机械类文献翻译5轴铣床系统的几何刚体误差鉴定.docx
《机械类文献翻译5轴铣床系统的几何刚体误差鉴定.docx》由会员分享,可在线阅读,更多相关《机械类文献翻译5轴铣床系统的几何刚体误差鉴定.docx(17页珍藏版)》请在冰豆网上搜索。
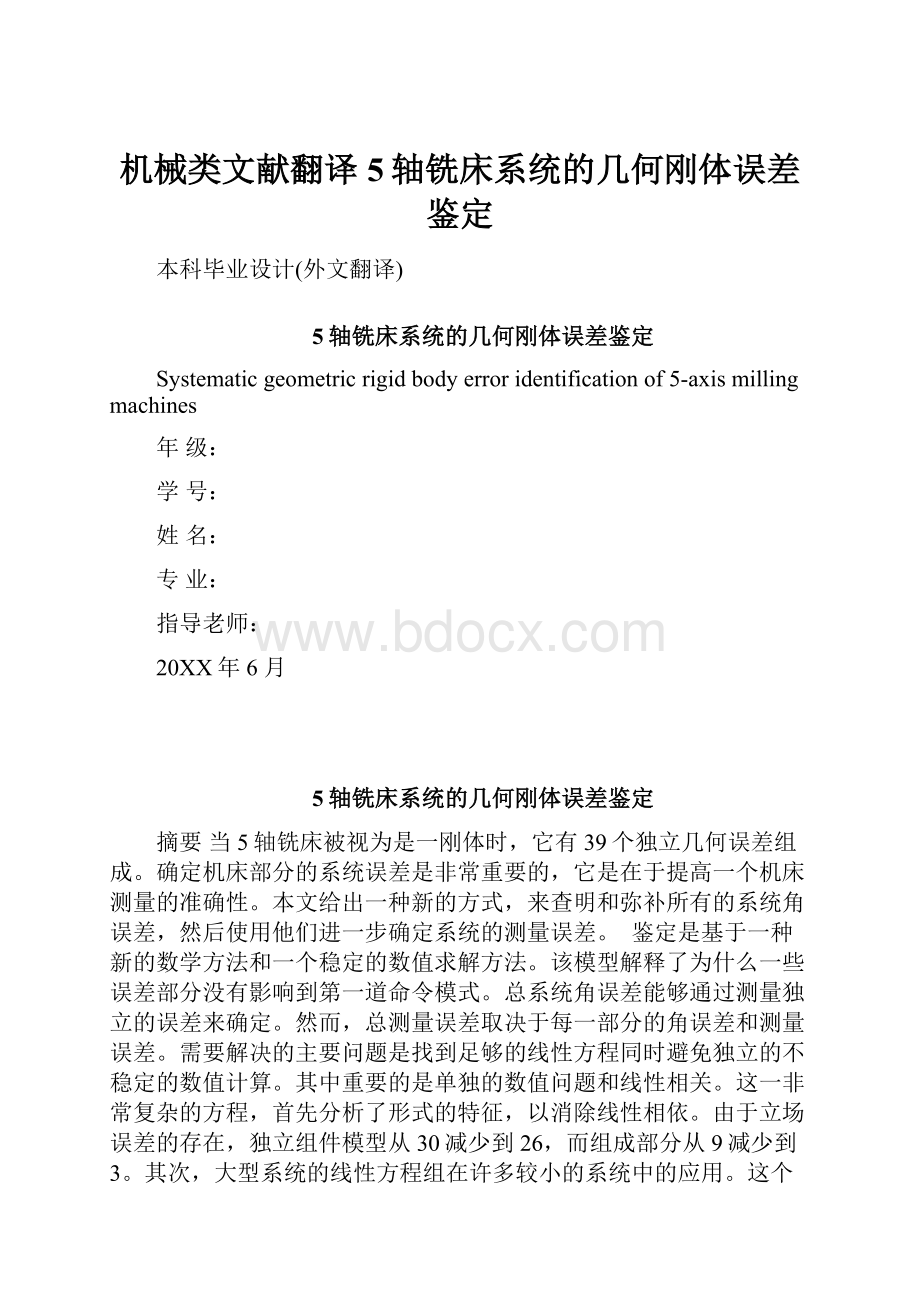
机械类文献翻译5轴铣床系统的几何刚体误差鉴定
本科毕业设计(外文翻译)
5轴铣床系统的几何刚体误差鉴定
Systematicgeometricrigidbodyerroridentificationof5-axismillingmachines
年级:
学号:
姓名:
专业:
指导老师:
20XX年6月
5轴铣床系统的几何刚体误差鉴定
摘要当5轴铣床被视为是一刚体时,它有39个独立几何误差组成。
确定机床部分的系统误差是非常重要的,它是在于提高一个机床测量的准确性。
本文给出一种新的方式,来查明和弥补所有的系统角误差,然后使用他们进一步确定系统的测量误差。
鉴定是基于一种新的数学方法和一个稳定的数值求解方法。
该模型解释了为什么一些误差部分没有影响到第一道命令模式。
总系统角误差能够通过测量独立的误差来确定。
然而,总测量误差取决于每一部分的角误差和测量误差。
需要解决的主要问题是找到足够的线性方程同时避免独立的不稳定的数值计算。
其中重要的是单独的数值问题和线性相关。
这一非常复杂的方程,首先分析了形式的特征,以消除线性相依。
由于立场误差的存在,独立组件模型从30减少到26,而组成部分从9减少到3。
其次,大型系统的线性方程组在许多较小的系统中的应用。
这个模型与误差模拟测试模型一起作为立方米多项式形式。
在人工识别和建议的基础上实施钻孔取决于不同地点和方向。
新的直接测量体积误差的方法是给予建议。
直接测量总容积误差的工作量大大低于分别测量每台机器的所有6个组成部分,尤其如果是5轴机床的情况下。
关键词:
系统误差;刚体;5轴机床;误差补偿;逆运动学
1导言
三线性轴的机器共有21个线性独立的几何误差。
这些误差可以在许多研究成果中识别和补偿。
但是,应该很清楚3轴机床的这些误差可以通过在工具和刀具联系(CC)点之间的一个单一联络点被纠正。
点选择的校正是CL(刀位)点。
CL点是一个方便的参照点,如刀尖坐标。
一个在3轴机床中不能排除的误差,是由于连接CC和CL之间的所讨论的角误差向量误差。
5轴机床给我们弥补这些系统角误差可能性,就是通过用调整旋转轴的方法。
当机床被看作是一套严格的机构时,5轴铣床由39独立几何误差部分组成。
被视为刚体的每个轴的每个自由度有6个误差。
误差是由于非正交的机床坐标系统或方形误差有独立的组成部分所引起的。
2文献复习
从文献中可以得出如下结论,研究人员减少参数的数目并没有明确的理由,根据的是第一原则。
减少参数的原因是明确的,参数越多数值问题就越多。
这同多项式的程度和类型是相同的。
所采用的方法可分为机器上的直接测量和一个工件或参考的一部分的脱机或联机测量。
直接测量方法现今常常依赖放置在机器外或机器的表面上的激光干涉仪。
那个干涉仪在5轴机床情况下有可能直接确定所有的39个组件。
然而,在激光束轴中机器幻灯片的轮换误差是难以确定的。
同样也很难确定旋转轴元件的误差。
商业系统通常是基于一个放置在机床主轴上的球板或孔板的测量探头之下。
这些系统相当一部分的费用是花费在黑箱型软件上。
其中大部分只是为了3轴机床和CMM机器的校准。
表1显示,试图解决5轴机床误差鉴定问题的研究人员总是提出简化一些参数,而非依据首要原则。
减少一些参数的基本原因或方法在上文已给予。
在其余本文中,线性独立参数的总数目服从第一原则,在以下各节中将被讨论。
3数学模型
3.1自由度和独立的误差组件
一个硬质体有6个自由度。
这6个坐标确定刚体在三维空间中唯一的位置。
一个5轴机床拥有可彼此移动的五个机构。
其中两个被固定在机床上的机构是工具和工作区。
每个机构有6个独立的误差TMX,TMY,TMZ,RMx,RMY和RMZ。
在前面的符号T代表测量,R代表旋转。
旋转误差常常指的是滚轮。
第一个下标M代表的是有关刚体的名称。
字母M将采取下列名称:
X,Y,Z,A,B或C。
轴心误差是T误差,旋转轴误差是R误差。
根据刚体相对坐标系统的位置,误差的总数目为6×7=42。
这些机构的动作是相互关联的。
每个固定的刚体坐标系统的位置仍然可能存在误差。
对于独立误差部分的数目,这些问题都可以通过连接这些刚体的最低数目被找到。
三刚体可以通过刚性三角形来连接。
四刚体需要6个刚性四面体。
七刚体将需要15个刚性多面体。
对N刚体可采用方程式3(n-2)来得到结果。
7刚体总的独立误差组件是(42+15)=57。
由于工件而产生的误差部分在模型中没有被考虑,这些误差是随机的,对每个来说性质上是不同的。
然而,上述关于误差部分的决定清楚地表明,这些误差的是存在的,并应当通过工具和工件的谨慎定位尽可能减小。
测量过程中这些要求显然对工具和工件的偏移测量是有利的。
图15轴机床示意图
图25轴机场动态链接图
我们只考虑5刚体情况的模型。
共有30+9=39个独立的误差。
图1和2显示了5轴机床和相应的运动学链接图,这将在我们的研究中被考虑。
图1显示工件坐标系O1与刀位矢量(CL)之间的关系。
这种CL载体与工具应该是重合的。
CL载体和工具之间的区别是存在闭环体积误差。
这个概念是非常有用的,特别在评估每一个误差组成部分的影响的时候。
3.2参考坐标系和方形误差
机器任何方便的设置都可以被选择应用。
在机器内部有一个固定的参考坐标系,它联系着每个机构的运动链。
对Cartesian坐标系统而言,所有的X-参考轴与真正的X轴机床相配合,因此真正的X轴没有角误差。
穿过机床X轴和Y轴的平面被选中作为参考平面。
因此,真正的Y轴只能有一个角误差或垂直误差。
真正的Z轴将有两个方形误差。
这些方形误差如图3示。
方形误差是由于机床在轴方向上的误差引起的。
例如,A轴与X参考轴不完全平行,在A轴上将有2个方形误差SAY和SAZ。
其他旋转轴B或C同理可得。
在图1中5-轴机床的垂直误差将是:
X轴:
没有,因为真正的X轴与X参考轴重合
Y轴:
SYZ
Z轴:
SZX和SZY
A轴:
SAY和SAZ。
B轴:
SBX和SBZ。
3.3刚体误差
当机床根据相应的坐标系移动时,角误差和线性误差将增加轮换。
绝对参考坐标系同每个机构固定在一起,并和机内的固定参考坐标系是重合的。
由于系统误差,移动机器的部分将产生3小测量和3个小轮换,只有4个参考坐标系需要加以考虑,工件参考坐标系O1同旋转工件是固定在一起的。
参考坐标系O2同固定的旋转工作台固定在一起。
当机器是在参考位置时,每个轴所有参考坐标系的方向与机控制器正好显示为零。
O2和O3不是在同一地点起始的。
其中有一个距离rAB,因此在两个旋转轴A和B之间给予了位置误差。
这是为了使实际的Z轴和实际的A轴相交。
这计划是独特的,因此rAB只有两个独立的组成部分,如图4所示。
在Z轴方向抵消一阶的效果。
图4还说明了如何设置参考位置。
真正的Z-轴对应于主轴的中线或刀具中心线。
它的意思是使真正的a轴中心线和真正的Z-轴相交。
给出了点O2。
这定义了一个平面交叉。
由于X测量有可能使真正的B轴与真正的Z轴相交。
在O2坐标系中一个被固定在B-机构上的参考坐标系统被提及。
在O3坐标系中一个被固定在Y-机构上的参考坐标系统也被提及。
最后01坐标系被迁往O2中以从方程中删除工件的偏移。
同理04坐标系被迁往O3中.。
这次工具从我们的方程中的移除抵消,是消除需要被协调的系统之间的一切多余补偿要求的一个方便的方法。
3.4由于偏心旋转轴引起的误差
根据旋转轴头的方形误差,模型中围绕A轴机床轮换的方形误差SAY和SAZ被给
出了:
X(A)=X+YSAZ−ZSAY−YSAZcos[A]+ZSAZsin[A]+YSAYsin[A]+ZSAYcos[A]
Y(A)=Ycos[A]−Zsin[A]−XSAZcos[A]+XSAYsin[A]+XSAY
Z(A)=Ysin[A]+Zcos[A]−XSAZsin[A]−XSAYcos[A]+XSAZ.
上述方程是通过O2轴坐标系周围旋转点X和Y的坐标得到的。
同样的方程也可以在B轴和C轴中得出。
3.5一阶模型的误差假定工具已符合真正的Z-轴机床。
由于在提示Z轴机构时垂直方向会有坐标误差如下(Z是真正机床Z轴的测量):
在物理参考坐标系测量之后协调为:
X4t=SZY(Ztip+Z)+RZY(Ztip+Z)+TZX;
Y4t=−SZX(Ztip+Z)−RZX(Ztip+Z)+TZY;
Z4t=Ztip+Z+TZZ
Ztip是工具提示的协调。
已经可以观察到,RZZ部分只有二阶效应,它将不会出现在一阶模型中。
工件将沿实际的机器轮流测量角度A和B并测量X和Y轴的距离。
在机器物理参照系统中工件坐标X4w,Y4w和Z4w的最后位置会通过由三个方程组成的条件被得出。
刀尖和工件坐标之间的的误差将是不同的。
误差的条件和相应的系数在表2-4中给出了。
这一立场误差,也可以在固定工件的工件坐标系统中被表示,采用的是逆的B和A的位置轮换误差dX,dY,dZ。
这些误差可以被测量例如通过用激光干涉仪,让它作为一个功能不同的机器来测量X和Y的坐标,如果干涉固定在机器内部,表2-4中的方程可以被用到。
如果干涉是固定在机器表面,表2-4中的方程必须首先转化为工件坐标系下。
后一种方法对直接干涉的测量经常是不切合实际的。
然而,如果误差仅是从一个参考工件中得出,表2-4中的方程也必须转变到工件坐标系。
图3O2与O3的测量
仔细观察可看出,某些误差条件有零个系数。
这意味着,他们没有影响到相应的误差。
还可以看到,在误差条件中还有方形旋转误差。
如果在O1坐标系统中所有误差条件都等于零,CL载体和X1,Y1,Z1,i1,j1,k1之间关系可表示如下:
X=−(X1cos[B]+Xo1o2cos[B]+Xo2o3cos[B]+Zo2o3sin[B]+Z1cos[A]sin[B]+Zo1o2cos[A]sin[B]
+Y1sin[A]sin[B]+Yo1o2sin[A]sin[B])
Y=−(Y1cos[A]+Yo1o2cos[A]−Z1sin[A]−Zo1o2sin[A])
Z=Zo3o4−Ztip+Zo2o3cos[B]+Z1cos[A]cos[B]+Zo1o2cos[A]cos[B]+Y1cos[B]sin[A]+Yo1o2cos[B]sin[A]−X1sin[B]−Xo1o2sin[B]−Xo2o3sin[B]
i=−sin[B];j=sin[A]cos[B];k=cos[A]cos[B].
在O2,Xo1o2,Yo1o2和Zo1o2中的工件坐标偏移坐标将会是零,因为O1将与O2配合。
O2的坐标将会是二阶的。
在这种情况下Zo2o3被直接测量的结果是-0.080毫米。
这个值可用一个非常简单的方式来测量,就是把一个在A轴机床中线的参考量放在合适的位置。
百分表被放在主轴上,并将其调节为零。
B-轴机床接着旋转180。
该百分表将显示Zo2o3的双倍。
表2-4中的方程给出了如下的参考:
dX=TBX+TXX+TYX−TZX+RBZY+RXZY+RYZY+SBZY−SYZY+RAYZ+RBYZRXYZ+RYYZ
−RZYZ+SAYZ−SZYZ−cos[A](SAYZ+SAZYcos[B])+SAZZsin[A]+cos[B](TAX
+(RAZ+SAZ−SBZ)Y−SAYYsin[A])+TAZsin[B]−RAXYsin[B]+SBXYsin[B]
dY=TAY+TBY+TXY+TYY−TZY−RBZX−RXZX−SBZX−RBXZ−RXXZ−RYXZ+RZXZ−SBXZ
+SZXZ+cos[B](−RAZX−SAZX+SBZX−RAXZ+SBXZ+SAZXcos[A]+SAYXsin[A])
+(RAXX−SBXX−RAZZ−SAZZ+SBZZ+SAZZcos[A]+SAYZsin[A])sin[B](5)
dZ=TBZ+TXZ+TYZ−TZZ+RAYX+RBYX+RXYX+SAYX−RBXY−RXXY−RYXY−SBXY
+(TAZ−RAXY+SBXY)cos[B]+SAZXsin[A]−TAXsin[B]−RAZYsin[B]−SAZYsin[B]
+SBZYsin[B]+SAYYsin[A]sin[B]+cos[A](−SAYX+SAZYsin[B]).
3.6一阶模型中的误差倾向
均衡器清楚地表明,该工具载体元件只根据A和B的轮换而转换,这不仅仅在5轴机床这里被发现,据观察还有其他的机床模型也被观察到。
相对于O4参考坐标系,单位向量组成部分将会是:
i4t=SZY+RZYj4t=−SZX−RZXk4t=1.
工件将不断转换角度A和B并将测量沿真正的机器上的X和Y轴的距离。
机器物理参照系统中刀位矢量i4w,j4w和k4w的最后方向将被给出,通过由三个方程组成的许多条件。
刀尖和工件坐标之间的的误差将是不同的。
从表5-7中可看出,一阶误差大大减少了相应的条件和系数。
这些表格给出了固定在机床内部的机床坐标系的误差。
图4影响Z方向上矢量的因素
可以看到,系统的误差部分SYZ,RBZ,RXZ,RYZ和RZZ没有影响到一阶角误差。
这正如预期所料。
当工件沿着真正的Y轴作如图所示的运动时,上滑运动并没有在方向上引入误差。
所有的围绕Z轴机床的旋转误差也没有受影响。
这也可以解释这样一个事实,即工具始终是沿着Z轴,它和矢量转化方向CL之间的差异只有di和dj。
所以对具体的机器而言,围绕Z-轴机床小的轮换只会有一个二阶的影响。
然而这个轮换却影响到了B轴的位置。
只有当B是在零参考位置时,影响才是无效的。
当B是90°时,影响达到最大。
方程的轮换误差受到较少的约束,因为它们没有受到测量误差的影响。
所以先查明这些误差组件然后使用得到的结果来查明测量误差是很简单的。
3.7数学模型
方程提供了5刚体中垂直误差和角误差之间的关系。
这意味着可将问题分为两个独立的问题。
很大一部分方向误差可被确定为独立的。
使用表2-4中系统的方程可以识别其余的误差方向和测量误差。
误差可近似的看作是主要测量X和Y坐标或A和B轮换的一维多项式。
选择合适的程度,往往不是一件容易的事情。
程度越高逼近程度越好。
这可以通过在泰勒级数中的扩充功能很容易地被证明。
然而众所周知,在数值计算中这可能会导致线性方程组的制约。
要获得不同机器坐标的线性独立方程组,我们必须使用两套线性独立机坐标,使每一个坐标集必须是线性独立的。
4数学模型的解决
4.15轴机床的工件
重要的是要在整个工作机床确定系统误差。
这种情况下在工件坐标系中的工件在表8中已给出了,这是基于机器表面的大小。
相应的机器测量和X,Y,Z及A,B的轮换在表9中给予了。
机器真正的行程如下:
X=600毫米,Y=450毫米,Z=400毫米,A转360°,B从15°转至-195°。
从表9中可以看出,在这个模型中,我们几乎覆盖了所以的行程。
表9将用于独立变量的多项式逼近。
范围将从0到1扩展。
这个尺度数值大大减少了不稳定的计算。
图5直接测量与干涉
4.2仿真
4.2.1误差数据模拟
为了研究模型的数值使用了模拟误差。
从文献看来,可以使用三次多项式来完成旋转和平移系统误差的功能,误差角度不断的减小,此外,线性误差的测量与干涉情况如图所示,在X,Y和Z轴中的平均结果显示在图8中。
误差的轮换使用的比例因子是
,而误差测量则为
。
这些模拟误差的绝对值与准确机床工具相对应。
在模拟中对所有的方形误差而言,使用相同的精度。
所有的旋转中的误差将有如下形式:
RMN(M)=RMN3M3+RMN2M2+RMN1M+RMN0。
在测量中的误差会有如下形式:
TMN(M)=TMN3M3+TMN2M2+TMN1M+TMN0.。
参数m的取值范围见于表10。
通过这些多项式的模拟,误差dX,dY,dZanddi,dj可以用表2-7中的方程被计算出来。
4.2.2误差方向的鉴定
旋转误差逼近立方米多项式而直线误差逼近常数。
因此,如果是一阶系统方程则将有23×(5×4+3)个未知系数,如果是二阶系统将会有19×(4×4+3)个未知数。
不过,应当明确的是,从SMN中区分出RMN0是不可能的。
SAY和SAZ可从第一线性系统中确定。
最小二乘法现在很容易解决这类线性系统问题。
表11和表12的最后一栏给出了一阶模型的估计值和实际值之间的误差。
影响方向误差的参数现在已经被确定。
在这一阶段影响角误差的所有误差组成部分在仿真中已经被确定。
确定旋转部件至少需要21个CL载体。
如果机器的线性精度被认为是足够精确的,就不需要补偿这些线性误差。
5.1节中提出的补偿可用于后面的鉴定。
只有此步骤的执行才可以很大程度上改善测量的准确性,在切屑铣削表面时,刀具的接触不是一个点而是一条曲线。
4.2.3模拟识别的测量误差
线性误差现在可以认为是基于表2-4上的方程得出的。
上面被确定的方向误差可取代这些方程从而很大程度上减少线性方程组的大小。
这也将给予更好的数值稳定性和较小的条件数目。
4.2.3.1鉴定尖端测量误差。
表13给出了影响dX的误差的因素,要找到误差条件的系数多项式,联系条件和系数多项式的线性依赖必须结合起来。
例如系数TYX3Yp3将与RYZ2yp2Y线性相依。
另一种办法是逐步区分一定数量的机床坐标。
通过保持Y和B的协调,同时随机的变化其他机床坐标,一个较小的系统线性方程组就可以被得到,除了常数没有线性依赖多项式。
表14给出了可以估计误差值的一些参数。
表14中YP的值0.33对应为一个Y=0。
下一步机器协调保持在零,同时其他机器坐标X和Y,Z和B被随机的分配到不同的机器工作空间。
这套系数现在可以在表15中得到确定。
系数TAZ3,TAZ2和TAZ1仍然需要被确定,这可以通过维持Xp,Yp,Zp都为零,Bp=1,只来分配A来完成,结果见于表16。
条件数是110,所有的剩余都少于
。
参数估计的误差在表14-16的每一个最后一栏给出了。
可以看出,估计误差大于在方向误差情况下的估计误差。
这可能是由于大量的参数和一个方向误差估计结果的使用引起的。
另外的原因是,测量误差中最大程度的条款有四个,因此,由于轮换而产生的线性误差要乘以其长度。
需要最少30个不同的CL载体以确定所有的系数。
4.2.3.2测量误差dY和dZ的鉴定
dX关系中全部条件现在都被确定了。
同样在dY和dZ中也必须这样。
上述dX中尚未确定的条件必须被查明。
表17和18给出了误差组成部分,但仍然需要在dY和dZ误差的基础上来确定。
dX中计算这些系数的方法大体上是相同的。
另外有17个CL载体被需求以确定所有影响dY的未知系数,同样在dZ中需要14个CL载体。
5补偿
不管角度误差还是系统误差都可以被补偿,通过在后处理器下增加非常简单的工具来实现。
数控系统已为每个控制轴提供了两个补偿表:
一个是线性补偿,另一个为循环补偿。
对轴的旋转过程中25个同样距离的点,我们可以输入补偿值。
但是各工作点的总误差是一个所有位置的函数,不能用在这里。
这只有通过软件来补偿且是唯一的选择。
5.1角误差补偿
一旦系统误差系数已被确定,他们就应该被用来补偿。
问题看起来相当复杂。
然而,如果A和B的实际值离参考值差别很小,一阶全微分均衡器就可以被使用。
因此利用逆运动学关系用计算来校正A和B是很快的。
对这里考虑的5轴机床工具而言,关系在如下矩阵符号中:
这个方程的逆向被用来完成dA和dB的更正。
这种更正无论怎样并不总是有效的,因为从下面的例子中可以看到。
想象一个一般的CL载体X1,Y1,Z1之间是互相协调的,但i=1和j=k=0。
然而真正的CL载体将包含小误差di,dj和dk。
补偿这些误差所需的轮换将很大,第一近似值从均衡器中可以计算出为A=arctg[dj/dk]。
这种新的轮换将产生新的误差。
相应的机器测量也将会得到不同的误差,这是一个明确的例子,证明这种情况下进行弥补将需要额外旋转C轴。
5.2测量误差的补偿
X,Y,Z坐标补偿的计算通过总微分均衡器获得了:
dXcor=−Zo2o3cos[B]dB−Z1cos[A]cos[B]dB−cos[B]dX1−Y1cos[B]dBsin[A]
−Y1cos[A]dAsin[B]+X1dBsin[B]−cos[A]dZ1sin[B]+Z1dAsin[A]sin[B]
−dY1sin[A]sin[B];
dYcor=z1cos[A]dA−cos[A]dY1+Y1dAsin[A]+dZ1sin[A];
dZcor=Y1cos[A]cos[B]dA−X1cos[B]dB+cos[A]cos[B]dZ1−Z1cos[B]dAsin[A]
+cos[B]dY1sin[A]−Zo2o3dBsin[B]−Z1cos[A]dBsin[B]−dX1sin[B]−Y1dBsin[A]sin[B].
图6样品工件
计算误差dXcor,dYcor,dZcor被添加到X,Y,Z的部分。
如在第6节的情况下,均衡器必须被使用来更正机器测量中新产生的误差值。
6执行和实验
基于模拟误差,用来确定参数的该模型已经被建立和分析。
结果非常明确的表明,所有相关系数都可被确定即使无数值问题,至少对三次多项式是这样的。
从表15中看出,在保持轮换时,多项式系数是基于沿X,Y,Z轴运动所产生的CL点来确定的。
在样品工件上实施钻孔和在三坐标测量机上测量结果,这种做法有很多好处,如:
(一)在钻孔过程中只有一个机器轴动作,而所有其他轴在钻孔启动之前被放置。
(二)如果洞的深度相比Z轴的行程是相对较浅的,可以进行合理的假设,Z机构的误差沿着孔的长度没有显现。
(三)实验中机器停工的时间很少。
(四)机械变形可以通过缓慢的进给而减少。
上述方法可通过圆锥形钻洞得到提高。
图7三坐标测量机
孔的位置误差和方向误差被测量,并根据这些值将参数进行了确定。
通过在一个200×200×100毫米的长方体上钻直径为10毫米的孔得出了结果。
CL载体在表19中给出了。
钻孔之后,钻孔的确切位置和方向在三坐标测量机上就被测量出来。
测量结果在表20中给出了。
钻孔的补偿也被测量出来,是借助CMM。
表21显示了相当大的改进。
洞位置的最大线性误差是0.177毫米。
通过补偿,最大的线性误差成为0.009毫米,与机器精度0.001毫米更加接近。
最大方向误差从0.058下降到0.0002,补偿后,低于
角分辨率0.001。
CL载体名义上符合x轴机器。
补偿试图结果在表22和23中给出。
为了补偿所要测