拉深工艺及拉深模具的设计Word文档下载推荐.docx
《拉深工艺及拉深模具的设计Word文档下载推荐.docx》由会员分享,可在线阅读,更多相关《拉深工艺及拉深模具的设计Word文档下载推荐.docx(74页珍藏版)》请在冰豆网上搜索。
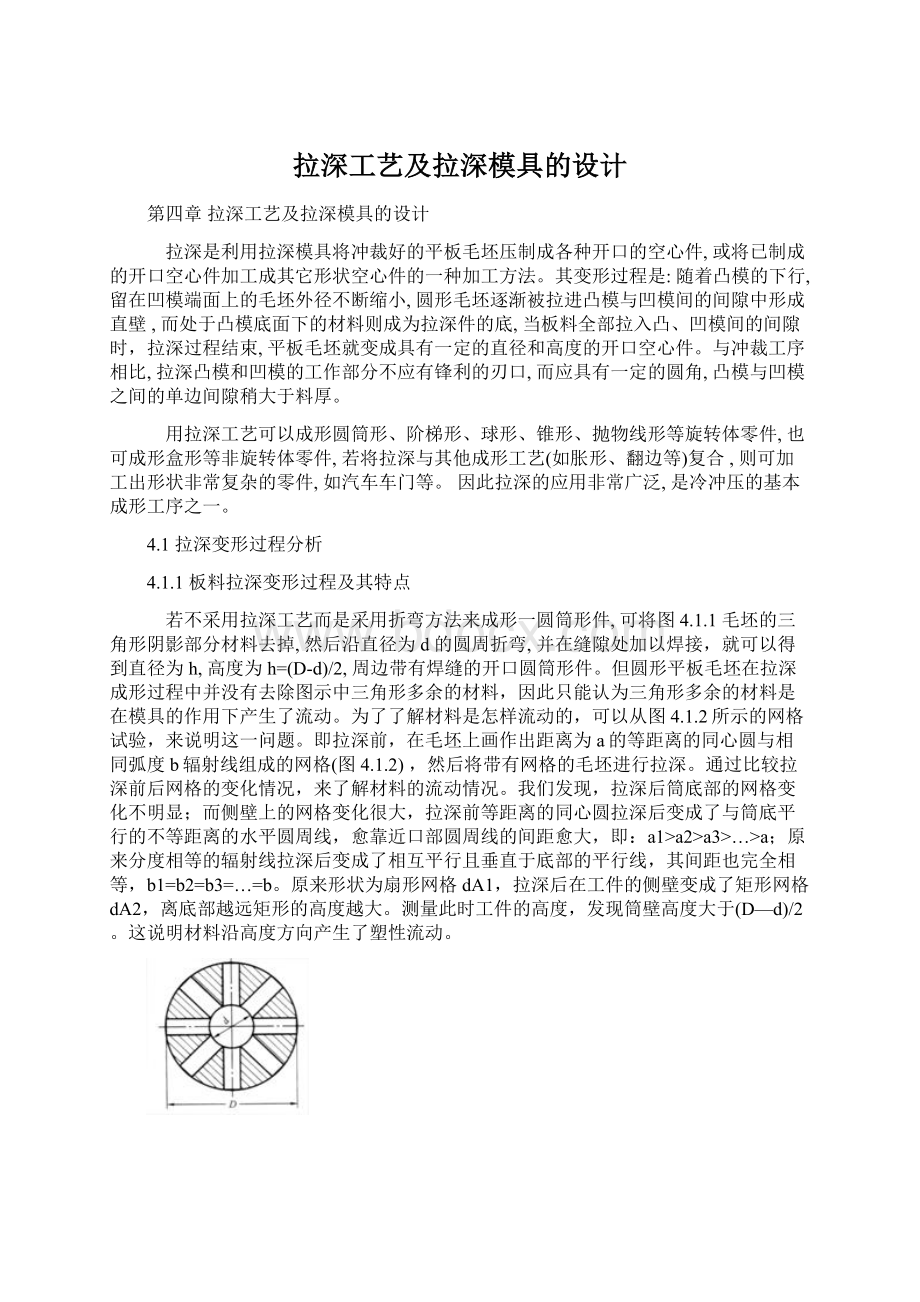
部分材料
金属是怎样往高度方向流动,或者说拉深前的扇形网格是怎样变成矩形的。
从变形区任选一个扇形格子来分析,如图4.1.3所示。
从图中可看出,扇形的宽度大于矩形的宽度,而高度却小于矩形的高度,要使扇形格子拉深后要变成矩形格,必须宽度减小而长度增加。
很明显扇形格子只要切向受压产生压缩变形,径向受拉产生伸长变形就能产生这种情况。
而在实际的变形过程中,由于有三角形多余材料存在(图4.1.1),拉深时材料间的相互挤压产生了切向压应力(图4.1.3),凸模提供的拉深力产生了径向拉应力。
故(D—d)的圆环部分在径向拉应力和切向压应力的作用下径向伸长,切向缩短,扇形格子就变成了矩形格子,三角形多余金属流到工件口部,使高度度增加。
a)单元网格的受力 b)网格的挤压模型
图4.1.3拉深网格的挤压变形
这一受力过程如同一扇形毛坯被拉着通过一个楔形槽(图4.1.3b)的变化是类似的,在直径方向被拉长的同时,切向则被压缩。
在实际的拉深过程中,当然并没有楔形槽,毛坯上的扇形小单元体也不是单独存在的,而是处在相互联系、紧密结合在一起的毛坯整体。
在凸模力的作用下,变形材料间的相互拉伸作用而产生了径向拉应力σ1,而切线方向材料间的相互挤压而产生了切向压应力σ3。
因此,拉深变形过程可以归结如下:
在拉深过程中,毛坯受凸模拉深力的作用,在凸缘毛坯的径向产生拉伸应力σ1,切向产生压缩应力σ3。
在它们的共同作用下,凸缘变形区材料发生了塑性变形,并不断被拉入凹模内形成筒形拉深件。
4.1.2拉深过程中变形毛坯各部分的应力与应变状态
图4.1.4是拉深变形后,沿圆筒形制件侧壁材料厚度和硬度变化的示意图。
一般是底部厚度略有变簿,且筒壁从下向上逐渐增厚。
此外,沿高度方向零件各部分的硬度也不同,越到零件口部硬度越高,这些说明了在拉深变形过程中坯料的变形极不均匀。
在拉深的不同时刻,毛坯内各部分由于所处的位置不同,毛坯的变化情况也不一样。
为了更深刻地了解拉深变形过程,有必要讨论在拉深过程中变形材料内各部分的应力与应变状态。
(b)
图4.1.4拉深件材料厚度和硬度的变化
现以带压边圈的直壁圆筒形件的首次拉深为例,说明在拉深过程中的某一时刻(图4.1.5)毛坯的变形和受力情况。
假设σ1、ε1为毛坯的径向应力与应变;
σ2、ε2为毛坯的厚向应力与应变;
σ3,ε3为毛坯的切向应力与应变。
图4.1.5拉深中毛坯的应力应变情况
根据圆筒件各部位的受力和变形性质的不同,可将整个变形毛坯分为5个区域:
(1)平面凸缘区—主要变形区
这是拉深变形的主要变形区,也是扇形网格变成矩形网格的区域。
此处材料被拉深凸模拉入凸模与凹模之间间隙而形成筒壁。
这一区域变形材料主要承受切向的压应力σ3和径向的拉应力σ1,厚度方向承受由压边力引起的压应力σ2的作用,该区域是二压一拉的三向应力状态。
由网格实验知:
切向压缩与径向伸长的变形均由凸缘的内边向外边逐渐增大,因此σ1和σ3的值也是变化的
由网格试验知道,变形材料在凸模力的作用下挤入凹模时,切向产生压缩变形ε3,径向产生伸长变形ε1;
而厚向的变形ε2,取决于σ1和σ3之间的比值。
当σ1的绝对值最大时,则ε2为压应变,当σ3的绝对值最大时,ε2为拉应变。
因此改区域的应变也是三向的。
由图4.1.2可知,在凸缘的最外缘需要压缩的材料最多,因此此处的σ3是绝对值最大的主应力,凸缘外缘的ε2应是伸长变形。
如果此时σ3值过大,则此处材料因受压过大而失稳而起皱,导致拉深不能正常进行。
(2)凹模圆角区—过渡区
这是凸缘和筒壁部分的过渡区,材料的变形比较复杂,除有与凸缘部分相同的特点,即径向受拉应力σ1和切向受压应力σ3作用外,厚度方向上还要受凹模圆角的压力和弯曲作用产生的压应力。
该区域的变形状态也是三向的:
ε1是绝对值最大的主应变(拉应变),ε2和ε3是压应变,此处材料厚度减薄。
(3)筒壁部分—传力区
这是由凸缘部分材料塑性变形后转化而成,它将凸模的作用力传给凸缘变形区的材料,因此是传力区。
拉深过程中直径受凸模的阻碍不再发生变化,即切向应变ε3为零。
如果间隙合适,厚度方向上将不受力的作用,即σ2为零。
σ1是凸模产生的拉应力,由于材料在切向受凸模的限制不能自由收缩,σ3也是拉应力。
因此变形与应力均为平面状态。
其中ε1为伸长应变,ε2为压缩应变。
(4)凸模圆角区—过渡区
这是筒壁和圆筒底部的过渡区,材料承受筒壁较大的拉应力σ1、凸模圆角的压力和弯曲作用产生的压应力σ2和切向拉应力σ3。
在这个区域的筒壁与筒底转角处稍上的位置,拉深开始时材料处于凸模与凹模间,需要转移的材料较少,受变形的程度小,冷作硬化程度低,加之该处材料变薄,使传力的截面积变小,所以此处往往成为整个拉深件强度最薄弱的地方,是拉深过程中的“危险断面”。
(5)圆筒底部—小变形区
这部分材料处于凸模下面,直接接收凸模施加的力并由它将力传给圆筒壁部,因此该区域也是传力区。
该处材料在拉深开始就被拉入凹模内,并始终保持平面形状。
它受两向拉应力σ1和σ3作用,相当于周边受均匀拉力的圆板。
此区域的变形是三向的ε1和ε3为拉伸应变,ε2为压缩应变。
由于凸模圆角处的摩擦制约了底部材料的向外流动,故圆筒底部变形不大,只有1%~3%,一般可忽略不计。
4.1.3拉深变形过程的力学分析
1.凸缘变形区的应力分析
(1)拉深过程中某时刻凸缘变形区的应力分析
将半径为R0的板料毛坯拉深半径为r的圆筒形零件,采用有压边圈(图4.1.7)拉深时,在凸模拉深力的作用下,变形区材料径向受拉应力σ1的作用,切向受压应力σ3的作用,厚度方向在压边力的作用下产生后向压应力σ2。
若σ2忽略不计(与σ1和σ3比较,较小),则只需求σ1和σ3的值,即可知变形区的应力分布。
图4.1.6首次拉深某瞬间毛坯
图4.1.7圆筒件拉深时的应力分布
凸缘部分单元体的受力状态
σ1和σ3的数值可根据金属单元体塑性变形时的平衡方程和屈服条件来求解。
为此从变形区任意半径处截取宽度为dR、夹角为dΦ的微元体,分析其受力情况,如图4.1.6所示,建立微元体的受力的平衡方程得:
因为,
,取
,并略去高阶无穷小,得:
(4.1.1)
塑性变形时需满足的塑性方程为:
,式中β值与应力状态有关,其变化范围为1~1.155,为了简便取β=1.1得:
(4.1.2)
联合上述两式,并考虑边界条件(当R=Rt时,σ1=0),经数学推导就可以求出径向拉应力σ1和切向压应力σ3的大小为:
(4.1.3)
(4.1.4)
式中:
——变形区材料的平均抗力(MPa);
Rt——拉深中某时刻的凸缘半径(mm);
R——凸缘区内任意点的半径(mm)。
当拉深进行到某瞬时,凸缘变形区的外径为Rt时,把变形区内不同点的半径R值代人公式(4.1.3)和公式(4.1.4),就可以算出各点的应力,图4.1.6b是它们的分布规律,从分布曲线可看出,在变形区的内边缘(即R=r处)径向拉应力σ1最大,其值为:
(4.1.5)
而
最小,为
。
在变形区外边缘R=Rt处压应力
最大,其值为:
(4.1.6)
而拉应力σ1最小为零。
从凸缘外边向内边σ1由低到高变化,
则由高到低变化,在凸缘中间必有一交点存在(图4.1.6b),在此点处有
,所以:
化简得:
即:
即交点在R=0.61Rt处。
用R所作出的圆将凸缘变形区分成两部分,由此圆向凹模洞口方向的部分拉应力占优势(
),拉应变ε1为绝对值最大的主变形,厚度方向的变形ε2是压缩应变。
由此圆向外到毛坯边缘的部分,压应力占优势(
),压应变ε3为绝对值最大的主应变,厚度方向上的变形ε2是伸长应变(增厚)。
交点处就是变形区在厚度方向发生增厚和减薄变形的分界点。
(2)拉深过程中
和
的变化规律
当毛坯半径由R0变到Rt时,在凹模洞口处有最大拉应力σ1max,而在凸缘变形区最外缘处有最大压应力σ3max。
在不同的拉深时刻,它们的值是不同的。
了解拉深过程中σ1max和σ3max如何变化,何时出现最大值
与
就可采取措施来防止拉深时的起皱和破裂。
①
的变化规律
由
可知
两者的乘积有关。
随着拉深变形程度逐渐增大,材料的硬化加剧变形区材料的流动应力
增加,使
增大。
表示毛坯变形区的大小,随着拉深的进行,变形区逐渐缩小,使σ1max减小。
将不同的Rt所对应的各个σ1max连成曲线(图4.1.7c),即为拉深过程凸缘变形区σ1max的变化规律。
从图中可以看出示,拉深开始阶段
起主导作用,σ1max增很快,并迅速达到
,此时Rt=(0.7~0.9)R0。
继续拉深,
起主导作用,σ1max开始减小。
②
因为
,则
只与材料有关,随着拉深的进行,变形程度增加,材料变形区硬化加剧,
增大,则
也增大。
的变化规律与材料的硬化曲线相似。
增大易引起变形区失稳起皱的趋势,而凸缘变形区厚度的增加却又提高抵抗失稳起皱的能力。
所以凸缘变形区材料的起皱取决于这两个因素综合的结果。
2.筒壁传力区的受力分析
是拉深时变形区内边缘受的径向拉应力,是只考虑拉深时转移“三角形多余材料”所需的变形力。
此力是凸模拉深力F通过筒壁传到凹模口处而产生的。
假如筒壁传过来的力刚好等于它,是不能实现拉深变形的,因为拉深时除了变形区所需的变形力外
,还需要克服其他一些附加阻力(图4.1.8)。
包括材料在压边圈和凹模上平面间的间隙里流动时产生的摩擦应力引起的摩擦阻力应力。
毛坯流过凹模圆角表面遇到的摩擦阻力,毛坯经过凹模圆角时产生弯曲变形,以及离开凹模圆角进入凸凹模间隙后又被拉直而产生反向弯曲都需要力,拉深初期毛坯在凸模圆角处也有弯曲应力。
因此,从筒壁传力区传过来的力至少应等于上述各力之和。
上述各附加阻力可根据各种假设条件,并考虑拉深中材料的硬化来求出。
有关拉深力的计算可查阅有关设计手册。
图4.1
.8拉深毛坯内各部分的受力分析
4.1.4拉深成形的障碍及防止措施
由上面的分析可知,拉深时毛坯各邵分的应力应变状态不同,而且随看拉深过程的进行应力应变状态还在变化,这使得在拉深变形过程中产生了一些特有的现象。
1.起皱及防皱措施
拉深时凸缘变形区的材料在切向均受到σ3压应力的作用。
当σ3过大,材料又较薄,σ3超过此时材料所能承受的临界压应力时,材料就会失稳弯曲而拱起。
在凸缘变形区沿切向就会形成高低不平的皱褶,这种现象称为起皱,如图4.1.9所示。
起皱在拉深薄料时更容易发生,而且首先在凸缘的外缘开始,因为此处的σ3值最大。
图4.1.9毛坯凸缘的起皱情况
图4.1.10反拉深
变形区一旦起皱,对拉深的正常进行是非常不利的。
因为毛坯起皱后,拱起的皱褶很难通过凸、凹模间隙被拉人凹模,如果强行拉人,则拉应力迅速增大,容易使毛坯受过大的拉力而导致断裂报废。
即使模具间隙较大,或者起皱不严重,拱起的皱褶能勉强被拉进凹模内形成筒壁,皱折也会留在工件的侧壁上,从而影响零件的表面质量。
同时,起皱后的材料在通过模具间隙时与凸模、凹模间的压力增加,导致与模具间的摩擦加剧,磨损严重,使得模具的寿命大为降低。
因此,起皱应尽量避免。
拉深是否失稳,与拉深件受的压力大小和拉深件的凸缘变形区几何尺寸有关。
主要决定于下列因素:
(1)凸缘部分材料的相对厚度
凸缘部分的相对料厚,即为t/(Df-d)或t/(Rf-r)(t为料厚;
Df为凸缘外径;
d为工件直径;
r为工件半径;
Rf为凸缘半径)。
凸缘相对料厚越大,即说明t较大而(Df-d)较小,即变形区较小较厚,因此抗失稳能力强,稳定性好,不易起皱。
反之,材料抗纵向弯曲能力弱,容易起皱。
(2)切向压应力σ3的大小,拉深时σ3的值决定于变形程度,变形程度越大,需要转移的剩余材料越多,加工硬化现象越严重,则σ3越大,就越容易起皱。
(3)材料的力学性能板料的屈强比σs/σb小,则屈服极限小,变形区内的切向压应力也相对减小,因此板料不容易起皱。
当板厚向异性系数R大于1时,说明板料在宽度方向上的变形易于厚度方向,材料易于沿平面流动,因此不容易起皱。
(4)凹模工作部分的几何形状与普通的平端面凹模相比,锥形凹模允许用相对厚度较小的毛坯而不致起皱。
生产中可用下述公式概略估算拉深件是否会起皱。
平端面凹模拉深时,毛坯首次拉深不起皱的条件是:
用锥形凹模首次拉深时,材料不起皱的条件是:
D,d为毛坯的直径和工件的直径(mm);
t为板料的厚度
如果不能满足上述式子的要求,就要起皱。
在这种情况下,必须采取措施防止起皱发生。
最简单的方法(也是实际生产中最常用的方法)是采用压边圈。
加压边圈后,材料被强迫在压边圈和凹模平面间的间隙中流动,稳定性得到增加,起皱也就不容易发生。
除此之外,防皱措施还应从零件形状、模具设计、拉深工序的安排、冲压条件以及材料特性等多方面考虑。
当然,零件的形状取决于它的使用性能和要求。
因此,在满足零件使用要求的前提下,应尽可能降低拉深深度,以减小圆周方向的切向压应力。
在模具设计方面,应注意压边圈和拉深筋的位置和形状;
模具表面形状不要过于复杂。
在考虑拉深工序的安排时,应尽可能使拉深深度均匀,使侧壁斜度较小;
对于深度较大的拉深的零件,或者阶梯差较大的零件,可分两道工序或多道工序进行拉深成形,以减小一次拉深的深度和阶梯差。
多道工序拉深时,也可用反拉深防止起皱,图4.1.10。
将前道工序拉深得到直径为d1的半成品,套在筒状凹模上进行反拉深,使毛坯内表面变成外表面。
由于反拉深时毛坯与凹模的包角为180°
,板材沿凹模流动的摩擦阻力和变形抗力显著增大,从而使径向拉应力增大,切向压应力的作用相应减小,能有效防止起皱。
冲压条件方面的措施主要是指均衡的压边力和润滑。
凸缘变形区材料的压边力一般都是均衡的,但有的零件在拉深过程中,某个局部非常容易起皱,这就应对凸缘的该局部加大压边力。
高的压边力虽不易起皱,但易发生高温粘结,因而在凸缘部分进行润滑仍是必要的。
2.拉裂与防止措施
拉深后得到工件的厚度沿底部向口部方向是不同的,如图4.1.4所示。
在圆筒件侧壁的上部厚度增加最多,约为30%;
而在筒壁与底部转角稍上的地方板料厚度最小,厚度减少了将近10%,该处拉深时最容易被拉断。
通常称此断面为“危险断面”。
当该断面的应力超过材料此时材料的强度极限时,零件就在此处产生破裂。
即使拉深件未被拉裂,由于材料变薄过于严重,也可能使产品报废。
防止危险断面破裂的根本措施是减小拉深时的变形抗力。
通常是根据板料的成形性能,确定合理的拉深系数,采用适当的压边力和较大的模具圆角半径,改善凸缘部分的润滑条件,增大凸模表面的粗糙度,选用σs/σb比值小,n值和r值大的材料等。
4.2直壁旋转体零件拉深工艺的设计
圆筒形零件是最典型的拉深件,掌握了它的工艺计算方法后,其它零件的工艺计算可以借鉴其计算方法。
下面介绍如何计算圆筒形零件毛坯尺寸、拉深次数、半成品尺寸,拉深力和功,以及如何确定模具工作部分的尺寸等。
4.2.1圆筒形拉深件毛坯尺寸计算
1.拉深件毛坯尺寸计算的原则
(1)面积相等原则
由于拉深前和拉深后材料的体积不变,对于不变薄拉深,假设材料厚度拉深前后不变,拉深毛坯的尺寸按“拉深前毛坯表面积等于拉深后零件的表面积”的原则来确定(毛坯尺寸确定还可按等体积,等重量原则)。
(2)形状相似原则
拉深毛坯的形状一般与拉深件的横截面形状相似。
即零件的横截面是圆形、椭圆形时,其拉深前毛坯展开形状也基本上是圆形或椭圆形。
对于异形件拉深,其毛坯的周边轮廓必须采用光滑曲线连接,应无急剧的转折和尖角。
拉深件毛坯形状的确定和尺寸计算是否正确,不仅直接影响生产过程,而且对冲压件生产有很大的经济意义,因为在冲压零件的总成本中,材料费用一般占到60%以上。
由于拉深材料厚度有公差,板料具有各向异性;
模具间隙和摩擦阻力的不一致以及毛坯的定位不准确等原因,拉深后零件的口部将出现凸耳(口部不平)。
为了得到口部平齐,高度一致的拉深件,需要拉深后增加切边工序,将不平齐的部分切去。
所以在计算毛坯之前,应先在拉深件上增加切边余量(表42.1、4.2.2)。
表4.2.1无凸缘零件切边余量Δh(mm)
表4.2.2有凸缘零件切边余量ΔR(mm)
2.简单形状的旋转体拉深零件毛坯尺寸的确定(图4.2.1)
对于简单形状的旋转体拉深零件求其毛坯尺寸时,一般可将拉深零件分解为若干简单的几何体,分别求出它们的表面积后再相加(含切边余量在内)。
由于旋转体拉深零件的毛坯为圆形,根据面积相等原则,可计算出拉深零件的毛坯直径。
圆筒直壁部分的表面积:
(4.2.1)
圆角球台部分的表面积:
(4.2.2)
底部表面积为:
(4.2.3)
图4.2.1毛坯尺寸的确定
工件的总面积:
则毛坯直径为:
(4.2.4)
(4.2.5)
式中D为毛坯直径(mm);
∑Ai为拉深零件各分解部分表面积的代数和(mm2),对于各种简单形状的旋转体拉深零件毛坯直径D,可以直接按表4.2.3所列公式计算。
表4.2.3常用的旋转体拉深零件毛坯直径D计算公式
其它形状的旋转体拉深零件毛坯尺寸的计算可查阅有关设计资料。
4.2.2无凸缘圆筒形件的拉深工艺计算
1.拉深系数
拉深系数是表示拉深后圆筒形件的直径与拉深前毛坯(或半成品)的直径之比。
图4.2.2所示是用直径为D的毛坯拉成直径为dn、高度为hn工件的工序顺序。
第一次拉成d1和h1的尺寸,第二次半成品尺寸为d2和h2,依此最后一次即得工件的尺寸dn和hn。
其各次的拉深系数为:
(4.2.6)
工件的直径dn与毛坯直径D之比称为总拉深系数,即工件总的变形程度系数。
拉深系数的倒数称为拉深比,其值为:
(4.2.7)
图4.2.2拉深工序示意图
拉深系数是拉深工艺的重要参数,它表示拉深变形过程中坯料的变形程度,m值愈小,拉深时坯料的变形程度愈大。
在工艺计算中,只要知道每次拉深工序的拉深系数值,就可以计算出各次拉深工序的半成品件的尺寸,并确定出该拉深件工序次数。
从降低生产成本出发,希望拉深次数越少越好,即采用较小的拉深系数。
但根据前述力学分析知,拉深系数的减少有一个限度,这个限度称为极限拉深系数,超过这一限度,会使变形区的危险断面产生破裂。
因此,每次拉深选择使拉深件不破裂的最小拉深系数,才能保证拉深工艺的顺利实现。
2.影响极限拉深系数的因素
极限拉深系数mmin与下列的因素有关:
(1)材料方面
①材料的力学性能和组织材料的塑性好、组织均匀、晶粒大小适当、屈强比σs/σb小、塑性应变比值大时,板料的拉深成形性能好,可以采用较小的极限拉深系数。
②毛坯的相对厚度t/D相对厚度t/D小时,拉深变形区易起皱,防皱压边圈的压边力加大而引起摩擦阻力也增大,因此变形抗力加大,使极限拉深系数提高。
反之,t/D大时,可不用压边圈,变形抗力减小,有利于拉深,故极限拉深系数可减少。
③材料的表面质量材料的表面光滑,拉深时摩擦力小而容易流动,所以极限拉深系数可减小。
(2)模具方面
①拉