转炉流程生产管线钢钢中硫含量的控制文档格式.docx
《转炉流程生产管线钢钢中硫含量的控制文档格式.docx》由会员分享,可在线阅读,更多相关《转炉流程生产管线钢钢中硫含量的控制文档格式.docx(45页珍藏版)》请在冰豆网上搜索。
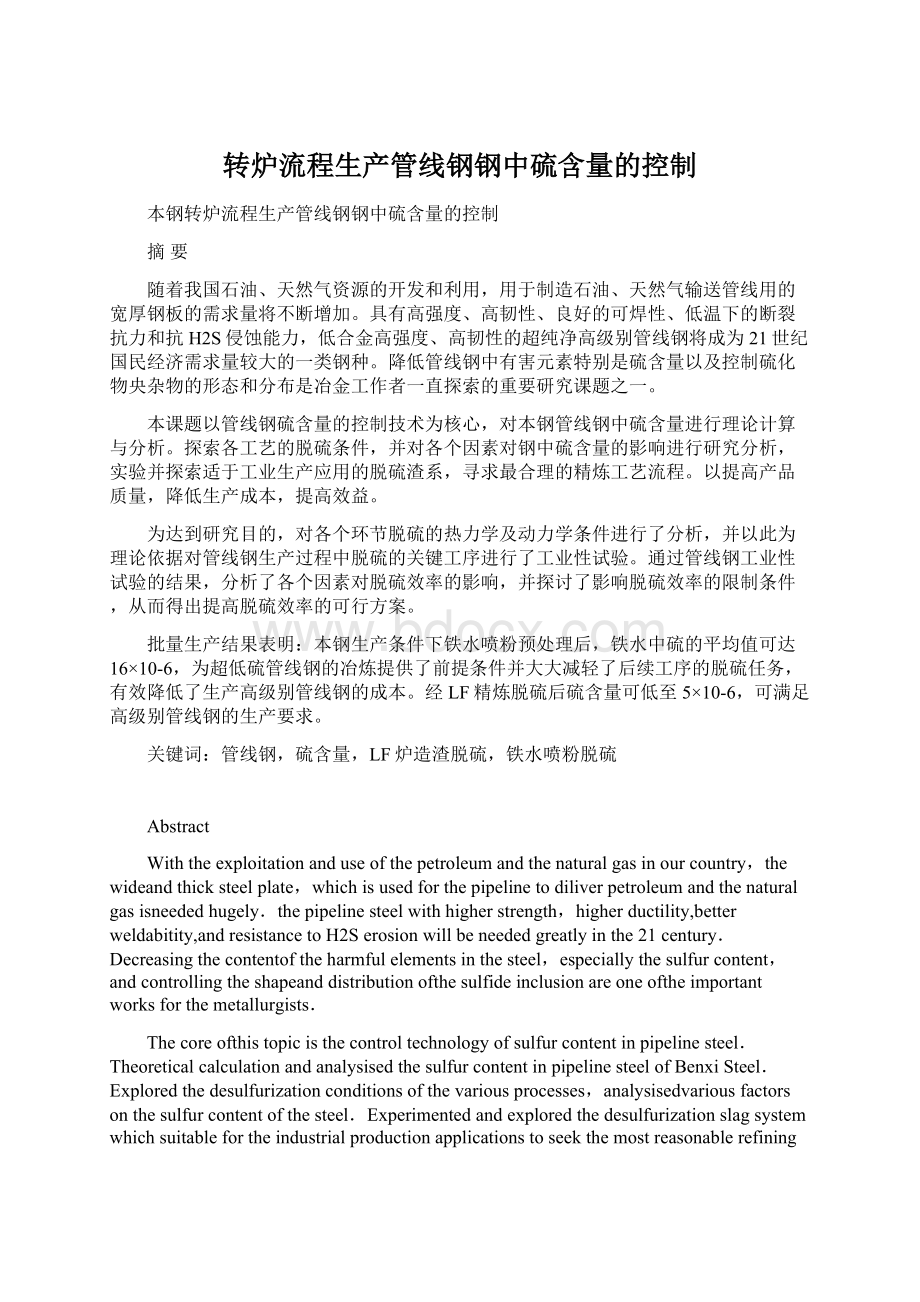
特别是本钢通过2002年对炼钢、热轧进行现代化改造后,加快了高性能管线钢的研制开发力度,先后研制开发了能够满足用户要求的高性能石油管线用钢X52~X70、石油套管用钢J55,参与了国家“973”项目“新一代钢铁材料的重大基础研究”中的子课题“高强度管线钢的产业基础研究”工作。
在国家组织实施的“振兴东北老产业基地高技术产业项目”中,本钢同中科院金属研究所共同申报的“高性能管线钢生产产业化”通过了专家组的评审,并获得国家资金的支持。
“高性能管线钢生产产业化”项目的实施将使本钢成为国内继宝钢、武钢、鞍钢之后能生产具有高附加值的X70以上级别管线钢的钢铁企业。
到目前为止,石油管线钢X52~X70先后通过中石油管材所、管道局的板卷及钢管的性能评定,实物质量满足国家西气东输对管线钢特殊质量的技术要求。
其产品已应用于多条输气、输油、成品油管线工程。
目前,本钢已批量生产石油管线钢,产品经华油钢管##、##石油钢管厂等多家钢管厂的生产使用,产品质量完全符合用户的特殊标准及技术要求。
X80管线钢也已通过鉴定验收,并于2009年第一季度进行了试生产。
高品质高附加值管线钢的批量生产在为企业创造经济效益的同时也为我国经济发展起到一定的推动作用。
1.1.2本课题目的
以管线钢硫含量的控制技术为核心,对本钢生产条件下从铁水预处理经转炉到精炼过程中的钢中硫含量控制技术进行理论计算与分析。
以提高产品质量,降低成本,提高效益。
1.1.3管线钢控制钢中硫含量研究的意义
能源是整个世界发展和经济增长的最基本的驱动力,是人类赖以生存的基础。
在21世纪里,石油和天然气在整个世界的能源结构中的比重将会进一步增加。
绝大多数的石油和天然气的运输都要依靠管道。
预计今后10年,我国将建设超过5万km的油气管道,平均每年需铺设5000km,每年天燃气管道需要钢材近400万t,共需各类油气输送干线用钢约1000万t。
研究表明,石油、天然气管道的建设成本会随着所用管线钢级别的提高而下降,如图1.1所示[1]。
图1.1管线建设采用不同钢级钢管的成本变化率
与此同时,随着石油、天然气需求量的不断增大,管道的输送压力和管径也需要不断地增大,以增加其输送效率。
因此对管线钢材的质量和性能要求也日益苛刻,需要其具有高强度、高韧性、良好的可焊性、低温下的断裂抗力和抗H2S侵蚀能力等特性,而在管线钢中影响影响这些性能的主要元素就是硫,硫含量的高低直接影响到管线钢质量的好坏。
长远来看,研究管线钢中硫含量的控制具有深远而重大的意义。
1.2文献综述
1.2.1国外现状
早期的管线钢一直采用C、Mn、Si型的普通碳素钢,在冶金上侧重于性能,对化学成分没有严格的规定。
自60年代开始,随着输油、输气管道输送压力和管径的不断增大,开始采用低合金高强钢(HSLA),主要以热轧及正火状态供货。
这类钢的化学成分:
C≤0.2%,合金元素≤3~5%。
随着管线钢的进一步发展,到60年代末70年代初,美国石油组织在API5LX和API5LS标准中提出了微合金控轧钢X56、X60、X65三种钢。
1968日本X65级管线钢的使用,为高强度管线钢的生产开创了新的里程碑,此后,高级别管线钢的开发速度加快。
图1.2示出了高强度管线钢的发展历程[2]。
图1.2各级别管线钢的主要合金成分与生产工艺进展
20世纪70年代初,TransCanada首次使用了X70钢管。
20世纪80年代,X70级管线钢逐渐引入工程建设中。
欧洲钢管公司到2001年底已经生产X70钢管近321万t。
X70钢管的生产技术在欧洲钢管、新日铁、住友、NKK、KAWASAKI、IPSCO、ILVA等公司均已成熟,并且批量供应,用于工中。
1985年,API标准又增加了X80钢,而后又开发了X100管线钢,碳含量降到0.01-0.04%,碳当量相应地降到0.35以下,真正出现了现代意义上的多元微合金化控轧控冷钢[3]。
1996年,美国埃克森美孚公司与日本新日铁公司、住友公司签订了X120级管线钢联合开发协议,2001年成功开发出具有高止裂韧性的X120级管线钢,并于2004年进行了示X段的敷设。
随后JFE公司也已经完成了高强度X120级管线钢的开发。
提高钢液纯净度是大幅度提高管线钢强度、韧性和使用寿命的基础。
近二十年来随着冶炼技术的进步,管线钢的纯净度水平不断提高,以钢中碳、磷、硫、氮、氢、氧含量为例,1980年德国蒂森公司生产的钢上述杂质总量可去除到600×
10-6,到90年代则可去除到100×
10-6。
韩国浦项可将P、S、O、N、H总量去除到80×
10-6的水平。
德国人预测,在今后几年中上述杂质含量可以达到以下水平:
[C]≤20×
10-6,[P]≤l5×
10-6,[S]≤5×
10-6,[N]≤15×
10-6,TO≤10×
10-6,[H]≤0.7×
10-6,总和为65.7×
而日本人预测将来日本纯净钢的冶炼水平可达到:
[C]≤6,[P]=2,[S]≤1×
10-6,[N]≤14×
10-6,TO≤5×
10-6,[H]=0.2×
10-6,总量为:
28.2×
下面是国外几个先进的管线钢生产厂家的管线钢工艺。
(1)日本新日铁、JFE、住友
表1.1是日本三大钢铁公司高强度管线钢的生产工艺。
表1.1日本三大钢铁公司高强度管线钢的生产工艺
公司
生产技术
显微组织构成
其他技术
新
日
铁
(1)KIP技术(向钢包内钢水喷粉来生产低硫钢的高效二次精炼技术,通过调整钢包内渣的成分获得超低S含量)
(2)板坯轻压下技术
(3)控制轧制技术+连续在线控制冷却技术
X100钢:
上贝氏体+MA
X120钢:
上贝氏体+弥散碳化物(含碳钢)
HTUFF技术、FEA精密成型技术、高精度制管技术
JFE
(1)采用低Si铁,在铁水预处理炉中采用无渣炼钢法提高钢的纯净度
(2)控制轧制技术+超级在线加速冷却技术,并与在线热处理工艺相结合
贝氏体中分散有硬质M/A
铁素体+贝氏体双相组织(无硼钢)
EWEL技术、提高了大线能量焊接的HAZ任性
住友
金属
(1)采用高纯净钢技术,降低P、S、N等杂质
(2)住友控轧技术+动态加速冷却技术,水冷停止温度低于400oC
贝氏体+马氏体
下贝氏体+弥
散碳化物(含碳钢)
SHT技术、焊接部位超声波探伤技术
注:
HTUFF—新日铁开发的提高厚板HAZ韧性技术;
EWEL—JFE开发的提高厚板HAZ韧性技术;
SHT住友金属开发的高韧性技术
表1.2列举了新日铁、JFE公司高强度、抗大变形性能管线钢的化学成分。
(2)日本钢管京滨厂
日本钢管的京滨厂电弧炉车间包括一台50t高功率电炉,1台VAD和VOD双联精炼炉。
由计算机控制电炉熔炼过程,并在电炉上安装了辅助燃烧器、搅拌器,在精炼工位上安装了喷粉设备,精炼的钢水可由电炉或转炉供应。
该厂利用上述设备生产超低硫、低磷、低氧、低氮、低氢、低碳钢管用钢。
(3)日本新日铁
新日铁生产管线钢的工艺流程为:
复合铁水预处理→顶底复吹转炉→减压下的钢包喷粉(V-KIP)→RH处理→连铸轻压→形变热处理控轧→UOE.
表1.2新日铁、JFE公司高强度、抗大变形性能管线钢化学成
钢级
化学成分(质量分数)/%
C
Si
Mn
P
S
Nb
Ti
其他元素
Ceq
Pcm
X80
0.06
0.26
1.81
0.005
0.002
0.04
0.01
NiMo,Mg
0.41
0.17
X100低C
0.03
0.20
1.96
Ni,Cu,Cr,Mo,V
0.60
0.22
X100中C
0.007
Ni,Cu,Mo
0.46
0.19
X120
1.93
含有
0.02
Ni,Cu,Cr,Mo,B
0.21
1.80
0.001
X100
0.07
2.0
0.15
1.91
Mo,无B
Ceq=C+Mn/6+(Ni+Cu)/+(Cr+Mo+V)/
Pcm=C+Si/30+(Mn+Cu+Cr)/20+Ni/60+Mo/15+V/10+5B
(4)俄罗斯
俄罗斯塔干罗格钢铁厂为提高产品质量,生产出高强度、耐低温、耐腐蚀的无缝钢管,2000年在平炉炼钢车间建成了钢包精炼炉,采用精炼技术后,该厂可将钢中的硫含量降低到120×
10-6以下。
(5)德国蒂森钢铁公司
德国蒂森管线钢(HIC钢)的冶炼工艺路线为:
铁水脱硫(S<
30×
10-6)→复吹(P<
50×
10-6)→钢包内加合成渣、Ar搅拌深脱硫(S<
10×
10-6)→RH脱气→TN喷粉(钙处理和搅拌排除夹杂物)。
另一种冶炼路线为:
10-6)→复吹→钢包罐脱气处理(真空下同时加合成渣,脱至[S]10×
10-6以下,然后喂入Ca-Si包芯线)。
1.2.2国内现状
我国管线钢的应用和起步较晚,过去已铺设的油、气管线大部分采用Q235和16Mn钢。
尽管原油、成品油、天然气的运输基本上已经实现了管道运输。
但是与世界上工业发达国家相比,国内的管道运输在质量上和数量上都存在很大差距。
中国虽然为世界的主要石油出产国之一,但输油输气的管道不足世界管线总长度的百分之一,而且普遍存在输送压力低、管径小的缺点。
“六五”期间,我国开始按照API标准研制X60、X65管线钢,并成功地与进口钢管一起用于管线铺设。
90年代初宝钢、武钢又相继开发了高强高韧性的X70管线钢,并在涩宁兰管道工程上得到成功应用。
到目前为止我国已具备了X52至X120管线钢的生产能力。
随着国内外管道建设的不断升温,国内市场管线钢的需求量不断扩大。
面对如此大的需求市场,国内各钢厂早已意识到了国内管线钢巨大的潜在市场以及开发管线钢的紧迫性,都在积极加大对工艺装备的技改投入,争取占领市场最大份额。
在加紧建设设备的同时,各钢厂也在加大技术研究投入力度,由于影响性能的最终决定因素是钢坯的成分,只有冶炼出高纯净的钢水,才能为生产高等级的管线钢创造良好的原材料条件。
因此,加强对钢水冶炼工艺技术的研究是成功生产高级管线钢的前提条件。
国内管线钢的生产企业和工艺技术如下。
(1)宝钢
宝钢从1995年开始,高韧性管道由研究试制阶段转为工业性批量生产。
到1996年为我国三个重要的输油、输气管道工程提供了X52、X60、X65高韧性管线钢板。
其工艺主要包括:
铁水预处理(TDS)→顶吹转炉(LD)→顶渣→循环真空脱气(RH)→喷粉(KIP)→连铸(CC),按上述工艺路线,管线钢的中间包钢水成分可达到[S]≤20×
10-6,[P]≤90×
10-6,T[O]≤25×
10-6,[N]≤35×
10-6,[H]≤2×
当生产要求[S]极低的抗HIC管线锕时,采用:
铁水预处理(TDS)→顶吹转炉(LD)→顶渣→精炼脱硫(LF)→循环真空脱气(RH)→喷粉(KIP)→连铸(CC)的工艺路线,此时能够保证[S]≤10×
(2)武钢
武钢三炼钢厂采用“BOF→Ar→RH→LF→CC”工艺生产的管线钢,采取示踪剂跟踪、系统取样、综合分析的方法,对RH处理前后、LF处理前后、中间包和铸坯中T[O]、显微夹杂及宏观夹杂物的变化进行了系统研究。
各工序钢中夹杂物洁净度的变化情况见表1.3。
(3)酒钢L290管线钢洁净度研究
酒钢L290管线钢的生产工艺流程为:
铁水预脱硫处理→50t转炉→吹氩处理→LF精炼→全封闭注流保护板坯连铸。
采用加示踪剂连续跟踪,并在转炉终点、LF进出站、中间包和结晶器的前、中和后期以及铸坯取样,对钢中的夹杂物、T[O]和氮含量进行全面系统的分析研究。
各工序钢中夹杂物数量、T[O]和氮含量变化如表1.4。
表1.3武钢管线钢各工序钢中洁净度的变化
项目
T[O]
/10-6
显微夹杂数
/个·
mm-2
大型夹杂量
/mg·
(10kg)-1
吹氩后
20.8
7.28
31.52
RH处理后
16.5
4.74
10.87
LF处理后
17.3
2.46
32.27
中间包
21
3.78
36.56
铸坯
14.7
2.78
1.13
目前国内大型钢铁企业在研制开发管线钢控制钢中硫含量技术方面与日本、韩国及西欧的一些国家相比存在着不小的差距。
宝钢所生产的超低硫管线钢[S]=15×
10-6[4],开发试制的5炉X70管线钢中[S]=(6~18)×
10-6[5],平均仍为10×
##钢铁二炼钢、三炼钢拥有先进的钢水精炼设备,产品的最终[S]近20×
10-6[6]。
鞍钢的铁水镁脱硫可以把[S]降到30×
10-6以下,在转炉冶炼时因废钢和石灰等原料的硫含量高而使终点[S]约增加45×
包钢在LF精炼炉进行钢水脱硫的工业试验,在还原条件下脱硫,钢水终点[S]可达100×
10-6以下[7]。
而高强度管线钢要求要求[S]<100×
由此可见,在管线钢硫含量控制方面,我国还存在着一些差距,进一步开发钢液精炼深脱硫技术具有现实意义。
表1.4酒钢L290管线钢各工序钢中夹杂物数量、T[O]和氮含量变化
工序
/×
10-6
[N]
/×
106
转炉终点
~
23.7
50
LF前
102.5
98.3
9.33
LF后
92.5
26.0
173.6
4.97
中包
88.5
35.0
61.7
5.35
49.4
32.3
45.2
3.62
1.2.3管线钢的性能要求
(1)强度要求
这里主要指屈服强度和抗拉强度。
屈服强度是工厂水压试验,工地强度试压的主要参数。
钢的抗拉强度和屈服强度是由钢的化学成分和轧制工艺所决定的。
输气管线选材时,应选用屈服强度较高的钢种,以减少钢的用量。
但并非屈服强度越高越好,屈服强度太高会降低钢的韧性。
选钢种时还应考虑钢的屈服强度与抗拉强度的比例关系—屈强比。
随着材料强度的提高,材料的抗拉强度增大,脆性增大,屈服强度与抗拉强度之比增大。
API标准对冷扩径管要求屈服强度与抗拉强度之比不大于0.93。
用以保证制管成型质量和焊接性能。
钢在经反复拉伸压缩后,力学性能会发生变化,强度降低,严重的降低15%,即包申格效应[8]。
可采取在该级别钢的最小屈服强度的基础上提高40~50MPa来应对。
(2)冲击韧性
脆性断裂是低温下使用管线的突出质量问题。
为了衡量钢的脆性断裂特性,广泛应用V型缺口的夏贝冲击试验和落重破损试验(DWTT-DmpWeightTearTests),后者是一种有效的工业测试法,能真实地反映管线钢脆性断裂扩展特性。
在1975年前后,对改进管子的韧性的强烈要求已反映到要修改的标准上,有些规程中还特别规定了对焊缝热影响区的(DAZ-HeatAffectZone)冲击韧性要求。
为达到高韧性水平,必须采用碳和硫极低的钢。
这使得目前为满足高冲击韧性要求,管线钢的碳硫含量不断降低。
在焊缝上的韧性可用裂纹开始迁移试验(COD-CrackOpeningDisplacement)来估算,根据工业试验实物数据分析表明,在工作温度条件下,脆性断裂是低温下使用管线的突出质量问题。
临界COD值为0.1mm对,足可以防止X65钢中的脆性断裂的发生。
剪切断裂的传播是天然气管线的另一个问题。
由于气体的可压缩性,在裂纹端部的压力并非一下子消失,因而裂纹可能扩展到相当远的距离处,尽管其速度很慢。
这种剪切断裂的扩展是一个非常复杂的问题,受许多因素影响,诸如管子尺寸、操作压力和温度、材料的韧性等等。
一般材质的管材,其屈服强度比低,韧性好,而材质高的管材(屈服强度大于400MPa)韧性变差。
在高寒地区使用的管材必须达到一定的韧性指标。
(3)抗腐蚀性
由于腐蚀性油、气田的