成果报告Word文档下载推荐.docx
《成果报告Word文档下载推荐.docx》由会员分享,可在线阅读,更多相关《成果报告Word文档下载推荐.docx(7页珍藏版)》请在冰豆网上搜索。
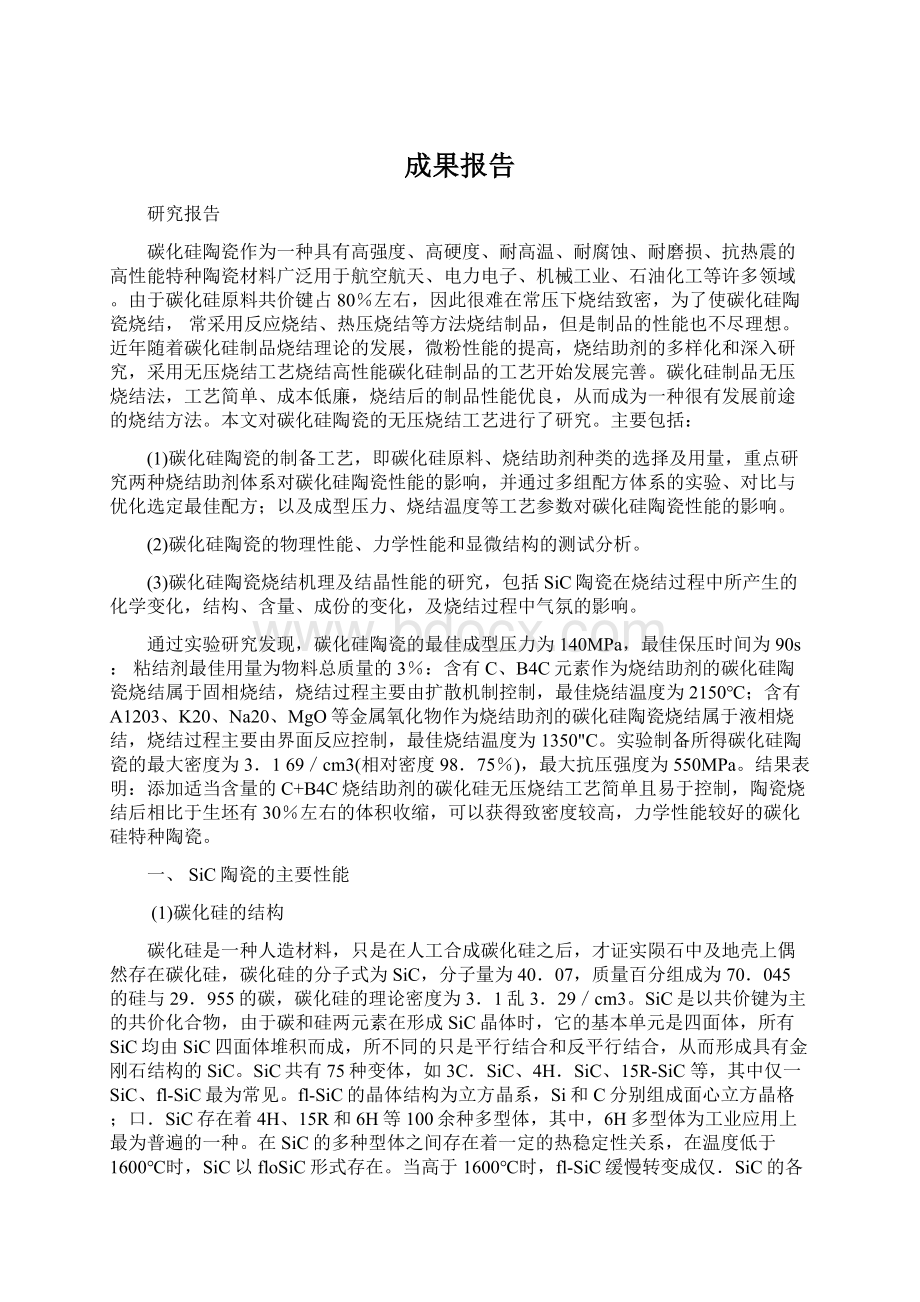
一、SiC陶瓷的主要性能
(1)碳化硅的结构
碳化硅是一种人造材料,只是在人工合成碳化硅之后,才证实陨石中及地壳上偶然存在碳化硅,碳化硅的分子式为SiC,分子量为40.07,质量百分组成为70.045的硅与29.955的碳,碳化硅的理论密度为3.1乱3.29/cm3。
SiC是以共价键为主的共价化合物,由于碳和硅两元素在形成SiC晶体时,它的基本单元是四面体,所有SiC均由SiC四面体堆积而成,所不同的只是平行结合和反平行结合,从而形成具有金刚石结构的SiC。
SiC共有75种变体,如3C.SiC、4H.SiC、15R-SiC等,其中仅一SiC、fl-SiC最为常见。
fl-SiC的晶体结构为立方晶系,Si和C分别组成面心立方晶格;
口.SiC存在着4H、15R和6H等100余种多型体,其中,6H多型体为工业应用上最为普遍的一种。
在SiC的多种型体之间存在着一定的热稳定性关系,在温度低于1600℃时,SiC以floSiC形式存在。
当高于1600℃时,fl-SiC缓慢转变成仅.SiC的各种多型体。
4H.SiC在2000℃左右容易生成;
15R和6H多型体均需在2100℃以上的高温才易生成;
对于6H.SiC,即使温度超过2200℃,也是非常稳定的。
SiC中各种多型体之问的自由能相差很小,因此,微量杂质的固溶也会引起多型体之间的热稳定关系变化。
(2)SiC的化学性质
SiC的化学稳定性与其氧化特性有密切关系。
SiC本身很容易氧化,但它氧化之后形成了一层Si02薄膜,氧化进程逐步被阻碍。
在空气中,SiC于800℃时就开始氧化,但很缓慢;
随着温度升高,则氧化速度急速加快。
它的氧化速率在氧气中比在空气中快1.6倍:
氧化速率随着时间推移而减慢。
如果以时间推移对氧化的数量描图,可以得到典型的抛物线图形,这反映出Si02保护层对SiC氧化速率的阻碍作用。
氧化时,若同时存在着能将Si02薄膜移去或使之破裂的物质,则SiC就易被进一步氧化。
例如:
铁、锰等金属有几种化合价,其氧化物能将SiC氧化,并且又能与Si02生成低熔点化合物,能侵蚀SiC。
FeO在1300℃、MnO在1360℃能侵蚀碳化硅;
而CaO、MgO在1000oC就能侵蚀SiCl引。
水蒸汽与SiC在高温下反应相当强烈,于1100℃以上时,视情况不同,可生成硅、碳或Si02,在1000。
C左右时,SiC能与H2S等含硫化合物生成红棕色的硫化硅(SiS2或SiS),这一反应也是碳化硅制品在烧成时色泽变红的原因之一。
SiC陶瓷的优异性能与其独特的结构密切相关。
SiC是共价键很强的化合物,SiC中Si.C键的离子性仅12%左右。
因此,SiC强度高、弹性模量大、具有优良的耐磨损性能。
纯SiC不会被HCI、HN03、H2S04和HF等酸溶液以及NaOH等碱溶液侵蚀。
在空气中加热时易发生氧化,但氧化时表面形成的Si02会抑制氧的进一步扩散,故氧化速率并不高。
在电性能方面,SiC具有半导体特性,少量杂质的引入会表现出良好的导电性。
(3)SiC的热学性质
SiC是在高温下合成的,其制品也多是在高温下制备或者在高温下使用。
因此,了解碳化硅的热膨胀系数很有必要。
如果只作较粗略计算时,碳化硅的平均热膨胀系数在25~1400oC范围内可以取4.4x10"
6/℃。
SiC的热膨胀系数测定结果表明:
其量值与其他磨料及高温材料相比要小得多,如刚玉的热膨胀系数可高达(7~8)xlO‘6I。
Ct引。
SiC的导热系数很高,这是SiC物理性能方面的另一个重要特点。
它的导热系数比其他耐火材料及磨料要大的多,约为刚玉导热系数的4倍。
所以,SiC所具有的低热膨胀系数和高导热系数,使其制品在加热及冷却过程中受到的热应力较小,这就是SiC陶瓷抗热震性特别好的原因峭J。
(4)SiC的硬度和韧性
SiC的硬度相当高,仅次于几种超硬材料,高于刚玉而名列普通磨料的前茅,莫氏刻痕硬度为9.2,克氏显微硬度为2200~2800kg/mm2(负荷lOOg)。
值得指出的是,所给
范围之所以如此大,这是因为SiC晶体的硬度与其晶轴方向有关。
研究表明:
在一个结晶体内,由于方向不同,最硬的与最软的差别可达800kg/mrn2以上例。
SiC的热态硬度虽然随着温度的升高而下降,但仍比刚玉的硬度大很多。
绿色碳化硅和黑色碳化硅的硬度,不论在常温或是在高温下都基本相同,没有发现本质上的差别。
碳化硅的机械强度高于刚玉,如SiC的抗压强度为224MPa,刚玉为75.7MPa;
SiC的抗弯强度为15.5MPa,刚玉则为8.72MPa。
SiC颗粒的韧性,通常是用一定数量某种粒度SiC颗粒在定型模子中,施加规定压力之后未被压碎的颗粒所占百分率来反映的,它受颗粒形状等许多因素的影响。
二、碳化硅的性能测定
1、体积密度、吸水率和气子L率的测定
用液体浸泡试样,然后再用沸水煮3h,尽量使试样达到饱和。
用液体静力天平和电子天平称干试样质量(m1)、饱和试样表观质量(m2)、饱和试样空气中质量(m3)和浸渍液体的密度(Di)。
体积密度按下式计算:
Db=[聊。
×
Df/(m3一所2)】×
100%(3.1)吸水率按下式计算:
睨=[(脚3--m1)/ml】×
100%(3.2)气孔率按下式计算:
只=【(聊3--m1)/(跏3--m2)]x100%(3.3)式中:
ml—干试样质量;
m2—饱和试样表观质量;
m3—饱和试样空气中质量;
D,--燃度下,浸渍液体密度,单位:
g/cm3(本实验选用液体为蒸馏水密度为19/cm3)。
2、抗压强度的测定
抗压强度指外力只是压力时材料的强度极限,特种陶瓷的抗压强度是指在无侧束状态下所能承受的最大压力,换言之,它指把特种陶瓷加压至破裂所需要的应力。
试样实验时受压方向应为制品成型时加压方向,加载速率为90MPa/min。
抗压强度的计算公式:
Rc:
一P(3.4)式中:
√卜试样受压面积(cm2);
d1、d2—试样上、下受压面的直径(cm);
卜试样破坏时的压力(kg);
RC.-{式样的抗压强度(kg/cm2)。
其中:
1MPa=1N/mm2。
三、两种烧结助剂体系对SiC陶瓷性能的影响
1、粘结剂用量的确定
在本研究中加入粘结剂的作用只是增加素坯的强度,而并不参加烧结反应。
在使用了纤维素作为粘结剂的实验中,首先应确定粘结剂的最佳加入量(粘结剂的加入量均指相对于碳化硅原料及烧结助剂总质量的百分比)。
由图4.1(a)和图4.1(b)可以看出,在模压成形中随着粘结剂含量由2%增加到3%,碳化硅陶瓷的生坯密度是增加的。
粘结剂的增加,增加了SiC物料的塑性,在单向加压成型过程中降低了颗粒之间以及颗粒与模具内壁的摩擦力,使得消耗掉的挤压力减小,而更多的压力用来挤压物料本身,排除其中的气孔,使得小颗粒填充到大颗粒的空隙中,而粘结剂填充到固体颗粒之间的缝隙中,提高了碳化硅陶瓷的致密度。
而粘结剂过少,虽然也可以实现成形,但物料塑性差,颗粒的移动重排摩擦力比较大,使制品不易致密。
当粘结剂由3%增加到3.5%时,碳化硅陶瓷的生坯密度、强度又有不同程度的下降。
是因为不同含量的粘结剂物料不同的含水量,在粘结剂含量为3.5%时,含水量比粘结剂含量低的物料的含水量高,在水分挤出后,生坯需要干燥,水分的挥发在生坯内部留下了许多的气孔,以致颗粒之间结合的不是很紧密。
导致制品的生坯密度、强度都有所下降。
而对于烧结后制品的密度、强度的变化规律,也和未烧结前相差不多。
这主要是因为在碳化硅陶瓷烧结过程中基本上没有外来物质的加入,所以生坯的密度对其影响非常大,应该说具有决定性的影响,而制品的烧结密度,对制品的其它的性能有着很大的影响,密度大的,制品烧结程度好,气孔率小,其强度也就会相应地增加。
所以其变化规律和未烧结前基本差别不大,只是它们之间的差别有所放大而已。
这些都可以从图4.1(b)的气孔率的变化规律得到验证。
粘结剂可以有效地提高样品生坯的密度,使不同粒径的SiC颗粒在一定的压力下产生一定的强度。
随着粘结剂含量的增加,试样的生坯强度也随之增加。
这主要是因为粘结剂与水所形成的溶液均匀涂覆在颗粒表面,在成形过程中粘结剂溶液填充在颗粒空隙处,干燥后形成复杂的网络结构,使颗粒紧紧结合在一起。
粘结剂含量越多,干燥后网络越密实,所显现出来的粘结力也越强,但粘结剂含量过多会降低碳化硅陶瓷生坯的密剧371。
2、压力对制品生坯密度的影响
(1)压力大小的确定
在粉末的成型过程中,成型压力是一个重要的工艺参数。
它对坯体的密度、强度和气孔率等性能的影响,要比其它因素更为关键,同时对坯体烧结后的性能具有明显的影
响。
实验采用固定保压时间,用不同压力进行加压,测出坯体密度以得到最佳成型压力。
图4.2所示,随着压力的增大生坯的密度也增大,在增加压力的过程中,60~140MPa
时坯体密度增长很快,此时在压力作用下,粉体颗粒发生位移、填隙、变形、粉碎等,从而导致坯体密度迅速增大,颗粒发生重排,粘结剂填充到内部孔隙中,使孔隙内部的
气体排出坯体在压力达到140MPa后,密度增加趋缓,达到最大值,如果压力继续增大,密度随压力增加基本没有明显变化或甚至减小,这是因为:
成型压力升高到一定程度时,颗粒间的孔隙大大减少,颗粒的塑性变形受到限制,而且颗粒加工硬化严重,颗粒更难进一步变形。
且压力太大造成坯体内部产生很大应力,导致坯体泄压之后体积回复,使体密度反而降低。
而且容易使样品产生弹性后效(是指停止压制压力并把压坯顶出压模以后,由于内应力的作用,压坯发生弹性膨胀的现象,一般包括纵向和径向膨胀),本实验所用模具则更容易受到纵向内应力的影响,发生纵向膨胀,使样品产生分层裂纹,对制品的成型有很大的影响。
所以压力一般选取在140MPa,这样更有利于提高生坯的强度和成品率。
(2)保压时间长短的确定
保压时间对提高坯体密度有重要意义,保压时间的选择决定了制品的质量,太长则浪费时间且影响压机使用寿命,太短则达不到最好效果,影响坯体的均匀性和致密度。
实验中,为了确定保压时间对样品的影响,采用以固定压力,不同保压时间对样品进行保压,通过对样品的体积密度的比较来得出最佳保压时间。
图4.3是密度随保压时间的变化曲线,从图中可以看出:
30s~90s制品体密度增长很快,可见由于开始升压很快使坯体很不均匀,压坯芯部较外层松软得多,粉料颗粒之间的位移和颗粒本身的变形均需要一定的时间。
随着保压时间的延长,应力从最外层逐渐向内部传递,当在90s附近时生坯密度达到最大值。
而在90s之后,样品生坯密度几乎没有增加。
这是因为在保压初始阶段,颗粒发生重排,内部大部分气孔消失,气孔内的空气被排出样品。
而后随着时间的延长,颗粒之问发生“拱桥"
现象,使得颗粒重排遇到较大阻力,内部残留部分气孔,制品的密度提高就比较缓慢。
在150s时生坯密度稍微小于90s、120s时的生坯密度,似乎与一般规律不符,这一点可以解释为90s~120s时坯体已经相当致密,保压时间增加而坯体体积不会再减小,坯体内应力聚集,导致在泄压后坯体体积反而发生膨胀,使得制品生坯密度不升反降所以在压制样品过程中,从保护压机少受损坏的情况下,保压时间一般选取90s,这样更能提高压制的效率。
四、SiC陶瓷的烧结机理及结晶性
(1)首先是要使适量的液相将固体粒子的间隙填满。
液相过多,则会在自重下软化变形;
液相过少,则产生未润湿部分。
(2)熔化物能够将固体填料很好润湿。
润湿程度可用接触角9测定,最少也应在900以下。
0如果接近于零,熔化物既使少到百分之几,也会在温度上升时完全覆盖固体粒子表面。
(3)熔化物能够将固体适当溶解。
在烧结过程中,通过液相烧结进行传质,较小的固体粒子或粒子表面凸起部分溶解,而在较大的粒子表面沉积,出现晶粒长大和晶粒形状的变化。
同时,固体粒子不断进行重排产生进一步致密化。
1、SiC陶瓷的结晶性
绝大多数单晶是由熔体或溶液生长的,目前SiC晶体还不能用这两种方法生长,这是因为在1个大气压时,SiC相图有包晶体,只有在压力>
1010pa、温度>
3200℃时才能形成化学计量熔体;
当温度为1412~2830℃时,C在Si中的溶解度仅为O.01‰19%,且在1700-1750℃时Si的挥发使得生长过程不稳定。
在熔体中添加某些金属元素可使C的溶解度大于50%(如加入Pr,T.b,Sc等),金属添加物在晶体中的溶解度也比较高,可以促使晶体的生长【70,711。
Tairov等人于1978年提出,结晶过程主要受气相过饱和度控制,生长速度则与过饱和度成正比。
SiC晶体生长是SiC蒸汽和SiC分解形成的Si、Si2C、SiC2气体参与晶体生长的结果。
Si、Si2C、SiC2或者转移至较低温度的部位,凝集于SiC晶体上,或者不转移至低温处而直接凝聚在附近的较大晶体上,促使晶体尺寸逐渐增加。
由于晶体表面质点受到束缚力较小,因而蒸汽压随物质的结晶大小而异,即愈小的晶体具有愈大的蒸汽压。
同~蒸汽压对于小晶体来说是不饱和的,而对于大晶体来说可能就是过饱和的了,这就促使了小晶体的不断蒸发乃至消失,大晶体的不断发育长大17引。
碳化硅生长的规律遵循着~般晶体气相生长的规律。
流行最广的是以弗朗克(Frank)为代表的螺旋位错机理174J。
位错是晶体结构上的一种物理缺陷,即晶体中两部分晶格之间的相对位置发生了错动。
位错可以看作是晶体自身平面的部分沿着晶体中一个平面的平移。
螺旋位错则是晶体两部分之间发生了形同螺旋的扭动。
螺旋位错产生后,晶面上出现了阶梯。
晶体沿螺旋位错进行螺旋形生长时,其阶梯始终不会消失,并在晶体表面上留下了相应的生长蜷线。
如本实验中,烧结过程形成的阶梯如图5.3所示。
2、结晶颗粒形貌
晶体的长大是在临界晶核的基础上一列列、一层层的生长壮大的。
晶体与液体、气体、无定形非晶质固体相比,是具有最低位能的物质,在已形成的结晶单元上加入新质点时,将析出相当于晶格位能的能量。
在晶体表面有这样三个地方:
三面凹角,质点落于此,将为三个最近的质点所吸引;
两面凹角.质点落于此,将为两个最近的质点所吸引;
无凹角处,只有一个最近的质点吸引。
显然,游离的质点将优先落于三面凹角处,即图中所示的台阶处,等到没有三面凹角之后,再轮到两面凹角.最后才是无凹角的地方,如此一行一行地进行下去,直到把整个晶体铺满以后,再在新的面上重新开始出现新的生长阶梯(或台阶),当然,在晶体生长韵实际过程中,不一定长满一个晶面后才开始形成二维晶核。
当成核条件合适时,往往在一层未长满以前,就在正在生长着的晶面的平整部分上形成新的二维晶核,这使晶体在增厚的方向上迅速生长。
在液相烧结过程中,不断有卢SiC融入液相中,而a.SiC则不断的从液相中析出,在溶解一结晶过程中,产生了卢SiC向卅SiC的转变,新生成的一SiC结晶在原颗粒晶界处,一般不会沿着晶面法线方向生长,这一点不同于固相烧结。
烧结过程中,当炉温降低后,共融液相结晶在颗粒晶界之间.形成了与周围区域晶相不同的结构。
3、总结
碳化硅的固相烧结过程中一般都是在原a-SiC颗粒的晶面上生长的,沿着晶面进行二维方向上生长;
而在液相烧结过程中一般都形成了新的玻璃相,新生成的玻璃相主要填充在颗粒间隙处,使体系的传质方式由扩散传质变为粘性流动,降低了致密化所需能量和烧结温度。
五、结论
(1)碳化硅生坯的最佳成型压力为140MPa,最佳保压时间为90s;
粘结剂最佳用量为物料总质量的3%。
(2)含有C、B4C作为烧结助剂的碳化硅陶瓷的烧结属于固相烧结,烧结过程主要是由扩散机制控制的。
含有A1203、K20、Na20、MgO等金属氧化物作为烧结助剂的碳化硅陶瓷属于液相烧结,烧结过程主要由界面反应控制。
(3)C+B4C烧结助剂体系的碳化硅陶瓷烧结温度较高,最佳烧结温度为2150℃,获得制品最大密度为3.169/cm3,最大抗压强度为550MPa;
金属氧化物烧结助剂体系的碳化硅陶瓷烧结温度相对较低,最佳烧结温度为1350℃,获得制品最大密度为2.80g/cm3,最大抗压强度为442MPa。
(4)有金属氧化物参与的碳化硅的液相烧结可以降低碳化硅的烧结温度,但各类氧化物烧结助剂不可加入过多,一般以10%左右为合适,即长石粉+滑石粉+硅微粉占总质量的10%,且三者比例为2:
1:
l。
(5)在金属氧化物作为烧结助剂的液相烧结过程中,以80日:
150目:
320fl=7:
l:
2混合的黑色t1.SiC原料的制品性能优于以纯度为99%的W3.59m绿色fl-SiC原料的制品性能,说明以合理的颗粒级配体系碳化硅为原料更有利于制备性能优良的碳化硅陶逸扛Lo
(6)在C+B4C烧结助剂体系中,C和B4C的均匀分布对SiC陶瓷的致密度和力学性能起很大作用,环氧树脂作为碳源比石油焦和炭黑更好,另外,添加粒度较细的石油焦的烧结样品性能优于粒度稍大的炭黑的烧结样品性能,说明烧结助剂的粒度越细,则烧结体的性能越好。
(7)使用仅.SiC与fl-SiC混合原料代替单一的a或fl-SiC。
在烧结过程中,以仅.SiC作为晶母,psic产生相变,转化为口.SiC,生成的倪.SiC沉积在原口.SiC晶母上,使颗粒生长呈各向异性,形成的晶体具有更好的长径比,通过晶粒桥联会起到增强增韧作用。
(8)添加适当含量的C+B4C的SiC无压烧结工艺,工艺简单,易于控制,材料致密度较高,最大密度为3.169/cm3(相对密度98.75%);
力学性能较好,最大抗压强度为550MPa。
(9)碳化硅的固相烧结过程中一般都是在原口.SiC颗粒的晶面上生长的,沿着晶面进行二维方向上生长;