5NC加工基本操作流程PPT推荐.ppt
《5NC加工基本操作流程PPT推荐.ppt》由会员分享,可在线阅读,更多相关《5NC加工基本操作流程PPT推荐.ppt(22页珍藏版)》请在冰豆网上搜索。
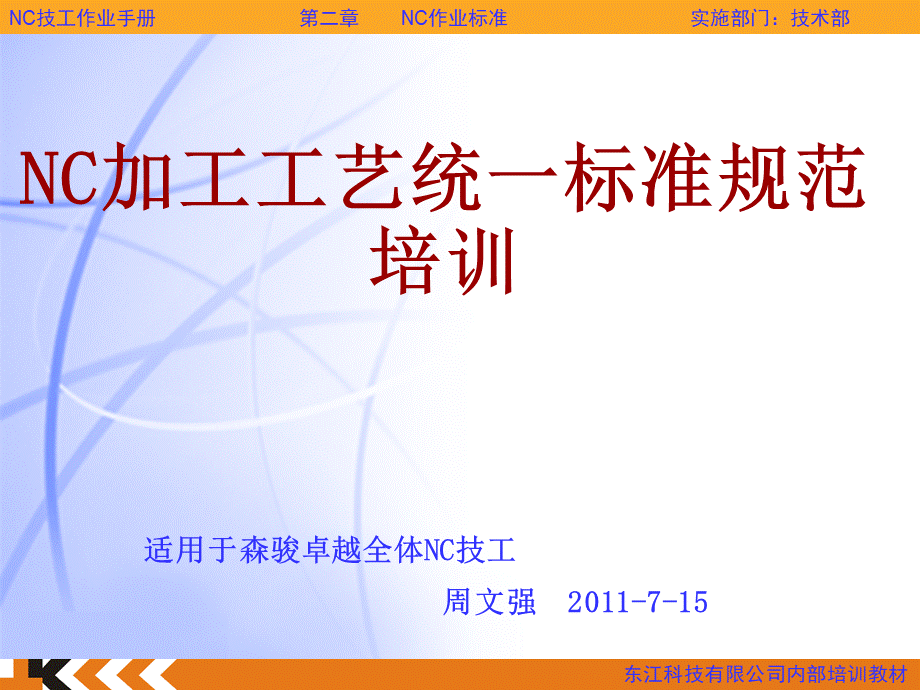
所有脚仔、底板未经部门负责人确认不可擅自翻磨,已经翻新的须作好标示并单独摆放。
以防使用时混淆。
二、加工前准备工作标准规范,1、接到工作编排表时,首先根据模号确定图纸、工件及程序单三者齐全相符,如三者模号、形状、材料、尺寸大小等。
2、查看本部网络上是否有此工件的程序,若没有则要及时通知相关人员,以避免工件上机后才发现,而造成停机等待。
3、
(1)根据图纸、程序清单所标基准及碰数方式,核对工件底部所标识的基准角是否正确;
(2)据程序清单的摆向、碰数方式、基准角及工件的基准和现状,确认碰数方式是否合理,并用白油笔在工件的顶部标出工件的基准角、向出方向。
对于尚未开粗的工件须明确其顶部的余量,已淬火的工件须明确其实际余量;
(3)根据程序清单、工件的现状明确工件装夹方式的合理性及安全性。
准备要用到的夹具、较表、卡尺、分中棒等。
工件面应用油石推掉毛边及碰坏的位置;
(4)依据程序清单,结合电脑图档对相关程序进行刀路模拟。
若上述(4)项有不明确、不清楚的地方,如:
没有图纸,图纸不明确,工件上未标明基准角或无明显标识辨别摆放方向,碰数、取数方式不合理,程序选用之刀具或走刀方式不合理等,要立即通知小组负责人或其它相关人员,以便作出明确指示,确认无误之后方可上机加工。
三、上机装夹标准规范,1、工件上机时应根据工件长、宽、高,确定机床行程及承载量是否满足要求,严禁超负荷加工。
2、根据程序单基准、运水方向以及工件尺寸之数据进行收夹工件,必须注意工件尺寸数据的写法为X、Y、Z(长*宽*高),同时,须核对程序单与散件图形是否相符,以及X、Y轴的摆放方法。
3、铜公装夹则要检查其开料尺寸是否有足够余量,对于一板收多件铜料的情况,应检查其方向是否正确,各铜料加工时是否干涉,粗、精(幼)公的字唛要分清并在程式单注明每件铜公的坐标,避免出现混乱现象。
对于需使用3R夹具的,须注意夹持部位以上的部分是否满足最大加工深度。
4、工件上机,应尽量选择靠边的位置,在装夹时应尽可能使X方向的基准面同机台的T型槽平行,以减少拖表次数)以防在加工过程中出现突发问题时,可以再装其它工件或插入其它急件进行加工,避免不必要的时间浪费。
5、码码仔时,注意程序中安全高度的设定及工件的形状,确保刀具在运行过程中畅通无阻;
必要时可与编程师沟通,要求编程明确标出装夹位置;
对于须底部垫高加工的工件,则码仔必须对准垫正方之位置,以达到受力均衡之目的。
6、对于大工件的装夹,同事间应积极协助以减少上机装夹时间。
7、检查所吊完工件的吊令有无松开取走(Y轴方向),避免不小心碰伤或撞伤Y轴合页、Z轴防护罩;
对于卧式机床尽可能用钩链将工件固定在机床上,以防因码仔断裂或其它突发事故而造成工件下滑。
四、较表标准规范,1、较表前应再次确认摆放方向,图纸与程序单及工件基准摆放方向是否一致。
2、较表保证所拖的面为基准面,要先较平与Z轴垂直的基准平面(即与机台平面相互平行的工件表平面或底平面)然后再较平与X轴方向或Y轴方向平行的基准面;
对于水平和垂直度存在偏差的工件,应立即与制作部相关人员沟通,确定采用何种方法进行较表以减少碰数误差或退回相关部门返工。
3、较表前应先把压住收板或脚仔的码仔稍微收紧,(其它装夹方式除外)4、较表时应尽量朝里敲向出的一边,并将另一边轻轻压住,避免反向敲打或人站在机床面上从里向外敲打工件。
5、拖表时校表不能松动或被压死,且应尽量以最少的次数和时间完成工件的较正,最后以对角方式轮流夹紧工件。
6、夹紧工件时,如须接驳螺杆,上下螺杆须用连接套连接,每只螺杆旋入部分应各占连接套的二分之一,中间不可有空隙,不能选择已损丝杆或只收螺纹的少部分,以防在加工中工件受震动,螺杆滑牙松脱造成工件位移。
7、夹紧工件后应再次拖表验证,看是否会因压紧后有变动,8、大工件应采用大较表进行较正,避免采用加长索柄吸小较表的方式,完成校表后应采用手动的方式将机头及较表升到安全高度(比工件最高面高出10mm以上)才能按快速键将机床归零位。
五、分中碰数标准操作规范,1、分中前一定要看清程序单上的要求,是分中、单边还是偏中,若为单边碰数要切记补回分中棒半径(注:
分中前主轴转速可设置为S=400转)。
2、若为分中则应利用程序单上的标数进行碰数,并尽可能在MDI方式下使用G91GOOX或Y/Z,以减少计算时间和失误;
Z轴能够用同一深度分中的尽量采用同一深度分中并利用分中棒在同一侧面靠近两端位置碰两次数,进行比较以验证其拖表水平度是否水平。
3、分中碰数完后须进行复检,对于300X300以上的工件复检时,尽可能要另一位同事或小组负责人代替,检查要以第一次分中的中心为基准,然后同一条轴中出两边碰数,看绝对坐标正、负两个数是否相符,若其中一条轴的正、负两个数不相符,则证明这条轴的分中数不正确。
如:
复检时得出X轴的正、负两个数为50。
5与-50。
5,Y轴为30。
4与-30。
6,则Y轴分中不正确。
复检完毕须签名确认;
如复检后仍出错(未复检出来的错),两个人须扣绩效分。
4、铜公分中,一般情况对于正方铜料,可在空余时间先用卡尺测量铜料并按尺寸大小先画出中心交点线,待上机后用尖刀对准交点直接设为加工中心。
(注:
为粗皮料即可使用)对于返锣铜公一定要利用分中棒碰数。
5、单边碰数的复检可将分中棒在工件边上移行1/2半径,看分中棒的中心是否在工件的边上,若程序单上要求进行偏数的,切记要偏好数后再抄座标中心数。
6、对已加工完成的孔或镶件进行检测,以确前后程序的中心吻合。
六、加工操作标准规范,1、按照程序单所标的刀径及最大加工深度进行装夹,索刀的长度应比加工深度略长3-4毫米左右,采用加长索咀时,索刀长度要根据所加工位置的深度值相对于第一个最高面(即是加长索咀的端面有可能碰到的那一个面)来计算索头长度。
2、须用于精加工的刀具必须经过刀库检测或使用较表自测后,才能使用。
3、计算对刀数要根据图纸核对程序单要求,应看清楚是底取数还是顶部取数,若为底面取数则应考虑收板或脚仔的高度,可把实际测出的脚仔或板的高度写在程序单上,对刀数计算必须利用笔算或计算器辅助计算,将计算过程写在程序单空余位置,以便复查计算过的数据是否正确。
4、对好刀后Z轴不动,Z轴相对座标清零,输入对刀数后,返回到综合座标面页,按面板上的RESET复位键,观看Z轴相对座标值是否为零,绝对座标值和对刀数是否相符或对完刀后将刀尖放到工件的顶部或有基准数据位置,复检对刀是准确5、碰完数后移动机头时应采用手摇的方式将机头升高超过安全高度,再用快速键,将主轴抬起。
机床的主轴应停止转动。
七、加工标准规范,1、查看程序中的主轴转速和F进给量,可根据刀具切削进给参数表和所加工的材料及加工内容,对加工参数进行调配,如有重大出入的应反映给编程师进行更改;
如对刀具使用有疑问的应在加工前了解清楚。
2、第一刀加工时,根据情况可先吊高行走一刀空刀,看看加工环境、加工位置,核对程式名、刀具直径,检查刀长补、刀径补、转速等是否有错误,如果一切正常,然后再降回实际高度重新启转,控制“快移”调至25%及进给调至0%,一手放在暂停掣上,另一手控制进给速度,当刀具十分接近工件面时可停止,注意核对Z轴的剩余行程,待加工切削行顺及稳定后,再将各控制调回正常状态。
3、淬火工件光刀时,NC技工不能自己留淬火余量,按程序单数即可(淬火前已开过粗的工件)第一刀必须先提高1-2mm,看开粗的余量有多少或变形大小,对于变形较大的工件应及时与相关人员进行沟通,确定如何进行加工,再降回到实际高度加工,否则,这种情况很容易出现蹦刀、断刀、偏位事故。
4、加工过程式中应对转速及进给速度进行密切监控,发现有不适当之处及时进行调整,以防止出现效率低或因转速过高而造成刀具的浪费,无论开粗或光刀时,如遇到有急转弯或转角的地方,进给速度要进行适当调慢,以免在这些地方发生弹刀而造成磞刀或工件过切现象。
5、如加工中需要重新索刀、重新对刀的,一定要看清楚绝对座标值所显示的对刀数是否正确,对于OKK机床,须在MDI的模式下输入M05或MO9(主轴停止或切削油停止),取消超前预读,输入的对刀值才有效。
6、对于程序单上特别容易看错的刀具,可建议编程师用颜色笔将它们区分出来,如:
D16R0.8和D16R8,D20R5和D25R5一些相同类似的R刀,一定要特别注意。
7、对于大工件开完粗后一定要用较表进行检查,看是否有松动走位现象。
8、工件进入正常加工阶段后,了解并检查剩下程序的走刀方式及用刀是否合理,准备并装好下一条程序所用的刀具,应充分利用空余时间将上机的工件做好准备工作。
8、若在加工中插入其它急件时,要先等加工中的程序走完,在这一部分时间内把机床上未做完的工件座标值、刀具补正值抄下来反复核对并记录下来,并将已加工程序和未加工程序明确分开,待加工完急件后再抄回这些数据确认无误后再继续加工。
9、工件分型面需复检而没有做程序复检的,所有NC技工有责任要求编程师多做一条程序进行复检或进行自检。
八、下机标准规范,1、下机前应确定所有程序都已加工完毕,并依照图纸对工件进行全面检查,如一些细小的槽沟、骨位、角位以及需接顺的地方,每个位置是否加工到位,是否有弹刀、过切等现象,确认无误后方可下机。
2、较大及重要工件下机前应通知相关人员,须注意安全并保护好工件,以防划花工件,同时做好工件和机床的5S。
3、NC加工、锣床加工、车床加工、线割加工的所有电极,如果是简单的电极且有编程师标出的可测数据,全部由操作人员自检并在电极尺寸简图上签名,自检结果由工组长或制作组长审核,合格后才能上EDM加工;
复杂的电极,则提交QC检测,(QC仅检测加工人员无法测出的部分)合格后才能上EDM加工,不合格交品质部主管处理;
对于下机的铜公,如果有其它原因导致与编程所标数据不相符时(例:
料不够大,手锣正边位),须在QC简图的相应位置标出实际数据并签名确认。
(所有检查人的签名必须使用正楷字,所有加工后的电极尺寸简图必须保留,以备检查,此检查流程已获各制作部经理、品质部主管确认。
),操作要则:
渐序渐进,切忌急功近利。
连环紧扣,防止遗忘错漏。
深思熟虑,做到计划周详。
知根知底,做到胸有成竹。
先知先觉,措施防患未然。
此次培训到此结束!
谢谢大家的参与!