自动控制系统论文电泳涂漆.docx
《自动控制系统论文电泳涂漆.docx》由会员分享,可在线阅读,更多相关《自动控制系统论文电泳涂漆.docx(28页珍藏版)》请在冰豆网上搜索。
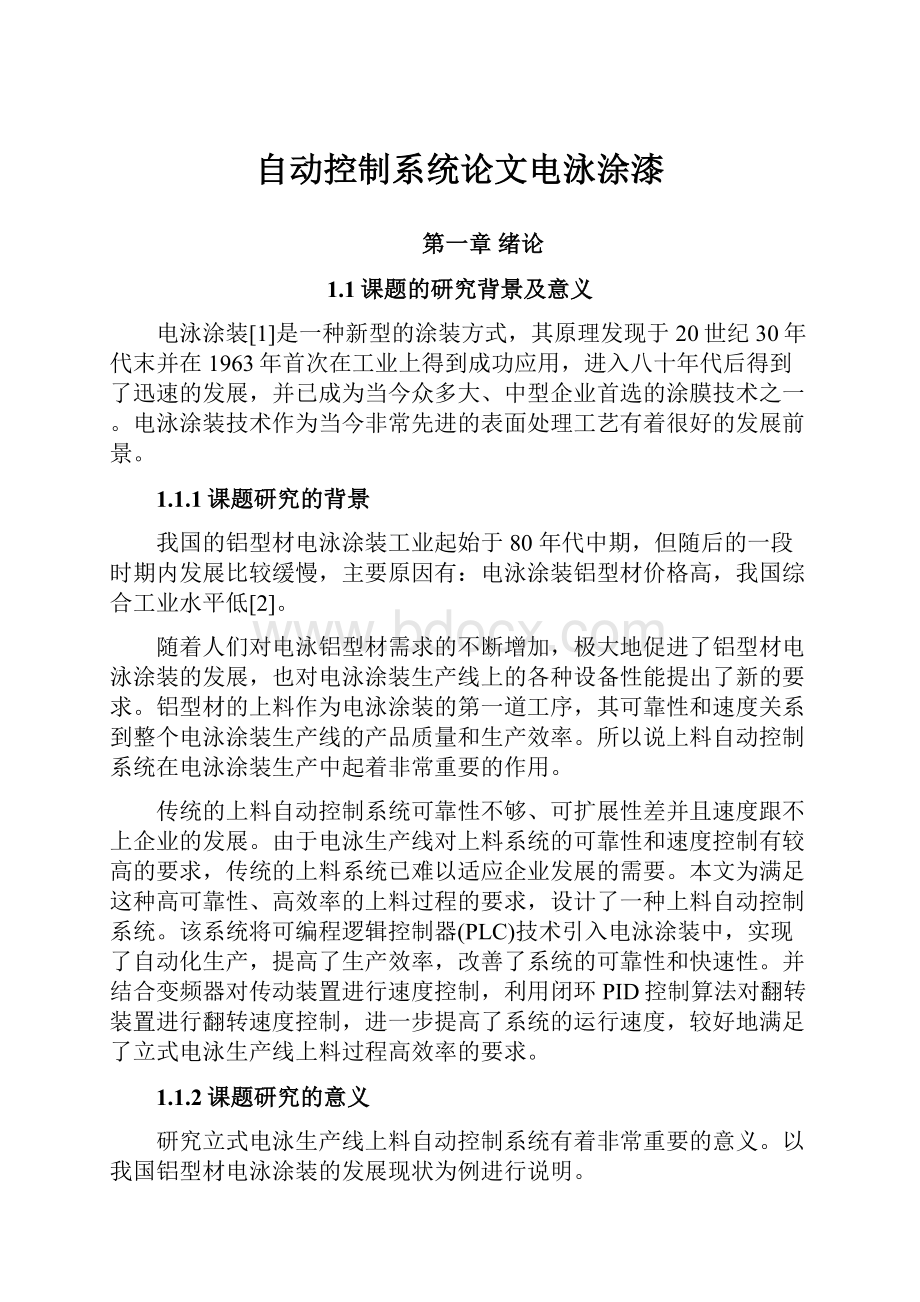
自动控制系统论文电泳涂漆
第一章绪论
1.1课题的研究背景及意义
电泳涂装[1]是一种新型的涂装方式,其原理发现于20世纪30年代末并在1963年首次在工业上得到成功应用,进入八十年代后得到了迅速的发展,并已成为当今众多大、中型企业首选的涂膜技术之一。
电泳涂装技术作为当今非常先进的表面处理工艺有着很好的发展前景。
1.1.1课题研究的背景
我国的铝型材电泳涂装工业起始于80年代中期,但随后的一段时期内发展比较缓慢,主要原因有:
电泳涂装铝型材价格高,我国综合工业水平低[2]。
随着人们对电泳铝型材需求的不断增加,极大地促进了铝型材电泳涂装的发展,也对电泳涂装生产线上的各种设备性能提出了新的要求。
铝型材的上料作为电泳涂装的第一道工序,其可靠性和速度关系到整个电泳涂装生产线的产品质量和生产效率。
所以说上料自动控制系统在电泳涂装生产中起着非常重要的作用。
传统的上料自动控制系统可靠性不够、可扩展性差并且速度跟不上企业的发展。
由于电泳生产线对上料系统的可靠性和速度控制有较高的要求,传统的上料系统已难以适应企业发展的需要。
本文为满足这种高可靠性、高效率的上料过程的要求,设计了一种上料自动控制系统。
该系统将可编程逻辑控制器(PLC)技术引入电泳涂装中,实现了自动化生产,提高了生产效率,改善了系统的可靠性和快速性。
并结合变频器对传动装置进行速度控制,利用闭环PID控制算法对翻转装置进行翻转速度控制,进一步提高了系统的运行速度,较好地满足了立式电泳生产线上料过程高效率的要求。
1.1.2课题研究的意义
研究立式电泳生产线上料自动控制系统有着非常重要的意义。
以我国铝型材电泳涂装的发展现状为例进行说明。
现在,我国的原铝产量已经达到250万吨,在世界居第三位,生产能力已经达到350万吨。
在当今的多种铝型材表面处理技术之中,电泳涂装是一种最具有发展前景的表面处理技术[3]。
所以,铝型材电泳涂装技术在近几年得到了巨大的发展。
铝型材的电泳涂装方法和铝型材的其他涂装方法比较[4]有着以下几个优势:
(1)易实现生产过程中的自动化。
(2)涂膜致密且均匀。
(3)涂装过程中涂料的利用率非常高。
(4)环保与安全。
(5)质量好。
由于电泳涂装具有许多其他涂装方式无法比拟的优势,铝型材电泳涂装工艺得到了快速发展,许多大型铝型材厂都应用了电泳涂装生产线以满足消费市场对具有高质量的铝型材的需求。
国内铝型材的电泳涂装工艺正在进入一个崭新的发展时期[2],随着国内城市建设的迅速发展,装修技术的改进和应用领域的迅速扩大,铝型材电泳涂装必将在我国有着更大的发展。
从我国铝型材电泳涂装的发展现状可以看出,电泳涂装技术正在迅速代替传统的涂装工艺[5]。
上料控制系统性能的优良与否,直接关系到产品的质量和整个系统的生产效率。
所以说,设计能够适应企业发展需要的上料系统也必将成为一个重要的技术课题。
1.2国内外铝型材表面处理技术的发展状况
1.2.1铝型材电泳的工艺流程及所需设备
以阳极电泳为例,通常按如下工艺进行:
脱脂冷水洗冷水洗(逆流)
碱蚀冷水洗冷水洗(逆流)纯水洗(加喷淋)阳极氧化冷水洗冷水洗热洗烫洗阴极电泳RO1水洗(加喷淋)Ro2水洗(加喷淋)滴水烘干强冷。
电泳涂装的涂料必须在涂装生产线上转化和生产才能够成为高品质的电泳涂装涂膜。
所以,电泳涂装生产线上的设备的运行状况是决定能否把高品质涂料转化成为高品质产品的关键。
常用的电泳生产线设备由以下几个部分组成:
1.电泳槽
2.电源
3.电极
4.精致系统(IR)
5.回收装置(RO)
6.过滤循环系统
7.烘烤系统
1.2.2常用的铝型材表面处理方法及其发展
铝型材表面处理常用的方法有以下三种:
1、阳极氧化,阳极氧化处理技术是最早的铝型材表面处理技术并得到了非常广泛的应用,到现在依然是这方面常用的处理方法;
2、阳极氧化后电泳丙烯酸树脂,这种技术在日本和欧洲都得到了普遍应用;
3、电泳涂层,白色电泳涂层的发展非常迅速,是一种新型的涂装工艺,有着非常好的发展前景。
纵观铝型材生产线的发展,其可分为卧式生产线和立式生产线。
铝型材电泳涂装生产线中最先得到广泛应用的是卧式电泳生产线。
随着人们对电泳铝型材需求的不断增加,极大地促进了铝型材电泳涂装的发展,也对电泳涂装生产线上的各种设备性能提出了新的要求。
铝型材的上料作为电泳涂装的第一道工序,其可靠性和速度关系到整个电泳涂装生产线的产品质量和生产效率。
所以说上料自动控制系统在电泳涂装生产中起着非常重要的作用。
卧式生产线将铝挤压型材水平装卡在导电支柱上进行阳极化处理,而立式生产线的是将挤压型材垂直装挂,其工艺过程与水平式相同。
立式电泳生产线可按常规方法对挤压铝型材进行本色或者着色阳极化,也可以对铝型材进行木纹化处理,但是其产量则会大大降低。
卧式装挂中遇到的问题是铝型材的弯曲问题,而立式中遇到的问题是铝型材被吊车送进处理槽中前摆动的问题。
所以,被装挂的铝型材最下端相互之间应该留有足够的间距以避免在吊车停止时发生碰撞。
线性电动机能够让铝型材以不同的速度平稳的行驶。
阳极化处理过程一般要30至40分钟,这样才能使氧化膜厚度达到标准值,所以是整个工艺过程中耗时最长的一个部分。
因此,实际生产中,通常在一条生产线中建造多个相同的阳极化处理槽,这样就可以同时在几个处理槽中进行阳极化处理,避免了因铝型材不能够及时入槽阳极化而浪费时间。
阳极化处理中所需要的阳极化处理槽的数目由每个氧化吊架所能够装挂铝型材的数量来决定。
在卧式生产线中,每次所能够装挂的铝型材的数量取决于装挂空间的高度,此外还会受到装料速度的限制。
随着环境污染1970年作为社会问题被提出,与此同时节省能源也被作为另一个重大课题在工业界中被提出。
为了适应社会可持续发展对上述两个问题提出的要求,阳极化生产线逐渐采用了闭路系统。
新型阳极化生产线在氧化铝材的同时可减少操作人员的劳动量并能控制环境污染。
卧式阳极化生产线不能同时满足以上两方面的要求,因此很快被立式生产线所取代。
总而言之,电泳生产线正由传统的卧式向新型的立式发展,立式线适用于大批量生产,能源和药品的消耗量都比卧式生产线[6]低,并且容易进行自动化生产。
1.3课题的主要任务和论文的组织
1.3.1课题的主要任务
课题研究的主要任务是利用PLC来控制上料系统各部分装置协调工作;PLC根据升降过程的需要对变频器进行控制实现对升降电机的速度调节;PLC根据翻转过程的需要对起立装置的比例阀进行控制实现对翻转架翻转的速度调节。
研究的重点内容有:
1、PLC选型及各模块的选择;
2、变频技术的学习及变频器的选型;
3、PLC程序控制系统各组成部分的运行;
4、电动机调速机械特性和调速原理;
5、利用PID控制算法对比例阀开度进行控制。
1.3.2论文的组织
论文的第一章是绪论,对该论文的研究背景及意义和国内外的发展状况进行了概述,然后介绍了本课题研究的主要内容。
第二章是立式电泳生产线上料自动控制系统的总体方案设计,着重论述了系统的总体功能和PLC控制网络。
第三章是系统硬件方面的设计,包括PLC与变频器的选型和控制系统各部分的实现。
第四章是软件方面的设计,包括系统流程图的设计和主要模块的子程序设计。
第五章是对翻转架变速控制的实现,包括翻转过程的分析和PID控制的实现。
第六章是总结与展望,包括对论文设计的总结和对本文缺点和应该改进的地方进行分析。
第二章立式电泳生产线上料自动控制系统总体方案设计
2.1系统的总体功能介绍
立式电泳生产线上料控制常用于电泳生产线的上料传送。
该系统的机械装置由上料起立装置、实梁搬出装置和空梁搬入装置三部分组成[7]。
上料自动控制系统机械图如图2.1所示。
图2.1上料自动控制系统机械图
其中,上料起立装置主要由翻转架、夹紧装置和液压缸组成,上料起立装置主要实现铝型材的夹紧和翻转传送的功能;实梁搬出装置主要由升降机A、输送链B和升降机C组成,实梁搬出装置主要实现将实梁传送到输送链B的功能;空梁搬入装置主要由升降机D、输送机F和输送机A组成,空梁搬入装置主要实现将下料部分送过来的空梁传送到升降机B的功能。
翻转架上翻过程:
翻转架在夹具把材料夹紧后如果运行条件满足则启动上翻程序,在刚开始翻转时处于加速阶段,当速度达到设定值时翻转架匀速翻转,在PLC检测到限位开关时翻转架减速翻转,当系统检测到超限位开关时液压缸立即停止运动。
翻转架下翻过程:
翻转架在得到空梁后如果运行条件满足则启动下翻程序,翻转架在刚开始翻转时处于加速阶段,当速度达到设定值时翻转架匀速翻转,在PLC检测到限位开关时翻转架减速翻转,当系统检测到超限位开关时液压缸立即停止运动。
上料自动控制系统的上料流程图如图2.2所示。
图2.2上料自动控制系统上料流程图
2.2系统的PLC控制网络
2.2.1PLC控制网络的组成及各组成部分的功能
该系统利用可编程逻辑控制器(PLC)对系统的各个组成部分进行控制,使系统的各组成部分协调有序地工作,首先要建立一个PLC控制网络。
该控制网络由主控制盘和5个远程端组成。
主控制盘及其5个远程端的I/O点数如表2.1所示。
表2.1主控制盘和5个远程端的I/O点数
主控制盘
I:
198
O:
20
动力盘1
I:
20
O:
59
动力盘2
I:
8
O:
16
实梁搬出
I:
13
O:
11
空梁搬入
I:
25
O:
18
起立装置
I:
23
O:
30
其中,动力盘1包括升降机C的升降电机、升降机C的左右输送电机、升降机D的升降电机、升降机D的左右输送电机、升降机A的左右输送电机、升降机B的左右输送电机、翻转架上的传送带电机;动力盘2包括单轨车、升降机A的电机、升降机B的电机、输送机A的电机、输送机F的电机、输送机A的气缸、输送机B的气缸、输送机F的气缸。
主控制盘选用32个I/O点数,5个远程端均选用16个I/O点数,在考虑10%到20%的可扩展余量后,PLC控制网络可选用1个SLC500PLC1747—L543CPU模块、6个1747—P4电源模块、1个1747—SN远程I/O扫描模块、1个1746—NO4V模拟量输出模块、2个1746—OB32输出模块、8个1746—IB32模块、5个1747—ASB、13个1746—OB16输出模块、9个1746—IB16输入模块。
PLC控制网络图如图2.3所示。
由图可知,装料处控电盘的组成为:
1个1746—NO4V模拟量输出模块,2个1746—OB32输出模块,8个1746—IB32输入模块,1个1747—SN远程I/O扫描模块,1个SLC500PLC1747—L543CPU模块,1个1747—P4电源模块;装料处动力盘1的组成为:
4个1746—OB16输出模块,2个1746—IB16输入模块,1个1747—ASB,1个1747—P4电源模块;装料处动力盘2的组成为:
4个1746—OB16输出模块,2个1746—IB16输入模块,1个1747—ASB,1个1747—P4电源模块;实梁搬出现场操作盘的组成为:
2个1746—OB16输出模块,1个1746—IB16输入模块,1个1747—ASB,1个1747—P4电源模块;起立装置现场操作盘的组成为:
2个1746—OB16输出模块,3个1746—IB16输入模块,1个1747—ASB,1个1747—P4电源模块;空梁搬入现场操作盘的组成为:
1个1746—OB16输出模块,1个1746—IB16输入模块,1个1747—ASB,1个1747—P4电源模块。
图2.3PLC控制网络图
在SLC500系统中,每个框架都需要配备一个电源,该电源的作用是给控制器和I/O模块供电,电源安装在机架左侧。
SLC500系统总共有7种电源可供选择,目录号分别为1476-P1、1476-P2、1476-P3、1476-P4、1476-P5、1476-P6和1476-P7。
其中1476-P1、1476-P2、1476-P43种为交流电源(DC120/220V通过跳线选择),1476-P3、1476-P5、1476-P6和1476-P74种为直流选择。
本系统选用1476-P4模块。
SLC框架主要用于安放控制器和I/O模块。
有4种框架尺寸可以选择:
4槽(1746-A4)、7槽(1746-A7)、10槽(1746-A10)和13槽(1746-A13)。
电源安装在框架的最左侧。
所有的模块都可以沿着框架上的导轨方便地进行安装。
本系统采用13槽(1746-A13)框架。
2.2.2上料自动控制系统的网络通信
本系统通信采用DH+(DataHighwayPlus)网络。
DH+网络是在DH-485网络的基础上发展起来的一种工业局域网[8]。
不过DH+在网络的传输距离和接点容量以及稳定性的方面都比DH-485有了明显的增强。
DH+网络技术参数见表2.2。
表2.2DH+网络技术参数
名称
描述
网络节点范围
最多64个节点
干线最大长度
3050m
传输波特率
57.6kbit/s,115.2kbit/s和230.4kbit/s,
总线寻址方式
多主方式,令牌传递
2.2.3PLC控制网络的基本控制思路
机械装置的位置控制采用行程开关对机械装置的位置进行检测,然后将检测到的信号传送给PLC控制器,PLC根据装置的位置做出相应的响应;对于升降装置的速度控制,采用PLC控制变频器调节电机变速运行;对于翻转装置的速度控制,采用PLC控制液压器的比例阀来调节翻转装置变速运行。
位置控制的基本思路:
当装置触发限位开关,这一信号传递给PLC使该装置减速或停止;系统中某个装置的运动会受到其他装置运动情况的约束,该装置的运动条件和与之相约束的其他装置是否处于相应的限位处相关,检测各装置的相应的限位信号并传递给PLC,然后利用PLC来控制系统各装置的动作。
定位控制过程的条件如图2.4所示。
图2.4定位控制过程
电机变频调速的基本思路:
电机开始运行时在低速档运行;随后,PLC控制变频器对电机进行加速,电机在高速档匀速运行;在装置接近限位开关时,PLC控制变频器使电机回到低速档运行;当装置触发限位开关时,PLC控制电机停止运行。
比例阀控制的基本思路[9]:
翻转架根据PLC中的程序设置的速度运动,PLC系统首先计算实际速度和程序设定速度的偏差△v,当偏差比较大时,P调节起主要作用,PID调节器的开度变大,则比例阀的开度也加大;当偏差比较小时,只有I调节,PID调节器的开度基本上保持不变,比例阀开度也相应地保持恒定。
第三章立式电泳生产线上料自动控制系统的硬件设计
3.1PLC的选型及各模块的选择
3.1.1PLC概述
1.PLC的发展
20世纪60年代,在工业控制中计算机技术开始得到应用。
鉴于当时计算机技术还不够成熟,编写程序具有很大的难度,抗干扰能力差难以适应相对恶劣的工业环境,计算机控制技术没能够在工业控制中得到广泛应用。
在当时的工业控制中,由继电器和接触器组成的控制系统应用最为广泛。
1968年,美国通用汽车公司为适应汽车型号更新,提出了“GM十条”[10]。
随后,美国数字设备公司研制出第一台PLC并在通用汽车公司的自动装配线上得到成功的应用,从而开创了工业控制的新局面。
自PLC问世以来,美国、德国、日本、法国等工业发达国家相继研发出了自己的PLC[11],使PLC技术得到了广泛应用和快速发展。
20世纪70年代,PLC中全面引入了计算机技术,PLC的功能逐步完善,再加上其价格低、小型化、可靠性高等特点,从而奠定了PLC在现代工业中的重要地位。
在20世纪70年代末,PLC已经成为工业控制领域中主要的自动化设备。
目前,随着数字控制技术[12]、通信技术、计算机技术、容错控制技术、微电子技术的快速发展,PLC在各方面都得到了快速发展。
立式电泳生产线可按常规方法对挤压铝型材进行本色或者着色阳极化,也可以对铝型材进行木纹化处理,但是其产量则会大大降低。
卧式装挂中遇到的问题是铝型材的弯曲问题,而立式中遇到的问题是铝型材被吊车送进处理槽中前摆动的问题。
所以,被装挂的铝型材最下端相互之间应该留有足够的间距以避免在吊车停止时发生碰撞。
线性电动机能够让铝型材以不同的速度平稳的行驶。
阳极化处理过程一般要30至40分钟,这样才能使氧化膜厚度达到标准值,所以是整个工艺过程中耗时最长的一个部分。
因此,实际生产中,通常在一条生产线中建造多个相同的阳极化处理槽,这样就可以同时在几个处理槽中进行阳极化处理,避免了因铝型材不能够及时入槽阳极化而浪费时间。
阳极化处理中所需要的阳极化处理槽的数目由每个氧化吊架所能够装挂铝型材的数量来决定。
在卧式生产线中,每次所能够装挂的铝型材的数量取决于装挂空间的高度,此外还会受到装料速度的限制。
2.PLC的组成
通常,可以认为PLC是一种专门用于工业控制领域的计算机系统,硬件结构和微型计算机大体上一致。
PLC主要由以下几部分组成。
1、电源
2、中央处理单元(CPU)
3、存储器
4、输入输出接口电路
5、功能模块
6、通信模块
PLC的基本结构图如图3.1所示。
图3.1PLC的基本结构图
主控制盘选用32个I/O点数,5个远程端均选用16个I/O点数,在考虑10%到20%的可扩展余量后,PLC控制网络可选用1个SLC500PLC1747—L543CPU模块、6个1747—P4电源模块、1个1747—SN远程I/O扫描模块、1个1746—NO4V模拟量输出模块、2个1746—OB32输出模块、8个1746—IB32模块、5个1747—ASB、13个1746—OB16输出模块、9个1746—IB16输入模块。
PLC控制网络图如图2.3所示。
由图可知,装料处控电盘的组成为:
1个1746—NO4V模拟量输出模块,2个1746—OB32输出模块,8个1746—IB32输入模块,1个1747—SN远程I/O扫描模块,1个SLC500PLC1747—L543CPU模块,1个1747—P4电源模块;装料处动力盘1的组成为:
4个1746—OB16输出模块,2个1746—IB16输入模块,1个1747—ASB,1个1747—P4电源模块;装料处动力盘2的组成为:
4个1746—OB16输出模块,2个1746—IB16输入模块,1个1747—ASB,1个1747—P4电源模块;实梁搬出现场操作盘的组成为:
2个1746—OB16输出模块,1个1746—IB16输入模块,1个1747—ASB,1个1747—P4电源模块;起立装置现场操作盘的组成为:
2个1746—OB16输出模块,3个1746—IB16输入模块,1个1747—ASB,1个1747—P4电源模块;空梁搬入现场操作盘的组成为:
1个1746—OB16输出模块,1个1746—IB16输入模块,1个1747—ASB,1个1747—P4电源模块。
3.SLC500简介
SLC500[13]是由罗克韦尔公司生产的模块化可编程控制器(PLC)。
ABPLC作为高品质的工业控制产品,具有易于扩展的输入输出模块,方便的内置通讯接口,非常丰富的第三方专用模块,这些特点使SLC500成为当前最好的中小型PLC。
SLC500特点:
1、具有功能强大的处理器。
适用于高速生产线操作和数据采集监控系统(SCDADA)等各种场合。
2、具有先进的控制指令集。
3、增强的通讯能力,使SLC5/03,SLC5/04和SLC5/05处理器能提供数据采集监控系统(SCADA)中的主控功能。
4、具有从1K到64K字大小的内存可供选择。
该系统中我们选取SLC5/04处理器。
SLC5/04处理器除了提供标准功能外,还提供工业控制中常用的DH+网络通讯的功能。
SLC5/04处理器的运算速度比SLC5/03处理器的运算速度要快15%左右。
3.1.2PLC的选型及模块的选择
本系统选用ABSLC500系列PLC。
SLC500具有两种硬件结构:
模块式控制器与固定式控制器。
固定式SLC控制器是把电源模块、输出模块、输入模块和控制器集中在一起,另外还提供一个2槽的扩展框架。
模块式控制器是一种安装在1476机架中的具有单槽的控制器。
SLC模块式控制器除组态比较灵活外,SLC500控制器之间还可以通过其内置的网络接口来通信。
(1)电源和框架的选择
在SLC500系统中,每个框架都需要配备一个电源,该电源的作用是给控制器和I/O模块供电,电源安装在机架左侧。
SLC500系统总共有7种电源可供选择,目录号分别为1476-P1、1476-P2、1476-P3、1476-P4、1476-P5、1476-P6和1476-P7。
其中1476-P1、1476-P2、1476-P43种为交流电源(DC120/220V通过跳线选择),1476-P3、1476-P5、1476-P6和1476-P74种为直流选择。
本系统选用1476-P4模块。
SLC框架主要用于安放控制器和I/O模块。
有4种框架尺寸可以选择:
4槽(1746-A4)、7槽(1746-A7)、10槽(1746-A10)和13槽(1746-A13)。
电源安装在框架的最左侧。
所有的模块都可以沿着框架上的导轨方便地进行安装。
本系统采用13槽(1746-A13)框架。
(2)SLC500控制器选型
本系统采用SLC5/04控制器,该控制器能够利用内置的网络接口与外界通信。
此外,SLC5/04还提供DH+网络接口,因此控制器可以无需另外的网络接口硬件,直接和DH+网上的其他控制器和设备通信。
控制器属性如图3.2所示。
图3.2控制器属性
(3)数字量输入、输出模块
数字量输入模块主要用于采集和接收现场设备输入信号,其主要包括选择开关、行程开关、按钮、数字拨码开关的数字输入信号。
数字量输出模块主要用于向执行机构输出控制信号,包括向指示灯、电磁阀和开关输出数字信号[14]。
这些模块具有能直接接受和输出交流电压(100V和220V)信号交流输入/输出单元、直流电压(24V、12V或5VTTL电平)信号直流输入或输出单元[15]。
数字量模块从1746I/O框架的背板接受电源信号,而背板的电源信号由安装在框架上的电源模块供应的。
数字量输入输出模块前部面板由指示灯、接线端子及标签组成。
本系统选用1746-IB16灌电流直流数字量输入模块,其I/O点数为16个;数字量输出模块选用1746-OB16拉电流直流输出模块,具有16个I/O点数。
(4)模拟量输出模块
模拟量输出模块主要用来向调速装置输出模拟量控制信号。
该模块将SLC的二进制信号转换成满足IEC标准的直流信号(如4~20mA、1~5V、-10~+10V、0~10V),提供给执行机构。
模拟量输出模块通过D/A转换器实现把二进制数字量转换成模拟量的功能,并最终将模拟量信号输送到端子之上。
整定PID数据数字量输入与0~10V模拟量输出之间的转换关系如图3.3所示。
图3.3整定PID数据数字量输入与模拟量输出之间的转换
本系统选用1476-NO4V模拟量电压输出模块。
该模块提供了4通道模拟量的电压输出。
1746-NO4V模拟量模块的输出映像区为模块的数据字和组态字,输入映像区为模块的状态字,都分别作为一个单独的字来寻址。
NO4V模块的组态字的设定如表3.1所示:
表3.1NO4V模块组态字的设定
位数
15
14
13
12
11
10
9
8
7
6
5
4
3
2
1
0
通道0
1
0
0
0
0
0
0
0
0
0
1
0
0