烧结矿质量对高炉冶炼的影响 精品.docx
《烧结矿质量对高炉冶炼的影响 精品.docx》由会员分享,可在线阅读,更多相关《烧结矿质量对高炉冶炼的影响 精品.docx(21页珍藏版)》请在冰豆网上搜索。
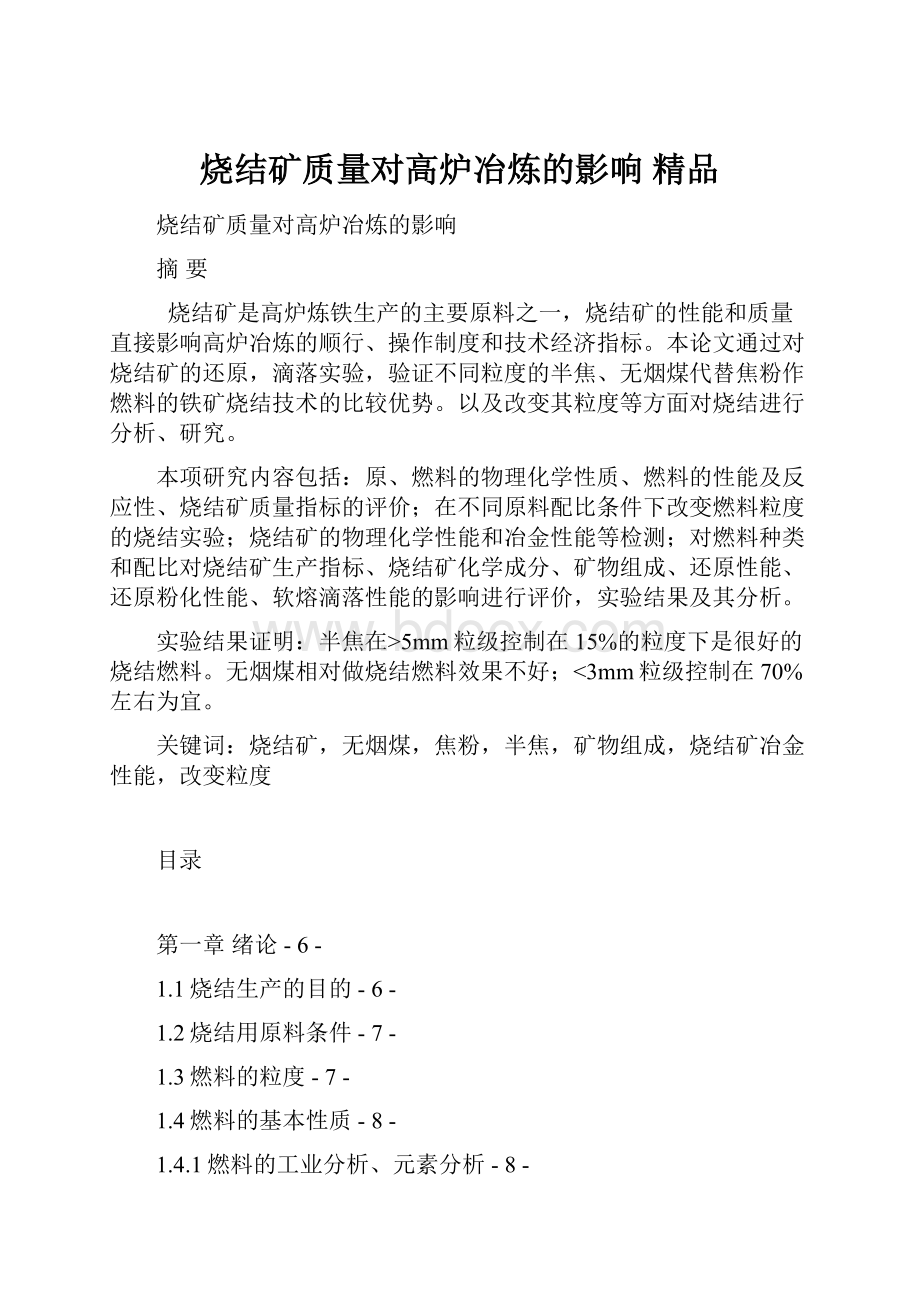
烧结矿质量对高炉冶炼的影响精品
烧结矿质量对高炉冶炼的影响
摘要
烧结矿是高炉炼铁生产的主要原料之一,烧结矿的性能和质量直接影响高炉冶炼的顺行、操作制度和技术经济指标。
本论文通过对烧结矿的还原,滴落实验,验证不同粒度的半焦、无烟煤代替焦粉作燃料的铁矿烧结技术的比较优势。
以及改变其粒度等方面对烧结进行分析、研究。
本项研究内容包括:
原、燃料的物理化学性质、燃料的性能及反应性、烧结矿质量指标的评价;在不同原料配比条件下改变燃料粒度的烧结实验;烧结矿的物理化学性能和冶金性能等检测;对燃料种类和配比对烧结矿生产指标、烧结矿化学成分、矿物组成、还原性能、还原粉化性能、软熔滴落性能的影响进行评价,实验结果及其分析。
实验结果证明:
半焦在>5mm粒级控制在15%的粒度下是很好的烧结燃料。
无烟煤相对做烧结燃料效果不好;<3mm粒级控制在70%左右为宜。
关键词:
烧结矿,无烟煤,焦粉,半焦,矿物组成,烧结矿冶金性能,改变粒度
目录
第一章绪论-6-
1.1烧结生产的目的-6-
1.2烧结用原料条件-7-
1.3燃料的粒度-7-
1.4燃料的基本性质-8-
1.4.1燃料的工业分析、元素分析-8-
1.4.2燃料的灰成分和灰熔点-10-
第二章烧结的作用-11-
2.1烧结矿的作用-11-
2.2烧结机的作用-12-
2.3烧结矿中MgO作用机理-12-
第三章烧结生成工艺及生产的工艺流程-13-
3.1烧结生成工艺-13-
3.2烧结生产的工艺流程-13-
3.2.1烧结原料的准备-14-
3.2.2配料与混合-14-
3.2.3烧结生产-15-
第四章烧结矿对高炉冶炼的影响-18-
4.1烧结矿指标对高炉冶炼过程的影响-18-
4.2烧结矿指标和冶金性能的影响因素-20-
第五章结论-24-
参考文献-25-
致谢-26-
第一章绪论
1.1烧结生产的目的
炼铁反应大多在气流与固体填充料床之间进行,固体炉料相对上升气流而下降,稳定的操作要求填充床具有一定透气性,这就要求炉料必须具有一定粒度且粒度均匀。
天然或加工的炉料(铁矿、熔剂及燃料)往往不具备这样的要求,所以必须供应块状的含铁炉料。
因此,必须通过烧结法或球团法将粉块造成块状。
高炉生产要想实现良好的运行,就必须要求炉料具有较高的冷态强度和良好的冶金性能。
烧结生产的目的主要体现在以下几个方面:
①钢铁工业的迅速发展加大了烧结生产对贫矿的利用,特别是贫矿富选,选矿所获精粉及天然富矿在开采、准备处理过程中会产生粉末,这些粉末不能直接入炉,必须通过造块处理才能供高炉使用。
②粉矿通过烧结之后,可进一步控制和改善含铁原料的冶金性能(如成分、粒度、还原性、软熔性等),为强化高炉冶炼提供更好的原料条件,有助于高炉炉况的稳定与经济技术指标的改善与提高。
首先,铁矿粉在烧结前经过仔细的混合,成分更均匀;其次,烧结中因固体燃料消失,熔剂分解,液相冷凝收缩,形成大量的孔隙,石灰石、白云石提供的CaO、MgO与矿粉中的其它组分反应,生成有利于还原、造渣的矿物成分;最后,通过烧结可以去除80%~90%的硫,大大减轻了高炉冶炼过程中的脱硫任务,提高了生铁质量。
同时也可去除部分的氟、锌、钾、钠等对高炉冶炼有害的元素,这样,高炉可以少加或不加生熔剂,使炉内还原、造渣过程得以改善,同时,也有助于操作制度的稳定,为优质、高产、低耗创造条件;稳定了高炉生产。
③烧结矿具有较高的强度可以适应高炉冶炼、直接还原等在流体力学的要求。
④烧结对原料的适应性强,通过烧结造块可有效地回收利用冶金、化工等生产部门产生的含铁废料,如矿尘、轧钢皮、钢渣、硫酸渣等,即充分利用了资源,又消除了环境污染,还可以降低成本,增加经济效益和社会效益。
为了使烧结矿或铁矿石能经济高效地得到温度和成分合乎要求的液态生铁,高炉能够稳定顺行地生产,对烧结矿的质量要求是:
具有良好的冷强度,减少烧结矿在运输和倒翻过程的破坏作用,保证烧结矿在冶炼过程时仍能保持一定的粒度及强度;良好的热强度,减少烧结矿在还原过程中的破碎及产生的粉末量;具有良好的还原性保证烧结矿在高炉内快速还原;具有良好的软熔滴落性能,保证高效率地完成还原、造渣、传热和渣铁分离过程。
1.2烧结用原料条件
根据炼铁厂的实际情况,本实验采用的含铁原料分别为60%澳大利亚铁精矿、20%巴西铁精矿、20%伊朗铁精矿和返矿,熔剂分别为石灰石粉、生石灰、菱镁石粉,其化学成分见表2.1。
表1-1含铁原料、熔剂的化学成分,w%
品名
TFe
FeO
SiO2
CaO
MgO
Ig
澳矿
61.86
0.35
4.65
0.14
0.15
4.58
巴西矿
65.39
0.54
3.17
0.1
0.1
2.1
伊朗矿
54.72
13.23
8.16
5.05
1.33
3.51
返矿
54.58
11.31
6.18
10.7
2.85
-0.98
石灰石
0.28
0.27
3.48
51.93
1.79
41.50
生石灰
0.56
0.18
6.31
68.24
3.72
19.35
菱镁石
3.28
1.35
7.82
12.67
32.42
40.91
1.3燃料的粒度
为了用尽可能少的燃料达到所需温度,烧结过程中的传热速度和燃烧速度必须接近。
而燃料的粒度、反应性和外部燃烧条件等都将影响其燃烧速度。
为充分利用燃料的燃烧热,提高燃料的利用率,需合理选择燃料的粒度及粒度分布。
合理的燃料粒度是根据燃料本身条件,烧结原料粒度和烧结工艺参数确定的。
实验用燃料的粒度组成见表2.2。
由表2.2可见,若以焦粉的粒度为实验参考,半焦中>5mm粒度级只占2.65%,考虑到烧结过程燃料对透气性的影响,故半焦的烧结实验分为两步,第一步采用半焦粉自身的粒度进行实验,第二步是将半焦的粒度调整到与焦粉相当的粒度级再次实验;而无烟煤由于反应性较强,粒度范围可适当宽一些,但粒度的上、下限应尽量与焦粉接近。
细粉含量应尽量少。
一般认为<3mm粒度级占70.0%为宜。
实验用无烟煤中<3mm粒度级,与要求的粒度比较接近,粒度较粗。
表1-2燃料的粒度组成,w%
编号
>5
5-3
3-1
<1
JF
15.0
22.5
37.5
25.0
BJ
2.65
28.4
49.05
19.9
BJ*
15.33
24.71
42.67
17.31
WYM
14.0
18.0
43.0
25.0
注:
BJ*—改变粒度后的半焦
1.4燃料的基本性质
1.4.1燃料的工业分析、元素分析
热值和可磨性见表2.3。
燃料的发热量采用GB/T213-2003煤的发热量测定方法测定。
表1-3燃料的工业分析、元素分析和热值
燃料
工业分析
元素分析
Qnet,v,ar
MJ·kg-1
HGI
Mt
Mad
Ad
Vdaf
FCd
St,d
Cad
Had
Oad
Nad
JF
0.88
0.84
14.10
1.98
83.49
0.75
83.15
0.24
0.67
0.38
28.27
33
BJ
10.4
7.55
10.48
11.24
73.46
0.61
71.50
1.25
5.76
0.72
24.40
53
WYM
5.6
0.94
18.30
6.46
73.79
0.16
74.78
0.76
2.95
0.49
24.14
68
注:
Mt—全水;Mad—分析基水分;Ad—干基灰分;Vdaf—干燥无灰基挥发份;FCad—分析基固定碳;
Qnet,v,ar—低发热量。
由表2.3可见,三种燃料比较具有如下特点:
(1)灰分:
半焦的灰分最低为10.48,无烟煤灰分最低为18.30。
半焦比焦粉的灰分低3.62%,。
无烟煤比焦粉的灰分高4.20%
(2)挥发份:
半焦的挥发份为11.24,为焦粉的5.68倍。
无烟煤为6.46,为焦粉的3.263倍。
(3)含硫量:
半焦的硫份为0.61%,与焦粉的接近。
无烟煤的硫份为0.16%,无烟煤为焦粉硫份的21.33%。
(4)固定炭:
半焦的固定炭为73.46%,与无烟煤相近,比焦粉低12%。
(5)可磨性:
半焦的可磨性为53,明显高于焦粉的可磨性36。
无烟煤的可磨性68,也明显高于焦粉的可耐磨性。
(6)发热量:
半焦的发热量为24.40MJ·kg-1,无烟煤为24.14,而焦粉的为28.27MJ·kg-1,半焦比焦粉低13.69%。
无烟煤比焦粉低15.69%
烧结要求燃料的灰分尽可能低些,因为燃料中灰分含量增多必然引起烧结料含铁量降低和酸性氧化物增多(灰分中的SiO2数量高达50%以上),因而必然相应需要增加溶剂的消耗量,同时灰分的增加将引起燃料消耗量不成正比的增加。
做为烧结燃料,要求它挥发份的含量不能太高,以免燃料中的挥发物质在温度较低的地方凝结下来恶化料层透气性和粘结在集气管及抽风机的叶片上,影响烧结过程的正常进行。
此外,燃料中的挥发分在着火前即已挥发出去,不能在烧结过程中被利用。
所以,烧结生产使用的燃料最好选用固定碳高、灰分低、挥发分低及含硫量低的优质燃料。
烧结生产对燃料的要求一般是发热量>25MJ·kg-1,挥发份<10%,灰分<15%,硫<1%。
根据此要求,半焦粉的灰分、含硫量和发热量基本满足烧结用燃料的要求,而挥发份略超出烧结用燃料的标准。
1.4.2燃料的灰成分和灰熔点
燃料的灰成分和灰熔点见表2.4。
表1-4燃料的灰成分和灰熔点
燃料
灰熔点/℃
灰成分分析,w%
DT
ST
HT
FT
SiO2
Al2O3
Fe2O3
CaO
MgO
Na2O
K2O
TiO2
SO3
JF
1320
1360
1370
1390
39.76
22.83
7.68
6.82
1.84
1.48
3.79
BJ
1150
1160
1170
1180
28.56
10.90
9.34
26.94
2.28
0.55
0.66
0.50
6.55
WYM
1220
1240
1260
1280
49.83
17.49
5.62
11.77
2.40
0.80
2.55
1.01
2.17
DT—变形温度;ST—软化温度;HT—半球温度;FT—流动温度
由表1-4可见,半焦、无烟煤与焦炭相比,半焦灰成分中的CaO与Fe2O3含量均高,半焦灰成分中CaO含量高达26.94%,是焦炭灰分含CaO的4倍,无烟煤灰分含CaO含量11.77%,是焦炭灰分含CaO的1.726倍。
半焦灰分中Fe2O3为9.34%,是焦粉的1.22倍。
无烟煤灰分中Fe2O3为5.62%,是焦粉的0.732倍。
半焦灰分中的MgO含量为2.28%,与无烟煤的2.40%相近,是焦炭灰成分中MgO含量的1.24倍,无烟煤灰成分中MgO含量是焦粉的1.304倍。
上述半焦灰成分中的有用成分CaO,MgO,Fe2O3都高,可补充烧结矿的原料和熔剂。
灰分中的MgO对改善铁矿石的还原强度、炉渣的熔化性能等是有利的。
半焦灰分的软化温度(熔点)ST和流动温度FT均低于焦粉和无烟煤。
软化温度(熔点)和流动温度按焦粉、无烟煤和半焦的顺序依次降低。
图2.1示出了燃料灰分软化温度ST和流动温度FT与灰分碱度(RA)的关系。
灰分碱度的计算式为:
(1.1)
图1-1软化温度(熔点)ST和流动温度FT与碱度R的关系
由图2.1可见,随灰分碱度的增加,灰分软化温度(熔点)和流动温度呈降低趋势,半焦灰分的碱度比焦粉和无烟煤灰分的碱度高出3~5倍,灰分软化温度(熔点)低80~200℃,灰分流动温度低100~210℃。
但是灰分碱度高可以增加烧结矿中的粘结相量,尤其是灰分软化温度(熔点)和灰分流动温度降低,在烧结过程中容易生成液相,有利于矿石的烧结,灰成分中的MgO对实现低硅烧结技术的实施是有利的。
第二章烧结的作用
2.1烧结矿的作用
烧结是把粉状物料转变为致密体,是一个传统的工艺过程。
人们很早就利用这个工艺来生产陶瓷、粉末冶金、耐火材料、超高温材料等。
一般来说,粉体经过成型后,通过烧结得到的致密体是一种多晶材料,其显微结构由晶体、玻璃体和气孔组成。
烧结过程直接影响显微结构中的晶粒尺寸、气孔尺寸及晶界形状和分布。
无机材料的性能不仅与材料组成(化学组成与矿物组成)有关,还与材料的显微结构有密切的关系。
2.2烧结机的作用
烧结机适用于大型黑色冶金烧结厂的烧结作业,它是抽风烧结过程中的主体设备,可将不同成份,不同粒度的精矿粉,富矿粉烧结成块,并部分消除矿石中所含的硫,磷等有害杂质。
烧结机按烧结面积划分为不同长度不同宽度几种规格,用户根据其产量或场地情况进行选用。
烧结面积越大,产量就越高。
2.3烧结矿中MgO作用机理
(1)随着烧结矿中MgO含量的增加,烧结液相
开始形成温度明显上升,烧结液相流动性降低.
MgO的这一烧结行为是影响烧结矿产、质量指标的
本质问题所在.
(2)在MgO质量分数在015%~210%范围
内,随着MgO含量的增加,烧结试样的黏结相强度
有降低趋势.为了提高烧结矿固结强度,应该适当
降低烧结矿MgO含量.
(3)不同镁质熔剂对烧结试样黏结相强度的影
响各不相同,镁质熔剂使用蛇纹石试样的黏结相强
度相对最高,其次是轻烧白云石,而使用白云石时则
黏结相强度相对最低.
(4)基于获得优良的烧结矿的产量、质量指标
和冶金性能之目的,烧结矿中适宜的MgO质量分
数在112%左右,镁质熔剂适宜选用白云石和蛇纹
第三章烧结生成工艺及生产的工艺流程
3.1烧结生成工艺
铁矿粉烧结是一种铁矿粉造块方法,即将细粒含铁原料与燃料、熔剂按一定比例混合,加水润湿、混匀而制成烧结料,然后布于烧结机上,通过点火、抽风,并借助烧结料中燃料燃烧产生高温,进而发生一系列的物理化学反应,生成部分低熔点物质,并软化熔融产生一定数量的液相,将铁矿物颗粒润湿粘结起来,冷却后形成具有一定强度的多孔产品一烧结矿。
3.2烧结生产的工艺流程
目前生产上广泛采用带式抽风烧结机生产烧结矿。
主要包括烧结料的准备,配料与混合,烧结和产品处理等工序。
如图3-1烧结生产工艺流程图。
图3-1烧结生产工艺流程图
3.2.1烧结原料的准备
①含铁原料
含铁量较高、粒度<5mm的矿粉,铁精矿,高炉炉尘,轧钢皮,钢渣等。
一般要求含铁原料品位高,成分稳定,杂质少。
②熔剂
要求熔剂中有效CaO含量高,杂质少,成分稳定,含水3%左右,粒度小于3mm的占90%以上。
在烧结料中加入一定量的白云石,使烧结矿含有适当的MgO,对烧结过程有良好的作用,可以提高烧结矿的质量。
③燃料
主要为焦粉和无烟煤。
对燃料的要求是固定碳含量高,灰分低,挥发分低,含硫低,成分稳定,含水小于10%,粒度小于3mm的占95%以上。
3.2.2配料与混合
①配料
配料目的:
获得化学成分和物理性质稳定的烧结矿,满足高炉冶炼的要求。
常用的配料方法:
容积配料法和质量配料法。
容积配料法是基于物料堆积密度不变,原料的质量与体积成比例这一条件进行的。
准确性较差。
质量配料法是按原料的质量配料。
比容积法准确,便于实现自动化。
②混合
混合目的:
使烧结料的成分均匀,水分合适,易于造球,从而获得粒度组成良好的烧结混合料,以保证烧结矿的质量和提高产量。
混合作业:
加水润湿、混匀和造球。
根据原料性质不同,可采用一次混合或二次混合两种流程。
一次混合的目的:
润湿与混匀,当加热返矿时还可使物料预热。
二次混合的目的:
继续混匀,造球,以改善烧结料层透气性。
用粒度10~Omm的富矿粉烧结时,因其粒度已经达到造球需要,采用一次混合,混合时间约50s。
使用细磨精矿粉烧结时,因粒度过细,料层透气性差,为改善透气性,必须在混合过程中造球,所以采用二次混合,混合时间一般不少于2.5~3min。
我国大多采用二次混合。
3.2.3烧结生产
烧结作业是烧结生产的中心环节,它包括布料、点火、烧结等主要工序。
①布料
将铺底料、混合料铺在烧结机台车上的作业。
当采用铺底料工艺时,在布混合料之前,先铺一层粒度为10~25mm,厚度为20~25mm的小块烧结矿作为铺底料,其目的是保护炉箅,降低除尘负荷,延长风机转子寿命,减少或消除炉箅粘料。
铺完底料后,随之进行布料。
布料时要求混合料的粒度和化学成分等沿台车纵横方向均匀分布,并且有一定的松散性,表面平整。
目前采用较多的是圆辊布料机布料。
②点火
点火操作是对台车上的料层表面进行点燃,并使之燃烧。
点火要求有足够的点火温度,适宜的高温保持时间,沿台车宽度点火均匀。
点火温度取决于烧结生成物的熔化温度。
常控制在1250±50℃。
点火时间通常40~60s。
点火真空度4~6kPa。
点火深度为10~20mm。
③烧结
准确控制烧结的风量、真空度、料层厚度、机速和烧结终点。
烧结风量:
平均每吨烧结矿需风量为3200m3,按烧结面积计算为(70~90)m3/(cm2.min)。
真空度:
决定于风机能力、抽风系统阻力、料层透气性和漏风损失情况。
料层厚度:
合适的料层厚度应将高产和优质结合起来考虑。
国内一般采用料层厚度为250~500mm。
机速:
合适的机速应保证烧结料在预定的烧结终点烧透烧好。
实际生产中,机速一般控制在1.5~4m/min为宜。
烧结终点的判断与控制:
控制烧结终点,即控制烧结过程全部完成时台车所处的位置。
中小型烧结机终点一般控制在倒数第二个风箱处,大型烧结机控制在倒数第三个风箱处。
带式烧结机抽风烧结过程是自上而下进行的,沿其料层高度温度变化的情况一般可分为5层,各层中的反应变化情况如图2—5所示。
点火开始以后,依次出现烧结矿层,燃烧层,预热层,干燥层和过湿层。
然后后四层又相继消失,最终只剩烧结矿层。
①烧结矿层
经高温点火后,烧结料中燃料燃烧放出大量热量,使料层中矿物产生熔融,随着燃烧层下移和冷空气的通过,生成的熔融液相被冷却而再结晶(1000—1100℃)凝固成网孔结构的烧结矿。
这层的主要变化是熔融物的凝固,伴随着结晶和析出新矿物,还有吸入的冷空气被预热,同时烧结矿被冷却,和空气接触时低价氧化物可能被再氧化。
②燃烧层
燃料在该层燃烧,温度高达1350~1600℃,使矿物软化熔融黏结成块。
该层除燃烧反应外,还发生固体物料的熔化、还原、氧化以及石灰石和硫化物的分解等反应。
③预热层
由燃烧层下来的高温废气,把下部混合料很快预热到着火温度,一般为400~800℃。
此层内开始进行固相反应,结晶水及部分碳酸盐、硫酸盐分解,磁铁矿局部被氧化。
④干燥层
干燥层受预热层下来的废气加热,温度很快上升到100℃以上,混合料中的游离水大量蒸发,此层厚度一般为l0~30mm。
实际上干燥层与预热层难以截然分开,可以统称为干燥预热层。
该层中料球被急剧加热,迅速干燥,易被破坏,恶化料层透气性。
⑤过湿层
从干燥层下来的热废气含有大量水分,料温低于水蒸气的露点温度时,废气中的水蒸气会重新凝结,使混合料中水分大量增加而形成过湿层。
此层水分过多,使料层透气性变坏,降低烧结速度。
烧结过程中的基本化学反应
①固体碳的燃烧反应
固体碳燃烧反应为:
反应后生成C0和C02,还有部分剩余氧气,为其他反应提供了氧化还原气体和热量。
燃烧产生的废气成分取决于烧结的原料条件、燃料用量、还原和氧化反应的发展程度、以及抽过燃烧层的气体成分等因素。
②碳酸盐的分解和矿化作用
烧结料中的碳酸盐有CaC03、MgC03、FeC03、MnC03等,其中以CaC03为主。
在烧结条件下,CaC03在720℃左右开始分解,880℃时开始化学沸腾,其他碳酸盐相应的分解温度较低些。
碳酸钙分解产物Ca0能与烧结料中的其他矿物发生反应,生成新的化合物,这就是矿化作用。
反应式为:
CaCO3+SiO2=CaSiO3+CO2
CaCO3+Fe2O3=CaO·Fe2O3+CO2
如果矿化作用不完全,将有残留的自由Ca0存在,在存放过程中,它将同大气中的水分进行消化作用:
CaO+H2O=Ca(OH)2
使烧结矿的体积膨胀而粉化。
③铁和锰氧化物的分解、还原和氧化
铁的氧化物在烧结条件下,温度高于l300℃时,Fe203可以分解
Fe304在烧结条件下分解压很小,但在有Si02存在、温度大于1300℃时,也可能分解。
第四章烧结矿对高炉冶炼的影响
4.1烧结矿指标对高炉冶炼过程的影响
高炉冶炼过程是在一个密闭的竖炉内进行的,其特点是:
高炉过程中决定性的因素是炉料自上而下,煤气自下而上的相互紧密接触才能完成这一过程。
在炉料与煤气逆流运动过程中完成多种错综复杂的化学变化和物理变化。
高炉对炉料质量的要求,除含铁品位高、化学成分稳定、粒度要求合适和冶金性能良好,以及耐磨、抗压等物理性能良好以外,更重要的是对其在高炉冶炼过程中的还原性、还原粉化和高温冶金性能的要求。
由于含铁原料的加工工艺过程不同,化学成分及组织结构直接影响其在炉内的冶金性能。
炉料的性能指标及其对高炉冶炼的影响主要有以下几个方面:
(1)还原性RI
铁矿石还原性是模拟炉料自高炉上部进入高温区的条件,用还原气体从铁矿石中排除与铁结合氧的难易程度的一种度量,高还原性的炉料是高炉冶炼的理想精料。
还原性是含铁炉料冶金性能的基础,其对高炉冶炼,尤其是加强稳定和降低焦比有很大影响,许多冶金工作者进行了大量的研究工作,发现还原性和含铁炉料的化学成分、矿物组成、矿物结构及物理性能(包括粒度、气孔率、气孔大小等)有很大的关系[12,13]。
烧结矿还原性对高炉上部的间接还原率和高炉煤气利用率以及软熔带初渣中的FeO含量产生影响。
从而,对高炉的能源利用率,以及炉渣脱硫能力带来较大影响。
烧结矿和球团矿的还原性及冶金性能优于生矿。
烧结矿的还原性好,就表明矿石氧化物中的氧容易通过间接还原反应被夺去。
还原效率高,高炉煤气利用率提高,燃料降低,可有效地节约资源和能源。
(2)转鼓指数TI
烧结矿的冷强度TI,影响到运输和倒翻过程中的破坏作用,以便进入冶炼过程时仍能保持一定的粒度和强度。
烧结矿冷态强度指标的高低,关系到高炉上部的透气性。
烧结矿的强度主要与烧结矿的矿物组成、单个矿物的强度、原料破碎的粒度、烧结点火温度、燃料单耗、料层厚度、烧结机带速和烧结矿冷却速度等工艺条件有关。
烧结矿中加入6%~10%的石灰,可大幅度提高其冷强度。
在碱度合适的范围内,适当增加硅石配比,提高粘结液相的比例,可提高转鼓强度。
(3)低温还原粉化率RDI
烧结矿低温粉化性能指标:
表示烧结矿在低温条件下(500℃)受还原气氛作用及移动后,其块度变化及粉化程度。
该指标是模拟烧结矿在高炉上部低温区受还原气氛作用并下移过程中的块度变化及粉化情况。
烧结矿的低温还原粉化率对高炉上部的透气性有一定影响。
烧结矿在高炉上部的低温区还原时发生还原粉化,会使料柱的空隙度降低,透气性