运载火箭箭体结构制造技术发展与应用.docx
《运载火箭箭体结构制造技术发展与应用.docx》由会员分享,可在线阅读,更多相关《运载火箭箭体结构制造技术发展与应用.docx(19页珍藏版)》请在冰豆网上搜索。
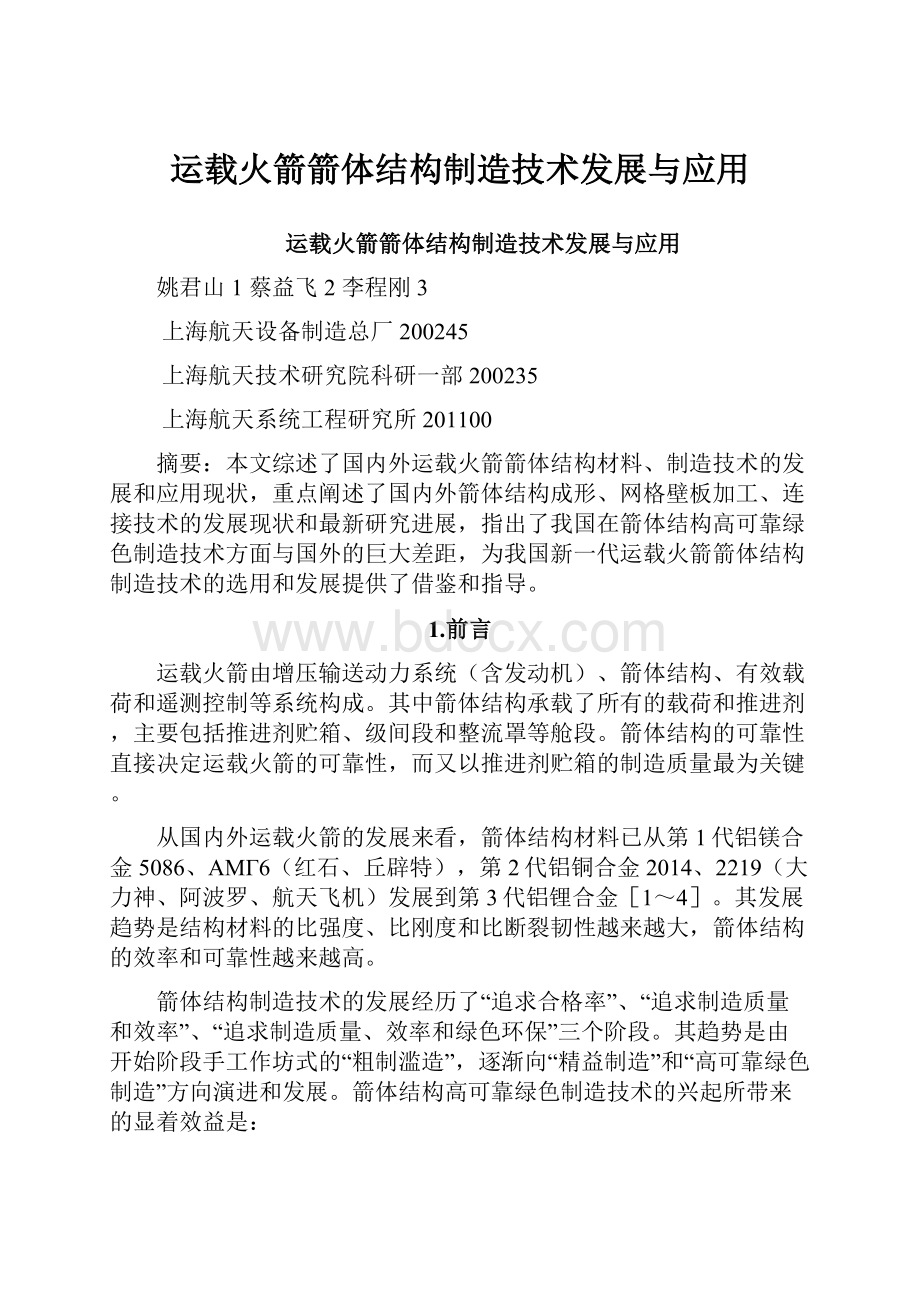
运载火箭箭体结构制造技术发展与应用
运载火箭箭体结构制造技术发展与应用
姚君山1蔡益飞2李程刚3
上海航天设备制造总厂200245
上海航天技术研究院科研一部200235
上海航天系统工程研究所201100
摘要:
本文综述了国内外运载火箭箭体结构材料、制造技术的发展和应用现状,重点阐述了国内外箭体结构成形、网格壁板加工、连接技术的发展现状和最新研究进展,指出了我国在箭体结构高可靠绿色制造技术方面与国外的巨大差距,为我国新一代运载火箭箭体结构制造技术的选用和发展提供了借鉴和指导。
1.前言
运载火箭由增压输送动力系统(含发动机)、箭体结构、有效载荷和遥测控制等系统构成。
其中箭体结构承载了所有的载荷和推进剂,主要包括推进剂贮箱、级间段和整流罩等舱段。
箭体结构的可靠性直接决定运载火箭的可靠性,而又以推进剂贮箱的制造质量最为关键。
从国内外运载火箭的发展来看,箭体结构材料已从第1代铝镁合金5086、AMГ6(红石、丘辟特),第2代铝铜合金2014、2219(大力神、阿波罗、航天飞机)发展到第3代铝锂合金[1~4]。
其发展趋势是结构材料的比强度、比刚度和比断裂韧性越来越大,箭体结构的效率和可靠性越来越高。
箭体结构制造技术的发展经历了“追求合格率”、“追求制造质量和效率”、“追求制造质量、效率和绿色环保”三个阶段。
其趋势是由开始阶段手工作坊式的“粗制滥造”,逐渐向“精益制造”和“高可靠绿色制造”方向演进和发展。
箭体结构高可靠绿色制造技术的兴起所带来的显着效益是:
1、箭体结构(尤其是推进剂贮箱)的结构可靠性得到阶跃式提高;
2、制造过程显着降低能耗、“三废”排放大幅降低甚至零排放,对人体健康的危害大幅降低或消失;
3、箭体结构实现优质高效的精益制造和“保形”制造。
其中,高速数控铣削+等距压弯净成形、双向拉伸近净成形、整体旋压+后热处理、数控搅拌摩擦焊和搅拌摩擦点焊等技术是最具代表性和最有发展前景的箭体结构高可靠绿色制造技术。
2.箭体结构和相关制造技术
如图1所示,箭体结构主要由推进剂贮箱、整流罩、级间舱段、增压管路等组件构成。
其中,助推器又分为液体助推器和固体助推器,而以液体助推器的应用最为广泛。
本文所提及的推进剂贮箱均指液体推进剂贮箱,所牵涉的制造技术有钣金成形、铣削加工、焊接、铆接、复合材料(含低温贮箱绝热层)施工等。
推进剂贮箱是箭体结构中最大的结构部件,作为压力容器用来贮存液氢/液氧或液氧/煤油推进剂,同时作为运载器的主承力结构,起着支撑热防护系统(即绝热防护层)以及为其它系统仪器设备提供安装基础和空间的作用。
由于推进剂贮箱属于铝合金压力容器,抗断裂性能和气密性是其关键性能,主要采用钣金成形、铣削加工和焊接等制造技术生产。
整流罩、级间舱段等其它组件大多属于铝合金或“铝合金+复合材料”铆接构件,其功能为有效载荷、仪器设备提供安装空间,主要采用钣金成形、铆接等技术生产。
对于采用低温推进剂(如液氧/煤油、液氧/液氢等推进剂)的运载火箭,其贮箱属于低温推进剂贮箱,除了要求具备优异的低温抗断性能和气密性能外,还必须具备良好的深冷绝热性能,为此还需要进行绝热包敷层施工。
绝热包敷层一般由低温缓冲层、绝热层和密封防护层构成,如图2所示。
其涉及的制造技术有聚氨酯/或聚氯乙烯发泡工艺、低温缓冲层和防护层施工工艺等。
3.箭体结构制造技术的发展与应用
3.1推进剂贮箱成形技术
如图3所示,常温推进剂贮箱结构主要由箱底、筒段、γ型材框、前后短壳和输送管路等构成。
其结构件的制造均离不开成形技术,如箱底瓜瓣和顶盖成形技术、箱底整体旋压成形技术、γ型材框拉弯成形技术和筒段成形技术等。
由于国内外宇航工业发展水平不一,各类成形技术的发展和应用水平也参差不齐。
3.1.1箱底成形技术
箱底的制造分为“零件拼接”和“整体旋压成形+热处理”两类。
在运载火箭发展初期,由于铝合金材料质量和旋压技术发展水平的限制,贮箱箱底的制造均采用零件拼焊(见图3)。
箱底拼焊的零件有瓜瓣、顶盖、γ型材框和法兰等。
法兰主要采用锻件机加工而成。
顶盖的成形采用带有压边圈的拉伸成形工艺。
退火状态的板材在阳模上拉伸成带一定曲率半径的成形件后再热处理成使用状态。
由于顶盖零件形状简单,带压边圈拉伸成形工艺能够完全满足顶盖零件的成形精度要求。
γ型材框的制造采用型材拉弯机成形,然后用焊接对接成为框环。
型材拉弯机是一种基于计算机控制的液压拉弯机,具有成形精度可控,生产效率高等优点。
瓜瓣的成形目前在生产中存在三种弯曲成形工艺:
压力机压弯成形、蒙皮拉形单向拉伸成形和压力机双向拉伸成形。
上述三种箱底瓜瓣成形工艺中以压力机双向拉伸成形工艺的成形精度最高、回弹量最小。
20世纪70年代初,随着大尺寸、大厚度铝合金板材质量的稳定和旋压技术发展的成熟,箱底整体旋压成形+后热处理技术得到迅速发展和应用,箱底结构的制造工艺大大简化、可靠性显着提高。
整体旋压成形的箱底如图4所示。
旋压成形是一种冷成形方法,板材在旋压滚轮剪切力碾压作用下,形成对称几何形状,受碾压的材料厚度变薄。
箱底成形过程一般经历两个阶段即凸模半成品成形和凹模半成品成形,并辅以适当的机加工和后续的热处理即可完成箱底的成形制造。
旋压成形的优点是实现板材等厚度近净成形,成形过程中可控制材料厚度变化,公差小,可重复加工和加工成本低。
其缺点是存在残余弯曲应力,需要通过中间或最终热处理消除。
俄罗斯曾开发出半球形箱底爆炸成形的工艺,并为美国DC-XA航天器贮箱成形了直径2.4m的1460铝锂合金半球形顶箱底。
爆炸成形的优点是工装简单、成本低、回弹小、无需焊接和对称性好。
其缺点是属于特殊工艺,应用难以普及,需要抽真空,成形尺寸受模具尺寸和材料的限制。
应用情况:
美国航天飞机外贮箱、欧盟Ariane5火箭贮箱、俄罗斯火箭贮箱和中国长征系列火箭贮箱箱底的瓜瓣零件成形均大量采用了基于水压机的双向拉伸成形工艺。
对于直径5m以下的火箭,如美国的Atlas系列和Delta系列、日本的H-2B火箭等,其贮箱箱底均采用“整体旋压成形+热处理”工艺制造。
俄罗斯开发的半球形箱底爆炸成形工艺部分用于本国火箭箱底的成形制造。
与国外相比,我国在箱底整体旋压成形技术方面的差距较大。
3.1.2筒段成形技术
贮箱筒段制造工艺分为两类:
1)滚弯成形+化学铣削+焊接;2)高速数控铣削+等距压弯成形+焊接。
因此,筒段的成形技术有滚弯成形和等距压弯成形两种。
滚弯成形采用三轴辊轧机进行成形,工艺简单,但成形精度较差。
等距压弯成形的实质是多次压弯累积成形,具有成形精度高、回弹量小等特点,是一种净成形工艺(图5)。
随着航天制造技术向高可靠、高效、绿色、环保方向发展,国外宇航企业大量采用“高速数控铣削+等距压弯成形+搅拌摩擦焊”这一组合制造工艺来实现贮箱筒段的优质、高效、绿色制造。
应用情况:
我国长征系列火箭贮箱筒段的制造广泛采用“滚弯成形+化学铣削+TIG熔焊”组合制造工艺,制造精度差、产生“三废”、损害人体健康和污染环境等问题日益突出,亟需通过制造技术的升级换代来解决。
美国、欧盟、日本和俄罗斯等国火箭贮箱筒段的制造均采用优质、高效、绿色环保的“高速数控铣削+等距压弯成形+搅拌摩擦焊/熔焊”组合工艺,不仅提高了筒段的制造质量和制造精度,而且最大限度地减少了对环境的破坏,值得我国航天制造企业借鉴和学习。
3.2推进剂贮箱焊接技术
3.2.1贮箱结构焊缝分类
如图3和图6所示,推进剂贮箱的结构焊缝按照空间分布和结构特点,主要分为以下几类:
1)纵缝:
筒段纵缝、瓜瓣纵缝和γ型材框纵缝;
2)环缝:
筒段对接环缝、箱底Φ1380环缝、箱底顶盖环缝、圆环-γ型材框环缝、筒段-γ型材框环缝、法兰环缝、前/后短壳-γ型材锁底环焊缝;
3)其它焊缝:
点焊缝、角焊缝等。
本文重点讨论推进剂贮箱纵缝(γ型材框纵缝除外)和环缝(法兰焊缝除外)焊接技术的发展和应用现状。
3.2.2贮箱结构材料及其焊接工艺的发展
如图7所示,自运载火箭诞生以来,国外推进剂贮箱的结构材料已从第1代铝镁合金(5086和AMГ6),第2代铝铜合金(2014和2219)发展到第3代铝锂合金(1460和2195)。
其发展趋势是材料的强度越来越高、比重越来越轻,而其熔焊焊接性呈明显的下降趋势。
贮箱的焊接工艺,也由最初的钨极氩弧焊、逐渐发展到电子束焊、变极性等离子弧焊和现在的搅拌摩擦焊。
我国运载火箭推进剂贮箱的结构材料由开始的5A06铝镁合金发展到2A14、2219铝铜合金,其中2A14铝合金作为贮箱结构材料使用至今,而2219铝铜合金则被确定为我国新一代运载火箭贮箱的结构材料。
由图8可知,随着贮箱结构材料的更新换代,其焊接工艺也获得了长足的发展,但贮箱材料熔焊接头的强度系数呈明显下降趋势,而搅拌摩擦焊接头的强度系数下降并不明显,说明搅拌摩擦焊方法不仅具有广泛的材料适用性,而且其接头强度最高,是推进剂贮箱结构材料理想的焊接工艺。
3.2.3搅拌摩擦焊工艺
搅拌摩擦焊是铝合金焊接技术的一次重大创新。
它是一种基于微区锻造(如图9所示)的绿色固态焊接工艺,其工艺特点是:
非填丝固相自动焊接,接头力学性能优异、单面一次焊透、低应力、近无变形,工艺简单、可靠、无弧光,尤其适于高强、熔焊难于焊接铝合金的焊接。
试验研究表明,各类铝合金搅拌擦焊接头的质量和综合力学性能均大大优于其TIG焊接头。
搅拌摩擦焊技术的核心是搅拌头的设计制造和结构选材。
搅拌头按照工装支撑方式分为单轴肩搅拌头和双轴肩搅拌头。
单轴肩搅拌头是最常见的搅拌头,焊接时需要背部的刚性垫板支撑。
如图10所示,双轴肩搅拌头是为了解决背部无法刚性支撑的焊缝进行搅拌摩擦焊而开发出来的。
顾名思义,双轴肩搅拌头具有上下两个轴肩焊接过程中起到相互支撑的作用,可是实现贮箱环缝的悬空搅拌摩擦焊,完全消除了单轴肩搅拌摩擦焊可能产生的背部未焊透等缺陷。
搅拌摩擦焊是一种机床焊接工艺,易与数控机床技术集成,能够实现铝合金构件复杂曲线焊缝(箱底焊缝、筒段环焊缝等)的优质高效焊接。
因此,从工艺特性来看,数控搅拌摩擦焊非常适于推进剂贮箱纵缝和箱底复杂焊缝的高可靠、近无缺陷焊接。
应用情况:
目前搅拌摩擦焊技术已广泛应用于美国Delta系列、Atlas系列火箭贮箱、航天飞机外贮箱纵缝的高质量焊接。
在日本,三菱重工已经开发出成熟的基于双轴肩搅拌头的数控搅拌摩擦焊工艺,并将其应用于新型运载火箭H-2B贮箱的筒段纵缝和对接环缝的高可靠、高效、无缺陷焊接(图11)。
按照进度计划,日本首枚H-2B火箭将于2008年发射升空。
在国内,随着新一代运载火箭的正式立项研制,搅拌摩擦焊作为推进剂贮箱的一项关键制造工艺,正在深入进行工程化应用研究,搅拌头、焊接装备和工装夹具等关键技术均获得突破(图12),目前正在进行接头质量分级评定标准的制定工作,不久将建立起我国航天工业自己的搅拌摩擦焊技术体系。
3.2.4变极性等离子焊接工艺
如图13所示,铝合金变极性等离子(VPPA)穿孔立焊技术集成了变极性电源和等离子弧穿孔效应两项技术特性,完美解决了铝合金表面氧化膜的阴极清理和钨极烧损两者的矛盾—既满足交流焊铝所需的阴极清理作用,又能将钨极的烧损降低到最低。
得益于穿孔焊接和等离子弧能量集中、一次穿透焊接等特点,变极性等离子穿孔立焊尤其适于中厚度(3~16mm)铝合金焊缝的优质高效自动焊接。
20世纪80年代,变极性等离子穿孔立焊工艺曾被美国NASA誉为铝合金“无缺陷”焊接工艺。
由于在工艺上采用向上立焊的焊接方式,所以焊缝熔池金属的结晶不同于其它熔焊方法。
小孔周围的液体金属在电弧力、表面张力、重力和浮力等多种力的共同作用下保持平衡,形成一定形状和尺寸的熔池。
熔化金属被排挤在小孔周围,随着焊接的进行,熔化金属沿电弧周围熔池壁向下、向背面流动结晶成形。
由于强烈的穿孔冲刷效应和复杂的熔池金属流动行为有效消除了气孔和固体杂质。
变极性等离子焊接工艺突出的特点是:
有效消除铝合金熔焊气孔和固态杂质,单面焊双面自由成形,焊缝成形美观,深宽比大,最适于焊接3~16mm厚的铝合金对接焊缝;接头采用I形平头对接,无需开坡口,简化焊前准备,工装简单,焊接过程稳定、效率高,具有较大的工艺柔性。
研究和焊接实践均已证明,变极性等离子穿孔立焊工艺是2219铝合金熔焊首选的焊接工艺。
结合其高能束焊、工装简单和工艺柔性好的特点,变极性等离子焊工艺非常适于贮箱筒段环缝的“无缺陷”焊接。
应用情况:
1985~至今,变极性等离子穿孔立焊工艺已广泛应用于美国航天飞机外贮箱(图14)、运载火箭(如大力神、Delta和Atlas等系列)推进剂贮箱(图15)的焊接生产[5、6]。
例如美国航天飞机外贮箱的纵缝、环缝和箱底焊缝均采用了基于计算机控制的变极性等离子穿孔立焊工艺,其焊接工作量一度达到85%以上。
20世纪90年代随着搅拌摩擦焊技术的出现,航天飞机外贮箱和运载火箭贮箱的纵缝均采用搅拌摩擦焊工艺替代了原来的变极性等离子穿孔立焊工艺,但纵缝以外的焊缝(如环缝、箱底焊缝等)仍采用工艺柔性好的变极性等离子穿孔立焊工艺。
受限于抗干扰计算机控制、变极性电源和等离子焊枪等诸多技术发展水平和国外禁止出口的限制,我国在变极性等离子穿孔立焊电源、高精度等离子焊枪和多参数实时闭环检测控制等方面尚未发展成熟,造成该工艺至今尚未应用于我国现役运载型号贮箱的生产制造。
但随着我国新型号运载火箭的立项研制,变极性等离子穿孔立焊工艺作为箭体结构的关键制造工艺之一,必将得到广泛的应用。
3.2.5TIG类熔焊工艺
用于推进剂贮箱焊接的TIG类熔焊工艺有直流正接氦弧焊、交流脉冲氩弧焊、方波交流TIG焊和变极性TIG焊等。
其中变极性TIG焊接电源和变极性等离子焊接电源类似均属于新型的变极性电源,其它三种TIG焊工艺均使用脉冲波形调制交直流两用焊接电源。
直流正接氦弧焊使用氦气作为保护气,钨极为负极,没有阴极雾化去除氧化膜的作用,依靠氦气氛电弧的短弧(≤0.5mm)高能、高速等离子流冲击破碎氧化膜,因此氦弧焊适于不加丝短弧自动焊。
由于氦弧热量集中、挺度大、较氩弧集中和短弧施焊等特点,特别适于多层焊的打底焊,背面可以充分熔透成形。
方波交流TIG焊和交流脉冲TIG焊原理相似,均是通过电流波形调制获得相应的电流波形,其主要区别在于脉冲频率和电流波形。
这两种焊接工艺既适于自动焊,也适于手工焊。
由于正半波和负半波的波形相同,用于产品的焊接易出现热输入大、钨极烧损和钨夹杂等问题。
变极性TIG焊则是基于变极性焊接电源而发展起来的一种新型TIG焊工艺。
其最大的特点在于正负半波幅值和持续时间均可单独调节,电流波形灵活多样,既提供充分的氧化膜清理作用,又为焊接熔深提供充分的热输入,适于自动焊和手工焊。
应用情况:
上述四种TIG焊工艺已广泛应用于国内外运载火箭推进剂贮箱的焊接生产。
可以说,自运载火箭诞生以来,TIG焊工艺就一直是箭体结构必不可少的焊接工艺,曾是推进剂贮箱主导焊接工艺之一。
如欧盟Ariane5火箭推进剂贮箱的纵/环缝采用变极性TIG焊工艺(图16),我国和俄罗斯现役火箭的推进剂贮箱主要采用方波交流TIG焊工艺等。
总之,TIG类熔焊工艺作为一种贮箱焊接生产工艺依然是法兰焊缝、角焊缝、锁底焊缝等箭体结构焊缝的主导焊接工艺,也是手工焊/手工补焊的必备焊接工艺。
冷战时期,美国和前苏联为了争夺航天领先地位,各自研制了大型运载火箭,如美国的土星系列火箭和前苏联的能源号火箭。
能源号火箭一级芯级贮箱直径为8m,长54m,贮箱纵缝焊接厚度达40mm,贮箱环缝焊接厚度达20mm,可将100吨的有效载荷送入近地轨道,或将18吨的有效载荷送入地球同步轨道。
由于贮箱焊接厚度在16mm以上,属于中厚度以上对接,为提高贮箱的焊接生产效率,前苏联在贮箱纵缝和环缝上分别使用了局部真空电子束焊和高频脉冲MIG焊工艺。
局部真空电子束焊具有能量密度高、穿透能力强、对称性好、变形小和缺陷少等优点,将其用于能源号火箭贮箱纵缝的焊接可以实现一次穿透、快速焊接。
由于必须解决局部稳定密封、抽真空和接头延伸率低等问题,造成工艺柔性差、局限性较大,因此不具备推广应用价值。
高频脉冲MIG焊是一种中厚板多层焊工艺。
焊接过程中熔化的焊丝作为负极,被焊工件作为正极,采用大电流射流过渡,阴极雾化效果好,但熔深能力较差,焊缝质量不及TIG焊,且高频弧光射线强烈,对操作人员的健康危害较大,因此该焊接工艺在贮箱生产上已基本被弃用。
为了焊接大尺寸变厚度的γ型材框,前苏联开发了一种优质高效的焊接工艺—闪光对焊。
其工作原理是:
将被焊对接面两边分别夹住、相对压紧,然后通电加压,电流密度可达12~20A/mm2,数秒钟内对接面氧化膜破碎、金属熔化,氧化膜、夹渣和部分熔化物均被挤出,形成牢固的焊接接头,随后把接头飞边切除即可。
闪光对焊过程的工艺参数可全部采用微机自动控制。
该工艺的缺点是耗电量巨大、闪光对焊噪声如雷,操作人员均需要配带有效保护装置。
在航天制造领域,仅有前苏联使用过该工艺。
应用情况:
局部真空电子束焊、高频脉冲MIG焊和闪光对焊均是前苏联针对其大厚度火箭贮箱焊缝而开发的焊接工艺。
因而在前苏联能源号系列火箭的生产上得到广泛应用。
20世纪60~70年代,美国在研制土星系列火箭时,为解决大厚度贮箱上大厚度焊缝(如法兰焊缝、γ型材框对接焊缝等)的焊接问题也曾大量使用局部真空电子束焊工艺。
3.3箭体结构铆接技术
铆接是整流罩、级间段、仪器舱和尾翼等箭体结构零件的主导制造工艺。
这类铆接零件大多由硬铝或超硬铝框环、桁条构成,手工钻铆是最通用的铆接工艺。
手工钻铆工艺的缺点主要有:
铆接位置精度差、噪音和后坐力大、劳动强度高,各工序均通过人工完成,不符合21世纪高效绿色生产的要求。
鉴于箭体结构中铆接构件均为一次性使用构件,最适于采用铆接精度高、无噪音污染、生产效率高、操作简单可靠、低成本的钻铆技术。
为满足箭体结构铆接构件在结构可靠性、几何气动外形和承载应力水平等方面的严格要求,需要使用干涉配合铆接工艺,但传统的手工铆接工艺很难实现沿整个钉杆都有干涉,限制了干涉配合连接的广泛应用。
同时,箭体结构的铆接构件大多属于封闭/半封闭的结构件,无法大量应用自动压铆技术,只能采用手工钻铆,但工人对铆接噪声、后坐力等难以忍受,已成为影响生产的一个瓶颈问题。
20世纪90年代,新型的低压电磁铆接(亦称应力波)技术被开发出来,既保证了优异的干涉配合铆接效果,又大幅降低了手工铆接的劳动强度、噪声和后坐力,成为最具发展和应用前景的铆接新技术。
低压电磁铆接技术的突出特色为:
电磁铆接产生的干涉量均匀,质量稳定,铆接噪声小。
如美国Electroimpact公司开发的一种11kg的钻铆两用电磁铆枪铆接4.7mm的普通铝铆钉时后坐力为35kg,绝对噪声不超过90分贝。
此外,电磁铆接一次完成铆钉的成形,噪声的持续时间短,对人的影响远小于锤铆。
按等效连续噪声计算,电磁铆枪的噪声约为10分贝,远低于先进风动工具的35分贝等效连续噪声。
在美国,电磁铆接属于低噪声铆接工艺,不需要劳动保护。
应用情况:
在美国、欧盟和俄罗斯等国家,箭体结构的普通铆接技术(手工钻铆、锤铆和液压自动钻铆等)已被新兴的低压电磁铆接技术所替代。
在我国,由于低压电磁铆接技术发展尚未成熟,落后的手工钻铆工艺依然是长征系列火箭箭体结构铆接构件的主导制造工艺,有待于铆接技术的升级换代,缩短与国外的差距,提高箭体结构铆接构件的可靠性和几何制造精度,实现高效绿色生产。
4.箭体结构制造技术发展趋势
近年来,随着国内外多种新型号运载火箭的立项研制,进一步带动了箭体结构制造技术发展和提高,出现了多种引人注目发展动向。
简述如下:
4.1推进剂贮箱箱底高可靠制造工艺
在贮箱箱底的优质高效制造技术研究方面,最新的进展主要体现两个方面:
其一是,2004~2006年,日本三菱重工为实现H-2B火箭贮箱箱底的高可靠制造,自主开发成功箱底“整体旋压成形+后热处理”技术,成为世界上第三家掌握这一制造技术的国家。
这主要得益于日本发达的冶金、机电等工业基础。
其二是,对于采用拼焊生产的箱底,将拼焊工艺改进为数控搅拌摩擦焊,实现箱底的低应力、近无变形和高效制造,能够显着提高箱底的结构可靠性。
箱底焊缝虽然复杂,但对于数控搅拌摩擦焊工艺而言非常简单,焊接过程稳定可控,焊接质量稳定一致,是实现箱底高可靠绿色制造的另一有效技术途径。
2007年5月,上海航天技术研究院在国内率先实现了新一代运载火箭Φ3350贮箱箱底复杂焊缝的搅拌摩擦焊(图17),为实现箱底的全搅拌摩擦焊提供了可靠的技术支撑[7、8]。
4.2贮箱筒段制造工艺
筒段网格壁板制造技术分为网格壁板加工和成形两类工艺。
过去主要采用“滚弯成形+化学铣削”组合工艺进行生产,现在则主要采用“高速数控铣+等距压弯净成形”组合工艺进行绿色高效生产。
但我国在筒段网格壁板制造方面依然采用危害环境、制造精度差的落后工艺。
筒段网格壁板采用“高速数控铣+等距压弯净成形”组合工艺是实现其高效绿色制造必由之路。
贮箱筒段制造技术的另一个突破是筒段环缝实现无需背部垫板支撑的搅拌摩擦焊。
日本三菱重工率先在H-2B火箭贮箱环缝上实现了搅拌摩擦焊(图18)。
贮箱环缝实现搅拌摩擦焊需要突破三项关键技术:
1)双轴肩自支撑搅拌头;2)环缝匙孔等强补焊技术;3)环缝接头同心对中装夹工装。
在国内,上海航天技术研究院正在进行贮箱环缝的搅拌摩擦焊研究工作,相信不久我国就能够突破上述关键技术,自主掌握这一先进焊接工艺。
4.3铆接构件制造工艺
在箭体结构铆接构件制造工艺方的最新进展有:
1)低压电磁铆接工艺正加速替代落后手工铆接工艺;2)搅拌摩擦点焊工艺日益受到青睐,部分替代铆钉铆接工艺。
搅拌摩擦点焊的原理为:
搅拌点焊头在搭接(即铆接)位置进行原位摩擦搅拌致金属塑性状态,通过搅拌针和搅拌针套筒间的相互轴向运动将搭接处的塑性金属充分混合并填充回原位,形成可靠的搭接连接。
铝合金搅拌摩擦点焊接头形貌如图19所示。
从搅拌摩擦点焊原理可知,该工艺简单、可靠、效率高,既可用于替代铝合金铆接接头,又可进一步推广应用于搅拌摩擦焊匙孔等缺陷的等强补焊,是一种应用前景广阔的新型绿色点焊技术。
5.结束语
综上所述,“精益制造”和“高可靠绿色制造”是箭体结构制造技术的终极发展方向。
这也是人类追求与自然和谐、科学协调发展的时代要求,也是21世纪先进制造技术最鲜明的发展特色。
从以上论述可知,美国、欧盟和日本在箭体结构制造技术方面,不断精益求精和升级换代,已完全弃用了对环境污染严重的化学铣削工艺和落后的手工钻铆、压弯成形、方波交流TIG焊等工艺,以搅拌摩擦焊、变极性等离子焊、变极性TIG焊、旋压成形和等距压弯成形等为代表的先进制造工艺得到广泛应用,基本上实现了“精益制造”和“高可靠绿色制造”的目标。
俄罗斯则依靠其独立的科学技术体系,开发出多种独具特色的箭体结构制造技术,但推广应用的局限性较大。
我国则受限于材料工业发展基础薄弱、工艺技术革新缺乏后劲和体制限制等因素,方波交流TIG焊、压/滚弯成形、化学铣削和手工钻铆等落后工艺依然在箭体结构生产中大行其道,其技术水平刚刚发展到“追求制造质量和效率”阶段,与国外相比差距甚大。
以我国新一代运载火箭立项研制为牵引,通过自主创新和集成创新,尽快建立起自主的先进制造技术体系,实现我国箭体结构的高可靠绿色制造已迫在眉睫。
参考文献
1.夏德顺,航天运载器贮箱结构材料工艺研究,导弹与航天运载技术,1999,(3):
32~41.
2.夏德顺.新型轻合金结构材料在航天运载器上的应用于分析(上).导弹与航天运载技术.2000,(4):
18~22.
3.夏德顺.新型轻合金结构材料在航天运载器上的应用于分析(下).导弹与航天运载技术.2000,(5):
5~10.
4.姚君山,周万盛,王国庆等.《航天贮箱结构材料及其焊接技术的发展》.航天制造技术,2002,(5):
17~22.
5.NunesAC,Bayl