塑料模设计计算过程讲解Word文档下载推荐.docx
《塑料模设计计算过程讲解Word文档下载推荐.docx》由会员分享,可在线阅读,更多相关《塑料模设计计算过程讲解Word文档下载推荐.docx(36页珍藏版)》请在冰豆网上搜索。
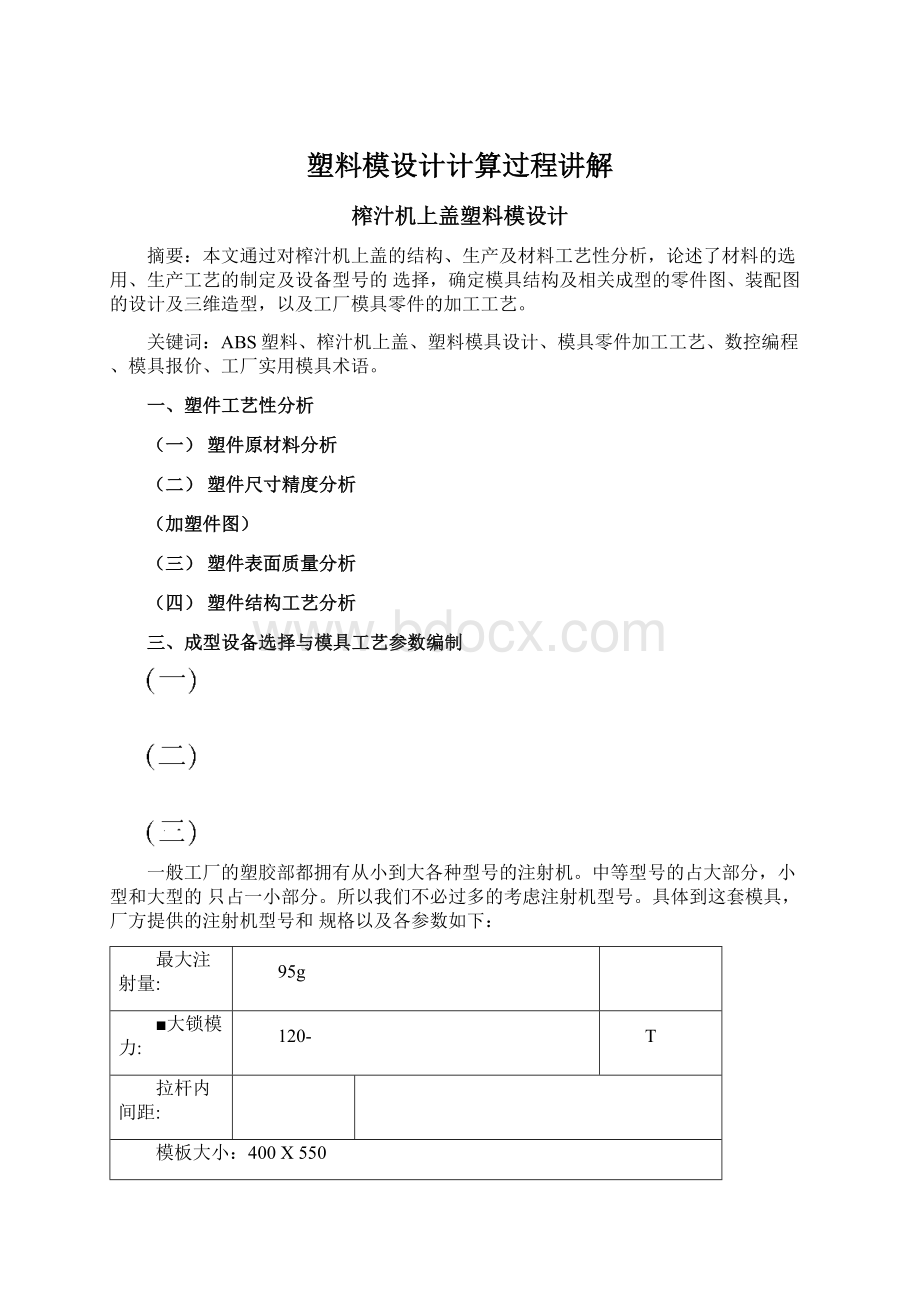
(一)确定型腔数量及排列方式
型腔的数量是由厂方给定,为“一出二”即一模二腔,他们已考虑了本产品的生产批量(小批量生产)和自己的注射机型号。
因此我们设计的模具为多型腔的模具。
考虑到模具成型零件和抽芯结构以及出模方式的设计,模具的型腔排列方式如下图所示
SHT1IDWA)WD口KF
图
(2)
(二)模具结构形式的确定
由于塑件外观质量要求高,尺寸精度要求一般,且装配精度要求高,因此我们设计的模具采用多型腔单分型面。
根据本塑件榨汁机上盖的结构,模具将会采用单个分模面,二个行位的结构。
(三)分型面位置的确定
如下图所示,采用A-A平直的分型面,前模(即定模)做成平的就行了,胶位全部做在后
模(即动模),大简化了前模的加工。
A-A分型面也是整个模具的主分模面。
下图中虚线所示的B
-B和C-C分型面是行位(即滑块)的分型面。
这样选择行位分型面,有利于线切割行位以及后
模仁和后模镶件这些成型零件。
分型面的选择应尽可能使塑件在开模后留在后模一边,这样有助于
后模设置的推出机构动作,在下图中,从A-A分型了,B-B处的行位向左移开,C—C处的行
位向右移开后,由于塑件收缩会包在后模仁和后模镶件上,依靠注射机的顶出装置和模具的推出机构推出塑件。
1rr
亠BC二
I
五、浇注系统设计
主流道设计
1、主流道尺寸
主流道是一端与注射机喷嘴相接触,另一端与分流道相连的一段带有锥度的流动通道。
主流道小端尺寸为3.5〜4mm。
2、主流道衬套的形式主流道小端入口处与注射机喷嘴反复接触,属易损件,对材料要求较严,因而模具主流道部分常设
计成可拆卸更换的主流道衬套形式(俗称浇口套,这边称唧咀),以便有效的选用优质钢材单独进
行加工和热处理。
唧咀都是标准件,只需去买就行了。
常用唧咀分为有托唧咀和无托唧咀两种下图为前者,有托唧咀用于配装定位圈。
唧咀的规格有①12,①16,①20等几种。
由于注射机的喷嘴半
径为20,所以唧咀的为R21。
图(4)
3、主流道衬套的固定
因为采用的有托唧咀,所以用定位圈配合固定在模具的面板上。
定位圈也是标准件,外径为①120mm,内径①35mm。
具体固定形式如下图所示:
j|—
///〈y/■
//
1
v
//;
//-//>
/
「/咆
7丄
;
^///\///
1///〒
ir-b
i///
\\\\
F■*■、X丄匸刀
11[L•••、\1-
\\\\\
X.
\
\\^I1
\\J1'
WAL
\、\、\\\'
\r
1'
\\\\\X
图(5)
(二)分流道设计
在多型腔或单型腔多浇口(塑件尺寸大)时应设置分流道,分流道是指主流道末端与浇口之间这一段塑料熔体的流动通道。
它是浇注系统中熔融状态的塑料由主流道流入型腔前,通过截面积的变化及流向变换以获得平稳流态的过渡段。
因此分流道设计应满足良好的压力传递和保持理想的
充填状态,并在流动过程中压力损失尽可能小,能将塑料熔体均衡地分配到各个型腔。
1、主分流道的形状及尺寸
主分流道是图(6)中从注射喷嘴开始到分流道为止的熔融塑料流动通道,主流道设计在浇口套之中。
为了便于加工及凝料脱模,分流道大多设置在分型面上,分流道截面形状一般为圆形、梯形、U形、半圆形及矩形等,在分流道设计中,若要减小在流道内的压力损失,则希望流道的截面面积大;
若要减小传热损失,则希望流道的表面积小。
因此可用流道的截面面积与周长的比值来表示流道的效率,该比值越大则流道的效率就越高。
各种流道截面的效率如下:
圆:
0.250D矩形:
0.250D半圆:
0.153D梯形:
0.195D
其中,圆形具有最大体积和最小表面积的特点,分流道的截面形状应以圆形截面为最佳,还有U形截面较常用。
本设计采用圆形截面的分流道,经查《注塑模具设计实用教程》第160页可得:
圆形截面
的分流道直径D一般在2~12mm之间,D》产品最大壁厚+1.5mm。
由于榨汁机上盖塑件的
最大壁厚为3.5mm,所以D>
3.5+1.5,暂取D为?
5mm。
由于榨汁机上盖塑件所选的材料为ABS,
所以查表10-1可得,ABS一般的流道直径尺寸在4.8~9.5mm的范围内,所以选圆形截面的分流道直径D为?
如图6所示:
2、主分流道长度
分流道要尽可能短,且少弯折,便于注射成型过程中最经济地使用原料和注射机的能耗,减少压力损失和热量损失。
将分流道设计成直的,总长70mm。
3、分流道的表面粗糙度
由于分流道中与模具接触的外层塑料迅速冷却,只有中心部位的塑料熔体的流动状态较为理想,因面分流道的内表面粗糙度Ra并不要求很低,一般取1.6卩m左右既可,这样表面稍不
光滑,有助于塑料熔体的外层冷却皮层固定,从而与中心部位的熔体之间产生一定的速度差,以保证熔体流动时具有适宜的剪切速率和剪切热。
实际加工时,用铳床铳出流道后,稍微省一下模,省掉加工纹理就行了。
(省模:
制造模
具的一道很重要的工序,一般配备了专业的省模女工,即用打磨机,沙纸,油石等打磨工具将模具型腔表面磨光,磨亮,降低型腔表面粗糙度。
)
4、分流道的布置形式
分流道在分型面上的布置与前面所述型腔排列密切相关,有多种不同的布置形式,但应遵循两方面原则:
即一方面排列紧凑、缩小模具板面尺寸;
另一方面流程尽量短、锁模力力求平衡。
本模具的流道布置形式采用平衡式,如下图:
图(7)
(三)浇口的设计
浇口亦称进料口,是连接分流道与型腔的通道,除直接浇口外,它是浇注系统中截面最小的部分,但却是浇注系统的关键部分,浇口的位置、形状及尺寸对塑件性能和质量的影响很大。
5、浇口的选用
浇口可分为限制性和非限制性浇口两种。
我们将采用限制性浇口。
限制性浇口一方面通过
截面积的突然变化,使分流道输送来的塑料熔体的流速产生加速度,提高剪切速率,使其成为理想的流动状态,迅速面均衡地充满型腔,另一方面改善塑料熔体进入型腔时的流动特性,调节浇口尺寸,可使多型腔同时充满,可控制填充时间、冷却时间及塑件表面质量,同时还起着封闭型腔防止塑料熔体倒流,并便于浇口凝料与塑件分离的作用。
从图⑹中可看出,我们采用的是侧浇口。
侧浇口又称边缘浇口,国外称之为标准浇口。
侧浇口一般开设在分型面上,塑料熔体于型腔的侧面充模,其截面形状多为矩形狭缝,调整其截面的厚度和宽度可以调节熔体充模时的剪切速率及浇口封闭时间。
这灯浇口加工容易,修整方便,并且可以根据塑件的形状特征灵活地选择进料位置,因此它是广泛使用的一种浇口形式,普遍使用于中小型塑件的多型腔模具,且对各种塑料的成型适应性均较强;
但有浇口痕迹存在,
会形成熔接痕、缩孔、气孔等塑件缺陷,且注射压力损失大,对深型腔塑件排气不便。
具体到这套模具,其浇口形式及尺寸如图(8)所示。
浇口各部分尺寸都是取的经验值。
实际加工中,是先用圆形铳刀铳出直径为①5mm的分流道,再将材料进行热处理,然后做一个
铜公(电极)去放电,用电火花打出这个浇口来的。
2、浇口位置的选择
模具设计时,浇口的位置及尺寸要求比较严格,初步试模后还需进一步修改浇口尺寸,无论采用何种浇口,其开设位置对塑件成型性能及质量影响很大,因此合理选择浇口的开设位置是提高质量的重要环节,同时浇口位置的不同还影响模具结构。
总之要使塑件具有良好的性能与外表,一定要认真考虑浇口位置的选择,通常要考虑以下几项原则:
(1)尽量缩短流动距离。
(2)浇口应开设在塑件壁厚最大处。
(3)必须尽量减少熔接痕。
(4)应有利于型腔中气体排出。
(5)考虑分子定向影响。
(6)避免产生喷射和蠕动。
(7)浇口处避免弯曲和受冲击载荷。
(8)注意对外观质量的影响。
9)所示的一个进胶
根据本塑件的特征,综合考虑以上几项原则,每个型腔设计如图(进浇点分流道开在前模仁上。
U--
图(9)
(四)浇注系统的平衡
对于中小型塑件的注射模具己广泛使用一模多腔的形式,设计应尽量保证所有的型腔同时得到均一的充填和成型。
一般在塑件形状及模具结构允许的情况下,应将从主流道到各个型腔的分流道设计成长度相等、形状及截面尺寸相同(型腔布局为平衡式)的形式,否则就需要通过调节浇口尺寸使各浇口的流量及成型工艺条件达到一致,这就是浇注系统的平衡。
显然,现模具浇注系统布置是平衡式的,即从主流道到各个型腔的分流道的长度相等,形状及截面尺寸都相同。
(五)冷料穴的设计
在完成一次注射循环的间隔,考虑到注射机喷嘴和主流道入口这一小段熔体因辐射散热而低于所要求的塑料熔体的温度,从喷嘴端部到注射机料筒以内约10-25mm的深度有个温度逐渐升高
的区域,这时才达到正常的塑料熔体温度。
位于这一区域内的塑料的流动性能及成型性能不佳,如果这里温度相对较低的冷料进入型腔,便会产生次品。
为克服这一现象的影响,用一个井穴将主流道延长以接收冷料,防止冷料进入浇注系统的流道和型腔,把这一用来容纳注射间隔所产生的冷料的井穴称为冷料穴。
冷料穴一般开设在主流道对面的动模板上(也即塑料流动的转向处),其标称直径与主流道大
端直径相同或略大一些,深度约为直径的1-1.5倍,最终要保证冷料的体积小于冷料穴的体积,冷
料穴有六种形式,常用的是端部为Z字形和拉料杆的形式,具体要根据塑料性能合理选用。
本模具
中的冷料穴的具体位置和形状如图(6)中所示,将冷料穴做在动模的深度方向,深度为分流道截
面面积的(1~1.5)倍,由于分流道截面直径为5mm,所以深度为(5~7.5)之间,本设计就取深度
为5mm。
实际上只要将分流道顺向延长一段距离就行了。
五、成型零件的设计与加工工艺
模具中决定塑件几何形状和尺寸的零件称为成型零件,包括凹模、型芯、镶块、成型杆和成型环等。
成型零件工作时,直接与塑料接触,塑料熔体的高压、料流的冲刷,脱模时与塑件间还发生摩擦。
因此,成型零件要求有正确的几何形状,较高的尺寸精度和较低的表面粗糙度,此外,成型零件还要求结构合理,有较高的强度、刚度及较好的耐磨性能。
设计成型零件时,应根据塑料的特性和塑件的结构及使用要求,确定型腔的总体结构,选择分型面和浇口位置,确定脱模方式、排气部位等,然后根据成型零件的加工、热处理、装配等要求进行成型零件结构设计,计算成型零件的工作尺寸,对关键的成型零件进行强度和刚度校核。
(一)成型零件的结构设计
本套模具的成型零件包括前模仁,后模仁,四个行位,两个镶件。
由前面分析分型面的确定可知,成型零件总体上可分为前模仁V平的,即图
(2)中A—A分
型面以上的部分〉,左边一个行位<图
(2)中B—B分型面以左的部分〉,右边一个行位<图
(2)
中C—C分型面以右的部分〉,后模仁<图
(2)中B—B分型面和C—C分型面以下的部分〉这三大部分,另外在后模仁上必须镶两个镶件上来,以形成榨汁机上盖塑料模中间的成形部位。
1.前模仁的设计
前模仁成形榨汁机上盖塑料件的外表面,外表面需要镜面抛光,模仁受的压力较大,据经验厚度需设计厚点,另外还要考虑到固定前模仁的螺丝孔的位置、运水(冷却水道)的布置、两个分流道孔、斜导柱从前模仁穿过的斜孔以及前模仁固定到前模框中的固定形式等。
设计前模仁的宽100mm,厚25.5mm,长190mm。
最终设计结构如图(10)所示,上面对称有四条运水,因此在前模框上钻对应四条运水的四个孔,再通过螺纹牙,锁紧到前模仁上的。
图(10)
(1)行位1的设计
行位1,即图
(2)中B—B分型面左边部分的成型零件。
其成型的关键部位的形状如下图虚线路径所示,即为行位成型部分的总体截面形状。
注意
其尺寸是已经由产品图放过缩水的,即产品图放大(1+平均缩水)的倍数
.“…'
图(11)
整个行位截面形状设计成下图所示的样子,总长22.5mm,总高6mm,由于我们设计的斜
导柱的倾斜角a为15°
,所以行位的锁紧角a‘=15+2°
〜3°
=15°
+2°
=17°
。
图(12)
72.5mm,
下图是上图从左边方向看过去的样子,即表达了行位长度方向的情况。
总长为每边还有5mm是导向用的。
图(13)
下面开始设计此行位的行程。
由于斜导柱倾角a—般在15°
~25。
之间选取,最常用的是
18°
和20°
特殊情况下也不可超过30°
角度太小斜导柱易磨损,甚至烧坏;
角度太大滑块
易卡死,即无法抽芯。
所以本设计的斜导柱倾角a取15°
;
锁紧角度B应比斜导柱倾斜角a大2°
~3°
,因为①开模时,滑块和锁紧块必须先分开,然后斜导柱才能拨动滑块实现侧向抽芯;
②合模时,斜导柱拨动滑块首先合模,然后锁紧块
锁紧。
若a,锁紧块与滑块将发生干涉,俗称撞模”。
所以本设计的锁紧角度B取17°
抽芯距S仁制品侧向凹凸深度S+(2~5)mm,(2~5)mm为安全距离。
本次设计的榨汁机上盖塑料件的侧向凹凸深度为3mm,所以抽芯距S仁制品侧向凹凸深度S+(2~5)=3+(2~5)=5~8mm,本次设计抽芯距为12mm。
斜导柱大小和数量可以查看《注塑模具设计实用教程》第131页表9-1,由表可得滑块宽度
在20~30的,斜导柱直径可取6~9mm,斜导柱数量为1;
本次设计取斜导柱直径为9mm,斜导柱
数量为1;
a—斜导柱倾角(15°
)
L=46.36+15.23+23tan15°
/2+(10-15)=35.94+3.08+15mm
图(14)
下面开始设计此行位上成型型腔的形状与工作尺寸。
首先设计榨汁机上盖塑料件上如下图所示的部分。
下图是该部分的尺寸图,一般情况下精确到小数点后两位即‘丝’就可以了。
成型型腔的工作尺寸就是产品图的尺寸再乘以(1+平均缩水率)。
这是对于产品图上未注公差的尺
寸而言。
图(15)
下图是上图放大
(1+0.005)倍后的图形,因此型腔上的凹槽的尺寸也就跟下图是一模一样
的。
图(16)
图(17)
另外,行位上面定位的孔,由于定位珠是标准件,定位孔是随着定位珠来的。
其截面形状和尺寸如下图所示:
图(18)
最后,还要设计斜导柱孔,因为斜导柱是选用的标准件,直径为09,而斜导柱孔要比斜
导柱单边要大50丝,所以直径为010,斜度为15°
另外还要开流道,其尺寸前面已经介绍。
最终的形状如下图所示。
更详细的情况请参见零件图纸。
图(19)
图(20)
(2)行位2的设计
行位2,即图
(2)中C—C分型面右边部分的成型零件。
其成型的关键部位的形状如下图粗线路径所示,即为行位成型部分的总体截面形状。
同样
其尺寸是已经由产品图(即图中的粗线)放过缩水的,即产品图放大(1+平均缩水)的倍数。
图(21)
导柱的倾斜角a为15°
所以行位的锁紧角a=15+2°
〜30=15°
下图是上图从右边方向看过去的样子,即表达了行位长度方向的情况。
op
图(23)
图(24)
F图是上图放大(1+0.005)倍后的图形,因此型腔上的凹槽的尺寸也就跟下图是一模一样的。
图(25)
6、后模仁的设计
(1)后模仁总体设计
后模仁,即图
(2)中B—B和C—C分型面下面部分的成型零件。
其成型的关键部位的形状如下图深蓝色线路径所示,即为行位成型部分的总体截面形状。
同样其尺寸是已经由产品图(即图中的粗线)放过缩水的,即产品图放大(1+平均缩水)的倍
图(26)
其整个截面总体尺寸如下图所示,中间凸出来的是成型部位。
左边要与图(12)所示的行位1
相吻合,右边要与图(21)所示的行位2相吻合。
后模仁的长度方向的情况与总体尺寸如下图所示,水直径为$6mm,深度从底面上来10mm。
总长为190mm,宽为100mm,其中四条运
图(28)
F面将设计后模仁上用于成型的型腔部分。
后模仁上要加工的成型型腔的部分不多。
首先
须在后模仁上开两个对称的多边形的通孔,用于配后模仁的镶件上来。
至于开孔的路径和尺寸
在如下图中已标示,粉红色的为线割路径,先用$3mm的钻一个穿丝孔,再用线割机编程加工;
上述两部分结构设计完后,后模仁就变成了下图所示的样子。
图(30)
最后要在后模仁上设计顶针孔的大小与位置,顶针就是脱模推出机构,即将塑件从后模上顶出。
由于产品面积不大,所以采用顶针顶出,如下图所示,本设计是将顶针设计在后模仁的镶件上,图中共有16支顶针,上下对称,直径都为$5伽。
qIDS口
QCDQQ
■•■
15.DC
in
图(31)
顶针孔在镶件上的位置与尺寸如下图所示。
JT
/f
T忖
chpu
II
fX.J、
亍〒一二二弋-
最终设计的形状如下图所示:
图(32)
图(33)
(2)后模仁镶件的设计
后模仁镶件就是镶在后模仁的镶件孔中,再顶到前模仁上,以形成榨汁机上盖塑料件中间
的成型零件。
它的总体截面外形及尺寸前面已确定,后模镶件在产品中的形状与位置如下图所示,由于后模仁的成型部份整体上来说就是镶件,图中的深蓝色也就表示了镶件所成型的部分。
简单的说,塑件哪里是空的镶件就要到哪个位置。
图(34)
在镶件上要做出如下图中粗虚线框所示的胶
镶件上的结构基本上都是与成型有关的结构。
位来,对称的另外一边也要做出同样形状的胶位。
图(35)
上述结构设计完后镶件就成了下图所示的样子。
同样必须注意,下图中特意标出来的尺寸,
在产品图上是有公差要求的,同样取上下偏差的中值加上基准尺寸(土0.10),再乘以(1+0.005)
得到型腔的工作尺寸。
Lp
1-—<
5.^1—-54.0C
sjr"
:
八于岳°
11J
让
图(36)
最终设计的后模仁镶件的形式如下图所示,当然还要做2个M6的螺丝孔以通过螺钉固定
在后模框上。
图(37)
另外在后模仁上还要设计出如下图所示的两个小镶件。
有利于排气;
图(38)
上述结构设计完后两个小镶件就成了下图所示的样子。
同样必须注意,下图中特意标出来的尺寸,
在产品图上是有公差要求的,同样取上下偏差的中值加上基准尺寸(土0.10),再乘以(1+0.005)
图(39)
成型零件的加工工艺
此部分内容是本毕业设计的特色所在。
成型零件结构设计完后,就要开始零件的下材料和加工制作等。
由于此塑件榨汁机上盖的材料的主要成分是ABS,要求有耐热性和耐低温的性能,同时耐酸、碱、盐,耐油,耐水,具有一定的化学稳定性和良好的介电性能,不易燃烧等。
由于本产品表面需要镜面抛光,因此其成型零件的材料的各种性能要求相当好,并且必须进行热处理,提高它们的硬度。
本套模具的成型零件都采用一种牌号叫S136-H的瑞典进口模具钢。
它是一般模具钢材中性能最好也是价格最贵的一种,一公斤要一百一十多港币。
它是一种预加硬透明耐蚀镜面模具钢,其主要成份和性能如下:
主要成份:
碳矽锰铬钒
%
0.380.90.513.60.3
出厂状态:
淬火加回火,HRC31-35
钢材特点:
1、最佳之抛光性。
2、渗透性良好。
3、良好之搞腐蚀性。
4、此钢材经淬火及镜面磨光后,其抗腐蚀性能更加可靠。
所有的成型零件的加工工艺大致可分为:
a)订材料、开料,b)热处理前的加工,c)热处理后的
加工,d)加工型腔等几道工序。
1、前模仁的加工工艺
(1)订材料、开料
由前面前模仁的结构设计可知,前模仁就是一个长方体。
其设计尺寸为190X100X25,
而订材料时的尺寸每边必须大约留3伽的余量,订料的尺寸为193X103X28,市场上的材
料厚度尺寸是有系列的,正好有厚度为28mm的料。
材料到了后,就要进行开料既开粗,开
粗的最终尺寸仍然单边要留20丝的余量,因为材料热处理后会有少量变形,余量是留给最
后精磨的,即190.4X100.4X25.4。
开粗既用开粗的铳床铳掉材料的表层,再到平面磨床上将材料粗磨成长方体。
(2)热处理前的加工
这里所说的热处理,其作用就是要提高材料的硬度,即将原来的HRC31〜35,淬硬到
HRC48〜52。
这种热处理具体采用的是什么方式,这是热处理厂的专利,另叽不知道,据说是真空油淬,且这种热处理后的材料变形量相当小。
反正只要告诉热处理厂材料要求的硬度就行了,热处理完后他们会测试材料的硬度是否达到了要求。
由于热处理后材料的硬度达到了HRC48〜52,普通的刀具再也加工不动了。
因此热处
理前加工一些精度要求不高的地方,如螺丝孔、运水、流道等。
在前面图(10)前模仁最终设计结构图中的所有结构,包括6个M10的内螺纹,四条
06的运水,4个运水螺纹牙,4个斜导柱孔,2个锥形的分流道孔,这些都是热处理前要加工的。
其中的个斜导柱孔必须和前模框装配好后,再一起钻09伽大的斜孔,钻好就要把
斜导柱配进去。
它们的配合必须是紧配合,绝对不能有松动,一有松动,斜导柱十有八九会断。
(3)热处理后的加工
前模仁热处理后,只