Eddy current analysis of midbore and corner cracks in bolt holes.docx
《Eddy current analysis of midbore and corner cracks in bolt holes.docx》由会员分享,可在线阅读,更多相关《Eddy current analysis of midbore and corner cracks in bolt holes.docx(11页珍藏版)》请在冰豆网上搜索。
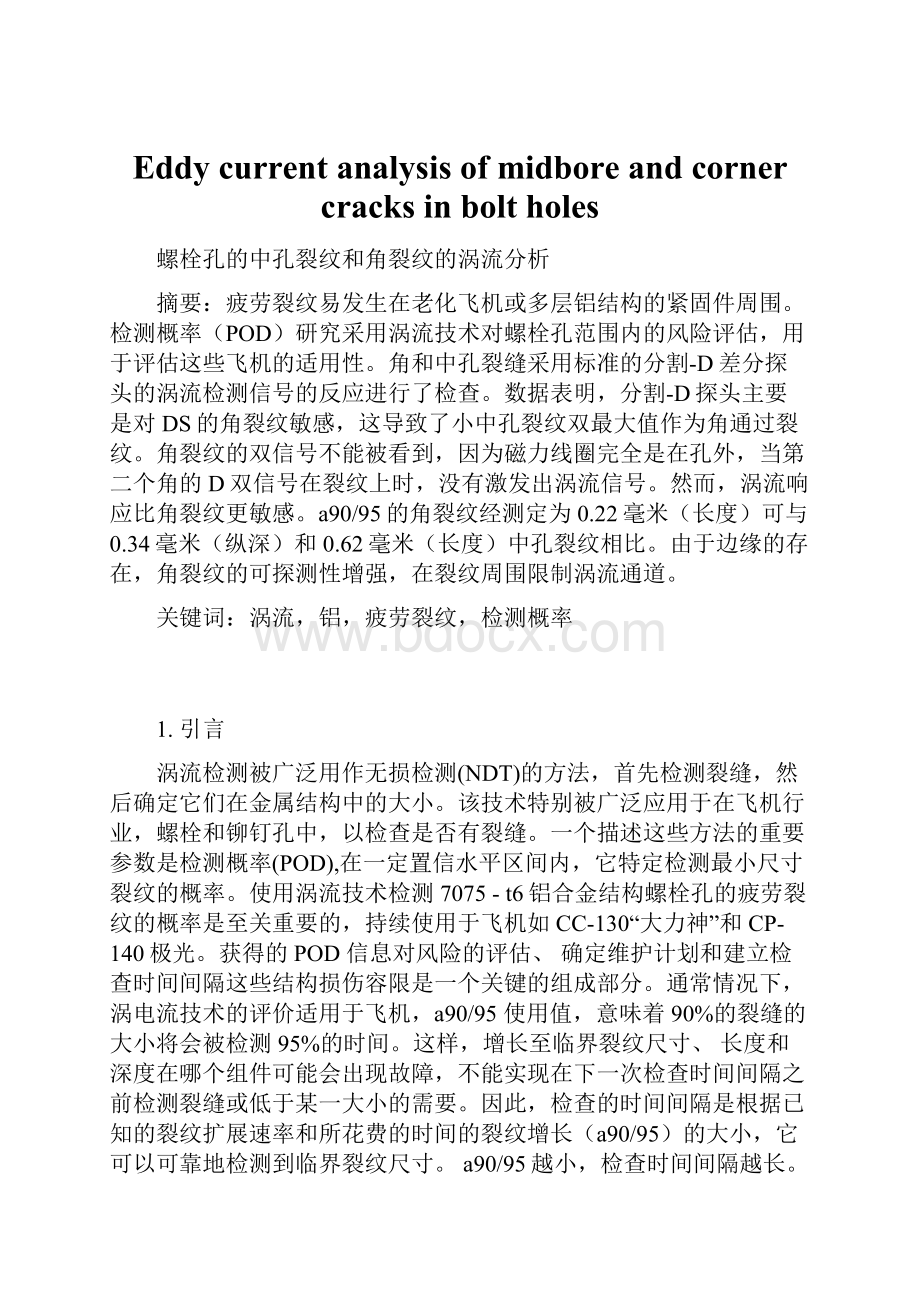
Eddycurrentanalysisofmidboreandcornercracksinboltholes
螺栓孔的中孔裂纹和角裂纹的涡流分析
摘要:
疲劳裂纹易发生在老化飞机或多层铝结构的紧固件周围。
检测概率(POD)研究采用涡流技术对螺栓孔范围内的风险评估,用于评估这些飞机的适用性。
角和中孔裂缝采用标准的分割-D差分探头的涡流检测信号的反应进行了检查。
数据表明,分割-D探头主要是对DS的角裂纹敏感,这导致了小中孔裂纹双最大值作为角通过裂纹。
角裂纹的双信号不能被看到,因为磁力线圈完全是在孔外,当第二个角的D双信号在裂纹上时,没有激发出涡流信号。
然而,涡流响应比角裂纹更敏感。
a90/95的角裂纹经测定为0.22毫米(长度)可与0.34毫米(纵深)和0.62毫米(长度)中孔裂纹相比。
由于边缘的存在,角裂纹的可探测性增强,在裂纹周围限制涡流通道。
关键词:
涡流,铝,疲劳裂纹,检测概率
1.引言
涡流检测被广泛用作无损检测(NDT)的方法,首先检测裂缝,然后确定它们在金属结构中的大小。
该技术特别被广泛应用于在飞机行业,螺栓和铆钉孔中,以检查是否有裂缝。
一个描述这些方法的重要参数是检测概率(POD),在一定置信水平区间内,它特定检测最小尺寸裂纹的概率。
使用涡流技术检测7075-t6铝合金结构螺栓孔的疲劳裂纹的概率是至关重要的,持续使用于飞机如CC-130“大力神”和CP-140极光。
获得的POD信息对风险的评估、确定维护计划和建立检查时间间隔这些结构损伤容限是一个关键的组成部分。
通常情况下,涡电流技术的评价适用于飞机,a90/95使用值,意味着90%的裂缝的大小将会被检测95%的时间。
这样,增长至临界裂纹尺寸、长度和深度在哪个组件可能会出现故障,不能实现在下一次检查时间间隔之前检测裂缝或低于某一大小的需要。
因此,检查的时间间隔是根据已知的裂纹扩展速率和所花费的时间的裂纹增长(a90/95)的大小,它可以可靠地检测到临界裂纹尺寸。
a90/95越小,检查时间间隔越长。
因此,通过提高POD优化检查系统,可以产生显着的经济效益,减少检查的频率。
检测的概率的研究涉及了大量的标本的生成,从中获得足够量的检查数据,以产生精确的POD函数,最近的一个例子是角裂纹的POD使用24套检测器和117的不连续点分割-D螺旋在不锈钢护套用来建立POD螺栓孔的涡流(45电火花缺口和72实验室培养的疲劳裂纹)。
它的设备在最有效的操作条件下进行操作,并了解仪器对两个角和中孔裂纹的响应的是必要的。
尤其是,在顶部或底部的包含角裂纹的板边缘的存在可能会进一步混淆螺栓孔的晶粒。
Bowler和Theodoulidis[3][4]为了进一步阐明这效果,但更复杂的解决方案,特别是微分transmit–receive探针响应在边缘的裂纹适用在这里获得的响应的阻抗探头下板边缘的数值解决方案,尚未制定。
在本文中,涡流数据已从7075-T6铝裂缝中同时使用多个频率获得。
这允许信号在不同的频率下得到有效的检验,频率影响两种不同类型的裂纹的线性度,并允许两个不同裂缝类型的响应的比较。
特别是,它允许在边缘(板的表面角裂纹)的存在下是如何影响物理响应的检测。
这反过来又提供了一种方法来解释螺栓孔的C扫描图像的空间信息。
2.实验
配备一个RA2000旋转螺栓孔扫描仪的奥林巴斯MS5800涡流仪和拆分-D密切接触探头被用来收集在这项工作中报告的涡流数据。
图1示出了探头跟踪轮廓外侧的图像,略呈椭圆形,励磁(传输)线圈和内部差分连接D形接收线圈对,都在同一平面上,并平行于表面的钻孔。
外侧励磁线圈的尺寸也被表示。
所有线圈旋转作为钻孔内的一个单元。
图2说明了在测量过程中探头的方位,并定义了裂纹的长度和深度。
扫描仪以1500RPM的速度旋转。
同时收集在4个频率,200,400,800和1600千赫的数据。
每个频率点的信号被过滤(200赫兹到500赫兹通过)和循环的剥离(lift-off)的组成部分在利萨图中是水平的。
因为这些测量值在800和1600千赫的频率比在较低的频率更敏感,只有在这些频率上的结果在这项工作中[5]的其余部分被报告。
数据可以作一个电压-时间的带状图来呈现,如利萨形式,或为C-扫描。
图1.在这项工作中所用的拆分-D探头的形状和尺寸。
所述励磁线圈外侧略呈椭圆形。
每个D是一种传感器线圈。
传感器线圈相连接,以产生一个差分信号。
图2.在测量过程中的的拆分-D探头定位。
裂纹的长度和深度中定义如插入件中所示。
外线圈内的传送内圈的差分接收。
试样可以用4.3毫米(0.125英寸)或9.5毫米(0.375英寸)厚的铝7075-T6冷轧薄板制作。
孔在24.5毫米宽,147毫米长的试样(1×6in)的中心。
正面和背面砂磨300或600号砂纸,以消除孔的边缘处的任何毛刺。
后将试样放置在液压负载框架下循环采用完全反向的负载(R=-1)。
在设定的周期数的时间后停止负载,电动载物台,用于驱动扫描器上通过试样的螺栓孔,以确定任何裂缝是否已开展。
请注意,没有起动器的槽口,用来发起裂纹增长。
任何疲劳裂纹的产生,可以通常推测与螺栓孔的内表面上尺寸小于20微米小缺陷有关。
这种由点缺陷的起始反映实际式起始裂纹,并再现真实裂纹的纵横比,如果有多个裂纹,不会发生连接。
这与起动器的槽口相反,这可能会引入变量和更大的长度与深度的纵横比[10]。
一旦测量完成,样本的循环恢复。
测量和循环过程可以如期望那样重复。
在某些情况下,试样一旦检测到了裂纹就被停止。
在其他情况下,裂纹继续增长。
当裂纹扩展过程完成后,将试样断裂准确地获得被观察的裂缝的尺寸。
在许多情况下,其他更小的未检测到的裂纹也被发现。
这些裂缝也可以在检测概率研究中使用。
较厚的试样往往有利于中孔裂纹的萌生和扩展。
3.结果
图3和图4显示为一个单一的中孔裂纹和一个单一的角裂纹,分别获得的结果。
中孔裂纹的信号最突出的特点是双峰。
这是由于边角D探头更大的灵敏度,其中由外发送或励磁线圈产生的涡电流密度大于在中间的传感器[9]。
驼峰的最大值之间的距离大约为1.4mm,对应于每个D角之间(参见图1)相同的间距。
因为裂纹是远小于探测传感器,它被检测到两次,一次越过D的的每个角。
两个驼峰之间也有轻微不对称,一个的幅度比其他稍大。
这是由于探头的轻微不对称。
图3.垂直于发射信号在四个频率(沿顶部千赫)的中孔裂纹显示在c扫描图像(被@1600kHz)的右边。
对每个频率的幅值比例已设定,以使填满可用区域。
C扫描图像中的向下箭头显示带状图扫描到左的大致范围。
只有一个物理中孔裂纹的位置的信号被后断裂分析所确定。
图4.垂直于发射信号的信号在四个频率(沿顶部在千赫)的角裂纹显示在c扫描图像(被@1600kHz)到右边。
对每个频率的振幅比例已任意设定,以填充可用的空间。
C扫描图像中的箭头显示出扫描到左边的大致范围。
4个扫描中大量的水平线绘制在每个扫描的最大信号高度点。
角裂纹的信号只有一个单峰,在所有频率上是不对称的,与信号跌落更迅速地在一边的毗邻裂纹比对面侧生的优先。
还设有一个换档的位置作为增加探针的最大频率。
图5说明来自角裂缝单一的峰值响应的效果更为明显,左侧的C扫描图像中,两个中孔裂纹的双信号可以观察到。
在这种情况下的上部的一个最大值被叠加在其他的较低的最大值上。
由此可以看出,顶部角裂纹的信号的C扫描图像开始比底部的最大的较低的中孔裂纹高。
尽管角裂纹在合成图中显然远远低于中孔。
图5.(右)左侧4.2毫米直径的两个中孔和右侧的一个小角裂纹的两侧复合断口状态图。
大小是在右上和右下相关尺寸的拆分-D传感器线圈的叠加。
(左)在1600千赫孔的C扫描图像。
这种明显的差异可以解释,是否拆分D-传感器被建模为最敏感的角D。
这是可以预期的,因为最大的感应电流密度是在励磁线圈正下方[9]。
差动线圈配置的敏感性是配对直线边缘相对Ds之间最大的。
这两个效应的结合是探头将最高灵敏度放在Ds的边角。
由于圆形感应涡流通过在一个中孔裂纹,他们在圆的任意一次扰动两次。
图5还显示一个拆分D传感器的一半叠加毗邻的裂缝问题。
可以看出在顶角在中孔裂纹上以前底角的D在角裂纹上。
因此,在这个模型中,来自前者的信号应该在后者之前启动。
这个模型还解释了为什么只有一个最大角裂纹。
励磁线圈几乎在孔外,所以试样几乎没有涡流激发。
最后它还解释了不对称的信号和被视为励磁频率增加的转变。
随着励磁线圈开始离开孔,区段和感应涡流也下降。
激励频率越高,该区段被定位在励磁线圈下,边缘越少受影响,在图3中可以观察到。
图5中可以观察到角裂纹产生的信号的强度几乎一样大,然而角裂纹只有一小部分的中孔的裂纹的大小。
这一观察结果可以使用在800和1600千赫激励频率获得的的两种类型的裂纹数据在POD分析中被量化。
角和中孔裂纹的POD数据使用概率函数进行了分析[8]。
命中/错过的依据根据C-扫描图像清晰可见的裂纹进行分析。
角裂纹有30个观测值,而中孔有44个观测值。
1600Khz的角裂缝的分析的结果显示在图6中,中孔的裂纹长度基于图7,深度基于图8。
图6.第二组数据设置使用探头的POD角裂纹分析。
实线是最适合的分析概率。
图中的虚线是概率分析的95%的上限。
X轴是对数尺度。
图7.4.62毫米的孔的中孔裂纹命中/错过的数据作裂纹长度的函数。
实曲线是最适合的概率函数,虚曲线是95%的上限上的最合适的概率曲线。
图8.4.62毫米的孔的中孔裂纹命中/错过的数据作裂纹长度的函数。
实曲线是最适合的概率函数,虚曲线是95%的上限上的最合适的概率曲线。
表1比较总结800和1600khz的角和中孔裂缝的etectability参数。
裂纹检测到在较高的频率为1600千赫。
深度为0.22mm的角裂纹的a90/95小于0.34毫米的中孔裂纹的a90/95。
既然(所检测的裂纹的平均尺寸)两个A50大致相同(0.15毫米),这种差异反映在,中孔裂纹的数据比角裂纹数据有更大的分散。
然而,一个孔中的裂纹检测(A50)的平均区域,假设一个椭圆形的裂缝,平均面积为0.041平方毫米,和0.018平方毫米角裂纹相比。
要大两倍。
在800千赫a90/95角和中孔裂缝在1.5和2之间的因素与在1600千赫更大。
然而,A50中孔裂纹的平均面积估计相比800kHz的角裂纹是现在的3倍。
这些结果清楚地显示了对于角裂纹有更高的灵敏度的技术。
表1.角和中孔裂缝检测参数之间的比较。
4.讨论
透入深度的关系的一个检验,可用于进一步阐明所观察到的A50和a90/95中孔和角裂缝得到的值。
透入深度δ,假设一个无限的导电半空间和平面的磁场可从[9]中获得。
ρ是电阻率,μ是磁导率,f是涡流仪的工作频率。
7075-T6铝合金的电阻率是5.3μΩ厘米(32%IACS的导电性)[9],因此,本次检查中使用的为1600千赫透入深度δ,为0.09毫米。
这些数字的基础上,估计最高取样深度3δ为0.27毫米。
虽然人们意识到,中孔探头内只是一个近似的平面场,这个透入深度的范围符合a50(深度)0.15毫米的角和中孔裂缝和的a90/95的深度0.22毫米角裂缝和0.34毫米中孔的裂缝的观测值。
在800千赫透入深度为0.13毫米,3δ是0.39毫米,再次符合示于表1的A50(深度)的观测值和跟踪方程所描述的预期频率。
平均A50区被考虑时有一个更大的差距(800千赫的系数3相比于在1600千赫的系数2)。
假设平面场及无限导电半空间用来获得透入深度的结果,超出3δ深度角裂缝几何形状不能确切的模拟,归因于增加的长度可提高探测响应,作为裂纹的长度也是一个可检测的因素[10]。
然而,在这里检测出的典型的裂纹尺寸远远小于探头的实际直径1.8mm,深度为A50(0.15毫米)和a90/95(0.34毫米)之间,在1600千赫跨度值为3δ。
这一观察表明,在这种尺寸下的可探测性的裂缝的深度和长度都起作用。
在带状图表显示的中孔裂缝的信号曲线,如图3所示,其特征在于有一个双峰值。
正如“结果”部分所指出的,双峰值的图形反映发射线圈和差分D-拆分线圈下方的圆感应的涡流的相互作用,如图1所示。
信号轮廓的不对称是由于探头制造的轻微变化。
例如,Ds可能并不完全对称的位置或可能会稍微倾斜于探头主体。
图2中较早的(低级)的信号分量比后来(上)峰值具有30%以上的信号幅度。
在人工检测下这种峰值幅度的差异可能会成为一个中孔的POD因素,或者是峰值幅度可能会选择作为本地记录的最大值。
如果是角裂纹,这种影响会引入一个在正面和背面上的裂缝系统之间的差异。
观察试样反转时有这种一致的差异。
明确进行研究,创建和测试事实后对裂缝(或EDM凹槽)的影响。
如果没有测试样本在两个几何或多个探头,将建成的数据一致的的偏置。
图4显示信号叠加的效果从两个相隔约2毫米的裂纹开始,如图1所示它对应于探头尺寸。
两个裂缝的叠加的效果。
较大的幅度的中央峰的出现是由于第二个尾随的响应与来自第二大裂缝的反应重合。
两个裂纹靠近彼此的情况,是POD的一个因素,因为该组合信号的响应会被检测,反映存在两个较小的裂缝,而不是一个单一的裂纹。
与中孔裂纹的信号相比,其特征在于角裂纹的信号只有一个单一的峰值。
缺乏第二个峰值的原因已在上面讨论过,因为它已经大于通过的孔,可以理解为,由于励磁线圈不能产生显着的涡流。
Bowler和Theodoulidis已经计算单个线圈的涡流的阻抗,激发线圈越过无限半导体电板(与铝相似)的边缘时产生的电导率为35MS/ m。
假如孔的直径和探头的尺寸有极大的关联,当励磁线圈的外边缘刚刚超过板的边缘,它们的结果显示约50%的板的边角的涡电流密度的增加。
产生增加密度的涡流是因为试图完成的励磁线圈的镜像模型,但被限制在导体内流动。
即使当线圈的中心超过边缘,板右上角的的涡电流密度达到最大值,显示的值大于当线圈在导体上远离边缘时的值。
假设探头对裂纹的响应是线性的涡电流密度,这表明,一个角部裂纹产生的反馈远大于相同大小的中孔裂纹,在这里所给出的是定性一致的裂纹的数据。
在1和10千赫之间的线圈的电抗的频率依赖于也被建模,这可能是800到1600千赫频率之间观察到的反应指标的差异。
4.总结
角和中孔裂纹螺栓孔的涡流探伤,使用标准的分割-D差分探头的信号响应有关方面已研究。
这些数据表明,差分的拆分D-探头对裂缝中的角部D是最敏感的,与区域中最大的感应涡流密度重合,而这引起了一个双最大值小的中孔裂纹的每个角通过裂纹。
由于励磁线圈在孔外,双信号在角裂纹中没有见过,当第二个D角通过裂纹的时候也没有激发涡流。
可以看出该装置要对角裂纹敏感得多。
角裂纹在1600千赫的a90/95测得为0.22毫米(长度)可与0.34毫米(纵深)和0.62毫米(长度)中孔裂纹相比。
基衬敏感性增加归因于板材边缘的存在,即不允许远侧感应出的涡流通道周围不连续,从而提高了有效阻抗的不连续性和所产生的差动线圈响应。