大容量注射剂生产企业检查要点文档格式.docx
《大容量注射剂生产企业检查要点文档格式.docx》由会员分享,可在线阅读,更多相关《大容量注射剂生产企业检查要点文档格式.docx(10页珍藏版)》请在冰豆网上搜索。
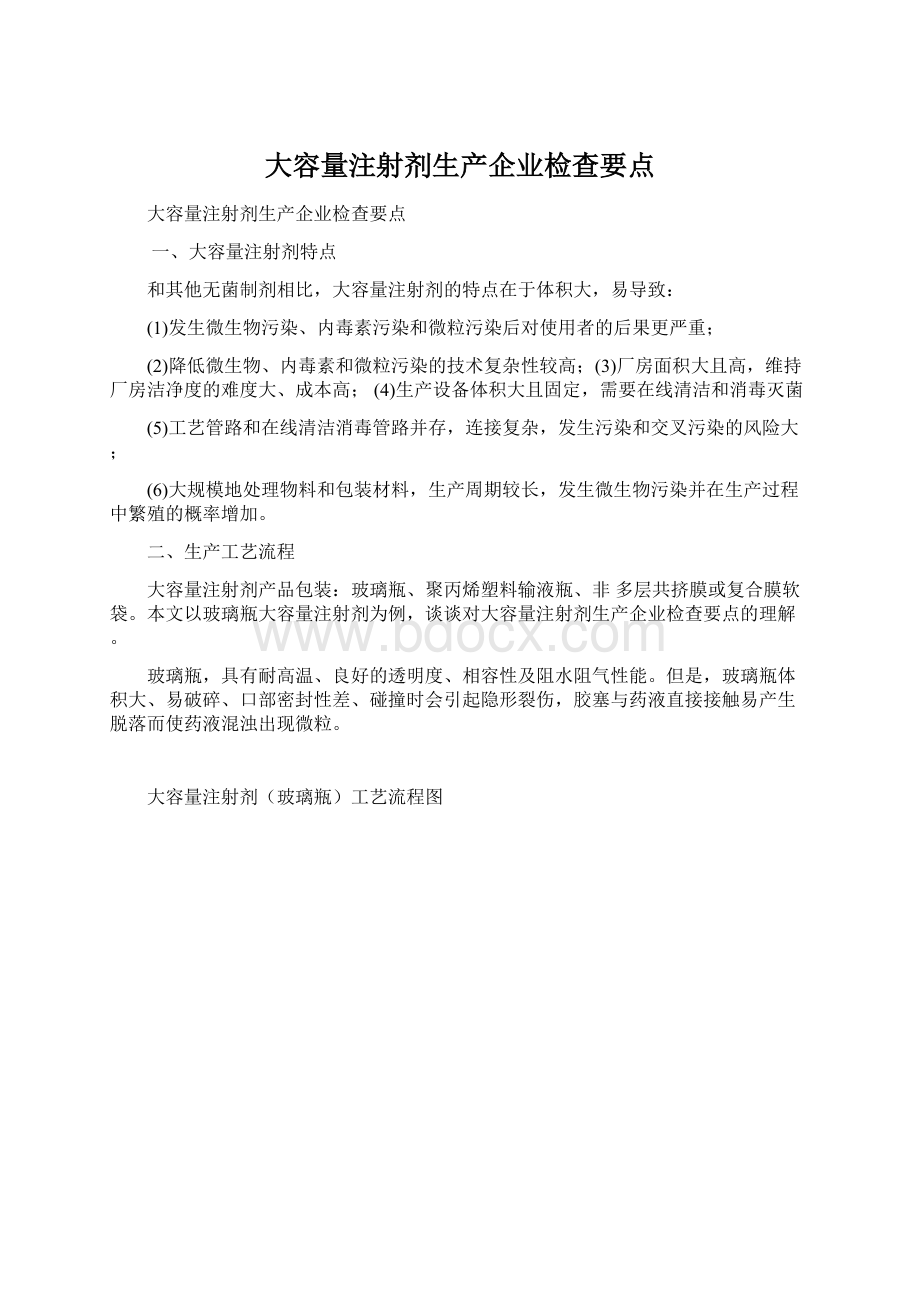
检验检验检验
紫外线消毒
检验
D级区C级区
A级区
(一)原料称重
在D级区进行。
应设计有足够大的待称重原料和己称重原料的存放场地。
称量器具的量程应适用。
同一批产品使用的多种原料应集中存放。
应由中间控制人员对称好的物料及重量进行双重复核。
技术先进的企业已采用计算机化的自动物料识别一重量控制系统代替人工复核。
(二)配制
1.浓配和稀配:
我国大部分企业采用浓配一稀配两步。
通过加入活性炭粉末于热的浓溶液中,以吸附分子量较大的杂质,如细菌内毒素。
但该工艺有明显的缺点:
①活性炭中的可溶性杂质将进入药液而无法除去;
②容易污染洁净区和空调净化系统。
从风险一利益角度,更合理的配制工艺是一步配制。
2.一步配制法目前工业发达国家已普遍取消了加活性炭浓配一过滤一稀配的传统工艺,而采用不加活性炭的一步配制工艺。
一步配制法避免了传统工艺的风险。
采用一步配制法的前提是原料生产企业采用可靠的去除细菌内毒素污染的工艺,如粗品溶解后加活性炭处理后结晶,使活性炭带入的可溶性杂质留在母液中。
原料生产企业还应采取防止微生物污染的措施,能稳定可靠地供应微生物和细菌内毒素污染受控的原料。
配制投料过程中应通过收集核对物料标签等措施进行投料复核,保证原辅料按要求加入。
(三)过滤大容量注射剂通常采用孔径为O.22微米的弹筒式终端过滤器,并配合使用适当的预过滤器,截留溶液中的微粒和微生物。
应在使用前后对终端过滤器进行完整性试验,如发泡点试验,以确保过滤效果。
也有采用两个串联的0.22微米终端过滤器以进一步降低使用过程中过滤器破损的风险。
(四)灌封
1.洗瓶和洗塞:
洗瓶通常采用粗洗一精洗工艺。
粗洗常用毛刷刷洗或超声波清洗,以去除瓶内外壁的各种污染物。
精洗多采用多道注射用水喷射淋洗,以彻底去除污染物。
应对精洗后的输液瓶进行可见异物检查。
2.丁基胶塞使用前应由洗塞机进行清洗,必要时加入一定量的甲基硅油进行硅化。
硅化的目的是防止胶塞粘连,并有利于胶塞在自动压塞机轨道上的运动。
但硅化后的胶塞可能向药液释放微量硅油,并吸附在玻璃瓶壁上造成挂壁现象,虽然对使用者无害,但容易引起输液瓶未洗干净的误解。
经清洗的胶塞如不立刻使用应灭菌。
应采用纯蒸汽,以过度杀灭程序进行灭菌。
对胶塞的灭菌有两种形式:
在洗塞机内在线灭菌和装袋后在灭菌釜内灭菌。
①在线灭菌使用具备在线灭菌的洗塞机时,可采用在线灭菌。
该类洗塞机与纯蒸汽连接。
胶塞清洗完成后,通入纯蒸汽的同时,装置胶塞的篮筐继续转动,保证胶塞均匀受热。
经过度杀灭程序后,用经0.22微米除菌过滤的空气将胶塞吹干、冷却。
完成后在A级层流下装入无菌塑料袋中存放。
由于最后包装染菌的风险较高,胶塞存放时间不宜过长。
②装袋后灭菌经清洗的胶塞,在防止微粒污染的措施下装入可通透水蒸汽的塑料袋中并密封,再放入灭菌设备中灭菌。
经验证的灭菌程序能可靠地杀灭微生物,因此胶塞可存放较长时间。
两种灭菌工艺都应经过验证。
3.灌装与压塞:
灌装和压塞在C级背景下的A级层流下进行。
应采用自动灌装和压塞机完成灌装和压塞过程。
应对灌封环境进行动态监控。
4.轧盖:
轧盖会产生大量金属微粒,对洁净区环境产生影响,故轧盖间的设计应保证压盖过程不污染对环境要求最高的灌装间及灌装过程。
另外,未轧盖的产品,胶塞可能松脱,存在产品污染的风险,因此经灌封的产品应尽快轧盖。
在厂房平面设计和工艺布局设计中必须权衡两方面的风险和利益。
目前实际工业生产中轧盖工序既有设计在与灌装间一墙之隔的D级区的,也有设计在紧邻灌装间的C级区内的。
从尽量降低产品风险且简化洁净区域布局,减少辅助面积的角度,轧盖工序设计在与配制和灌装同一级别C级,这样可以共用一个人员更衣通道,但应做到以下两点,以防止微粒对产品的污染:
①轧盖机和灌装机应分置于两个房间。
②轧盖间对灌装间为相对负压;
或者轧盖机安装在有足够排风的装置内,该装置对其外围环境为相对负压。
可采用其他防止微粒污染风险的措施,但应通过验证证明其有效性。
在完成轧盖进行灭菌前,应根据需要取样监测产品灭菌前微生物污染及污染菌的耐热性。
(五)灭菌
灭菌区应限制无关人员进入。
产品应在规定时间内进行灭菌。
产品灭菌主要有蒸汽灭菌和过热水喷淋或过热水浴三种。
①蒸汽灭菌:
采用清洁蒸汽(工业蒸汽经过滤除去铁锈等异物)为加热介质。
冷却介质为经消毒处理的水。
②过热水喷淋:
采用纯化水为直接接触产品的介质。
在灭菌腔室中加入一定量的纯化水,通过循环泵经喷嘴均匀喷洒在产品上。
纯化水通过由工业蒸汽加热的热交换器达到灭菌需要的温度。
在冷却阶段该纯化水又通过低温水冷却的热交换器降温,并使产品降温。
③过热水浴:
与过热水喷淋相同的加热一冷却原理。
区别在于产品完全浸没在水中。
国际上普遍要求具有防止灭菌后产品二次污染微生物的措施,主要方法有:
①蒸汽灭菌采用的冷却介质为经消毒处理的水,消毒方法主要是化学消毒法,如加入次氯酸,使游离氯浓度达到以上并至少保持1小时,可以杀灭生长态的微生物。
但该方法无法保证杀灭细菌芽孢,可靠性较差,已趋于淘汰。
②过热水灭菌采用的冷却介质即经过腔室-加入热交换器-冷却热交换器-腔室循环的纯化水。
在产品灭菌阶段该纯化水自身也被灭菌,在封闭状态下冷却后依然保持无菌,是最可靠的防止产品二次污染的设计。
③如果能对所有产品进行检漏,确保有密封缺陷的产品能被剔除,则可不控制产品冷却水的微生物污染。
(六)灯检通过灯检剔除个别有异物的产品。
应通过生产工艺及其控制保证产品中有异物的概率很低。
灯检仅为防止有异物产品上市的最后措施。
(七)包装产品经贴标签、装箱后成为成品。
包装线最重要的是防止混淆。
应确保标签正确,批号、生产日期和有效期等信息准确。
产品数、标签消耗数等应合理平衡。
为防止混淆,包装区应防止无关人员进入。
三、工艺布局
大容量注射剂因加工处理的物料量大,在布局时应注意生产现场有足够的空间满足人流和物流的合理流动。
传统灌封工艺包括洗瓶,灌装,加塞三个步骤。
通常洗瓶结束到密封完成需要数秒乃至数十秒的时间,来自环境的微粒和微生物污染的风险较大,应采用C级背景的局部A级保护暴露的容器和药液。
输液瓶经最终清洗后由A级层流保护的传送带送入灌装机。
欧盟对污染风险不高的产品灌装环境要求为C级。
所谓污染风险不高指产品不易长菌、灌装速度很快、采用非敞口的容器、容器暴露于空气数秒以内即密封等情况。
近年国际国内越来越多地采用吹-灌-封系统。
该系统实际上使得容器从高温塑料颗粒制备后即刻完成灌装和密封,与外界几乎没有空气交流。
欧盟允许在D级区安装该系统,用于最终灭菌的大容量注射液的生产。
四、质量风险分析与质量风险控制方法
大容量注射剂质量保证的重点在于无菌保证、细菌内毒素和微粒污染的控制。
此外,防止混淆和交叉污染也需要特别关注。
生产人员的技能、所接受的培训及其工作态度是达到上述目标的关键因素。
生产必须严格按照以风险分析和控制为基础精心设计并经验证的方法和规程进行。
产品无菌或其他质量特性绝不能只依赖于任何形式的最终处理或成品检验。
风险管理的理念应贯穿于生产与质量管理的全过程。
无菌保证的风险主要来自以下四个重要方面,即:
1产品灭菌前微生物污染水平
2灭菌工艺的可靠性
3容器密封完整性
4无菌保证管理体系
每个方面都包含有多个常见的风险因素。
具体的风险因素,不同的企业和生产线各不相同,需要具体问题具体分析。
以下分别论述常见的风险因素及其控制方法。
(一)无菌保证风险与质量风险控制点
1.产品灭菌前微生物污染水平:
产品灭菌前通常都存在一定程度的微生物污染,污染的程度用一瓶产品或单位体积药液中的微生物个数表示。
微生物污染数大致受五类因素影响,分别为:
(1)原材料和包装材料中的微生物:
存在于原材料和包装材料中的微生物可能进入产品。
而固体原料中的微生物分布可能是不均匀的,导致样品检验结果不一定能代表该批原料的整体情况。
质量风险控制方法:
①制定原辅料采购标准,规定微生物限度。
通常应不超过/g,并不得检出致病菌。
②进行供应商的确认时应重点关注供应商的生产过程对微生物污染、细菌内毒素污染、产品混淆和交叉污染风险的控制措施。
③对供应商及其供应的原料进行年度质量回顾分析,以评估其质量状况。
对有质量不良趋势的供应商应采取针对性的措施,如增加现场检查的频率,更严格的抽样方案。
④严格管理仓储条件,确保原料储存过程中质量受控。
如干燥、防虫、防鼠等。
⑤包装材料如玻璃瓶应定点采购,其包装应能防止昆虫进入,储存过程防止受潮长霉。
(2)生产环境:
大容量注射剂的生产从原料称量开始直至完成密封,都分别在相应的卫生洁净区中进行。
上述生产步骤中都存在药物直接暴露于环境的环节,存在来自于生产环境中的微生物污染的风险。
为控制上述风险,国际上较普遍地采用A、B、C、D四个等级的洁净区标准,分别对应注射剂的各生产工序。
其中与大容量注射剂相关的主要为A、C、D三级。
如果能证明在动态下生产区的洁净度能符合上述标准,则来自环境的微生物污染风险是较低的。
然而,目前国内多数企业尚未有计划、有标准地开展对洁净区的动态监控,或者监控计划不够完善。
①洁净区应配置设计良好并经过验证、定期再验证且良好维护的空调净化系统。
洁净区新风和人员数量的关系,应至少达到50457.2008《医药工业洁净厂房设计规范》规定的室内每人新3鲜空气量应不小于40m/h的标准。
②空调净化系统应保证持续稳定地运行。
③空调净化系统停机超出规定时间后,应重新进行洁净区的验证。
④应精心设计、实施动态环境监控方案,保证监控数据能反映洁净区的实际情况。
⑤每年对环境监控结果进行环境质量统计分析。
⑥根据环境质量统计结果制定、修订环境监控警戒标准和纠偏标准,确保能及时发现、纠正环境恶化的趋势。
⑦养成良好的个人卫生习惯和意识,即环境监控取样时段与非取样时段的行为一致⑧制定明确规定发生诸如停电、空调净化系统故障、环境超标等偏差后相应的措施。
(3)生产设备:
大容量注射剂通常采用固定的设备,安装了生产及在线清洗、消毒等多种工艺管道。
因此设备存在残留微生物的可能,对产品有潜在风险。
质量风险控制方法①设备在线清洁和在线灭菌的方法应足够详细,应包含所有影响清洁效果的参数,如水温、清洁剂浓度、流速、时间、阀门的开闭次序和时间、蒸汽温度、压力等的书面规定,以确保清洁效果的重现性。
②设备清洁与灭菌方法,包括清洁、灭菌后最长存放时间应经过验证。
③认真执行、记录清洁和灭菌过程,发生偏差应及时调查、纠正。
④应制定