传动杆零件的机械加工工艺规程设计文档格式.docx
《传动杆零件的机械加工工艺规程设计文档格式.docx》由会员分享,可在线阅读,更多相关《传动杆零件的机械加工工艺规程设计文档格式.docx(25页珍藏版)》请在冰豆网上搜索。
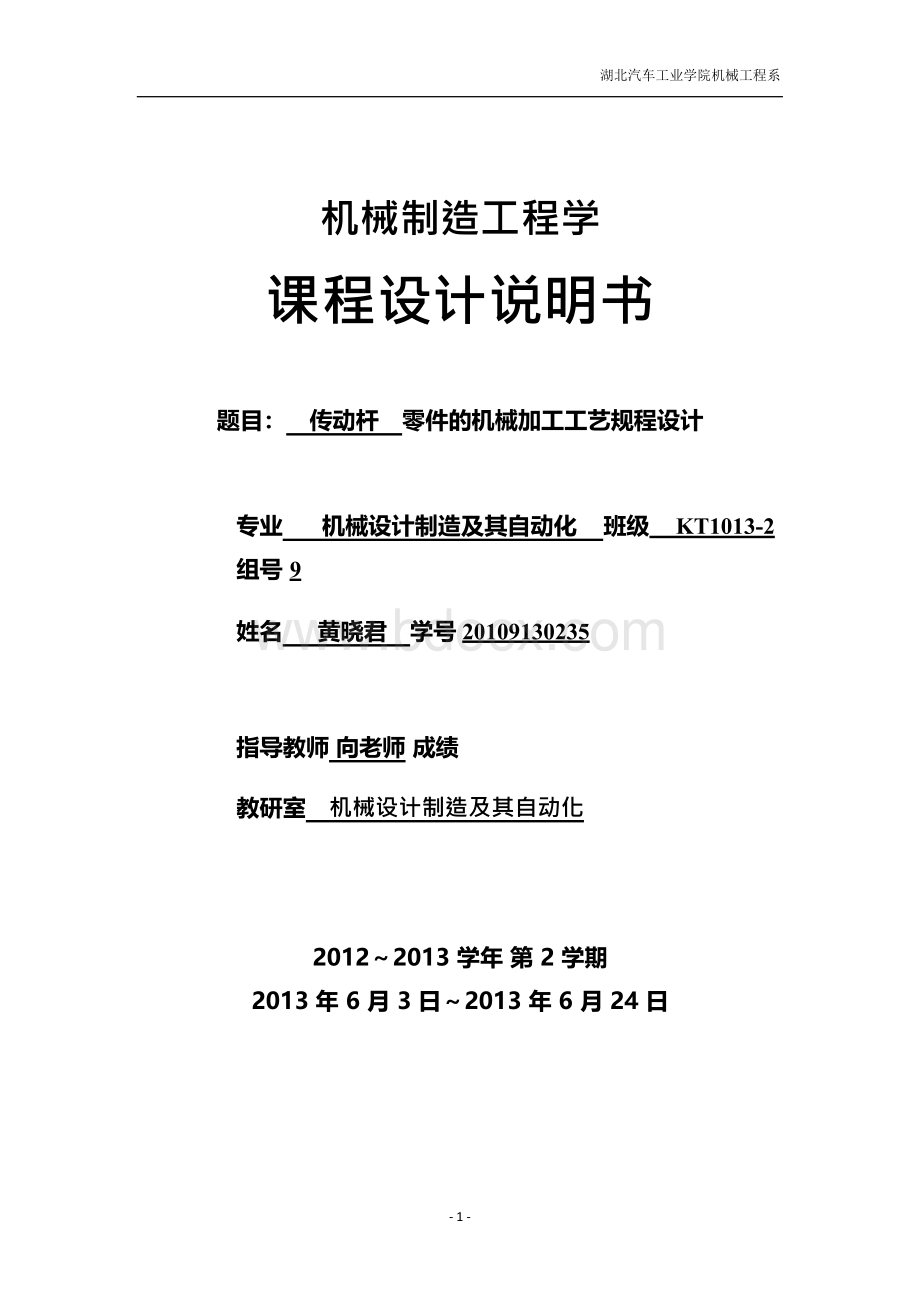
第一章零件生产纲领类型和分析 3
1.1确定生产纲领和类型 3
1.2零件工艺分析 3
第二章毛坯选择与毛坯图说明 5
第三章加工工序、方案和尺寸的确定 6
3.1零件表面加工方法的选择 8
3.2零件的工艺路线的制订 8
3.3工序间尺寸,公差,表面粗糙度及毛坯尺寸的确定 8
3.4加工余量,切削用量,工时定额的确定 11
第四章、夹具设
计 19
第五章总结 23
附 参考文献 25
课程设计任务书
题 目:
设计 传动杆 零件的机械加工工艺规程
内
容:
1
绘制零件图(按1︰1的比例)
张
2
绘制毛坯图(按1︰1的比例)
3
填写零件机械加工工艺规程卡片
套 (包括:
机械加工工艺过程卡片1套,机械加工工序
卡片1套)
4 编写零件课程设计说明书 1
份
原始资料:
零件图样1张;
零件生产纲领为10000件/年;
每日1班。
25
第一章 零件生产纲领类型和分析
1.1确定生产纲领和类型
如图所示的传动杆零件图,该零件的产量为10000件/年,设其零件备品率为10%,机械加工废品率为1%,制订该零件的机械生产纲领。
N=Qn(1+a)(1+b)
=10000*1.1*1.01
=11110件/年
已知该零件为轻型零件,根据生产类型与生产纲领的关系,可确定其生产类型为大批量生产。
图1.1传动杆零件图
1.2零件工艺分析
零件的作用:
零件的结构特点:
如图1.1所示,传动杆是一个结构简单的零件,总共有六处需要加工。
分别为:
一个下端面,两个
Φ60,Φ25的上圆柱端面,两个Φ36,,Φ15孔,一个键槽。
三个端面及键槽的粗糙度度都是Ra3.2μm,要求不高。
两个内孔的粗糙度为Ra1.6μm,要求较高,加工时需要注意。
其它面的粗糙度没有要求。
零件的结构工艺分析:
传动杆结构简单,外表面粗糙度没有要求,可以考虑采用铸造。
在精度、公差方面,Φ36、Φ15两个孔的粗糙度为Ra1.6μm,且与下端面有垂直度公差,同时下端面是两个上圆柱端面的定位基准,所以在加工时应该以下端面为粗基准待两个上端面加工完成后,再精加工下端面。
下端面的粗糙度为
Ra3.2μm,采用粗铣、半精铣的过程就可以满足要求。
Φ36的孔有加工尺寸公差且粗糙度为Ra1.6μm,故其加工要求较高,采用粗镗、半精镗的过程可以达到要求。
键槽直接采用插键槽的工序就可以。
Φ15的通孔,加工尺寸公差相比于Φ36的通孔更小,并且加工前其为盲孔,所以可以采用钻、扩、粗铰、精铰四步工序来加工
关键表面的技术要求分析:
传动杆的零件图上没有关键表面技术要求,毕竟这只是个普通的简单零件,要求不多,所以只要在最后去毛刺,校验即可。
,
。
第二章 毛坯选择与毛坯图说明
毛坯的选择:
由于毛坯的选择要考虑零件的力学性能要求,零件的结构形状和外轮廓的尺寸,零件生产纲领和批量以及现场生产条件和发展等。
考虑该设计零件的以上因素,该毛坯的制造方法选用金属型铸造。
金属型铸造可降低铸件的公差等级,使其表面光滑减少加工余量。
金属型铸造毛坯的公差等级为7-9级,我们选择是
IT8.材料选用HT200,其工艺性能是流动性能好,体收缩小,线收缩也小,偏析倾向小,铸造应力小等优点。
其切削加工性能一般。
其力学性能中抗拉极限强度为200Mpa,冲击韧度很低。
传动杆毛坯图2.1
分析该零件的加工要求确定其毛坯的尺寸为:
下端面A,上端面B和C,加工精度不高,需要的加工工序也不多,所以其加工余量不易太大。
孔D的加工精度是较高的,加工工序较多,故其加
工余量相应的需要增大。
其它的面不属于加工面,其加工余量可以不留,直接为铸造尺寸即可。
最后综合选用各面加工余量为:
A面,B面和C面加工余量
2.5mm,D内圆面单面加工余量为3.8mm,其它不加工面为0.5mm即可。
确定圆角和拔摸斜度及分型面:
由于该铸件的尺寸较小,为保证各加工余量直接选择圆角R1为4mm,R2为5mm。
分析该毛坯的结构知拔斜度为外表面和内孔面,查表2.2-8得拔摸斜度为1°
第三章加工工序、方案和尺寸的确定
3.1零件表面加工方法的选择
该零件的加工面主要是端平面,孔,键槽。
材料为HT200,参考有关设计手册和资料,其加工方法选择如下:
(1)下端面:
未标注尺寸公差,规定其公差等级为IT14,表面粗糙度为Ra3.2μm,需要进行粗铣、半精铣。
(2)Φ60的上圆柱端面:
(3)Φ25的上圆柱端面:
(4)Φ36孔:
上偏差为0.027μm,下偏差为0,表面粗糙度为Ra1.6μm,需要粗镗,半精镗。
(5)Φ15孔:
上偏差为0.019μm,下偏差为0,表面粗糙度为Ra1.6μm,需要进行钻孔、扩孔、粗铰、精铰。
3.2零件的工艺路线的制订
零件的工艺路线的制定要考虑的因素很多,为了制定出更好的工艺路线需要先拟制出多种工艺路线,同时结合先加工基准面先粗后精,基准统一等原则将这几种路线进行比较,从中找出较好的一种,结合该零件的各因素现拟制以下两种工艺方案进行比较:
方案一:
(以零件图所示)
以下端面A为粗基准:
粗铣、半精铣上圆柱面B和C
以上端面B为基准:
粗铣、半精铣下端面A
以下端面A为基准:
粗镗、半精镗Φ36的孔
钻、扩、粗铰、精铰Φ15的孔
在Φ36的孔中插槽
去毛刺
方案二:
以壁厚为20mm的非加工台阶面为粗基准:
以下端面A为精基准:
粗铣、半精铣圆柱面B
和C
粗镗、半精镗
Φ36的孔
钻、扩、粗铰、精铰
Φ15的孔
插键槽
方案三:
以圆柱面B为粗基准:
粗铣,半精铣下端面A
粗细,半精铣圆柱面A
和B
先在B面上找正,后粗镗,半精镗孔至Φ36
在Φ36的孔中插键槽
先在C面上找正,钻、扩、粗铰、精铰孔至Φ15
通过比较以上三种方案,第一种方案在加工工艺和加工的难易程度等方面上都优于另外两种方案,因此第一种方案较好。
3.3工序间尺寸,公差,表面粗糙度及毛坯尺寸的确定
本零件各圆柱表面的工序加工余量、工序尺寸及公差、表面
粗糙度见下表:
表1:
外圆柱面φ60上圆柱面加工余量计算
工
序
表面粗糙度
Ra/μm
工序基
标注工序
工序名
工序间
本尺寸
尺寸公差
称
余量/mm
经济精度/mm
/mm
半精铣
IT12
3.2
70
70~70.3
71
粗铣2
1.5
IT14
6.3
72
72~72.74
粗铣1
73.5
毛坯
±
1.6
75±
表2:
外圆柱面φ25上圆柱面加工余量计算
26
27
28
29.5
31±
1。
1.3
表3:
下端面加工余量计算
工序名称
工序间余量/mm
工序基本尺寸
标注工序尺寸公差
表4:
Φ36孔的加工余量计算
半精镗
IT7
36
34.3~34.4
粗镗
IT11
35
32.