热水壶外壳塑料模具设计.docx
《热水壶外壳塑料模具设计.docx》由会员分享,可在线阅读,更多相关《热水壶外壳塑料模具设计.docx(42页珍藏版)》请在冰豆网上搜索。
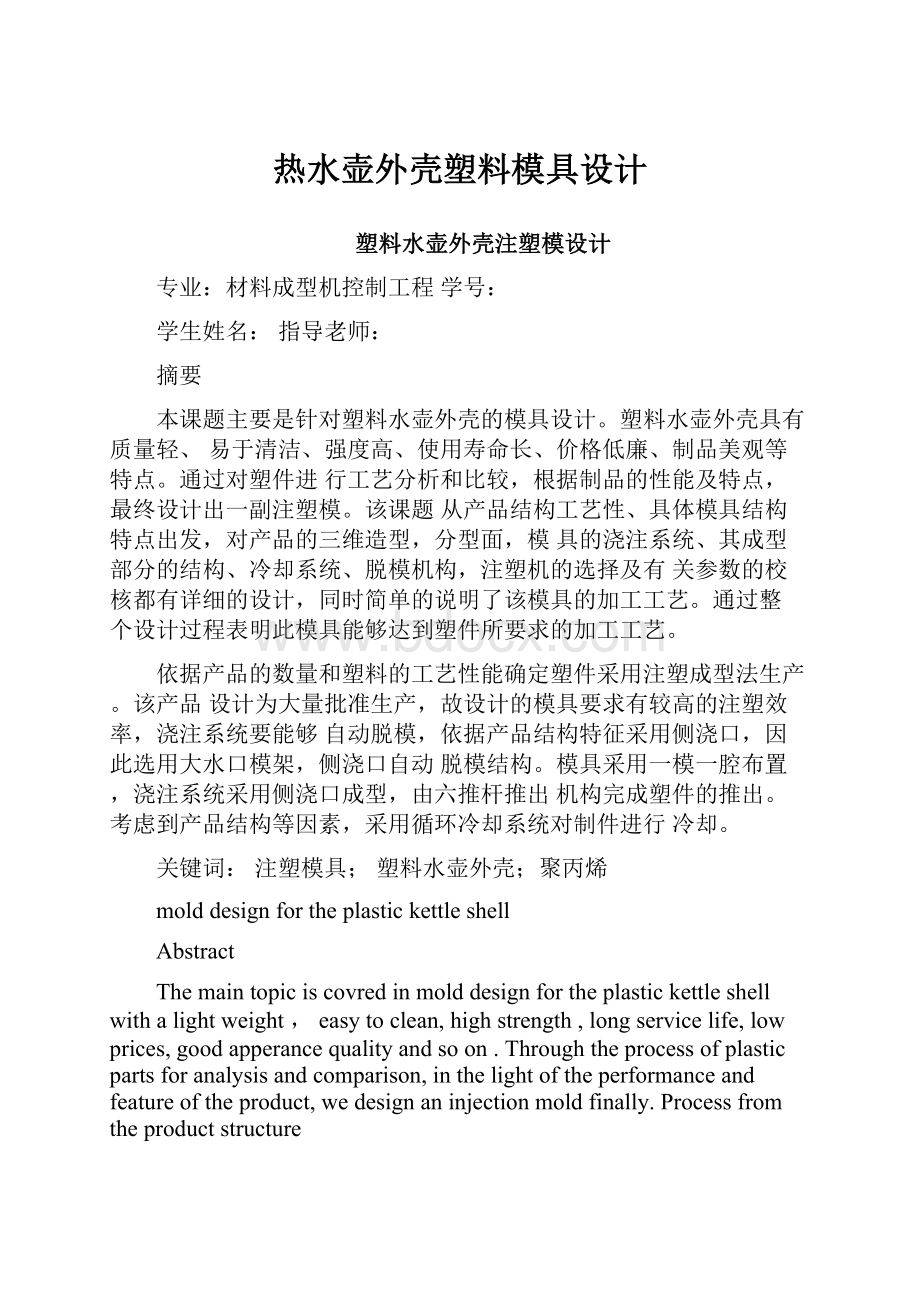
热水壶外壳塑料模具设计
塑料水壶外壳注塑模设计
专业:
材料成型机控制工程学号:
学生姓名:
指导老师:
摘要
本课题主要是针对塑料水壶外壳的模具设计。
塑料水壶外壳具有质量轻、易于清洁、强度高、使用寿命长、价格低廉、制品美观等特点。
通过对塑件进行工艺分析和比较,根据制品的性能及特点,最终设计出一副注塑模。
该课题从产品结构工艺性、具体模具结构特点出发,对产品的三维造型,分型面,模具的浇注系统、其成型部分的结构、冷却系统、脱模机构,注塑机的选择及有关参数的校核都有详细的设计,同时简单的说明了该模具的加工工艺。
通过整个设计过程表明此模具能够达到塑件所要求的加工工艺。
依据产品的数量和塑料的工艺性能确定塑件采用注塑成型法生产。
该产品设计为大量批准生产,故设计的模具要求有较高的注塑效率,浇注系统要能够自动脱模,依据产品结构特征采用侧浇口,因此选用大水口模架,侧浇口自动脱模结构。
模具采用一模一腔布置,浇注系统采用侧浇口成型,由六推杆推出机构完成塑件的推出。
考虑到产品结构等因素,采用循环冷却系统对制件进行冷却。
关键词:
注塑模具;塑料水壶外壳;聚丙烯
molddesignfortheplastickettleshell
Abstract
Themaintopiciscovredinmolddesignfortheplastickettleshellwithalightweight,easytoclean,highstrength,longservicelife,lowprices,goodapperancequalityandsoon.Throughtheprocessofplasticpartsforanalysisandcomparison,inthelightoftheperformanceandfeatureoftheproduct,wedesignaninjectionmoldfinally.Processfromtheproductstructure
oftheproject,specificmoldstructurestartingonthecastingmoldsystem,therearedetialeddesignwit,hthethre-dimensionalmodeling,binarytypesurface,gatingsystem,themouldstucture,coolingsystem,demouldingmechanism,thechoiceoftheinjectionmoldingmachine,andthecheckofsomerelatedparameter,andintroducethemoldprocessessimply.Throughtheentiredesignprocessthatcanbeachievedinthemoldplasticpartsrequiredinthisprocess.
Basedonthevolumeanddeterminetheprocessperformanceofplasticinjectionmoldingmethodusingplasticpartsproduction.Theproductisdesighnedformassproduction,sothedesignofthemoldrequiresahighinjectionefficiency,andthegatingsystemtobeabletoautomaticmoldejection.,inadditiontousesitegateaccordingtoproductstructuralfeature,sowechooseasinglesubserfaceinjectionmold,sitegateautomaticejectionstructure.Moldcavityone-cavitymold,gatingsystemusingsitegateforming,introduedextrusiondevicetocompletesixthputtingtheintroductionofplasticparts.Inconsiderationofthefactorssuchastheperformanceandsoon,usecirculatingcoolingsystemtocoolproducts.
Keywords:
injietionmould;Plastickettleshell;Polypropylene
摘要错误!
未定义书签。
Abstract错误!
未定义书签。
目录Ⅲ
第一章对塑料成型模具的认识1
1.1模具在加工工业中的地位1
1.2模具的发展趋势1
1.3设计在学习模具制造中的作用3
第二章塑件制品分析4
2.1塑件工艺分析4
2.2塑料水壶外壳材料的成型特性与工艺参数4
2.3.制品的结构工艺性5
2.4.注塑机的选择6
第三章分型面及浇注系统的设计10
3.1分型面的选择10
3.2浇注系统的设计11
3.2.1主流道和定位圈的设计12
3.2.2分流道的设计13
3.2.3浇口的设计14
3.2.4冷料穴的设计16
3.2.5排气系统的设计17
第四章分型面及浇注系统的设计18
4.1型腔布置18
4.2成型零件的结构确定18
4.2.1型腔设计18
4.2.2型芯设计19
4.2.3侧向分型与抽芯机构设计19
4.3导向定位机构设计21
4.4顶出机构设计22
4.5.温度调节系统的设计23
4.5.1.冷却系统的设计24
4.5.2加热系统的设计25
第五章主要零部件的设计计算26
5.1成型零件的成型尺寸26
5.2模具型腔壁厚的确定27
5.3标准模架的确定27
5.4安装尺寸校核28
5.5锁模力校核28
5.6注射压力校核28
5.7开模行程校核29
第六章模具零件的加工工艺设计简介30
6.1注塑模型腔的加工30
6.2导柱导套的加工30
6.3模板的加工31
第七章模具的装配32
7.1模具的装配顺序33
7.2模具的维护34
第八章设计总结错误!
未定义书签。
参考文献错误!
未定义书签。
致谢37
附录38
附录A外文翻译原文38
附录B外文翻译47
第一章对塑料成型模具认识
1.1模具在加工工业中的地位
模具是利用其特定形状去成型具有一定形状和尺寸制品的工具。
在各种材料加工工业中广泛使用着各种模具,例如金属铸造成型使用的砂型或压铸模具、金属压力加工使用的锻压模具、冷压模具等等。
对于模具的全面要求是:
能生产出尺寸精度、外观、物理性能等各方面都满足使用要求的公有制制品。
以模具的使用角度,要求高效率、自动化操作;从模具制造角度,要求结构合理、制造容易、成本低廉。
模具影响着制品的质量。
首先,模具型腔的形状、尺寸、表面光洁度、分型面、进浇口和排气槽位置以及脱模方式等对制件的尺寸精度、和形状精度以及之间的物理性能、机械性能、电性能、内应力的大小、各项同性、外观质量、表面光洁度和可能存在的缺陷如气泡、凹痕、烧焦、银纹等都有十分重要的影响。
其次,在加工过程中,模具结构对操作的难易程度影响较大。
在大批量生产塑料产品时,应尽量减少开模、合模的过程和取制品过程中的手工劳动。
为此,常采用自动开合模自动顶出机构,在全自动生产时还要保证制品能自动从模具中脱落。
另外,模具对制品的成本也有影响,当批量不大时,模具的费用在制件上的成本所占比例将会很大,这时应尽可能的采用结构合理而简单的模具,降低成本。
现代生产中,合理的加工工艺,搞笑的设备、先进的模具是必不可少的三项重要因素,尤其是模具对现实材料加工工艺要求、塑料制件的使用要求和造型设计起重要的作用。
高效的全自动设备也只有装上能自动化生产的模具才有可能发挥其作用,产品的生产和更新都是以模具的制造和更新为前提的。
由于制件品种和产量需求很大,对模具也提出了越来越高的要求,从而促进模具不断向前发展。
1.2模具的发展趋势
近年来,模具增长十分迅速,高效率、自动化、大型、微型、精密、高寿命的模具在整个模具产量中所占的比重越来越大。
从模具设计和制造角度来看,模具的发展趋势可分为以下几个方面:
(1)提高大型、精密、复杂、长寿命模具的设计水平及比例。
这是由于塑料模成型的制品日渐大型化、复杂化和高精度要求以及因高生产率要求而发展的一模多腔所致
(2).在塑料模设计制造中全面推广应用CAD/CAM/CAE技术。
CAD/CAM技术已发展成为一项比较成熟的共性技术,近年来模具CAD/CAM技术的硬件与软件价格已降低到中小企业普遍可以接受的程度,为其进一步普及创造良好的条件;基于网络的CAD/CAM/CAE一体化系统结构初见端倪,其将解决传统混合型CAD/CAM系统无法满足实际生产过程分工协作要求的问题;CAD/CAM软件
的智能化程度将逐步提高;塑料制件及模具的3D设计与成型过程的3D分
(3)推广应用热流道技术、气辅注射成型技术和高压注射成型技术。
采用热流道技术的模具可提高制件的生产率和质量,并能大幅度节省塑料制件的原材料和节约能源,所以广泛应用这项技术是塑料模具的一大变革。
制订热流道元器件的国家标准,积极生产价廉高质量的元器件,是发展热流道模具的关键。
气体辅助注射成型可在保证产品质量的前提下,大幅度降低成本。
目前在汽车和家电行业中正逐步推广使用。
气体辅助注射成型比传统的普通注射工艺有更多的工艺参数需要确定和控制,而且常用于较复杂的大型制品,模具设计和控制的难度较大,因此,开发气体辅助成型流动分析软件,显得十分重要。
另一方面为了确保塑料
(4)开发新的成型工艺和快速经济模具。
以适应多品种、少批量的生产方式。
(5)提高塑料模标准化水平和标准件的使用率。
我国模具标准件水平和模具标准化程度仍较低,与国外差距甚大,在一定程度上制约着我国模具工业的发展,为提高模具质量和降低模具制造成本,模具标准件的应用要大力推广。
为此,首先要制订统一的国家标准,并严格按标准生产;其次要逐步形成规模生产,提高商品化程度、提高标准件质量、降低成本;再次是要进一步增加标准件的规格品
(6)应用优质材料和先进的表面处理技术对于提高模具寿命和质量显得十分必要。
(7)研究和应用模具的高速测量技术与逆向工程。
采用三坐标测量仪或三坐标扫描仪实现逆向工程是塑料模CAD/CAM的关键技术之一。
研究和应用多样、调整、廉价的检测设备是实现逆向工程的必要前提.
1.3设计在学习模具制造中的作用
通过对模具专业的学习,掌握了常用材料在各种成型过程中对模具的工艺要求,各种模具的结构特点及设计计算的方法,以达到能够独立设计般模具的要求。
在模具制造方面,掌握一般机械加工的知识,金属材料的选择和热处理,了解模具结构的特点,根据不同情况选用模具加工新工艺。
毕业设计能够对以上各方面的要求加以灵活运用,综合检验大学期间所学的知识。
第二章塑件制品分析
2.1塑件的工艺分析
塑件形状如下图2-1所示:
图2-1电热水壶外壳
依据实体零件分析,该塑件主体为空间曲面结构,底部为平面支撑板,壁厚为2mm,大体上较为均匀,周边有嵌件配合,并带有螺纹用于紧固,还有多个孔,零件造型较为复杂,给模具的加工带来了很大的难度。
该制件强度要求不高,只需满足日常使用即可,但是外观要求较高。
聚丙烯(Polyporylene简称PP)的注塑成型制品表面光洁,具有较高的表面硬度和刚性,耐应力开裂、耐热,常用于成型壳、罩类零件,故该制品选用PP材料注塑而成。
2.2塑料水壶外壳材料的成型特性与工艺参数
PP化学名称聚丙烯,无色、无味、无毒的,外观似聚乙烯,但比聚乙烯更透明是一种半结晶性材料,不吸水、光泽好、易着色,密度小,它比PE更坚硬且具有更高的熔点,为160~175℃,具有良好的电性能和高频绝缘性,不受湿度影响,但低温时变脆、不耐磨、易老化,经改善后可作为一种工程材料,广泛应用于家用电器、管材等多个领域,改性PP用作汽车配件具有十分广阔的开发前景。
PP收缩率为1.0~2.5%,成型温度为160~220℃,其注塑成型特性为:
1)结晶料,湿性小,易发生融体破裂,长期与热金属接触易分解;
2)流动性好,但收缩范围及收缩值大,易发生缩孔、凹痕、变形;
3)冷却速度快,浇注系统及冷却系统应缓慢散热,并注意控制成型温度,料温低温高压时容易取向,模具温度低于50度时,塑件不光滑,易产生熔接不良,流痕,90度以上易发生翘曲变形,故温度应该控制在80度左右;
4)塑料壁厚须均匀,避免缺胶,尖角,以防应力集中
2.3制品的结构工艺性
2.3.1塑件的尺寸精度分析
该塑件许标注公差的尺寸有9900.88,232-01.80,23-00.44,10000.88,110-01.00,22801.60,1.60
2310,40-00.56属于一般精度要求,其他未标注公差的尺寸均为自由尺寸,可采用8级精度。
表2.3.1塑件主要尺寸的公差要求
部位
塑件标注尺寸
塑件尺寸公差
外形尺
寸
55
0
-1.40
114
0
-2.00
56.5
0
-1.40
114
0
-2.00
98
0
-1.80
75
0
1.60
内形尺
寸
7×4
+0.560
37×35
1.00
0
Φ3
0.48
0
2×12
+0.720
Φ5
0.56
0
35
1.00
0
56
1.40
0
2.3.2塑件的表面质量分析
该塑件要求外观光洁,不允许有成型斑点和熔接痕,塑件表面粗糙度无特殊要求。
2.3.3塑件的结构工艺分析
1)从图纸看来,该塑件的外形为空间曲面,壁厚大体均匀,且符合最小壁厚要求。
2)由于塑件有多个侧孔,故四周都须设置侧向分型抽芯机构。
3)为使塑件顺利脱模,可在塑件内部增设1°~2°的拔模斜度。
综上分析,该塑件可采用注塑成型加工。
2.3.4塑件的生产批量该塑件的生产类型是大批量生产,因此在模具设计中要提高塑件的生产率,倾向于采用高寿命、自动脱模模具,以便降低生产成本。
2.4注塑机的选择
2.4.1计算塑件体积和重量
33
Vg=70857mm3=70.857cm3塑件质量计算:
查有关手册,取PP的密度ρ=0.91g/cm3,所以塑件的质量为
M=V*ρ=Vg*ρ=70.857*0.91g=64.5g。
2.4.2确定型腔数量
由于塑件存在多个孔类结构,四周都须设置外侧抽芯机构,故采用一模一腔。
2.4.3确定注塑成型的工艺参数
PP注塑模工艺条件:
注塑机选用:
由于PP具有高结晶性,需采用注射压力较高及可多段控制的电脑注塑机。
锁模力一般按3800t/m2来确定,注射量20%-85%即可。
熔化温度:
PP的熔点为160-175℃,分解温度为350℃,但在注射加工时温度设定不能超过275℃。
熔融段温度最好在240℃。
模具温度:
模具温度50-90℃,对于尺寸要求较高的用高模温。
型芯温度比型腔温度低5℃以上。
注射压力:
采用较高注射压力(1500-1800bar)和保压压力(约为注射压力的80%)。
大概在全行程的95%时转保压,用较长的保压时间。
注射速度:
为减少内应力及变形,应选择高速注射,但有些等级
的PP和模具不适用(出现气泡、气纹)。
如刻有花纹的表面出现由浇口扩散的明暗相间条纹,则要用低速注射和较高模温。
根据以上所述及计算结果,可选择设备型号、规格、确定型腔数。
注射机的
额定注射量为注射量为Vb,每次的注射量不超过它的80%,即n=(0.8Vb-Vj)/Vg式中n—型腔数;
Vj—浇注系统的体积(g);
Vg—塑件体积。
估算浇注系统的体积Vj:
根据浇注系统初步方案进行估算浇注系统体积。
Vj=4.8cm3
该模具确定为一一模一腔,即n=1
则Vb=(nVg+Vj)/0.8=94.6cm3根据该塑件的结构特点和PP的成型性能,查有关资料初步确定塑件的注射成型工艺参数,如下表所示:
表2-1塑件的注射成型工艺参数
工艺参数
内容
工艺参数
内容
预热和干燥
温度80~90℃
成型时间/s
注射时间
0~2
时间2h
保压时间
20~60
料筒温度/℃
前段
200~220
冷却时间
15~50
中段
220~240
总周期
37~112
后段
180~210
螺杆转速/(r/min)
30~60
喷嘴温度
/℃
190~220
后处理
方法
热水浸泡
模具温度
/℃
0~50
温度/℃
70
注射压力
/MPa
40~80
时间/h
2~4
2.4.4确定模具温度和冷却方式
PP为半结晶型塑料,在熔融温度下有较好的流动性,壁厚一般,在保证顺利脱模的前提下可尽量降低模温,以缩短冷却时间,从而提高生产率。
所以模具应考虑适当的循环水冷却,成型模具度控制在30~50℃。
2.4.5确定成型设备
由于塑件采用注射成型加工,使用一模一腔分布,因此可计算出一次注射成
型过程所用塑料量为:
W=n*w+w废料=1X64.5+64.5×20%=77.4g
根据以上一次注射的分析以及考虑到塑件品种、塑件结构、生产批量及注射工艺参数、注射模具尺寸大小等因素,参考设计手册,初选SX—ZY-500型螺杆式注射机。
记录下SX—ZY-500型螺杆式注射机的主要技术参数,见下表:
表2-2SX—ZY-500型螺杆式注射机的主要技术参数
号
序
主要技术参数项目
参数数值
1
最大注射量/cm3
500
2
注射压力/MPa
1040
3
锁模力/kN
1400
4
动、定模模板最大安装尺寸(/mm×mm)
620x520
5
最大模具高度/mm
450
6
最小模具高度/mm
300
7
最大开模行程/mm
500
8
喷嘴前端球面半径/mm
12
9
喷嘴孔直径/mm
4
0
1
定位圈直径/mm
125
11
定位孔径/mm
180
第三章分型面及浇注系统的设计
3.1分型面的选择
3.1.1分型面的定义
分型面是指模具上用以取出制品或者浇注系统凝料的可分离接触面,通过分型面将模具分成两个或若干个部分,开模时,有序的完成制品脱模,再由顶出系统把制品及浇注系统凝料从模具中顶出(自动脱落)或取出(机械手或者手工取出),之后将模具型腔内的杂物清除,或将嵌件安放于模具型腔内。
3.1.2分型面设计原则
分型面出售排位影响外,还受制品的形状、外观、精度、浇口位置、滑块、顶出及加工等多种因素影响。
合理的分型面是制品完好成型的先决条件,一般应遵循一下几个原则:
(1)利于脱模:
分型面应取在塑件的最大轮廓处,同时应使塑件留在顶出侧,由于推出机构通常设置在动模一侧,将型芯设置在动模部分,塑件冷却收缩后包紧型芯,使塑件留在动模,这样有利于脱模。
如果塑件的壁厚较大,内孔较小或者有嵌件时,为了使塑件留在动模,一般应将凹模也设在动模一侧。
把模斜度小或塑件较高时,为了便于脱模,可将分型面选在塑件中间部分,但此塑件外形有分型的痕迹。
(2)确保之塑件的尺寸精度:
为保证美观,分型面应尽量不破坏制品光滑的外观面;为保证制品尺寸,当制品外形比较长,应考虑减小脱模斜度造成塑件大小端尺寸的差异。
(3)简化模具结构:
应尽量避免定模侧抽芯,本例的四个侧滑块都设在动模一侧满足此要求,而且侧向抽芯应尽量短,楔紧机构尽量小,同时要便于排气和合理安排浇注系统。
(4)便于加工。
(5)满足注塑机技术规格的要求。
综合上述条件,本例的分型面设计如下图3-1所示:
图3-1水壶外壳分型面
3.2浇注系统的设计
浇注系统是注塑机喷嘴到型腔之间的进料通道,一般是由主流道、分流道、浇口和冷料穴组成。
浇注系统在注塑成型过程中主要起输送物料、传递压力、交换热量以及封堵型腔的作用。
浇注系统的设计是注塑模具设计的一个重要环节,它对注塑成型周期和塑件的质量(如外观、物理性能、尺寸精度)都有直接影响,在设计时要注意以下几点原则:
(1)型腔布置和浇口开设部位力求对称,防止模具承受偏载而造成溢料现象。
(2)型腔和浇口的排列要尽可能地减少模具外形尺寸。
(3)系统流道应尽可能短,断面尺寸适当(太小则压力及热量损失大,太大则塑料耗费大):
尽量减少弯折,表面粗糙度要低,以使热量及压力损失尽可能小。
4)对多型腔应尽可能使塑料熔体在同一时间内进入各个型腔的深处及角
落,及分流道尽可能平衡布置
(5)满足型腔充满的前提下,浇注系统容积尽量小,以减少塑料的耗量。
(6)浇口位置要适当,尽量避免冲击嵌件和细小型芯,防止型芯变形浇口的残痕不应影响塑件的外观。
考虑到塑件的外观要求较高,其结构较为复杂,为顶出方便以及能顺利将废料拉出,浇口采用分便加工修整、凝料去除容易且不会在塑件外壁留下痕迹的侧浇口,模具采用单分型面结构两板模,模具制造成本比较容易控制在合理的范围内。
浇注系统的设计如下图3-2所示:
图1-2浇注系统的设计
3.2.1主流道和定位圈的设计
注塑模的主流道是使注塑机喷嘴与型腔(单型腔模)或分流到连接的一段进料通道,它将注塑机喷嘴注出的塑料熔体导入分流道或型腔,其形状为圆锥形,便于熔体顺利的向前流动,开模时主流道凝料又能顺利拉出来,主流道的尺寸直接影响到塑料熔体的流动速度和充模时间,由于主流道要与高温塑料和注塑机喷嘴反复接触和碰撞,通常不直接开在定模上,而是将它单独设计成主流道套镶入定模板内。
主流道套通常又高碳工具钢制造并热处理淬硬。
塑件外表面不许有浇口痕,又考虑取料顺利,采用带直流道与分流道的侧浇口,为了方便于拉出流道中的凝料,将主流道设计成锥形
主流道与注射机的高温喷嘴反复接触碰撞,故应设计成独立可拆卸更换的浇口套,采用优质钢材制作,常用T8A、T10A制造,并经热处理提高硬