机械制造专业毕业论文连杆钻孔φ10H9专用夹具设计.docx
《机械制造专业毕业论文连杆钻孔φ10H9专用夹具设计.docx》由会员分享,可在线阅读,更多相关《机械制造专业毕业论文连杆钻孔φ10H9专用夹具设计.docx(12页珍藏版)》请在冰豆网上搜索。
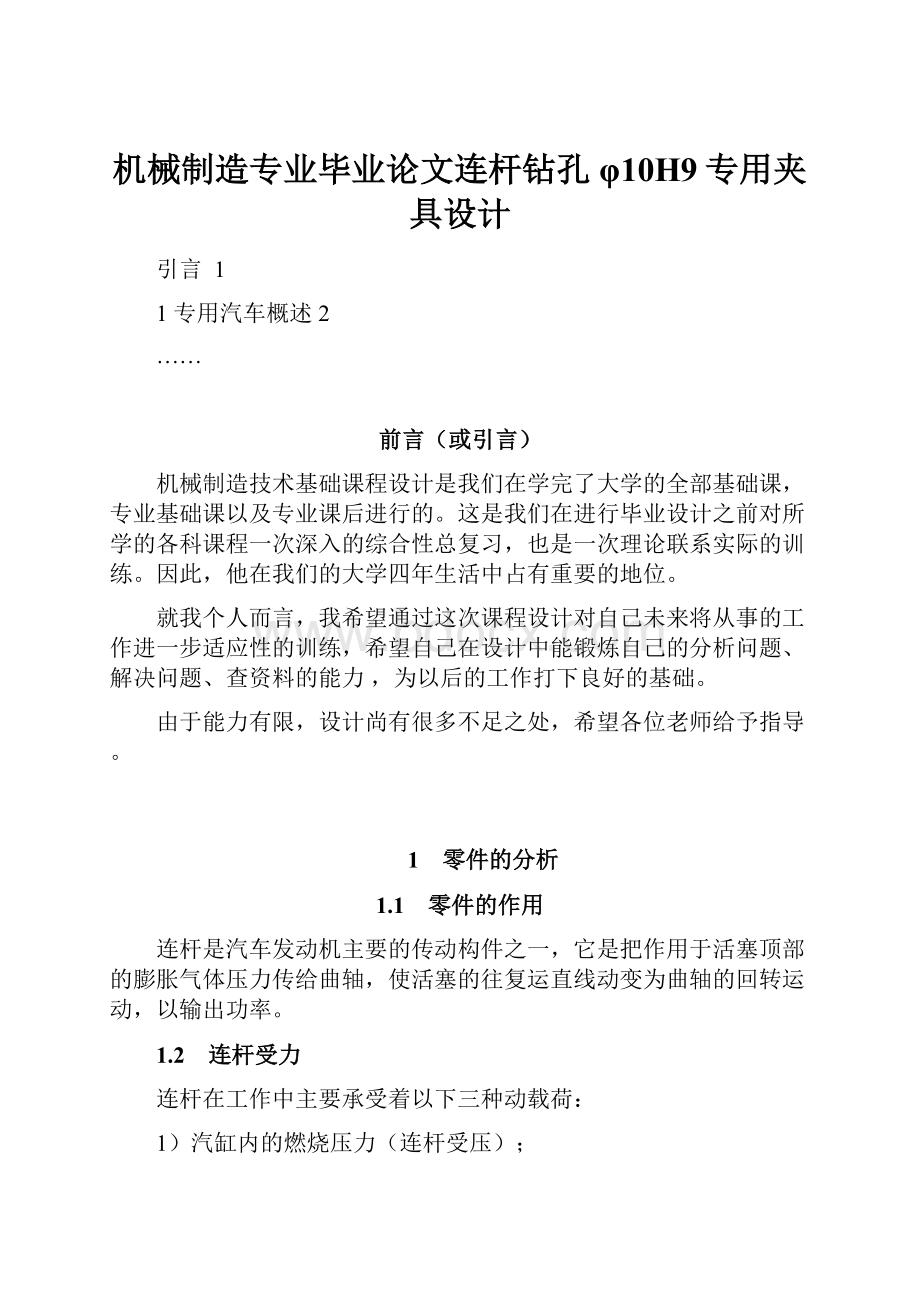
机械制造专业毕业论文连杆钻孔φ10H9专用夹具设计
引言1
1专用汽车概述2
……
前言(或引言)
机械制造技术基础课程设计是我们在学完了大学的全部基础课,专业基础课以及专业课后进行的。
这是我们在进行毕业设计之前对所学的各科课程一次深入的综合性总复习,也是一次理论联系实际的训练。
因此,他在我们的大学四年生活中占有重要的地位。
就我个人而言,我希望通过这次课程设计对自己未来将从事的工作进一步适应性的训练,希望自己在设计中能锻炼自己的分析问题、解决问题、查资料的能力,为以后的工作打下良好的基础。
由于能力有限,设计尚有很多不足之处,希望各位老师给予指导。
1 零件的分析
1.1 零件的作用
连杆是汽车发动机主要的传动构件之一,它是把作用于活塞顶部的膨胀气体压力传给曲轴,使活塞的往复运直线动变为曲轴的回转运动,以输出功率。
1.2 连杆受力
连杆在工作中主要承受着以下三种动载荷:
1)汽缸内的燃烧压力(连杆受压);
2)活塞连杆组的往复运动惯性力(连杆受拉);
3)连杆高速摆动时产生的横向惯性力(连杆受弯曲应力);
2 工艺规程设计
2.1 连杆材料及毛坯制造方法
由于连杆在工作中承受多种急剧变化的动载荷,所以不仅要求其材料具有足够的疲劳强度及结构刚度,而且还要使其纵剖面的金属宏观组织纤维方向应沿着连杆中心线并与连杆外形相符,不得有扭曲、断裂、裂纹、疏松、气泡、分层、气孔和夹杂等缺陷。
连杆成品的金相显微组织应为均匀的细晶结构,不允许有片状铁素体。
连杆材料采用35MnVs,经调质处理后,硬度为HB226~271。
采用整体模锻的加工方式。
具有劳动生产率高、锻件质量好、材料利用率高、成本底等优点。
另外,为避免毛坯出现缺陷(疲劳源),要求对其进行100%的硬度测量和探伤。
2.2 基面的选择
基准面选择是工艺规程设计中的重要工作之一。
基面选择的正确与合理,可以使加工质量得到保证,生产效率得以提高。
否则,加工工艺过程中会问题百出,更有甚者,还会造成零件大批报废,使生产无法正常进行。
粗基准的选择:
在选择粗基准时,应满足以下要求:
(1)连杆大小端孔圆柱面及两端面应与杆身纵向中心线对称;
(2)连杆大小端孔及两端面应有足够而且尽量均匀的加工余量;
(3)连杆大小端外形分别与大小端孔中心线对称;
(4)保证作为精基准的端面有较好的表面质量。
为此,第一道工序为粗磨两平面,为了保证两平面有均匀的加工余量,采用互为基准。
先选取没有凸起标记一侧的端面为粗基准来加工另一个端面,然后以此加工过的端面为基准加工没有凸起标记一侧的端面,并在以后的大部分工序中以此端面作为精基准来定位,这样,作为精基准的端面有较好的表面质量。
因加工是在同一台磨床,通过工作台回转完成加工的,故调整夹具定位面高度差与加工余量相等。
这样既能保证两平面有足够的加工余量,又能很好地保证两端面与连杆杆身纵向中心对称。
在加工连杆小端时以其外表面定位,这样可以保证加工后的孔与其外表面的同轴度误差较小。
由于大小端端面面积大、精度高、定位准确、夹紧可靠,所以大部分工序选用其一个指定的端面(消除三个自由度)和小端孔(消除两个自由度),以及大端孔处指定的一个侧面作为精基准。
这不仅使基准统一,而且还减少了定位误差(基准重合)。
2.3 连杆的主要加工表面及技术要求
连杆的主要加工表面有:
大小端孔、上下端面、大端盖、体结合面以及连杆螺栓孔等。
主要技术要求为:
1大小端孔的精度:
大端孔尺寸为¢30
mm,小孔尺寸为¢20
mm,大端孔及小端孔粗糙度均为Ra0.8μm,大端孔的圆柱度公差为0.006mm,小端衬套孔的圆柱度公差为0.00125mm。
且采用分组装配。
2上下端面的精度:
大小端孔的上下端面粗糙度均为Ra6.3μm
3大小端孔的中心距:
大小端孔的中心距影响气压的压缩比,所以对其要求较高,即中心距为100
mm
4大端的斜孔精度:
大端处斜孔尺寸为φ10H9,距上端面的距离为¢20
mm,粗糙度均为Ra0.8μm,斜孔对大端孔内表面的对称度为0.3mm。
斜孔的轴心与大小端孔圆心的连线在X平面内投影的夹角为60度。
2.4 制定工艺路线
制订工艺路线的出发点,应当是使零件的几何形状,尺寸精度及位置精度等技术要求得到合理的保证。
在生产纲领为中批生产的条件下,可以考虑采用万能性机床配以专用夹具来提高生产效率。
除此以外,还应当考虑经济效率,以便使生产成本尽量下降。
连杆机械加工工艺过程的拟定:
(1)连杆两个平面:
粗磨→半精磨→精磨。
(2)连杆小端孔:
钻孔→拉孔→精镗底孔→精镗。
(3)连杆大端孔:
扩孔→拉孔→扩孔→粗镗→半精镗→精镗→珩磨。
(4)检验:
连杆总成的关键工序和最终加工之后,均应安排检验工序。
(5)去毛刺:
在铣大小端去重凸块、铣连杆体等工序时,均应安排去毛刺工序。
2.5 连杆的强度计算
(一)连杆小头的应力计算
1.连杆小头的受力计算
=1Kg
式中,x取0.9——1.4;D为缸径。
=3611.3N
式中,
为连杆小头的受力(N);r为曲柄半径(mm);n为曲柄转速(r/min);mp为活塞组质量;L为连杆中心距(mm)。
2.连杆小头截面拉伸力负荷Ft及弯矩M
假设惯性力Fi在油膜的作用下以余弦方式分布在连杆小头孔的上方,可得出连杆小头任意截面上所受的拉伸负荷Ft和弯矩M
a)拉伸力负荷Ft的计算
(当0≤α≤π/2时)
式中,
(当0.1π<α≤π时)
取α=45°,K=-0.605,Ft=754.89N
b)弯矩M的计算
式中,M为弯矩(N·mm);rm为中性层曲率半径(mm).
c)任意截面应力计算
式中,σ为应力(MP);A为小头横截面积(mm2);e1、e2、y、r、rm、w
(二)连杆大头应力计算
1.连杆大头受力
式中,mrecip为连杆的往复质量(kg);mrot为连杆大头的旋转质量(kg);mc为连杆盖的质量(kg);
为连杆大头的受力(N);r为曲柄半径(mm);n为曲柄转速(r/min);mp为活塞组质量;L为连杆中心距(mm)。
2.连杆大头截面拉伸力负荷Ft及弯矩M
a)拉伸力负荷Ft的计算
(当0≤α≤π/2时)
式中,
(当0.1π<α≤π时)
取α=45°
K=-0.605
b)弯矩M的计算
式中,M为弯矩(N·mm);rm为中性层曲率半径(mm).
c)任意截面应力计算
式中,σ为应力(MP);A为小头横截面积(mm2);e1、e2、y、r、rm、w
3.连杆杆身的强度计算
连杆摆动平面内的惯性力引起的弯曲应力可忽略不计。
由压缩上止点时的气体压力及排气上止点的惯性力引起的杆身应力分别为:
对连杆杆身进行强度校核时,通常按连杆杆身的双应力幅的大小来判断。
连杆杆身的双应力幅为:
其中Fp=62800NAs=34254mm2
双幅应力:
±2σa=240MP
式中,σa为应力幅(MP);Fp为最大燃气压力(N);As为连杆杆身截面积(mm2)。
4.连杆的强度评估
部位
工作转速范围内
超速工况时
连杆杆身双应力幅
250
连杆小头
无应力集中处
300
550
有应力集中处
200
350
连杆大头
无应力集中处
250
450
有应力集中处
170
300
3 专用夹具设计
为了提高劳动生产率,保证加工质量,降低劳动强度,需要设计专用夹具。
这里的夹具为连杆大端处斜孔φ10mm的专用夹具,用于z5025圆柱立式钻床,φ10的钻头。
3.1 设计主旨
本夹具主要用来钻φ10mm孔的,且有一定的技术要求。
但加工本道工序时,φ10mm孔尚未加工,因此,主要应该考虑如何提高劳动生产率,降低劳动强度,同时还要达到要求的精度。
3.2 夹具的设计
3.2.1 定位基准的选择
由零件图可知,φ10mm孔大端处斜孔尺寸为φ10H9,距上端面的距离为¢20
mm,斜孔内表面粗糙度为Ra0.8μm,对大端孔内表面的对称度为0.3mm。
斜孔的轴心与大小端孔圆心的连线在X平面内投影的夹角为60度。
3.2.2 切削力及夹紧力的计算
切削刀具:
麻花钻,钻头直径D=10mm,β=30°,2kr=118,α0=12°,ψ=50°,则
切削扭矩M=0.40D2f0.7Kp
其中,D=10mm,f=5mm,Kp==1,所以
M=0.40
102
50.7
1=123.4N·mm
切削力Ff=1402Df0.7Kp
所以
Ff=1402
10
50.7
1=43254N
计算切削力时,必须考虑安全系数,安全系数K=K1K2K3K4
式中K1-----基本安全系数,K1=1.5
K2-----加工性质系数,K2=1.1
K3-----刀具钝化系数,K3=1.1
K4-----断续切削系数,K4=1.1
于是,F=FfK=43254
1.5
1.1
1.1
1.1=86356.6N
上面计算的力为麻花钻垂直方向的力,水平方向的力由四个螺栓保证,由于钻孔时,钻头所引起的水平方向的力很小,只要不螺栓拧紧即可,这里不做具体计算。
3.2.3 定位误差分析
(1)定位元件尺寸及公差的确定。
本夹具的主要定位元件为一定位销和三角斜块,定位销与夹具体上相应的孔采用过赢配合且能保证连杆小端的公差要求,即为:
定位销A20f7
28GB2203-80
三角块的斜面要与连杆杆身的斜面一致,且粗糙度为Ra3.2μm。
(2)钻φ10mm孔的钻套确定。
由于待加工的φ10mm孔面为弧面,所以采用特殊钻套,来起导向作用以及接触加工表面时的力均衡。
钻套底部与连杆大端圆柱面有0.2mm的间隙,用于排削,为避免发生干涉,钻套下端一侧设有倒圆角。
见图
(1)
图
(1)
3.2.4 夹具设计及操作的简要说明
如前所述,在设计夹具时,为了提高劳动生产率,应首先着眼于机动夹紧,所以采用四个螺栓用来夹紧连杆。
连杆要准确处于30°的位置才能进行钻孔,考虑连杆小端可以用定位销定位,为保证30°的位置,将斜块确定在连杆杆身上,同时,斜块也起到平衡钻刀向下钻孔的力,用钻套来引导钻刀的走向,设计了特殊钻套。
加工时将连杆的小端孔插入定位销里,之后,连杆会自然由于重力停在斜块上面,既30°的位置,此后,将四个螺栓用螺母拧上。
注意,处在滑槽里的螺栓要使橡胶套的表面完全与连杆表面相切,起到完全定位的作用。
图
(2)为装配后的立体图。
图
(2)
4结论
我国的汽车行业正在飞速发展,汽车的动力部分也在不断改进,连杆是汽车动力不可缺少的一部分,它的工作情况会直接影响汽车的运行状态。
所以,如何能使连杆的生产高效率、高质量,省成本、省时间是我们今天汽车行业的努力方向。
本文根据连杆加工的一个特殊工序来对其夹具的设计,使其加工过程得以顺利进行,保证钻孔的位置及精度的准确性,同时也借助这个夹具的设计,来提高连杆加工的效率,解决连杆的定位、夹紧问题,为连杆的加工提供一个更方便的路径。
本夹具还存在不足之处。
一事绘图软件本人掌握的还不够熟练,二是对夹具设计的知识还有欠缺。
绘图时细节地方会画的不准确,造成重复性的修改,影响工作的效率,另一方面,夹具的工作质量和工作寿命还未探讨,这些都需要进一步研究和进一步实践来解决。
参考文献
[1]王光斗王春福.机床夹具设计手册.第3版.上海科学出版社,2000.
[2]肖继德陈宁平.机床夹具设计.第2版.机械工业出版社,2000
[3]赵家齐.机械制造工艺学课程设计知道书.第2版.机械工业出版社,2002
[4]刘守勇.机械制造工艺与机床夹具.第2版.机械工业出版社,2005
[5]陆剑中家宁.金属切削原理与刀具.第3版.机械工业出版社,2004