电泳涂料及涂装技术培训.docx
《电泳涂料及涂装技术培训.docx》由会员分享,可在线阅读,更多相关《电泳涂料及涂装技术培训.docx(70页珍藏版)》请在冰豆网上搜索。
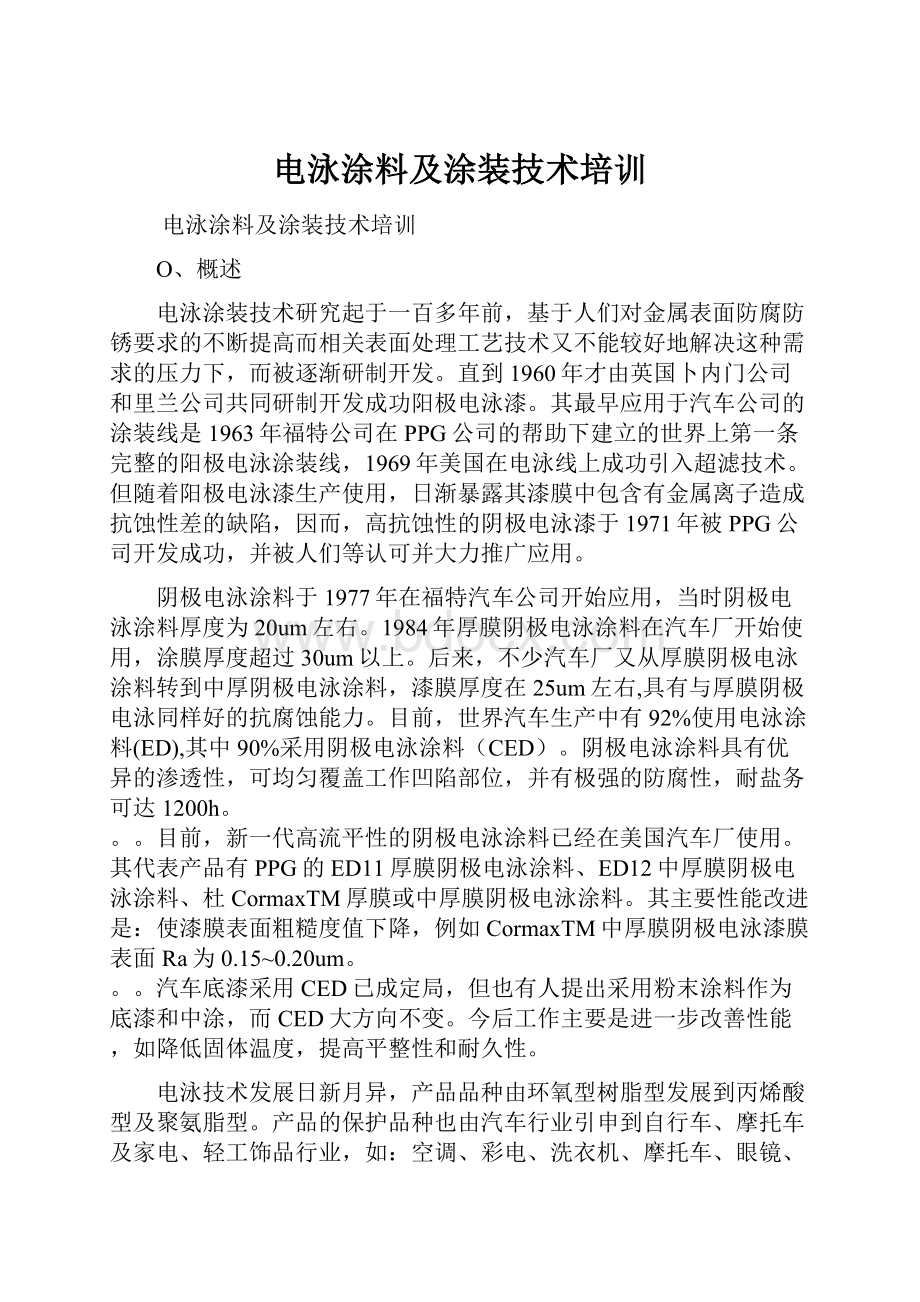
电泳涂料及涂装技术培训
电泳涂料及涂装技术培训
O、概述
电泳涂装技术研究起于一百多年前,基于人们对金属表面防腐防锈要求的不断提高而相关表面处理工艺技术又不能较好地解决这种需求的压力下,而被逐渐研制开发。
直到1960年才由英国卜内门公司和里兰公司共同研制开发成功阳极电泳漆。
其最早应用于汽车公司的涂装线是1963年福特公司在PPG公司的帮助下建立的世界上第一条完整的阳极电泳涂装线,1969年美国在电泳线上成功引入超滤技术。
但随着阳极电泳漆生产使用,日渐暴露其漆膜中包含有金属离子造成抗蚀性差的缺陷,因而,高抗蚀性的阴极电泳漆于1971年被PPG公司开发成功,并被人们等认可并大力推广应用。
阴极电泳涂料于1977年在福特汽车公司开始应用,当时阴极电泳涂料厚度为20um左右。
1984年厚膜阴极电泳涂料在汽车厂开始使用,涂膜厚度超过30um以上。
后来,不少汽车厂又从厚膜阴极电泳涂料转到中厚阴极电泳涂料,漆膜厚度在25um左右,具有与厚膜阴极电泳同样好的抗腐蚀能力。
目前,世界汽车生产中有92%使用电泳涂料(ED),其中90%采用阴极电泳涂料(CED)。
阴极电泳涂料具有优异的渗透性,可均匀覆盖工作凹陷部位,并有极强的防腐性,耐盐务可达1200h。
。
。
目前,新一代高流平性的阴极电泳涂料已经在美国汽车厂使用。
其代表产品有PPG的ED11厚膜阴极电泳涂料、ED12中厚膜阴极电泳涂料、杜CormaxTM厚膜或中厚膜阴极电泳涂料。
其主要性能改进是:
使漆膜表面粗糙度值下降,例如CormaxTM中厚膜阴极电泳漆膜表面Ra为0.15~0.20um。
。
。
汽车底漆采用CED已成定局,但也有人提出采用粉末涂料作为底漆和中涂,而CED大方向不变。
今后工作主要是进一步改善性能,如降低固体温度,提高平整性和耐久性。
电泳技术发展日新月异,产品品种由环氧型树脂型发展到丙烯酸型及聚氨脂型。
产品的保护品种也由汽车行业引申到自行车、摩托车及家电、轻工饰品行业,如:
空调、彩电、洗衣机、摩托车、眼镜、锁具、灯具及饰品、发夹、领带夹及各个金属行业以及铝材表面防锈行业。
一、什么是电泳涂料
电泳涂料是一类仅适用于电泳涂装的水性涂料,它在水中可离解为可成膜的水溶性成膜物,在直流电场中泳向相反的电极,并在上面沉积下来形成涂膜。
一般把在聚合物中有羧酸或胺的聚合物用胺或酸中和而水溶化或水分散化,将被涂物作为阳极或阴极,用电泳法,通过聚合物的不溶化而在被涂物上析出,这种方法称电泳涂装。
按照离解的水溶性成膜物的极性不同,可分为阳极电泳涂料和阴极电泳涂料两类。
阴极电泳涂料:
环氧型阴极电泳涂料丙烯酸阴极电泳涂料
阳极电泳涂料:
环氧酯阳极电泳涂料氨基丙烯酸阳极电泳涂料
但是,阳极电泳时因被涂物是阳极,在通电过程中底材会溶出,而产生着色情况,特别是溶出的金属离子积蓄在涂料浴中会污染涂料浴。
从耐腐蚀方面看,氧化铝膜处理底材自身耐腐蚀性优异而不成问题,但底材为钢底材时,例如磷酸锌处理等化学处理的钢底材因这样的化学处理膜也能溶出,所以防锈效果下降。
在阴极电泳中因 被涂物是阴极而不会产生这样的问题,一般耐腐蚀性优异。
现在阴极电泳涂装法产生了高耐腐蚀性,正在用于汽车车身的底漆涂装。
由于阴极电泳涂料具有比阳极电泳涂料更好的涂装稳定性和涂膜的性能,目前被广泛应用于汽车及金属涂装领域,这是目前唯一一种方法能使形状复杂的金属结构在涂饰后,具有均匀的涂层和优良的防腐性。
二、电泳涂装之优势
1、在很凹的部位,即可形成完成均匀之保护膜,并可利用调整不同之操作电压,即可控制镀层的厚度,达到极高的防腐性,并消除了电镀过程中的厚薄不均电极效应,同时也消除了喷漆过程中的结皮、泪痕之故障。
2、涂料利用率高达95%,与喷漆法相比,减少了材料的浪费。
3、以水作溶剂,免除了火灾危险,也大大降低了水处理及空气污染,安全性提高,减少了环保设备费用。
4、可减少贵金属镀层厚度,仍可维持及超越原来镀层寿命,用彩色电泳漆可取代镀金,大大降低了生产成本。
生产性高,生产时间缩短。
金属表面处理、电镀、皮膜等,完成后携带大量水,传统喷涂方法要先行烘干再生产,费时而且浪费能源,而电泳可连续作业,易于大量及自动化生产。
三、电泳涂装流程及附属设备
A、电泳涂料的组成
大多数场合,电泳涂料均是双组分的(色浆和乳液),也有单组分的。
色浆
乳液
颜料:
钛白
碳黑
体质颜料
防锈颜料
触媒:
有机锡
颜料分散树脂:
季胺盐树脂等
树脂:
改性环氧树脂
硬化剂:
封闭多异氰酸脂
添加剂:
表面活性剂、防缩孔剂等
中和剂:
甲酸、醋酸
溶剂:
醇醚类
B、阴极电泳涂装的机理
电泳涂装是一个在电泳槽中发生的电化学过程,可简单的分为四个过程:
1、电解(分解)-在阴极反应最初为电解反应,生成氢气及氢氧根离子OH-,此反应造成阴极面形成一高碱性边界层,当阳离子与氢氧根作用成为不溶于水的物质,涂膜沉积,方程式为:
H2O→OH-+H2
2、电泳动(泳动、迁移)-阳离子树脂及H+在电场作用下,向阴极移动,而阴离子向阳极移动过程。
3、电沉积(析出)-在被涂工件表面,阳离子树脂与阴极表面碱性作用,中和而析出不沉积物,沉积于被涂工件上。
4、电渗(脱水)-涂料固体与工件表面上的涂膜为半透明性的,具有多数毛细孔,水被从阴极涂膜中排渗出来,在电场作用下,引起涂膜脱水,而涂膜则吸附于工件表面,而完成整个电泳过程。
环氧聚氨酯型阴极电泳涂料是由阳离子型树脂、封闭型或部分封闭型多异氰酸酯类交联剂,并配合其它成分组成。
阳离子树脂多采用环氧树脂为基料,并在其基体上引入N、P、S等成盐基团,一般采用有机多元胺类引入成盐基团,再用有机或无机酸中和成盐,而分散于水中。
电泳过程中,在电场的作用下,产生电解、电泳、电沉积和电渗等电化学现象,带正电荷的树脂粒子,向阴极移动,同时在阴极上发生如下的电化学过程:
①阴极反应:
2H2O+2e-H2+2OH-
R-NH3++OH-R-NH2+H2O
②阳极反应:
2H2O4H++O2+4e
这样,呈碱性的R-NH2粒子及其携带成分就沉积于阴极上,经冲洗后,通过烘烤固化,形成电泳涂膜。
C、电泳涂装工序可分为四个部分:
(1)前处理:
主要用于金属工件表面的清洁和磷化,以便满足最终电泳涂装的要求,常用的磷化有铁系和锌系磷化。
常采用喷淋和浸渍的方法。
(2)电泳槽液
电泳槽液含有80~90%的去离子水和10~20%的涂料固体。
固体中含有成膜的树脂组分以及提供颜色的颜填料组分。
(3)电泳槽及附属设备
a.整流器:
提供直流电压,供电泳涂装;
b.循环:
提供槽液循环,使槽液保持持续均一稳定;
c.热交换系统:
提供合适的工作液温度;
d.过滤:
用以除去涂料中的机械杂质;
e.超滤:
控制涂料槽液的电导率,维护槽液品质;
f.槽液的回收系统:
回收后冲洗带出的电泳涂料,提高涂料的利用率;
(4)烘道:
提供漆膜固化所需的涂料固化温度。
四、阴极电泳工艺示意简图:
1)循环系统:
设置循环搅拌的目的,一是防止颜料的沉降;二是使树脂和颜料均匀分散,从而取得均一漆膜;三是散发电泳产生的焦尔热,除去电泳涂装时产生的氢气。
2)超滤系统:
设置超滤系统的目的是为了有效地控制槽液的电导率、PH值,减少杂质离子对电泳施工的干扰,除去槽液中的杂离子,净化槽液,保证涂膜质量,幷且根据槽液参数进行调整,提高涂料利用率。
每小时通过通过滤器的槽液量应为槽液总量的1/4-1/2。
3)阳极系统:
设置阳极系统的目的一是通过整流器提供的直流电源在阳极电极与工件(阴极)之间形成电场,使电泳涂料在电场作用下向阴极运动,在工件表面进行电泳沉积;二是调整槽液中多余的酸,维持槽液PH值保持一定,并对电泳过程中发热的阳极电极进行冷却。
隔膜阳极构造:
用隔膜阳极管理PH值的方式
ED槽内面衬FRP或PVC或环氧涂层时,采取阳极接地(吊具接地)方式。
电泳时,ED槽内电极反应如下:
在阴极(被涂物表面)阳离子树脂、颜料附着其上成为涂膜,阴离子酸在阳极游离,继续电泳涂装,该游离酸会引起很多问题(涂膜外观不良、氢气增多、库仑效率低等),因此,槽液的PH值要保持一定。
槽液中多余酸的调整如下:
槽液的电透析方式(隔膜方式)
使用阴离子交换膜的理由如下:
通电时,电泳生成的CH3COO-离子通过隔膜,在阳极变成CH3COOH,排到系统外。
这种阴离子交换膜,只有CH3COO-离子能通过,CH3COOH和涂料的树脂离子都不能通过。
阳极液中的阳离子还具有不在涂料中移动的性质,不会污染涂料,有将学分制料中的酸分离的功效。
因此,槽液中的PH值不会下降,且可以自动地保持一定;停电时,阴离子交换膜阻止水、有机酸从隔膜内向槽液中移动,槽液中的PH值不变化。
电泳时随着电泳的进行,与被消耗掉的树脂等量的酸,将自动地向隔膜转移。
因此,阳极液的电导率将上升,但可安置电导率仪设定管理幅度,到达上限时,自动补加纯水,到达下限时停止加水。
多余的酸自动排到系统外,保持一定的电导率。
阳极液的功能有如下3点:
①在阳极罩内将通过阴离子交换膜的酸从槽液中排到系统外;②如果阳极罩内的电导率正确的话,阴极~隔膜间的电压损失就小;③阳极液的水质满足电泳用纯水规格,万一隔膜破裂,也不会因阳极液而污染涂料。
电泳槽的控制
方式
隔膜方式
阳极
装在阳极罩内的极板
电泳槽
阳极罩在ED槽内面绕一周
PH控制原理
通过隔膜将醋酸浓度过高的阳极液废弃到系统外从而控制PH值
优点
槽液的PH值可通过极液水的电导率管理来自动控制
缺点
隔膜需维护、保养
五、施工应用
(一)、涂装工艺流程
虽然各用户涂装设备与工艺设计有所不同,但其设计主旨都是一致的,即工艺流程能获得良好的前处理效果并能与电泳施工条件具有好的互配性。
以下为KF-998阴极电沉积涂料典型的施工工艺。
脱脂→水洗→(除锈→)水洗→水洗→表调→磷化→水洗→去离子水洗→去离子水洗→电泳→水洗→超滤液冲洗→水洗→去离子水洗→烘干
(二)、电泳施工设备
电泳施工设备由纯水系统,供漆系统,电泳槽设备、循环系统、超滤系统、恒温系统、供电系统、冲洗喷淋系统、干燥系统组成。
纯水系统
KF-998阴极电沉积涂料要求纯水PH值6.5-7.5,电导率≤20μS/㎝,出水量能确保满足正常生产所需。
纯水器至少有通往加漆罐、阴极罩、电泳主槽及其它用纯水各槽的管路。
供漆系统
Ø调漆罐材质:
冷轧钢板,最好内衬玻璃钢
Ø容积:
1-2M³
Ø搅拌转速≥240转/分
Ø叶片形式:
桨式,透平式或齿盘式
Ø调漆罐口离操作台高度应≤50CM
Ø有纯水和槽液管路通入调漆罐
Ø调和后的漆送往电泳付槽
1.电泳槽设备
电泳槽
1)材质:
可采用冷轧钢板焊制,内衬玻璃钢;
2)体形:
步进式作业可为长方形,通过式作业可为船形。
但必须均有溢流槽(付槽)
3)容积:
根据用户自身工件形状大小而定
4)槽体应满足以下要求:
a)槽底各转角连接处均为弧形,以避免循环死角;
b)船形槽长度能确保工件电泳时间为2-4分钟;
c)工件距液面、槽底装置及阴阳极间距均不低于300㎜;
5)主、付槽底部有连接管道,以便投槽与清洗
6)主槽溢流口与付槽连接管路与循环量配套,确保无泡沫阻挡在主槽中。
阳 极
1)材质:
不锈钢板,不得用铜、铝材质
2)面积:
按阴阳表面积比约为3:
1来确定
3)阳极罩:
采用专业半透膜
4)阳极板应均匀排放,排放原则是两头电场强度弱,中间强。
5)为避免短路,阴极应与槽体绝缘。
2.循环系统
循环搅拌的目的一是防止颜料的沉降,二是使树脂和颜料均匀分散,从而取得均一漆膜。
1)循环泵:
一般采用普通离心泵
2)泵的流量按国外资料要求应为槽液总量的10-15次/时,槽上液流线速度0.2米/秒,槽底为0.5米/秒。
实际证明循环量达到6次/时以上即可取得满意的施工效果。
3)喷嘴:
可采用鸭嘴式,或增效特制嘴,最好不采用管上打孔方式,打孔式极易产生堵塞。
4)喷嘴排布方式:
喷嘴在槽底应均匀排布,总的要求是:
要周密考虑安装位置及角度。
(喷嘴的位置、大小、多少及喷射能力)不要在槽底形成喷射不到的死角。
5)循环管道的安装要便于拆卸、安装、维修、清洗、并且应备有不通过附槽可进行自循环的回路。
6)因KF-998阴极电沉积涂料要求24小时循环搅拌,所以循环泵必须有两套,以备更换使用和检修。
3.超滤系统:
为了有效地控制槽液的电导率、PH值,减少杂质离子对电泳施工的干扰,施工系统必须具有超滤系统。
超滤器的造型各施工单位可根据其性能和要求指标自己决定,每小时通过通过滤器的槽液量应为槽液总量的1/4-1/2。
4.恒温系统:
为便于槽液各项参数控制,让电泳施工始终处于良好的工作状态,槽液必须恒温,最佳温度为28±1℃
Ø设备:
列管式换热器
Ø材质:
无缝钢管
Ø交换面积:
根据当地气温以冷冻水的温度确定。
该换热器必须具备冷却与加热双重功能。
为避免管道堵塞,换热器宜采用卧式。
5.供电系统
输出电流:
额定电流能保证工件电泳电流密度为20A/M²;
输出电压:
输出的直流电能在0-350V范围内无级调压。
6.冲洗喷淋系统
A)超滤液喷淋:
按照我国传统工艺,入槽电泳工件一般不进行烘干,大多为带电进槽,如果工件前处理或磷化膜不理想,致使入槽工件表面附有大量水珠,这些水珠的存在极易使漆膜产生水迹点。
因此工件入槽时最好用超滤液喷淋一次,借以削除并增加工作液与工件的亲合能力,取得满意的电泳漆膜。
实际证明只要前处理及磷化膜较理想,无此喷淋程序亦可取得满意漆膜。
出槽工件离槽时最好也用超滤液喷淋一次以消除工件表面堆积物,取得平整漆膜。
B)工件第一道水洗:
此道冲洗基本上可将工件表面浮漆冲洗干净,如果不考虑回收利用可用自来水冲洗,自来水的PH值应调整到6.2左右,其目的是避免浮漆用大量自来水突然冲淡后,产生凝聚结块堵塞泵和管道,此冲洗水可循环使用定期排放,调PH值可用中和剂。
如果考虑到回收利用,此道冲洗应具备以下条件:
a.去离子水,电导率20µs/㎝以下。
b.用中和剂,调PH至6.2左右。
c.经反复循环冲洗后其浓度应达到4-5%。
d.回收时的电导率应控制在900µs/㎝以下。
e.冲洗量根据工件形状及单位时间的冲洗面积确定。
f.此冲洗水可代替超滤液喷淋工件或原漆调稀。
C)二道冲洗水:
如果第一道冲洗水是循环使用的,则应设第二道冲洗,此道冲洗水可用PH为6.2左右的自来水,调PH值可用中和剂。
D)最后一道喷淋水:
为消除工件烘干前表面所附杂质离子,提高漆膜性能,此道冲洗水采用去离子水。
7.干燥系统
KF-998阴极电沉积涂料要求170℃,30分钟烘干,这是指工件本身已经预热到170℃,有效烘干时间为30分钟,工件预热时间不包括在内。
因此各施工单位可根据自己的线速度及工件热容量的大小决定烘道的长短。
原则上烘道高温区不要超过200℃。
烘干方式各单位本着节电、烘干效果好这一原则自行选择。
8.电泳系统所有设备的安装要求
1)于安装、拆卸、检修及施工。
2)尽可能缩短管道的输送距离。
3)尽可能减少弯管的数量。
4)泵类不宜放在槽底,应便于检修;主循环过滤器和换热器应设置旁路,便于更换过滤袋和检修。
5)电泳槽的附槽可与主槽相连,也可分开排放,槽底最好为锥形。
6)控制室应设在电泳槽近旁,以便随时观察电泳线各部位工作情况。
7)无阳极液循环系统的,阳极罩必须具备抽出水和补加去离子水的能力。
8)考虑到电泳线长期使用难免造成管道堵塞或槽底产生沉降,为给清槽提供方便,最好设1-2个储槽,其容积应与电泳槽相符。
储槽同样要求设有循环搅拌装置,其循环次数为4-5次/时
(三)、投槽与调试
1.电泳槽的清洗
A.清洗前的准备工件
电泳槽清洗前,所有与电泳相关设备都必须经过调试。
单台设备调试运转正常、工件输送及其控制系统运转正常后,清洗工作方可进行。
B.电泳槽的清洗
a)先将主、副槽、溢流槽等槽体内杂物彻底清除。
b)用2%的表和剂水溶液对超滤以外的所有系统循环清洗三小时。
c)用清洁自来水循环清洗一小时。
放水后,打开过滤器,清除残渣。
d)用1%的中和剂、0.5%的补充剂对所有系统循环清洗五小时。
e)用自来水、去离子水各冲洗一次,将水彻底放尽。
2.槽液的配制
方法一:
I.加入半槽去离子水(电导率低于20µs/㎝),启动辅助循环系统;
II.将原漆加入调漆缸,搅拌均匀后泵入附槽。
此项工作最好能在48小时内完成。
III.原漆加完后补加去离子水到刚好溢流循环为止。
循环搅拌一小时后,取样测定槽液参数。
IV.以下几项参数必须测定:
固体份:
应为18-19%,否则应调整;
PH值:
应为6.2±0.3左右;
槽液温度:
应为27-29℃,否则应进行热交换。
槽液电导率:
此为槽液起始值,供以后参考监控。
3.槽液的熟化
槽液配好后,必须连续循环搅拌进行熟化,熟化时间不低于72小时。
熟化48小时后,即可取样,进行全项分析试验。
其中包括:
固体份、PH值、电导率、胺值、电泳成膜情况等试验,以便对不理想项目进行适当调整。
经检验,各项指标均符合施工要求方可进入施工调试。
4.施工调试
A.调试前准备
电泳调试前应做到以下几点准备工作:
a)电泳前处理各工序已调试完毕,能及时提供符合电泳要求的磷化工件;
b)具有浮漆回收系统的生产线,应事先将第一清洗槽的去离子水的PH值调整至6.5左右;
c)开启加热烘道,电泳处理后的工件能及时进行烘干处理。
B.调试过程
a)根据电泳槽大小,工件结构、极间距及阴阳极面积比等情况,预先设定调试压的区间,区间值最好不大于60V,同时设定电泳时间(或悬链速度)。
b)先以预设电压区间的下限开始电泳涂装,然后以20V电压差为一档次,逐步升压施工。
每一档次电泳涂漆工件的最低数量不得低于三只。
如发现电泳后所得湿膜有堆漆或击穿现象,应立即降低电压档次进行试车。
c)电泳后工件经清洗浮漆后,入烘道进行170℃×30min干燥。
d)对干燥后的涂膜进行全面测试,根据漆膜质量选定最佳施工电压。
e)稍降选定电压、稍升电泳时间或稍升选定电压、稍减电泳时间进行电泳施工。
根据涂膜质量并兼顾生产能力,确定最佳施工电压与施工时间。
f)维护槽液参数状态,按最终选定的施工电压和时间进行电泳施工。
(四)、施工工艺规范的确定
1.基本参数
Ø槽液PH值,6.2±0.3
Ø固体份,18-19%
Ø电导率,小于1200µS/㎝,应努力控制得稍低。
Ø槽液温度,应努力控制在27-29℃。
Ø电泳时间,2-4min,具体时间确定后,不宜随意改动。
Ø施工电压,160-300V,调试确定后不宜随便改变。
Ø颜基比,1:
3-4
Ø烘干温度,170℃×30min。
Ø槽液更新周期,不多于四个月。
另外,槽液要始终处于连续循环搅拌状态。
2.施工工艺规范的确定
电泳涂装施工工艺规范应在电泳调试结束后及时确定。
用户可单方或在我方协助下共同确定本规范,其基本要求是施工工艺的确定要以上述基本工艺参数为准则。
(五)、新漆补加的操作程序
通过回路先将槽液打入调漆缸中(或用去离子水),在搅拌情况下慢慢加入原漆,原漆与工作液的比例为1:
2,搅拌1-2小时后用玻璃板沾漆观察其溶解性,如玻璃板上无不溶颗粒,即为溶解完全,然后打入附槽。
如果发现溶解不好,适当延长搅拌时间,延长时间无效,往调漆缸中补加中和剂,溶解完全后打入附槽。
六、电泳施工管理
(一)槽液管理:
是阴极电泳涂装工艺中的重要管理项目,直接影响到电泳涂料的涂装效果。
1.槽液固体份
槽液固体份是稳定性管理的一个重要参数。
若电泳槽液长期在较低的固体状态下工作,就会使漆液的稳定性变得难以维护。
因为固体分低,不仅会道致泳透力下降,电解反应加剧,产生针孔、膜薄等漆膜弊病,而且导致槽液中的颜料和树脂分离沉淀。
固体分过高,不仅会因泳涂工件时造成不必要的浪费,在生产过程中,应维护恒定的固体分一般为18+2%,根据化验结果和产量随时调整,使槽液固体分控制在工艺规定范围内。
2.槽液PH值
漆液的PH值是影响漆液稳定性的关键参数。
阴极电泳的PH值一般为6.0+0.5。
当PH值小于规定值,造成工件泳透力低,所以在正常生产时一定要每班测定一次PH值,操作人员根据测定值及时调整设备及补加PH值调整剂,以确保PH值在规定范围,PH值偏低,排放阳极水;PH值高补加中和剂;补加中和剂时,一定要在补加原漆时补入调漆罐内,切勿直接加入主槽中。
3.槽液的电导率
槽液的电导率和槽液的固体分、PH值一样,都是每班必检的重点管理工艺参数。
科富涂料正常的控制指标为1200+500µs/m,若电导率上升,说明槽液中杂质离子增多,此时可以用排放超滤液幷向槽液补加去离子水来调整。
若电导率下降,说明槽液中树脂或颜料浆内在质量发生变化,应与供漆厂商协商,采用特殊组分来调整槽液,以避免影响膜厚及泳透力。
所以在生产中一定要监控原漆的电导率、加入槽液内去离子的电导率、入电泳槽前工件滴水的电导率、阳极液及超滤液的电导率等,这样可有效控制槽的电导率在规定值范围。
4.槽液的颜基比
槽液的颜基比反应了漆液的颜料的浓度。
对于双组分的乳液型电泳漆,颜基比一般控制在1/3~1/4范围的漆种较多。
在生产运行中,由于各种成膜物质泳到工件的比例不一定与原漆配比相同,加上漆液的稳定性的影响,颜基比会发生变化,因此,需要定期检测颜基比,幷根据检测结果添加乳液或色浆来调整颜基比,以确保颜基比控制在工艺范围内。
5.槽液溶剂的含量
目前,国内生产的阴极电泳漆在使用过程中都在补加溶剂,不同品种的电泳漆溶剂含量不同,所以补加量要根据电泳漆本身要求和槽液检测结果来添加,槽液溶剂含量需要每周测定一次,在夏季高温时,可适当增加检测次数,以确保槽液的稳定和涂膜质量;溶剂含量低补加补给剂,补加溶剂时,一定要在补加原漆时补入调漆罐内,切勿直接加入主槽中。
6. 槽液的温度
温度对电泳的质量、槽液的稳定性、涂膜的厚度影响较大。
由于在电泳过程中要产生热量,槽液循环搅拌时,也产生热量,所以一般电泳槽液以冷却为主。
但是,为了使槽液温度保持在工艺规定值+2℃的范围,对于大型电泳槽,均需设有专门的冷却和加热系统,以便更好控制槽液温度在规定范围内。
为保证制冷及加热系统的工作状态,一定要控制好冷却水、冷媒水的进、出口温度。
检查热交换器进口压力及自动控温系统的工作状态。
7.电泳施工对前处理要求
入槽工件无油、锈及残留磷化液,磷化膜应致密、均匀无浮灰、花斑。
进入电泳槽工件滴水电导率小于50µS/㎝。
8.原漆补加和去离子水补加
应坚持每天补加,最好是每班补加;液面下降需补入去离子水时,应在加原漆时补入调漆罐内(原漆溶解良好之后补入),或调整PH值为6.2左右后补入阳极水(或阳极罩)中。
9.一定要重点维护好超滤设备,超滤效果不佳,超滤液排出减少,滤膜要及时清洗更换。
10.循环搅拌
应努力坚持24小时连续搅拌。
极特殊情况下,最长停搅时间不超过两小时。
11.施工中常测数据
①固体份 ②PH值 ③电导率 ④MEQ值 ⑤槽液温度 ⑥各道冲洗水电导率及PH值,尤其是工件入槽滴水电导率及PH值 ⑦施工电压 ⑧施工电流