工时损失管理办法Word下载.docx
《工时损失管理办法Word下载.docx》由会员分享,可在线阅读,更多相关《工时损失管理办法Word下载.docx(9页珍藏版)》请在冰豆网上搜索。
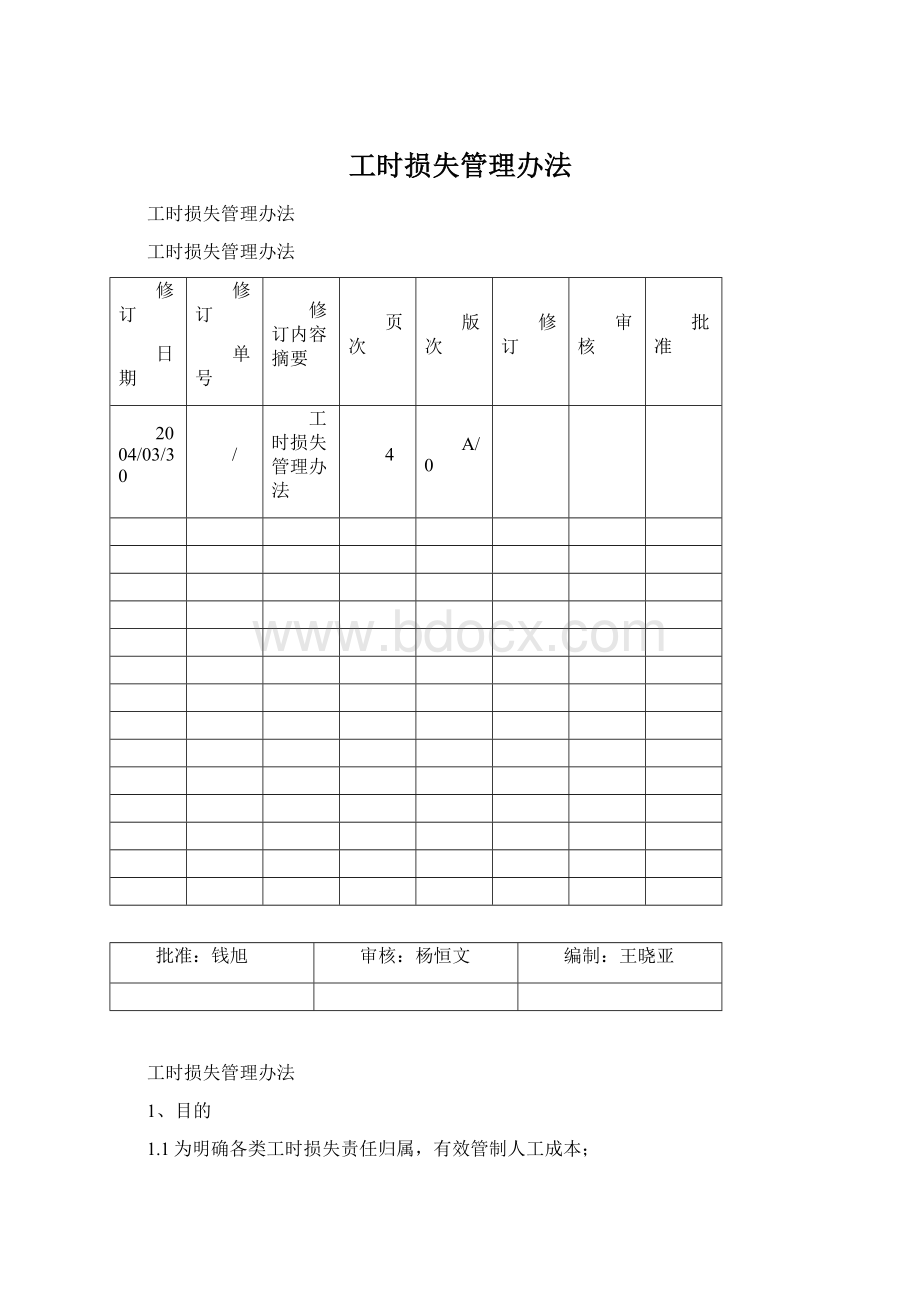
1.4规范工时损失填写,签核,转嫁依序进行,特制定本办法。
2、范围
公司所有直接人力。
3、权责
3.1技术部:
工时损失管理办法制定修改和补充及执行过程监督;
3.2生产部:
过程实施;
3.3综合办:
对工时损失管理办法执行协助;
3.4其它部门:
工时损失单的审核,确认。
4、定义
4.1工时损失是直接人员投入工时中的非正常工时;
4.2工时损失分为额外工时和异常工时;
4.3额外工时包含:
打样、试产、计划性换线、盘点、设备机台保养,培训等非异常造成的有价值工时损失;
额外工时包含:
固定和非固定额外工时;
如盘点和机台保养等为固定额外工时,打样、试产为非固定额外工时;
4.4异常工时包含:
非计划换线、工程变更、返工、特采、待料、来料不良、制程异常、设备/工具异常因异常造成的无价值工时损失。
5、工时损失类别及执行办法
5.1换线(停线):
换线前机种最后一件产品完成到换线后机种第一件产品出来并确认合格的全过程;
5.1.1换线损失范围:
流水线作业和机台作业,其余任何个人作业不可报换线工时损失;
5.1.2换线损失依IE所颁布换线工时(见附表)计。
由生产组长填写,生产科长/计划员共同签认,生产部门与公司各吸收50%;
5.1.3计划排配换线分为:
计划性换线和非计划性换线;
5.1.3.1计划性换线依5.1.2之规定计算;
5.1.3.2非计划性换线不可报换线损失项目,以实际异常项目填写,损失时间依以下规定计算;
5.1.3.2.1由于急单插入造成换线等损失由市场部签认吸收;
5.1.3.2.2由于待料/待工治具造成换线等损失由上制程或责任单位签认吸收;
5.1.3.2.3因制程异常,设备/工/治具异常,无法顺畅生产而换线,损失工时由责任单位签认吸收;
5.1.3.2.4因来料异常等外购物料造成换线等损失供应商100%吸收投入工时,相关责任部门承担相应的责任处罚;
5.1.4非计划性换线工时损失=(异常时间+换线时间)*受影响人数;
5.1.5计划性换线工时损失=换线时间*受影响人数。
5.2设备、工/治/模具异常
5.2.1设备、工/治/模具发生异常,但受影响人员有其它生产任务可做,即只可产生换线损失工时,以非计划性换线损失规定填写和审批;
5.2.2设备、工/治/模具发生异常,但受影响人员无其它生产任务可做,按以下规定处理;
5.2.2.1因对设备、工/治/模具操作不当,违规操作造成异常,由设备、工/治/模具管理单位明确注明,则工时损失由责任人或责任部门100%吸收;
5.2.2.2非人为操作原因由设备管理单位注明原由,并由设备、工/治/模具管理单位吸收因设备、工/治/模具异常影响正常生产的工时损失;
5.2.2.3设备、工/治/模具管理单位回复维修时间超过1H,由设备、工/治/模具管理单位和计划各吸收超出部分的50%,如设备、工/治/模具管理单位回复时间不准确(差异在0.5H以内合格),则由设备、工/治/模具管理单位吸收;
5.2.2.4设备、工/治/模具管理单位人员只确定维修时间,工艺人员确定恢复生产时间及受影响人数;
5.2.2.5故障时间以组长通知设备、工/治/模具管理单位时间为起点,生产部确认合格为终点,恢复生产时间以设备、工/治/模具合格为起点至出合格产品为终点,由现场工艺员记录;
5.2.2.6受影响人数指故障设备、工/治/模具(含)后工位配备受影响人数;
5.2.3设备、工/治/模具工时损失=(故障时间+恢复生产时间)*受影响人数。
5.3新产品试产
5.3.1指新产品在量产(转产前)的小批量生产,新产品试产工作由项目部主导,品管、工艺、生产均需派专人协助,在试产期间承担本部门的工作职责和工作联络;
试产期间发生任何工时损失均依照工时损失管理办法,由责任单位签认吸收;
例:
(1.)根据试产任务单试产时间确定为PM2:
00,而计划部PM2:
40才发料至生产线,这样计划部便需负责签认吸收这一部分损失=(2:
40-2:
00)*人数;
(2.)试产期间发生设备(工/治/模具)故障按照5.2条处理,样板问题由责任单位签认吸收,设备、工/治/模具问题由责任单位签认吸收;
(3.)试产时间确定为PM2:
00,而生产线却单方面延至PM3:
00,则投入工时应由PM2:
00计起,损失的这一个小时由生产部门吸收。
5.3.2新产品试产之前生产线必须做直接人员教育训练,训练时间统一为30分钟/次,注明培训主要内容和人员岗位,新产品教育训练工时损失由QE人员签认,公司吸收;
教育训练工时损失=参加训练直接人员数*30分钟
5.3.3试产标准工时由IE参照相似机种制订,试产依照IE工时填写日效报表,并按照正常日效报表处理。
5.4工程变更
5.4.1成品、半成品、在制品由于工程变更导致的工时损失依实际发生时间计,由提出单位签认,要求工程变更单位100%吸收;
5.4.2公司内部提出变更由责任单位100%吸收;
如因设计问题由项目吸收,因工艺难度大由现场工艺吸收,因物料采购难度大由采购吸收;
5.4.3客户提出可转嫁客户吸收,不可转嫁者由公司吸收;
5.4.4工时损失为与现有定额差异的部分,未转产前不可报此项损失。
5.5新人作业
5.5.1适用新进厂直接人力,以进厂第一个工作日起,试工期15日内为转正期限,过期未能转正的工时损失由生产部门和人事部门各吸收50%;
5.5.2新人作业必须填写报表,否则概不报工时损失,且经查实对负责人以“8H/天”的直接人力工资处罚;
5.2.3工时损失=产出工时*新进人数*系数;
系数:
检验岗位,转正前为40%,转正后半个月为20%,第二个月转为熟练工;
其它工种转正前40%,转正后为熟练工;
转正前:
扣除工时=产出工时*(1-系数)(针对集体或流水线作业),为未及时转正吸收之工时;
转正后:
贴补工时=产出工时*系数(对个人和集体皆适用)。
5.6支援(含代理)
5.6.1生产部门划分为:
注塑、涂装(含结构件、按键涂装)和装配(含结构件、按键装配);
5.6.2各部门间支援,在被支援部门填写日效报表,具体损失按以下规定执行;
5.6.2.1检验类作业前7天补给40%的产出工时,由人事和计划各吸收20%,7天过后不得补给;
5.6.2.2非检验类作业前7天补给20%的产出工时,由人事和计划各吸收10%,7天过后不得补给;
5.6.3生产部门内部作业人员岗位临时调动为部门内部管理问题,不按支援记;
5.6.4间接人力支援(支援职能部门),依实际发生的时间计算,填写日效报表,工时损失由职能部门吸收;
5.6.5部门内部间接人力代理必须严格按照公司代理制度执行,特殊情况如间接人力离职或职位空缺若需从直接人员提拔,则依所管理的直接人员出勤时间计算,代理时间不可超过1个月,工时损失由部门吸收;
5.6.6外出支援,支援时间等相关事项需被支援公司签认,其他时间依本公司作业时间制度给予,负责派遣部门责任人确认,相关责任单位吸收。
5.6.7支援时必须填写工时损失单才可补给工时,由技术部IE资料员在输入处理报表时进行折扣补给。
5.7返工(库存返工、制程返工、品退返工、客退返工)
5.7.1因IQC来料检验判为合格料后,在制程中或成品后发现因物料不符合客户品质要求产生返工损失工时由IQC吸收或通过IQC、计划部转给供应商吸收;
5.7.2生产送检后由FQC判退,返工工时由FQC签认,由责任人或生产部门100%吸收,无责任人则由生产部门吸收;
5.7.3因IPQC首件签错,FQC判退,返工工时由IPQC吸收40%,责任部门吸收60%;
5.7.4客户退货:
5.7.4.1为批量性不良退货,返工损失工时由品管吸收60%,相关责任部门吸收40%;
5.7.4.2为客户认定为重大缺陷且为非批量性不良,返工工时损失由生产部门100%吸收;
5.7.5所有涉及供应商来料不良则由供应商100%吸收投入工时,相关责任部门承担相应的责任处罚;
5.7.6支援返工,按支援项计,投入工时100%由被支援部门吸收;
5.7.7半成品/成品库存返工;
5.7.8.1因产出不足,与客户达成放宽标准,重新对已判NG的半成品投入工时,责任单位100%吸收;
5.7.8.2因限度样板问题导致半成品返工由QE100%吸收;
如品管签板已超书面标准或客户封样,则相应责任由公司吸收。
5.7.8.3因客户取消订单导致库存,过后恢复订单需返工,投入工时转客户吸收,无法转嫁则由公司和市场部各吸收50%;
5.7.9损失工时=总投入工时;
计划负责审核,责任部门确认吸收。
5.8特采
5.8.1来料合格,制成的成品特采出货后,客户退货所造成的工时损失由特采权限单位签认吸收40%,责任单位吸收60%;
5.8.2来料判特采,工时损失(含零件挑选,返工工时)依IE提供标准工时计,由计划部签认,转责任单位100%吸收;
5.8.3来料判特采,制成的成品特采出货后,客户退货所造成的工时损失(因来料特采造成时),由计划签认,判定单位担当责任处罚,工时损失转来料责任单位100%吸收;
属于自制零件由责任单位吸收80%,品管吸收20%;
5.8.4特采标识产品与正常良品区分不清导致混料,所带来的挑选和检查损失工时由QE签认,责任单位100%吸收。
5.9待料
5.9.1待料且无其它工作可做;
5.9.1.1在30分钟之内(含)则依实际发生时间计,工时损失由上制程或管理干部(部门)签认吸收。
工时损失=待料时间*受影响人数;
5.9.1.2超过30分钟且无其它事情可做的等待工时,主要是生产部与计划部调配不合理造成,工时损失分别是,生产部吸收60%,计划部吸收40%;
工时损失=待料时数*受影响人数
5.9.2待料并有其它事情可做
损失工时=待料时间*受影响人数+换线损失工时(见5.1.3.2.2条);
由计划审核,责任单位吸收;
因计划不当造成由计划吸收;
因来料不良造成的等待工时,供应商100%吸收投入工时,相关责任部门承担相应的责任处罚;
上制程造成由上制程吸收。
5.10来料不良
5.10.1因来料不良造成换线工时损失请参照“5.1.3.2.3”项;
5.10.2因来料不良造成返工工时损失请参照“5.7.6”项;
5.10.3因来料不良造成的等待工时损失请参照“5.9.2”项;
5.10.4IQC判合格物料,生产线实际生产时发现物料不良,应可开出来料不良异常单,通知品管处理。
因来料不良造成的挑选、返工、异常停线处理等各项损失均由品管签认,工时损失以投入工时计算,转供应商吸收,不能转供应商的由品管部和计划部共同吸收;
5.10.5公司内部来料,超出允收范围判挑选,造成检验难度加大,则挑选和增加检验项工时损失按投入工时计,由计划签认,责任单位品管吸收20%,责任单位吸收80%;
(允收范围可由品管与生产部门协议确定);
5.10.6供应商来料不良,品管已判退,但由于交期压力改为上线挑选,造成的各项损失由计划部签认,转供应商吸收,不能转供应商吸收的由计划部吸收;
5.10.7所有来料不良损失单必须由责任单位确认,供应商和外协由计划部确认;
对供应商和外协商扣款工时损失数量必须经由IE核对签认。
5.11盘点
5.11.1盘点前期确定盘点人员、级别、盘点时间段、需求直接人力参与盘点必须明确提报姓名/工号/盘点时间数等各种信息;
工时损失=影响时间*受影响人数,由财务签认并吸收;
间接人力不报工时损失。
5.12停电/水/气(以现已有自备电力、水、气等设备)
5.12.1外因停电30分钟以内,工时损失由设备科签认,公司吸收;
工时损失=影响时间*受影响人数;
5.12.2内因停电30分钟以内,工时损失由设备科签认吸收;
工时损失=影响时间*受影响人数
5.12.3停水/气同上
5.12.4停电/停水/气30分钟以上;
5.12.3.1设备科在30分钟内对停电或停水的情况进行维修能力作出评估,则工时损失由计划部与对应生产部签认各吸收50%;
工时损失=(影响时间-30min)*受影响人数
5.12.3.2设备科未能在30分钟内做出评估的,评估时间段的工时损失由设备科吸收,过后依“5.12.3.1”执行。
5.13教育训练
5.13.1指以授课方式进行的临时的停产8H(8:
30---17:
30或20:
30—4:
30)内(不含中午、下午休息时间)教育训练,工时损失依实际发生时间计;
由综合办签认,转公司吸收。
5.13.2如因订单不足,生产线未排生产任务而进行的教育训练,不可报工时损失;
5.13.3在人力培训计划内的教育训练不可报工时损失;
5.13.4为配合公司活动而开展的系列教育训练和培训时间由综合办签认,公司吸收。
5.14制程异常
5.14.1供应商或外协来料不良导致产线异常依“5.10”项处理;
5.14.2设备/工/治/模具导致产线异常依“5.2”项处理;
5.14.3投料错误:
5.14.3.1因BOM表错误或不合理由责任部门100%吸收,品管审核;
5.14.3.2因生产仓库发料错误由仓库100%吸收,品管审核;
5.14.3.3因生产投料错误,由生产部门100%吸收,品管审核;
5.14.3.4影响工时数在50H以上,责任单位吸收60%,品管吸收40%;
5.14.4制程异常需开出制程异常单,由现场品管或计划员确认,由责任单位人员签认吸收;
5.14.5为本部门造成的异常必须开工时损失单,经IE查核有隐瞒或经员工投诉的,对管理干部进行行政处分处罚,工时损失由责任部门100%吸收。
5.15协助工程打样及配合客户参观等
5.15.1协助工程打样;
5.15.1.1限于打样量小于200件,超过200件参照“5.3”条款;
5.15.1.2打样工时以投入工时计,计划或质量审核,项目签认吸收;
5.15.2配合客户参观,工时损失由计划签认,由公司吸收。
5.16机台保养,消防教育演习
5.16.1机台日常性点检和周边5S等不可报损失工时;
5.16.2周期性设备保养(周/月/年)参照IE制定的保养时间进行提报,高出部分须提报详细的说明报告,固定保养时间由IE签认公司吸收;
5.16.3临时性大保养(超过30min)由计划部审核,相关责任单位100%吸收;
5.16.4消防教育训练及消防演习所造成的工时损失(在正常班(8:
30—17:
30和20:
30---4:
30,不含休息时间)由生产各部门填写,综合办签认并吸收,非正常班内不可报损失。
5.17其它
对各种突发事件无法对应以上项目,统一规划为其它项处理,由责任单位或公司吸收。
6.工时损失办法执行规定
6.1工时损失单错误责任承担为,填写担当:
80%;
审核担当:
10%,确认担当:
10%;
6.2对于填写合理之工时损失,责任单位不得拒签;
经IE查证,属该单位责任而不签收者进行考核扣分;
6.3工时损失不得虚报及冒签,经IE查证属冒签,给予冒签人员以所签工时损失工资200%的处罚;
6.4异常(本办法无明确规定)工时损失责任,经IE了解相关工时损失单位的意见后,由IE直接判定工时损失的归属及工时损失分摊转嫁;
6.5工时损失单提交时间同日效报表,如有延误,按《数据报表管理办法》相关条款处理;
6.6IE根据生产日报表,每周/月统计各单位产生及吸收之工时损失,对各类别之工时损失分类汇总,造成的工时损失作为各部门考核基础数据;
6.7以上所有损失项填写单位为生产部门,审核单位为计划部或品管部,并由吸收单位人员签名确认,最后由现场IE人员稽核签名,无IE人员签名的工时损失单无效。
7.工时损失管控
7.1工时管控的重点是异常工时损失类;
7.2额外工时管控重点在协助项目工程打样,重点涉及部门为:
项目、计划、生产,此部分依照财务成本核算进行控制,IE统计打样工时并每周提交财务部一份;
7.2.1机台设备周期保养时间由IE制定标准保养时间,超出部分纳入异常工时损失控制范围,其它额外工时损失依实际情况处理;
7.3异常工时损失控制以计算异常工时损失率(见附表二),并设定相应的指标,纳入各部门考核,具体指针见附件。
8.附表
8.1表一:
《工时损失单》
8.2表二:
《直接人工工时结构项目与管理综合表》
8.3表三:
《量试制程工时管制表》
8.4表四:
《换线工时表及说明》