的型腔。
3.数控机床加工:
自动加工,减少停机时间
7.塑料模型腔抛光方法有哪些?
各有何特点?
⑴手工抛光:
手工抛光的特点一是自定位,二是手工能使磨具以比较恒定的接触力(熟练的模具抛光工人)附着在模具的自由表面上进行抛光
⑵机械抛光:
机械抛光的特点有:
简单、适应性广;对多相材料较合适,
⑶电解修磨抛光特点①电解修磨抛光不会使工件产生热变形或应力。
②工件硬度不影响加工速度。
③对型腔中用一般方法难以修磨的部分及形状,可采用相应形状的修磨工具进行加工,操作方便灵活。
④粗糙度一般为~μm。
⑤装置简单,工作电压低,电解液无毒,生产安全。
⑷超声波抛光特点①抛光效率高,能减轻劳动强度。
②适用于各种型腔模具,对窄缝、深槽、不规则圆弧的抛光尤为适用。
③适用于不同材质的抛光。
8.根据凹模零件图,编制零件机加工工艺路线。
答:
工艺路线:
备料—锻造—退火—铣六面—磨六面—划线、作螺纹孔及销孔、穿丝孔—热处理—磨六面—线切割挡料销孔及型孔—研磨型
1备料:
将毛坯锻成平行六面体。
尺寸166mm×130mm×25mm
2热处理:
退火
3铣平面:
铣各平面,厚度留磨削余量,侧面留磨削余量
4磨平面:
磨上下平面,留磨削余量~磨相邻两侧面保证垂直
5钳工划线:
划出对称中心线,固定孔及销孔线
6钳工:
加工固定孔及销孔及穿丝孔
7检验
8热处理:
按热处理工艺保58~62HRC
9磨平面:
磨上下面及其基准面达要求
10线切割:
切割挡料销孔及型孔,留研磨余量
11研磨:
研型孔达规定技术要求
12检验
9.根据上模座零件图,编制零件机械加工工艺路线。
(上模座)
备料—刨/铣平面—磨平面—划线—钻孔—镗孔—铣油槽(先面后孔)工艺过程如下:
1
备料
铸造毛坯
2
刨(铣)平面
刨(铣)上、下平面,保证尺寸
3
磨平面
磨上下平面达尺寸50mm;保证平面度要求
4
划线
划前部及导套安装孔线
5
铣前部
按线铣前部
6
钻孔
按线钻导套安装孔至尺寸Φ43mm
7
镗孔
和下模座重叠镗孔达尺寸Φ45H7,保证垂直度
8
铣槽
铣圆弧槽
9
检验
10.根据浇口套零件图,编制零件机械加工工艺路线.
工艺路线
工序号
工序名称
工艺说明
1
备料
按零件结构及尺寸大小选用热轧圆钢或锻件毛坯保证直径和长度方向上有足够的加工余量
若浇口套凸肩部分长度不能可靠夹持,应将毛坯长度适当加长
2
车削加工
车外圆d及断面留磨削余量
车退刀槽达设计要求
钻孔
加工锥孔达设计要求
调头车D1外圆达设计要求
车外圆D留磨量
车端面保证尺寸L
车球面凹抗达设计要求
3
检验
4
热处理
5
磨削加工
以锥孔定位磨外圆d及D达设计要求
6
检验
11.根据导套零件图,编制零件机械加工工艺路线。
题11图导?
套
工艺路线
工序
工序名称
工序内容
设备
1
下料
按尺¢52mm×115mm切断
锯床
2
车外圆及内孔
车端面保证长度113mm
卧式车床
钻¢32mm孔至¢30mm
车¢45mm外圆至¢
倒角
车3×1退刀槽至尺寸
镗¢32mm孔至¢
镗油槽
镗¢32mm孔至尺寸,倒角
3
车外圆
车¢48mm的外圆至尺寸
卧式车床
倒角
车端面保证长度110mm
倒内外圆角
4
检验
5
热处理
按热处理工艺进行,保证渗碳层深度~,硬度58~62HRC
6
磨内外圆
磨45mm外圆达图样要求
万能外圆磨床
磨32mm内孔,留研磨量
8
检验
研磨¢32mm孔达图样要求
12.根据圆形凸模零件图,编制零件机械加工工艺路线。
(1)备料;
(2)锻:
锻成φ28×38;
(3)热处理:
退火;
(4)车:
车端面及中心孔;双顶尖装夹,车D、d面留单面磨削余量;
(5)检验;
(6)热处理:
淬硬HRC58~62;
(7)研磨:
中心孔;
(8)磨:
磨外圆D及d至尺寸;
(9)线切割:
两端顶尖孔处
答:
双顶尖法:
备料—锻造—热处理—车端面、外圆—热处理—研中心孔—磨削—线切割
13.根据凸模零件图,编制零件机械加工工艺路线。
1、下料:
φ56×117
2、锻造:
锻成110×45×55
3、热处理:
退火
4、铣削:
铣六面留单面余量
5、磨削:
上/下平面及相邻两侧
6、钳工:
划线、钻/攻螺纹孔,钻穿丝孔、漏料孔
7、热处理:
淬火、低温回火
8、磨削:
平面磨上、下面及相邻两侧面
9、线切割:
割内、外刃口面
10、研磨:
研内、外刃口面
11、检验
备料—锻造—退火—铣六面—磨六面—划线/作螺纹孔/漏料孔/穿丝孔—热处理—线切割内外形—研磨内外形
第六章模具的装配
一、填空题
1.装配好的推杆及复位杆,当模具处于闭合状态时,推杆顶面应?
?
?
高出?
型面?
?
?
?
mm,复位杆端面应?
?
低于?
分型面?
?
?
mm。
2.互换装配法制成分为?
?
?
完全互换法?
?
?
和?
?
?
?
不完全互换法?
?
?
。
3.合并加工修配法是把?
?
?
?
?
?
两个?
?
?
?
?
或?
?
?
?
两个以上?
?
的零件装配在一起后,再进机械加工?
?
?
?
?
,以达到装配精度要求。
4.模具生产属?
?
?
?
?
?
?
单件?
?
?
?
生产,在装配工艺上多采用?
?
修配法?
和?
?
?
调整法?
?
?
?
来保证装配精度。
?
?
?
?
二、名词解释
1.修配装配法:
装配时根据实际需要修整预留面来达到装配精度的方法
2.完全互换法:
控制零件的加工误差,零件装配时不需挑选,装配后即能保证装配精度的装配方法。
3.塑料模试模:
指模具在注塑机上初装后进行的试验性注塑,以考核模具的性能及其加工的塑件质量。
4.调整装配法:
利用一个可调整零件改变装配情况,从而达到装配精度的方法。
三、问答题
1.在模具装配中,常采用修配装配法和调整装配法,比较其两者的异同点。
相同点:
装配精度高。
依赖工人的技术水平,生产效率低。
③都要增加工序和工时。
不同点:
调整法往往需要增加调整件,而修配法不需要。
2.塑料模装配好后为什么要进行试模?
答①检查模具在制造上存在的缺陷,并查明原因加以排除;②对模具设计的合理性进行评定并对成形工艺条件进行探索。
3.如图所示,试述塑料模大型芯的固定方式装配顺序。
答:
固定方式:
螺钉固定式
装配过程:
①在加工好的型芯1上压入实心的定位销套3。
②在型芯螺孔口抹红丹粉,根据型芯在固定板上的要求位置,用定位块4定位,把型芯与固定板2合拢,用平行夹板5夹紧在固定板上。
将螺钉孔位置复印到固定板上,取下型芯,在固定板上钻螺钉过孔及惚沉孔,用螺钉将型芯初步固定。
③在固定板背面划销孔位置,并与型芯一起钻、铰销孔,压入销钉。
4.如图所示是装配后在型芯端面与加料室底平面间出现了间隙,可采用那些方法进行消除?
(10分)
答
(1)修磨固定板平面A修磨时,磨去的金属层厚度等于间隙值Δ;
(2)修磨型腔上平面B修磨时,磨去的金属层厚度等于间隙值Δ;
(3)修磨型芯(或固定板)台肩C,采用这种修磨法应在型芯装配合格后再将支承面D磨平。
题4图型芯端面与加料室底平面间出现间隙
5.拉深模试模时出现制件起皱的缺陷,找出其产生的原因以及调整方法。
答:
原因:
压边力不足,拉深模间隙过大,凹模圆角半径过大。
调整方法:
需要增加压边力,减少拉深模间隙,减少凹模圆角半径。
6.冲裁模装配的主要技术要求是什么?
答:
(1)装配好的冲模,其闭合高度应符合设计要求。
(2)除浮动模柄外模柄轴心线对上模座上平面垂直度不大于。
(3)凸模与凹模配合间隙符合设计要求,均匀一致。
(4)定位装置保证定位正确可靠。
(5)卸料及推件灵活、正确。
(6)在生产条件下试模获得合格制件。
7.弯曲模试模时出现制件的弯曲角度不够的缺陷,找出其产生的原因以及调整方法。
答:
原因:
工件回弹太大会使工件弯曲角度不足
调整:
需要对弯曲角度进行修正,增加弯曲角度。
在实际生产中,还应通过正确调整压力机滑块的下止点位置,保证弯曲模加工出现的工件符合要求。
例如当发现弯曲角度不足时,则应把滑块下止点调低些,使弯曲时的凸模对材料的顶弯力大一些,以便增大弯曲角度。
8.冲裁模试模时出现送料不畅通或被卡死的缺陷,找出其产生的原因以及调整方法。
答:
原因①?
连续模中两导料板之间的尺寸过小