完整版年产5000吨H62黄铜棒挤压车间设计实现可行性计划方案.docx
《完整版年产5000吨H62黄铜棒挤压车间设计实现可行性计划方案.docx》由会员分享,可在线阅读,更多相关《完整版年产5000吨H62黄铜棒挤压车间设计实现可行性计划方案.docx(47页珍藏版)》请在冰豆网上搜索。
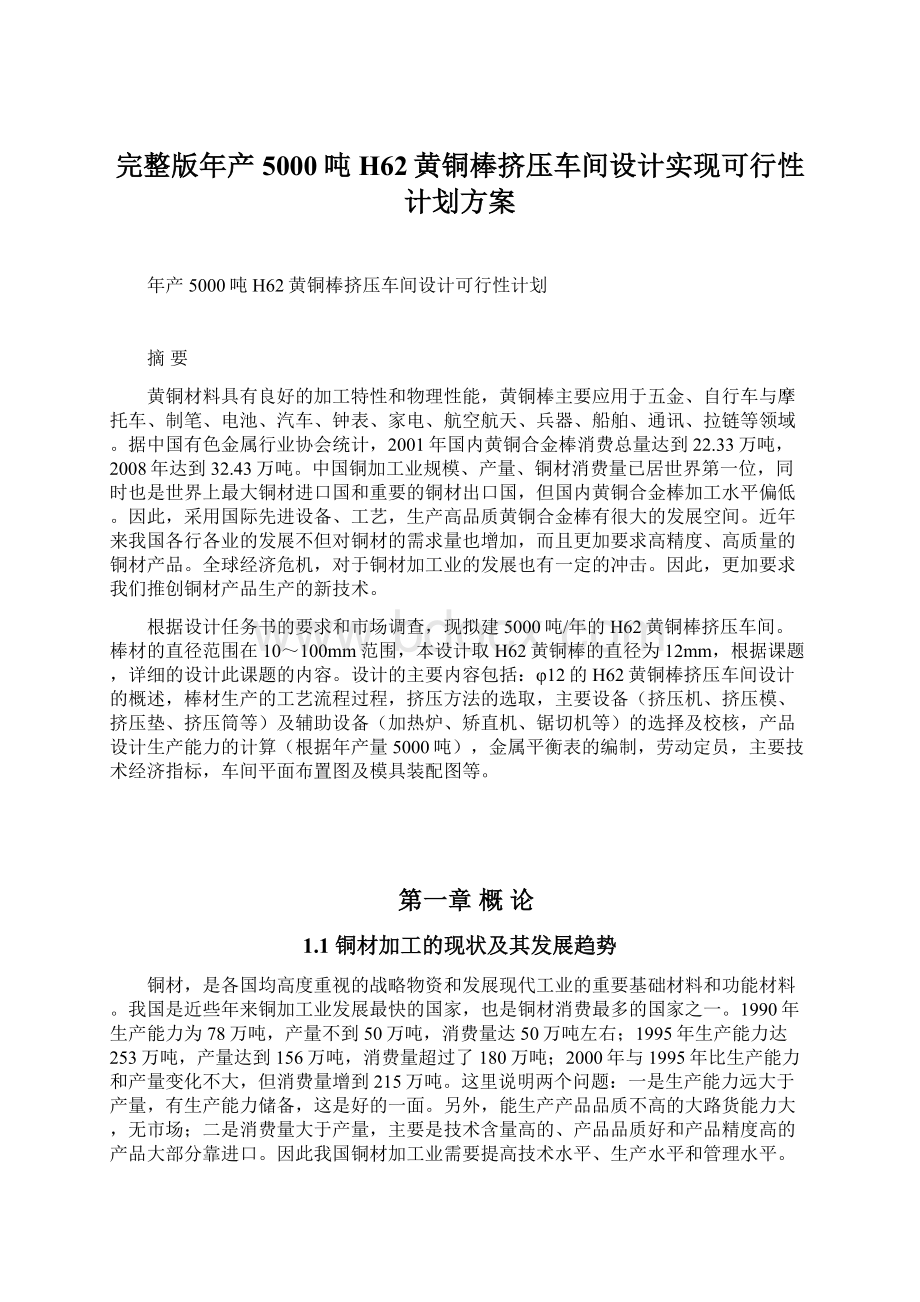
完整版年产5000吨H62黄铜棒挤压车间设计实现可行性计划方案
年产5000吨H62黄铜棒挤压车间设计可行性计划
摘要
黄铜材料具有良好的加工特性和物理性能,黄铜棒主要应用于五金、自行车与摩托车、制笔、电池、汽车、钟表、家电、航空航天、兵器、船舶、通讯、拉链等领域。
据中国有色金属行业协会统计,2001年国内黄铜合金棒消费总量达到22.33万吨,2008年达到32.43万吨。
中国铜加工业规模、产量、铜材消费量已居世界第一位,同时也是世界上最大铜材进口国和重要的铜材出口国,但国内黄铜合金棒加工水平偏低。
因此,采用国际先进设备、工艺,生产高品质黄铜合金棒有很大的发展空间。
近年来我国各行各业的发展不但对铜材的需求量也增加,而且更加要求高精度、高质量的铜材产品。
全球经济危机,对于铜材加工业的发展也有一定的冲击。
因此,更加要求我们推创铜材产品生产的新技术。
根据设计任务书的要求和市场调查,现拟建5000吨/年的H62黄铜棒挤压车间。
棒材的直径范围在10~100mm范围,本设计取H62黄铜棒的直径为12mm,根据课题,详细的设计此课题的内容。
设计的主要内容包括:
φ12的H62黄铜棒挤压车间设计的概述,棒材生产的工艺流程过程,挤压方法的选取,主要设备(挤压机、挤压模、挤压垫、挤压筒等)及辅助设备(加热炉、矫直机、锯切机等)的选择及校核,产品设计生产能力的计算(根据年产量5000吨),金属平衡表的编制,劳动定员,主要技术经济指标,车间平面布置图及模具装配图等。
第一章概论
1.1铜材加工的现状及其发展趋势
铜材,是各国均高度重视的战略物资和发展现代工业的重要基础材料和功能材料。
我国是近些年来铜加工业发展最快的国家,也是铜材消费最多的国家之一。
1990年生产能力为78万吨,产量不到50万吨,消费量达50万吨左右;1995年生产能力达253万吨,产量达到156万吨,消费量超过了180万吨;2000年与1995年比生产能力和产量变化不大,但消费量增到215万吨。
这里说明两个问题:
一是生产能力远大于产量,有生产能力储备,这是好的一面。
另外,能生产产品品质不高的大路货能力大,无市场;二是消费量大于产量,主要是技术含量高的、产品品质好和产品精度高的产品大部分靠进口。
因此我国铜材加工业需要提高技术水平、生产水平和管理水平。
我国铜加工先进与落后并存,传统经典的生产技术仍然占据主导地位,其加工工艺仍然是:
合金熔炼—半连续铸造—热加工—冷加工,因此工艺流程长、能耗高、成品率低、环保条件差、迫切需要技术和装备创新。
中国经济稳定增长为铜材加工业提供了宽广的内需市场,这在全球范围内也是唯一的。
各行各业对铜加工材,特别是高、精、尖的铜加工材的需求量猛增,加之我国加入WTO,给我国铜加工企业带来了机遇和挑战,这就要求我们要大力改进技术,提高生产技术水平,提高产品品质。
高度重视技术创新、发展以短流程、节流、环保、高效的生产技术,建设连续化、自动化、专业化生产线;重要产业创新技术:
潜流式铸造、连续挤压、管材行星轧制等。
加强信息标准等研发工作,为铜加工业发展服务。
新增板带工程中,铜陵、江西、大冶、紫金矿业等均为我国重要的矿产铜产地,约32万吨板带产能。
这是铜原料企业向下游延伸产业链的重要部署,对节约运输成本,综合利用资源意义重大,将长远造福我国铜加工业。
对于铜合金棒材来说,均以潜流式、多线水平连铸棒坯为开坯手段,然后配合连续拉拔生产机列。
这种方法在宁波金田已经产业化,具有产量大、生产成品率高、环保、设备投资少等明显优点。
充分发挥挤压开辟能力,生产合金棒坯料,然后采用冷拉伸办法产出成品,这是现代企业挖潜改造的方向。
在发展铜及合金棒型线生产中,上引铜杆—连续挤压—高精拉伸法,因其投资少、高效、连续化、节能、环保、高成品率而倍受重视。
1.2挤压法的优缺点
1.2.1优点
(1)挤压时金属在挤压筒内受到比轧制、锻造更强烈的三向压应力的作用。
因此它能充分发挥金属的塑性;实现挤压比达10以上的大变形。
可以挤压轧制或锻造难以加工的塑性低的金属;
(2)只要改换挤压模或挤压针,就可以用一台挤压机生产不同品种、不同尺寸规格的制品,操作方便,生产灵活;
(3)挤压制品表面质量好,尺寸精度高。
1.2.2缺点
(1)挤压机结构复杂,投资费用大;
(2)挤压残料比较多,要占锭坯的10%~15%,挤压大直径棒材时,成品率较低;
(3)正挤压时金属与挤压工具表面的摩擦力大,金属不均匀变形严重,使挤压制品产生缩尾,内部组织与性能不均,使切头、切尾几何损失增加;
(4)挤压工具在高温、高压条件下工作,工具消耗大,增加制品生产成本。
1.3挤压工艺的现状及其发展趋势
挤压法在金属塑性加工领域中出现的比较晚,是一种新的金属加工工艺。
据文献记载,大约在1797年英国人J.Bramah首先发明了一种挤压铅管的装置,继而将此原理应用到电缆包铅上面。
因为当时尚不能解决挤压时所需要的巨大而持续的压力,所以只能挤压低熔点软金属。
直到1894年,由德国人A.Dick设计和制造了第一台可以用来挤压黄铜的挤压机。
自此之后,挤压生产日益发展,二战结束后,由于航空、火箭、宇宙航行技术,以及汽车、船舶、铁路运输等各部门的发展,促进了挤压生产的急剧发展。
挤压机的台数和能力不断地增加,挤压生产线的自动化程度不断提高,新的挤压技术不断出现,理论研究有突破性的进展。
近年来计算机的普及对挤压模具的优化设计创造了条件,并且能够实现更加复杂的断面型材。
应用CAD/CAE/CAM技术可使挤压工艺生产的设计从费时、费钱的传统设计提高到准确、快速、高精度的现代化水平。
挤压工艺生产的发展方向是:
减少劳动力和材料消耗,主要体现在尽量缩短更换产品的时间,尽可能在生产过程中更换及自动更换;在挤压生产线控制系统中不断应用感测技术、控制技术和人工智能技术,使制品的质量和生产的稳定性得到进一步的提高。
1.4本设计的内容
本设计的产品生产方案——生产年产量为5000吨H62黄铜棒挤压的车间设计。
1.5本设计的目的和意义
1、通过毕业设计,可以使我们对大学四年所学的知识融会贯通,可以提高我们全面思考的能力,并且使专业课的部分内容得到深化巩固。
2、在设计的过程中通过参观生产现场,可以更直观的了解生产工艺流程及生产设备。
3、还能够培养我们检索文献设计与计算方案制订,编写论文,全面系统地进行一次有关工程设计的基本训练。
从而培养学生的工程设计能力。
4、通过毕业设计,培养同学理论联系实际,严谨求实的科学态度,培养和提高学生独立分析问题的能力,检验学生三年所学课程的掌握和综合运用程度,并以此作为评定学生毕业成绩的主要依据之一。
第二章H62黄铜棒挤压车间的工艺设计
2.1挤压生产工艺
最佳的挤压工艺应包括:
1)正确选择挤压方法及挤压设备;
2)正确确定挤压工艺参数;
3)选择优良的润滑条件;
4)确定合理的锭坯尺寸;
5)采用最佳的挤压模设计方法等。
2.1.1.挤压生产工艺流程图
各种挤压制品的生产流程基本相同。
但是,因制品的种类、合金牌号及对制品质量要求等的情况不同,可采用不同结构的挤压机和不同的挤压方法。
下图为管、棒材挤压生产工艺流程图。
如图2-1:
图2-1棒材挤压生产工艺流程图
2.1.2挤压方法与挤压设备的选择
一、挤压方法
挤压不同金属及其合金的管,棒,型,线材时,可以选择不同的挤压方法
选择时可以考虑以下几个方面:
1)在选定的挤压机上实现所需的工艺的可能性;
2)挤压条件下被挤压金属材料的高温塑性;
3)挤压过程中能否满足产品质量要求。
(1)根据被挤压金属材料的不同特性,可以采用不同挤压方法。
1)脱皮挤压用于挤压因金属流动不均匀而生成挤压缩尾的铜合金棒材,如黄铜和铝青铜。
2)静液挤压用于挤压低塑性金属材料,复合金属制品,粉末材料成型,以及断面形状复杂的制品。
3)等温挤压用于挤压热塑性较差的合金材料如硬铝合金,和挤压后立即淬火,要求沿长度上性能均一的合金材料,如LD31锻铝合金等。
4)包套挤压用于挤压表面摩擦强烈。
易氧化或易受大气污染的金属材料,如钛及其合金,铌,铍,锆,铀和钍等金属材料;对一些高脆性的金属材料或热脆性的金属材料,亦可以使用包套挤压法防止过程中产生裂纹。
5)焊接挤压用于挤压焊接性能良好的,断面形状复杂空心型材或圆形,方形管材的合金材料,如铝,镁,钛及其合金。
6)液体挤压用于挤压低熔点金属材料,如铝及其合金。
(2)挤压对流动不均匀性敏感的材料,如铅及其合金。
1)润滑挤压与金属接触的工具如挤压筒,挤压模与穿孔针的表面上,涂以润滑剂以改善表面摩擦条件,减少缩尾与压余长度。
2)反向挤压挤压筒内不存在正向挤压所特有的锭,筒间相对运动,无摩擦阻力,使流动较为均匀。
3)有效摩擦挤压挤压筒相对锭坯移向挤压模的速度快。
筒壁对锭坯作用的摩擦力为促进外层金属流动的动力,致使筒内金属外层流动较之内层快。
4)静液挤压锭坯与筒壁不接触,其间存在高压工作介质,摩擦很小。
由于筒内的高压,部分工作介质进入模孔,形成模孔内壁上的流体动力润滑,摩擦小,金属流动均匀。
5)多模孔挤压对称排列的型材模孔,使挤压时的金属流动较为均匀,制品质量易有所提高。
铜合金中硬的如铍青铜、锌白铜系合金等通常都用润滑挤压,其它合金大多采用无润滑脱皮挤压,根据本设计的内容,因此选择挤压方法是带润滑脱皮挤压。
二、挤压设备
铜及铜合金管棒材型材的挤压设备主要包括:
挤压机、锭坯加热炉、锭坯加热后的运输与供锭机构、挤压制品的受料台和水封挤压用的冷却水槽、以及制品的锯切、矫直等精整设备。
挤压机的选择
(1)单动挤压机与双动挤压机
单动挤压机无独立穿孔系统,适于挤压实心的型材与棒材;使用空心锭与随动针,或使用实心锭与组合模,亦可挤压管材与空心型材。
双动式挤压机具有独立穿孔系统,一般用于挤压管材;更换实心的挤压挤压杆与挤压垫亦可挤压型材和棒材。
(2)正向挤压机和反向挤压机
正向挤压机已使用于所有挤压过程挤压各种制品。
在挤压条件相同时,反向挤压机相对于正向挤压机可节能20~40%,制品质量和生产率均较高。
但是,由于制品规格受工具强度限制,对锭坯表面质量要求较高,操作交复杂,国内外使用反向挤压机尚不如正想挤压机广泛。
(3)卧式挤压机与立式挤压机
卧式挤压机的操作,监测和维修均较方便,普片使用于所有规格,各种合金制品的挤压。
但是卧式挤压机容易失调。
长期使用过程中的磨损,变形,各种零部件的热膨胀,可导致主要挤压工具,如挤压杆,穿孔针,挤压筒,模座不对中,使管材壁厚不均或型材挤压时流动不均匀。
根据上述挤压机的类型简介,在此次设计中可以选择卧式挤压机。
2.1.3挤压时的润滑
(1)挤压时的润滑作用
一次变形量很大,金属与工具接触面上的单位正压力极高,这是挤压所具有的特殊变形条件。
在此条件下,变形金属的表面更新作用加剧,从而使金属粘结工具的现象严重。
因此,挤压时润滑剂的作用是尽可能的使表面干摩擦转变为边界摩擦。
这不仅提高了制品表面质量和工具的使用寿命,而且由于降低了工具对金属的冷却作用,使金属流动不均匀性减少,挤压能耗降低。
(2)常用的润滑剂
在高温高压的热挤压条件下,要求润滑剂具有足够的粘度与活性,具有较高的闪点和较少的灰分,以保证良好的表面润滑状态。
同时,还要求润滑剂具有一定的化学稳定性,对金属与工具无腐蚀作用,无污染环境,有害于人体健康的作用。
1)铝及铝合金
对铝和铝合金,多采用在粘性矿物油中添加各种固体填料的悬浮状润滑剂。
2)铜及铜合金
大多数铜和铜合金管棒材的挤压,可采用45号机油和20%30%鳞片状石墨调制成的润滑剂;
3)高温高强合金
挤压高温高强合金如铜镍合金、镍、钛及钢时,石墨润滑剂有可能使钢材表面