煤制烯烃项目投资可行性研究报告年副产硫磺27072吨Word下载.docx
《煤制烯烃项目投资可行性研究报告年副产硫磺27072吨Word下载.docx》由会员分享,可在线阅读,更多相关《煤制烯烃项目投资可行性研究报告年副产硫磺27072吨Word下载.docx(68页珍藏版)》请在冰豆网上搜索。
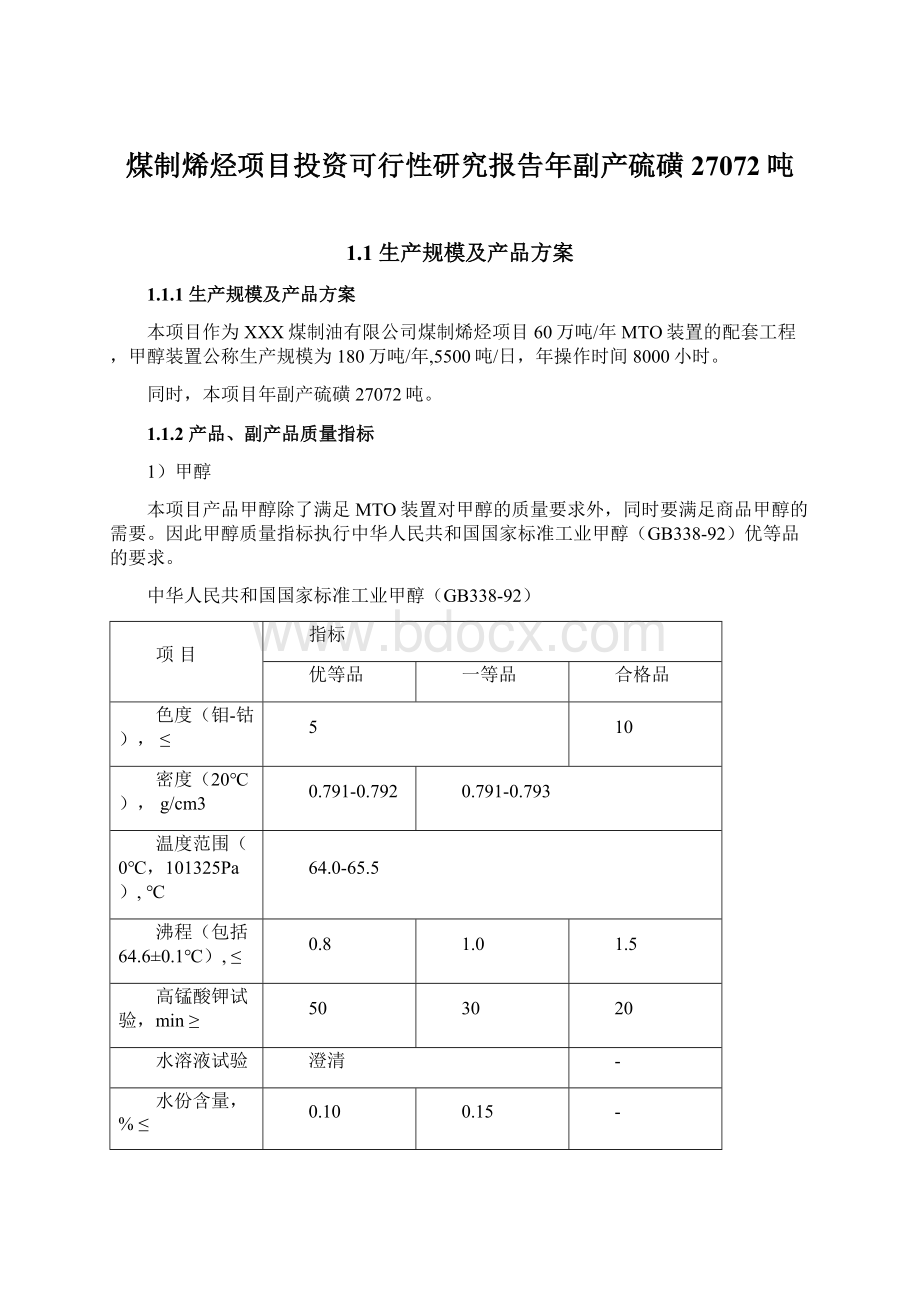
酸度(以HCOOH计),%≤
0.0015
0.0030
0.0050
碱度(以NH3计),%≤
0.0002
0.0008
羰基化合物(以CH2O计),≤
0.002
0.005
0.010
蒸发残渣含量,%≤
0.001
0.003
2)副产品硫磺
硫磺产品符合中华人民共和国国家标准(GB2449-92)优等品指标。
硫,%≥
99.9
99.5
99.0
酸度(以H2SO4计),%≤
0.02
水份,%≤
0.50
1.00
灰份,%≤
0.03
0.20
砷,%≤
0.0001
0.01
0.05
粒度
片状
1.2工艺技术选择
1.2.1原料路线确定
甲醇是由一氧化碳与氢在催化剂存在的情况下进行化学反应而制得。
煤、焦炭、天然气、炼厂气、石脑油(轻油)、渣油(重油)、焦炉气和乙炔尾气等均可用来制造一氧化碳和氢(合成气),作为合成甲醇的原料。
在甲醇生产装置中,合成气的制备,在装置总投资中占绝大部分(约为60%),而甲醇的合成、粗甲醇的精馏以及公用工程等部分的投资所占比例较少,所以,甲醇生产原料路线的选择,主要是对合成气制备所用原料以及工艺路线的选择。
甲醇生产装置各工序的投资比例见下表:
甲醇生产装置各工序投资比例表
序号
占总投资的比例
1
合成气制备(包括气化、净化、冷冻)
60%
2
甲醇合成
10%
3
甲醇精馏
4
公用工程等
20%
选用生产甲醇合成气的原料,可以从原料储量、现有生产能力、原料价格、成本、投资费用与技术水平等进行综合考虑。
XXX集团万利煤矿地处鄂尔多斯市,矿区有丰富的煤炭资源,从储量和目前的生产能力上看,完全可满足合成甲醇所需合成气原料的需要。
以煤或天然气为原料制合成气的生产工艺都比较成熟,国内外都有大型工业化装置在运转。
国外大型甲醇装置大多采用以天然气为原料的生产路线,主要原因除了一次性投资较低外,也与国外的天然气价格低有关。
比如沙特阿拉伯1998年的天然气价格为0.15元/Nm3,目前价格为0.279元/Nm3。
俄罗斯的天然气价格在0.20元/Nm3左右。
因此中东地区及俄罗斯以天然气为原料的大型甲醇生产装置甲醇成本较低,约在100~120美元之间。
近年来,美国的天然气价格上涨幅度较大,由0.5元/Nm3涨到0.7元/Nm3,2001~2002年已先后关闭340万吨甲醇生产能力。
一般认为,天然气价格高于0.7元/Nm3,则甲醇成本大于1100元/吨,已无竞争能力。
与国外相比,我国以天然气为原料的甲醇厂由于规模小(目前最大能力为20万吨/年)、能耗高(一般为1100~1260Nm3/t,最高达1770Nm3/t甲醇),其成本一般为1300~1400元/吨。
2002年我国进口179.96万吨甲醇,到岸价全年平均为154.88美元/吨(折人民币1285.5元),我国以天然气为原料的甲醇厂生产的甲醇在价格上无法与国外同类产品竞争。
然而,以煤为原料的大型甲醇生产装置,则产品成本较低,且有成熟技术,可以与国外厂家相竞争。
本项目推荐以煤为原料生产甲醇的技术路线。
1.2.2工艺技术方案比较与选择
1)气化工艺技术
a)国外气化工艺技术概况
以煤为原料的气化方法主要有固定床和流化床、气流床等。
固定床气化技术
固定床气化技术在我国运用较广,较为先进的有鲁奇(Lurgi)气化技术。
此技术经过英国煤气公司和鲁奇公司联合攻关,开发一种新炉型-BGL炉,变干粉排渣为熔融排渣,气化效率和气体成分有了很大改进,污染问题也有所改善。
现有一台工业示范炉在德国运行,用于处理城市垃圾,所用原料为各种城市垃圾、废塑料和烟煤。
但因气化温度变化不大,生成气中甲烷及氮气含量大,不宜做合成气;
但其热值较高,用于做城市煤气较好。
流化床气化技术
流化床气化技术主要有德国温克勒(Winkler)流化床粉煤气化技术。
该技术压力较低,建有生产燃料气的装置,目前没有生产合成气的装置。
气流床气化技术
气流床气化技术有美国德士古气化(Texaco)技术和荷兰壳牌谢尔(shell)粉煤加压气化技术。
b)国内气化工艺技术概况
固定床气化
固定层间歇气化技术,该技术投资低,技术成熟,目前我国小氮肥、小甲醇厂90%以上采用该工艺生产。
该技术气化效率低,单炉产气量少,常压间歇气化,吹风过程中放空气对环境污染严重,每吨合成氨的吹风放空气量达2800~3100立方米。
该技术在国外已被淘汰。
国内固定床气化还有富氧连续气化技术,虽然该技术连续气化无吹风气排放,污染较少,但只能采用焦炭或无烟煤作原料,原料价格高,且生成气中氮气含量高,不适合作合成甲醇的原料气。
流化床气化
国内流化床气化主要有中科院山西煤化学研究所开发的灰熔聚流化床粉煤气化技术,该技术可用多种煤质作原料,如烟煤、焦炭、焦粉等,使用粉煤在1100℃下气化,固体排渣,无废气排放。
该技术工业示范装置已于2001年在陕西城固氮肥厂建成,小时耗煤量4
.2吨。
其煤种适应性广,操作温度约为1000℃,反应压力为0.03MPa(G)。
气化炉是一个单段流化床,结构简单,可在流化床内一次实现煤的破粘、脱挥发份、气化、灰团聚及分离、焦油及酚类的裂解。
带出细粉经除尘系统捕集后返回气化炉,再次参加反应,有利于碳利用率的进一步提高。
产品气中不含焦油,含酚量低。
碳转化率为90%。
主要的缺点是合成气中(CO+H2)为68~72%,有效气体成分较低,其次是气化压力低、单炉产气量小。
恩德粉煤气化
恩德粉煤气化技术,在朝鲜有30多年的运行经验,适用于灰分不大于40%的褐煤、长焰煤、不粘或弱粘结的煤粉(0~10mm)。
气化剂采用蒸汽和富氧,富氧分为两段加入气化炉,在常压下进行气化反应,反应温度为1000~1100℃,固态排渣,无废气排放。
气化炉无炉筚,空筒气化,操作可靠,气化炉运转率可达92%。
单炉产气量有10000Nm3/h,20000Nm3/h,40000Nm3/h等。
合成气(CO+H2)为62~65%,CO2为27~28%,其它为惰性组分。
由于气化剂为富氧,故合成气中氮气含量高,故此合成气适用于作为合成氨原料气。
主要的缺点也是有效气体成分较低、且含氮高,气化压力低、单炉产气量小。
气流床气化
我国煤气化技术科研人员经过多年努力研究,开发出了具有中国知识产权的煤气化技术,即华东理工大学会同鲁南化肥厂等单位合作开发的水煤浆四喷嘴撞击流气化技术,该技术氧耗、煤耗比德士古气化技术低,碳转化率可达98%,有效气体成分(CO+H2)83~85%,这些指标均比德士古气化技术高。
采用该技术建立的日处理煤量20吨的工业性试验装置已运转400小时以上,并经过72小时考核,取得了国家专利,经过科技部组织的评审与验收。
德州恒升公司大氮肥国产化工程及兖矿集团年产24万吨甲醇项目均采用了该技术,现正在设计、建设中。
由于该技术中试试验时间较短,大型装置未投产验证,有一定的风险。
气化炉烧嘴较多,停车检修或更换烧嘴时影响面较大,由于采用四喷嘴,需要配多台高压煤浆泵及相应管线和仪表控制系统,加之炉体加长,气化流程中增加了分离器等,投资与采用德士古水煤浆气化技术相比(计入德士古专利费后)略低。
以日处理750吨煤的气化炉进行比较,初步估算投资费用差别如下:
德士古与四喷嘴炉投资比较
气化技术
德士古水煤浆气化
水煤浆四喷嘴撞击流气化
德士古炉-四喷嘴炉
气化炉设备费(万元)
1台
-200
煤浆泵设备费
2台
自控仪表材料费(万元)
1套
4套
-500
其他工程费(万元)
-410
软件费(万元)
1660
200
1460
合计(万元)
150
从上表可看出,水煤浆四喷嘴撞击流气化炉和典型的德士古水煤浆气化炉相比,硬件投资增加,但软件投资可节省,两者相抵,总投资相差不多,采用国内有自主知识产权的四喷嘴撞击流气化炉稍微低一点。
但鉴于该炉型尚无工业运行的经验,加之事故和停车的几率增加,运行的可靠性较差,故本项目暂不推荐。
原化工部临潼化肥研究所(现西北化工研究院)早在60年代末就已开展水煤浆纯氧气化的研究,70年代初建立日处理50吨的气化装置。
从水煤浆制备、纯氧气化、灰水处理等试验中取得工艺流程的优化,最终工艺条件的选择、设备材料的选择、自动控制,软件开发等一系列工程数据。
本世纪初该院又开发了焦煤水加添加剂的混合煤浆气化技术,已成功地应用于油气化装置的改造,建有工业化装置,该技术已申请国家专利并获得批准,专利号00113911.8。
为配合水煤浆气化的研究试验工作,洛阳材料研究所研究制成了水煤浆气化炉的耐火砖,原化工部化工机械研究所开发了二流道、三流道的烧嘴,重庆热工仪表研究所开发了适于水煤浆气化的测温度计等。
这一系列科研成果得到了化工部科技司、国家科委的大力支持和技术鉴定,为今后我国水煤浆气化工程应用奠定了基础,也为工程设计提供了基础数裾。
c)气化技术的选择
目前大型煤气化技术较为先进的有Texaco水煤浆气化,Shell粉煤加压气化,Lurgi固定床加压气化。
国外大型气化技术比较表
Texaco
Shell
Lurgi(传统)
气化压力
3.0~6.5
2.0~4.0
3.0
气化温度℃
1300~1400
1400~1600
850
单炉最大能力
吨煤/天
500~2000
2000
600
气化炉型式
热壁式、单喷嘴
冷壁炉、四喷嘴
热壁炉
进煤方式
水煤浆浓度
>
60%泵送
煤粉用氮气输送
粒度90%<
90μm
碎煤干法加料
热回收方式
激冷、废锅
废锅
废锅
排渣
液态排渣
固态排渣
碳转化率%
96—98
99
90
有效成份(CO+H2)
较高>
80%
高>
90%
68%
净化气中惰性气含量
<
0.5%
5%
10%(N2+CH4+Ar)
吨甲醇耗煤量(干,弛放气氢回收时)
1.31
1.27
氧气用量
高(比Shell炉高10%)
较低
低
工业化装置数
7
多
在中国已投产/在建的工业装置
4/7
0/7
4/0
环境影响
友好
有污染治理问题
投资(含空分)
高(比Texaco约高15%)
国产化率
高
建设周期
较短
长(比Texaco炉长半年以上)
Shell气化技术
Shell气化技术是荷兰壳牌公司开发的一种先进的气化技术,该技术采用纯氧、蒸汽气化,干粉进料,气化温度达1400~1700℃,碳转化率99%,有效气体(CO+H2)90%以上,液态排渣,采用特殊的水冷壁气化炉,使用寿命长。
采用废锅流程,可副产高压蒸汽。
采用干粉气化,氧耗量较低,但需要氮气密封,气化压力不能太高;
气化炉(带废锅)结构复杂庞大;
设备费及专利费均较高。
Shell气化由于采用氮气密封及吹送,因而气化产生的合成气中惰性组分含量约为5%,因此对于甲醇合成来说弛放气量要增加。
与德士古综合比较,两种气化工艺的吨甲醇煤耗相差不大。
Shell气化压力最高到4.0MPa,若甲醇合成采用5.2MPa合成压力,则合成新鲜气需要压缩。
用Shell气化制甲醇合成气要增加一套净化合成气增压机;
由于变换气进低温甲醇洗净化装置的压力低,也造成净化系统的投资增加。
此外,因合成循环气中的惰气高,使合成回路循环压缩机的功耗增加;
不但抬高了压缩机的造价,也增加了运行费和生产成本。
该技术目前只有国外两套以煤为原料大型装置在运行,用于联合循环发电,工业化的经验不多,技术须依赖进口,国内技术支撑率低。
国内有六套Shell气化装置正在建设,另有几个项目也签了引进合同。
但从实际建设情况看,气化炉供货周期不少于18个月,关键设备国产化率低,使得Shell气化装置投资高,建设周期长,国内并无运行经验,因此也加大了投资的风险。
德士古气化
德士古气化技术属于气流床气化技术,是美国德士古(Texaco)公司根据油气化技术的思路开发出来的。
它是在煤中加入添加剂、助熔剂和水,磨成水煤浆,加压后喷入气化炉,与纯氧进行燃烧和部份氧化反应。
气化温度1300~1400℃,气化炉无转动部件,对于生产合成气的气化炉,大多采用冷激流程。
该技术由于是水煤浆进料,大量水份要进行气化,因而以单位体积的(CO+H2)计的煤耗和氧耗均比Shell气化高。
但其粗水煤气中惰性气体含量很少,因而在甲醇合成时不仅循环气量小、省压缩功,而且弛放气量小,可以不设弛放气氢回收装置。
德士古气化还有以下优点:
单台炉处理煤量大,最大日处理煤量2000吨;
气化压力高,新鲜气可不需增压、且合成气压缩功耗省,尤其是生产甲醇时,可实现等压合成;
有效气(CO+H2)含量高,生成的新鲜合成气惰性组分含量低,特别适合做生产甲醇的合成气,甲醇合成弛放气排放量低。
煤的适应性宽。
可利用粉煤,原料利用率高;
三废量小,污染环境轻,废渣可做水泥原料;
该技术在世界上已有7套装置运行,其中我国有4套;
同时2004年,中国在建的德士古装置有7套。
德士古气化技术在我国使用最多,鲁南化肥厂、渭河化肥厂、上海焦化厂三联供装置、淮南化肥厂均以水煤浆气化技术进行改造或扩建。
本装置的原料煤属低变质长焰煤,化学活性良好,灰熔点1130℃,符合Texaco气化用煤。
另外水煤浆气化技术经过我国有关科研、设计、生产、制造部门的多年研究,已基本掌握该技术,并能设计大型工业化装置,国产化率达90%以上,气化炉在国内制造,可以控制并节省大量投资、同时可有效缩短建设周期。
此外,该技术国内支撑率高,生产运行管理经验多,风险少,故推荐做为本项目的气化工艺技术。
鲁奇固定床加压气化
鲁奇固定床加压气化工业化的时间最长,目前国外仍有100多台炉子在运行,在我国也建有兰州、哈尔滨、天脊、义马、解化等5套装置。
该技术虽然能连续加压气化,但由于气化温度较低(~1000℃),生成气中甲烷含量大,同时生成气中含苯、酚、焦油等一系列难处理的物质,净化流程长;
尤其是该技术只能用碎煤不能用粉煤,因而原料利用率低,尽管筛分下来的粉煤可以配燃煤锅炉加以利用。
应当指出的是,上个世纪九十年代此技术经过英国煤气公司和鲁奇公司联合攻关,开发出了一种新的炉型BGL炉,变干粉排渣为熔融排渣,气化效率和气体成分有了很大改进,污染问题也有所改善,目前有一台能力日处理500吨煤的示范炉在德国运行,原料为城市垃圾与煤混烧。
由于尚无大的以煤为原料的BGL气化炉的数据和运行经验,故上表中仍暂列传统鲁奇炉的数据。
由于BGL炉与传统鲁奇气化炉在气化温度上变化不大,生成气中甲烷及氮气含量仍然很大,对于生产甲醇来说,意味着大量合成气要放空,煤耗和功耗都要增加;
其次,煤气净化流程变长,且三废治理难度加大,故不推荐做为大甲醇项目可研的气化技术。
d)气化流程
煤浆气化工艺流程有两种:
激冷流程和废锅流程。
废锅流程可产生高压蒸汽,但由于气化气温度高、带有大量煤渣,对废锅有磨蚀冲刷,设备材质要求高,一次投资及维修费用较大;
激冷流程是在气化炉内将气体用水激冷降温的同时,洗涤除尘,出气化炉的气体带有大量的水蒸汽,在变换工段不再补加蒸汽;
这种流程气化设备投资较低,维修工作量较少。
本项目气化采用激冷流程。
e)气化压力
煤浆加压气化压力可以采用2.8MPa、4.0MPa和6.5MPa三种。
三种气化压力均已有大型装置的运行经验。
采用6.5MPa(G)压力煤浆气化,由于气化压力高,净化后合成气压力仍保持在5.2-5.7MPa(G),正好符合低压合成甲醇的压力,因此合成气不需增压,比采用4.0MPa生产甲醇压缩机可降低30%能耗,故本项目选择6.5MPa压力气化。
f)气化炉规格
气化炉的规格有φ3.2×
12.2m和φ2.8×
12.2m两种,可根据合成气规模确定。
由于本项目日处理煤量为8256吨,拟选用φ3.2m气化炉六台,五开一备。
每台气化炉日处理煤量为1651吨,最大可达2000吨,有20%的增产能力。
气化炉烧嘴正常的更换时间约为每40-60天一次,每次约8-16小时,每年至少更换或检修耐火砖一次,时间约1.5个月,因此保证安全稳定连续生产需备用一台气化炉。
g)灰水处理
现有的生产装置中灰水处理流程有三种:
四级闪蒸、三级闪蒸加汽提及二级闪蒸。
相比较而言,四级闪蒸或汽提工艺后被浓缩的灰水温度较低,有利于灰水的澄清,故本项目灰水处理工艺采用四级闪蒸、其中高压闪蒸将气化炉黑水和碳洗塔黑水分开进行,澄清槽沉淀、真空过滤机分离细渣。
2)净化工艺技术
a)净化工艺技术概况
采用煤浆气化工艺生产的粗煤气除含CO、H2、CO2外,还有少量H2S、COS、CH4、N2,微量的氯,氨等成分。
硫化物、氯、重金属镍等对甲醇合成催化剂是毒物,必须除去。
另外H2与CO的比例也不能满足甲醇合成的需要,因而粗煤气需经部分变换调整H2/CO、除去多余CO2、H2S、COS等净化过程方可进行甲醇合成。
变换
煤浆气化气中CO含量为49~51%,H2含量为34~35%,不符合甲醇合成新鲜气的要求,需将部分粗合成气进行CO变换,增加H2含量。
这部分气量约占总气量的55%左右,以调整甲醇合成气的组成。
采用耐硫变换时,煤浆气化粗合成气经洗涤后含尘量1~2mg/m3(标),温度为230~245℃,并被水蒸汽饱和,水汽比约为1.4~1.6,直接经过加热升温后即可进入变换,不需再补加蒸汽。
由于流程短,能耗低,故水煤浆气化配耐硫变换是最佳选择。
CO变换反应会产生大量的热,反应热可用来产生蒸汽、预热脱盐水。
脱硫脱碳
从国内外煤气化装置中所采用的脱除酸性气体的工艺来看,低温甲醇洗(Rectisol)和NHD(或Selexol)较常见。
低温甲醇洗(Rectisol)工艺是采用冷甲醇作为溶剂脱除酸性气体的物理吸收方法,是由德国林德公司和鲁奇公司联合开发的一种有效的气体净化工艺。
该技术成熟可靠,能耗较低,气体净化度高,可将CO2脱至10ppm以下,H2S小于0.1ppm。
NHD(或Selexol)同低温甲醇洗一样,同属物理吸收,其对CO2、H2S等均有较强的吸收能力,但对COS的吸收能力较弱。
NHD净化可将CO2脱至0.1%以下,H2S小于1ppm。
制取甲醇合成气的净化流程,一般在NHD净化后,增加精脱硫装置,这样才能保证合成气的总S小于0.1ppm。
目前世界上大型煤气化装置产生的合成气净化采用低温甲醇洗技术较为普遍;
采用NHD技术的装置很少,NHD净化大都用于中小型装置。
压缩制冷
低温甲醇洗净化工艺需外供冷量,提供冷量的技术较多,较常用的有溴化锂吸收制冷技术,适用于提供4~20℃级的冷量;
氟制冷技术,适用于提供-5~-35℃级的冷量;
氨制冷技术,适用于提供-25~-45℃级的冷量;
乙烯制冷技术,适用于提供-43~-115℃级的冷量等等。
本项目采用的低温甲醇洗技术需要-35℃级的冷量移出反应热,采用氨压缩制冷工艺流程。
b)净化工艺技术的比较及选择
将粗水煤气调整为甲醇合成气,CO变换有两种流程,即部分变换和全部变换。
两种工艺各有优点:
部分变换的优点是由于部分气体进变换炉,气量少,气体中水/汽比高(约1.4),变换反应推动力大,催化剂用量少,其中经变换气体中的有机硫约95%以上可转化为H2S;
H2/CO的调整靠配气,容易调整,变换炉及粗煤气预热器设备小;
缺点是有部分粗煤气不经变换,其中的有机硫未能部分转化为无机硫,但是如果采用低温甲醇洗净化,有机硫也能完全脱除。
全部变换时全部粗煤气经过变换,其中的灰尘会被催化剂截留,但变换率靠调整气体的水/气来实现,生产控制难度较大,且由于气体水气比小,变换反应推动力小,催化剂用量大,其中有机硫的转化会降低到60%左右,总的有机硫的转化与部分转化差不多。
全部变换流程中粗煤气需先经废热锅炉换热产生低压蒸汽,将粗煤气中的水/汽比降下来,粗煤气冷凝出来的工艺冷凝液含有一定的灰尘,用这部分高温冷凝液去气化碳洗塔洗涤粗煤气,洗涤效果差;
变换前的低压废热锅炉也容易被灰尘堵塞。
根据粗水煤气量,本项目采用部分变换流程,变换气和未变换气分开,这样使得设备尺寸减小,变换炉尺寸约为φ4.0m,便于制造和运输。
部分变换的催化剂装填量约51m3,在进变换之前水煤气首先经过气液分离器、煤气过滤器除去气体中杂质和液体,然后经过预热器加热到一定温度进入变换炉。
低温甲醇洗(Rectisol)工艺技术成熟可靠,能耗较低,气体净化度高,可将合成气中的CO2脱至10ppm以下,H2S小于0.1ppm。
而且溶剂吸收能力大,循环量小,能耗省,溶剂价格便宜,操作费用低亦是此法的优越性所在。
该法缺点是在低温下操作,设备低温材料要求较高,整个工艺投资较高。
NHD(或Selexol)溶液对CO2、H2S等均有较强的吸收能力,采用这种技术可将合成气中的CO2脱至0.1%以下,H2S小于1ppm,但对COS吸收能力差,需增加水解装置,而且该工艺须将脱硫和脱碳分开脱除,使得流程复杂,另外其溶剂昂贵,吸收能力比甲醇低,因而,溶剂循环量大,操作费用较高,该法的优点在于设备无腐蚀,可采用碳钢设备,整个工艺投资较少。
关于低温甲醇洗和NHD的比较见如下表:
低温甲醇洗和NHD技术比较
单位
低温甲醇洗
NHD
蒸汽
相对值
循环水
4.5
冷冻量
1.6
电
有效气损失
气提气,N2
投资
1.4
从上表对比中可以看出,虽然NHD的投资低于低温甲醇洗,但其运行费用较高。
而且低温甲醇洗在国内具有丰富的生产操作经验,除部分低温材料需引进外,设备设计和制造等均可在国内解决。
最主要的问题是由于本项目规模大,如采用NHD工艺溶液循环量大,液相管道较大,因此,推荐酸性气体脱除选用低温甲醇洗工艺。
目前,国外低温甲醇洗工艺国外有林德工艺和鲁奇工艺二种流程,二者在基本原理上没有根本区别,而且技术都很成熟。
两家专利在工艺流程设计、设备设计和工程实施上各有特点。
国内大连理工大学经过近20年的研究,也开发成功了低温甲醇洗工艺软件包,并