汽轮机轴承检修.docx
《汽轮机轴承检修.docx》由会员分享,可在线阅读,更多相关《汽轮机轴承检修.docx(42页珍藏版)》请在冰豆网上搜索。
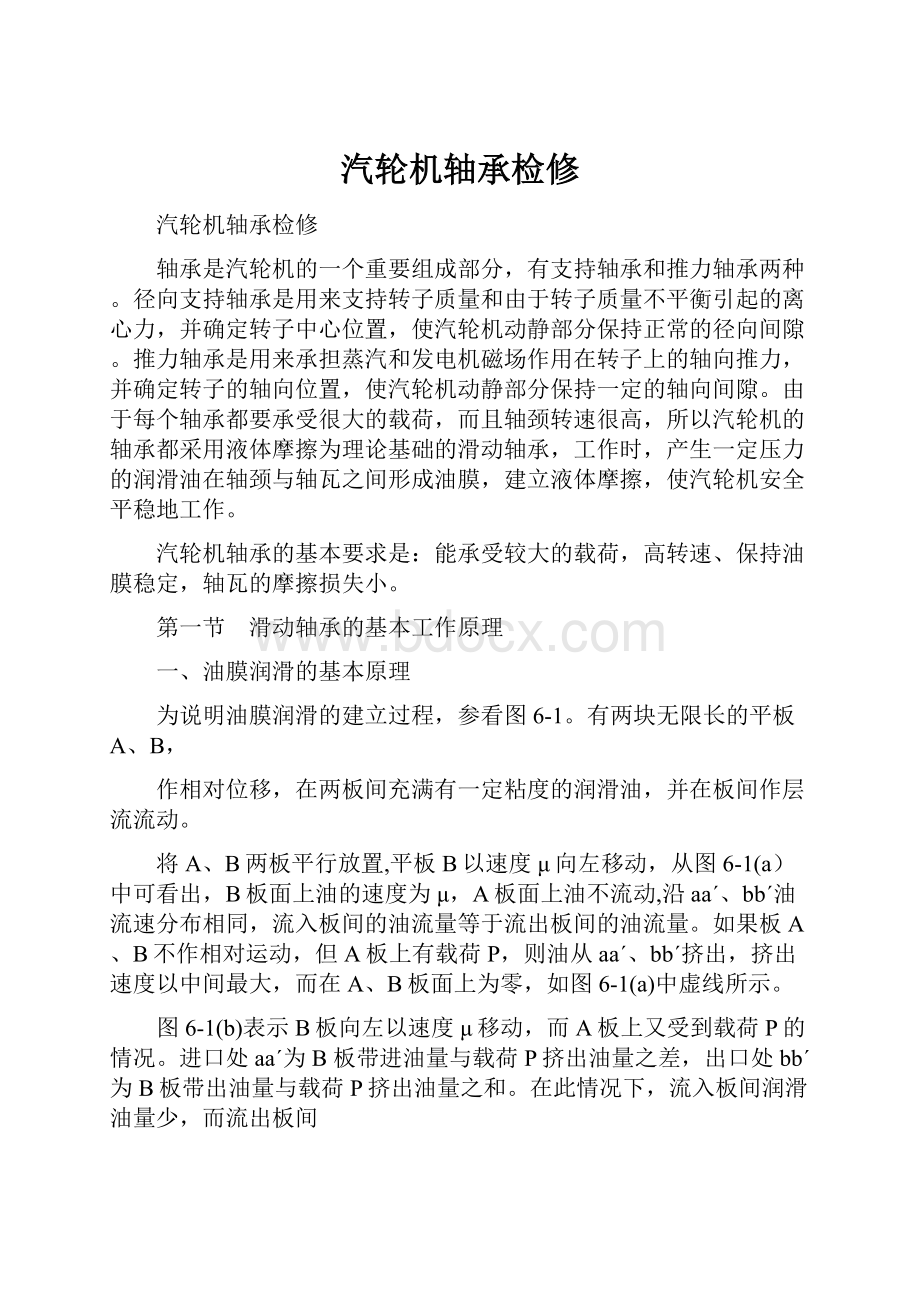
汽轮机轴承检修
汽轮机轴承检修
轴承是汽轮机的一个重要组成部分,有支持轴承和推力轴承两种。
径向支持轴承是用来支持转子质量和由于转子质量不平衡引起的离心力,并确定转子中心位置,使汽轮机动静部分保持正常的径向间隙。
推力轴承是用来承担蒸汽和发电机磁场作用在转子上的轴向推力,并确定转子的轴向位置,使汽轮机动静部分保持一定的轴向间隙。
由于每个轴承都要承受很大的载荷,而且轴颈转速很高,所以汽轮机的轴承都采用液体摩擦为理论基础的滑动轴承,工作时,产生一定压力的润滑油在轴颈与轴瓦之间形成油膜,建立液体摩擦,使汽轮机安全平稳地工作。
汽轮机轴承的基本要求是:
能承受较大的载荷,高转速、保持油膜稳定,轴瓦的摩擦损失小。
第一节 滑动轴承的基本工作原理
一、油膜润滑的基本原理
为说明油膜润滑的建立过程,参看图6-1。
有两块无限长的平板A、B,
作相对位移,在两板间充满有一定粘度的润滑油,并在板间作层流流动。
将A、B两板平行放置,平板B以速度μ向左移动,从图6-1(a)中可看出,B板面上油的速度为μ,A板面上油不流动,沿aa´、bb´油流速分布相同,流入板间的油流量等于流出板间的油流量。
如果板A、B不作相对运动,但A板上有载荷P,则油从aa´、bb´挤出,挤出速度以中间最大,而在A、B板面上为零,如图6-1(a)中虚线所示。
图6-1(b)表示B板向左以速度μ移动,而A板上又受到载荷P的情况。
进口处aa´为B板带进油量与载荷P挤出油量之差,出口处bb´为B板带出油量与载荷P挤出油量之和。
在此情况下,流入板间润滑油量少,而流出板间
润滑油量多,这将使A、B板间没有油而接触在一起,形成干摩擦。
图6-1 平板间液体摩擦的建立
(a)A、B不作相对运动;(b)B板向左以速度μ移动;
(c)A、B两板楔形布置,B板向左以速度μ移动
A、B两板置成楔形,B板向左移动(从宽口向狭口移动),如图6-1所示。
流进aa´处油量大于流出bb´处油量,油在两板间积聚而产生油压。
此时,如无载荷P,此油压会使bb´张大,以保持进、出口油量相等。
如果A板上有载荷P,如前所述,进口aa´处油量会减少,而出口bb´处油量会增加,就能使进出口油量相等,保持间隙中形成稳定油膜,建立油膜润滑,如增加B板移动速度或增大油粘度,将使油膜厚度增加,当载荷减小,也将使油膜厚度增加。
综上所述,要使有载荷相对运动(移动)的平板间建立油膜润滑必须满足:
(1)两滑动面之间要形成斜隙;
(2)两滑动面之间要充满足量的具有一定油性和粘性的润滑油;
(3)两滑动面之间要有相对运动,其运动方向是使润滑油由楔形间隙的宽口流向窄口。
显然,当润滑油粘性增大、两滑动面间的间隙小、楔形角度增大以及两板之间相对移动速度增加时,都会使间隙中的油膜压力升高。
二、轴承的工作原理
以圆筒形轴瓦为例,见图6-2(a),轴瓦直径是大于轴颈直径的,在静止状态下,轴颈置于轴瓦底部,轴颈圆心O´在轴瓦中心O的正下方,轴颈与轴瓦之间构成自上而下的楔形截面间隙。
当连续向轴承内提供足量的润滑油,并使轴颈高速旋转(图示为顺时钟向旋转),右侧楔形间隙中有粘性的润滑油附在轴颈上一起转动,并带动各层油一起转动,而且将润滑油由宽口带向窄口,楔形间隙的进油量大于出油量,并且由于润滑油几乎不可压缩,使积聚在狭窄的楔形间隙中产生油压,当油压超过轴颈上的载荷时,就抬起轴颈,轴颈抬起后,楔形间隙增大,油压有所下降,轴颈又下落一些,直至楔形间隙内油压与轴颈上载荷平衡,轴颈便稳定在一定位置上旋转。
此时,轴颈与轴瓦间有油膜隔开,建立了液体摩擦,使轴承稳定工作。
图6-2轴承中液体摩擦的建立
(a)轴在轴承中构成楔形间隙;
(b)轴心运动轨迹及油楔中的压力分布(周向);
(c)油楔中的压力分布(轴向)
如载荷不变,油粘度愈高、转速愈高,油膜压力也随之增大,轴颈就抬得越高;如载荷不变、油粘度不变,随转速升高,轴颈中心位置改变,当转速达无穷大时,理论上轴颈中心与轴瓦中心重合[参看图6-2(b)]。
随着转速升高,轴颈中心线轨迹近似为一半圆的曲线。
油楔中压力分布也可从图6-2(b)中看出。
在径向,楔形进口处油压最低,随着楔形口的缩小而油压升高,并逐渐达到最大值Pmax,而后油压又下降,在楔形出口处(即最小间隙后)为零。
在轴向,由于轴瓦有一定宽度,润滑油要从两端流出,所以在两端油压为零,而宽度的中间位置油压最高,如图6-2(c)所示。
所以轴瓦宽度(长度)也影响承载能力,所以在下瓦中间是不开圆周油槽的。
理论上讲,当载荷、供油条件、轴颈及其转速等不变的条件下,轴瓦宽度尺寸愈大,其油压愈高,轴颈被抬得越高。
但轴瓦宽度尺寸大会影响轴承冷却,并影响油膜稳定性(因轴颈抬得越高,相对偏心距愈小),所以必须合理地选择轴瓦宽度。
第二节轴承的油膜振荡
由于油膜支持轴颈在轴瓦内高速转动,希望轴颈中心相对轴瓦中心在某一固定位置,这就是轴承工作时的稳定性。
油膜振荡是轴承工作过程中失去稳定性的一种现象。
随着机组容量增大,机组的临界转速就下降,出现轴承油膜振荡的可能性增大。
油膜振荡的出现,将使机组无法安全运行,因此,已引起普遍的关注。
一、油膜振荡现象
油膜振荡的本质是一种自激振动,所谓自激振动是运动体通过本身的运动不断向自身馈送能量,自己激励自己产生与外界激振力无关的振动。
对轴承讲,轴颈在轴瓦内高速旋转,在一定条件下,被轴颈带动而流动的润滑油反过来激励轴颈而发生的一种自激振动,即称油膜振荡。
众所周知,对振动体振动的研究,主要办法是通过激振力频率(转速)与振动体的振幅、振动频率、振型之间的关系来得出产生振动的原因。
首先观察受一定载荷的轴颈在轴瓦中的工作情况,当转子转速由零逐渐加速时,轴颈中心的运动状态。
当转速达到一定值时,轴心的振动频率除有与转速相同的由不平衡质量引起的振动外,又出现低频振动,低频振动频率几乎为转速(主频率)的1/2左右,轴心出现涡动运动。
这种现象可以在一只轴承内产生,也可以在相邻几个轴承内同时出现,此时,刚开始产生轴心涡动的转速称失稳转速,涡动频率几乎为转速的1/2。
失稳转速的大小,取决于转子和支持轴承的特性和工作条件,如果这些因素不变,失稳转速是某一固定值,如图6-3上横坐标上A点。
当转速由失稳转速升高至转子第一阶临界转速时,振幅增加,这是转子自身的自激振动,其振动频率为ωc1,如图上A1,所示。
转速超过第一临界转速后,振幅又减小,轴心的涡动频率约为此时转速的1/2。
当转速继续升高到A2点,相当于两倍第一临界转速2ωc1时,振动再次加剧,振幅大增,涡动频率约为此时转速的1/2,即1/2ωc1=ωc1。
此后,随着转速增加,振幅不会再减小,而且涡动频率不再改变,始终维持在ωc1,这通常被称为油膜振荡的惯性效应。
图6-3转轴涡动的频率、振幅与转速的关系
由A点至A2点轴颈中心发生的振动频率约等于当时转速1/2的小振动称半速涡动。
自A2点以后轴心发生的振动频率等于转子的第一阶临界转速ωc1称油膜振荡。
将在A点处开始失去稳定时(即开始产生半速涡动)的转速称失稳转速。
综上所述,当半速涡动频率等于第一阶临界转速(此时转子的转速为两倍的第一阶临界转速)时,就产生油膜振荡,即油膜振荡频率正好等于转子的固有频率,产生了共振。
显然,油膜振荡的干扰力来自轴颈本身的涡动运动,与外界无关,因此油膜振荡属于自激振动的范畴。
油膜振荡一旦发生,不能用升高转速的办法来消除,因油膜振荡能够在一个较宽的转速变动范围内保持,振幅也处于共振状态下的大振幅特性。
油膜振荡下的振幅比半速涡动时振幅大得多,油膜破坏,轴颈与轴瓦相碰撞而损坏,而此时振动频率又与转子第一阶临界转速相重合,成为激发转子共振的激振力,使转子产生象在第一阶临界转速下运行时的共振现象,导致转子损坏。
至于半速涡动,振幅较小,虽然不会破坏油膜,但由于振动是动载荷,长期工作时,会引起零件松动和疲劳损坏。
因此,半速涡动也应尽力去消除。
如前述,只有转子的转速等于或高于二倍的第一阶临界转速时才有可能出现油膜振荡。
由于大容量机组临界转速显著下降,轴承产生油膜振荡可能性增大。
对于刚性转子或第一阶临界转速高于1500r/min的挠性转子,在工作转速范围内只可能产生半速涡动,而不会产生油膜振荡。
二、产生油膜振荡的原因
从轴承的工作原理可知,在一定的转速、载荷、油粘度下,轴颈中心O´将处于某一固定位置而达到平衡状态,这时载荷P和油膜作用力Pg的大小相
等,方向相反并处于一条直线上,即两者合力为零,轴颈中心稳定在O´不动,
如图6-4所示。
如果外界给轴颈一个干扰,使轴颈中心由O´移动至O",油楔相应变化,油膜作用力合力的大小、方向随之变化,由Pg变化为
。
载荷P与油膜作用力合力
两者合力不再为零,而为F,如图6-4所示。
F可分解成沿油膜变形方向的弹性恢复Fr和垂直于油膜变形方向的切向力Ft,这个切向分力Ft,就是破坏轴颈稳定转动,引起涡动的根源,此力(Ft)称为失稳分力。
图6-4 油膜振荡的产生
轴颈在轴瓦内工作受到阻尼,如失稳分力小于轴颈的阻尼力,涡动是收敛的,属稳定工作状态,轴颈受到干扰位移后,又将自动回到平衡位置,如图6-5(a)所示。
图6-5 轴颈中心涡动轨迹
当失稳分力大于阻尼力时,涡动是发散的,属于不稳定状态。
此时轴颈中心绕平衡位置涡动,这种涡动本身又会使转轴受到离心力的作用,从而进一步扩大了轴颈的位移量,使失稳分力又进一步增大,涡动加大,如此恶性循环,最终导致油膜振荡,如图6-5(c)所示。
介于两者之间的情况是失稳力与阻尼力相等,涡动轨迹是近似于椭圆的封闭曲线,如图6-5(b)所示,这属不稳定状态,但振幅较小,此时涡动频率接近于当时转速的一半,称为半速涡动。
半速涡动的频率总是约为当时转速的一半的原因,可以作如下简释:
设有一个无载荷半径为r的轴颈,在充满润滑油的轴瓦内以角速度ω沿逆时针方向转动,并设轴瓦为无限长,即轴向两端无油泄漏。
此时轴颈中心J的稳定位置应与轴瓦中心0相重合,如图6-6(a)所示。
轴瓦间隙内各截面的油流情况相同,沿轴颈流速为γω,轴瓦表面处油流速度为零,通过间隙各截面的油流量相等,为1/2γωc(c为半径间隙)。
图6-6半速涡动的简单解释
现一受载轴颈在干扰下,中心在J位置,如图6-6(b)所示,连OJ线,左下半间隙的油容积流量(单位轴长度流量,此时仍设轴瓦为无限长,两端无泄漏)为:
流入流量
(c+e)
流出流量
(c-e)
式中e----偏心距。
由于流入流量与流出流量不等,并且流入量大于流出量,由于油不可压缩,轴颈势必作垂直于偏心距和与旋转方向作同向涡动,使轴颈让出图6-6(b)中的阴影部分空间,这部分空间面积大小等于2reΩ其中Ω为轴颈涡动的角速度),此面积应等于进出间隙油流量之差额时,才能维持流量平衡。
因此
(c+e)-
(c-e)=2reΩ(6-1)
由上式得Ω=
上式从理论上说明了轴颈涡动频率为轴颈转速1/2的原因。
但由于轴瓦不是无限长,两端有泄漏,而且轴瓦间隙内油流速的分布实际上如图6-6(c)所示,流入间隙流量要比理论的少一些,而流出的流量比理论的稍大一些,因此轴颈上实际发生的涡动频率略低于轴颈转速的1/2。
三、油膜振荡的防止和消除
防止和消除油膜振荡的基本方法是提高转子的失稳转速,使失稳转速高于工作转速,或者提高机组第一阶临界转速,使第一阶临界转速在1500r/min以上,因刚性转子和第一阶临界转速高于额定转速1/2的柔性转子至多只会产生半速涡动,而不会产生油膜振荡。
但对大容量机组而言,机组第一阶临界转速很难低于额定转速的1/2,因而只能从提高转子失稳转速着手,失稳转速提高到额定转速以上,即使转子第一阶临界转速低于额定转速的1/2,也能避免出现油膜振荡。
提高转子失稳转速也就是提高油膜工作的稳定性。
实践证明,失稳转速大小与轴承结构型式、间隙、载荷及临界转速等因素有关,只要诸因素不变,失稳转速为一定值。
图6-7 相对偏心率
如前述,转子在轴瓦中运行不稳定的根本原因是转子受到扰动后产生的失稳分力Ft.扰动愈大,轴颈在轴瓦内的偏移(相对偏移)愈大,失稳分力也愈大,越易产生半速涡动直至油膜振荡。
在同样的扰动下,如运行中本来轴颈的偏心距00´越大(油膜越薄),其相对偏移量就越小,失稳分力就越小,越不易产生半速涡动和油膜振荡;同理,在同样的扰动强度下,如运行中本来轴颈的偏心距00´小(油膜厚),就容易产生半速涡动和油膜振荡。
偏心距大小应以相对值来衡量。
轴颈中心O´与轴瓦中心O的距离00´称绝对偏心距,00´与它们的半径差(R-r)的比值称相对偏心率(相对偏心距),以k表示,如图6-7所示。
k=
k值愈大,失稳转速愈高,油膜稳定性愈好;k值愈小,则油膜稳定性愈差。
通常认为k值大于0.8,轴颈在任何情况下都不会产生油膜振荡。
因此,降低轴颈中心产O´在稳定状态下轴瓦内的位置以增大相对偏心率k值,就成为防止和消除油膜振荡的基本出发点。
增大相对偏心率的措施:
1、增加轴瓦的压比
轴颈上载荷不同,使轴颈中心在轴瓦内位置不同,相对偏心率k值也不同,失稳转速值也不同。
图6-8(a)表示轻载情况,失稳转速发生在第一阶临界转速之前,其油膜稳定区最小,转速升高到失稳转速时产生半速涡动,转速升至约二倍于第一临界转速时发生油膜振荡;图6-8(b)表示中载情况,失稳转速发生在第一临界转速和二倍第一临界转速之间,其油膜稳定区域较前者扩大,半速涡动范围缩小,在转速稍高于二倍第一临界转速时产生油膜振荡;图6-8(c)表示重载情况,它的油膜稳定区域最大,转速高出二倍第一临界转速较多时,轴承失稳,且不经半速涡动,而直接发生油膜振荡。
----频率 ———振幅
图6-8 载荷对油膜振荡的影响
(a)轻载ωe<ωc1;(b)中载ωc<ωe<2ωc1;(c)重载ωe>2ωc1
ωe—失稳转速;ωe1—第一临界转速
显然,在一定转速下,轴承在重载下的稳定性比轻载下稳定性好,这主要是由于重载下的相对偏心率k值大的原因。
工作转速愈高,轴颈相对偏心率愈小,愈容易产生油膜振荡,这对带动给水泵的小汽轮机来讲应引起注意。
图6-9给出了相对偏心率随轴承负荷系数s和轴瓦长径比β(轴瓦长度L与直径D之比)变化的一组曲线,以便找出增大相对偏心率的办法。
从图6-9中可看出,相对偏心率k是随轴承负荷系数s的增加以及长径比β的减小而增大的。
图6-9 圆筒形轴承相对偏心率k与负荷系数s的关系
轴承的负荷系数又称沙马菲尔特数,其值与轴承结构、转速、润滑油粘度以及轴瓦间隙等因素有关,可由下式决定:
s=
=
(6-2)
式中p----轴承载荷;
----轴瓦相对间隙,
=
;
p----轴瓦比压,p=
;
D、L----轴瓦直径、长度
d----轴颈直径;
ω----轴颈角速度,ω=
n----轴颈每分钟转速;
----润滑油动力粘度,
;
γ----润滑油运动粘度;
ρ----润滑油密度。
增加轴瓦压比P可以增加油膜稳定性,这是由于压比加大后可以增加相对偏心率k。
具体做法是:
缩短轴瓦长度以减小轴瓦长径比β
这样不仅可以增加压比,而且增加轴瓦两端泄油的影响,使油膜减薄,使相对偏心率k增大;调整轴瓦中心的标高以改变轴承间载荷的分配,增加产生油膜振荡的轴承的压比,使k值增加。
增加轴瓦压比应考虑运行中轴瓦金属温度及原设计时轴瓦的压比,压比控制在p=0.8~2.OMPa较合适。
增加轴瓦压比方法目前使用得最广泛。
2、降低润滑油粘度
润滑油粘度越大,轴颈旋转时带人油楔的油量越多,油膜增厚,相对偏心率k减小,油膜稳定性降低,易产生油膜振荡。
因此,在运行机组上可适当提高油温使油粘度降低或直接更换粘度小的透平油以提高油膜稳定性的。
3、调整轴承间隙
调整轴承间隙主要针对圆筒形和椭圆形轴承而言,尽管目前尚无一致看法,但通过不少实践,一般认为减少轴瓦顶部间隙,可以增加轴颈油膜的阻尼,产生(圆筒形轴瓦)和增加(椭圆形轴瓦)向下的油膜作用力,相当于增加轴承载荷,从而增加了相对偏心率k,提高油膜稳定性。
如果同时加大轴瓦两侧间隙,其效果将更明显。
4、采用可倾瓦轴承
可倾瓦轴承在理论上是不会产生油膜振荡的。
以往认为三油楔轴承比圆筒形轴承、椭圆形轴承有更大阻尼力,但实际运行过程中并不理想,在国产N125、N200、N300型汽轮机组轴承上油膜振荡时有发生。
从引进机组看,对容易产生油膜振荡的支持轴承(高、中压转子的轴承、载荷较轻的轴承)普遍采用了可倾瓦轴承。
例如从西屋公司引进技术生产的300MW汽轮机(高、中压合缸加一只低压缸),高中压转子前后轴承,低压转子前轴承下部为可倾瓦,上部为圆筒形轴瓦;又如从西屋公司引进技术生产的600MW汽轮机(高、中压缸各一只,低压缸两只),每个缸有两只轴承,其中高、中压转子四个轴承均采用可倾瓦轴承,低压转子(两根)四只轴承均采用椭圆轴承;浙江省北仑港发电厂600MW一号机(日本东芝公司生产),也为四缸(高、中压缸及低压缸两只),共八个轴承,前面五只轴承均采用可倾瓦轴承,后面三只轴承均采用椭圆轴承。
为防止出现油膜振荡,支持高、中压转子的轴承(载荷较轻的轴承)均采用可倾瓦轴承,这是目前世界上较一致的措施,而支持低压转子的轴承(载荷较大的轴承)均采用椭圆轴承。
上海石洞口第二电厂由ABB公司生产的600MW超临界汽轮机采用的是袋式轴承(相当于椭圆轴承),该机组基本上属于二转子三轴承结构,轴承载荷较大,所以采用椭圆(袋式)轴承。
当新机或大修后的机组投运发生油膜振荡,则应首先检查转子中心、润滑油温、轴瓦间隙及紧力等是否在要求范围内,然后再采取相应措施予以消除油膜振荡。
应当指出,除采取上述防止和消除油膜振荡的措施外,还应尽量做好转子的动、静平衡,以充分降低在临界转速下的共振放大能力。
这样,即使发生油膜振荡,其共振振幅也可以受到约束。
第三节轴承的结构
汽轮机轴承可分两大类:
一类是承担转子重量及不平衡重量产生的离心力和确定转子在汽缸内径向位置的支持轴承或称径向轴承、主轴承;另一类是确定转子在汽缸中轴向位置和承受转子轴向推力的推力轴承。
支持轴承中有圆筒形轴承、椭圆轴承、袋式轴承、多油楔轴承、可倾瓦轴承和组合轴承(下部为可倾瓦,上部为圆筒形)等;推力轴承中有单一的止推轴承和支持及止推联合在一起的轴承。
现对具体结构分别介绍。
一、支持轴承
1、圆筒形轴承
圆筒形支持轴承按支持方式可分为固定式和自位式(球面式)两种。
当转子中心变化引起轴颈倾斜时,自位式圆筒形支持轴承的轴瓦随之转动,能自动调位,使轴颈与轴瓦间的间隙沿整个轴瓦长度保持不变。
轴瓦球面与球面座之间的球形配合面既要求在运行中能保证滑动,又要求不可出现松位而引起振动。
以往球形配合面均采用过盈配合,而现在采用过渡甚至滑动配合,其原因是运行中轴瓦温度高于球面座温度,考虑了热膨胀量后因此将球面配合放松,这是有道理的,实际运行中也证明了这点。
图6-10为固定式圆筒形轴承,它用在国产50MW、10OMW等汽轮机上,轴瓦1是由上、下两半组成,并用螺栓8和止口连接成一整体。
下轴瓦支持在三个用碳钢制成的垫块2上,垫块2用螺钉与轴瓦固定在一起,垫块与轴瓦之间有垫片3,采用增减垫片厚度来调整轴瓦中心的位置,上瓦顶部的垫块2和垫片3可用来调整轴瓦与轴承盖之间的紧力。
图6-10固定式圆筒形支持轴承
1-轴瓦;2-调整垫块;3-垫片;4-节流孔板;5-油档;
6-进油口;7-锁饼;8-连接螺栓
润滑油从轴瓦水平面下方15度垫块2进油孔进人,节流孔板4可调节进油量。
由于轴旋转,油进人后先经轴瓦顶部间隙,再经轴颈和下瓦之间的间隙,然后从轴瓦两端泄出,由轴承座油腔返回油箱。
水平结合面上的锁饼7用来防止轴瓦随轴颈一起转动。
轴承座在汽轮机一侧装有油档5,以防止油从轴承座中甩出。
瓦背一般用HTZO-40铸造(为改善轴承合金与瓦背的粘结牢固也有用碳钢材料的,在瓦背内孔先车出燕(鸽)尾槽、搪锡后,浇铸一层巴氏合金,汽轮机轴瓦的巴氏合金采用锡基合金(ChSnSbll-6),其成分为含Sb10%-12%、Cu5.5%~6.5%,其余为锡。
这种合金质软、熔点低,具有良好的耐磨性能,万一油膜破坏,以致巴氏合金与轴颈直接磨擦时,巴氏合金先行烧熔而保护轴颈不被磨坏。
自位轴承又称球面支持轴承,它用在31-25-7型等汽轮机上,其结构与固定式支持轴承基本相同,只是轴承体外形为球面,当转子轴颈倾斜时,轴瓦可随之转动,自动调位,保持沿轴颈长度方向与轴瓦的间隙不变,但这种轴承的球面配合加工和调整较麻烦。
圆筒形支持轴承一般应用在容量不很大的机组上。
静止状态下,其轴瓦顶部间隙为轴颈直径的1.5/1000~2/1000,轴瓦两侧间隙为顶部间隙的1/2。
如31-25-7型汽轮机Ф260后轴承为圆筒形支持轴承,其顶部间隙为0.39~0.52mm,侧边间隙为0.195~0.26mm。
2.椭圆形支持轴承
椭圆形支持轴承的结构与圆筒形支持轴承结构基本相同,只是将轴瓦顶部间隙缩小为轴颈的1/1000~1.5/1000,每边侧边间隙放大为顶部间隙的两倍。
例如51-50-3型汽轮机2号轴承,其轴颈为Ф325,轴瓦顶部间隙a=0.30~0.45mm,两侧间隙b=0.60~0.70mm。
椭圆轴承在运行中轴瓦顶部和下部都形成了油楔,所以椭圆轴承实际上也是双油楔轴承。
由上部油楔产生向下的油压力,压低轴颈中心,增加相对偏心率,因此比圆筒形轴承的油膜稳定性好。
这种轴承的比压一般可达1.2~2MPa,甚至可达2.5MPa。
椭圆轴承在各种容量的低压转子上普遍采用。
图6-11椭圆形支持轴瓦示意图
3、三油楔支持轴承
国产大容量机组中常采用三油楔支持轴承。
图6-12为国产N125型、N300型等汽轮机所采用的不对称三油楔支持轴承的轴瓦。
三油楔支持轴承的轴瓦有三个长度不等的油楔,上瓦有两个油楔,下瓦有一个油楔,它们所对应的角度分别为θ1=105º~110º,θ2=θ3=55º~58º。
设计中为了使油楔分布合理,上、下瓦结合面M-M不放在水平位置上(现为检修方便有的已改为放置在水平位置),与水平面倾斜一个角度Ф,一般Ф为35º,并用销子锁牢。
轴颈旋转时,三个油楔都建立起油膜,油膜力作用在轴颈的三个方向,如图6-12中的F1、F2、F3。
下部大油楔产生的油压力F1,起承受轴颈上载荷的作用,上部两个小油楔产生的压力F2、F3使轴运转平稳,由于三个油楔的力相互作用,使轴承抗振性提高。
轴承中除固定油楔面及排油沟外,都是光滑连续的圆柱面。
固定油楔两端的窄面称为阻油边,使固定油楔不与外界直接相通,以减少轴端泄油,增加承载能力。
图6-12三油楔轴瓦
(a)示意图;(b)油楔压力分布图;(c)结构图
1-调整垫片;2-节流孔Ф35;3-带孔调整垫铁;4-轴瓦体,
5-内六角螺钉;6-止动垫圈;7-高压油顶轴进油
轴承进油口与水平面成20º角,油从进油口进人环形槽内,然后分别经过三个油楔的进油口进人固定油楔。
在轴瓦下部工作面上开高压油顶轴油枕及进油孔。
三油楔轴承加工制造和安装、检修比较复杂。
有些三油楔轴承(N125型汽轮机)在完善化改进中,已改为椭圆形轴承。
从几台国产机组的三油楔支持轴承油膜振荡现象发生来看,其承载能力、稳定性并不十分理想。
4.可倾瓦轴承
随着汽轮发电机组单机容量的不断增大,轴系临界转速下降,将直接影响到轴承工作的稳定性。
为此,寻求更为稳定的轴承结构就显得十分迫切,国内、外已普遍采用一种较新型的轴承―可倾瓦支持轴承。
可倾瓦轴承又称活支多瓦轴承,它通常有3~5块或更多块能在支点上自由倾斜的弧形瓦块组成,其原理图如图6-13所示。
瓦块在工作时可以随着转速、载荷及轴承油温(油粘度