连杆螺钉课程设计报告Word下载.docx
《连杆螺钉课程设计报告Word下载.docx》由会员分享,可在线阅读,更多相关《连杆螺钉课程设计报告Word下载.docx(30页珍藏版)》请在冰豆网上搜索。
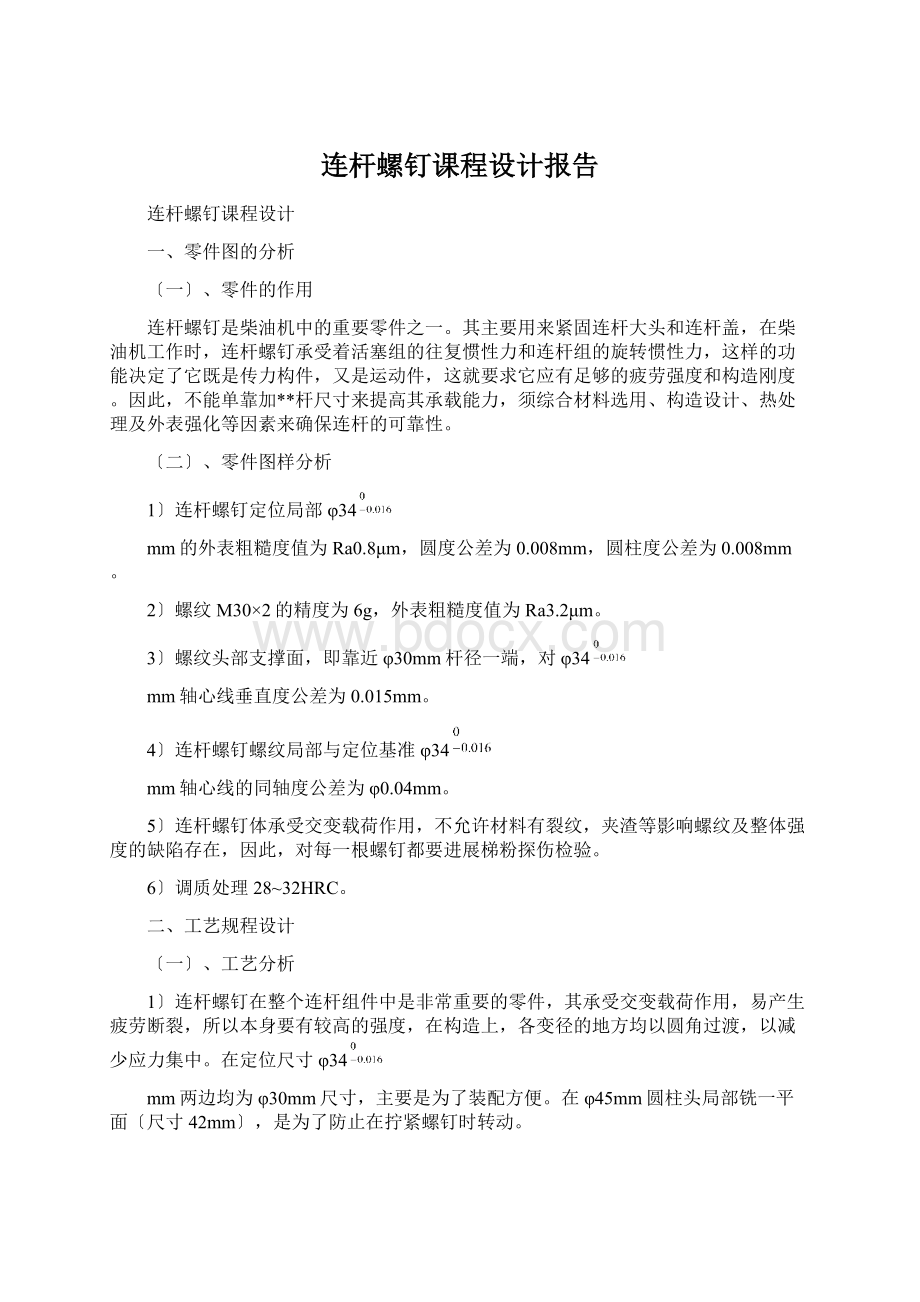
〔一〕、工艺分析
1〕连杆螺钉在整个连杆组件中是非常重要的零件,其承受交变载荷作用,易产生疲劳断裂,所以本身要有较高的强度,在构造上,各变径的地方均以圆角过渡,以减少应力集中。
在定位尺寸φ34
mm两边均为φ30mm尺寸,主要是为了装配方便。
在φ45mm圆柱头局部铣一平面〔尺寸42mm〕,是为了防止在拧紧螺钉时转动。
2〕毛坯材料为40Cr锻件,根据加工数量的不同,可以采用自由锻或模锻,锻造后要进展正火。
锻造的目的是为了改善材料的性能。
下料尺寸为φ60mm×
125mm,是为了保证有一定的锻造比,以防止金属烧损,并保证有足够的毛坯用料量。
3〕图样要求的调质处理应安排在粗加工后进展,为了保证调质变形后的加工余量,粗加工时就留有3mm的加工余量。
4〕连杆螺钉上不允许留有中心孔,在锻造时就留下工艺留量,两边留有φ25mm×
7.5mm工艺凸台,中心孔钻在凸台上,中心孔为A2.5。
5〕M30×
2-6g螺纹的加工,不宜采用板牙套螺纹的方法〔因为这种方法达不到精度要求〕。
应采用螺纹车刀,车削螺纹。
6〕热处理时,要注意连杆螺钉的码放、不允许穿插放置,以减小连杆螺钉的变形。
7〕为保证连杆螺钉头部支撑面〔即靠近φ30mm杆径一端〕对连杆螺钉轴心线的垂直度要求,在磨削φ34
mm外圆时,一定要用砂轮靠端面的方法,加工出支撑面来,磨削前应先修整砂轮,保证砂轮的圆角及垂直度。
8)对连杆螺钉头部支撑面(即靠近φ30mm杆径一端)对中心线垂直度的检验,可采用专用检具配合涂色法检查图2-5。
专用检具与连杆螺钉φ34
mm相配的孔径应按工作实际公差分段配作。
检验时将连杆螺钉支撑面涂色后与专用工具端面进展对研,当连杆螺钉头部支撑面与检具端面的接触面在90%以上时为合格。
图2-5连杆螺钉垂直度检具
技术要求
1、φ34mm尺寸分为三个尺寸段,
φ34
mm、φ34
mm
2、热处理56~62HRC。
3、材料GCr15。
9〕连杆螺钉M30×
2-6g螺纹局部对φ34
mm定位直径的同轴度的检验,可采用专用检具图2-6和标准V形块配合进展。
1、调质处理28~32HRC。
2、材料40Cr。
专用检具特点是采用1:
100的锥度螺纹套。
要求螺纹套的外径与内螺纹中心线的同轴度公差在零件同轴度误差1/2*围内,以消除中径加工的误差。
检查方法是先将连杆螺钉与锥度螺纹套旋合在一起,以连杆螺钉φ34
mm为定位基准,放在V形块上(V形块放在标准平板上),然后转动连杆螺钉,同时用百分表检测锥度螺纹套外径的跳动量,其百分表读数为误差值(图2-7)。
图2-7连杆螺钉同轴度检验方法
(二)、制定工艺路线
连杆螺钉的加工工艺路线一般是先进展外形的加工,再进展孔、槽等加工。
连杆的加工包括各侧面和端面的加工。
按照先加工基准面及先粗后精的原则,其加工可按下面工艺路线进展。
又因为此零件要求批量生产,所以工序安排要求较集中以提高生产率。
除此之外,还应该考虑经济成果,以便使生产本钱尽量下降。
1、工艺路线方案一:
工序一:
下料,棒料尺寸为φ60mm×
125mm
工序二:
锻造,自由锻造成形,锻件尺寸:
连杆螺钉头部为φ52mm×
27mm部为
φ41m×
183mm,零件总长为210mm〔留有工艺余量〕
工序三:
正火处理
工序四:
调质处理28~32HRC
工序五:
划毛坏两端中心孔线,照顾各局部加工余量
工序六:
钻两端中心孔A2.5,也可以在车床上加工
工序七:
粗车,夹φ37mm外圆,车另一端毛坯外圆φ52mm至φ48mm
工序八:
粗车,以φ52mm×
27mm定位夹紧〔毛坯尺寸〕,顶尖顶紧另一端中心孔,以
毛坯外圆找正,将毛坯外圆φ41mm车至φ37mm,长度185mm
工序九:
精车,修研两中心孔。
夹紧φ48mm〔工艺过程尺寸〕,顶紧别一端中心孔,
车工艺凸台〔中心孔处〕外圆尺寸至φ25mm,长7.5mm,车φ37mm外圆至
φ35mm,长178.5mm
工序十:
精车,夹φ35mm(垫上铜皮),车工艺凸台〔中心孔局部〕φ25mm×
7.5mm,
尺寸φ48mm车至图样尺寸φ45mm,倒角1×
45°
工序十一:
精车,以两中心孔定位,卡环夹紧φ45mm外圆,按图样车连杆螺钉各部尺寸至图样要求,其中φ34
mm处留磨量0.5mm,保证连杆螺钉头部φ45mm长15.1mm总长190mm,螺纹一端长出局部车至φ25mm,车螺纹局部至φ30
工序十二:
以两中心孔定位装夹,磨φ34.5mm尺寸至图样要求φ34
mm,同时磨削φ45mm右端面,保证尺寸15mm
工序十三:
夹紧φ34
mm外圆〔垫上铜皮〕,并以外圆找正,车螺纹M30-6g,倒角1×
工序十四:
用V形块或组合夹具装夹工作,铣φ45mm处42mm尺寸为〔42±
0.1mm〕
工序十五:
用专用钻模或组合夹具装夹工件,钻2×
φ6mm孔〔以〔42±
0.1〕mm尺寸定位〕
工序十六:
用V形块或组合夹具装夹工作,铣螺纹一端中心孔工艺凸台,与螺纹端面平齐即可。
注意不可碰伤螺纹局部
工序十七:
用V形块或组合夹具装夹工作,铣另一端工艺凸台,与φ45mm端面平齐即可。
注意不可碰伤倒角局部
工序十八:
按图样要求检验各部,并进展磁粉探伤检查
工序十九:
涂防锈油、包装入库
2、工艺路线方案二:
125mm
27mm,杆
局部为φ41m×
183mm,零件总长为210mm〔留有工艺余量〕
粗车,夹φ37mm外圆,车另一端毛坯外圆φ52mm至φ48mm
调质处理28~32HRC
夹紧φ48mm〔工艺过程尺寸〕,顶紧别一端中心孔,车工艺凸台〔中心孔处〕外圆尺寸至φ25mm,长7.5mm,车φ37mm外圆至φ35mm,长178.5mm
7.5m,尺寸φ48mm车至图样尺寸φ45mm,倒角1×
精车,夹紧φ34.5mm外圆〔垫上铜皮〕,并以外圆找正,车螺纹M30-6g,倒角1×
0.1mm〕〔为以下工序中用〕
3、工艺方案的比拟与分析:
方案一是先进展调质处理再进展毛坯尺寸加工,加工过程中先进展粗车,再根据尺寸要求将定位尺寸进展磨削。
接着进展其它尺寸的处理,最后加工时先进展铣φ45mm处的42mm尺寸〔42±
0.1mm〕以及钻2×
φ6mm孔,之后再铣两端的工艺凸台,最后检验,入库。
这种做法,本想先进展定位尺寸的加工,以使之后的尺寸加工更加准确,但这样会导致之后的加工使磨削变得毫无意义,粗糙度更无法保证。
而且,在进展凸台处理与平面铣削和钻孔加工时,其顺序有些不太合理。
方案二则与方案一有所区别,是先进展毛坯尺寸加工再进展调质处理,其次在粗精车时,先车出工艺凸台,通过中心孔的定位,按图样车连杆螺钉各部尺寸至图样要求〔其中φ34mm处留磨量0.5mm〕,接着夹紧φ34.5mm外圆,车图示螺纹及倒角,之后再进展φ34.5mm外圆和φ45mm右端面的磨削。
最后加工时先铣削两端的工艺凸台,之后再进展铣φ45mm处的42mm尺寸〔42±
0.1mm〕以及2×
φ6mm钻孔,最后检验,入库。
从以上两种工艺加工路线分析中可知:
工艺路线方案二比拟好。
因为它更清晰具体地说明了该工件的加工所需步骤路线,它的加工路线更为准确,加工顺序更为精细合理,能够更好地到达所要求的加工标准。
因此,最后确定的加工路线为方案二,即如下表2—3的加工工艺过程卡:
表2-3连杆螺钉机械加工工艺过程卡
工序号
工序名称
工序内容
工艺装备
1
下料
棒料φ60mm×
锯床
2
锻造
自由锻造成形,锻件尺寸:
27mm,杆部为φ41mm×
锻
3
热处理
热
4
划线
5
钻
C620
6
粗车
以φ52mm×
27mm定位夹紧〔毛坯尺寸〕,顶尖顶紧另一端中心孔,以毛坯外圆找正,将毛坯外圆φ41mm车至φ37mm,长度185mm
7
夹φ37mm外圆,车另一端毛坯外圆φ52mm至φ48mm
C620
8
9
精车
修研两中心孔。
10
夹φ35mm(垫上铜皮),车工艺凸台〔中心孔局部〕φ25mm×
7.5mm,尺寸φ48mm车至图样尺寸φ45mm,倒角1×
。
11
以两中心孔定位,卡环夹紧φ45mm外圆,按图样车连杆螺钉各部尺寸至图样要求,其中φ34
12
夹紧φ34.5mm外圆〔垫上铜皮〕,并以外圆找正,车