eg04三缸发动机缸盖加工工艺本科论文文档格式.docx
《eg04三缸发动机缸盖加工工艺本科论文文档格式.docx》由会员分享,可在线阅读,更多相关《eg04三缸发动机缸盖加工工艺本科论文文档格式.docx(20页珍藏版)》请在冰豆网上搜索。
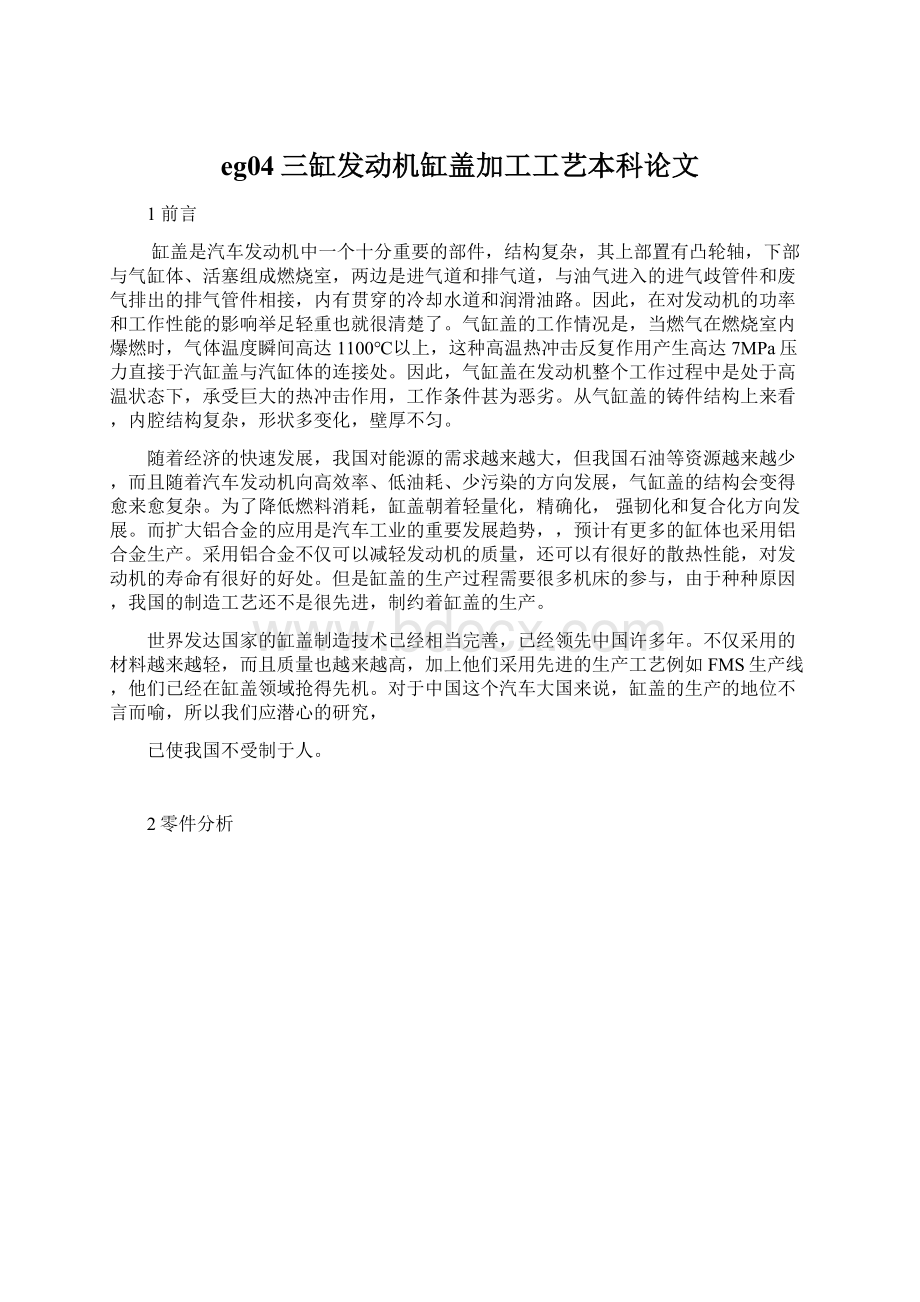
已使我国不受制于人。
2零件分析
2.1缸盖功用
汽车发动机缸盖是发动机的主要零件之一,如上图。
位于发动机的上部,其底平面经气缸衬垫用螺栓紧固在缸体顶面上,主要功用如下:
1封闭气缸上部,并与活塞顶部和汽缸壁一起形成燃烧室;
2作为顶置气门发动机的配气机构,进气管和出水管的装配基体;
3汽缸盖内部有冷却水套,其底面上的冷却水孔与缸体冷却水孔相通,以便利用循环水套冷却燃烧室等高温部分。
2.2结构特点
缸盖应该具有足够的强度和刚度,以保证在气体的压力和热应力的作用下可靠的工作。
他与汽缸垫的结合面应具有良好的密封性,其内部的进排气通道应使气体通过时流动阻力最小,还应冷却可靠,并保证安装在其上的零部件能可靠的工作;
缸盖形状一般为六面体,系多孔薄壁件,其上有气门座孔,气门导管孔,汽油机的火花塞孔,柴油机的喷油器孔,还有各种孔及螺纹孔等。
2.3工艺性分析
缸盖的基本加工工序分为平面加工,一般孔加工,高精度孔加工。
2.3.1平面加工工序
缸盖的顶面、底面和排气管结合面等都是大面积的平面,精度要求高,又是全部工艺过程中的工艺基准,所以这些大面积平面的加工工序应注意合理的安排工艺顺序和采用高效率的加工方法。
其中缸盖的上结合面即顶面如上图,对它有较高的要求,表面粗糙度为3.2um,平面度的要求为0.08mm,与下结合面的位置度要求为0.1mm。
所以可先进行粗铣加工,最后在进行半精铣
缸盖的下结合面即底面如下图,对它的要求更高,表面粗糙度为1.6um,平面度要求为0.05mm,位置度要求为0.4mm,可对它进行粗铣,在其它加工加工工序结束后,再进行精铣
2.3.2高精度孔的加工工序
缸盖上的气门座孔,导管孔和凸轮轴孔等都是孔系,有配合关系,其尺寸精度,位置精度和表面粗糙度要求极为严格,所以这些高精度孔系的加工工序是缸盖工艺的核心工序,应给予充分的注意。
其中进、排气门座孔ø
310+0.025如下图,其表面粗糙度值为0.8um,与基准的位置度要求为ø
0.2mm,孔轴线的平行度要求为ø
0.05mm,圆柱度值为0.01mm。
可先进行粗镗孔,在进行精镗,最后在磨孔。
进气孔旁的一个孔如下图,加工精度要求也挺高并且很复杂,位置度要求为ø
0.2mm,表面粗糙度为1.6um,其加工工艺为先钻孔ø
11,然后再扩孔至ø
14,最后再铰孔。
2.3.3一般孔的加工工序
精度要求不是特别高的孔加工比较简单,例如排气孔面的5×
ø
8螺纹孔的加工,其加工工序如下:
先用钻头钻深20,然后直接攻丝,深16即可。
3工艺流程设计
3.1毛坯的制造形式
此缸盖的材料为压铸铝合金ZALSi5Cul-Mg,批量生产,采用低压铸造,充型平稳,工艺出品率高,铸件轮廓清晰,力学性能好。
3.2基准的选择
选择定位基准是制定工艺过程中首要解决的问题,合理的基准可以使加工质量得到保证,生产效率提高。
3.2.1粗基准的选择
(1)如果必须首先保证工件上加工表面与不加工表面之间的位置要求,应以不加工表面为粗基准;
如果在工件上有很多不需加工表面,则应以其中与加工表面的位置精度要求高的表面作为粗基准[1];
(2)如果必须首先保证工件某重要表面的余量均匀,应该选择该表面作为粗基准。
[1]
(3)选作粗基准的表面,应平整,没有浇口,冒口或飞边等缺陷,以边定位可靠。
(4)粗基准一般只能使用一次,以免产生较大的位置误差。
经过分析选用一面两销定位方式进行定位,粗基准为上结合面和火花塞孔。
3.2.2精基准的选择
精基准的选择原则
(1)应尽可能选用设计基准为定位基准,实现基准重合,以免产生基准不重合误差,这叫座基准重合原则;
(2)应尽可能选用统一的定位基准加工各表面,以保证各表面的位置精度,
同时还可以减少工装设计费用,提高生产效率,避免基准转换误差,称为统一基准原则;
(3)为了获得均匀的加工余量或较高的位置精度,可遵循互为基准原则,反复加工的原则;
(4)有些精加工工序要求加工余量小而均匀,以保证加工质量和提高生产效率,这时以加工表面作为精基准面,称为自为基准原则该加工表面与其他面的位置精度要求由先行工序保证。
精基准也选用一面两销定位方式,下结合面和它面上的两个2×
10对角孔。
3.3加工阶段的划分
零件的加工质量要求较高时,必须把整个加工过程划分为几个阶段:
1)粗加工阶段,在这一阶段要切除较大的加工余量,加工变速箱箱体时,主要是粗铣前后端面及粗镗各孔。
2)半精加工阶段,在这一阶段应为主要表面的精加工阶段作好准备(达到一定的
加工精度,保证一定的精加工余量),并完成一些次要表面的加工(钻孔、攻螺纹、
铣键槽等),一般在热处理之前进行。
3)精加工阶段保证各主要表面达到图样规定的质量要求。
4)光整加工对于精度要求很高、表面粗糙度值要求很小的零件,还要有专门的光整加工阶段。
光整加工阶段以提高零件的尺寸精度和降低表面粗糙度为主,一
般不用于提高形状精度和位置精度。
3.4加工顺序的安排
3.4.1切削加工顺序
1)先粗后精。
先安排粗加工,中间安排半精加工最后安排精加工和光整加工。
2)先主后次。
先安排主要表面的加工,后安排次要表面的加工。
3)先基面后其他。
加工一开始,先把精基面加工出来。
如果精基面不止一个,则
应按照几面转换的顺序和逐步提高加工精度的原则来安排基面和主要表面的加工。
4)先加工平面后加工孔。
箱体类零件的加工应遵循先面后孔的原则:
即先加工箱体上的基准平面,以基准平面定位加工其他平面。
然后再加工孔系。
其次,先加工平面可以先切去铸件表面的凹凸不平。
为提高孔的加工精度创造条件,便于对刀及调整,也有利于保护刀具。
5)为保证加工质量的要求,有些零件的最后加工必须放在部件装配后或在总装过
程中进行。
3.4.2热处理工序
EG04三缸缸盖采用的是铸造铝合金,由于铸造后会有残余应力,力学性能还没达到最佳,需进行热处理。
铝合金铸件的热处理就是选用某一热处理规范,控制加热速度到某一相应温度下保温一定时间并以一定的速度冷却,改变其合金的组织,其主要目的是提高合金的力学性能,曾倩耐腐蚀性能,改善加工性能,获得尺寸的稳定性。
对于铝合金,它经过淬火后,强度与硬度并不会立即升高,至于塑性非但没有下降,反而有所上升,但放置一段时间(4~6昼夜后),强度和硬度会显著提高,塑性
明显降低。
淬火后铝合金的强度、硬度随时间增长而显著提高的称为时效。
时效可以在常温下发生,称为自然时效。
该缸盖选用的材料是铸造铝合金ZALSi5Cul-Mg,缸盖工作时由于燃烧产生大量的
热量,温度高,所以必须要经过热处理,选用T7处理。
先淬火处理,加热温度为525±
5℃,保温时间为3—5h,冷却水温度为60—100℃;
然后进行时效处理,加热温度为240±
10℃,保温时间为3—5h,采用空气冷却。
3.4.3辅助工序
如检验,在零件全部加工完毕后、各加工阶段结束时、关键工序前后,都要适当安排。
其他辅助工序还有清洗、去毛刺、表面处理、气密试验、包装等,也应按其要求加入工艺过程。
3.5机床的选择
机床选择原则
1)机床主要规格的尺寸应与工件的轮廓尺寸相适应。
即小的工件应选择小的规格
2)的机床加工,而大的工件则选择大规格的机床加工,做到设备的合理使用。
3)机床的结构取决于机床规格尺寸、加工工件的重量等因素的影响。
4)机床的工作精度与工序要求的加工精度相适应。
根据零件的加工精度要求选择机床,如精度要求低的粗加工工序,应选择精度低的机床,精度要求高的精加工工序,应选用精度高的机床。
5)机床的功率与刚度以及加工范围应与工序的性质和最合适的切削量相适应。
如粗加工工序取出的毛坯余量大,就要求机床有大的功率和较好的刚度。
6)装夹方便、夹具结构简单也是选择数控设备最需要考虑的一个因素。
选择采用卧式加工中心,还是选择立式加工中心,将直接影响所选择的夹具的结构和加工坐标,直接关系到数控编程的难易程度和数控加工的可靠性。
根据以上原则可选择出以下各机床:
本次加工的是缸盖,需要加工的面有六个,有顶面,底面,两个侧面,前后面,各个表面上还有很多需要加工的孔,螺纹孔,为了提高加工精度,减小误差,方便加工,提高生产效率,加之前面通过对零件的分析,加工工序复杂,且类型多,所
以选择卧式加工中心MA—400HA。
其参数如下:
工台面积400×
400mm
XYZ轴行程分别为560mm、610mm、625mm
主轴最高转8000rpm
刀库容量30把
主轴电机15/11kw(vac)
占地面积2394×
4532mm2
3.6工艺路线的制定
3.6.1制定工艺路线时需要注意的问题
工艺路线的制定是工艺规程的设计过程中的重要的一步。
制定工艺路线的出发点
应当是使零件的几何形状、尺寸精度及位置精度等技术要求得到合理保证。
在生产纲领以确定为大批生产的条件下,通过对缸盖的分析,可以考虑采用卧式加工中心,卧
式加工中心配以专用夹具,并尽量采用工序集中的原则来提高生产效率。
此外,还应
当从企业经济环境和使用环境等诸多因素方面进行具体分析,使生产成本尽量降到最低。
因此我们需要从以下几个方面来考虑:
1)对于那些加工精度要求较高和粗糙度值要求较低的零件,在制定工序时常常
需要将其划分为粗加工和精加工两个阶段;
对于加工精度要求很高、粗糙度值要求很低的零件,则常需要划分为粗加工阶段、半精加工阶段、精加工阶段和光整加工阶段。
因为缸盖表面最高的表面粗糙度要求为Ra=3.2μm,精加工就可以达到技术要求,所以零件加工时将各个表面的粗精加工分开进行,可以将整个工艺过程划分为粗加工、半精加工、精加工阶段就可以了,不必进行光整加工阶段。
但是对于表面粗糙度要求更高的孔。
2)充分的分析和研究零件图,并参考同类零件的加工方法,对各表面选择相应的加工方法,选择合理的加工顺序,并将工艺过程划分为若干个工序,划分工序时采用工序集中的原则,因为这样可以减少工件的装夹次数,在一次装夹中可以加工许多表面,有利于保证各表面之间的相互位置精度,也可以减少机床的数量,相应地减少工人