产品部件生产加工工艺流程Word文档下载推荐.docx
《产品部件生产加工工艺流程Word文档下载推荐.docx》由会员分享,可在线阅读,更多相关《产品部件生产加工工艺流程Word文档下载推荐.docx(11页珍藏版)》请在冰豆网上搜索。
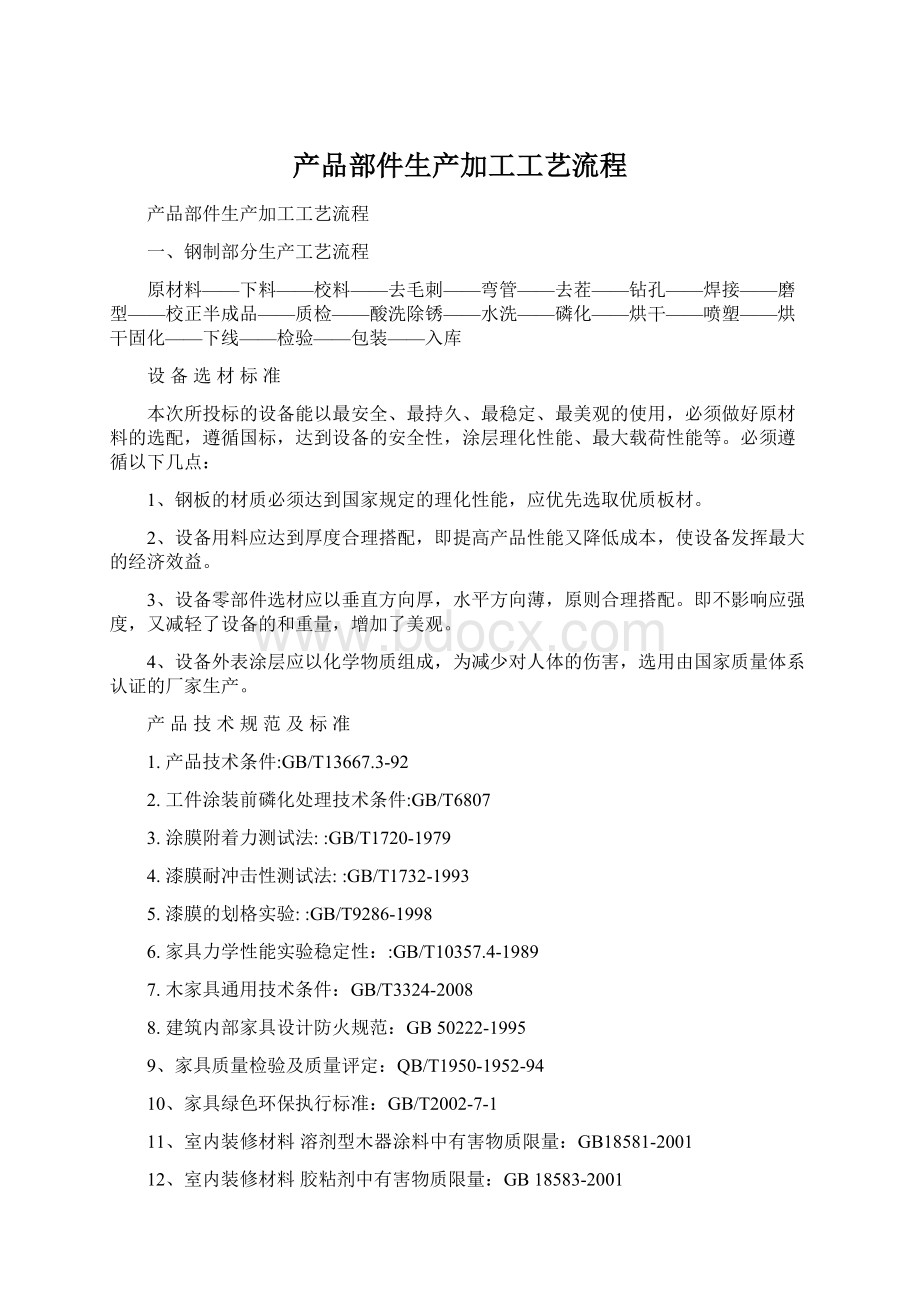
11、室内装修材料溶剂型木器涂料中有害物质限量:
GB18581-2001
12、室内装修材料胶粘剂中有害物质限量:
GB18583-2001
13、室内装饰装修材料、木家具中有害物质限量:
GB18584-2001
14、金属家具通用技术条件:
GB/T3325-1995
15、软体家具、沙发质量检验及分等综合评定:
QB/T1952-1-99
16、家具、桌、椅、凳类主要尺寸:
GB/T3326-1997
17、家具、柜类主要尺寸:
GB/T3327-1997
18、家具五金、拉手安装尺寸:
QB/T1241-1991
磷化喷塑工艺介绍
(一)、磷化
因钢板、钢管在制造和储运过程中,都加入有防护油,在生产成产品过程中其表面也都不可避免地沾有各种污物,如:
润滑油,金属氧化层,与人接触而带来的汗渍以及灰尘等。
这些污物的存在,对涂装工艺十分不利,并将最终影响涂层的内在综合质量。
本公司全自动9工位喷淋式前处理机组全长50米,就是为了清洗钢板上的各种污物和增强金属基体自身的防护能力,增加与涂层的结合力。
(磷酸盐处理)确保金属制品的综合质量和耐用性,保证产品达到国家《GB6807-86涂装腔作势前的表面处理技术落后要求》标准。
磷化工艺流程:
热水洗--预脱脂---脱脂---水洗--水洗表面---调整磷酸盐----处理水洗---纯水洗。
封闭式9工位前处理机组,能在一个全封闭的空间内自动连续完成工件的清洗、调整、磷化处理,克服了手工作业质量无稳定之弊端,保证了各种质量指标的稳定性和可靠性。
热水洗起到预先湿润工件上的固态油脂和浮锈以及洗掉工件上的灰尘,为工件清除出党洗彻底打下了基础。
预脱脂、脱脂。
在经过三工位的药液清洗(在喷淋的机械冲击和药物的双重作用下),能彻底清洗掉工件上的各种油脂和腐蚀物,温度由电子仪器自动跟踪检测,自动补偿,始终保证药液的工艺温度,确保清洗质量的稳定。
四和五工位为大小工位清洗。
工件经脱脂后,其表面带有的残留药液(碱),经中和清洗后为七工位的磷酸盐处理奠定了坚实的基础。
表面调整:
在脱脂处理中,对金属基本体表面的化学成分,物进性能在一不定的损坏。
为使钢铁有更高的物理性能和提高磷化膜的质量,利有胶体磷酸钛对磷化前的工件进行表面调整,使工件形成一层钛离子,使磷化膜致密,均匀,同时也提高了磷化速度。
磷酸盐磷化处理:
使用锌系磷化液,工件经磷化,涂装后的防腐,附着力耐氧化性更好,符合GB6807-86国家标准。
水洗、纯水洗:
工件经磷酸盐处理后,形成一层致密,均匀的磷化膜,但也带来了一定的磷酸盐残液,这将影响涂装后的质量。
经水洗掉残余的药液,但自来水也含有一定量的钙镁离子,沾附在工作的表面上,将会影响涂层的结合能力,所以用去离子纯水做最后的清洗,使工作的表面更清洁,使涂装后的工作综合质量更有保证,更可靠。
(二)、喷塑
我公司采用先进的静电喷塑工艺涂装,其原理是粉末在压缩空气的吸引下,经喷枪使之雾化,当雾化后的粉末经过由喷枪产生的高压负电场时,粉末粒子就均匀地捕集到大量的负电荷。
因工件是接地的,这样就形成了正负相吸的原理,在此原理的作用下,粉末就均匀的积聚在工件上。
工件进入烘干后,经熔化、流平、固化、降温、下架。
经检验合格后,本工序结束。
表面涂装工艺流程
序号
名称
说明
1
予脱脂
除油(自动)
2
脱脂
3
水洗
(自动)
4
表调
中和(自动)
5
磷化
表面处理(自动)
6
去除表面尘渣(自动)
7
8
燃油烘干
予处理(自动)
9
静电喷塑
表面涂装(自动)
10
燃油固化
固化流平(自动)
11
下件
产品工艺流程、技术规范
缺陷分析及检验标准
(一)、涂装前工件应符合一下列要求:
1、检测验工件无弯曲、翘曲现象。
2、冲压件表面无毛刺、裂痕。
3、处表焊缝应磨光,无焊潭、飞溅等现象。
(二)、涂装工艺流程
脱脂—水洗—除锈—水洗—表调—磷化—水洗—烘干—喷涂
(三)、涂装前处理配槽用量及管理标准
脱脂:
yp4358药剂0-100公斤总碱度18-22点
时间6—10分钟
水洗:
工业用水碱污染≤0.5水宜溢流时间1分钟
水洗后快速进行下道工序。
除锈:
yp5301药剂1000公斤总碱度450-500点
时间10-30分钟
工件起落不小于5次
表调:
ypA药剂6公斤ph值7.5时间1分钟
磷化:
yp3502药剂180公斤30-35点NaoH1.6公斤
FA0.6-1.5点yp131药剂6公斤AC3-5点
时间3-5分钟
工业用水质量中性不宜溢流时间1分钟
烘干:
温度不宜太高目的:
快速脱水,以便磷化膜进入稳定状态。
(四)、前处理药剂补加及浓度调整
除锈槽总酸度:
每补加药剂yp-530120公斤总酸度上升一个点。
磷化槽总酸度:
每补加yp-3502A药剂2-2.4公斤总酸度上升一个点,游离酸度每补加NaoH药剂0.12公斤FA下降0.1个点,每补加yp131药剂0.5公斤,AC上升1个点。
(五)、前处理技术规范
除油除锈时,一般低温进行,油、锈严重的,应提高温度并延长时间。
熔液使用一段时间后,分析Fe2+含量,若不超过20g/t可补加新液,超过120g/t时更抽象新液。
水洗时应除尽除锈液并快速进行下道工序。
加表调剂时,要在空气搅拌下缓慢加入,使用过程中PH≤7时,加Na2co2每处理1000M2工件,应补加yp-A药剂0.5-1公斤。
磷化时必须控制酸比TA30:
FA0.6,同时控制促进剂浓度3-5,并注意经常维护溶液清洁。
(六)、磷优膜的检验
外观检验:
检测工作磷化膜表面颜色呈现灰色到深灰色或采色,腊层结品致密、均匀、连续。
不应有表面严重挂灰,锈蚀或绿斑,磷化抗腐蚀性能检验。
点滴法:
用酒精控试磷化过工件表面,待挥发完后,在15℃--25℃下,滴上数滴硫酸铜溶液,(CHSO4.5H2O41g/1Nacl35g/lHcl13g/L三者混合使用),同时启动秒表,若在1分钟工件表面不泛红,说明磷化膜抗腐蚀性能合格。
经外观检验和抗腐蚀性能检验不合格的工件,需在除锈溶液中浸泡1-1.5分钟,在经水洗、表调后重新磷化。
(七)、工件磷化膜缺陷分析
工件产生锈膜原因,酸比低、水洗不净,空气中暴露时间过长或水污染严重等。
工件产生采斑原因,促进剂浓度高或分布不均。
工件产生黑条纹或磷化膜黑而粗糙原因,促进剂浓度低.
工件表面挂灰原因,糟液含渣量太多或糟液温度高,根据工件缺陷,应细心分析原因,补救时应按可能原因逐条排除。
(八)、表面喷涂(喷漆、喷塑)
经检验磷化膜合格的工件,必须在磷化后16小时对其表面进行喷涂(喷漆、喷塑)。
对特殊加工序及特殊零件可适当延长间隔的时间,但此期间内工件的表面不得被污染或重新锈蚀。
喷涂后工件,必须经红外线烤炉烘烤,烘烤温度在90-120度,时间不低于20分钟。
(九)、涂层的检验
目测平整光滑、色泽均匀一致;
不应有挂流、漏底、剥落、伤痕、皱皮等现象。
物理性能检验:
涂层应大于20um,涂层不应太厚,太厚既浪费材料又降低涂层的冲击强度,
涂层光泽度应为60%-70%,近似亚光。
涂层硬度大于0.4。
涂层冲击强度大于0.4gb.m
涂层附着力不低于2级。
抗腐蚀性能检验:
取样板7*1503件,用18号缝纫机针将少层划成12cm的交叉线(划痕深至钢铁基体,对角线步贯穿对角),划痕面朝上。
将样板隔开放入温度为15度、25度,溶液浓度3%NacL中,浸泡100小时。
100小时内,样板划痕两侧3mm以外无气泡产生。
100小时后样板划痕两侧3mm以外无锈迹、剥落、皱皮、变色等现象。
说明涂层抗腐蚀性能合格。
采购人可对本次产品的制作进行现场考察及对产品进行发货前的检测,本公司对采购人进行产品检测提供方便,我方在生产10组后,由采购人进行检验确认后,方能大规模进行生产,在生产开始后我方在每星期及时向采购人报送生产进度表,提供具体、真实、详细的生产数量、库存数量、发货数量等相关数字。
在供货期间,如果我方提供的产品质量不符合要求,采购人可拒绝支付货款,我方无条件调换符合质量要求的产品,如我方仍无法提供合格的产品,采购人和采购代理机构将有权取消其我方资格。
货物验收在货物到达安装地点后进行,验收时供需双方派员一起当场开箱验货,如发现货物短缺、质次、损坏、产地和规格不符等问题,应作详细记录,由我方立即无条件为需方调换或补齐,同时由我方承担因此而产生的一切后果。
安装的产品无刺激性气味,否则可一律退货。
投标产品全部安装完毕后,对全部产品进行检验。
二、木制部分生产工艺流程:
东北桦木—旋切—分类—烘干—(自然烘干、人工烘干)—再整理—铺装—高频热压—检验—加工(锯边—铣边—磨边)—再检验—抛光—油漆—验收—包装—入库
A、用料要求一般有以下几个标准:
1、木材含水≤8-12%
2、采用的树种质地应相似,针、阔叶材不得混合使用
3、虫蛀材须经杀虫处理
4、外表不得使用腐朽材,内部或封闭部位用材轻微腐朽,面积不超过零件面积的15%,深度不得超过材厚25%
5、外表及存放物品部位的用材不得有树脂囊
6、只要受力部位用材和斜纹程度超过20%的不得使用
7、节子宽不超过可见宽1/3,直径不超过12mm,经修补加工后来不影响产品结构强度或外观的可以使用
8、其他轻微材质缺陷,如裂纹等,应进行修补加工,不影响产品结构强度和外观的可以使用
9、各种木质零件不得有贯通、裂缝
B、木工要求一般有以下几个标准:
1、产品外表的倒枝、圆角、圆线应均匀一致
2、榫及自装配件、拆装产品零件结合应严密、牢固
3、塞角、拉屉条支承零件等的结合应牢固。
装板部件配合不得松动
4、启闭部件和配件应使用灵活
5、写字桌装有键盘托的,其安装应牢靠,击键时应稳固
6、各种配件,连接件安装应严密、平整、端正、牢固、结合处应无崩茬或松动,不得少件、漏钉、透钉。
7、车木的线条应基本一致,车削线条应清晰
C、外形尺寸极限偏差的标准要求:
:
1、宽的标准要求为±
5mm
2、深的标准为±
3、高的标准为±
D、主要尺寸的标准要求:
1、宽在1200mm-240mm范围内
2、深在60mm-1200mm范围内
3、中间净空高为≥580mm内
4、中间净空宽为≥520mm内
5、侧柜抽屉内宽为≥230mm内
E、状和位置公差的标准要求:
1、翘曲度在≤3.0mm内
2、邻边垂直度、柜架≤3.0mm内
3、条面的邻边垂直度为≤2.5mm内
4、底脚平稳性在≤2.0mm内
5、平整度在≤2.0mm内
6、门与柜架、门与门的位差度在≤3.0mm内
7、抽屉与柜架、抽屉与门、抽屉与抽屉的位差度在≤2.0mm内
8、抽屉的分缝必须≤2.0mm
9、抽屉的摆动度须≤15mm内
F、涂饰标准要求:
1、整件产品或成套产品色泽应相似
2、产品表面漆膜不得有皱皮,发粘和漏漆现象
3、正视面涂层应光滑平整、清晰;
漆膜实干后应无明显木孔沉陷;
其他部位涂层手感应光滑,无明显粒子;
漆膜实干后允许深陷,允许有小涨边和不平整,涂层应无明显加工痕迹、划痕、雾光、白楞、白点、鼓泡、油白、流挂、缩孔、刷毛、积粉和杂渣
4、软、硬质覆面表面纹理、色泽应相似,不允许有皱皮、裂痕、划伤、崩角和刃口
G、力学性能的标准要求:
1、相关性零件部件不应断裂和豁裂
2、用手揿压某些应为牢固的部位时不应出现永久性松动
3、零件不应出现影响使用功能的损坏或变形
4、螺钉或五金连接件不应松动
5、活动部位应灵活
附:
一个产品达到上述标准后,另外,还有注意抽屉结构强度,抽屉滑轨强度、移门和倒向启闭卷门的耐久性、移门和侧向启闭的猛开,以上这些项目的外移与功能是否完好。
真皮沙发类:
针对这类产品的国家一般依据为:
GB/T1952-94《软体家具沙发质量检验及分等综合评定》。
制定原则:
基本项目均应合格:
分效项目均达到C级以上;
一般项目中允许存在1项B类不合格和1项C类不合格,或3项C类不合格,判为合格品,否则,判为不合格品。
一般从以下几个方面检验;
H、主要尺寸技术要求:
1、单人位宽≥480mm
2、双人位宽≥1440mm
43、三人位宽≥1960mm
4、座深在480mm-660mm内
5、座前高在360mm-420mm内
6、扶手高≤250mm
7、木制件工艺结构的结合处不能松动或断痕
8、木制件的漆膜表面不得有粘漆
9、木制件的外表用材不得使用虫蛀、腐朽、节子、树脂囊等到木材且斜纹不超过20%
10、木制件的内部用材、虫蛀材须经杀虫处理,不能有昆虫尚在侵蚀木材
11、装饰性零件必须牢固无松动
12、金属件必须安装牢固,且无明显毛刺和刃口
13、金属配件和弹簧应作防锈处理
14、木制件的漆膜必须无裂缝、鼓泡、失光、变色现象等
15、衬垫料的棕丝要干燥,且一定要达到国家卫生标准,不能使用不卫生的杂物和损伤人体安全的物质,且不能使用旧料和霉烂变质的衬垫料
16、产品的标志必须明显,要有出厂产品商标或厂标。
Ⅰ、面料缝纫及外观的技术要求:
1、拼接面料图案完整,连续绒面的绒方向要一致
2、面料必须无明显色差、残疵点,且不允许有色污、油污、面料划伤现象
3、嵌线圆滑挺直
4、不能有跳针、外露鞋钉、泡钉间距基本相等,排列整齐无松动脱落,明显敲扁、毛刺、脱漆
J、木制作漆膜涂层外观要求:
1、漆膜平整、手感光滑、色泽均匀
2、无明显流挂、鼓泡、皱皮、漏漆、涨边、过楞、白点、刷毛现象
3、涂漆部位边沿无刃口、毛刺现象
4、木制件漆膜耐磨性为2000转
K、座背耐久性技术要求:
1、中凹形弹簧加载:
A级:
90000次、B级:
50000次、C级:
30000次
2、加载后无断簧、断绳、面料破损现象
3、座面弹簧加载:
60000次、B:
级40000次、C级:
20000次
4、加载后无断簧、断绳、面料破损现象
5、且必须无垫料移位、托簧档、托簧带松动或拆断、脚轮损坏现象等
L、木制件结构工艺结构技术要求:
1、出本部件、纹理、颜色相似
2、外表细光
3、外表倒棱、圆角对称、均匀
4、车木线型一致,凹凸台阶匀称,对称部位对称、车崩线条清晰,加工表面无崩茬、刀痕或砂痕会议椅类:
我公司的会议椅检验依据为:
GB/T2280-96《转椅》,一般可分以下几个方面检验:
M、主要尺寸的技术要求:
1、扶手内宽≥440mm
2、座前宽≥360mm
3、座深在340mm-540mm内
4、最低座面高在340mm-440mm之间
5、升降行程≥60mm
7、背高≥275mm
N、形状和位置的公差技术要求:
1、椅背偏心度≤140mm
2、外形对称度≤6mm
3、座面水平偏差≤6mm
4、着地平稳性≤2mm
O、用料的技术要求:
1、底座软质泡沫塑料的密度≥25kg/m3
2、底座软质泡沫塑料的抽伸强度≥85kg/m3
3、其他部位软质泡沫塑料≥22kg/m3
4、木材的含水率一般不高于(产品所在地区年平均木材平衡含水率15-1万加1.0万)
P、管材和冲击件的技术要求:
1、不允许有裂缝、脱层
2、无裂缝、无错位、无结疤、弯曲处圆滑一致,无波纹、冲压件平整
Q、工程塑料构建的技术要求:
1、牢固无裂口
2、工程塑料光滑、无气泡、无明显杂质、无波纹、无凹陷、颜色均一等
R、焊接的技术要求:
1、牢固无虚焊、漏焊、焊穿现象等
2、表面波纹高低≤1mm、无气孔、无夹渣、无焊瘤、无咬边、无飞溅、无焊丝头出现象
S、安全性能的技术要求:
1、不允许有刃口、,毛刺、固定装置牢固可靠
T、软包装及缝纫的技术要求:
1、外形饱满、圆滑一致
2、对称部位对称
3、缝纫线迹均匀
4、无明显浮浅跳针、嵌线圆滑挺直
5、图案清晰、色泽一致
U、其他一些技术要求:
1、装配性连接可靠,不轻易松脱、无防脱落处理
2、升降机构和角度调节机构的技术要求,即为机构升降灵活、配合良好、平稳、无漏气、无噪音
3、脚轮的转动、手动轻快灵活,无破损、连接牢固
4、金属配件必须做防锈处理
5、漆膜涂层的外观无露底、无凹凸、无麻点、无皱皮、无色差、无漏涂、无明显流挂、无划痕、无飞漆且图案完整、无返锈、粘漆等
6、镀层的外观无烧焦、无起泡、无针孔、无裂纹、无花纹、无划痕、无明显毛刺、无雾光、无露底、返锈、剥落现象等
7、椅座加载1300N必须可试10次无损,椅背加载560N必须可试10次无损
8、跌落高度为200mm时,试10次无损坏现象
9、回转频率为10-15次/mm、回转次数30000次必须无损坏现象,脚轮磨损的技术要即为:
在座面垂直加载600N时回转行程5kg时必须无损坏现象