机械论文矿用自卸车驾驶室FOPSROPS试验台设计及机械结构分析.docx
《机械论文矿用自卸车驾驶室FOPSROPS试验台设计及机械结构分析.docx》由会员分享,可在线阅读,更多相关《机械论文矿用自卸车驾驶室FOPSROPS试验台设计及机械结构分析.docx(7页珍藏版)》请在冰豆网上搜索。
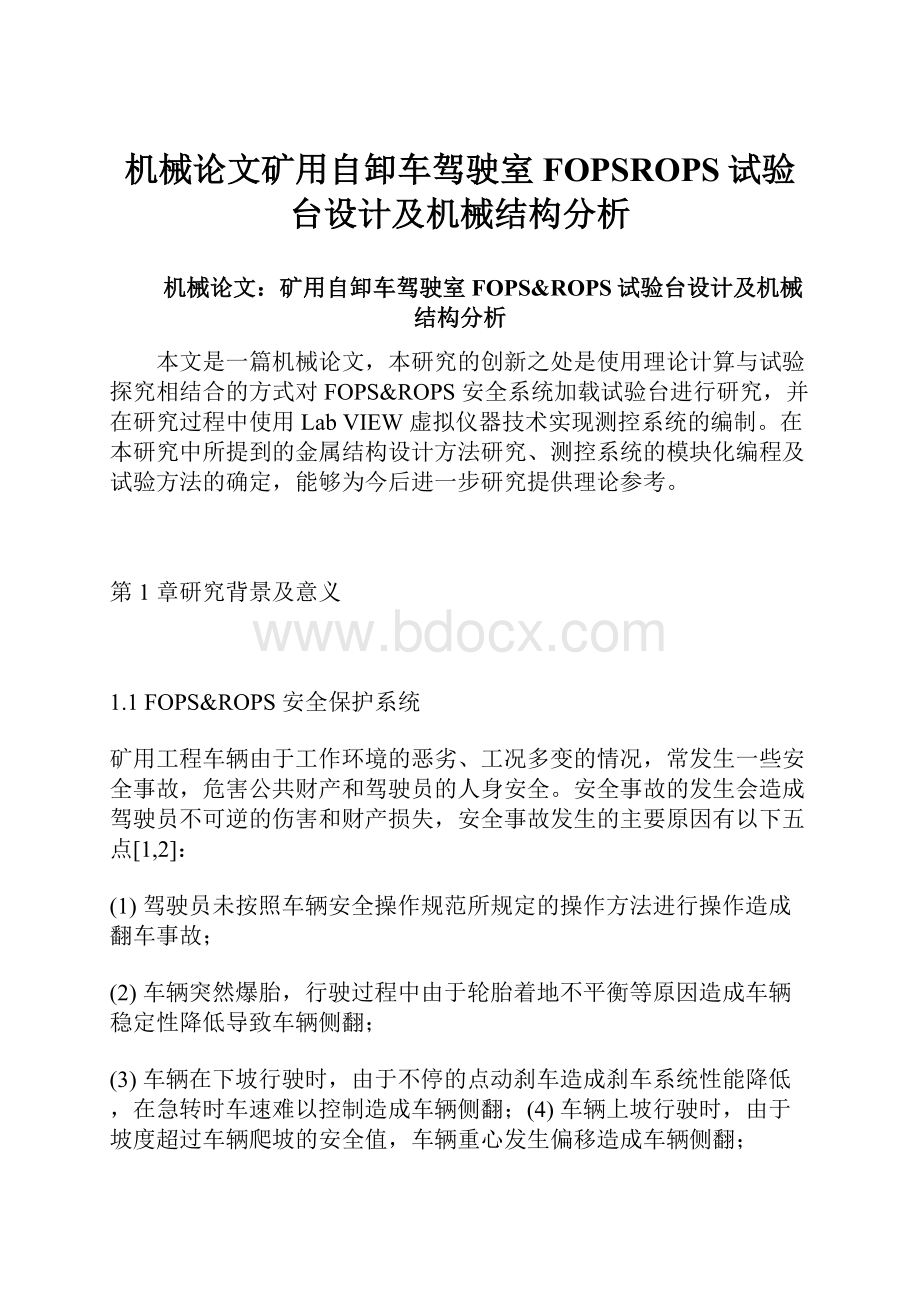
机械论文矿用自卸车驾驶室FOPSROPS试验台设计及机械结构分析
机械论文:
矿用自卸车驾驶室FOPS&ROPS试验台设计及机械结构分析
本文是一篇机械论文,本研究的创新之处是使用理论计算与试验探究相结合的方式对FOPS&ROPS安全系统加载试验台进行研究,并在研究过程中使用LabVIEW虚拟仪器技术实现测控系统的编制。
在本研究中所提到的金属结构设计方法研究、测控系统的模块化编程及试验方法的确定,能够为今后进一步研究提供理论参考。
第1章研究背景及意义
1.1FOPS&ROPS安全保护系统
矿用工程车辆由于工作环境的恶劣、工况多变的情况,常发生一些安全事故,危害公共财产和驾驶员的人身安全。
安全事故的发生会造成驾驶员不可逆的伤害和财产损失,安全事故发生的主要原因有以下五点[1,2]:
(1)驾驶员未按照车辆安全操作规范所规定的操作方法进行操作造成翻车事故;
(2)车辆突然爆胎,行驶过程中由于轮胎着地不平衡等原因造成车辆稳定性降低导致车辆侧翻;
(3)车辆在下坡行驶时,由于不停的点动刹车造成刹车系统性能降低,在急转时车速难以控制造成车辆侧翻;(4)车辆上坡行驶时,由于坡度超过车辆爬坡的安全值,车辆重心发生偏移造成车辆侧翻;
(5)矿山落石对驾驶室造成冲击,对车辆及人员造成直接安全威胁。
1982年美国工程师Robert·M·Clarke对该年工程事故进行统计分析中提到,车辆翻滚造成的工程车辆事故占本年所有工程事故总量的56.7%,落物所造成的车辆事故占本年全美国所有工程车辆事故总数的2.6%,两者的事故总量占到全年工程事故的半数以上。
这是由于工程车辆在施工现场的施工环境恶劣,路况复杂所致,加之工程车辆自重及工作运载载重质量较大,产生较大的惯性所导致的。
翻车事故频繁发生,落物机顶刺穿驾驶室常常威胁驾驶员的生命安全。
为了保护驾驶员及车辆安全,结合常见事故发生原因,在车辆设计中设计了司机安全保护系统,即在驾驶室的内部或者外部安装钢架机构和落物保护结构,其中高架结构即翻车保护结构(roll-over-protectivestructure,ROPS)主要防止车辆侧翻时对驾驶员造成伤害,落物保护结构(falling-object-protectivestructure,FOPS)主要防止高空落物对驾驶室及驾驶员进行伤害。
........................
1.2FOPS&ROPS的国际标准
工程车辆保护装置,由美国工程与工业机械技术协会(ConstructionandIndustrialMachineryTechnicalCommittee,CIMTC)于二十世纪七十年代首先提出并在工程车辆上安装翻车保护装置ROPS与落物保护装置FOPS。
二十世纪八十年代,CIMTC通过静态试验方法确定了一系列静态性能指标用来检测评定FOPS&ROPS系统的安全性能,并对变形后的FOPS&ROPS狭小空间——人体极限安全域(CriticalZone)提出了极限变形标准,即挠曲极限量(DeflectionLimitingVolume,DLV)。
1974年,美国汽车工程协会SAE将CIMTC所提出的FOPS&ROPS系统实验室静态性能指标及DLV制定为车辆安全与保护性能标准SAEJ1040和SAEJ1043。
1979年和1980年,SAEJ1040和SAEJ1043两项标准相继被ISO国际标准化组织采用并制定了三项国际标准规定,分别为ISO3164、ISO3471和ISO3449。
二十世纪九十年代,美国汽车工程协会对工程车辆生产商及矿山管理者提出要求,要求所有进入危险环境及有在危险工作环境下工作需求的工程车辆必须配备符合ISO标准的FOPS&ROPS安全保护系统。
这一要求提出后,迅速在加拿大、英国、法国等国家形成影响,强制要求所有的工程车辆都需要安装翻车保护及落物保护装置[3]。
.........................
第2章FOPS&ROPS的试验和性能要求
2.1FOPS&ROPS的定义及性能要求
2.1.1FOPS&ROPS的定义及功能
矿用自卸车驾驶室FOPS&ROPS安全保护系统,作为一种安全保护的钢架结构,该结构可以后期固定在驾驶室的周围,也可以在车辆出厂时,制造商直接将其与驾驶室制作在一起,使安全保护系统与车辆驾驶室形成一体结构,该做法能够更好的保护驾驶员的生命安全。
FOPS&ROPS安全保护系统能够有效的减少矿用自卸车在工作事故中对司机的二次伤害。
FOPS&ROPS安全保护系统的主要功能有:
(1)FOPS落物保护结构可以有效的防止驾驶室不会因为落物撞击击破车顶造成驾驶员被击中头部而造成危险;
(2)FOPS&ROPS可以有效的防止当驾驶室遭受落物撞击和车辆翻滚时,驾驶室内人体极限安全空间遭到破坏,从而威胁驾驶室安全性;
(3)ROPS翻车保护结构,可以有效的防止矿用自卸车发生翻滚事故时连续翻滚,其结构可以刺入地面形成对车体的支撑,防止驾驶室的进一步变形;
(4)当车辆正在发生事故时,FOPS&ROPS安全保护系统能够有效的吸收一部分惯性所造成的冲击性能量,减少冲击对司机的伤害;
(5)当车辆翻转驾驶室着地时,
FOPS&ROPS安全保护系统能够支撑车体,为驾驶员提供一个安全能够自救的空间。
...........................
2.2国际标准对ROPS的性能要求
FOPS&ROPS静态载荷实验室试验要求应当满足ISO3471:
2008之规定,即,应当满足以下要求[13]:
(1)侧向应该能够承受住最小的侧向载荷,并能够吸收最小侧向能量;
(2)垂直方向应该能够承受最小的垂直载荷;
(3)纵向能够承受最小的纵向载荷。
2.2.1最小侧向承载力的性能要求及试验办法
当FOPS&ROPS安全保护系统能够承受最小侧向承受能力时,可以保证当运输车辆行驶在危险路面造成车辆翻滚时,ROPS结构能够插进地面中,能够缓冲翻滚时惯性所带来的的冲击力,能够有效的阻止车辆不停地翻滚。
最小侧向承载力的大小则取决于工程车辆的类型和车身质量,如表2.1中所截取的部分常用工程车辆对应的最小侧向载荷。
............................
第3章FOPS&ROPS试验台主体结构设计...........................17
3.1FOPS&ROPS试验台设计原则...........................................17
3.1.1FOPS&ROPS试验台主体结构设计要求................................17
3.1.2载荷计算原则...................................17
第4章试验台主体结构有限元分析................................38
4.1有限元求解方法..............................38
4.2加载试验台主体结构的有限元分析与求解....................................40
第5章试验方法的研究.....................................46
5.1测控系统总体设计................................46
5.1.1测控系统结构....................................46
5.1.2测控系统模块化设计方案................................46
第5章试验方法的研究
5.1测控系统总体设计
5.1.1测控系统结构
测控系统通常由测试系统与控制系统共同组合而成,其中测试系统通常包含传感器技术、数据采集技术和信息处理技术组成,控制系统则包含数据传输和动作控制技术。
传感器技术借助传感器可以将检测的物理信号转换为电信号进行传输,数据采集技术主要借助数据采集卡将传感器接收的信号进行A/D转换,信息处理则将A/D转换后的信号进行数据处理,经过信息处理后的数据通过信号传输系统将其传输到控制系统和显示器,控制系统根据信号处理结果进行动作。
在本研究中我们将借助LabVIEW虚拟样机进行测控系统设计。
5.1.2测控系统模块化设计方案
FOPS&ROPS试验台所用测控系统共由图5.1所示八个模块组成。
各模块之间各司其职又相互协调共同构成整个测控系统。
其中参数设置、数据采集、数据分析、数据显示和数据管理模块构成了数据测试系统,剩下的错误处理、开关监控模块构成了控制系统,辅助模块则能够帮助操作人员进行初始化操作。
各模块的有如下作用:
............................
第6章结论与展望
6.1结论
为了解决矿用自卸车在工作时由于环境问题造成车辆侧翻及落石对驾驶室和驾驶员造成财产及生命威胁,在矿用车的工程设计中通常会设计一套安全保护系统,本研究针对矿用车的安全保护系统的性能特点和国际制造标准针对FOPS&ROPS安全系统的要求设计一种试验台,即FOPS&ROPS安全保护系统试验台。
该试验台能够满足1000t试验加载要求,并且适用于不同型号的工程车辆所安装的FOPS&ROPS系统。
本研究主要工作及成果总结如下:
(1)本研究根据国际标准所要求及实际工况条件确定了FOPS&ROPS安全系统试验台的基本结构参数;
(2)根据金属结构基本设计方法——许用应力设计法和极限状态设计法,对FOPS&ROPS试验台进行强度、刚度和稳定性进行校核计算,得到加载试验台主体结构几何参数;
(3)针对校核计算后的FOPS&ROPS加载试验台结构几何尺寸,建立三维模型,并使用有限元分析软件ANSYS对其进行应力应变分析,分析表明试验台在最危险载荷施载情况下依然能够满足安全性能要求;
(4)使用LabVIEW软件对测控系统进行模块化编程,并根据FOPS&ROPS安全保护系统性能要求对试验方法进行确定。
本研究的创新之处是使用理论计算与试验探究相结合的方式对FOPS&ROPS安全系统加载试验台进行研究,并在研究过程中使用LabVIEW虚拟仪器技术实现测控系统的编制。
在本研究中所提到的金属结构设计方法研究、测控系统的模块化编程及试验方法的确定,能够为今后进一步研究提供理论参考。
参考文献(略)