工装检具规范.docx
《工装检具规范.docx》由会员分享,可在线阅读,更多相关《工装检具规范.docx(22页珍藏版)》请在冰豆网上搜索。
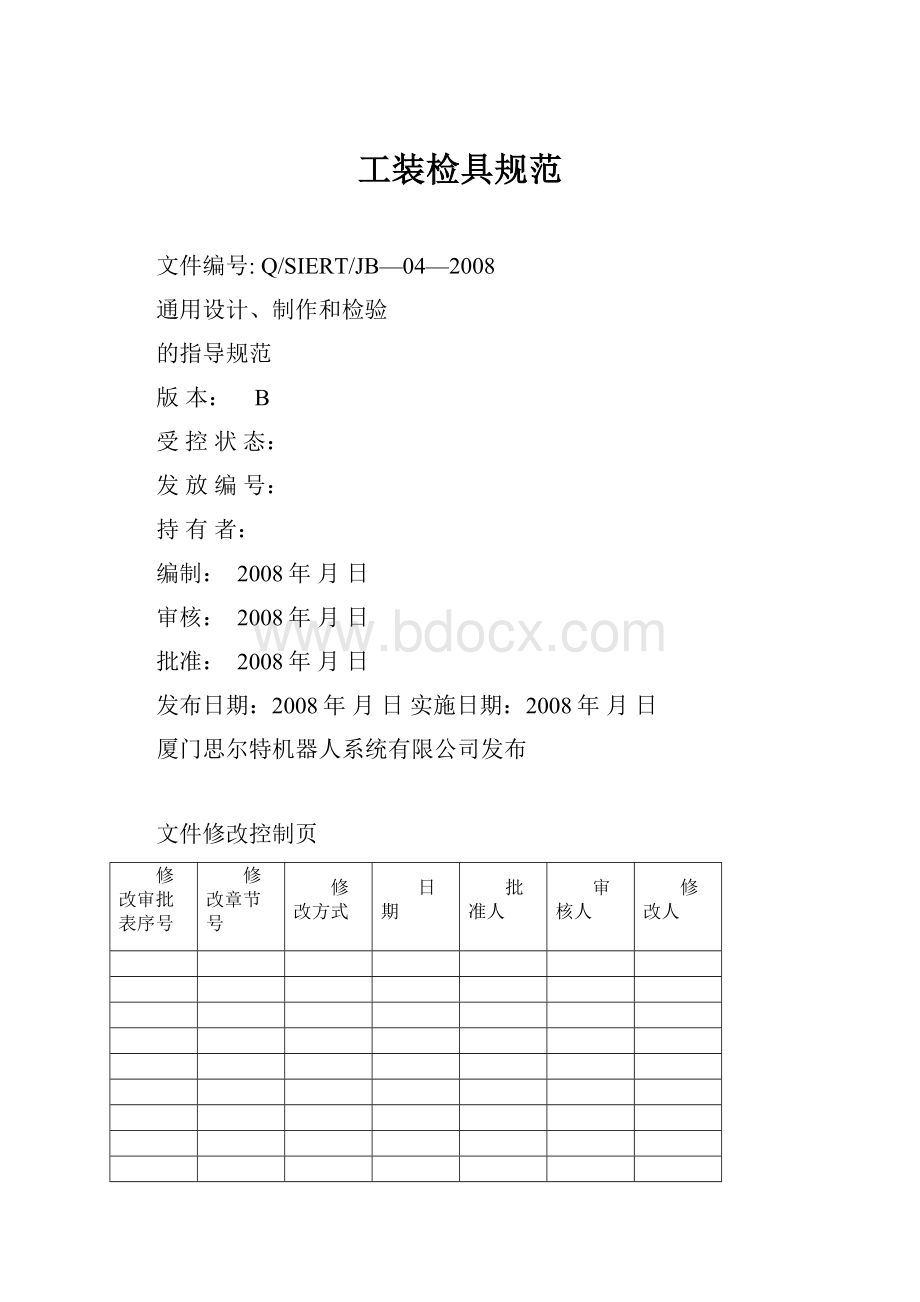
工装检具规范
文件编号:
Q/SIERT/JB—04—2008
通用设计、制作和检验
的指导规范
版本:
B
受控状态:
发放编号:
持有者:
编制:
2008年月日
审核:
2008年月日
批准:
2008年月日
发布日期:
2008年月日实施日期:
2008年月日
厦门思尔特机器人系统有限公司发布
文件修改控制页
修改审批表序号
修改章节号
修改方式
日期
批准人
审核人
修改人
目次
1.适用范围…………………………………………………………………………………………4
2.引用标准…………………………………………………………………………………………4
3.设计………………………………………………………………………………………………4
3.1.设计依据………………………………………………………………………………………4
3.2.检具的一般结构………………………………………………………………………………4
3.3.工装的结构形式………………………………………………………………………………6
3.4.机架的一般做法………………………………………………………………………………7
3.5.尺寸公差及表面粗糙度选择…………………………………………………………………8
3.6.材料及热处理选用……………………………………………………………………………9
3.7.电气相关要求…………………………………………………………………………………9
3.8.机械设计的其他要求…………………………………………………………………………9
4.制作………………………………………………………………………………………………10
5.外协加工要求……………………………………………………………………………………11
6.检验………………………………………………………………………………………………11
6.1.检验依据………………………………………………………………………………………11
6.2.检测法…………………………………………………………………………………………11
6.3.线形尺寸检测…………………………………………………………………………………11
6.4.形状和位置公差检测…………………………………………………………………………11
6.5.表面粗糙度的评价……………………………………………………………………………12
6.6.常用金属材料表面硬度测定…………………………………………………………………12
附录一检测规制作公差带的确定…………………………………………………………14
附录二检测规测量面的表面粗糙度………………………………………………………16
附录三千分尺和游标卡尺的不确定度……………………………………………………16
附录四指示表的不确定度…………………………………………………………………16
附录五计量器具不确定度的允许值………………………………………………………17
1.适用范围:
规范专用于协富光洋公司的设备、检具、工装的设计、制作及检验。
2.引用标准:
GB/T3177-1997《光滑工件尺寸的检验》
GB1957-1981《光滑极限量规》
GB/T1958-1980《形状和位置误差公差检测规定》
GB/T1031-1995《表面粗糙度参数及其数值》
3.设计
3.1.设计依据
3.1.1.设计任务书
设计任务书应给出设备、工装、检具的设计方案,明确设备、工装、检具的功能要求、性能参数,以及对定位基准、夹紧方式和夹紧力、生产率等的一般性要求,和客户要求的其他事项。
3.1.2.工件图纸
工件图纸应包含有工件轮廓和主要表面(如定位表面、夹紧表面、待加工/检测表面),完整标注有被加工/检测表面的尺寸公差等技术要求、加工要求、以及相应的基准面等信息。
3.1.3.设计过程中出现的问题,由设计者向业务人员提出沟通解决。
3.2.检具的一般结构
检具的结构形式可参考采用下列样式之一,或采用下列样式的组合。
3.2.1.内孔、轴类线性尺寸使用止通规方式检测
(1)内孔尺寸使用塞规检测
无特别要求时,塞规的通规与止规应分置塞规手柄的两端、或制成两件。
检验直径3~50mm的塞规一般采用滚花手柄与两端的锥柄测头组合的形式,锥柄锥度为1∶50;止规要比通规短,通规的长度不小于被测表面的配合长度;为便于更换通规,在手柄靠近通规测头锥柄尾部处开孔,如下图:
止通规的工作尺寸及制作精度按附录一确定。
(2)轴类尺寸使用卡/环规检测
轴类尺寸原则要求使用环规检测,通规的长度不小于配合长度,止规比通规短。
在保证轴的形状误差不致影响配合性质的条件下,允许以卡规代替环规:
片形双头卡规用于1~50mm的轴的检测,其厚度为2~5mm;圆片形单头卡规用于1~300mm的轴的检测,其厚度为2~20:
3.2.2.外形长度尺寸检测
外形长度尺寸检测采用检具座与塞规结合的方式,被测件置于检具座内,一端靠紧、另一端使用止通规进行检测。
止通规应在零件图上给出止端与通端的名义尺寸,最后加工尺寸应在检具装配完成后测量确定。
也可单独使用检具座,并将塞尺的尺寸检测功能改由其中的一端板承担,如下图所示。
使用此种方式应注意可能因被测件的歪斜影响测量结果的正确性。
3.2.3.孔距线形尺寸检测
孔距线性尺寸的检具结构示意如下图,以基准孔或基准面定位,按被测孔距、在被测孔位处使用检测塞规(装置于检测孔内)进行孔距符合性的检测。
检测塞规的名义尺寸=被测孔内径的名义尺寸-孔距的偏差值
工件中与被测孔距有关的尺寸公差,不论是单向的还是双向的公差,都应化为双向对称分布的公差。
如:
孔距的尺寸公差
应化为±、
应化为±,以及作为检具对应的名义尺寸。
当以孔的内表面作为定位基准时,为消除孔径偏差对孔距测量的影响,基准孔的定位销可采用锥销。
锥销高度等于圆柱销高度或不超过圆柱销高度的倍,锥销小径为基准孔最大实体尺寸、锥销大径为基准孔最小实体尺寸+。
例:
用于φ
孔的锥销大径为φ,小径为φ。
当采用锥销定位时,应注意被测件孔径偏差可能导至放置歪斜的情况。
3.2.4.孔距径向距离检测
孔距沿径向分布的角度检测,检测方法如下图示意,以基准孔定位,将被测孔的角度公差转化为线性公差进行检测。
检测塞规的名义尺寸=D-d
φD为被测孔名义尺寸
φd=2Rsin(
Δα),式中R=被测件半径、Δα=被测孔的角度偏差值
其余参照。
3.3.工装的结构形式
3.3.1.工装按用途划分,有溶接、压装、组合、孔位确认等类型,按定位方式有内/外孔与轴肩端面定位、内孔表面及其端面共同定位、外圆定位(采用V形块或U形槽)等方式。
3.3.2.内孔与轴肩端面定位,用于轴线高度及轴向位置的确定,有时可利用工件特点限制其在圆周方向的位置,一般用于孔位确认等:
3.3.3.内孔表面及其水平端面共同定位,用于承受大的压力,借助工件的特点或其他定位方式确定其圆周方向,一般用于压力装配:
3.3.4.使用V形块、或U形槽用于轴线或圆心的定位,一般用于装配组合。
无精度及强度要求的垫块,其材料可用尼龙等软材料制作。
3.3.5.具体工装采用的结构,须根据其特定任务要求,参考上述方式、并结合以下要求选择合理、简便的方式:
(1)工件的定位要符合六点定位原理;
(2)工装的夹紧力应通过或靠近主要支撑点,夹紧力应垂直于主要定位基准。
一般应进行夹紧力的分析和计算,以确定夹紧元件和传动装置的主要尺寸。
3.4.机架的一般做法
3.4.1.无特别要求时,机架采用50×50×3方管焊接制作;
3.4.2.机架一般采用如下图的结构形式:
(1)开关高度指按钮开关的面板高、拨动开关拨杆的中间高;
(2)启动开关架样式按协富光洋的样式;
(3)小件料架直立边高200、底边长430;
(4)机架宽度以保证其上装置不超出机架范围为原则、取小值;
(5)调整脚垫规格M12×100,安装螺孔位于机架底面的三角钢板上;
(6)调整支撑柱高度以保证工件中心高900、机架台面高750;
(7)电箱一般设置在操作面板下方,地位不够时应设置在机架后下方。
3.5.尺寸公差及表面粗糙度选择
3.5.1.固定的定位元件与安装孔的配合采用H7/m6(包括定位销),表面粗糙度为。
3.5.2.可换的定位元件与安装孔的配合采用H7/f7,表面粗糙度为。
3.5.3.定位元件的工作表面与其定位面的尺寸公差采用h6,表面粗糙度为。
3.5.4.重要的滑动配合采用H7/g6(如检测塞规导向运动段),表面粗糙度为。
3.5.5.一般的滑动配合可采用H9/f9(如工装的普通轴与套),表面粗糙度为。
3.5.6.检测规工作面的尺寸公差按附录一确定,表面粗糙度按附录二。
3.5.7.无相对运动的一般安装结合面采用自由公差,表面粗糙度按。
3.5.8.检测规工作段的形状和位置误差的公差值为检测规制造公差的50%,并且限制在检测规的尺寸公差带内。
当检测规制造公差≤时,其形位公差为。
3.5.9.以工件内孔或外圆表面作为定位基准的工装/检具,其相关零部件的形位公差要求应根据特定要求从下列中选择提出:
(1)工装/检具上的定位表面对其中心线的同轴度;
(2)工装/检具上的定位表面与其轴向定位轴肩的垂直度;
(3)工装的定位表面对其在设备上安装定位基面的垂直度或平行度;
(4)各定位表面间的垂直度或平行度;
(5)定位表面对安装基面的垂直度或平行度。
3.5.10.以工件端面、底面等平面作为定位基准的工装/检具,其相关零部件的形位公差要求应根据特定要求从下列中选择提出:
(1)工装/检具定位表面对其安装基面的平行度或垂直度;
(2)定位表面的平面度(直线度)或支撑件的等高性;
(3)定位表面间的垂直度和平行度;
(4)定位表面对找正基面的平行度或垂直度。
3.5.11.定位元件之间、孔与孔之间、定位元件与孔之间的距离和相互位置(如同轴度、平行度、垂直度等)的公差,一般取为工件上相应公差的三分之一,并向临近的标准等级靠级圆整。
3.5.12.工装/检具零件上
(1)相应于工件自由公差的直线尺寸公差可取为±;
(2)相应于工件无角度公差的角度公差可取为±10′;
3.5.13.检具/工装基座(或安装板)上的找正基面,与基座(或安装板)上安装其他元件的平面的垂直度误差≤,找正基面本身的直线度、平面度误差≤。
3.6.材料及热处理选用
3.6.1.不与工件直接接触的底板、基座等可选用Q235-A;
3.6.2.与工件直接接触的定位元件、定位面、螺纹调节机构等应采用45钢或碳素工具钢。
材料热处理一般为淬火,表面硬度依使用场合,45钢可从HRC28~48中选取、碳素工具钢为HRC52~62。
3.6.3.在图样上标注热处理硬度值的波动范围为4~5个HRC单位。
3.6.4.工装/检具中精度要求较高的重要元件(如检测规),为保持精度,应采用T10A或Cr12等其他适宜的材料制造,检测规测量面的硬度应为HRC58~63。
3.7.电气相关要求
3.7.1.操作面板上的常规按钮须统一,元件保证一致性。
3.7.2.启动开关应采用OMRONWLCL-2N或其他品牌的相应型号。
3.7.3.电控箱门及设备上开设的门均应配置弹簧锁。
3.7.4.设备如需配置光栅,一般选用SUNX的NA2系列。
3.8.机械设计的其他要求
3.8.1.设计须考虑零件更换的方便性,及零件调整的可能性。
3.8.2.总装配图的主视图应选取面对操作者的工作位置。
3.8.3.总装配图上的尺寸标注
(1)外形轮廓尺寸;
(2)可动部件的最大活动范围(直线运动部件的前后、左右、上下,旋转运动部件的活动半径和转动角);
(3)工件定位基准与定位元件间的配合尺寸以及定位元件之间的位置尺寸(相关尺寸的精度必须依照方案图中的标注);
(4)工装/检具与外部的联接尺寸,或安装尺寸。
3.8.4.工装/检具中具有导向、定位作用的零件,必须于零件图上、在其纵横基准的交汇处明确标示出所选取的设计基准(在角上画一φ2的小圆,并标注“基准标识”字样),并在装配图上标注出相应的装配位置关系。
3.8.5.矩形塞规的四角应设计成倒45°角的样式,不采用圆角方式。
3.8.6.检具上的独立检测规应在尾部设计有链条安装孔(如φ3),检具底板的相应位置也须设计有链条安装孔(如M4)。
3.8.7.零部件的表面处理应在零部件图样的技术要求中提出:
(1)检具/工装表面一般采用表面发黑处理;
(2)启动开关安装架采用喷漆(协富光洋公司的草绿色);
(3)较大的结构件表面采用喷漆(协富光洋公司的草绿色)。
3.8.8.装配定位的元件,应采用定位销定位方式,定位销的数目不得少于2个,且应分布在紧固螺钉的对称方向上。
定位销的首选规格:
直径6、公差m6的圆柱销,地位局限时可使用直径5、公差m6的圆柱销。
3.8.9.底板等安装基础的销孔孔距在图样中只给出名义尺寸,另一边的销孔应标注为配作。
3.8.10.快速换模板尺寸:
×
×
3.8.11.工装/检具各元件间的联接一般采用M8的圆柱头内六角螺钉,也可选用其他类型规格的紧固件。
3.8.12.工装/检具上应用的夹钳,首选嘉手牌,压头与工件接触处需采用较软的材料(如铜或尼龙)。
3.8.13.工装的运动配合部位应设计成可减少摩擦的机构(如采用铜套等)。
3.8.14.设备如设置有油压表,油压表应朝向便于操作者观测的正面。
3.8.15.设备两侧不允许开门、不要设置需要进行操作调整的装置。
4.制作
4.1.设备、工装、检具上所用的推栓,要指定专人制作以保证一致性。
4.2.除非特别要求,所有零件的棱边均须倒角,锐角须倒钝。
4.3.检具中设计有链条安装孔的检测规,须用链条将检测规与底板联接。
4.4.零件图上标注有“基准标识”字样的零件,其加工尺寸的基准要与设计基准相同,并在零件表面的相应位置打一样冲眼作为标志,装配时必须遵照设计确定的位置关系。
4.5.工装/检具的装配应以工件实物为依据校正综合精度要求;缺乏实物工件的,应借助辅助检具或其他方法校正各单项精度要求。
装配调整可采取包括修配的方式进行。
4.6.采用定位销定位的元件,其一边的销孔可在零件制作时加工,另一边的销孔须于装配调整达到图样要求的尺寸公差和位置精度后配作。
所有销孔均为铰制孔(H7)。
4.7.工装上的气动配管一般采用φ8(外径)软管,进气为蓝色、出气为红色。
用于熔接或焊接工装的气动配管须采用双层阻燃软管。
4.8.在搬运、装配过程中应轻拿轻放,装配时不得使用重锤击打零件。
4.9.零部件在生产装配过程中不允许磕碰、划伤和锈蚀。
4.10.已完成表面处理的零部件,应采取适当措施进行保护,防止表面的碰伤和刮擦,受损外观应在出厂前修复。
4.11.出货前,气动二联件(或三联件)的油雾器中须加注润滑油至标定位置。
4.12.电气布线的线槽应尽量宽松。
4.13.电气布线须在端子处配置线号管,并在传感器和电磁阀等处注明PLC上相应的输入输出号或名称。
4.14.控制柜中元件具有DIN轨安装方式的,须采用DIN轨安装。
4.15.不允许使用粘座固定电气布线或气管。
4.16.电气线路不允许与油管捆扎在一起。
5.外协加工要求
5.1.零部件外协加工时,须特别要求加工方按图要求对工件进行倒角。
5.2.外协加工项目应附带相关加工的检验报告作为验收参考,外协加工件回厂后,应按其图样对外协加工项目进行复核检验。
6.检验
6.1.检验依据:
检验测量依据零部件图样进行。
6.2.检测法:
检验测量可以采用:
(1)直接量法:
被测的量直接由量具(量仪)上读得其测量结果;
(2)间接量法:
测量与被测的量有一定函数关系的量,然后通过函数关系求出被测的量。
6.3.线性尺寸检测
6.3.1.一般长度测量中常用的测量器具有:
游标量具(卡尺、深度尺、高度尺)、外径千分尺、内径百分表、杠杆百分表。
6.3.2.测量器具的选择原则:
测量器具的不确定度≤测量器具不确定度允许值。
测量器具的不确定度见附录三、四;
测量器具不确定度允许值见附录五。
6.3.3.精密测量应用多次测量来求被测值。
6.4.形状和位置公差检测
6.4.1.工件的形状误差依靠加工过程的精度来控制,加强制程中的检查是保证加工精度的重要手段。
6.4.2.常用的形位公差检测如下所列,更多的检测原理和方式参阅GB/T1958-1980《形状和位置公差检测规定》
(1)直线度误差检测:
精度低于,使用平尺或刀口尺(对外圆表面)、塞尺测量;
(2)平面度检测:
一般机加工面使用刀口尺(或直尺)、塞尺测量;
(3)平行度误差检测:
a.孔轴线对平面使用平板、心轴、百分表和滑动表座配合进行;
b.孔轴线对孔轴线,两孔中心距不大时,使用心轴和外径千分尺配合进行。
两孔中心距较大时,使用平板、V形铁、心轴、百分表及滑动表座配合测量;
c.面对面,使用平板、带指示器的测量架;
(4)垂直度误差检测:
a.面对面(小型)使用平板、直角座、带指示器的测量架;
b.面对面(大型)使用水平仪、固定和可调支承;
c.面对线使用心轴、支承、带指示器的测量架;
d.孔轴线之间使用平板、百分表、可调支承、角尺、心轴配合进行;
(5)同轴度误差检测:
a.孔对孔使用平板、心轴、固定和可调支承、带指示器的测量架;
b.轴对轴使用平板、刃口状V形架、带指示器的测量架。
(6)孔系测量(孔的位置精度较高、中心距较大时):
使用平板、块规、块规架、高度尺、杠杆百分表、内径百分表配合,测量计算确定。
6.5.表面粗糙度的评定
6.5.1.表面粗糙度采用比较法评定:
把零件上被检的表面与粗糙度比较样块靠在一起,通过视觉、触感进行比较后,对被测表面的粗糙度作出评价。
6.5.2.表面粗糙度比较样块应分别按车、铣、磨等加工方法配备。
6.5.3.由于零件材料不同或表面形式(内孔、外圆、平面)不同,粗糙度在视觉或触觉上的反映也会不同,特别在视觉反映上的差异有时较大,因此在评定时应谨慎。
6.6.常用金属材料表面硬度测定
6.6.1.布氏硬度(HB)使用布氏硬度计测量。
一般碳钢或低合金钢在退火或正火状态下采用布氏法测定其硬度,如45钢调质处理后的硬度测量。
6.6.2.洛氏硬度(常用HRC)当钢材表面较硬时(HB>450),使用洛氏硬度计测量,如45钢整体淬火、表面淬火、碳素工具钢及合金工具钢等淬火后的硬度测量。
6.6.3.可采用便携式电子硬度计,一机即可测定多种硬度。
附录一
检测规制造公差带的确定
检测止通规的T值和Z值
工件基本尺寸
(D/mm)
工件精度等级
6级
7级
8级
9级
10级
IT6
T
Z
IT7
T
Z
IT8
T
Z
IT9
T
Z
IT10
T
Z
至3
6
1
1
10
14
2
25
2
3
40
4
>3至6
8
12
2
18
2
30
4
48
3
5
>6至10
9
15
22
36
5
58
6
>10至18
11
2
18
2
27
4
43
6
70
4
8
>18至30
13
2.
21
33
5
52
4
7
84
5
9
>30至50
16
25
3
4
39
4
6
62
5
8
100
6
11
>50至80
19
30
46
7
74
6
9
120
7
13
例:
计算配合代号为φ12
用的孔、轴工作量规的工作尺寸
1.查公差表得孔和轴的上、下偏差为
φ12H7(孔)ES=+EI=0mm
φ12f6(轴)es=-ei=-
2.查上表得IT6、IT7级、φ12mm量规的制造公差(T)和位置要素值(Z)
IT6T=Z=
IT7T=Z=
3.计算检测规的上下偏差
φ12H7孔用检测规
通规上偏差Ts=EI+Z+
=0++=+
下偏差Ti=EI+Z-
=0+-=+
止规上偏差Zs=ES=+
下偏差Zi=ES-T=-=+
φ12f6轴用检测规
通规上偏差Ts1=es-Z+
=--+=-
下偏差Ti1=es-Z-
=---=-
止规上偏差Zs1=ei+T=-+=-
下偏差Zi1=ei=-
4.检测规工作尺寸计算
φ12H7孔用检测规的极限尺寸
通规最大极限尺寸Tmax=12+Ts=12+=
通规最小极限尺寸Tmin=12+Ti=12+=
止规最大极限尺寸Zmax=12+Zs=12+=
止规最小极限尺寸Zmin=12+Zi=12+=
φ12f6轴用检测规的极限尺寸
通规最大极限尺寸T1max=12+Ts1=12+(-)=
通规最小极限尺寸T1min=12+Ti1=12+(-)=
止规最大极限尺寸Z1max=12+Zs1=12+(-)=
止规最小极限尺寸Z1min=12+Zi1=12+(-)=
5.工作图标注
φ12H7孔用检测规通φ
止φ
φ12f6轴用检测规通φ
止φ
附录二
检测规测量面的表面粗糙度
检测对象精度
工件基本尺寸/mm
至120
大于120至315
大于315至500
IT6级孔用检测规
IT6至IT9级轴用检测规
IT7至IT9级孔用检测规
IT10至IT12级孔、轴用检测规
附录三
千分尺和游标卡尺的不确定度(mm)
尺寸范围
mm
计量器具类型
外径千分尺
分度值
内径千分尺
分度值
游标卡尺
分度值
游标卡尺
分度值
大于
至
不确定度
0
50
50
100
100
150
150
200
200
250
250
300