由模具所引之射出成型Word文档下载推荐.docx
《由模具所引之射出成型Word文档下载推荐.docx》由会员分享,可在线阅读,更多相关《由模具所引之射出成型Word文档下载推荐.docx(27页珍藏版)》请在冰豆网上搜索。
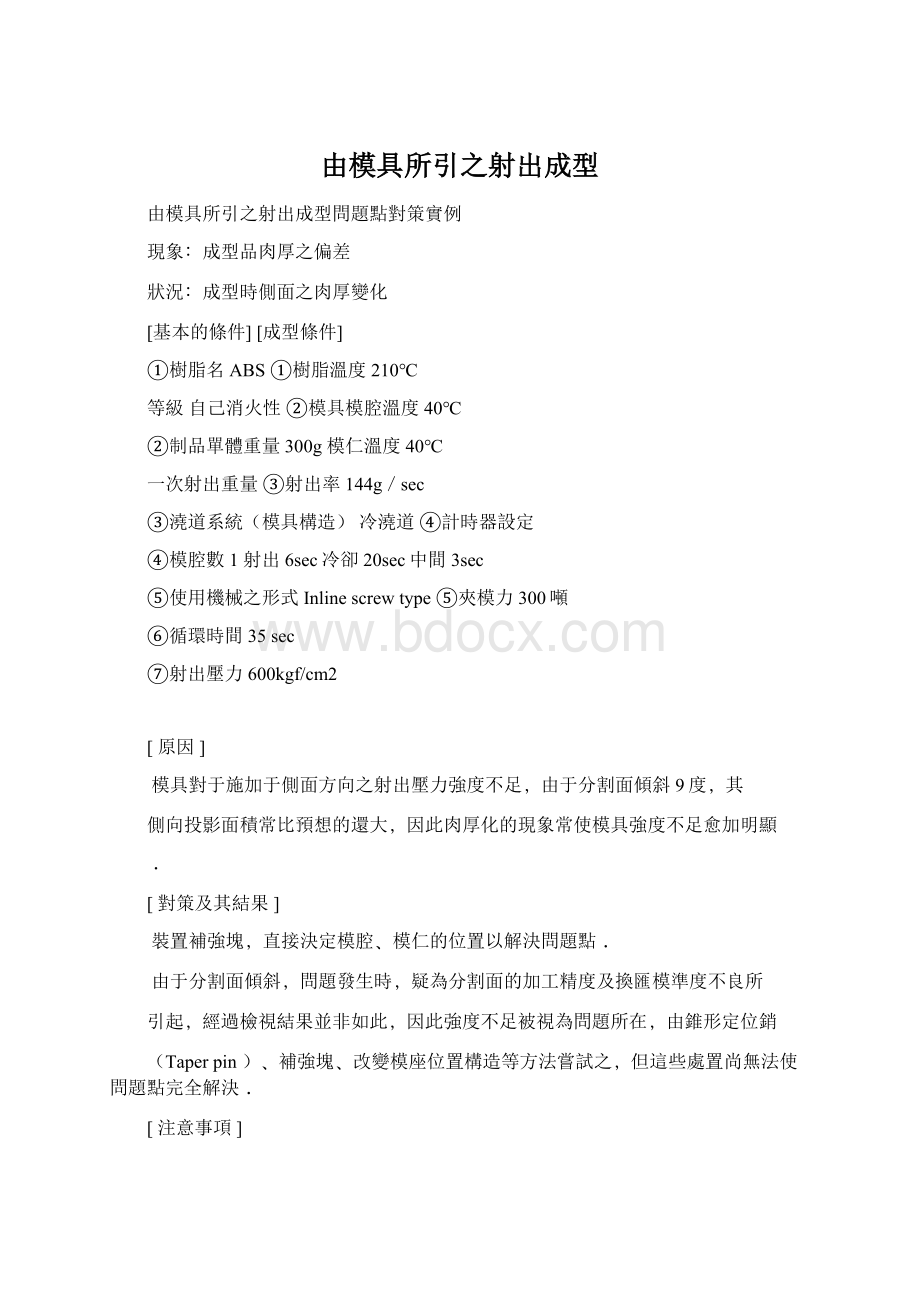
⑥循環時間42.4sec
⑦射出壓力1200kgf/cm2
[原因]
圓筒形狀部分過分研磨﹒為採取脫模對策﹐模具表面精度由﹒06S研磨至
0﹒03S﹐結果對模具的密著度增加反而使脫模更加不良﹒
[對策及結果]
精磨面用噴砂器加工使表面粗度至1S使解決了問題點﹒問題點發生時乃
進行問題分析﹑將表面粗度改善﹑給予斜度﹑改善周邊形狀的表面粗度或追加
頂出銷﹒但其結果並未改善﹐只是成型時問題點發生部位改變而已﹐這時乃開
始考慮反向因素﹒
脫模不良情形在表面粗度太好時也會發生﹒採用一種對策時應該也同時考
慮其反向因素﹒以本例而言﹐在進行追加斜度及表面精度改善之同時若能考慮
其反向因素則不致做多餘的工作﹒
現象﹕射出所形成的流紋
狀況﹕招牌面易生流紋﹐成型條件幅度小
1樹脂名聚酸醛(Ploycetal)①樹脂溫度205℃
等級90-35②模腔溫度70℃
2制品單體重量19g模仁溫度70℃
一次射出重量48g③射出率24g/sec
3澆道系統(模具構造)④計時器設定
冷澆道(1個下澆道口)射出18sec冷卻7sec中間2sec
4模腔數2⑤夾模力45噸
5使用机械之形式油﹐契⑥循環時間29sec
(toggle)式橫形⑦射出壓力720kgf/cm2
頂出梢縮短﹐設澆口凸耳﹐此處有下澆口﹐因此當流入樹脂碰到棒狀凸耳
﹐成品的表面(招牌面)因射模而發生流紋﹒
對策前澆口位置雖可由多段射出控制來解決﹐但成型條件限制多﹐此時澆
口若照圖所示的位置變更的話﹐流樹脂碰到模仁梢及模腔壁﹐不會直衝入招牌
面﹐則因射模所發生的流紋不再出現﹐而且成型條件變寬鬆﹐便利量產管理﹒
講求外觀之成品之澆口設計﹐應離招牌面(表面)較遠﹐使流入樹脂不直
接進入招牌面﹒
現象﹕內嵌玻璃的龜裂
狀況﹕內嵌玻璃成型時經常時發生龜裂
1樹脂名聚碳酸酯(Ploycarbonate)①樹脂溫度280℃
等級特殊②模具模腔溫度142℃
2制品單體重量46g模仁溫度140℃
一次射出重量64g③射出率45g/sec
3澆道系統(模具構造)冷澆道④計時器設定
4模腔數1射出10sec冷卻60sec中間10sec
5使用機械之形式Inlinescrewtype⑤模具結合力100噸
⑥循環時間80sec
⑦射出壓力1450kgf/cm2
受旁邊角凸緣的影響﹐成品因為傾斜著脫模﹐使得內嵌把持梢與玻璃相衝
突而發生龜裂﹒此時解決之方法應考慮到最佳之脫模點可能在被認為不可配置
頂出梢之面上﹒
确認不影響制品之機能原則下﹐在原來不可配置頂出梢之面配置頂出梢﹐
因此而解決問題點﹒上述問題原來用各种方法如把手持梢形狀變更﹐周邊形狀
部磨光﹑變更玻璃材質等去實施﹐但都無法解決﹐最后乃在制品設計上讓步﹐
在了解原設計規定此面不可配置頂出梢之用意只是為了避免因制造技術不良因
而在此面產生大毛邊之后﹐立即決一定了本處置方法﹒
頂出梢必定要配置最有效果的地方﹐本來是應遵守的原則﹐但有時因制品
上限制而無法依次原則時須多加注意﹒
以本例而言﹐若能盡快考慮是否一定不可配置頂出梢的話﹐則問題早就解
決了﹒
現象﹕因模具變形產生毛邊
狀況﹕成型還不到10萬次﹐模具即變形產生毛邊
1樹脂名①樹脂溫度250℃
2制品單體重量30g②模具模腔溫度40℃
一次射出重量150g模仁溫度35℃
3澆道系統(模具構造)冷澆道③計時器設定
4模腔數4射出3sec冷卻10sec
5使用機械之形式150SA④模具結合力140噸
日鋼140A⑤循環時間20秒
⑥射出壓力(樹脂部之壓力)
450kgf/cm2
咬斷狀的成型品為較不適當之設計﹐因其配合部發生咬嚙之現象﹐而成為
毛邊之形成原因﹒
如圖變更咬斷狀部之尺寸﹐可防止因咬嚙現象及模具變形而發生之毛邊﹐
改良前射出未達10萬次即發生問題﹐改良后30萬次仍未有異狀﹐可推測應具
有100萬次以上之耐久力﹒
成型品的要求特性中若有特地要避免毛邊之部分﹐或者對于毛邊的方向有
特別不容許的部分時﹐模具設計前﹐對于成品之要求應該充分理解后才開始進
行是很重要之一點﹒
現象﹕模具破損
狀況﹕滑動模仁周邊破損
1樹脂名ABS樹脂①樹脂溫度230℃
2制品單體重量40g②模具模腔溫度40℃
一次射出重量65g模仁溫度40℃
4模腔數1射出10sec冷卻15sec
5使用機械之形式東芝IS80④模具結合力80噸
⑤循環時間40秒
⑥射出壓力(樹脂壓力)600kgf/cm2
滑動模仁在隧道內滑動之構造在設計上是不得以之形狀﹐對此模具設計若
不加以注意將使模具破損﹒
成型品是ABS樹脂擴音器箱的蓋子﹐此蓋子為了要裝配于原箱子上有一
爪狀物在模仁側﹐由內滑動模仁以作內角(undercut)處理﹐如圖所示﹐
模仁在隧道狀之孔穴滑動而使較薄之「A」部破損﹐其對策是將滑動部分儘量
變小﹐把周邊薄的部分強化﹐以上的照片可能較難了解﹐左側是未對策品﹐右
側是改良品﹒
一般角狀梢式的滑動模仁﹐設有模仁本体滑動部之導引﹐原本滑動部之設
計越大的話耐久力應較強﹐本例則為減小以強化相反之例﹐是容易犯錯之形狀
狀況﹕成型品留于固定模上
[基本的條件][成型條件]
6樹脂名耐龍口66①樹脂溫度280℃
等級ラェポソザイテル101L②模具模腔溫度50℃
7制品單體重量2﹒88×
8模腔模仁溫度60℃
一次射出重量35g③射出率90g/sec
8澆道系統(模具構造)④計時器設定
冷澆道﹐下澆道口射出3﹒0/2﹒3sec冷卻20sec中間2﹒5sec
9模腔數8⑤模具結合力70噸
10使用機械之形式名機製作所⑥循環時間27sec
M-70A⑦射出壓力(樹脂壓力)700kgf/cm2
對于連結器機構部品成型模具之情形﹐在開模時如何設計使固定模﹑可動
模之脫模阻力大致相等時﹐因模具常有研磨或者內角(Undercut)之狀況﹐
其結果常使成型品殘留于固定模之情形﹒
固定模之模腔或者模仁在開模之前強制脫模﹐此處所指脫模方法之裝置一
般在可動模側﹐亦即開模及頂出同時行之﹐此种方式亦可使用于固定模側﹐則
固定與可動側之差异可消除﹐固定模之脫模問題可解決﹐尤其是開始成型試模
時﹐對除去短料之成型品也能揮發效果﹒
機構上多少會變成複雜﹐也許會提高成本﹐但成型生產順利的話﹐最后反
而可降低成本﹒在設計上或許因為較複雜而交期難縮短﹐此部分之機構之基本
形式若能標准化則能改善﹒
狀況﹕成型品固定附著
1樹脂名聚碳化合物(Polycarbonate)①樹脂溫度250~280℃
等級S-2000②模具模腔溫度80℃
2制品單體重量2﹒5g模仁溫度80℃(模仁梢115℃)
一次射出重量8g③射出率4g/sec
冷澆道﹐下澆道口射出6sec冷卻25sec中間3sec
4模腔數2⑤夾模力22噸
⑤使用機械之形式東芝IS-22P⑥循環時間40sec
⑦射出壓力960kgf/cm2
使用樹脂的特性表
廠牌(商品名﹐樹脂內容)三菱瓦斯化學
(コ-ピロソ﹐PC)
等級S-2000
性質單位條件
物比重1.2
理吸水率(%)23℃24hr
的23℃浸泡飽和0.23~0.26
性成型收縮率(%)0.5~0.8
質光線透過率(%)D10033mm厚85
熱熱變形溫度(℃)4﹒6㎏/㎝132~140
線膨脹系數(㎜/㎜/℃)18﹒6㎏/㎝6~7
的皮氏軟化點(℃)
性氧指數(%)1/16”
質燃燒性(UL94)1/8”V-2
絕緣破坏電壓(KV/㎜)D1491.6mm厚18~22
電誘電率60Hz2.85
氣D150106
的106Hz
性誘電正接60Hz
質106Hz0.082
體積固有抵抗(ohm-cm)23℃干燥2.1×
1016
耐電弧性(sec)D49580~120
抗拉強度(kg/cm2)D638600~700
伸降伏點(%)
力伸長破斷點(%)
引張彈性率(kg/cm2)
學彎曲強度(kg/cm2)D790820~920
彎曲彈性率(kg/cm2)D7902.3
的壓縮強度(kg/cm2)
壓縮彈性率(kg/cm2)
性斷強度降伏點(kg/cm2)
剪斷彈性率(kg/cm2)
質艾氏衝擊強度(kg.cm/cm)有凹口3.2mm75~120
引張衝擊強度(kg.cm/cm2)3.2mm24~27
耐疲勞限界(kg/cm2)
洛氏硬度(Rockwell)M尺寸
尺寸80~95
靜荷重變形(%)
斜度磨耗(mg)
Φ2及Φ3之模仁梢無法冷卻﹐成型時梢的表面溫度100℃以上﹐因此將成
型品帶往移動模側之表面阻力消失﹐而使成品附著于固定模側﹒
模仁梢之表面磨粗﹐冷卻時間延長至25秒即可量產﹐其永久對策乃為模具
重作﹒固定模及移動模反過來使套管凸出﹐其結果可使冷卻縮短到10秒左右﹒
若模仁梢較難控制溫度之情形時﹐則應先預測脫模阻力如何來決定模腔﹑
模仁之關系﹒此時必須十分注意制品設計所能允許的拔模斜度(或者反斜度)
現象﹕毛邊
狀況﹕通氣孔部的毛邊
①樹脂名PPS①樹脂溫度280~350℃
等級FZ1140②模具模腔溫度140℃
②制品單體重量0.05g模仁溫度140℃
一次射出重量2.4g③射出率7g/sec
③澆道系統(模具構造)④計時器設定
冷澆道﹐下澆道口射出1﹒5sec冷卻5sec中間1﹒5sec
④模腔數8⑤夾模力18噸
5使用機械之形式住友ミニマツト5/7
⑥循環時間10sec
⑦射出壓力1﹐000kgf/cm2
因樹脂流動良好及射出瞬間模具變形等因素而使0﹒09的通氣孔深度發生毛邊﹒
通氣孔深度減為0﹒003﹐但乃發生若干毛邊﹒由于高壓射出之瞬間模具產生變形﹐0﹒003實際上成為0﹒008之程度﹐因此將固定模加厚﹐通氣孔深度改為0~0﹒003﹐而解決通氣孔之毛邊問題﹒但每2小時若不做2次PL清除﹐則末端會有缺料情況發生﹒
較薄之小制品射出時須高壓﹐及高模溫﹐若用通常的通氣孔易生毛邊﹒因此有關通氣孔的深度﹐應考慮樹脂的流動性以及預知的成型條件才設定﹒
現象﹕頂出部隆起
狀況﹕頂出時﹐表面隆起
①樹脂名FR-PPS①樹脂溫度180~220℃
等級C-720X②模具模腔溫度45℃
②制品單體重量50g模仁溫度45℃(一部90℃)
一次射出重量60g③射出率15g/sec
冷澆道﹐下澆道口射出15sec冷卻30sec中間20sec
④模腔數8⑤夾模力40噸
⑤使用機械之形式日鋼J-40SA⑥循環時間69sec
⑦射出壓力800kgf/cm2
制品中央有一套管凸出﹐且周圍有四支頂出梢﹐因頂出梢所受的阻力太大﹐表面發生隆起之變形﹒
制品的外徑及內徑拔模斜度增大﹐頂出梢數量增加﹐結果至今雖然乃須慢慢頂出才可避免變形﹐但總算可以正常的成型﹒
對于各頂出梢或套管所受的拔模阻力是否均等應加以測試﹐尤其本次的產品其外周的內外皆在模仁之一邊﹐頂出時會發生真空狀態﹐比預想的頂出阻力還大﹐
必須加以注意﹒
現象﹕高度尺寸不良
狀況﹕由于冷卻不足而使高度尺寸不安定
①樹脂名加填充劑之PP(カルプ)①樹脂溫度180~230℃
等級3511G②模具模腔溫度45~50℃
②制品單體重量140g模仁溫度45~50℃一部105℃
一次射出重量320g③射出率53g/sec
冷澆道﹐下澆道口射出15sec冷卻50sec中間6sec
④模腔數2⑤夾模力150噸
⑤使用機械之形式東芝IS-150E⑥循環時間80sec
⑦射出壓力700kgf/cm2
固定模之子模A﹑B的前端之溫度上升至100℃以上﹐從固定模將板脫離
時引起變形而高度尺寸無法安定﹒
本來只有中央的子模有冷卻﹐現在全部子模都追加通氣口﹐而子模A﹑B之前端細小﹐冷卻作用無法暢通﹐乃將模具材料由Preharden鋼改成熱傳導性良好之鈹合金鋼﹐其結果40秒的冷卻程度即可達到50~60秒之冷卻效果﹐維持尺寸公差﹐不良降為零﹒
[注意]
板狀成型之拔模﹐若不充分考慮制品全體均等之頂出及中央側不同之脫模性﹐則高度尺寸就無法安定﹐尤其冷卻不完全之模具若不給予充分時間冷卻﹐高度尺寸亦無法安定﹒
現象﹕側脫模面的擦痕(脫模斜度小之情形)
狀況﹕成型時﹐制品側面拔模面產生擦痕
①樹脂名ABS樹脂①樹脂溫度210℃
等級難燃ABS②模具模腔溫度50℃
②制品單體重量1000g模仁溫度45℃
一次射出重量1170g③射出率65~85g/sec
梢頂澆口射出15sec冷卻35sec中間35sec
④模腔數1⑤夾模力430噸
⑤使用機械之形式直壓式650噸⑥循環時間85sec
廠牌(商品名﹐樹脂內容)ABS樹脂
等級AN260
物比重1﹒10
的23℃浸漬飽和
性成型收縮率(%)~6/1000
質光線透過率(%)
熱熱變形溫度(℃)4﹒6kg/cm90
線膨脹系數(mm/mm/℃)18.6kg/cm
性酸素指數(%)1/16”
質燃燒性(UL94)1/8”
抗拉強度(kg/cm2)460
力艾氏衝擊強度(kg.cm/cm)有凹口16
學引張衝擊強度(kg.cm/cm2)
的落錘衝擊強度(kg/cm)
性耐疲勞限界(kg/cm2)
質洛氏硬度(Rockwell)M尺寸
視問題面而處置
1成型條件分析樹脂溫度﹑射出壓力﹑模溫等之條件變更﹒
2側脫模面重作(側脫模面凹凸部改為曲面﹕excel處理)﹒
結果①②皆無法使問題面之擦痕消除﹒
原因追究
模具壁面測定(擦痕除去后)
1拔模斜度﹕良
2平面度﹕50um的凹凸﹒
目視測定良好﹐但乃用儀器定量測定﹒
原因﹕通常形雕機平面精度的經濟切削精度是35~50um﹒
平面度凹凸經過精密研磨形成良好摩擦面﹐可做一般成型﹒
1模具加工精度對制品品質有決定性影響﹒
2由于模具及成型技術高度進步使更困難的課題也可能達成﹒
3由側面觀之﹐設計者雖只對一個拔模斜度﹐但是乃應求得技術問題及經濟問題之整合來進行﹒
變現象﹕孔的真圓度不良
狀況﹕Φ10的真圓度規格為30um﹐但只能做到80-90um
①樹脂名PBT①樹脂溫度255℃
等級duranex3300②模具模腔溫度65℃
②制品單體重量7.5g模仁溫度68℃
一次射出重量44g③射出率40g/sec
冷澆道(6支梢澆口)射出8sec冷卻7sec中間2﹒5sec
④模腔數4⑤夾模力45噸
⑤使用機械之形式油壓﹐鍥式⑥循環時間19sec
(toggle)橫型⑦射出壓力700kgf/cm2
各成型品皆設有6點澆口﹐因為澆道設計不良﹐各澆口樹脂的流入不平衡﹐多路澆口的效果無法顯現出來﹒
由短料試驗法﹐知道六支次澆注口的一部分已呈流入平衡不良﹐澆道及6
支次流道之下設丹板狀根部成流入緩衡區則各澆注道及澆口樹脂之流入便可取得平衡﹐而因此孔之真圓度在對策后便由80~90um改善至28~30um﹒
現象﹕表面混濁
狀況﹕量產中時常發生
①樹脂名聚碳酸酯(Ploycarbonate)①樹脂溫度250℃
PC/ABS②模具模腔溫度60℃
②制品單體重量37﹒5g模仁溫度65℃
一次射出重量48﹒8g③射出率125g/sec
③澆道系統(模具構造)冷澆道④計時器設定
雙澆注口-側澆口射出5sec冷卻25sec中間4sec
④模腔數1⑤夾模力100噸
⑤使用機械之形式Toggle⑥循環時間37sec
inlinescrew⑦射出壓力950kgf/cm2
產生气体的殘留﹒模具製作之初時﹐澆注口頂出梢雖然裝有通氣口﹐但還不夠﹒(圖1)
澆道增加通氣口﹐大致可使混濁現象減少很多﹐但仍常發生(圖2)﹒澆道一部分嵌入燒結合金﹐使通氣口較完整﹒(圖3)﹐採取此種處理后混濁現象完全防止﹒
通氣孔的良好与否對成型品可產生相當之影響﹐但澆道部之通氣孔常有被疏忽之現象﹐尤其多數模之情形﹐澆道之通氣孔是不可或缺的﹒
狀況﹕澆口側触摸可感覺出毛邊存在
①樹脂名聚苯乙稀(Ploystyrene)①樹脂溫度230℃
②制品單體重量12g②模具模腔溫度29℃
一次射出重量55﹒6g模仁溫度33℃
③澆道系統(模具構造)下澆口③射出率165g/sec
④模腔數4④計時器設定
⑤使用機械之形式Toggle射出2.3sec冷卻4.8sec中間3sec
inlinescrew⑤夾模力120噸
⑥循環時間12sec
⑦射出壓力930kgf/cm2
模腔板之模腔中子之加工精度﹒(圖2﹑A部)
由毛邊狀況觀之﹐因進料壓力一旦使模具分開﹐射出完了再合緊時﹐則出現毛邊之現象﹐因此應檢視模具有否分開以及背板的通氣孔﹐若皆無异常﹐再調節A部(圖2)以解決﹒
下澆口以及梢頂澆口等澆口徑小之情形﹐進料壓力損失很大﹐另一方面樹脂溫度因澆口之摩擦而上升﹐因此為維持低黏度﹐對于小澆口之情形應注意其加工精度﹒
現象﹕合線紋
狀況﹕
①樹脂名丙稀(acryl)①樹脂溫度240℃
②制品單體重量20.8g②模具模腔溫度62℃
一次射出重量24.2g模仁溫度59℃
③澆道系統(模具構造)正澆口③射出率54g/sec
④模腔數1④計時器設定
⑤使用機械之形式Toggle射出6sec冷卻27sec中間3﹒5sec
inlinescrew⑤夾模力100噸
⑥循環時間38﹒9sec
⑦射出壓力980kgf/cm2
由于制品(如圖1)與圖2嵌合﹐合線只能允許在圖2范圍出現﹒圖1與圖2嵌合之孔在圖1之上﹐因此合線可能延伸至范圍之外﹒
模具溫度提升的話﹐但循環時間變長﹐為模具的梢(如圖3)A-1變更成圖A-2的形狀時﹐由梢A-2分開之溶融較A-1速度快﹐亂流較難產生﹐因此合線紋較短﹒
如圖1B部分在流入圖中有阻力的話﹐由中心流來之樹脂通過B部分時﹐衹要稍為通過的部分速度較快﹐此部分溫度即上升﹐無法流成同心圓狀而引起意想不到的表面不良﹒
現象﹕表面白化﹐尺寸差异幅度大
狀況﹕成型的脫模性非常不好
①樹脂名耐龍12①樹脂溫度180~230℃
等級AMN~O~P40②模具模腔溫度45~50℃
②制品單體重量Φ8×
2.7模仁溫度45~50℃一部105℃
一次射出重量4.5g③射出率53g/sec
③模腔數2④計時器設定
④使用機械之形式