焦化废水文档格式.docx
《焦化废水文档格式.docx》由会员分享,可在线阅读,更多相关《焦化废水文档格式.docx(9页珍藏版)》请在冰豆网上搜索。
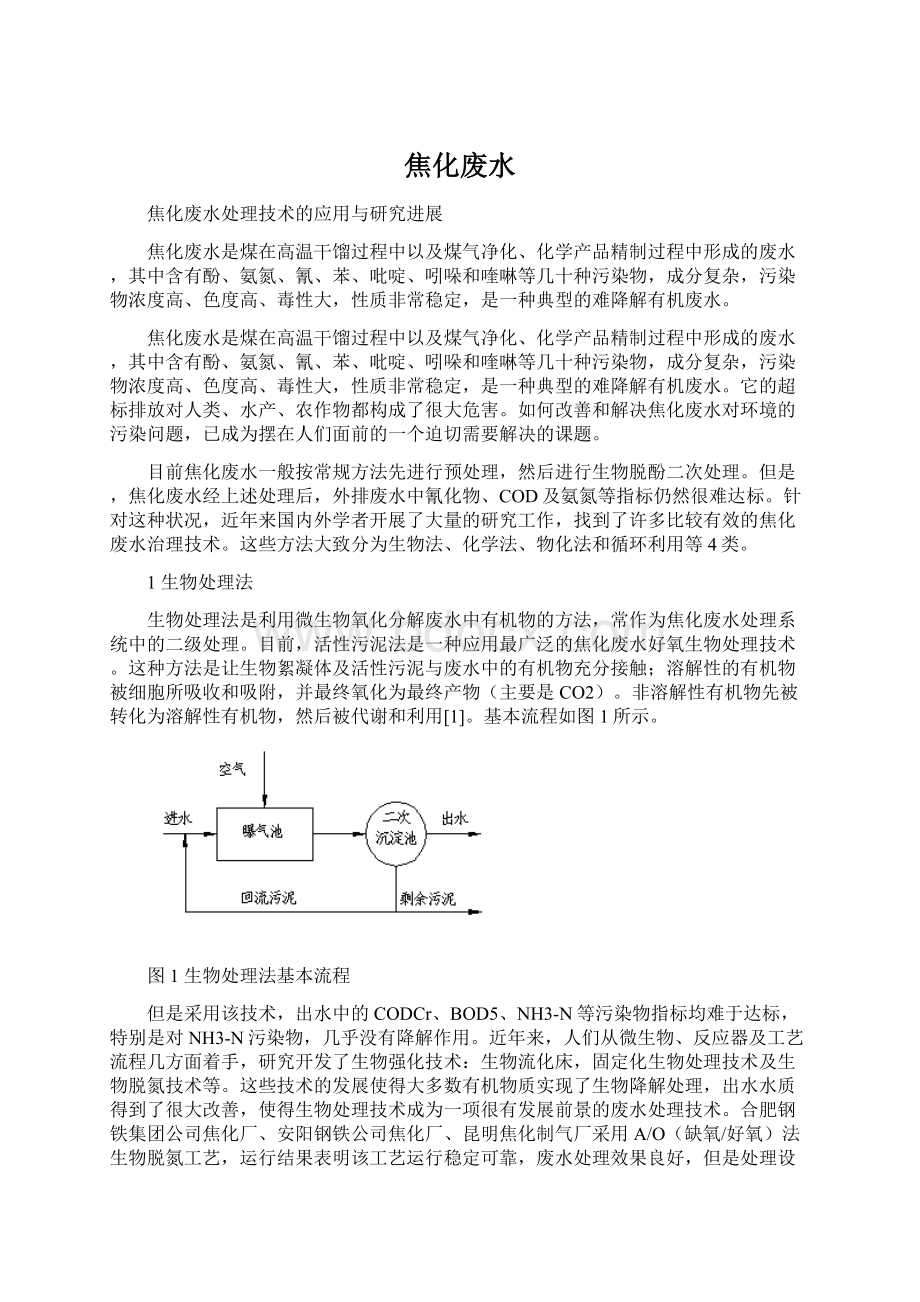
这些技术的发展使得大多数有机物质实现了生物降解处理,出水水质得到了很大改善,使得生物处理技术成为一项很有发展前景的废水处理技术。
合肥钢铁集团公司焦化厂、安阳钢铁公司焦化厂、昆明焦化制气厂采用A/O(缺氧/好氧)法生物脱氮工艺,运行结果表明该工艺运行稳定可靠,废水处理效果良好,但是处理设施规模大,投资费用高。
上海宝钢焦化厂将原有的A/O生物脱氮工艺改为A/OO工艺,污水处理效果优于A/O工艺[2],运行成本有所降低,效果明显。
总的来看,生物法具有废水处理量大、处理范围广、运行费用相对较低等优点,改进后的新技术使焦化废水处理达到了工程应用要求,从而使得该技术在国内外广泛采用。
但是生物降解法的稀释水用量大,处理设施规模大,停留时间长,投资费用较高,对废水的水质条件要求严格,废水的pH值、温度、营养、有毒物质浓度、进水有机物浓度、溶解氧量等多种因素都会影响到细菌的生长和出水水质,这也就对操作管理提出了较高要求。
2化学处理法
2.1催化湿式氧化技术
催化湿式氧化技术是在高温、高压条件下,在催化剂作用下,用空气中的氧将溶于水或在水中悬浮的有机物氧化,最终转化为无害物质N2和CO2排放。
该技术的研究始于20世纪70年代,是在Zimmerman的湿式氧化技术的基础上发展起来的。
在我国,鞍山焦耐院与中科院大连物化所合作,曾经成功地研制出双组分的高活性催化剂,对高浓度的含氨氮和有机物的焦化废水具有极佳的处理效果[3]。
湿式催化氧化法具有适用范围广、氧化速度快、处理效率高、二次污染低、可回收能量和有用物料等优点。
但是,由于其催化剂价格昂贵,处理成本高,且在高温高压条件下运行,对工艺设备要求严格,投资费用高,国内很少将该法用于废水处理。
2.2焚烧法
焚烧法治理废水始于20世纪50年代。
该法是将废水呈雾状喷入高温燃烧炉中,使水雾完全汽化,让废水中的有机物在炉内氧化,分解成为完全燃烧产物CO2和H2O及少许无机物灰分。
焦化废水中含有大量NH3-N物质,NH3在燃烧中有NO生成,NO的生成会不会造成二次污染是采用焚烧法处理焦化废水的一个敏感问题。
杨元林[4]等通过研究发现,NH3在非催化氧化条件下主要生成物是N2,不会产生高浓度NO造成二次污染。
从而说明,焚烧处理工艺对于处理焦化厂高浓度废水是一种切实可行的处理方法。
然而,尽管焚烧法处理效率高,不造成二次污染,但是其昂贵的处理费用(约为167美元/t[5])使得多数企业望而却步,在我国应用较少。
2.3臭氧氧化法
臭氧是一种强氧化剂,能与废水中大多数有机物,微生物迅速反应,可除去废水中的酚、氰等污染物,并降低其COD、BOD值,同时还可起到脱色、除臭、杀菌的作用。
臭氧的强氧化性可将废水中的污染物快速、有效地除去,而且臭氧在水中很快分解为氧,不会造成二次污染,操作管理简单方便。
但是,这种方法也存在投资高、电耗大、处理成本高的缺点。
同时若操作不当,臭氧会对周围生物造成危害。
因此,目前臭氧氧化法还主要应用于废水的深度处理。
在美国已开始应用臭氧氧化法处理焦化废水[6]。
2.4等离子体处理技术
等离子体技术是利用高压毫微秒脉冲放电所产生的高能电子(5~20eV)、紫外线等多效应综合作用,降解废水中的有机物质。
等离子体处理技术是一种高效、低能耗、使用范围广、处理量大的新型环保技术,目前还处于研究阶段。
有研究表明[7],经等离子体处理的焦化废水,有机物大分子被破坏成小分子,可生物降解性大大提高,再经活性污泥法处理,出水的酚、氰、COD指标均有大幅下降,具有发展前景。
但处理装置费用较高,有待于进一步研究开发廉价的处理装置。
2.5光催化氧化法
光催化氧化法是由光能引起电子和空隙之间的反应,产生具有较强反应活性的电子(空穴对),这些电子(空穴对)迁移到颗粒表面,便可以参与和加速氧化还原反应的进行。
光催化氧化法对水中酚类物质及其他有机物都有较高的去除率[8]。
高华等[9]在焦化废水中加入催化剂粉末,在紫外光照射下鼓入空气,能将焦化废水中的所有有机毒物和颜色有效去除。
在最佳光催化条件下,控制废水流量为3600mL/h,就可以使出水COD值由472mg/L降至100mg/L以下,且检测不出多环芳烃。
目前,这种方法还仅停留在理论研究阶段。
这种水处理方法能有效地去除废水中的污染物且能耗低,有着很大的发展潜力。
但是有时也会产生一些有害的光化学产物,造成二次污染。
由于光催化降解是基于体系对光能的吸收,因此,要求体系具有良好的透光性。
所以,该方法适用于低浊度、透光性好的体系,可用于焦化废水的深度处理。
2.6电化学氧化技术
电化学水处理技术的基本原理是使污染物在电极上发生直接电化学反应或利用电极表面产生的强氧化性活性物质使污染物发生氧化还原转变。
目前的研究表明,电化学氧化法氧化能力强、工艺简单、不产生二次污染,是一种前景比较广阔的废水处理技术。
Chang等[10]用PbO2/Ti作为电极降解焦化废水。
结果表明:
电解2h后,COD值从2143mg/L降到226mg/L,同时760mg/L的NH3-N也被去除。
研究还发现,电极材料、氯化物浓度、电流密度、pH值对COD的去除率和电化学反应过程中的电流效率都有显著影响。
梁镇海等[11]采用Ti/SnO2+Sb2O3+MnO2/PbO2处理焦化废水,使酚的去除率达到95.8%,其电催化性能比Pb电极优良,比Pb电极可节省电能33%。
2.7化学混凝和絮凝
化学混凝和絮凝是用来处理废水中自然沉淀法难以沉淀去除的细小悬浮物及胶体微粒,以降低废水的浊度和色度,但对可溶性有机物无效,常用于焦化废水的深度处理。
该法处理费用低,既可以间歇使用也可以连续使用。
混凝法的关键在于混凝剂。
目前一般采用聚合硫酸铁作混凝剂,对CODCr的去除效果较好,但对色度、F-的去除效果较差。
浙江大学环境研究所卢建航等[12]针对上海宝钢集团的焦化废水,开发了一种专用混凝剂。
实验结果发现:
混凝剂最佳有效投加量为300mg/L,最佳混凝pH范围为6.0~6.5;
混凝剂对焦化废水中的CODCr、F-、色度及总CN都有很高的去除率,去除效果受水质波动的影响较小,混凝pH对各指标的去除效果有较大的影响。
絮凝剂在废水中与有机胶质微粒进行迅速的混凝、吸附与附聚,可以使焦化废水深度处理取得更好的效果[13]。
马应歌等[14]在相同条件下用3种常用的聚硅酸盐类絮凝剂(PASS,PZSS,PFSC)和高铁酸钠(Na2FeO4)处理焦化废水,实验结果表明,高铁酸钠具有优异的脱色功能,优良的COD去除、浊度脱除性能,形成的絮凝体颗粒小、数量少、沉降速度快、且不形成二次污染。
3物理化学法
3.1吸附法
吸附法就是采用吸附剂除去污染物的方法。
活性炭具有良好的吸附性能和稳定的化学性质,是最常用的一种吸附剂。
活性炭吸附法适用于废水的深度处理。
但是,由于活性炭再生系统操作难度大,装置运行费用高,在焦化废水处理中未得到推广使用。
上海宝钢曾于1981年从日本引进了焦化酚氰废水三级处理工艺,但在二期工程中没有再建第三级活性炭吸附装置,以上所述就是原因之一[2]。
山西焦化集团有限公司利用锅炉粉煤灰处理来自生化的焦化废水。
生化出口废水经过粉煤灰吸附处理后,污染物的平均去除率为54.7%。
处理后的出水,除氨氮外,其它污染物指标均达到国家一级焦化新厂标准,和A/O法相近,但投资费用仅为A/O法的一半[15]。
该方法系统投资费、运行费都比较低,以废治废,具有良好的经济效益和和环境效益。
但是,同时存在处理后的出水氨氮未能达标和废渣难处理的缺点。
刘俊峰等[16]采用高温炉渣过滤,再用南开牌H-103大孔树脂吸附处理含酚520mg/L、COD3200mg/L的焦化废水,处理出水酚含量≤0.5mg/L,COD≤80mg/L,达到国家排放标准。
黄念东等[17]研究了细粒焦渣对焦化废水的净化作用。
他们对颗粒大小、pH、溶液滤速等各种因素对吸附能力的影响因素作了考察,结果显示,含酚30mg/L的液体,在流速为4.5mL/min,pH为2~2.5,温度25℃的条件下,酚的去除率为98%。
3.2利用烟道气处理焦化废水
由冶金工业部建筑研究总院和北京国纬达环保公司合作研制开发的“烟道气处理焦化剩余氨水或全部焦化废水的方法”已获得国家专利。
该技术将焦化剩余氨水去除焦油和SS后,输入烟道废气中进行充分的物理化学反应,烟道气的热量使剩余氨水中的水分全部汽化,氨气与烟道气中的SO2反应生成硫铵[18]。
这项专利技术已在江苏淮钢集团焦化剩余氨水处理工程中获得成功应用。
监测结果表明,焦化剩余氨水全部被处理,实现了废水的零排放,又确保了烟道气达标排放,排入大气中的氨、酚类、氰化物等主要污染物占剩余氨水中污染物总量的1.0%~4.7%[19]。
该方法以废治废,投资省,占地少,运行费用低,处理效果好,环境效益十分显著,是一项十分值得推广的方法。
但是此法要求焦化的氨量必须与烟道气所需氨量保持平衡,这就在一定程度上限制了方法的应用范围。
4废水循环利用
将高浓度的焦化废水脱酚,净化除去固体沉淀和轻质焦油后,送往焦炉熄焦,实现酚水闭路循环。
从而减少了排污,降低了运行等费用[20]。
但是此时的污染物转移问题也值得考虑。
5结论
焦化废水治理技术能否成功应用,主要受3个因素制约:
处理效果、投资运行费用以及是否会造成二次污染。
目前的各种治理技术还不能完全满足这三方面的要求。
它们各有优缺点,这就需要因地制宜地选择适合自身特点的技术方法,以及对现有方法的有机结合来取得比较满意的效果。
同时,还要进一步研究开发处理效果更好、投资运行费用更低、无二次污染、易于操作管理的新技术,这样才能更加适合国情,才会有更广阔的发展前景。
焦化废水深度处理及回用技术方案探讨
1引言
近年来,全球经济与中国经济的持续发展形成了对钢铁等基础产业的拉动,中国2008年焦炭产量为32,757万吨,占世界总产量的50%以上。
焦化废水是在煤高温干馏、煤气净化和化工产品精制过程中产生的废水,由于焦化废水中氨氮、酚类及油分浓度高,有毒及生物抑制性物质较多,生化处理难以实现有机污染物的完全降解,对环境造成了严重污染,因此焦化废水是一种典型的高浓度、高污染、有毒、难降解的工业有机废水。
工信部于2008年12月19日下发的15号文《焦化行业准入条件(2008年修订)》中明确规定:
酚氰废水处理合格后要循环使用,不得外排。
因此对焦化污水不再是单纯追求达标排放,还要考虑处理后如何回用的问题。
2008-2009年,笔者对国内焦化废水处理与利用情况进行了调研,实地考察了多家焦化废水处理与利用项目,对国内焦化废水深度处理技术的应用状况、废水回用现状及存在的问题有了较为深入的了解。
本文在总结了国内相关研究成果的基础上,结合调研中发现的问题,对焦化废水回用技术提出了改进建议及方案。
2焦化废水深度处理技术研究及应用现状
近年来,我国的环保工作者对焦化废水处理做了大量的工作,将传统的水处理技术针对焦化废水进行了适应性改造及组合,最大限度地发挥了生化、高级氧化等技术的效能,取得了一定成绩。
目前,对焦化废水的深度处理技术主要包括:
混凝沉淀法、吸附法、高级氧化技术(Fenton氧化、O3氧化、催化湿式氧化等)以及反渗透技术。
2.1混凝沉淀法
传统焦化废水的深度处理选用的混凝剂有聚合氯化铝、聚合硫酸铁等,卢建杭[1]开发出宝钢焦化废水专用混凝剂M180,处理宝钢生化处理后的污水,出水COD在40~70mg/L,F-浓度为3.0~6.0mg/L,色度为50~100倍,总CN-在0.3~0.5mg/L左右,各指标的平均去除率COD约为70%、F-约为85%、色度约为95%、总CN-约为85%。
2.2吸附法
吸附法是利用多孔性吸附剂吸附废水中的一种或几种溶质,使废水得到净化。
通常采用的吸附剂有粉煤灰、熄焦粉、活性炭、树脂等。
蒋文新[2]等采用混凝沉淀、活性炭吸附以及混凝沉淀+活性炭吸附工艺对焦化厂生化出水进行深度处理,单独混凝沉淀或活性炭吸附均可以将水样中COD浓度降到100mg/L以下,达到国家污水一级排放标准和冷却用水建议标准;
对于焦化厂生化出水,煤质炭Ⅰ和果壳炭均表现出良好的吸附效果,并使出水COD<
100mg/L,但处理成本较高,当COD从147mg/L降至100mg/L,采用煤质炭Ⅰ的成本为1.2元/m3。
2.3高级氧化技术
(1)Fenton氧化法
Fenton试剂法是以过氧化氢为氧化剂、以亚铁盐为催化剂的均相催化氧化法。
Fenton试剂是一种强氧化剂,反应中产生的?
OH是一种氧化能力很强的自由基,能氧化废水中有机物,从而降低废水的色度和COD值。
许海燕等人[3]在生化处理后的焦化废水中加入Fenton试剂,之后又加入絮凝剂FeCl3和助凝剂PAM,过滤除去废渣,处理后水样中的COD从223.9mg/L降至43.2mg/L。
(2)臭氧氧化
刘金泉[4]等人分别用O3、H2O2/O3及UV/O3对焦化生化出水进行深度处理,接触时间40min,溶液pH8.15,反应温度25℃,在此条件下废水COD及UV254的去除率最高可达47.14%和73.47%,COD可降至67mg/L。
臭氧是一种高效干净的氧化剂,但臭氧发生器耗电量大,运行及投资费用高,在自来水厂做为消毒设施使用较多,但在工业废水处理中应用较少。
(3)电化学氧化技术
电化学氧化处理技术的基本原理是使污染物在电极上发生直接电化学反应或利用电极表面产生的强氧化性活性物质使污染物发生氧化还原转变。
李玉明等人[5]采用三维电极固定床技术对焦化废水进行深度处理的实验研究,研究结果表明,在槽电压为12V,液体催化剂量为1500mg/L、反应时间为60min、pH为3的条件下,COD去除率可达62%。
在三维电极电解体系中以及在酸性和碱性条件下,都能产生活性中间体H2O2,但是在碱性条件下,Fe2+很快便生成絮体,影响了其进一步与H2O2生成Fenton试剂的反应,导致随着pH的增大,COD去除率呈现逐渐降低的趋势。
总体来说,该方法仍处于探索阶段。
同时可以查看中国污水处理工程网更多技术文档。
(4)光催化氧化法
光催化氧化法是由光能引起电子和空隙之间的反应,产生具有较强反应活性的电子(空穴对),这些电子(空穴对)迁移到颗粒表面,便可以参与和加速氧化还原反应的进行。
光催化氧化法对水中酚类物质及其他有机物都有较高的去除率,且能耗低,有着很大的发展潜力。
2.4反渗透技术
反渗透是一种以压力为推动力的膜分离过程。
用水泵给含盐水溶液或废水施加压力,以克服自然渗透压及膜的阻力,使水透过反渗透膜,将水中溶解盐和污染杂质阻止在反渗透膜的另一侧。
周红等人[6]采用MBR+RO的工艺对焦化废水生化出水进行了深度处理,结果显示产水COD<10mg/L,脱盐率达到90%以上。
反渗透技术只是对废水中的污染物进行了浓缩,对污染物并没有分解去除的作用,产生的浓水通常得不到妥善的解决,而且使用中由于进水的水质不同,膜极易受到污染,因此在工业废水处理中应当谨慎使用[7]。
3焦化废水回用中存在的问题及改进建议
随着国家节能减排政策的提出,国内焦化厂对焦化废水的回用进行了很多探索和尝试。
主要回用方式包括湿熄焦、高炉冲渣、煤场抑尘用水、烧结混料用水,也有厂家用反渗透技术将焦化废水处理后回用作为工业给水。
表1是国内焦化废水回用的一些基本情况。
3.1一级达标废水的回用
(1)二次污染
采用湿法熄焦的焦化厂将生化处理后的废水用于熄焦处理,由于国内焦化厂生化处理后出水的COD、氨氮含量仍然较高,回用于湿熄焦、高炉冲渣时必然会使废水中的氨氮及部分有机物散发到空气中,感官刺激强烈,形成较大的二次污染;
一些钢厂对焦化废水引入烧结混料工段也做了一些尝试,污染物在之后的高温加工工段可以得到部分炭化分解,减少了二次污染。
运行中反馈的主要问题是焦化废水的气味使得工作环境变差,同时废水的含油量不稳定对添加水喷头有影响。
太原钢铁厂将传统A/O系统改造强化后出水达到一级排放标准,部分废水回用于高炉冲渣,现场基本闻不到刺激气味。
因此,降低废水COD及氨氮浓度会大大改善回用中对操作环境的不良影响。
有焦化废水需要处理的单位,也可以到污水宝项目服务平台咨询具备类似污水处理经验的企业。
正常情况下,焦化厂的二级生化处理通常可将氨氮浓度控制在10~20mg/L,但COD通常在200~400mg/L,通过投加聚合硫酸铁、Fenton试剂可将COD控制在100mg/L以下,投加药剂的主要缺点是使废水中的无机物增多,对腐蚀控制不利。
建议将投药与吸附法联合使用,以降低水质的二次污染。
(2)设备及管道腐蚀
焦化废水具有较强的腐蚀性。
从调研实测的相关资料中可以看出(见表2、表3),废水中的氯离子、氟化物、氨氮以及硫酸根离子浓度较高,对金属腐蚀性较强。
因此,焦化废水的腐蚀问题必须得到妥善解决。
张建磊等[8]对焦化废水回用于转炉煤气洗涤水系统的缓蚀阻垢进行了研究,经恰当处理后,循环水浊度可降至60NTU以下,阻垢率和缓蚀率可分别达到99%和95.6%,腐蚀率小于0.078mm/a,可满足系统稳定运行的要求。
但是,运行费用通常较高。
当作为烧结混料添加水时,投加缓蚀阻垢剂并不经济,因此可以采用混合部分其它循环水系统排污水(含缓蚀阻垢剂)的方式降低其腐蚀性。
3.2工业给水回用
单纯生产焦炭的企业没有联合型钢企所具有的消纳途径,因此很多焦化厂不得不采用反渗透技术将焦化废水进行浓缩,产品水水质较好,可以直接作为工业循环冷却水的补水,产生的浓水则作为抑尘水或伴煤燃烧。
图1是两种典型的反渗透处理工艺。
膜厂家针对工业废水开发了耐污染的反渗透膜,但是在实际工程中为保障膜系统安全,通常还是将进入反渗透系统的废水COD浓度控制在20~50mg/L,而以上两种方案进入反渗透系统的COD均在250mg/L左右,因此,膜系统稳定运行的关键是预处理的稳定有效。
絮凝沉淀、Fenton试剂等方法会在废水中引入大量铁离子及硫酸根离子,从而加重膜系统污染及结垢,因此不宜大量使用,但完全采用高级氧化的投资及成本太高,因此建议先使用混凝沉淀等方法将废水COD控制在100~150mg/L,然后再使用高级氧化技术(臭氧氧化、电化学氧化、湿式催化氧化)以及活性炭吸附的方法对进入膜系统的废水进行深度处理。
根据前面的介绍,电化学氧化、催化氧化技术的工业化应用较少,基本都停留在试验研究阶段。
大型臭氧设备在自来水厂作为消毒技术的应用较多,作为氧化技术在工程上的应用则较少,但是与其它高级氧化技术相比,设备相对成熟,国产化程度也较高,因此工程化的优势相对较大。
改进的焦化废水深度处理工艺。
处理后的焦化废水回用前提条件必须是满足达标,然后再根据回用水要求,考虑是否采用其他处理工艺。
对于回用水的指标,钢铁联合企业的焦化厂、煤焦联合企业、独立焦化厂是有区别的,而采用湿法熄焦或干法熄焦的焦化厂也是有区别的。
要实现焦化废水的零排放,需根据企业性质,对不同的回用用户采用相应的处理工艺,使处理后焦化废水资源得到最大限度地合理利用。
①钢铁联合企业,处理后焦化废水除了回用于焦化厂外,还可以用于钢铁企业浊循环水系统中。
这样废水处理就可以达到GBl3456-92《钢铁工业污染物排放标准》中的一级标准。
②煤焦联合企业,处理后焦化废水除了可用于焦化厂外,还可送往洗煤厂,用作洗煤补充水,同样需要达到GB8978-1996《污水综合排放标准》中的一级标准。
③独立焦化厂,如果采用湿法熄焦下艺,处理后焦化废水应该达到GB8978-1996《污水综合排放标准》中的一级标准,如果不允许外排,必须控制进废水处理站的稀释水量,并以熄焦水量来控制稀释水量。
④独立焦化厂,如果采用干法熄焦工艺,同时环保部门又不允许外排的,即使不考虑其他水量,仅蒸氨废水一项靠焦化厂本身是消耗不掉的。
必须采用深度处理工艺,同时尽量减少废水处理的稀释水用量,使深度处理的产水用于生产净循环水补充水;
少量的浓缩液可以喷洒到煤场或作为泡沫除尘的补充水。
⑤要求零排放的,仅靠焦化厂本身是消耗不掉处理后的焦化废水,必须采用深度处理工艺,使深度处理的产水用于生产净循环水补充水。
⑥部分地方环保部门要求更加严格,主要控制指标CODcr≤50mg/L。
也不能保证处理后水回用为工业用水。
GB/T19923-2005《城市污水再生利用一工业用水水质》中要求用于敞开式循环水系统补充水的CODcr≤60mg/L,溶解性总固体≤1000mg/Lo就现今处理技术而言,如果不采用膜分离技术,很难保证CODcr≤50mx/L,更不能保证对溶解性固体的去除率。
假如没有采用膜分离技术,即使主要控制指标CODcr≤50mg/L,必须增加除盐功能,方可回用,否则半途而废,得不偿失