数控车床操作作业指导书05112版.docx
《数控车床操作作业指导书05112版.docx》由会员分享,可在线阅读,更多相关《数控车床操作作业指导书05112版.docx(6页珍藏版)》请在冰豆网上搜索。
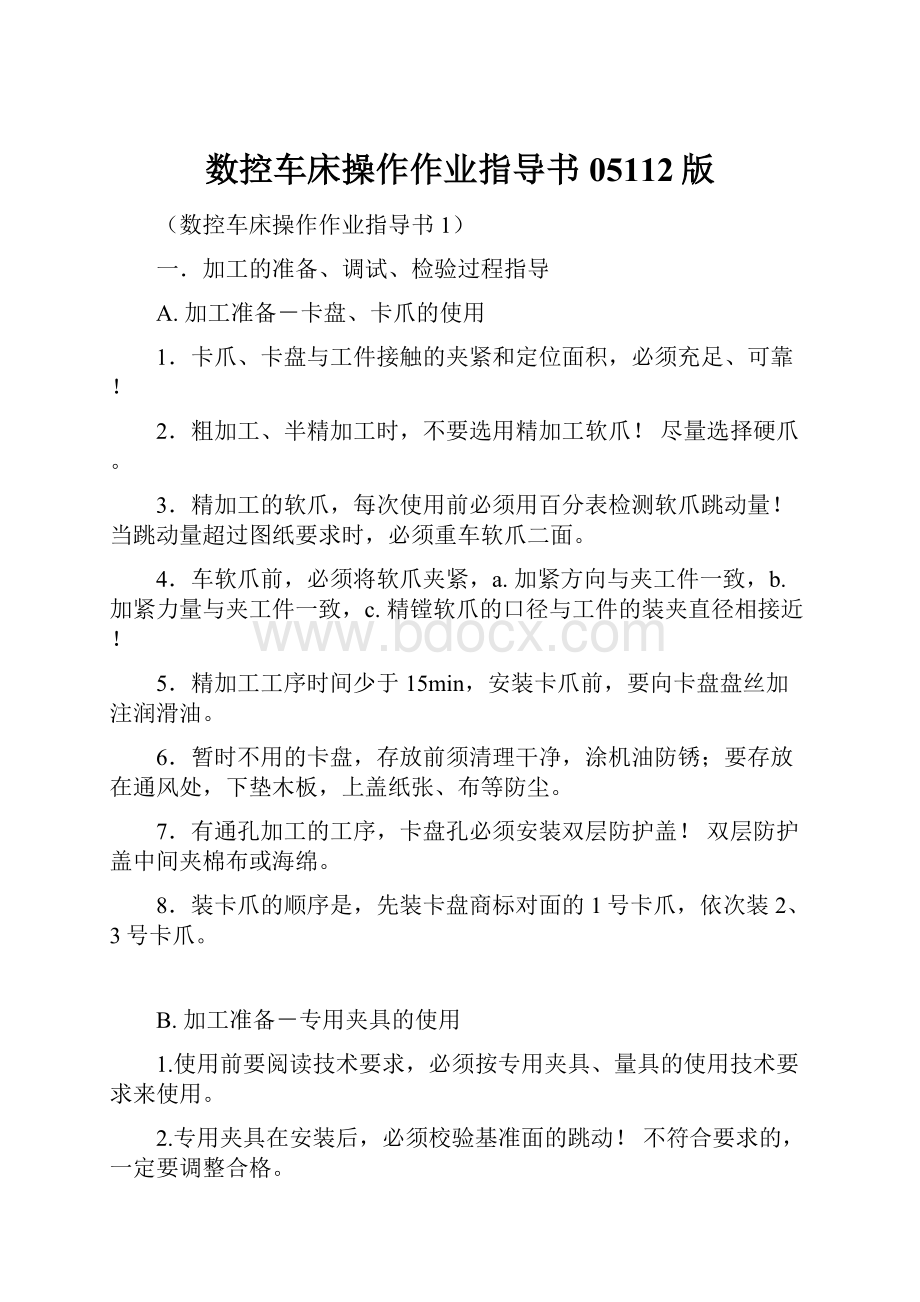
数控车床操作作业指导书05112版
(数控车床操作作业指导书1)
一.加工的准备、调试、检验过程指导
A.加工准备-卡盘、卡爪的使用
1.卡爪、卡盘与工件接触的夹紧和定位面积,必须充足、可靠!
2.粗加工、半精加工时,不要选用精加工软爪!
尽量选择硬爪。
3.精加工的软爪,每次使用前必须用百分表检测软爪跳动量!
当跳动量超过图纸要求时,必须重车软爪二面。
4.车软爪前,必须将软爪夹紧,a.加紧方向与夹工件一致,b.加紧力量与夹工件一致,c.精镗软爪的口径与工件的装夹直径相接近!
5.精加工工序时间少于15min,安装卡爪前,要向卡盘盘丝加注润滑油。
6.暂时不用的卡盘,存放前须清理干净,涂机油防锈;要存放在通风处,下垫木板,上盖纸张、布等防尘。
7.有通孔加工的工序,卡盘孔必须安装双层防护盖!
双层防护盖中间夹棉布或海绵。
8.装卡爪的顺序是,先装卡盘商标对面的1号卡爪,依次装2、3号卡爪。
B.加工准备-专用夹具的使用
1.使用前要阅读技术要求,必须按专用夹具、量具的使用技术要求来使用。
2.专用夹具在安装后,必须校验基准面的跳动!
不符合要求的,一定要调整合格。
3.夹具使用四不准:
①不准使用过长的扳手或接长板手来夹紧工件!
以防止夹具变形或夹伤工件;②校正时不准用力敲击夹具;③装卸夹具时不准磕碰;④夹具用完卸下后,清理干净,涂机油,存放通风处,以防生锈。
C.加工准备-量具的使用
D.加工准备-刀具的安装
1.安装数控刀柄时,必须按工序卡刀位图要求的刀号、伸出长度安装!
2.安装数控刀柄时,除特殊要求外,刀柄的侧面必须与刀架内侧面可靠的贴紧!
刀柄与刀架端面应平行!
3.安装刀片前,必须清理刀片槽、刀垫及刀片的各定位面,并向螺钉孔注润滑脂!
4.安装刀片(特别是陶瓷刀片)前,必须先用手试压放在刀片槽中的刀片,刀片不能有翘动的现象!
!
5.安装刀片时,必须在手压刀片下,使刀片与刀垫贴紧,再轻轻拧紧螺钉或定位销,检查刀片与刀片槽定位面是否贴紧。
推拉刀尖检查刀片是否可以转动!
(特别是V、D型刀片)最后压紧螺钉及压板!
6.更换刀片时,要检查新旧刀片的刀尖半径是否一致。
如有区别,必须在刀补界面中调整R值!
7.安装金属陶瓷刀片时,所有的压刀片螺丝只允许使用扳手的短柄拧紧。
8.安装数控刀柄后,必须按工序卡刀位图的要求检验刀柄伸出长度,是刀架最高点到刀尖的距离才可进入对刀流程。
E.调试阶段
1.对刀时,必须选择与工件同类的材料试切。
2.新程序传入后,先将刀架向Z正方向平移,空运行程序四次:
①检查程序是否有刀路错误报警;②检查刀路轨迹是否正确;③检查Z向对刀是否正确;④检查刀具及刀架运行与工件、卡盘、尾座、防护门之间是否会发生碰撞。
3.修改程序时,严禁随意改变G00、G01、G02、G03指令!
!
需要修改时,必须认真模拟检查修改后的刀路轨迹是否正确!
!
4.每一道工序的首件,必须按质检图检验该道工序加工的全部尺寸;工序首件尽量选择上道工序有问题的工件。
5.GSK980系统:
在有刀尖半径补偿的程序段中,尽量不要有空行;
6.GSK980系统:
遇到(限位开关)超程报警,在超程解除后,必须关机,重新启动机床和系统,重新回参考点。
7.HNC-21系统:
遇到(限位开关)超程报警,在超程解除后,必须重新回参考点。
F.加工阶段
1.外来粗加工工件的关键尺寸必须经过检验,上机床时还要目测相应的关键尺寸。
2.夹紧零件的夹紧力要适度!
精加工时用力要小一些,不允许夹伤已精加工过的表面。
3.精加工夹紧零件时,卡盘商标应在正上方。
4.精加工时,使用一个卡盘扳手孔夹紧零件;粗、半精加工时,要使用两个卡盘扳手孔夹紧零件。
5.单端夹紧零件,卸下时最后应留有一定的夹紧力,要一手推扳手一手扶工件,将工件卸下。
6.毛坯长度过长过短,要通过刀架平移来调整;工序尺寸过大过小,要调整相应刀号的刀补值!
7.GSK980系统在:
调整刀补值时,翻至000#刀补界面,输入U或W值之后,必须心算调整后的刀补值,等候复验!
8.每件工件在自动循环加工开始时,将防护门拉到一半处,目测检查毛坯跳动、冷却液喷出流量及喷射方向,正常时再拉好防护门!
8.GSK980系统:
遇到(限位开关)超程报警,在超程解除后,必须关机,重新合闸启动机床和系统,重新回参考点。
9.HNC-21系统:
遇到(限位开关)超程报警,在超程解除后,必须重新回参考点。
10.切槽刀崩刃后,必须用焊接切槽刀修净槽底的崩刃坑!
11.在加工的过程中,注意听加工声音是否正常,正常的声音是均匀的磨擦音和水花的飞溅音交织在一起。
F.加工阶段-检验
1.工序初始加工(刀具处于早期磨损)阶段(小件20件内),各个工序尺寸必须件件测量;更换新刀片的初始加工阶段(小件20件内),新刀片相应的工序尺寸必须件件测量。
2.工序正常加工(刀具处于正常磨损)阶段:
小件,所有的工序尺寸每间隔10件左右必须检查,
3.精加工刀尖加工时间超过60min后,粗加工刀尖加工时间超过80min后,刀具已进入后期快速磨损阶段,必须逐步缩减工序尺寸测量的间隔件数,并逐件检查表面粗糙度,随时准备更换新刀具。
4.公差值大于±0.1的尺寸,应采用游标卡尺测量;公差值小于±0.1的尺寸,应采用千分尺测量。
5.不能长时间握持量具!
(特别在冬季)不允许握持千分尺尺架部分,应握持尺架的两端或隔热塑料板!
6.每一道工序首件,必须按质检图检验该道工序加工的全部尺寸;正常加工后,只需检验工序尺寸(工序卡简图中的尺寸)。
7.使用内径百分表时,每间隔4小时和交接班时必须校验一次。
8.螺纹塞规的止规旋入不允许超过2扣(720度),通常控制在0-270度。
9.攻丝时和粗加工时工件必须夹紧。
10.不可忽视工件的热变形,不允许在工件温度较高时进行测量!
粗加工后的工件,必须放置温度下降到室温后,才能进行精加工!
11.大型、精密零件必须在车间放置24小时(体积越大时间越长)以上,才能加工!
粗精加工之间要间隔24小时以上!
12.在无空调的车间,当环境温度低于18℃(特别在冬季)进行精加工时(特别是加工大尺寸、精密零件),必须经常监测冷却液温度!
设法减少冷却液与室温的差别。
因冷却液温度的升高会造成工件膨胀,下机后随着温度下降而收缩,导致工件尺寸偏小,甚至超下差造成工件报废。
13.在无空调的车间,必须注意环境温度对测量精度的影响!
在冬季必须注意上下午转换,及开窗、开门通风造成室温的变化!
14.在有空调的车间,①冬季应当将室温控制在16℃左右,夏季应当将室温控制在24℃左右!
(测量标准温度为20℃)24小时不能停空调,保持室温的恒定;②经常监测冷却液的温度!
设法减少冷却液与室温的差别。
(数控车床操作作业指导书1)
二.数控车螺纹加工注意事项
A.螺纹刀具安装
1.安装数控螺纹刀柄时,刀柄的侧面必须与刀架内侧面可靠的贴紧!
刀柄与刀架端面应平行!
2.安装刀片前,必须清理刀片槽、刀垫及刀片的各定位面,并向螺钉孔注润滑脂!
3.安装刀片时,必须用手推紧刀片,使刀片与刀片槽定位面贴紧后,再压紧螺钉!
压紧力必须充足。
4.安装三角形刀片后,必须用刀口尺或白钢刀条检查刀片是否存在转角!
存在转角时,必须重新安装刀片!
B.螺纹加工初始阶段及测量
1.对刀后试切,刀补直径X方向应留有余量,宁车不足,勿过止规!
2.用通规测量螺纹余量较小时,在观察到重修一遍中的第一次吃刀后,应立即停止自动循环,检测螺纹尺寸!
3.加工中,注意观察最后二刀车削时主轴转速下降情况!
倒数第一刀车削时主轴转速下降幅度不得超过0.8%(并考虑螺纹导程的极限偏差要求);倒数第二刀车削时主轴转速下降幅度不得超过2.0%。
4.新刀尖在初始加工(刀具处于早期磨损)阶段(20~30件),必须逐件检查螺纹尺寸。
发现尺寸变化较大时,应检查刀片是否转位,甚至松动。
5.在刀尖的初始和后期加工阶段严禁使用螺纹顶径的间接测量方法!
C.螺纹加工阶段
1.螺纹车削过程中,严禁调整主轴转速!
2.螺纹车削过程中,严禁用手触摸螺纹,更不能用棉布擦回转中的螺纹!
3.尺寸突然变化,通规无法通过时,首先检查有无毛刺,如有要用油石清除;其次,检查刀尖形状,一般多为刀尖发生破损!
4.当使用标准型刀片时,在正常加工阶段,同一刀片上的刀尖加工出的螺纹,可采用内外径千分尺检测螺纹顶径的间接测量方法,但是每间隔30~40件必须用螺纹规校检。
注意:
在刀尖的初始和后期加工阶段严禁使用该测量方法!