四连杆机构的振动特性分析与研究刘俊勇Word格式.docx
《四连杆机构的振动特性分析与研究刘俊勇Word格式.docx》由会员分享,可在线阅读,更多相关《四连杆机构的振动特性分析与研究刘俊勇Word格式.docx(18页珍藏版)》请在冰豆网上搜索。
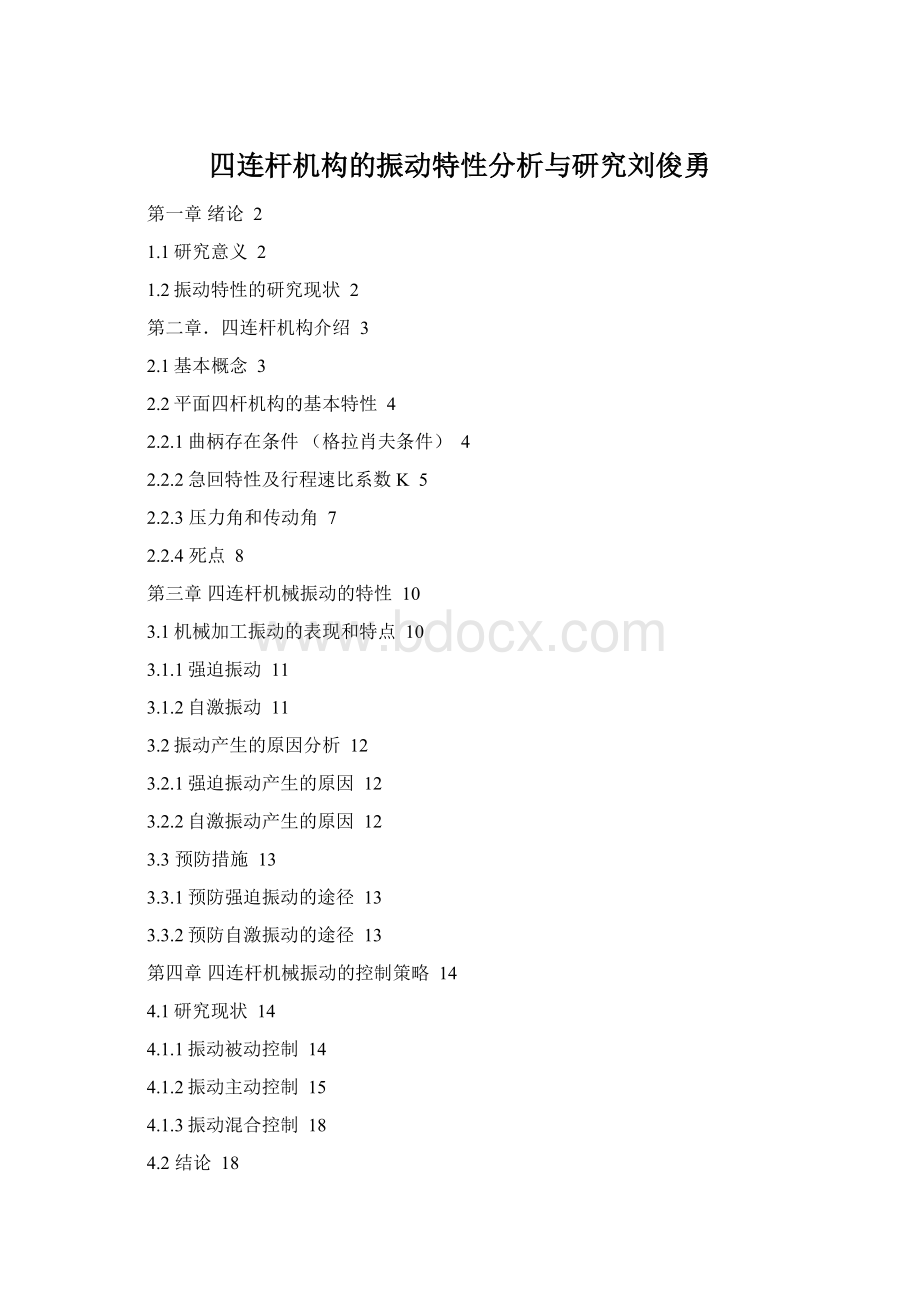
目前基于四连杆机构振动特性分析的机构运动弹性动力学研究正日趋完善,但如何改善机构的动态特性,有效地抑制弹性机构的有害振动,是机构学界面临的一个重要的研究课题。
节约能源和原材料、提高效能是当前世界经济、军事和科技发展面临的关键课题。
目前,从传统的机械制造业到航空航天技术领域、建筑设计、机器人制造等精密机械,低刚度与柔性化是这些领域内结构设计制造的一个重要发展趋势。
这些轻型结构可以增加有效承重载荷的重量,提高运载工具的效率,消耗的能源减少,生产成本降低,运行精度提高。
但是同时这类结构的设计、制造和使用带来了一系列新的问题,诸如:
结构模态阻尼减小,柔性增大,大振幅的振动响应持续时间长,结构疲劳问题严重影响系统的精度和使用寿命,甚至诱发相关部件的损坏。
特别对于高速机械和机器人领域,由于承载能力加大,造成设备整机刚度降低,不平衡质量引起的自激振动加剧,振动引起的弹性变形不仅影响了机构的轨迹精度和定位精度,延迟了机构稳定工作时间,破坏系统运行的稳定性和可靠性,同时降低了工作效率和整机的使用寿命。
对有害动态响应的消减是机械动力学研究的重要问题。
1.2振动特性的研究现状
连杆机构可以实现复杂的运动规律,且加工简便、强度高、可靠性大,所以广泛地用于农业、纺织、轻工、重型、冶金、精密等各机械行业中.但在在高速运行条件下,机构的弹性动力响应不仅使机构的运动轨迹产生偏差,同时还会造成构件疲劳破坏。
为获得高速运转条件下,高精度的运动轨迹和较小的振动响应,机构学界先后采用被动控制和主动控制两种方式抑制连杆机构的弹性振动。
被动控制具有成本低,易实现,无需外部能源,能够较好的抑制高频模态响应等优点,但对外界环境变化的适应性差,对低频模态的抑制效果有限,然而研究发现:
弹性连杆机构的低频模态对机构弹性振动响应的贡献较大。
随着材料科学的发展,含机敏材料机构的振动主动控制技术因其设计灵活、
效果显著、能满足特殊的控制要求等优越性而得到了广泛重视。
性连杆机构振动响应的控制研究中,给机构学界注入了极大的活力。
弹性连杆振动主动控制是基于一定的控制策略,根据对弹性连杆机构振动响应的测量信息,通过外界的能量输入对机构施加一定的控制力,使控制系统与机构本身构成同一整体,从而改变机构的动力学特性。
它涉及机构动力学、控制理论、材料科学以及作动传感技术的交叉学科,有着诱人的发展前景。
目前该领域的研究还处于理论研究和仿真计算阶段,开展实验研究的很少。
因此,根据实际弹性机构(粘贴或埋入传感材料和作动材料,包含阻尼材料、复合材料等)建立较为精确的非线性动力学模型,提高控制方法的警棒性‘实时性和自适应性,增强机构的抗振特性,已成为弹性连杆机构振动控制面临的一个堕待解决的问题,也是机械、航空航天及军事工业等领域设计良好产品必须解决的关键问题之一。
系统深入地开展这方面的研究,具有重要的理论意义和实际应用价值。
第二章.四连杆机构介绍
2.1基本概念
平面四连杆结构是由四根杆件(图2-1)1、2、3、4借助于转动副(2-1中的A,B,C,D)依次连接(铰销连接)而成,每个铰销的轴都互相平行,从而使活动杆件都在互相平行的平面上运动。
在四根杆件中,不论把那根杆件作为基架(固定杆或基杆),而把另一杆作为原动杆,那么其余的活动杆都作一定的强制运动。
因此平面四连杆运动链在选定了固定杆和原动杆之后,就构成了平面四连杆机构。
此外,又由于转动副属于V级的低副,所以平面四连杆机构时属于低副的平面机构。
22平面四杆机构的基本特性
2.2.1曲柄存在条件(格拉肖夫条件)
1最短杆与最长杆长度之和小于或等于其余两杆长度之和;
(杆长之和条件)
2连架杆与机架中必有一杆为最短杆。
(最短构件条件)
图2-2曲柄摇杆机构
图2-2曲柄摇杆机构中,设各杆长度依次为丨1、丨2、丨3、丨4,且丨1<
14。
假定AB为曲
柄,则曲柄AB回转一周过程中,必有两次与连杆BC处于共线。
据三角形两边之和大于第三边的定理,由△ACD有
I3+|4>
|l+l2
由厶AGD有
l2-|l+l4>
|3
l2-ll+l3>
l4
将上列三式整理,并考虑到四个杆件同时共线的情况,可得
ll+l2Wl3+14
ll+l3Wl2+l4
ll+l4Wl2+I3将上三式两两相加,化简得liWl2
IiWl3
liWl
在铰链四杆机构中,能作整周回转的连架杆称为曲柄。
而曲柄是否存在。
则取决于机
构中各杆的长度关系,即要使连架杆能作整周转动而成为曲柄,各杆长度必须满足一定的条
件,这就是所谓的曲柄存在的条件。
2.2.2急回特性及行程速比系数K
①机构的急回运动特性:
曲柄等速转动时,摇杆往复摆动的平均速度不相同,反行程的平均速度较快,这种运动
称为曲柄摇杆机构的急回运动特性。
如下图2-3所示
图2-3四连杆急回特性
曲柄摇杯机构中,当曲柄AB沿顺时针方向以等角速度转过01时,摇杆CD自左极限位置C1D摆至右极位置C2D,设所需时间为t1,C点的明朗瞪为V1;
而当曲柄AB再继续转过02时,摇杆CD自C2D摆回至C1D,设所需的时间为t2,C点的平均速度为V2。
由于01>
02,所以t1>
t2,V2>
VI。
由此说明:
曲柄AB虽作等速转动,而摇杆CD空回行程的平均速度却大于工作行程的平均速度,这种性质称为机构的急回特性。
摇杆CD的两个极限位置间的夹角“称为摇秆的最大摆角,主动曲柄在摇杆处于两个极限
位置时所夹的锐角0称为极位夹角。
他们之间的关系如表2-1所以
表2-1参数关系
曲柄棘常
曲柄转連
所需时闻
揺軒C点平均速度
工柞
Q)
込耳
回程
人二护/如
②行程速度变化结奧比鞍
〔糸数K
相等
-180oZe
好的传力性能,应控制机构的最小传动角
丫min。
一般可取丫min》40°
重载高速场合取
丫min>
50°
。
曲柄摇杆机构的最小传动角出现在曲柄与机架共线的
两个位置之一,如图所示的B1点或B2点位置。
图2-4四连杆压力角和传动角
偏置曲柄滑块机构,以曲柄为主动件,滑块为工作件,传动角丫为连杆与导路垂线所
夹锐角,如图所示。
最小传动角丫min出现在曲柄垂直于导路时的位置,并且位于与偏距方
向相反一侧。
对于对心曲柄滑块机构,即偏距e=0的情况,显然其最小传动角丫min出
现在曲柄垂直于导路时的位置。
对以曲柄为主动件的摆动导杆机构,因为滑块对导杆的作用力始终垂直于导杆,其传动
角丫恒为90°
即丫=丫min=丫max=90°
表明导杆机构具有最好的传力性能。
2.2.4死点
曲柄摇杆机构中,若以摇杆为原动件,当连杆与从动件(曲柄)共线时的位置称死点位
置。
这时机构的传动角丫=0,压力角a=900,即连杆对从动曲柄的作用力恰好通过其回转中
心A,不能推动曲柄转动。
机构的这种位置称为死点。
机构在死点位置时由于偶然外力的影
响,也可能使曲柄转向不定。
死点对于转动机构是不利的,常利用惯性来通过死点,也可采
用机构错排的方法避开死点。
图2-5四连杆死点位置
出现死点的利弊
利:
工程上利用死点进行工作如快速夹具、飞机起落架等。
图2-6死点的利用
弊:
机构有死点,从动件将出现卡死或运动方向不确定现象,对机构传动不利。
图2-7死点的弊端
第三章四连杆机械振动的特性
在利用四连杆的机械设备进行加工过程中的振动会恶化加工表面质量,损坏切削刀具,
降低生产率。
本文着重介绍振动的两种类型,振动产生的原因及消除方法。
机械加工中的振动对加工表面品质和生产率有很大的影响,是一种十分有害的物理现
象。
若加工中产生了振动,刀具与工件间将产生相对位移,会使加工表面产生振痕,严重影
响零件的表面品质和性能;
振动使刀具受到附加动载荷,加速刀具磨损,有时甚至崩刃;
同
时振动使机床、夹具等的连接部分松动,从而增大间隙,降低刚度和精度,缩短使用寿命,
严重时甚至使切削加工无法继续进行;
振动中产生的噪声还将危害操作者的身体健康。
为减
小振动,有时不得不降低切削量,使机床加工的生产效率降低。
因此,研究分析机械加工中
的振动原因和特性,寻求控制振动的有效途径是很有必要的。
3.1机械加工振动的表现和特点
振动分强迫振动和自激振动两种类型。
具体表现和特点如下。
3.1.1强迫振动强迫振动是物体受到一个周期变化的外力作用而产生的振动。
如在磨削过程中,由于电动机、高速旋转的砂轮及皮带轮等不平衡,三角皮带的厚薄或长短不一致,油泵工作不平稳等,都会引起机床的强迫振动,它将激起机床各部件之间的相对振动幅值,影响机床加工工件的精度,如粗糙度和圆度。
对于刀具或做回转运动的机床,振动还会影响回转精度。
强迫振动的特点是:
1强迫振动本身不能改变干扰力,干扰力一般与切削过程无关(除由切削过程本身所引起的强迫振动外)。
干扰力消除,振动停止。
如外界振源产生的干扰力,只要振源消除,导致振动的干扰力自然就不存在了。
2强迫振动的频率与外界周期干扰力的频率相同,或是它的整倍数。
3干扰力的频率与系统的固有频率的比值等于或接近与1时,产生共振,振幅
达到最大值。
此时对机床90_T_过程的影响最大。
4强迫振动的振幅与干扰力,系统的刚度及阻尼大小有关。
干扰力越大、刚度及阻尼越小,则振幅越大,对机床的加工过程影响也就越大。
3.1.2自激振动
自激振动是由振动系统本身在振动过程中激发产生的交变力所引起的不衰减的振动,就
是0激振动。
即使不受到任何外界周期性干扰力的作用,振动也会发生。
如在磨削过程中砂轮对工件产生的摩擦会引起自激振动。
工件、机床系统刚性差,或砂轮特性选择不当,都会使摩擦力加大,从而使自激振动加剧。
或由于刀具刚性差、刀具几何角度不正确引起的振动,都属于自激振动。
自激振动的特点是:
1自激振动是一种不衰减的振动。
振动过程本身能引起周期性变化的力,此力可从非交
变特性的能源中周期性地获得能量的补充,以维持这个振动。
2自激振动频率等于或接近系统的固有频率,即由系统本身的参数决定。
3自激振动振幅大小取决于每一振动周期内系统获得的能量与消耗能量的比值。
当获得的能量大于消耗的能量时,则振幅将不断增加,一直到两者能量相等为止。
反之振幅将不
断减小。
当获得的能量小于消耗的能量时,自激振动也随之消失。
3.2振动产生的原因分析
产生振动的原因复杂多变,根据机加工行业出现的振动现象及两种不同类型振动的表现形式,分析原因,大致如下:
3.2.1强迫振动产生的原因
1机床上回转件不平衡所引起的周期性变化的离心力。
如由于电机或卡盘、皮带轮回转不平衡引起的。
2机床传动零件缺陷所引起的周期性变化的传动力。
如因刀架、主轴轴承、拖板塞铁等机床部件松动或齿轮、轴承等传动零件的制作
误差而引起的周期性振动。
3切削过程本身不均匀性所引起的周期性变化的切削力。
如车削多边形或表面不平的工件及在车床上加工外形不规则的毛坯工件。
4往复运动部件运动方向改变时产生的惯性冲击。
如平面磨削过程的方向改变或瞬时改变机床的回转方向。
5由外界其他振源传来的干扰力。
在锻造车间附近,因空气锤的振动引起其他机床的强
迫振动,甚至共振。
3.2.2自激振动产生的原因
1切削过程中,切屑与刀具、刀具与工件之间摩擦力的变化。
2切削层金属内部的硬度不均匀。
在车削补焊后的外圃或端面而出现的硬度不均现象,常常引起刀具崩刀及车床自振现象。
3刀具的安装刚性差,如刀杆尺寸太小或伸出过长,会引起刀杆颤动。
4工件刚性差。
如加工细长轴等刚性较差工件,会导致工件表面出现波纹或锥度。
5积屑瘤的时生时灭,时切削过程中刀具前角及切削层横截面积不时改变。
6切削量不合适引起的振动,切削宽而薄的切削易振动。
3.3预防措施
3.3.1预防强迫振动的途径
强迫振动是由于外界周期性干扰力引起的,因此为了消除受迫振动,应先找出振源,然后采取适应的措施加以控制。
1减小或消除振源的激振力。
对转速在600r/min以上的零件如砂轮、卡盘、电动机转子等必须经过平衡,特别是高速旋转的零件,如砂轮,因其本身砂粒的分布不均匀和工作时表面磨损不均匀等原因,容易造成主轴的振动,因此对于新换的砂轮必须进行修整前和修整后的两次平衡。
提高齿轮的制造精度和装配精度,特别是提高齿轮的工作平稳性精度,从而减少因周期性的冲击而引起的振动,并可减少噪声;
提高滚动轴承的制造和装配精度,以减少因滚动轴承的缺陷而引起的振动:
选用长短一致、厚薄均匀的传动带等。
2调整振源频率。
避免激振力的频率与系统的固有频率接近,以防止共振。
采取更换电动机的转速或改变主轴的转速来避开共振区;
用提高接触面精度、降低结合面的粗糙度、消除间隙、提高接触刚度等方法,来提高系统的刚度和固有频率。
3采用隔振措施。
机床的电机与床身采用柔性联接以隔离电机本身的振动;
把液压部分与机床分开;
采用液压缓冲装置以减少部件
换向时的冲击;
采用厚橡皮、木材将机床地基隔离,用防振沟隔开设备的基础和地面的联系,以防止周围的振源通过地面和基础传给机床等。
3.3.2预防自激振动的途径
1合理选用刀具的几何参数
试验和理论研究表明,刀具的几何参数中,对振动影响最大的是主偏角Kr和前角丫0。
由于切屑越宽越容易产生振动,而Kr越小,切削宽度越宽,因此越易产生振动,前角丫0
越大,切削力越小,振幅也越小。
2提高工艺系统的抗振性工艺系统本身的抗振性能是影
响颤振的主要因素之一。
应设法提高工艺系统的接触刚度,如对接触面进行刮研,减小主轴系统的轴承间隙,对滚动轴承施加一定的预紧力,提高顶尖孔的研磨质量等。
加工细长轴时,使用中心架或跟刀架,尽量缩短镗杆和刀具的悬伸量,用死顶尖代活顶尖,采用弹性刀杆等都能收到较好的减振效果。
3采用减振装置
当采用上述措施仍然达不到消振的目的时,可考虑使用减振装置。
减振装置通常都是附加在工艺系统中,用来吸收或消耗振动时的能量,达到减振的目的。
它对抑制强迫振动和颤振同样有效,是提高工艺系统抗振性的一个重要途径,但它并不能提高工艺系统的刚度。
4调整振型的刚度比根据振型耦合原理,工艺系统的振动还受到各振型的刚度比以及其组合的影响。
合理调整它们之问的关系,就可以有效地提高系统的抗振性,抑制自激振动。
机械加工过程产生的振动非常复杂,是需要日常的不断分析和总结,根据不同情况分析原因,采取措施加以消除和控制,以保证加工工件的质量要求,提高生产率,创造良好工作环境。
第四章四连杆机械振动的控制策略
弹性连杆机构动态响应的消减始终是机器动力学的研究热点之一。
机构运动弹性动力学
(Kinetoelastodynamies,KED)理论提出后,学术界先后采取了以下几种方法,以抑制连杆
机构的弹性振动:
①优化构件的截面参数及几何参数,即KED综合。
②利用复合材料取代常
规金属材料。
③对构件进行阻尼处理,即阻尼减振。
④设计具有传感器与作动器的机敏机构,构造控制系统。
⑤设计具有多个可控原动件的受控机构,构造控制系统。
⑥基于完全动力分析的运动规划。
其中,方法①一③属于被动控制,方法④一⑥属于主动控制。
此外,综合运用主动、被动控制的混合控制方法,目前已成为振动工程一个新兴的研究方向,并已在柔性结构及柔性开链机构的振动控制中得到了应用。
4.1研究现状
4.1.1振动被动控制
4.1.1.1KED综合
量为设计目标的思想,并提出将动态运动误差限定在许用范围内的设计准则,把机构的截面参数作为优化变量,利用非线性规划的方法进行综合。
接着研究者借用结构设计领域的最佳性准则法,减少了优化的迭代次数,提高了KED综合的效率。
有研究者将结构分析的灵敏度
矩阵方法引人机构分析,对最佳性准则法进行了改进。
另一种KED综合方法是Erdran.AG
提出的以机构的弹性变形补偿动态轨迹误差的运动改善法,研究者FtnabashiH对该方法做
了不同程度的改进。
对于同时存在应力约束与运动误差约束的机构综合问题,研究者GrandinHT提出了一种优化设计方法,即利用最佳性准则法确定机构的截面参数以控制动应力;
以运动改善法对机构的几何参数进行微小调整,使机构的真实运动逼近期望运动,从而减小动态运动误差。
为避免共振,又有人提出了具有频率约束的弹性连杆机构优化设计方法。
应该指出采用KED综合方法,机构的低阶谐振现象难以根除。
4.1.1.2复合材料的应用复合材料的应用为高速弹性机构的设计提供了新的途径。
研究了由高分子复合材料构件
组成的弹性连杆机构的动态响应,利用复合材料高的比强度、比刚度与大的阻尼比有效地降低了机构的弹性振动。
可以预见,随着材料科学的发展与制造技术的不断完善,复合材料必将得到日益广泛的工程应用。
但就目前而言,由于碳纤维等复合材料的价格比较昂贵,一般工业领域还难以接受。
4.1.1.3阻尼减振由于应用粘弹性大阻尼材料对系统进行阻尼处理具有简单、可靠、价廉等优点,阻尼减
振技术已引起国内外学者的普遍关注。
阻尼处理通常有自由阻尼、约束阻尼两种办法,后者应用更为广泛。
对一高速曲柄摇杆机构的弹性连杆进行了约束阻尼处理,并对系统的动态响
应进行了数值分析。
结果表明,该方法可有效抑制弹性构件的高频振动。
但是,对于一般弹性机构,阻尼材料的结构形式、人方案、配置位置等还有待于进一步的研究。
4.1.2振动主动控制
近年,机构学界也借鉴了结构振动主动控制的思想,通过构造控制系统,为机构提供控制输人,最终使弹性构件的动态响应受到抑制。
振动主动控制方法具有修正设计方便、抑制低频振动效果显著、可适应未知扰动与参数不确定系统等优点,目前已在许多工程领域得到了成功的应用。
4.1.2.1机敏机构
机敏机构(Smartmeehanisms)是基于仿生思想的一种新型机构,是机构智能化发展的一个过渡阶段。
机敏机构可创成复杂的运动规律或运动轨迹,亦可用以改善机构的动力学品质。
学者SungCK以压电元件为作动器与传感器,对具有弹性摇杆的曲柄摇杆机构进行了振动主动控制。
学者ChenYC在摇杆中点的上下表面安装一对压电传感器,并在摇杆另外两点的上下表面对称安装两对压电作动器。
利用传感器的压电效应测定摇杆的动态应变,并由状态观测器估计系统的状态变量。
采用LQR理论设计状态反馈控制器,获得系统所需的控制电压,
即状态反馈电压与平衡刚体惯性力的前馈电压。
利用作动器的逆压电效应产生控制力矩,最终抑制摇杆的弹性振动。
用两片相同的压电陶瓷安装在弹性摇杆中点的上下表面,上片为作
动器,下片为传感器,有限元分析时计人了压电元件的影响。
上述两文献皆以降低弹性摇杆的一阶振动模态为目标,因此作动器安装位置较为合适。
控制规律上,将惯性力对系统状态的影响作为高斯白噪声处理,从而近似处理成LQG问题。
将压电薄膜贴于弹性构件的上下表
面分别作为作动器与传感器,采用与Chen.YC类似的方法对具有弹性连杆的曲柄滑块机构进
行了振动主动控制。
由于选用的压电薄膜压电系数较低,仿真中求得的控制电压峰值在千伏以上,给实际应用带来了困难。
上述文献的研究对象只含有一个弹性构件,故相当于对一个具有周期性载荷的简支梁进行了振动控制。
北京航空航天大学的张宪民应用独立模态空间控制理论,对含有多个弹性构件的开链、闭链机构的振动控制进行了研究,取得了较好的仿真效果,但试验研究没有开展。
天津大学的唐力伟基于LQR一LQG理论,深人研究了具有多个
弹性构件的曲柄摇杆机构的振动主动控制问题,并在试验研究方面取得了可喜的进展,曲柄转速为90r/nlin时,施控后机构输出点的动态响应降低了50%一70%。
天津大学的宋轶民以
具有压电作动器与应变传感器的平面弹性连杆机构为研究对象,系统地开展了基于神经网络
的弹性连杆机构振动主动控制的理论、方法与试验研究。
根据试验数据离线设计了神经网络辨识器与神经网络开环、闭环控制器,采用基于神经网络的直接自校正控制与间接自适应控制策略实现了机敏机构的在线控制,机构的动力学品质得到了显著改善。
此外,YuanSQ和
Zhang.L研究了基于内模控制的弹性机构振动主动控制问题,将机构视为5150线性系统,
视惯性力为结构已知的周期性扰动,将扰动信号的拉氏变换包含于闭环系统的传递函数之中,设计反馈控制器以抑制扰动引起的系统输出。
在试验研究方面,Thompson.BS率先以
压电陶瓷为作动器,以电阻应变计为传感器,采用输出比例反馈控制策略,对具有弹性连杆的曲柄滑块机构在曲柄转速为60、90及120r/min时进行了振动控制。
试验结果虽然没有仿
真效果理想,但弹性构件的动态响应确实得到了一定控制,振幅降低了近20%。
OliverJH基于多变量最优控制理论,以压电晶体作为作动器与传感器,对具有弹性连杆的曲柄摇杆机构进行了振动控制,取得了一定的试验效果。
目前,弹性连杆机构振动主动控制研究大多停留于理论分析与计算机仿真,开展的试验研究很少,仅有的几例试验研究控制效果都不理想。
试验研究中,弹性机构的原动件转速都比较低,和实际要求还相差较远。
4.1.2.2受控机构
近年,受控机构学方面的研究日益增多。
所谓受控机构,是指具有一个或多个可控原动件的闭链机构。
利用受控机构改善弹性连杆机构动力学品质的