油脂生产管控方案.docx
《油脂生产管控方案.docx》由会员分享,可在线阅读,更多相关《油脂生产管控方案.docx(11页珍藏版)》请在冰豆网上搜索。
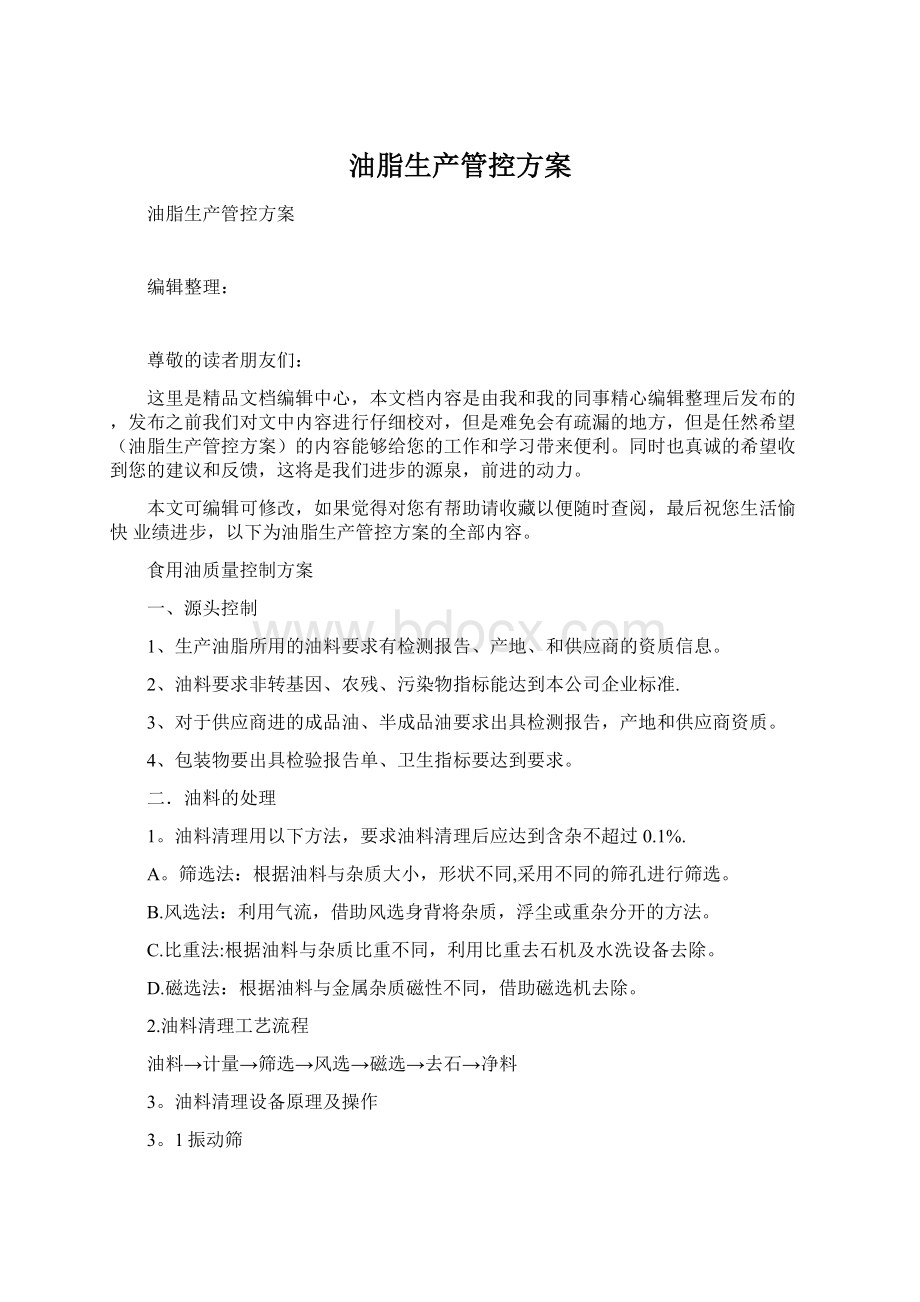
油脂生产管控方案
油脂生产管控方案
编辑整理:
尊敬的读者朋友们:
这里是精品文档编辑中心,本文档内容是由我和我的同事精心编辑整理后发布的,发布之前我们对文中内容进行仔细校对,但是难免会有疏漏的地方,但是任然希望(油脂生产管控方案)的内容能够给您的工作和学习带来便利。
同时也真诚的希望收到您的建议和反馈,这将是我们进步的源泉,前进的动力。
本文可编辑可修改,如果觉得对您有帮助请收藏以便随时查阅,最后祝您生活愉快业绩进步,以下为油脂生产管控方案的全部内容。
食用油质量控制方案
一、源头控制
1、生产油脂所用的油料要求有检测报告、产地、和供应商的资质信息。
2、油料要求非转基因、农残、污染物指标能达到本公司企业标准.
3、对于供应商进的成品油、半成品油要求出具检测报告,产地和供应商资质。
4、包装物要出具检验报告单、卫生指标要达到要求。
二.油料的处理
1。
油料清理用以下方法,要求油料清理后应达到含杂不超过0.1%.
A。
筛选法:
根据油料与杂质大小,形状不同,采用不同的筛孔进行筛选。
B.风选法:
利用气流,借助风选身背将杂质,浮尘或重杂分开的方法。
C.比重法:
根据油料与杂质比重不同,利用比重去石机及水洗设备去除。
D.磁选法:
根据油料与金属杂质磁性不同,借助磁选机去除。
2.油料清理工艺流程
油料→计量→筛选→风选→磁选→去石→净料
3。
油料清理设备原理及操作
3。
1振动筛
振动筛的操作要求:
A负荷要适当,不宜太大或太小,一般可控制料层的厚度来决定。
B及时清理筛面,要保持80%以上的筛孔畅通。
C及时调节下料量,保证物料在筛面上分布均匀。
3.2比重去石机
去石机操作要求:
A。
油料不应含有大杂及小杂。
B.流量应均匀稳定,流量过大油料不能形成悬浮状态,无法分级,过小料层易被气流吹穿。
造成气流分布不均,降低去石效率。
C。
风速要控制适当,过大过小都会使去石机无法正常工作。
D.保证设备密封性,以免造成气流短路降低去石效果。
3.3磁选
磁选工作原理是利用磁性对油料中的铁质进行清理,共分三种装置:
A。
分散装置:
在油料通过的流管处装置1-2块强力永久性磁铁,当油料通过时所含铁器被吸住。
B。
集中装置:
由若干块强力磁铁组成一个磁铁组,安装在溜管底部,进行去石。
C。
电磁铁装置:
利用通电线圈产生的磁力来清除铁杂质。
分为转筒式除铁机和带式吸铁机两种类型。
磁铁设备操作应注意:
(1)油料有均匀地流过磁版面,油料与磁版面距离不大于10毫米。
(2)油料流速不要太快。
溜管斜度应在60度以下,以免铁质被冲走。
(3)磁铁严禁敲打,撞击和高温,避免磁性减弱。
(4)及时清除磁铁上的杂质。
三.压榨法取油(热榨)
压榨法取油工艺流程
←油渣
回榨↓↑
清理→轧胚→蒸炒→压榨→饼→浸出工序
↓
毛油→过滤→精炼工序
压榨法取油是借助机械外力作用,将油脂从油料中挤压出来的制油方法。
压榨取油之前要进行油料轧胚并对油料进行蒸炒.
1.油料的轧胚
轧胚的要求:
料胚薄而均匀,粉末度小,不漏油。
料胚厚薄直接影响压榨和浸出出油率的高度,料胚越薄,出油率越高,但要求薄而不碎,尽量减少粉末度,以免对后续蒸炒压榨及浸出带来影响。
2。
料胚的蒸炒工艺要求
(1)润湿:
尽量使水分在料胚内部分布均匀。
方法有加水,喷直接蒸汽,水和直接蒸汽混合喷入等。
料胚的润湿水分分别为:
大豆16%-20%,菜籽16%—18%,花生仁15%-17%,棉籽18%—22%。
装料控制在80%-90%。
(2)蒸胚:
生胚润湿之后,在密闭的情况下进行加热,使物料胚蒸透蒸匀,经过蒸胚,料胚的温度提高至95-100℃,时间为50-60分钟.
(3)炒胚:
炒胚的作用是加热去水,使料胚达到最适宜压榨的低水分含量。
炒胚时要求尽量排除料胚中的水分,因此要打开排汽管插门,蒸锅的存料要少,控制在40%左右,出料温度应达到105—110℃,水分含量在5%—8%之间。
3.油料的压榨
(1)从料胚进入到出饼共分三个阶段:
A.进料阶段:
料胚开始塑性变形,油脂开始流出。
B.主压阶段:
压力加大,出油加速.C。
成饼阶段:
高压阶段,将挤出的油沥干,并防止料胚将油回吸。
(2)影响压榨的因素:
a料胚的水分和温度:
一般采用高温低水分压榨。
b压榨时间的影响:
转速越快,压榨时间越短;出饼越厚,压榨时间越短.新榨螺推力大,压榨时间越短。
4.毛油的过滤
(1)过滤的目的:
压榨毛油中含有10%的饼渣成为“油渣"。
压榨毛油中饼渣的存在,对毛油输送,暂存及油脂精炼都产生不良影响,因此应及时将毛油中的渣分离除去。
(2)毛油过滤的设备:
毛油过滤的设备分为:
a箱式压滤机,b板式过滤机,c叶片过滤机,d袋式过滤器。
(3)毛油过滤的方法:
a重力沉降分离:
只利用悬浮杂质与油脂的相对密度不同,在自然静置状态下,使杂质从油中沉降下来与油脂分离,其主要设备有沉降池,暂存罐,澄油箱。
澄油箱特点是对毛油中粗大饼渣的沉降效果好,机械捞渣和回渣。
但缺点是时间长,渣中含油大,油与空气接触时间长易氧化,影响毛油的品质.
b过滤分离:
是在重力机械外力的作用下,便悬浮液通过介质达到固液分离的目的.对过滤的介质的要求是具有多孔性,阻力小,耐热耐腐蚀,并有足够的强度。
通常采用的有:
棉织品,化纤织品,金属丝编织品及工业虑低等.过滤开始时,由于适宜的滤孔尚未形成,滤液一般浑浊,必须回油重滤,当滤框内滤渣层达到一定厚度后,滤出的油才能澄清。
(4)叶片过滤的操作:
叶片过滤机的每个周期由7个步骤组成,a进油循环.4—6分钟到出口视镜油清为止;b过滤.过滤阶段控制压力为0.35-0.4Mpa;c转罐(排空)。
关闭进油阀,用压缩空气将罐内毛油转入另一过滤机;d吹饼.转罐结束后,用压缩空气吹扫滤饼15—20分钟。
e打开蝶阀。
吹干后降低工作腔阀压力,通过压缩空气转向阀或转动手柄打开蝶阀;f卸滤饼。
打开压缩空气,启动振动器约一分钟,若排泄不彻底,可重复一次。
g关闭蝶阀进行下一步操作。
(5)叶片过滤操作注意事项:
a液滤浑浊,可能原因是滤网破损,泄露,出油口O型圈损坏,过滤压力不稳定等。
b梨形滤饼,原因是油固,液相密度差大,固体杂质多在工作中沉降。
c过滤压力上升过快,原因:
过滤速度低,油渣过细,进油量过大,滤网堵塞等。
四.冷榨工艺以花生为例
1、去杂分级
原料花生仁从投料口投入后,提升到比重去石机,去除重质杂质和灰尘后进入动态质量秤计量(设置频次50㎏/次),再进入花生分级筛,去除轻质杂质和细粒杂质,并对花生人工进行分级。
根据处理量设置筛选速度,电磁调速电机控制850~1000转/分之间.
2、烘干脱皮
经除杂后的花生仁进入烘干机,调节输送筛板速度和料层高度闸板(变频器控制在35~40之间)控制花生仁进料量,冷空气经蒸汽加热后送入烘干机内(干燥室内空气温度设置86~88℃)对花生仁进行烘干,使花生仁含水份在4~5.5%之间。
调节水分后的花生仁进入半粒机的存料箱,借助存料箱中旋转刮板的磨擦使部分红衣剥离。
花生仁再经三只胶辊二次破碎,绝大部分成1/2瓣,此时红衣基本剥离.红衣和胚分别用吸风和振动筛将其分离,脱除红衣和胚后的花生仁进行手工挑拣,去除霉变花生仁和其它杂质后,送去低温压榨。
操作要点:
a、及时清理半粒机下部振动筛筛网,防止堵塞.
b、根据生产处理量正确调节变频器设置,料层高度闸板和干燥室内空气温度。
锅炉送来的蒸汽压力应相对稳定,不能有太大的波动。
c、每班检测烘干花生仁水份二次,原料花生水份一次。
d、正确调节半粒机三胶辊间距,使破碎达到要求.
e、正确调节半粒机出料处和平胶带落料处红衣吸口的高低,避免花生仁细小粉末随红衣吸走。
严格控制仁中含皮及皮中含仁。
f、认真剔除霉变花生仁。
3、初榨
半粒状脱衣花生仁送入存料箱之前的进料绞笼处,调节后进行初榨,水分6%~8%,然后进入双螺杆低温榨油机上部蒸缸,调节温度在55~60℃,饼厚度在12~10㎜之间进入榨机,榨机电流一般在60~70A,控制初榨饼干基脂肪率15~17%。
4、复榨
粉碎的初榨饼送入单螺杆低温榨油机上部蒸缸,调节水分、温度后进行复榨,入榨水分8~10%,温度55~60℃,饼厚度在10~12㎜之间,榨机电流一般在35~40A,控制复榨饼干基脂肪率≤6.5%。
五.油脂精炼
1、油脂精炼的目的:
油脂精炼是根据不同的用途和要求,除去油脂中的有害成分,尽量减少中性油和有益成分的损失.同时尽可能为副产品的综合利用提供良好的原料.
2、油脂精炼包括的工艺过程。
A、去杂:
采用机械过滤的方法。
B、脱胶:
可用水化、酸炼,也可用碱炼的方法。
C、脱酸:
可用碱炼,水蒸汽蒸馏的方法.
D、脱色:
一般用白士,活性碳吸附的方法。
E、脱臭:
用水蒸汽蒸馏的方法。
F、脱蜡:
一般用低温结晶方法去除。
3、水化脱胶
水化脱胶是利用磷脂等胶溶性杂质的亲水性,将一定的量的热水或稀盐水,碱液或其它电解质在搅拌状态下加入热油中,使胶体杂质吸水、凝聚、沉淀后与油脂分离.
4、水化脱胶的质量控制要求:
(1)、加水量要适当,一般为含磷量的3。
5倍左右,过小磷脂脱不净,过大会使油脚太稀,严重的会造成乳化,不易分离。
(2)、温度视不同方法而定,要求操作温度与加水量相匹配,加水量大,温度宜高,加水量小,温度低些,但终温不应高于1000C.
(3)、搅拌速度控制:
开始要快些60-70r/min,当磷佛析出时减速到20-30r/min。
(4)、电解质的加量:
电解质促使磷脂凝聚紧密,沉降速度加快.降低中性油含量:
一般食盐或磷酸用量为油重的0。
2%~0。
3%,食盐与明不凡混合使用时,用量可各占油重的0.05%。
(5)、毛油的品质:
未成熟油料或变质油料所制取毛油,脱胶困难。
未蒸炒好的油料所取毛油影响胶胶效果。
5、碱炼脱酸
碱炼用的碱一般为烧碱溶液(NaoH),也可用纯碱溶液(Nazco3),烧碱有中和游离脂肪酸和较好的脱色作用,但也可能使部份中性油皂化而降低精炼率,纯不成可与游离脂肪酸发生分解反应,生成肥皂,二氧化碳和水,不与中性油发生皂化,对提高精炼率有好处。
但脱色能力差,生成的二氧化碳气体易造成溢锅。
设备利用率低,一般者采用烧碱进行碱炼,
其工艺流程为:
毛油中和静置水洗静置干燥过滤成品油
油肺器收中性油废水
6、碱炼脱酸的质量控制措施
(1)、用碱量:
用碱量可用计算方法或查表求得,通常称理论碱量,理论用碱量(千克)=0。
713X酸价X油重(吨)此外碱还会与中性油及其它杂质反应,还有如搅拌不匀等一些无形损耗,还得补加一些碱,才能达到碱炼效果,称为超碱量,一般加入量为油重0。
05%~0。
25%。
实际用碱量=理论碱量+超碱量.
(2)、碱液浓度:
主要由毛油酸价及色泽来决定。
一般菜用采用12—160Be碱液。
棉油酸价10以下用180Be碱液。
10—15酸价用200Be碱液。
酸价20以上用240Be碱液。
(3)、温度:
一般初温为防皂化采用较低温度。
终温一般60~800C太高皂粒疏松不易分利。
加热速度快有利二油皂分离,一般每分钟要升高10C。
(4)、搅拌:
中和反应时搅拌速度要快,加热升温时放慢搅拌速度。
水洗时搅拌速度不能太快。
搅拌时间不低于20分钟.加碱液时间10分钟左右。
(5)、毛油品质:
若毛油中含有多的磷脂,蛋白质等杂质会影响中和反应速度和增加皂脚含油。
因此碱炼前先脱胶,可提高精炼效果。
(6)在油脂在水洗罐里搅拌均匀取样检测酸值
7、脱色的基本原理及目的。
(1)、脱色的方法:
吸附脱色、加热脱色、氧化脱色、化学脱色等。
(2)、脱色作用:
脱除油脂中色素,微量金属,肥皂,磷脂及残留农药等。
(3)、原理:
主要由吸附剂的表面活力所产生的,在油与吸附剂加热按触后,达到吸附剂平衡。
从而达到脱色的目的,脱色前油脂必须脱水,因为活性白土吸附水分的能力比吸附剂色素更强,有微量水的存在会大