24电路Word文档格式.docx
《24电路Word文档格式.docx》由会员分享,可在线阅读,更多相关《24电路Word文档格式.docx(10页珍藏版)》请在冰豆网上搜索。
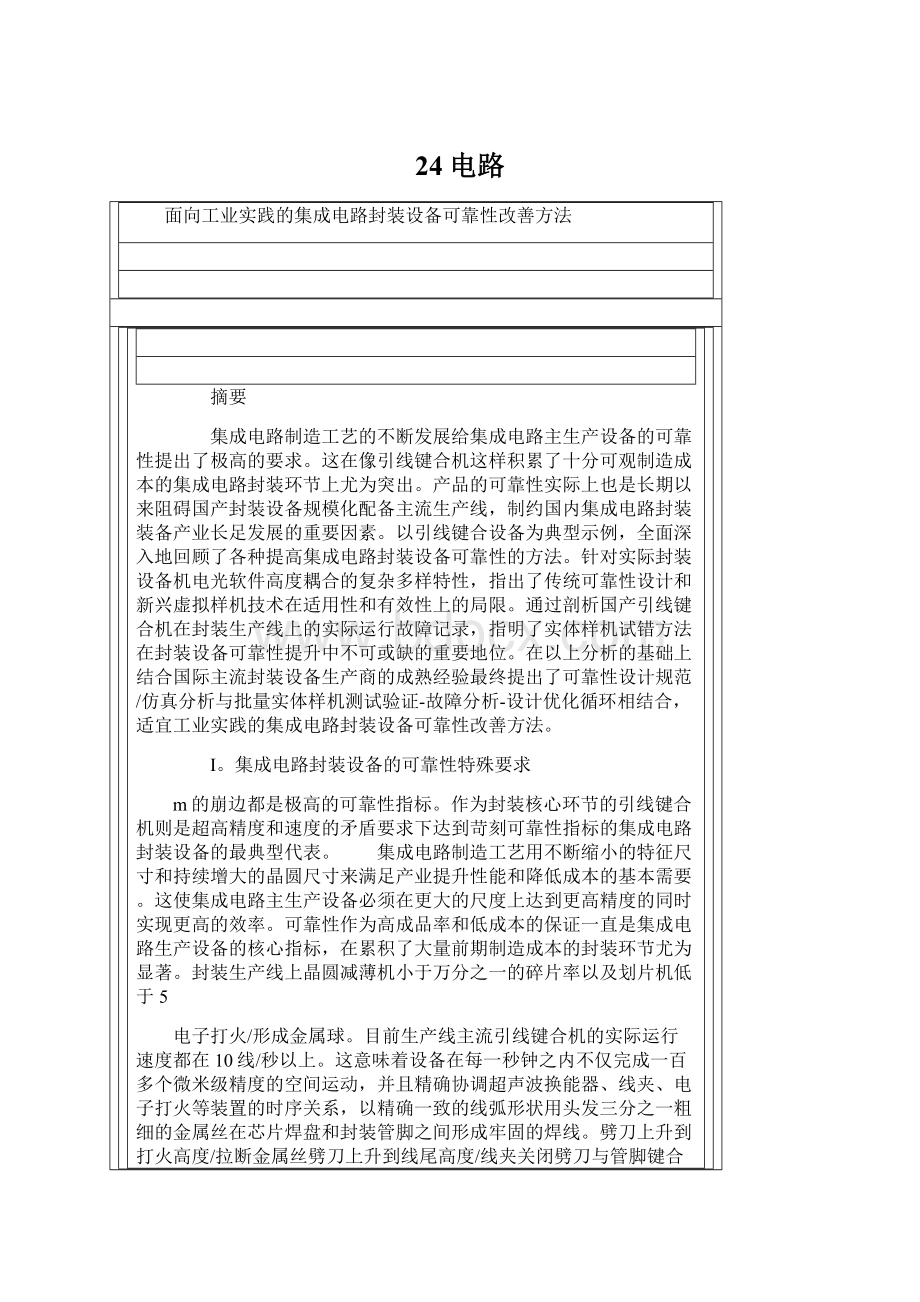
这意味着设备在每一秒钟之内不仅完成一百多个微米级精度的空间运动,并且精确协调超声波换能器、线夹、电子打火等装置的时序关系,以精确一致的线弧形状用头发三分之一粗细的金属丝在芯片焊盘和封装管脚之间形成牢固的焊线。
劈刀上升到打火高度/拉断金属丝劈刀上升到线尾高度/线夹关闭劈刀与管脚键合面接触/施加力和超声波/形成第二键合/线夹打开劈刀向下搜索键合面劈刀下降到搜索高度劈刀上升到弧长高度/线夹关闭劈刀与芯片键合面接触/施加力和超声波/形成第一键合劈刀向下搜索键合面 引线键合机完成集成电路封装中芯片与封装之间电气互连的核心环节。
图1显示了引线键合机在对应芯片焊盘和封装管脚之间用金属丝形成一根互连焊线的基本工艺过程,可以分为以下10个步骤:
劈刀下降到搜索高度
图1。
引线键合基本工艺过程
以上键合工艺过程是最为简化的基本线弧类型,实际生产中的线弧往往具有更多的单元运动和更加复杂的协同时序。
另外作为全自动设备必不可少的部分,机器视觉的图像采集-定位、物料传输的上料-分度-夹持-下料都必须高速、精密、可靠地运行以保证整个键合工艺的顺利完成。
根据国际领先设备生产商引线键合机产品MTBA(平均协助间时间,指设备无人工干预独立正常运行的平均时间)大于4小时,实际运行速度10线/秒以上估算,设备的键合故障率在十四万分之一以下。
也就是说,在设备持续高速精确焊线的过程中每完成十四万根引线还不能发生一次第一键失败、第二键失败及短尾等键合故障。
这样超高精度和速度下的极高可靠性几乎达到了机电设备的极限,对引线键合机的开发提出了前所未有的挑战。
设备的可靠性水平是用户选择的分水岭,直接决定着产品的市场定位。
当前引线键合机全球市场的格局清晰地印证着这一规律。
长期处于技术领先的美国K&
S的产品是行业内公认最为稳定可靠的设备,一直占据着高端集成电路市场。
全球的前几大封装企业如ASE(日月光)、SPIL(矽品)和ChipPAC(金鹏)等都和K&
S形成了非常稳固的采购关系,通常单一订单的数量达到200到500台之多。
国内代表性的封装企业如江苏长电和南通富士通等引线键合机也多数采购K&
S的产品。
香港ASM和日本Shinkawa(新川)、Kaijo等的产品近年来在技术上有很大进步,许多性能指标已经和K&
S十分接近,甚至成本和售价还低于K&
S。
而由于在可靠性上和K&
S还存在着相当的距离,这些公司产品的应用多数还局限于以LED为主的分立器件、低端集成电路或本国市场。
这也充分证明了产品可靠性是封装设备企业长期积累的产业化技术的集中体现,也是企业之间最难以跨越的差距。
目前国产引线键合设备的键合故障率徘徊在千分之一附近,和国外先进设备有着两个数量级的巨大差异。
在目前国产引线键合设备整机完成了从无到有的过程、关键技术取得了一定突破、性能指标逐渐接近进口设备的情况下,产品可靠性问题显得尤其突出和紧迫。
类似的情况也不同程度地体现在国产减薄机、划片机和粘片机等集成电路封装设备上。
可靠性问题是国产封装设备一直无法获得主流生产线批量订单的根本原因,是长期困扰国内封装设备行业的症结,是制约国内集成电路封装装备实现产业化的瓶颈。
可靠性问题是国产集成电路封装设备产业化道路上无法规避的严峻挑战,而在可靠性上填补与国际主流设备之间的巨大差距的任务较前期完成可行性样机的开发和实现单一关键技术的突破远为复杂和艰巨。
II。
传统可靠性设计
可靠性设计早已成为系统成熟的学科,可以对比较单一的对象例如机械零件/机构、电子元器件/电路板等提供系统有效的提高可靠性的途径。
增加安全裕度、冗余设计等常规设计方法被广泛地用来减小设计对象失效的可能。
基于概率论的串联和并联模型可以对简单系统进行可靠性建模和分析。
然而面对集成电路封装设备的复杂性和多样性,传统可靠性设计的方法显现出了极大的局限性。
首先,封装设备中存在着大量的多层次架构。
机械系统包括从零件到部件再到子系统最后到整机结构多个层次;
电气系统由元器件、电路板、功能模块、子系统逐级组成;
软件系统包括可编程器件程序、嵌入式模块程序、主控功能模块、主控程序等。
数量庞大、层级复杂的对象使针对单一机、电或软件系统采用传统可靠性设计方法进行逐级建模和分析已经十分困难。
而封装设备整机中机、电、软件系统密切耦合,多种物理量共存的状态就更是导致基于单一机械/电气物理量的传统可靠性设计方法几乎不可能有效准确地获得整机的可靠性估计。
其次,封装设备中大量采用来自主流厂商的零部件如电机/驱动、光栅尺、传感器、电磁阀、导轨、丝杠等。
对于这些缺乏详细准确的可靠性数据但已经具备很高可靠性的零部件没有必要也不便于进行传统意义上的可靠性分析。
传统可靠性设计方法在封装设备这些组成部分上没有意义。
最为重要的是,集成电路封装设备的可靠性问题更多地集中在设备的加工对象和工艺过程上,远远超越了传统意义上的一般设备失效模式的分析和预防。
也就是说问题的焦点已经不是设备本身的断裂、碰撞、形变、短路、击穿、过热等普通失效(这些问题已经在过去无数次的产品优化循环中得到了充分的解决),而是设备加工对象的完整性及工艺过程的正确和一致性。
相应地对设备可靠性指标的关注也由MTBF(平均故障间时间)向MTBA转移。
还是以最具代表性的引线键合机为例,在一根引线的焊接过程中即使所有的机械、电气和软件系统都运转正常甚至所有的空间运动和协同时序都准确无误,仍然可能因为高速运动下金属丝送线路径某一环节的微小偏差、引线框架夹持效果的变化或金属丝/键合面的轻微污染而导致第一键失败、第二键失败及短尾等键合故障。
这一类封装设备工艺的可靠性问题可以总结为一个极敏感的多参数过程的参数识别和优化的问题,满足可靠性要求的参数窗口极其狭窄。
这正是集成电路封装设备可靠性有别于传统设备可靠性的最突出特性,也是提高封装设备可靠性的挑战集中所在。
传统可靠性设计在这一挑战面前完全束手无策,因为即使出现了生产线上完全无法接受的工艺失效,绝大多数情况下在传统可靠性设计的意义上设备还是处于稳定可靠运行的理想状态。
III。
新兴虚拟样机技术
在过去的二、三十年当中,随着计算机软硬件的迅猛发展,仿真技术发生了革命性的变化。
有限元等数值分析方法的能量被充分解放出来,广泛地运用到各个领域并取得了显著的效果。
波音公司波音777飞机的全无纸化设计、生产和通用汽车公司用于碰撞实验的复杂精确全车虚拟模型都是充分利用仿真技术进行产品设计、分析和优化的代表性范例。
近年来以先进的仿真分析技术为基础提出了虚拟样机技术的概念,构建产品样机的完整数值模型并通过仿真分析进行系统的设计参数优化,在虚拟空间中形成设计-仿真-优化的完整闭环。
仿真技术在集成电路设备的设计当中也得到了广泛的应用以改善设备的可靠性。
图2左图显示引线键合机超声波换能器研制中使用有限元分析方法预测换能器的共振频率及相应模态形状,以此为依据进行设计优化来获得需要的共振频率、模态形状及振幅。
图2右图显示引线键合机底座的设计中有限元方法被用来估计底座的共振频率及相应模态形状,在此基础上实施结构优化来抑制可能发生的有害振动。
图2。
引线键合设备设计优化中仿真技术的应用
图3左图显示美国NovellusSystems公司在晶圆传输机械手的开发中运用有限元分析方法计算晶圆和真空吸盘形变下压力的分布以确保吸盘有足够吸力的同时尽量减小晶圆的负荷[1]。
图3右图显示Novellus在反应室的研制中采用非线性有限元方法求解晶圆在基座上冷却过程中的温度和应力分布以保证晶圆的应力水平在可接受的范围内[1]。
图3。
NovellusSystems集成电路生产设备设计中仿真技术的应用
图4左图显示引线键合机运动控制算法的开发中采用的一种脱离实体设备和运动控制卡独立运行的算法实时仿真调试方法,图4右图是仿真调试方法计算出的运动控制算法控制下设备工作台的各项运动参数[2]。
实时仿真调试方法有助于提高复杂控制算法脱机实时调试的效率,显著缩短了算法开发的周期。
图4。
引线键合设备运动控制系统设计中仿真技术的应用
仿真技术确实在集成电路设备的开发当中发挥了重要的作用。
对于局部、单一的零件或简单系统,有限元等数值方法可以就其关键特性进行准确的预测,从而为提高设备的可靠性提供依据。
然而与传统可靠性设计方法类似,集成电路封装设备的复杂性和多样性给新兴虚拟样机技术设置了很大的局限。
首先,数值分析方法在针对单一、连续、完整的对象时能够获得有效的结果,而对于存在着多个不同对象间交互作用的场合却很难处理。
以机械系统为例,有限元方法可以准确有效地计算单一零件如XY工作台滑块的共振频率、模态形状等动态特性,但滑块与导轨、滚柱和底座等一起组成XY工作台系统时,对系统动态特性的预测却有很大的困难。
导轨和滚柱之间的界面是问题的焦点。
界面间动态的应力应变及接触发生/脱离判断都是难于求解的典型非线性问题,整个工作台系统的动态特性分析是一个数值方法难以有效解决的复杂柔性多体动力学问题。
在实际仿真分析应用中经常采用一些简化的处理方法来缓解界面分析的难度。
预载条件下导轨和滚柱之间的界面作为高刚度、压缩状态下的弹簧来建模。
在一些理想状态下处于面接触的界面,例如引线键合机超声波换能器变幅杆和劈刀间的界面,有限元分析中通常采用将分析对象结合成为一个连续的整体从而消除对象间界面的处理方法。
这样的简化方法不仅一些仿真模型的关键参数,如代表导轨界面的弹簧的刚度,需要从实体样机中实测获得,而且分析结果最终的准确性也需要实体样机的确认,大大削减了仿真分析方法在不建造实体样机的前提下为设计提供依据的意义。
其次,目前仿真分析方法的有效和成熟性主要局限在单一物理场的范围内。
在单一的固体力学、热学、电磁学和流体力学等物理场中都形成了一套系统完整有效的建模和求解的方法,而多种物理场并存的耦合问题仍然是极大的挑战。
集成电路封装设备整机中机械、电路、光学、电磁等多种物理系统高度集成和紧密交互的状态使仿真分析方法对集成电路封装设备进行完整有效的建模和分析仍然无法实现。
最后,有限元分析为代表的仿真方法的本质在于以巨量的离散单元来极度趋近仿真的对象,对应着硬件/软件和分析时间的巨大开销。
这决定了在实际使用这些方法时如果不加区别地应用到设备的整体,将导致过于庞大复杂的模型,对模型求解所需的硬件/软件、人力和时间资源都远远超出工业实际允许的范围。
而在设备复杂的体系中分辨需要分析的关键环节,建立可行有效的仿真模型又必须基于长期积累的大量实体样机测试验证的经验。
仿真方法只能作为一种高度依赖于实体样机测试的辅助方法而存在。
在以上数值仿真方法局限性取得实质性突破之前,通过基于仿真分析方法的虚拟样机技术建立全面真实代表集成电路封装设备整机运行状况的虚拟模型并进行准确有效的设备可靠性分析和优化还只能是与现实存在巨大差距的理想。
IV。
国产设备生产线运行可靠性分析
生产线上的实际运行记录最能揭示集成电路封装设备可靠性的内在规律。
表1是根据国产引线键合设备在用户生产线上运行4个月的原始故障记录整理出的可靠性统计数据。
把设备运行中代表性的59个可靠性问题分为23个大类和A、B、C三种类型,在表中分别列出了每一大类问题的示例、数量和类型。
类型A的问题可以完全在设计阶段通过设计和仿真工具的运用得到解决;
类型B的问题的解决需要设计仿真工具充分结合从实体样机中获得的关键信息并在实体样机上得到验证;
类型C的问题无法借助设计仿真工具预先解决或改善而必须完全依靠实体样机的测试-优化循环来解决。
表1。
国产引线键合设备生产线运行情况统计
国产设备可靠性问题第一个突出的特点是碰撞/干涉、位置/尺寸正确性、结构/布局合理性等完全可以在设计阶段避免的问题大量存在,在所有问题中占有47%的高比例,国产设备在设计上确实存在着很大的不足。
这部分问题可以通过细致的设计规范和周密的设计流程管理得到迅速显著的改善。
机械/电气功能正确性、机械结构抗振/健壮性等问题需要设计仿真工具与实体样机实际运行的数据紧密结合来解决并最终在实体样机上得到验证。
这一类问题在问题总量中也占有36%的较高比重。
键合工艺可靠性和电气信号完整性等问题必须完全通过在实体样机上的测试-分析-优化循环来解决。
这一类问题在三类问题中数量最少,只占问题总数的17%,但却真正决定着国产设备在可靠性上与国际主流设备的巨大差距。
解决这些问题需要在物力、人力和时间各方面付出的成本也是最高的。
而都需要实体样机测试的B类和C类问题一共占问题总数的53%,超过了可以脱离实体样机的A类问题,这也印证了实体样机建造在集成电路封装设备开发中的重要地位。
V。
契合工业实践的集成电路封装设备可靠性改善方法
基于以上的分析重点针对国产集成电路封装设备设计阶段的缺陷以及与国际主流设备在可靠性上的巨大差距提出封装设备可靠性的改善方法。
首先,紧密结合集成电路封装设备的特性建立详细的设计规范和严密的设计管理流程,尽最大可能消除碰撞/干涉等问题,保证尺寸/位置的正确性和结构/布局的合理性。
从根本上弥补国产设备在设计上的不足。
其次,建立包括应力/应变、模态分析、温度/传热等的仿真分析和优化方法。
与实体样机充分结合,修正仿真模型参数并验证仿真结果。
对实体样机上的测试结果进行总结归纳以不断补充完善优化方法和设计规则。
最后,构建充分、严密和系统的批量实体样机测试和优化体系。
大量有序的实体样机测试验证是克服传统可靠性设计及新兴虚拟样机技术局限性的唯一方法,也是弥合国产封装设备与国际主流设备之间巨大差距的必经途径。
实体样机测试验证一直是国际各主流集成电路设备制造商大量使用的可靠性提升方法,具有无可替代的地位。
批量实体样机测试也是设备一致性改善的实用有效方法。
在美国应用材料公司,应用实验室和客户在样机使用中的问题识别及相应的问题纠正措施是与系统建模和可靠性参数设计并列的产品可靠性实现方法[3]。
开发了一种在样机连续24小时运行中跟踪设备可靠性的方法,建立运行状况数据库便于设备可靠性的长期分析和预测[4]。
国际领先引线键合设备厂商对批量样机测试验证方法非常重视,投入大量的资源。
表2是国际领先引线键合设备厂商在产品研发的不同阶段建造的实体样机的用途和数量。
表2。
国际领先引线键合设备厂商实体样机用途和数量
批产验证的流程进行。
每一阶段都建造相当数量的样机供充分测试并根据测试结果和分析对设计进行修正,同时与用户密切结合,把设备上线资格测试嵌入到完整的产品测试流程中。
在产品开发各阶段建造的样机总数达到45台,几乎相当于国内设备企业成熟产品一年的产量。
这种惊人的区别正是造成国产封装设备与国际主流产品可靠性上巨大差别的根本原因。
对于在成熟产品平台上进行重大改进的设备国际主流厂商在研发过程中建造了45台样机,而从无到有全新开发的国产设备批量生产前制造的样机通常只有2到3台。
这种样机验证上投入的严重不足有资源限制的原因,但更多来自观念和意识的落后。
国产设备企业实际上把产品开发最为关键的环节推到了批量生产阶段,大量可靠性不合格的产品发往用户后把生产线变成了设备的测试验证场所。
严格的产品故障分析和设计改进体系的缺失又造成设备在生产线上暴露的问题长期得不到有效彻底的解决,同时给用户和设备企业造成了巨大的损失。
试产验证设计验证工程验证 国际主流厂商的产品开发严格按照可行性
通过测试-优化不断循环的方法来提高集成电路封装设备可靠性的可行性是基于以下两个基本的前提:
设备中存在的可靠性问题是有限集合;
每次测试-优化循环都导致现有可靠性问题的解决而且不引入新的问题。
为了保证这两个前提的成立,首先要建立持续一贯的产品平台,在新产品设计中尽量采用前期积累的稳定技术单元,避免大量引入新方案、新技术而造成问题激增。
其次需要准确高效的故障捕获和问题识别/分析手段,保证迅速正确地发现样机测试中显露的问题并找到原因。
最后必须建立受控有序的根据测试结果和分析对设计进行修正并不断循环的机制,确保已发现的问题得到彻底解决的同时不引入新的问题。
以上是紧扣国内现状、契合工业实践的有效可行的集成电路封装设备可靠性改善方法。
VI。
结论
集成电路制造工艺的不断发展给集成电路主生产设备尤其是封装设备的可靠性提出了极高的要求。
封装设备的可靠性水平直接决定着产品的市场定位,是封装设备企业长期积累的产业化技术的集中体现,也是企业之间最难以跨越的差距。
可靠性问题是国产封装设备一直无法规模化配备主流生产线的症结所在,是制约国内集成电路封装装备实现产业化的瓶颈。
在可靠性上填补与国际主流设备之间的巨大差距较前期完成可行性样机的开发和实现单一关键技术的突破远为复杂和艰巨。
封装设备中存在着的大量多层次架构和多种物理量共存的状态使传统可靠性设计方法显现出了极大的局限性。
集成电路封装设备的可靠性问题更多地集中在设备的加工对象和工艺过程上,远远超越了传统意义上的一般设备失效模式的分析和预防。
封装设备工艺的可靠性问题可以总结为一个极敏感的多参数过程的参数识别和优化问题,这正是集成电路封装设备可靠性有别于传统设备可靠性的最突出特性,也是提高封装设备可靠性的挑战集中所在。
传统可靠性设计在这一挑战面前完全无能为力。
仿真技术在集成电路设备开发的局部、单一零件或简单系统的分析和优化中发挥了重要的作用。
仿真技术对于存在着多个不同对象间交互作用的场合很难处理。
多种物理场并存的耦合问题对仿真技术也是极大的挑战。
仿真方法巨量资源占用的特性决定它只能作为一种高度依赖于实体样机测试的辅助方法而存在。
在数值仿真方法局限性取得实质性突破之前,通过基于仿真分析方法的虚拟样机技术建立全面真实代表集成电路封装设备整机运行状况的虚拟模型并进行准确有效的设备可靠性分析和优化还只能是与现实存在巨大差距的理想。
国产引线键合设备在用户生产线上运行的可靠性统计数据显示产品在设计上存在很大不足。
需要借助实体样机测试来解决的可靠性问题占问题总数的53%,超过了可以脱离实体样机得到解决的问题,印证了实体样机建造在集成电路封装设备开发中的重要地位。
紧扣国内现状、契合工业实践提出了有效可行的集成电路封装设备可靠性改善方法。
首先,建立详细的设计规范和严密的设计管理流程。
其次,建立包括应力/应变、模态分析、温度/传热等的仿真分析和优化方法,充分利用实体样机修正仿真模型参数、验证仿真结果和完善设计规则。
最后,构建充分、严密和系统的批量实体样机测试和优化体系。
在测试验证样机数量上的悬殊是造成国产封装设备与国际主流产品可靠性上巨大差别的根本原因。
设备开发中要保证测试-优化循环方法有效性的两个基本前提:
参考文献
1。
Woytowitz,Peter,“Virtualprototypingofsemiconductorprocessingequipment”,ApplicationNotesofNovellusSystems,Inc。
2。
何田,“一种运动控制算法的高效实时仿真调试方法”,电子工业专用设备,2006年2月,35
(2),53-57页。
3。
Ditmore,D。
;
Stewart,J。
Dudley,R。
Bright,N。
,“Achievingsemiconductorequipmentreliability”,ProceedingsoftheSeventhIEEE/CHMTInternationalElectronicManufacturingTechnologySymposium,Sep。
25-27,1989,pp。
5-11。
4。
Azzano,L。
Gay,D。
Pasumamula,A。
,“Apracticalapproachtoequipmentreliabilityenhancement”,ProceedingsofIEEE/SEMI1995AdvancedSemiconductorManufacturingConferenceandWorkshop,Nov。
13-15,1995,pp。
255-259。