抗硫管道自动焊开发及应用.docx
《抗硫管道自动焊开发及应用.docx》由会员分享,可在线阅读,更多相关《抗硫管道自动焊开发及应用.docx(15页珍藏版)》请在冰豆网上搜索。
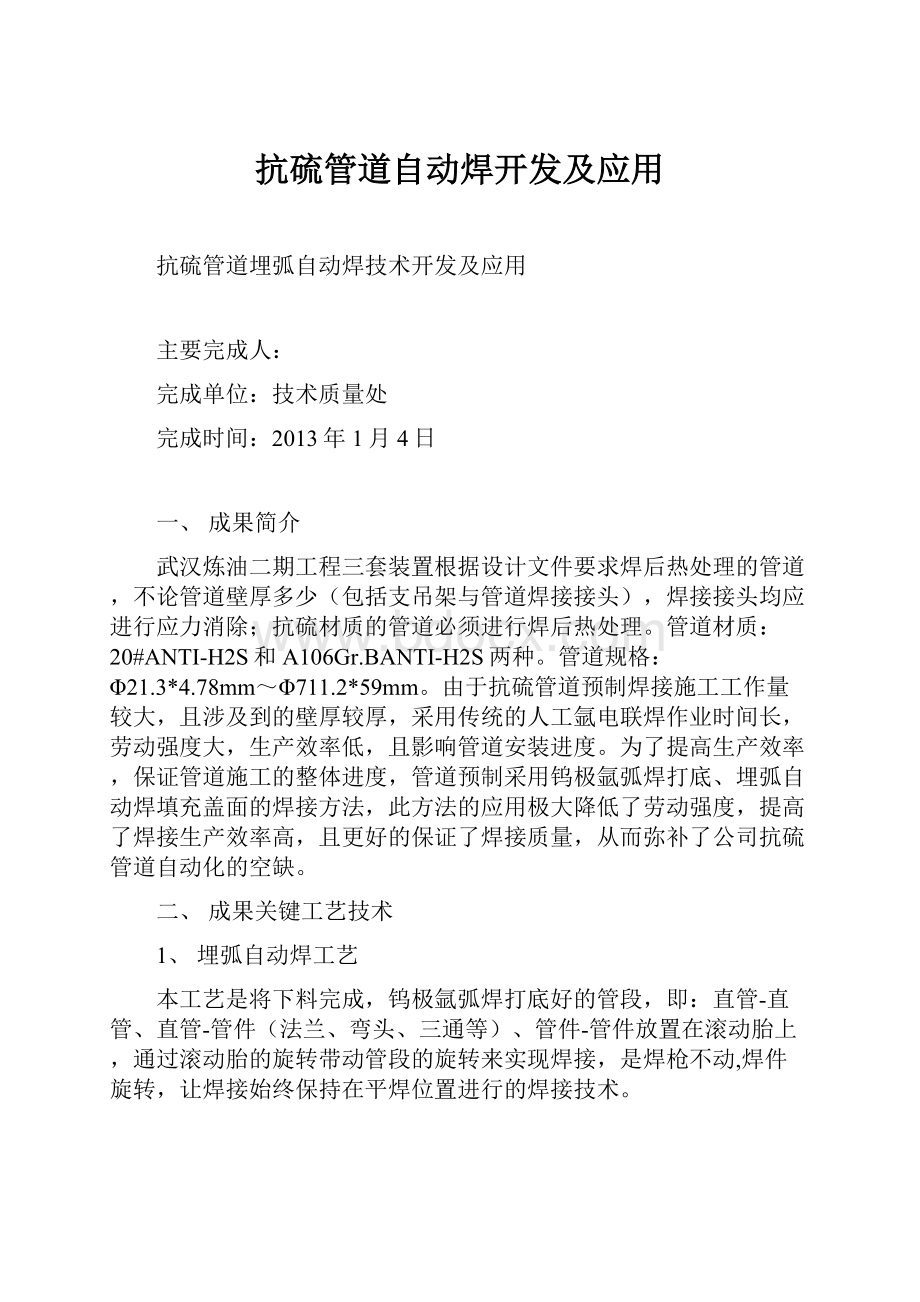
抗硫管道自动焊开发及应用
抗硫管道埋弧自动焊技术开发及应用
主要完成人:
完成单位:
技术质量处
完成时间:
2013年1月4日
一、成果简介
武汉炼油二期工程三套装置根据设计文件要求焊后热处理的管道,不论管道壁厚多少(包括支吊架与管道焊接接头),焊接接头均应进行应力消除;抗硫材质的管道必须进行焊后热处理。
管道材质:
20#ANTI-H2S和A106Gr.BANTI-H2S两种。
管道规格:
Φ21.3*4.78mm~Φ711.2*59mm。
由于抗硫管道预制焊接施工工作量较大,且涉及到的壁厚较厚,采用传统的人工氩电联焊作业时间长,劳动强度大,生产效率低,且影响管道安装进度。
为了提高生产效率,保证管道施工的整体进度,管道预制采用钨极氩弧焊打底、埋弧自动焊填充盖面的焊接方法,此方法的应用极大降低了劳动强度,提高了焊接生产效率高,且更好的保证了焊接质量,从而弥补了公司抗硫管道自动化的空缺。
二、成果关键工艺技术
1、埋弧自动焊工艺
本工艺是将下料完成,钨极氩弧焊打底好的管段,即:
直管-直管、直管-管件(法兰、弯头、三通等)、管件-管件放置在滚动胎上,通过滚动胎的旋转带动管段的旋转来实现焊接,是焊枪不动,焊件旋转,让焊接始终保持在平焊位置进行的焊接技术。
2、焊接工艺评定开发
2.1开发原因
2.1.1抗硫管道的埋弧自动焊在公司没有成熟的焊接工艺,且所用的焊材及焊剂在国内都没有批量生产。
2.2.2补充完善公司抗硫管道预制自动化的空缺。
2.2情况介绍
由于本装置抗硫管道壁厚较厚,需要能够覆盖抗硫管道壁厚范围的埋弧自动焊焊接技术要求,故选用规格为Φ114*8.5mm和Φ323.8*33.32mm的试件开发其焊接工艺技术的符合性。
2.3焊接工艺评定
抗硫管道在国内施工中几乎没有采用埋弧自动焊焊接,且埋弧自动焊的焊丝询问国内焊材厂家都没有生产及存货,故焊丝为特殊采购。
经过询价、生产能力、产品质量对比,最后确定由自贡大西洋提供Φ1.6mm焊丝(CHW-S1SH)及匹配的焊剂(CHF102SH)完成此项任务,其中焊丝为企业标准(企标B-001)。
2.3.1规格为Φ114*8.5mm的焊接工艺评定
(1)焊接方法及焊材
钨极氩弧焊打底,熔敷金属厚度为3mm,埋弧自动焊填充盖面。
打底焊丝:
型号为CHG-SH,牌号为ER50-G,规格为φ2.5mm,填充盖面焊丝:
型号为CHW-S1SH,牌号为H08SH,规格为φ1.6mm,焊剂牌号为CHF102SH。
(2)无损检测结果
经RT检测后,共计6张片,均为一级片。
(3)力学性能试验
1)拉伸试验结果:
试样编号
试样规格(mm)
破坏载荷(KN)
抗拉强度(MPa)
破坏部位
201224ASF-MV
20.4*8.4
78.64
460
焊道
201224ASF-MV
20.5*8.4
80.94
470
母材
2)弯曲试验结果:
试样编号
试样规格(mm)
弯曲类型
弯心直径(mm)
弯曲角度(゜)
实验结果
201224ASF-MV
38*8.5
焊道面弯
φ34
180
合格
201224ASF-MV
38*8.5
焊道面弯
φ34
180
合格
201224ASF-MV
38*8.5
焊道背弯
φ34
180
合格
201224ASF-MV
38*8.5
焊道背弯
φ34
180
合格
4)冲击试验结果:
试样编号
试样规格(mm)
缺口位置
冲击温度(℃)
冲击功AKV(J)
201224ASF-MV
10*5
焊道中心
-20
90
201224ASF-MV
10*5
焊道中心
-20
83
201224ASF-MV
10*5
焊道中心
-20
88
201224ASF-MV
10*5
热影响区
-20
52
201224ASF-MV
10*5
热影响区
-20
60
201224ASF-MV
10*5
热影响区
-20
40
5)硬度检验结果、:
试样编号
试样规格(mm)
检测部位
布氏硬度值
结果
201224ASF-MV
Φ114*8.5mm
焊道
143
合格
201224ASF-MV
Φ114*8.5mm
焊道
145
合格
201224ASF-MV
Φ114*8.5mm
焊道
145
合格
201224ASF-MV
Φ114*8.5mm
热影响区
155
合格
201224ASF-MV
Φ114*8.5mm
热影响区
160
合格
201224ASF-MV
Φ114*8.5mm
热影响区
159
合格
201224ASF-MV
Φ114*8.5mm
母材
151
合格
201224ASF-MV
Φ114*8.5mm
母材
151
合格
201224ASF-MV
Φ114*8.5mm
母材
151
合格
2.3.2规格为323.8*33.32mm的焊接工艺评定
(1)焊接方法及焊材同Φ114*8.5mm焊接一致。
(2)无损检测结果
经RT检测后,共计6张片,均为一级片。
(3)力学性能试验
1)拉伸试验结果:
试样编号
试样规格(mm)
破坏载荷(KN)
抗拉强度(MPa)
破坏部位
201225ASF-MV
35.2*20.8
309.9
425
焊道
201225ASF-MV
35*21
306.8
415
焊道
2)弯曲实验结果:
试样编号
试样规格(mm)
弯曲类型
弯心直径(mm)
弯曲角度(゜)
实验结果
201225ASF-MV
33*10
焊道侧弯
φ40
180
合格
201225ASF-MV
33*10
焊道侧弯
φ40
180
合格
201225ASF-MV
33*10
焊道侧弯
φ40
180
合格
201225ASF-MV
33*10
焊道侧弯
φ40
180
合格
3)冲击试验结果:
试样编号
试样规格(mm)
缺口位置
冲击温度(℃)
冲击功AKV(J)
201225ASF-MV
10*10
焊道中心
-20
298
201225ASF-MV
10*10
焊道中心
-20
296
201225ASF-MV
10*10
焊道中心
-20
298
201225ASF-MV
10*10
热影响区
-20
297
201225ASF-MV
10*10
热影响区
-20
298
201225ASF-MV
10*10
热影响区
-20
297
4)硬度检验结果
试样编号
试样规格(mm)
检测部位
布氏硬度值
结果
201225ASF-MV
Φ323.8*33.32mm
焊道
148
合格
201225ASF-MV
Φ323.8*33.32mm
焊道
150
合格
201225ASF-MV
Φ323.8*33.32mm
焊道
146
合格
201225ASF-MV
Φ323.8*33.32mm
热影响区
151
合格
201225ASF-MV
Φ323.8*33.32mm
热影响区
155
合格
201225ASF-MV
Φ323.8*33.32mm
热影响区
150
合格
201225ASF-MV
Φ323.8*33.32mm
母材
133
合格
201225ASF-MV
Φ323.8*33.32mm
母材
134
合格
201225ASF-MV
Φ323.8*33.32mm
母材
134
合格
通过以上焊接工艺评定试验,选用自贡大西洋的焊材及焊剂,测得各项试验结果均能符合设计、规范要求,且能够满足工程施工要求。
3、工程实际应用
3.1施工程序
3.2下料及坡口加工
管道下料及坡口宜采用机械加工,当管径较小或管子壁厚较薄采用氧乙炔焰切割时,切割后必须打磨掉影响焊接质量的表面淬硬层,并将凹凸不平处用砂轮机打磨平整。
坡口形式的选择以确保根部焊透为原则,在此基础上,考虑尽量减少焊缝尺寸,减少焊缝的熔敷金属量。
一般情况下,厚度小于25mm时,采用V型坡口,大于25mm时加工成双V型或VY型坡口,坡口加工见下图:
3.3组对
焊接接头组对前用角向磨光机和棒式砂轮机将坡口及两侧内外各20mm范围内的母材表面打磨露出金属光泽,不得有油污、锈斑、毛刺等。
组对时要保证内壁平齐,组对错边量不超过壁厚的10%且不大于2mm。
3.4定位焊
定位焊采用钨极氩弧焊,定位焊缝长度10~20mm,高度2~4mm,沿焊缝均布,公称直径DN>300的管道定位焊缝不少于4点,公称直径DN≤300的管道定位焊缝3~4点。
3.5焊前预热
当管道壁厚δ≥25mm时要求预热。
预热宜采用电加热法,预热温度≥80℃。
预热范围为坡口中心为基准,两侧各不小于壁厚的5倍,且不小于100mm,并应在坡口两侧均匀进行加热,防止局部过热,加热区以外的100mm范围内宜予以保温。
3.6打底焊
打底焊接采用钨极氩弧焊,所用氩气纯度不得低于99.99%,焊丝使用前应进行清理,除油、锈等污物,防止焊接缺陷产生。
3.7埋弧自动焊填充盖面
3.7.1焊接工艺参数
现场焊接工艺参数是经过多次焊接工艺评定而总结的,以下两个表格是管道规格为Φ114*8.5mm和Φ323.8*33.32mm的焊接工艺参数,以便指导焊接施工。
管道规格为Φ114*8.5mm的焊接工艺参数表
层数
道数
焊接
方法
焊材
焊接电流
电弧电压
(V)
焊接速度(cm/min)
线能量(KJ/cm)
层间温度(℃)
牌号或型号
规格
种类
极性
电流(A)
1
1
GTAW
CHG-SH/ER50-G
φ2.5
直流
正接
80~120
12~16
7~15
3.8~16.5
/
2
1
SAW
CHW-S1SH/H08SH
φ1.6
直流
反接
200~260
28~32
52~58
5.8~9.6
/
3
1
SAW
CHW-S1SH/H08SH
φ1.6
直流
反接
200~260
28~32
52~58
5.8~9.6
/
4
1
SAW
CHW-S1SH/H08SH
φ1.6
直流
反接
200~260
28~32
52~58
5.8~9.6
/
管道规格为Φ323.8*33.32mm的焊接工艺参数表
层数
道数
焊接
方法
焊材
焊接电流
电弧电压
(V)
焊接速度(cm/min)
线能量(KJ/cm)
层间温度(℃)
牌号或型号
规格
种类
极性
电流(A)
1
1
GTAW
CHG-SH/ER50-G
φ2.5
直流
正接
80~120
12~16
5~8
7.2~17
/
2
1
SAW
CHW-S1SH/H08SH
φ1.6
直流
反接
200~350
28~34
52~60
5.6~13.7
/
3
1
SAW
CHW-S1SH/H08SH
φ1.6
直流
反接
200~350
28~34
52~60
5.6~13.7
/
2
SAW
CHW-S1SH/H08SH
φ1.6
直流
反接
200~350
28~34
52~60
5.6~13.7
/
4
1
SAW
CHW-S1SH/H08SH
φ1.6
直流
反接
200~350
28~34
52~60
5.6~13.7
/
2
SAW
CHW-S1SH/H08SH
φ1.6
直流
反接
200~350
28~34
52~60
5.6~13.7
/
5
1
SAW
CHW-S1SH/H08SH
φ1.6
直流
反接
200~350
28~34
52~60
5.6~13.7
/
2
SAW
CHW-S1SH/H08SH
φ1.6
直流
反接
200~350
28~34
52~60
5.6~13.7
/
3
SAW
CHW-S1SH/H08SH
φ1.6
直流
反接
200~350
28~34
52~60
5.6~13.7
/
6
1
SAW
CHW-S1SH/H08SH
φ1.6
直流
反接
200~350
28~34
52~60
5.6~13.7
/
2
SAW
CHW-S1SH/H08SH
φ1.6
直流
反接
200~350
28~34
52~60
5.6~13.7
/
3
SAW
CHW-S1SH/H08SH
φ1.6
直流
反接
200~350
28~34
52~60
5.6~13.7
/
3.7.2焊接工艺要点
(1)有焊前预热要求的管道,填充盖面焊前应将焊缝预热到80℃以上方可焊接;
(2)埋弧焊接时调整好焊枪角度,使焊缝外观呈微凹形为宜;
(3)盖面过程中要通过微调按钮(焊接速度、频率及摆弧摆动宽度)来控制盖面焊道的余高和宽度;
(4)应有专人进行熔渣清理及道间接头打磨。
焊接过程中随时微调按钮
熔渣清理及道间接头打磨
3.8焊后热处理
对于设计文件要求焊后消应力热处理的抗硫管道,为避免无损检测不合格返修后增加热处理费用,待无损检测合格后,再进行消应力热处理。
3.8.1热处理采用电加热方法,当管道公称直径DN≤300时,每道焊缝至少放置1支测温热电偶,当管道公称直径DN>300时,每道焊缝对称放置2支测温热电偶。
3.8.2热处理加热范围为焊缝两侧各不少于焊缝宽度的3倍,且不少于25mm。
加热范围以外100mm区域内应予以保温,且管道端口应封闭。
恒温期间,各测点温度应在热处理温度规定的范围内,其温差不得大于50℃。
3.8.3严格控制升温、恒温和降温过程,升温至300℃后,加热速度按5125/t(℃/h)计算,且不大于220℃/h;恒温后的冷却速度按6500/t(℃/h)计算,且不大于260℃/h,冷至300℃后保温缓冷。
(t为管道实际壁厚)具体参数见下表。
材质
焊缝壁厚(mm)
恒温温度(℃)
恒温时间(h)
升温速度(℃/h)
降温速度(℃/h)
20#ANTIH2S
A106Gr.BANTIH2S
δ≤20
600~650
1
≤220
≤260
20<δ≤36
600~650
1.5
≤142
≤180
36<δ≤48
600~650
2
≤106
≤135
48<δ≤60
600~650
2.5
≤85
≤108
3.9硬度检测
3.9.1焊后热处理完毕后,按照每条管线对焊接接头进行20%的布氏硬度检测,焊缝及热影响区硬度值不大于母材硬度值的120%,且布氏硬度值≤200.
3.9.2当硬度值超过规定值时,应加倍检验,仍不合格时应重新进行热处理,并重新测定硬度值;
三、效益对比
1.保证焊接质量,提高焊接一次合格率
抗硫管道采用埋弧自动焊焊接,既保证了管道焊接外观质量,又提高了焊接一次合格率,其合格率达到了98%以上,有效地降低了返修率,促进了施工进度。
2.极大提高生产效率,节约人工使用率
在正常的施工条件下,按照传统的模式,每焊工采用氩电联焊作业,焊接工效为40寸D/天,最高可达60寸D/天,而采取埋弧自动焊焊接每台焊机焊接工效能达到200寸D/天,最高可达,300寸D/天。
经过对比,每天每台自动焊机的工作量相当于4-5名焊工的工作量,随着管道壁厚的增大,其工效就愈明显。
3.节约成本,提高经济效益
通过人工、设备、消耗材料的对比分析,管道焊接应用埋弧自动焊比氩电联焊每寸D节省约7~8元,管道壁厚越厚经济效益越明显。
抗硫管道共16000寸D,采用自动焊能够创造的直接经济效益为8*16000=12.8万。