涂装车间烘干炉烟气余热回收技术浅析.docx
《涂装车间烘干炉烟气余热回收技术浅析.docx》由会员分享,可在线阅读,更多相关《涂装车间烘干炉烟气余热回收技术浅析.docx(8页珍藏版)》请在冰豆网上搜索。
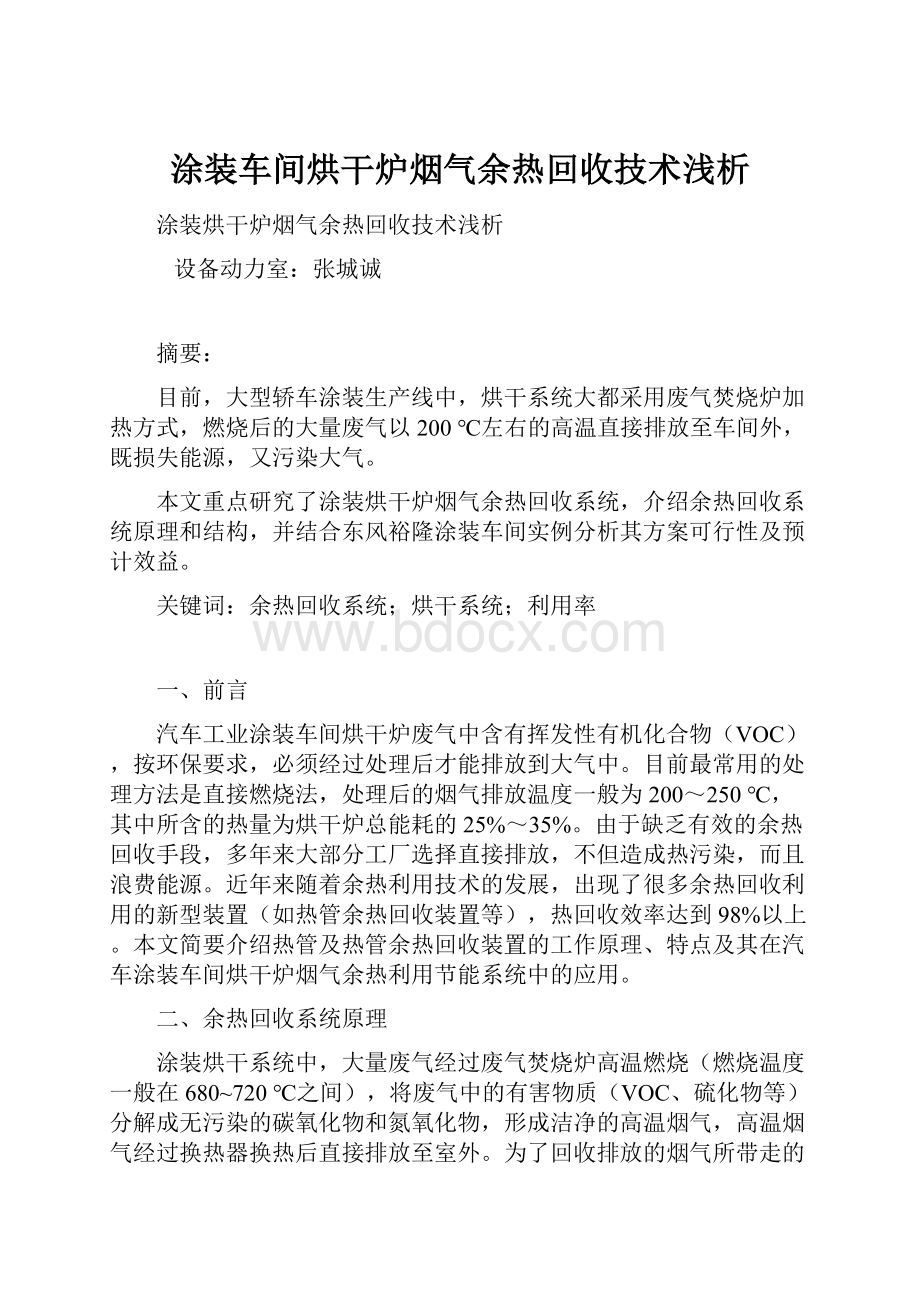
涂装车间烘干炉烟气余热回收技术浅析
涂装烘干炉烟气余热回收技术浅析
设备动力室:
张城诚
摘要:
目前,大型轿车涂装生产线中,烘干系统大都采用废气焚烧炉加热方式,燃烧后的大量废气以200℃左右的高温直接排放至车间外,既损失能源,又污染大气。
本文重点研究了涂装烘干炉烟气余热回收系统,介绍余热回收系统原理和结构,并结合东风裕隆涂装车间实例分析其方案可行性及预计效益。
关键词:
余热回收系统;烘干系统;利用率
一、前言
汽车工业涂装车间烘干炉废气中含有挥发性有机化合物(VOC),按环保要求,必须经过处理后才能排放到大气中。
目前最常用的处理方法是直接燃烧法,处理后的烟气排放温度一般为200~250℃,其中所含的热量为烘干炉总能耗的25%~35%。
由于缺乏有效的余热回收手段,多年来大部分工厂选择直接排放,不但造成热污染,而且浪费能源。
近年来随着余热利用技术的发展,出现了很多余热回收利用的新型装置(如热管余热回收装置等),热回收效率达到98%以上。
本文简要介绍热管及热管余热回收装置的工作原理、特点及其在汽车涂装车间烘干炉烟气余热利用节能系统中的应用。
二、余热回收系统原理
涂装烘干系统中,大量废气经过废气焚烧炉高温燃烧(燃烧温度一般在680~720℃之间),将废气中的有害物质(VOC、硫化物等)分解成无污染的碳氧化物和氮氧化物,形成洁净的高温烟气,高温烟气经过换热器换热后直接排放至室外。
为了回收排放的烟气所带走的热量,在排烟管道附近安装气液换热器来回收这部分余热,回收的热量作为其他设备的热源,如前处理工序槽液加热等。
烘干室烟气余热回收系统是利用复合管导热系数高的特点,设计制造管式换热器,安装在排烟管路上面回收余热。
为涂装车间需加热设备提供90℃左右的热水,替代锅炉或蒸气加热,为汽车制造企业节约煤或蒸气用量,达到节能减排的目的。
图1为管式换热器的原理
三余热回收系统组成
余热回收系统主要由3部分组成:
烟气换热系统、水循环系统、控制系统。
3.1烟气换热系统
烟气换热系统包括手自一体阀门、进出烟气温度传感器、压差开关等监测元件以及主体设备管式热交换器。
目前,烟气余热回收系统大都使用换热性能高的复合管组成管式热交换器,具有良好的防腐蚀能力,装置体积小。
管式热交换器是在一个圆筒形壳体内设置很多平行的管子,这些平行的管子称之为管束,让流体分别从管内空间(或称管程)和管外空间(或称壳程)流过进行热量交换。
其中的复合管是由2根同心的内外管组成,在内外管之间有一个薄壁同心管,薄壁同心管内充满液态金属。
当烟气对管式换热器加热时,薄壁同心管内的液态金属将由于内外壁温差而形成气液两相并进行循环,此种特殊的同心管气液两相流循环传热,使烟气进入余热回收系统后达到最佳的换热效果。
烘干炉250℃左右的高温烟气经过管式换热器换热后将热量转换成热水,使经过换热后的烟气温度下降至110℃,回收热量温差为140℃。
3.2水循环系统
水循环系统是余热回收热量的输出系统。
它由水箱、进水管路、回水管路、电磁阀、温度传感器等组成。
回收的余热将70℃的工艺回水加热至90℃。
具体循环方式是水箱中的工艺回水通过管式热交换器后加热至90℃,供给前处理的脱脂、磷化等工序加热槽液,加热槽液后冷却回流至水箱中,再重新输入到热交换器中,节约用水和能源。
3.3控制系统
烟气余热回收系统采用全自动控制方式。
由于涉及多个用能系统,各区域设备具有独立的自动化控制要求,烟气余热回收系统将各独立设备联系起来,因此各区域电控柜控制之间连锁关系比较复杂。
开机:
烟气余热回收系统接到锅炉房水泵或蒸气阀门开启信号,当进水管路的流量开关有水流信号时,烟气管路的手一体阀切换,烟气经过余热回收系统的换热器。
运行:
在烟气和水管的进出口管路上设置有温度传感器,通过温度传感器输出温度信号,来调节对应烟气或水管的阀门开度。
当出口水温过低时,加大入口烟气阀门开度;当出口水温过高时,给烟气管路阀门提供高温报警信号,烟气管路阀门切换,烟气不再经过换热器。
当排烟温度过低时(如低于120℃),给锅炉房或蒸气站提供信号,调节水路三通阀,减少经过余热换热器的水量。
关机:
余热回收系统接到锅炉房水泵或蒸气站停止运行信号(或待机信号),烟气管路阀门切换,烟气不经过余热换热器,锅炉房或蒸气站接到阀门关闭到位信号后,30min后,水泵停机或蒸气阀门关闭。
四、余热回收系统设计注意事项
在涂装生产线中,烘干炉高温排烟管管路长约100m,烟管一端接至废气焚烧炉炉膛,一端通向车间外部,管内压力从10000Pa逐渐降至1500Pa左右。
由于高温排烟管直通炉膛,且管内压力高,因此高温排烟管的畅通是确保烘干设备安全运行的先决条件。
烟气余热回收系统安装在烘干炉高温排烟管末端,为确保高温排烟管路通畅,必须采用设置旁通管路、编制严密的电控连锁控制程序以及相关报警装置等方法,避免余热回收系统堵塞,做到发生问题及时解决,确保涂装车间烘干设备安全、正常运行。
因此在余热回收系统设计时需注意以下几个问题:
传热管积灰问题;烟气温度过低腐蚀问题;电控连锁以及报警装置的设计。
4.1传热管积灰问题
传热管积灰会降低传热效率,污染换热管,大量积灰还会阻塞烟气流通,增加设备阻力,影响废气焚烧炉正常运行,存在严重安全隐患。
因此,为避免传热管堵塞,必须确保传热管的积灰为干灰状态。
要求传热管金属壁温度高于烟气中水蒸气露点温度,同时要求换热器结构中不能出现吹灰死角和积灰源,烟气流动应均匀,流速大于10m/s,使烟气在流动中具有自动吹灰功能。
同时还应预留压缩空气接口,定期用压缩空气吹扫换热管内的灰尘。
4.2换热管腐蚀问题
在烟气余热回收系统运行过程中,若出口排烟温度过低,会使换热器出口处管壁温度低于烟气中一些有害气体的露点温度,使有害气体凝结为液体附着在换热管壁上,引起换热管严重腐蚀,因此,不能将排烟温度降得过低,一般要求排烟温度比烟气露点高10~15℃,预留足够的安全余量。
4.3电控连锁及报警装置设计
余热回收系统应在确保烘干炉设备正常运转的前提下投入使用,因此,通过编制电控连锁程序和相关报警装置来确保高温烟气管路畅通,使余热回收系统正常运行。
余热回收系统的烟管和水管都设置有旁通管路,旁通管路安装手自一体阀(如自动功能失效,可手动打开),当烟温/水温达到设定值或余热回收设备阻力增大时,旁通管路阀门自打开,烟气或热水就会通过旁通管路输入下一工序。
为防止余热回收系统堵塞,在烟气进出口管路分别安装有2个压力检测装置(双压力检测,效果可靠)和热电偶。
正常运行时,废气焚烧炉出口处高温烟气管路压力为10000Pa左右,经逐级换热后(4~5个烘干设备换热器),余热回收系统入口高温烟管内压力达到1500Pa左右,设计余热回收系统压损(即设备阻力)为150~200Pa,最终排放至大气的排烟压力为1000Pa左右(有一部分管路压力损失)。
当烟气入口压力超过设定上限值(报警压力2000Pa)时,旁通管路自动阀门打开,迅速降低烟管入口压力,同时报警信号反馈至烘干炉废气焚烧炉电控系统中,焚烧炉电控系统收到报警信号后停止运行,切断燃料供给,规避危险源。
五、余热回收系统效益分析
5.1工程概况
已知东风裕隆涂装车间6台烘干炉总烟气流量约为8500m3/h*6=51000m3/h。
排烟温度平均为200℃的烘干炉。
,在其烟气排烟管末端改造安装余热回收系统,将烟温降至110℃排放,回收的余热将60℃的工艺回水加热至80℃,用于前处理槽液加热。
项目实施后既能减轻环境污染,满足企业生产工艺要求,又达到节约燃料的目标。
5.2设计方案
涂装车间一楼有锅炉房,锅炉热水通过循环水泵送至前处理各槽体对槽液进行加热,换热后的水再送至板式换热器与蒸气进行换热,热水的送水温度约为80℃,回水温度约为60℃。
具体工艺流程如图2所示。
为了回收余热,节约蒸气用量,在电泳烘干炉高温排烟管末端设置一台与之匹配的复合管式余热回收系统,将烘干炉所排放的高温烟气降至110℃左右进行排放。
在原回水管路上新增循环水泵,通过水泵将回水送入余热回收系统内,与烘干炉排放的高温烟气进行换热后进入原回水管路,通过原循环泵将加热后的热水送至槽体加热槽液。
电泳烘干炉余热回收系统工艺流程如图3所示。
5.3余热回收器设计参数
所选配余热回收器采用复合管技术材质全部采用国标304不锈钢,具体技术参数如下:
项目名称
烤炉烟气余热利用项目
安装位置
烤炉排烟管处
余热回收器型号
YRHS-8A型
数量
6
加热介质类型
水(气-液式)
烟气侧进口温度
200°C
烟气侧出口温度
110°C
设计水侧进口温度
60°C
设计水侧出口温度
80°C
设计烟气流量
8500Nm3/h
设计烟气阻力
200Pa
每小时回收热量
水管接口管径
DN80
烟气接口尺寸
与原烘炉烟管尺寸一致
材质
不锈钢无缝钢管
外形尺寸
长1500×宽1400×高1800(mm)
5.4方案大约预算金额
名称
单价(万)
数量
总价(万)
余热交换器
15.7
6
94.2
管道辅材及安装费
35.8
35.8
总计
130
5.5经济效益分析
5.5.1回收热量计算
已知烟气温度t1=200℃,烟气流量V=51000m3/h,经过余热回收系统后降至t2=110℃,则回收热量:
Q=C·ρ·V·Δt式中:
Q为回收的热量,kcal/h;
Δt为烟气温差,℃;
V为烟气在标准状态下的流量,m3/h;
C为烟气定压比热容,kcal/(kg·℃);
ρ为烟气密度,kg/m3。
最终计算得Q≈191.25万kcal/h。
5.5.2加热热水量
已知热水进水温度t1=60℃,出水温度t2=80℃,余热利用率按85%,则可加热热水质量:
G=Q·0.85/[C(t2-t1)]
式中:
G为热水量,t/h;
Q为回收的热量,kcal/h;
C为水的比热容,kcal/(kg·℃);
t1和t2为进出口水温。
最终计算得G≈66.3t/h。
5.5.3经济效益分析
余热回收系统一小时可回收热量:
Q2=Q85%=191*0.85=162万kcal/h,
天然气热值8600kcal/Nm3所以回收的热量也可以等同折算成天然气。
按每天工作12个小时,一年250工作日计,则
一年可节约天然气费用=4元/m³*12h*250天*162万kcal/h/8600kcal/Nm³≈226万元。
因投资金额为130万元,即约7个月可收回全部投资。
5结语
根据实例计算表明,安装烟气余热回收系统,可以提高生产线热效率,降低总体能耗,回收余热也越大,节约能源越多。
如果在实际生产中能够确保余热利用率,不仅可取得客观的经济效益,而且响应国家节能减排政策,为社会环境保护做出贡献。