上料机液压系统设计Word文档下载推荐.docx
《上料机液压系统设计Word文档下载推荐.docx》由会员分享,可在线阅读,更多相关《上料机液压系统设计Word文档下载推荐.docx(14页珍藏版)》请在冰豆网上搜索。
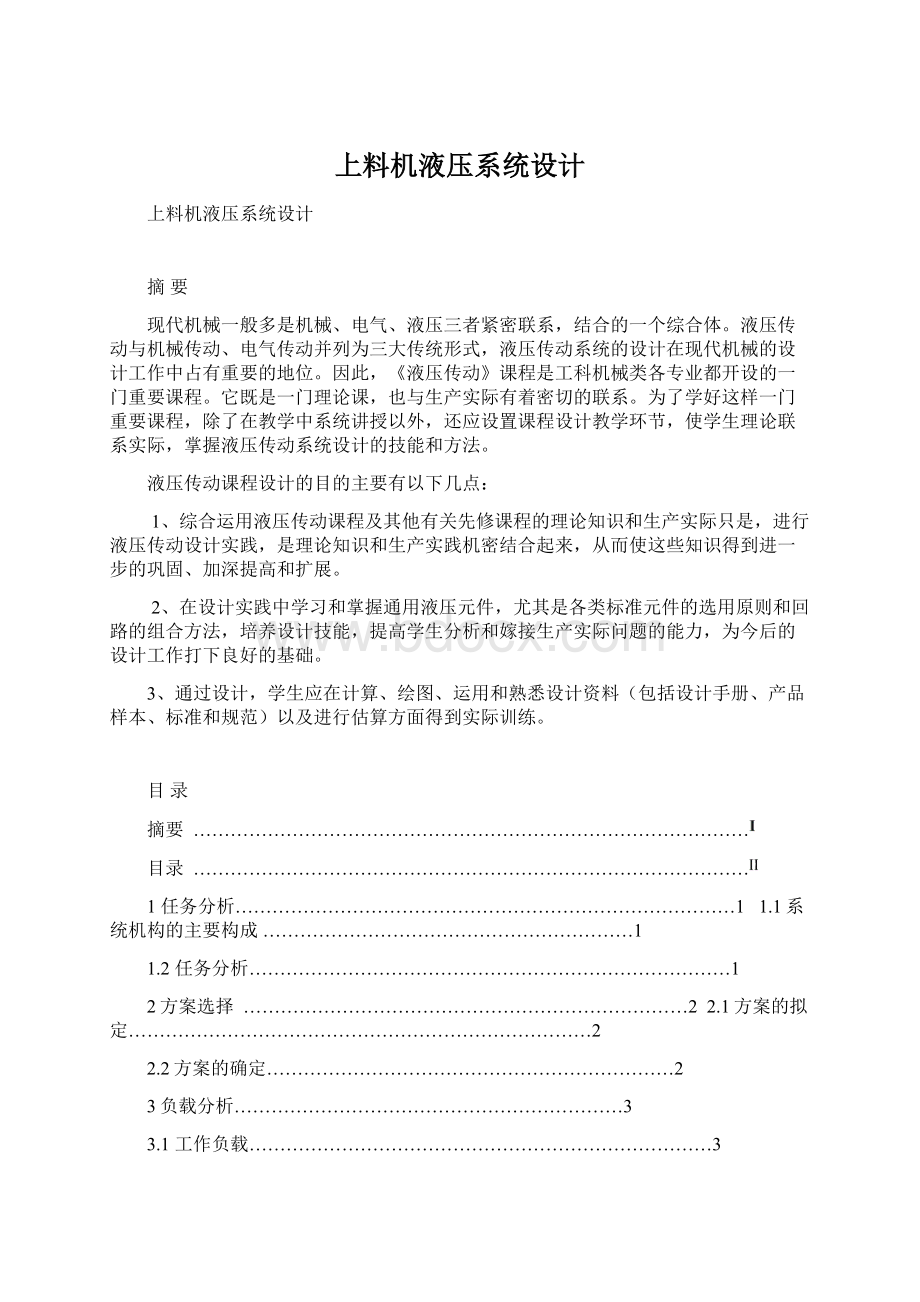
5.7活塞最大行程和活塞杆长度的确定……………………………………8
6液压系统原理图的拟定…………………………………………………………9
7液压元件的选择……………………………………………………………11
7.1确定液压泵的型号及电动机功率……………………………………………11
7.2选择阀类元件及辅助元件…………………………………………11
8液压系统的性能验算…………………………………………13
8.1压力损失及调定压力的确定………………………………………13
8.1.1沿程压力损失………………………………………………13
8.1.2局部压力损失…………………………………………………13
8.1.3总的压力损失…………………………………………………14
8.2系统的发热和温升…………………………………………14
参考文献………………………………………………………………15
致谢…………………………………………………………………………16
1任务分析
1.1系统机构的主要构成
机构不断地将材料从低的位置运到高的位置,然后又回到起始位置重复上一次的运动。
其结构如图1.1所示,滑台采用V形导轨,其导轨面的夹角为90度,滑台与导轨的最大间隙为2mm,工作台和活塞杆连在一起,在活塞杆的作用下反复做上下运动。
图1.1上料机构示意图
2任务分析
系统总共承受的负载为6500N,所以系统负载很小,应属于低压系统。
系统要求快上速度大于38m/min,慢上的速度大于9m/min,快下的速度大于58m/min,要完成的工作循环是:
快进上升、慢速上升、停留、快速下降。
但从系统的用途可以看出系统对速度的精度要求并不高,所以在选调速回路时应满足经济性要求。
2方案选择
2.1方案的拟定
2.11供油方式
从系统速度相差很大可知,该系统在快上和慢上时流量变化很大,因此可以选用变量泵或双泵供油。
2.12调速回路
由于速度变化大,所以系统功率变化也大,可以选容积调速回路或双泵供油回路。
2.13速度、换接回路
由于系统各阶段对换接的位置要求高,所以采用由行程开关发讯控制二位二通电磁阀来实现速度的换接。
2.14平衡及锁紧
为了克服滑台自重在快下过程中的影响和防止在上端停留时重物下落,必需设置平衡及锁紧回路。
根据上述分析,至少有两种方案可以满足系统要求。
(1)用变量泵供油和容积调速回路调速,速度换接用二位二通电磁阀来实现,平衡和锁紧用液控单向阀和单向背压阀。
系统的机械特性、调速特性很好,功率损失较小,但是系统价格较贵。
(2)用双泵供油,调速回路选节流调速回路,平衡及锁紧用液控单向阀和单向背压阀实现。
系统的机械特性、调速特性不及第一种方案,但其经济性很好,系统效率高。
2.2方案的确定
综上所述,考虑到系统的流量很大,变量泵不好选,第二种方案的经济性好,系统效率高,因此从提高系统的效率,节省能源的角度考虑,采用单个定量泵的、供油方式不太适,宜选用双联式定量叶片泵作为油源,所以选第二种方案。
3负载分析
3.1工作负载
工作负载等于工作台自重加上物料的重量即
(5500+1000)N=6500
3.2摩擦负载
由导轨的角度与间隙计算平均摩擦
由于工件为垂直起升,所以垂直作用于导轨的载荷可由其间隙和结构尺寸求得
,取
则有
静摩擦负载
动摩擦负载
3.3惯性负载加速
减速
制动
反向加速
反向制动
根据以上计算,考虑到液压缸垂直安放,其重量较大,为防止因自重而自
行下滑,系统中应设置平衡回路。
因此在对快速向下运动的负载分析时,就不考
虑滑台2的重量。
则液压缸各阶段中的负载如以下表3.1所示。
4负载图和速度图的绘制
按照前面的负载分析结果及已知的速度要求,行程限制等,绘制出负载图及速度图如下图4.1。
钢筒壁及法兰的材料选45钢,活塞杆材料选Q235
工况
计算公式
总负载F/N
缸推力F/N
启动
6533.94
7180.15
加速
7401.32
8133.32
快上
6516.97
7161.51
减速
5853.70
6432.64
慢上
制动
6295.88
6918.55
反向加速
1343.50
1476.37
快下
16.97
18.65
表3.1液压缸各阶段负载
图4.1负载图-速度图5液压缸主要参数的确定
5.1初选液压缸的工作压力
根据分析此设备的负载不大,按类型属机床类,所以初选液压缸的工作压力为2.0Mpa。
5.2计算液压缸的尺寸
按标准取:
D=80mm
根据d与D的关系取
,则液压缸的有效作用面积为:
无杆腔面积
有杆腔面积
5.3活塞杆稳定性校核
因为活塞杆总行程450mm,而活塞杆直径为56mm,l/d=450/56=8<
10,无需进行稳定性校核。
5.4求液压缸的最大流量
5.5绘制工况图
工作循环中各个工作阶段的液压缸压力,流量和功率如表5.1所示
表5.1
压力p/MPa
流量q/(L/min)
功率P/W
1.30
201.06
4356.3
50.27
1089.18
0.0066
153.81
16.92
由上表可绘制液压缸的工况图图5.1如下
图5.1
液压缸其它参数的选择
5.6最小导向长度当活塞杆全部外伸时,从活塞支承面中点到导向套滑动面中点的距离称为最小导向长度H。
如果导向长度过小,将使液压缸的初始挠度增大,影响液压缸的稳定性,因此设计时必须保留有一最小导向长度。
对于一般的液压缸,当液压缸的最大行程为L,缸筒直径为D时,最小导向长度为:
所以取
mm。
5.7活塞最大行程和活塞杆长度的确定
活塞的最大行程已由要求给定为450mm。
活塞杆的长度
活塞杆的长度应大于最大工作行程、导向长度、缸头、缸盖四者长度之和。
即
L+H+
+
=450+95+78+32=655mm.但是为了使其能够工作,必须和工作台连接,所以还应支出一部分。
考虑实际工作环境和连接的需要,取这部分长度为50mm。
所以液压缸的总长
=655+50=705mm。
6液压系统原理图的拟定
从以上液压缸工况图可知,该系统在快上和慢上时流量变化确实很大,因此可以选用双泵供油是正确的。
该系统在慢速和快下时速度需要调节,由于系统功率和速度变化大,但系统的工作负载变化小,调速特性要求不高,是可行的。
此外,为防止在上端停留时重物下落和在停留期间内保持重物的位置,在液压缸的无杆腔进油路上设置了液控单向阀。
另一方面,为了克服滑台自重在快下过程中的影响,设置了一单向背压阀。
快上、快下和慢上之间速度换接采用由行程开关发讯控制二位二通电磁阀来实现。
综上所述拟定液压系统原理图如图6.1。
系统工作过程:
快上时,电磁阀2有电,两泵同时工作,液压油经过电换向阀6、液控单向阀7、单向背压阀8,流入无杆腔,再经过调速阀9、换向阀2回油箱。
慢上时,活塞走到300mm处,压下行程阀9,使电磁阀3有电,大流量泵经过它卸荷,只有小流量泵供油,工作太速度下降。
快下时,电磁阀3复位,电磁阀1有电,双泵同时供油,经过换向阀6、调速阀9、单向背压阀8、液控单向阀7、换向阀6回到油箱。
图6.1系统原理图
7液压元件的选择
7.1确定液压泵的型号及电动机功率
液压缸在整个工作循环中最大工作压力为1.30Mpa.由于该系统比较简单,所以取其压力损失
,所以液压泵的工作压力为
两个液压泵同时向系统供油时,若回路中的泄漏按10%计算,则两个泵的总流量应为
,由于液压缸慢上时所需的流量为
50.27L/min,所以高压泵的输出流量不得少于
根据以上压力和流量的数值查产品目录,选用PV2R34型的双联叶片泵,其额定压力为14Mpa,小泵和大泵的排量分别为66ml/r,200ml/r;
容积效率
,总效率
,所以驱动该泵的电动机的功率可由泵的工作压力(1.70MPa)和输出流量(当电动机转速为970r/min)
查电机产品目录,拟选用电动机的型号为Y160L-6,功率为11KW,额定转速为970r/min。
7.2选择阀类元件及辅助元件
根据系统的工作压力和通过各个阀类元件和辅助元件的流量,可选出这些元件的型号及规格如下表7.1。
表7.1液压元件及规格
序号
名称
估计流量
/(L/min)
额定流量
型号及规格
1
滤油器
232.22
400
2
双联叶片泵
——
266
PV2R34
3
单向阀
174.60
230
AF3-Ea10B
4
电磁溢流阀
500
5
溢流阀
221.17
350
DBDS25K10/252
6
三位四通电液换向阀
300
H-4WEH
7
液控单向阀
284
4CT1-10C
8
单向背压阀
AXF3-E20B
9
行程阀
22C-100BH
10
单向调速阀
169.2
250
MSA30EF250
11
电动机
Y160L-6
油管油管内径一般可参照所接元件接口尺寸确定,也可按管路中允许流速计算。
在本题中,出油口采用内径为25mm,外径为34mm的紫铜管。
油箱油箱容积根据液压泵的流量计算,取其体积
,即
,取油箱的容积V=830L。
为了增加油液的循环距离,使油液有足够的时间分离气泡,沉淀杂质,消散热量,所以吸油管和回油管相距较远,并且中间用隔板隔开,油箱底应微微倾斜以便清洗。
油箱长、宽、高的确定:
根据油箱三个边长必须在1:
1:
1—1:
2:
3的范围内,又有油箱的容积为V=830L,所以油箱的长(L)、宽(D)、高(H)可以设计为L=1100mm,D=900mm,H=840mm。
8液压系统的性能验算
8.1压力损失及调定压力的确定
根据计算慢上时管道内的油液流动速度约为0.50m/s,通过的流量为1.5L/min,数值较小,主要压力损失为调速阀两端的压降,此时功率损失最大;
而在快下时滑台及活塞组件的重量和背压阀所平衡,系统工作压力很低,所以不必验算。
因而必须以快进为依据来计算卸荷阀和溢流阀的调定压力,由于供油量的变化,其快上时液压缸的速度为
此时油液在进油管中的流速为
8.1.1沿程压力损失
首先要判别管中的流态,设系统采用N32液压油。
室温为
时,
,所以有
管中为层流,则阻力损失系数
,若取进、回油管长度均为2m,油液的密度为
,则其进油路上的沿程压力损失为
8.1.2局部压力损失
局部压力损失包括管道安装和管接头的压力损失和通过液压阀的局部压力损失,前者视管道具体安装结构而定,一般取沿程压力损失的10%;
而后者则与通过阀的流量大小有关,若阀的额定流量和额定压力损失为和
和
。
则当通过阀的流量为q时的阀的压力损失
式为
因为本题的所有阀的额定流量比系统最大流量大很多且系统的压力很低,所以通过整个阀的压力损失很小,且可以忽略不计。
同理,快上时回油路上的流量
则回油路油管中的油速
由此可计算出:
(层流),
,所以回油路上的沿程压力损失为:
8.1.3总的压力损失
由上面的计算所得可求出
原设
,这与计算结果略有差异,应用计算出的结果来确定阀的调定值。
8.1.4压力阀的调定值
溢流阀的调定压力应大于系统压力0.3—0.5MPa,所以取溢流阀调定压力为1.7MPa,背压阀的调定压力以平衡滑台自重为根据,即
8.2系统的发热和温升
根据以上的计算可知,系统在快上和慢上的压力不变,慢上是大流量泵卸荷功率为零,所以在快上时,系统损失最大
油箱的三个边长在
范围内,则散热面积为
,假设通风良好,取
,所以油液的温升为
,室温为20,热平衡温度为24.65<
65,没有超出允许范围。
参考文献
[1]王积伟,黄谊,章宏甲.液压传动[M].北京:
机械工业出版社,2006.
[2]雷天觉,新编液压工程手册[M].北京:
北京理工大学出版社,1998.
[3]成大先,机械设计手册[M].北京:
化学工业出版社,2002.
[4]路甬祥,液压气动技术手册[M].北京:
机械工业出版社,2002.
[5]张利平.液压传动系统及设计[M].北京:
化学工业出版社,2005.
[6]王春行,液压控制系统[M].北京:
[7]李状云,液压元件与系统[M].北京:
致谢
非常感谢乔老师在本次课程设计期间给予我的指导和帮助,让我在整体思维和局部细节上都有了很大的进步。
由于时间和个人能力有限,本设计难免存在缺点和错误,恳请老师批评指正。