落料拉深复合冲压模具课程设计Word文档格式.docx
《落料拉深复合冲压模具课程设计Word文档格式.docx》由会员分享,可在线阅读,更多相关《落料拉深复合冲压模具课程设计Word文档格式.docx(10页珍藏版)》请在冰豆网上搜索。
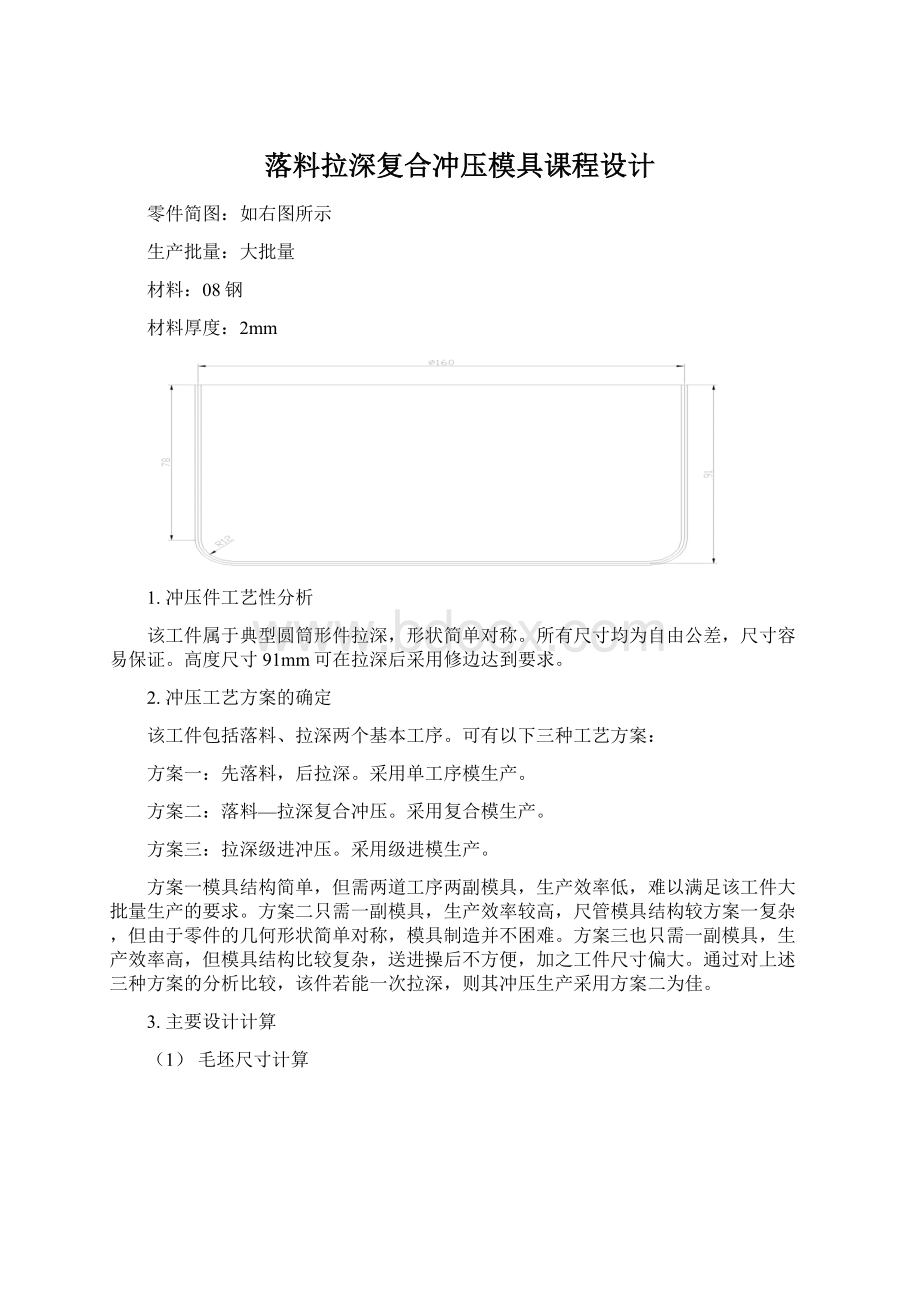
方案三也只需一副模具,生产效率高,但模具结构比较复杂,送进操后不方便,加之工件尺寸偏大。
通过对上述三种方案的分析比较,该件若能一次拉深,则其冲压生产采用方案二为佳。
3.主要设计计算
(1)毛坯尺寸计算
根据表面积相等原则,用解析法求该零件的毛坯直径D
D=√ ̄(d2*d2+4*d2H-1.72rd2-0.56r*r)
D=√ ̄(160*160+4*160*91-1.72*12*160-0.56*12*12)
D=283.65mm
(2)排样及相关计算
采用有废料直排的排样方式,相关如下示
冲裁件面积A=∏*D*D/4=∏*283.65*283.65/4
=63159平方毫米
条料宽度B=D+2a+C=283.65+2*1.8+1=288.25mm
a——侧搭边值,查冲压教程表2.5.2得最小侧搭边值a=1.8mm
c——导料板与最宽条料之间的间隙,其最小值查冲压教程表2.5.5得c=1
步距s=D+a=283.65+1.5=285.15mm
式中a1——工件间搭边值,查冲压教程表2.5.2得a1=1.5mm
一个步进距的材料利用率∩=A/BS*100℅
∩=63159/288.25*285.15*100℅
∩=76.8℅
式中:
A——一个步距内冲裁件的实际面积
B———条料宽度
S———步距
(3)成形次数的确定
该工件为简单圆筒形拉深件,求出拉深相对高度H/h=91/160=0.57。
毛坯相对厚度t/D*100=2/283.65*100=0.71
查冲压教程表4.4.3发现h/dmin等于表中数值,能一次拉深成形。
所以能采用落料拉深复合冲压。
(3)冲压工序压力计算
该模具拟采用正装复合模,具体冲压力计算如下:
落料力F落料=KLtTb
L——冲裁周边长度;
L=
T——材料厚度;
t=2mm
Tb——材料抗剪强度;
Tb查机械工业出版社《实用模具技术手册》表1-1
K——系数,K取1.3
所以,F落料=1.3*890.66*2*304=703977.66N
拉深力F=∏dtGK1
式中t——板料厚度;
D——拉深后的工序件直径;
G——拉深件材料的抗拉强度,查《使用模具技术手册》,表1-1,G=255~353MPa,综合考虑取G=304MPa;
K1——修正系数,查冲压教程得K1=
F拉深力=3.14*160*2*382*0.93=356965.25N
压边力Fy=∏[D*D-(d+2rA)*(d+2rA)]P/4
式中,rA——拉深凹模的圆角半径,
P——单位面积压料力,查教程表4.4.5,取P=2.3mm
所以,Fy=∏[283.65*283.65-(160+2*12.58)*(160+2*12.58)]*2.3
Fy=83365.52N
冲压工艺总力Fz=F落料+F拉深力+Fy=1144308.43N
根据冲压工艺总力计算结果结合工件高度,初选开式双柱可倾压力机
(4)工件部分尺寸计算
落料和拉深的凸、凹模的工作尺寸计算见下表所示。
尺寸及分类
凹凸模间双面间隙
尺寸偏差与磨损系数
计算公式
结果
备注
落料
直径257.3
查教程表2.3.3得Zmax=0.360mm
Zmin=0.246mm
⊿=1.3
X=0.5
DA=(Dmax-X⊿)0+⊿
256.650+0.032
1.落料件精度等级IT14.
2.模具制造公差是查教程表2.4.1所得,满足⊿A+⊿T≦(Zmax-Zmin
DT=(DA-Zmin)-⊿0
256.4-0.0520
拉深
直径160
查教程表4.8.2得Z=2mm
⊿=1
DA=(Dmax-0.75⊿)0+⊿
159.250+0.025
模具制造公差是查教程表4.8.3所得
DT=(DA-Z)-⊿0
157.25-0.040
4.模具的总体设计
(1)模具类型的选择
由冲压工艺分析可知,采用复合模冲压,所以模具类型为落料-拉深复合模。
(2)定位方式的选择
因为该模具使用的是条料,所以导料采用导料板,送进步距控制采用挡料销。
(3)卸料、出件方式的选择
模具采用固定卸料,刚性打件,并利用装在压力机工作台下的标准缓冲器提供压力力。
(4)导向方式的选择
为提高模具寿命和工件质量,方便安装调整,该复合模采用中间导柱的导向方式。
5.主要零部件设计
(一)工作零件的结构设计
由于工件形状简单对称,所以模具的工作零件均采用整体结构;
凸凹模、落料凹模、拉深凸模的结构分别如下图示:
(1)凸凹模设计
1)凸凹模结构如图示
2)凸凹模个段尺寸设计
由前面计算可知第一段D1=256.400-0.052
d1=159.25+0.0250
式中H——拉深件工件高度
h——拉深件的修边余量,查教程表4.3.1得h=
t——板料厚度
h——增加高度,为确保推件器在拉深凹模内的准确定位,应增加一高度h=5mm
所以L1=91+3+2+5=101mm
第二段D2=(D1+4)0-⊿
D2=(256.40+4)0-0.032
D2与凸凹模固定板采用过渡配合,选用IT6,查《公差配合》表2-4得:
⊿=0.032
D2=260.40-0.032
L2=H+⊿h+t=91+3+2=96mm
第三段:
该段的凸缘部分起固定凸凹模,防止松脱的作用,因此,凸缘高度L3可选6mm
凸缘直径D3=D2+10=260.4+10=270.4mm
退刀槽尺寸,选2X1.5mm
3)凸凹模强度较核
凸凹模最小壁厚g=(D2-4-d2)/2=46.57mm
查《模具设计与制造简明手册》表1-209可知:
g大于凸凹模允许最小壁厚,所以强度满足。
(2)拉深凸模设计
1)拉深凸模结构如图示
2)拉深突模各段尺寸的设计
第一段:
由前面计算可知d1=157.25-0.040
L-l2=H+⊿h+t=96mm
r=(0.7~1.0)rA,式中rA由前面计算得rA=12.58,在此取r=0.8rA。
所以:
r=0.8X12.58=10.06mm
第二段:
d2设计比d1大4mm与拉深突模固定板采用国度配合,d2公差选IT6。
所以:
d2=(d1+4)-⊿0
查《公差与配合》表2—4得g=0.025
d2=(d1+4)-0.0250
d2=(157.25+4)-0.0250
d2=161.25-0.0250
d3=d2+10=161.25+10=171.25mm
L3=6mm
透汽孔选D=6mm
(3)落料凹模设计
1)落料凹模结构图:
由前面计算可知:
d1=256.650+0.032
式中b—凹摸刃口的最大尺寸(mm);
K—系数,查教程表2.9.5得K=0.15
H总=0.18*256.65=46.2mm
凹模壁厚c=(1.5~2)H总,在此选c=2H总=2*46.2=92.4mm
D=d1+2c=441.45mm
h=H+t
H—拉深高度;
T—板料厚度;
h=91+2=93mm
(二)此他零件的设计与选用
(1)弹性元件的设计
顶件块在成型过程中一方面起压边作用,另一方面还可以将成型在拉深成型后包在拉深突模上的工件卸下。
其压力由标准缓冲器提供。
(3)模架及其它零部件的选用
模具选用中间导柱标准模架,可以承受较大的冲压力。
为防止装模时上模吴转180度装配,将模架中导柱与导套作成粗细不等。
导柱d/mmXl/mm分别为直径50X300,直径55X300;
导套d/mmXl/mmXD/mm分别为:
直径56X160X63;
直径55X160X63;
上模座厚度取55mm,即H上模=55mm;
上垫板厚度取20mm即H垫=20mm;
固定卸料板厚度取15mm即H卸=15mm;
下固定板厚度取46.2mm即H下固定=15mm;
下模座厚度取65mm即H下模=65mm;
下垫板厚度取10mm即H下垫板=10mm;
模具闭合高度:
H闭=H上模+H垫+H凸凹模+H凹模+H下固定+H下模+H下垫板-H入
H闭=55+20+197+46.2+30+10+65-93=330.2mm
可见该模具闭合高度小于所选压力机的最大装模具高度,可以用。
6.模具总装配图
由以上设计,可得到如下图所示的模具总装配图。
为了实现先落料,后拉深,应保证模具装配后拉深突模的端面比落料凹模端面低2mm。
7.模具的装配。
模具的装配选用凸,凹模为基准件,先装上模,在装下模。
具体就是要根据模具的特点和技术条件,以一定的装配的顺序和方法,将符合图纸技术要求的零件,经协调加工,组装成满足使用要求的模具。
在装配过程中,即要保证配合零件的配合精度,又要保证零件之间的位置精度,对于具有相对运动的零件,还必须保证它们之间的运动精度。
因此,模具装配是最后实现冲模个冲压工艺意图的过程。
是模具制造过程中的关键工序。
模具装配的质量直接影响工件冲压质量,模具的使用和模具寿命。
具体要求是:
a模架精度应符合标准。
b装配好的冲模,上模沿导柱上,下滑平稳,可靠。
c凸凹间隙符合图纸规定的要求,分布均匀。
凸模或凹模的工作行程符合技术要求条件的规定。
d定位和挡料装置的相对位置应符合图纸要求。
e卸料和顶出装置的相对位置符合设计要求。
f紧固装置应可靠。
g落料孔或出料槽应畅通无阻,保证制件或废料能自由排除。
h标准件应能互换。
紧固螺钉和定位螺钉与其孔的配合应正常,良好。
g模具应在生产的条件下进行实验,冲出的工件应符合设计要求。
具体它的工艺装配特点。
a选择装配的基准件。
b组件装配。
C总体装配。
E调整凸凹模间隙。
F检验,调试。
以上是该模具的装配要求。
8.模具的安装和调试。
在压力机上安装模具,是一项很重要的工作,它将直接影响到冲件的质量和安全生产。
因此,安装和调试模具不但要熟悉压力机和模具的结构性能。
而且要严格执行安全操作制度。
模具安装的一般注意事项有:
检查压力机的打料装置,将其暂时调到最高位置,以免在调整压力机闭和高度时没折弯。
检查模具闭和高度合和压力机闭和高度之间是否合理,检查下模顶竿和上模打赶杆是否符合压力机的除料装置的要求等等。
模具安装的一般顺序:
A根据冲模的闭合高度调整压力机滑块的高度,使滑快在下死点时其底面平面与工作台之间距离大于冲模的闭合高度。
B先将滑快升到上止点,冲模放在压力机工作台规定位置。
在将滑快停放在下止点,然后调节滑快的高度。
使其底面与冲模座上平面结束。
带有模柄的冲模,应使模柄进入模柄孔,并通过滑快上的压块和螺钉将模柄固定。
对于无模柄的大型冲模,一般用螺钉等将上模坐紧固杂压力机上,并将下模坐初步固定在压力机台面上。
C将压力机滑快上调3-5MM开动压力机,空行程1-2次。
将滑快停于下止点。
固定住下模坐。
D进行试冲,并逐步的调整滑快所需高度。
止到冲出合格品。
冲压模具设计与制造课程设计说明书
设计题目:
无凸缘筒形件的落料拉伸
模具的设计
系部名称:
材料工程系
班级:
模具043
姓名:
尹翠强
指导教师:
强书键
日期:
2007.03
河南机电高等专科学校
冲压模具设计与制造课程设计任务书
题目:
无凸缘筒形件的落料拉伸模
具的设计
内容:
(1)冲压工艺性的分析
(2)冲压工艺方案的确定
(3)毛坯尺寸的计算
(4)排样设计
(5)确定冲压类型及结构类型
(6)进行必要的计算
(7)模具的装配
(8)模具在试模的过程中出现的问题及调整的方法
(9)终结
(10)凹模的零件图
(11)上模座零件图
原始资料:
零件简图如下图所示